Praezisionsbearbeitung Loesung fuer Kurbelwelle Bohrungen
Die Bearbeitungsqualität der Kurbelwellenbohrung hat einen großen Einfluss auf die Leistung des Motors. Die Chery Engine Division hat den Endbearbeitungsplan der Kurbelwellenbohrung des Motorzylinders aus Gusseisen entsprechend den tatsächlichen Verarbeitungsbedingungen kontinuierlich erforscht und verbessert und bemerkenswerte Ergebnisse erzielt. Die Verarbeitungsqualität und Effizienz wurden effektiv verbessert.
Der Zylinderblock ist ein wichtiger Grundbestandteil des Motors. Seine Hauptfunktion besteht darin, die verschiedenen Mechanismen und Systeme zu einem zusammenzufügen. Die wichtigsten beweglichen Teile des Motors - die Kurbelwelle, der Kolben und die Pleuelstange - haben eine sehr enge Beziehung zum Zylinder. 1 ist eine schematische Ansicht eines Kurbelverbindungsmechanismus. Gegenwärtig erreicht unser herkömmlicher Benzinmotor eine Höchstgeschwindigkeit von mehr als 6000 U / min. Die Kurbelwelle bildet einen Ölfilm zwischen dem Kurbelwellenloch des Motorblocks und der Lagerbuchse und stützt und schmiert die schnell laufende Kurbelwelle mittels eines Gleitlagers. Dies stellt hohe Prozessanforderungen an die Präzisionsbearbeitung der Kurbelwellenbohrung.

Da die Bearbeitungsqualität des Kurbelwellenlochs einen großen Einfluss auf die Leistung des Motors hat, sind die Anforderungen an den Kurbelwellenlochprozess des Motors im Allgemeinen streng. Einschließlich Durchmesser, Position, Rundheit, Geradheit der Mitte jedes Kurbelwellenlochs und Oberflächenrauheit. Um diese anspruchsvollen Prozessspezifikationen zu erfüllen, wird bei der Präzisionsbearbeitung im Allgemeinen entweder Feinbohr- oder Klappbearbeitung eingesetzt.
I. Analyse der Feinbohrbearbeitung
Die Präzisionsbohrmethode wird zum Bearbeiten des Kurbelwellenlochs verwendet, und die anfänglichen Eingabekosten sind niedriger als bei der Scharniermethode. Es kann im selben Prozess wie die Endbearbeitung anderer Teile im Bearbeitungszentrum oder in speziellen Anlagen durchgeführt werden. Aufgrund der besonderen Prozessanforderungen setzen wir derzeit als Feinlösung eine Kombination aus zwei Präzisionsbohrwerkzeugen ein: Das erste Feinbohrwerkzeug führt die Kurbelwellenbohrungen des ersten und zweiten Zahnrads (siehe Abbildung 2). Das zweite Feinbohrwerkzeug wird von den verbleibenden Kurbelwellenlöchern unter der Auflage der Kurbelwellenlöcher des ersten und zweiten Zahnrads fein abgestützt (siehe Abbildung 3).
Da die Kurbelwellenbohrungen ein hohes Maß an Koaxialität zwischen den Zahnrädern gewährleisten müssen, muss beim Schlichten in die gleiche Richtung vorgeschoben werden. Wenn jedoch ein derart langes Kurbelwellenbohrwerkzeug das Kurbelwellenloch der ersten Geschwindigkeit bearbeitet, gibt es einen Fall, in dem der Sprung aufgrund mangelnder Unterstützung übermäßig ist. Daher wird das Kurbelwellenloch fertiggestellt, indem ein langes und ein kurzes Bohrwerkzeug kombiniert werden.
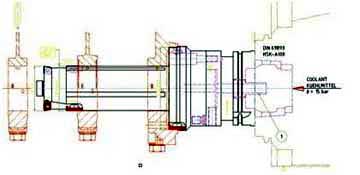
Abbildung 2 Feinbohrwerkzeug zur Bearbeitung von 1 und 2 Kurbelwellenbohrungen
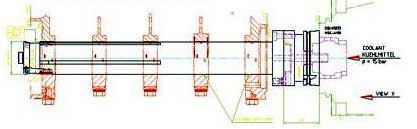
Abbildung 3 Feinbohrwerkzeug zur Bearbeitung der letzten Kurbelwellenbohrungen
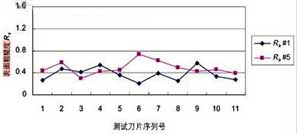
Abbildung 4 Klinge Karbidklinge Rauheit Schwankungen im Test, ein Teil erfüllen die Anforderungen des
Anschließend überprüften wir eine andere Lösung für das Schaufelmaterial des Feinbohrwerkzeugs, nämlich den Ersatz des vorhandenen Hartmetall Schaufel Materials durch CBN-Schaufelmaterial. Wir verlassen uns auf Werkzeuglieferanten, um mehr als 10 verschiedene CBN-Wendeschneidplatten für die Schnittprüfung der Kurbelwellenbohrung zu entwickeln. Die Testergebnisse zeigen: In Bezug auf die Rauheitskontrolle ist der CBN-Einsatz dem Hartmetalleinsatz deutlich überlegen und hat eine Verarbeitung Lebensdauer von über 200 Stück. Gleichzeitig sind aber auch einige neue Probleme aufgetreten: Wenn etwa 150 Teile mit einer CBN-Klinge bearbeitet werden, treten an der Seite des Lochs leichte Grate auf, und im Falle einer schweren Form kommt es zu einem Bördelung Phänomen. Die Grate und sogar das Bördeln stellen hier Qualitätsrisiken dar, die die Leistung des Motors beeinträchtigen und in schweren Fällen zu Qualitätsunfällen wie Buchsenkratzern und Blockierungen der Kurbelwelle führen. Bei der Behandlung des Kurbelwellenloch-Gratproblems haben wir die Bürste des Kurbelwellenlochs vergrößert, was die Existenz des Grats in gewissem Maße erleichterte, aber es besteht immer noch ein großes Qualitätsrisiko. Darüber hinaus ist die Qualitätsstabilität des Größenschemas der Kurbelwellenbohrung im Vergleich zum Scharnier schlecht, und das Risiko einer Qualitätskontrolle ist aufgrund des häufigen Werkzeugwechsels stark erhöht. Die Schwankung der Oberflächenrauheit des Werkstücks, die durch das Feinbohrwerkzeug erzeugt wird, nimmt schnell ab, wenn die Werkzeughaltbarkeit abnimmt. Ein Vergleich der Oberflächenrauheit eines mit einem CBN-Einsatz in einer feinen Kurbelwellenbohrung bearbeiteten Werkstücks ist in den Abbildungen 5 und 6 dargestellt.
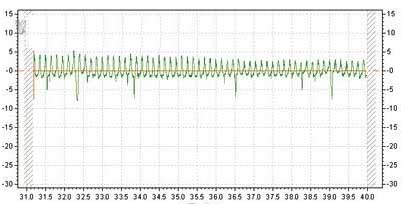
Abbildung 5 Nach dem Bohren des ersten Lochs die Oberflächenrauheit der Klinge feststellen
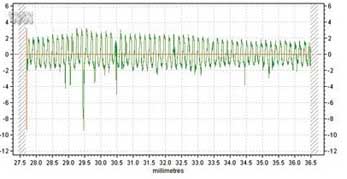
Abbildung 6 Oberflächenrauheitsbericht bei der Bearbeitung von 200 Teilen auf einer Bohrmaschine
II. Analyse der Scharnierbearbeitung
Wir haben viel an dem Kurbelwellenlochschema für die Präzisionsbohrbearbeitung geforscht. Wir haben eine Reihe neuer Wendeschneidplatten für die spanende Prüfung entwickelt, haben jedoch immer noch nicht die gewünschten Bearbeitungsergebnisse erzielt. Daher betrachten wir das Reibschema für die Kurbelwelle erneut. Aus Sicht der Kosten ist die einmalige Investition des Kurbelwellenlochscharniers groß. Das Vorangebot eines namhaften deutschen Honmaschinenherstellers beträgt 400.000 Euro (Preise variieren je nach Ausstattungsanforderung). Die Nachbearbeitungskosten des Scharniers sind jedoch viel geringer als die der Feinbohrung, und die Verarbeitungsqualität ist stabil. Die spezifische Implementierung des Kurbelwellenloch-Scharnierschemas ist in Fig. 4 gezeigt.
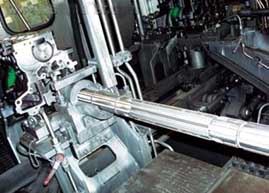
Abbildung 7 Implementierung des Scharnierschemas für das Kurbelwellenloch
Das Kurbelwellenlochscharnier wird mit einer Horizontalhonmaschine bearbeitet. Da die horizontale Honmaschine einen langen Arbeitshub hat, eignet sie sich zum Honen von tiefen Löchern wie Kurbelwellenlöchern und die Tiefe kann bis zu 3000 mm betragen. Während der Bearbeitung wird der Schleifstein des Honkopfes unter Einwirkung des Expansions- und Kontraktionsmechanismus radial vorgeschoben und das Werkstück nach und nach auf die erforderliche Größe bearbeitet. Der Außenumfang des Honkopfes wird mit 2 bis 10 Ölsteinen mit einer Länge von ca. 1/3 bis 3/4 der Bohrungslänge und sowohl der Drehbewegung als auch der Hin- und Herbewegung während des Bohrens eingestellt. Gleichzeitig wird es durch die Feder- oder Hydrauliksteuerung im Honkopf gleichmäßig angehoben, sodass die Kontaktfläche mit der Oberfläche des Lochs groß und die Verarbeitungseffizienz hoch ist.
Die Honzugabe beträgt im Allgemeinen nicht mehr als 0,2 mm. Bei der Bearbeitung von Gusseisen oder NE-Metallen kann die Umfangsgeschwindigkeit des Honens mehr als 50 m / min betragen, die Hubgeschwindigkeit des Honens sollte 15 - 20 m / min nicht überschreiten. Der Druck des Ölsteins auf die Lochwand beträgt im Allgemeinen 0,3–0,5 MPa, die grobe Bohrung kann etwa 1 MPa erreichen und die feine Bohrung kann weniger als 0,1 MPa betragen. Da der Schleifstein während des Honens in Oberflächenkontakt mit dem Werkstück steht, beträgt der vertikale Druck jedes Schleifpartikels auf der Oberfläche des Werkstücks nur 1/50 bis 1/100 desjenigen beim Schleifen. Darüber hinaus ist die Hongeschwindigkeit niedrig, so dass die Temperatur der Schneidzone im Bereich von 50 ° C bis 150 ° C gehalten werden kann, was vorteilhaft ist, um die Restspannung auf der bearbeiteten Oberfläche zu verringern und die Oberflächenqualität zu verbessern. Um die Späne zu waschen, ein Blockieren des Ölsteins zu vermeiden und die Temperatur und Oberflächenrauheit der Schneidzone zu verringern, muss die beim Honen verwendete Schneidflüssigkeit einen bestimmten Arbeitsdruck haben und gefiltert werden. Die meisten Schneidflüssigkeiten verwenden Kerosin oder Kerosin plus Spindelöl, und es können auch Hochdruckemulsionen verwendet werden.
Es wird aus dem Fluktuationstrend der Rauheitsmessungsberichtsdaten in 8 analysiert. Die Verarbeitungsstabilität des Scharniers ist sehr hoch, und die Haltbarkeit des Schleifkopfes kann mehr als 10.000 Stück auf einmal verarbeitet werden, und die Produktionseffizienz wird stark verbessert. Bei der Feinbearbeitungsmethode des CBN-Messers müssen alle 200 Teile einmal gewechselt werden. Der durchschnittliche Werkzeugwechsel und die erste Teilprüfung dauern 42 Minuten. Wenn die Zeit, die zum häufigen Wechseln des Werkzeugs benötigt wird, auf jedes Werkstück umgerechnet wird, gehen 12,6 s / Stück verloren. Nach der bestehenden Verarbeitungslinie von 120s / Stück beträgt die Produktion von Teilen 160.000 Stück / Jahr, der jährliche Verarbeitungsverlust wird 2.016.000 s betragen, mit dieser Zeit können mehr als 16.800 Stück pro Jahr verarbeitet werden.
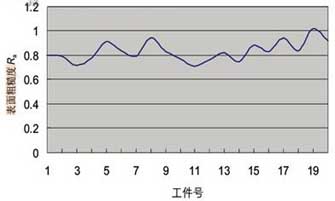
Abbildung 8 Bericht über die Messung der Produktrauheit nach 20 Tagen nach Durchführung des Programms für die Produktion mit Scharnieren
Die Tabelle stellt den Kostenverlust des Werkzeugverlusts dar, der durch verschiedene Endbearbeitungsmethoden der Kurbelwellenbohrung verursacht wird. Aus der Tabelle kann analysiert werden, dass der Werkzeugkostenunterschied des einzelnen Teils offensichtlicher ist. Der Analyse und Berechnung zufolge beträgt der Werkzeugverlust der Scharnierlösung bei einer Produktion von 1,03 Millionen Stück etwa 3,81 Millionen Yuan, verglichen mit der CBN-Präzisionslösung, die geringfügig dem Preis der Scharniervorrichtung entspricht. Die Qualitätskontrolle der Scharnierlösung ist wesentlich weniger schwierig und riskant.
Der Zylinderblock ist ein wichtiger Grundbestandteil des Motors. Seine Hauptfunktion besteht darin, die verschiedenen Mechanismen und Systeme zu einem zusammenzufügen. Die wichtigsten beweglichen Teile des Motors - die Kurbelwelle, der Kolben und die Pleuelstange - haben eine sehr enge Beziehung zum Zylinder. 1 ist eine schematische Ansicht eines Kurbelverbindungsmechanismus. Gegenwärtig erreicht unser herkömmlicher Benzinmotor eine Höchstgeschwindigkeit von mehr als 6000 U / min. Die Kurbelwelle bildet einen Ölfilm zwischen dem Kurbelwellenloch des Motorblocks und der Lagerbuchse und stützt und schmiert die schnell laufende Kurbelwelle mittels eines Gleitlagers. Dies stellt hohe Prozessanforderungen an die Präzisionsbearbeitung der Kurbelwellenbohrung.

Da die Bearbeitungsqualität des Kurbelwellenlochs einen großen Einfluss auf die Leistung des Motors hat, sind die Anforderungen an den Kurbelwellenlochprozess des Motors im Allgemeinen streng. Einschließlich Durchmesser, Position, Rundheit, Geradheit der Mitte jedes Kurbelwellenlochs und Oberflächenrauheit. Um diese anspruchsvollen Prozessspezifikationen zu erfüllen, wird bei der Präzisionsbearbeitung im Allgemeinen entweder Feinbohr- oder Klappbearbeitung eingesetzt.
I. Analyse der Feinbohrbearbeitung
Die Präzisionsbohrmethode wird zum Bearbeiten des Kurbelwellenlochs verwendet, und die anfänglichen Eingabekosten sind niedriger als bei der Scharniermethode. Es kann im selben Prozess wie die Endbearbeitung anderer Teile im Bearbeitungszentrum oder in speziellen Anlagen durchgeführt werden. Aufgrund der besonderen Prozessanforderungen setzen wir derzeit als Feinlösung eine Kombination aus zwei Präzisionsbohrwerkzeugen ein: Das erste Feinbohrwerkzeug führt die Kurbelwellenbohrungen des ersten und zweiten Zahnrads (siehe Abbildung 2). Das zweite Feinbohrwerkzeug wird von den verbleibenden Kurbelwellenlöchern unter der Auflage der Kurbelwellenlöcher des ersten und zweiten Zahnrads fein abgestützt (siehe Abbildung 3).
Da die Kurbelwellenbohrungen ein hohes Maß an Koaxialität zwischen den Zahnrädern gewährleisten müssen, muss beim Schlichten in die gleiche Richtung vorgeschoben werden. Wenn jedoch ein derart langes Kurbelwellenbohrwerkzeug das Kurbelwellenloch der ersten Geschwindigkeit bearbeitet, gibt es einen Fall, in dem der Sprung aufgrund mangelnder Unterstützung übermäßig ist. Daher wird das Kurbelwellenloch fertiggestellt, indem ein langes und ein kurzes Bohrwerkzeug kombiniert werden.
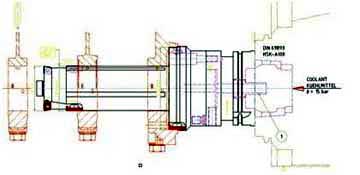
Abbildung 2 Feinbohrwerkzeug zur Bearbeitung von 1 und 2 Kurbelwellenbohrungen
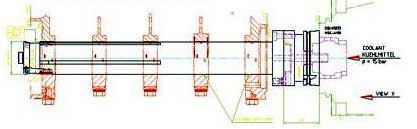
Abbildung 3 Feinbohrwerkzeug zur Bearbeitung der letzten Kurbelwellenbohrungen
Derzeit besteht das Bohrwerkzeug für das feine Kurbelwellenloch im Allgemeinen aus Hartmetall oder CBN. Hartmetalleinsätze sind weniger teuer, aber die Oberflächenrauheit des bearbeiteten Werkstücks ist nicht gut und die Haltbarkeit des Einsatzes ist gering. Als Reaktion auf dieses Problem haben wir mit Werkzeuglieferanten zusammengearbeitet, um die branchenweit am häufigsten verwendeten Rakelbeschichtungsmaterialien zu sammeln. Schneideversuche wurden an 16 Hartmetalleinsätzen unter Verwendung verschiedener Schneidwinkeltechniken durchgeführt. Um verschiedene geeignete Verarbeitungsparameter zu optimieren, sind die spezifischen Rauheitsschwankungen in Abbildung 4 dargestellt. Die besten experimentellen Ergebnisse von Hartmetalleinsätzen, die die Prozessanforderungen erfüllen, wie z. B. die Rauheit, sind nach einer Vielzahl von Überprüfungen 80 Teile auf einmal. Noch können die Anforderungen der Massenproduktion nicht erfüllt werden.
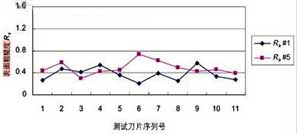
Abbildung 4 Klinge Karbidklinge Rauheit Schwankungen im Test, ein Teil erfüllen die Anforderungen des
Anschließend überprüften wir eine andere Lösung für das Schaufelmaterial des Feinbohrwerkzeugs, nämlich den Ersatz des vorhandenen Hartmetall Schaufel Materials durch CBN-Schaufelmaterial. Wir verlassen uns auf Werkzeuglieferanten, um mehr als 10 verschiedene CBN-Wendeschneidplatten für die Schnittprüfung der Kurbelwellenbohrung zu entwickeln. Die Testergebnisse zeigen: In Bezug auf die Rauheitskontrolle ist der CBN-Einsatz dem Hartmetalleinsatz deutlich überlegen und hat eine Verarbeitung Lebensdauer von über 200 Stück. Gleichzeitig sind aber auch einige neue Probleme aufgetreten: Wenn etwa 150 Teile mit einer CBN-Klinge bearbeitet werden, treten an der Seite des Lochs leichte Grate auf, und im Falle einer schweren Form kommt es zu einem Bördelung Phänomen. Die Grate und sogar das Bördeln stellen hier Qualitätsrisiken dar, die die Leistung des Motors beeinträchtigen und in schweren Fällen zu Qualitätsunfällen wie Buchsenkratzern und Blockierungen der Kurbelwelle führen. Bei der Behandlung des Kurbelwellenloch-Gratproblems haben wir die Bürste des Kurbelwellenlochs vergrößert, was die Existenz des Grats in gewissem Maße erleichterte, aber es besteht immer noch ein großes Qualitätsrisiko. Darüber hinaus ist die Qualitätsstabilität des Größenschemas der Kurbelwellenbohrung im Vergleich zum Scharnier schlecht, und das Risiko einer Qualitätskontrolle ist aufgrund des häufigen Werkzeugwechsels stark erhöht. Die Schwankung der Oberflächenrauheit des Werkstücks, die durch das Feinbohrwerkzeug erzeugt wird, nimmt schnell ab, wenn die Werkzeughaltbarkeit abnimmt. Ein Vergleich der Oberflächenrauheit eines mit einem CBN-Einsatz in einer feinen Kurbelwellenbohrung bearbeiteten Werkstücks ist in den Abbildungen 5 und 6 dargestellt.
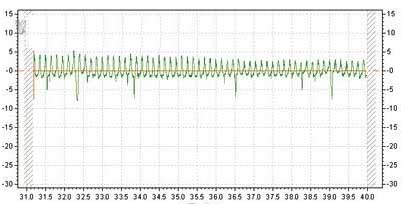
Abbildung 5 Nach dem Bohren des ersten Lochs die Oberflächenrauheit der Klinge feststellen
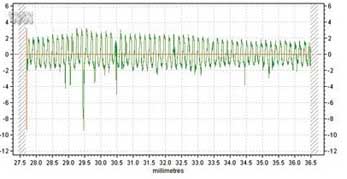
Abbildung 6 Oberflächenrauheitsbericht bei der Bearbeitung von 200 Teilen auf einer Bohrmaschine
II. Analyse der Scharnierbearbeitung
Wir haben viel an dem Kurbelwellenlochschema für die Präzisionsbohrbearbeitung geforscht. Wir haben eine Reihe neuer Wendeschneidplatten für die spanende Prüfung entwickelt, haben jedoch immer noch nicht die gewünschten Bearbeitungsergebnisse erzielt. Daher betrachten wir das Reibschema für die Kurbelwelle erneut. Aus Sicht der Kosten ist die einmalige Investition des Kurbelwellenlochscharniers groß. Das Vorangebot eines namhaften deutschen Honmaschinenherstellers beträgt 400.000 Euro (Preise variieren je nach Ausstattungsanforderung). Die Nachbearbeitungskosten des Scharniers sind jedoch viel geringer als die der Feinbohrung, und die Verarbeitungsqualität ist stabil. Die spezifische Implementierung des Kurbelwellenloch-Scharnierschemas ist in Fig. 4 gezeigt.
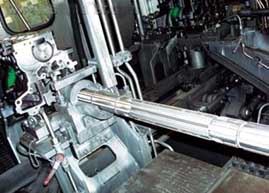
Abbildung 7 Implementierung des Scharnierschemas für das Kurbelwellenloch
Das Kurbelwellenlochscharnier wird mit einer Horizontalhonmaschine bearbeitet. Da die horizontale Honmaschine einen langen Arbeitshub hat, eignet sie sich zum Honen von tiefen Löchern wie Kurbelwellenlöchern und die Tiefe kann bis zu 3000 mm betragen. Während der Bearbeitung wird der Schleifstein des Honkopfes unter Einwirkung des Expansions- und Kontraktionsmechanismus radial vorgeschoben und das Werkstück nach und nach auf die erforderliche Größe bearbeitet. Der Außenumfang des Honkopfes wird mit 2 bis 10 Ölsteinen mit einer Länge von ca. 1/3 bis 3/4 der Bohrungslänge und sowohl der Drehbewegung als auch der Hin- und Herbewegung während des Bohrens eingestellt. Gleichzeitig wird es durch die Feder- oder Hydrauliksteuerung im Honkopf gleichmäßig angehoben, sodass die Kontaktfläche mit der Oberfläche des Lochs groß und die Verarbeitungseffizienz hoch ist.
Die Honzugabe beträgt im Allgemeinen nicht mehr als 0,2 mm. Bei der Bearbeitung von Gusseisen oder NE-Metallen kann die Umfangsgeschwindigkeit des Honens mehr als 50 m / min betragen, die Hubgeschwindigkeit des Honens sollte 15 - 20 m / min nicht überschreiten. Der Druck des Ölsteins auf die Lochwand beträgt im Allgemeinen 0,3–0,5 MPa, die grobe Bohrung kann etwa 1 MPa erreichen und die feine Bohrung kann weniger als 0,1 MPa betragen. Da der Schleifstein während des Honens in Oberflächenkontakt mit dem Werkstück steht, beträgt der vertikale Druck jedes Schleifpartikels auf der Oberfläche des Werkstücks nur 1/50 bis 1/100 desjenigen beim Schleifen. Darüber hinaus ist die Hongeschwindigkeit niedrig, so dass die Temperatur der Schneidzone im Bereich von 50 ° C bis 150 ° C gehalten werden kann, was vorteilhaft ist, um die Restspannung auf der bearbeiteten Oberfläche zu verringern und die Oberflächenqualität zu verbessern. Um die Späne zu waschen, ein Blockieren des Ölsteins zu vermeiden und die Temperatur und Oberflächenrauheit der Schneidzone zu verringern, muss die beim Honen verwendete Schneidflüssigkeit einen bestimmten Arbeitsdruck haben und gefiltert werden. Die meisten Schneidflüssigkeiten verwenden Kerosin oder Kerosin plus Spindelöl, und es können auch Hochdruckemulsionen verwendet werden.
Es wird aus dem Fluktuationstrend der Rauheitsmessungsberichtsdaten in 8 analysiert. Die Verarbeitungsstabilität des Scharniers ist sehr hoch, und die Haltbarkeit des Schleifkopfes kann mehr als 10.000 Stück auf einmal verarbeitet werden, und die Produktionseffizienz wird stark verbessert. Bei der Feinbearbeitungsmethode des CBN-Messers müssen alle 200 Teile einmal gewechselt werden. Der durchschnittliche Werkzeugwechsel und die erste Teilprüfung dauern 42 Minuten. Wenn die Zeit, die zum häufigen Wechseln des Werkzeugs benötigt wird, auf jedes Werkstück umgerechnet wird, gehen 12,6 s / Stück verloren. Nach der bestehenden Verarbeitungslinie von 120s / Stück beträgt die Produktion von Teilen 160.000 Stück / Jahr, der jährliche Verarbeitungsverlust wird 2.016.000 s betragen, mit dieser Zeit können mehr als 16.800 Stück pro Jahr verarbeitet werden.
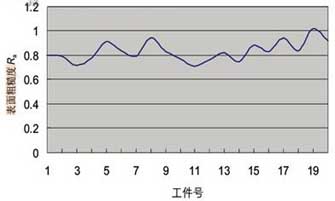
Abbildung 8 Bericht über die Messung der Produktrauheit nach 20 Tagen nach Durchführung des Programms für die Produktion mit Scharnieren
Die Tabelle stellt den Kostenverlust des Werkzeugverlusts dar, der durch verschiedene Endbearbeitungsmethoden der Kurbelwellenbohrung verursacht wird. Aus der Tabelle kann analysiert werden, dass der Werkzeugkostenunterschied des einzelnen Teils offensichtlicher ist. Der Analyse und Berechnung zufolge beträgt der Werkzeugverlust der Scharnierlösung bei einer Produktion von 1,03 Millionen Stück etwa 3,81 Millionen Yuan, verglichen mit der CBN-Präzisionslösung, die geringfügig dem Preis der Scharniervorrichtung entspricht. Die Qualitätskontrolle der Scharnierlösung ist wesentlich weniger schwierig und riskant.