CNC-Bearbeitung verschiedener Motorbasen
Die Motorbasis ist die Schlüsselkomponente des Motors. Die Rationalität des Aufbaus und der Verarbeitungstechnologie haben großen Einfluss auf die Leistung des Motors. Die Ungeeignetheit des Besens des Motors, niederfrequente elektromagnetische Geräusche, Vibrationen usw. hängen hauptsächlich mit der Bearbeitung des Maschinenfußes zusammen. Daher sollte die Struktur der Basis in angemessener Weise gemäß den Leistungsanforderungen des Motors ausgewählt und gemäß den technischen Anforderungen verarbeitet werden, um die durch die Bearbeitung der Basis verursachte Abweichung zu verringern und zu beseitigen. Heute werden wir die Motorständertypen und einige der grundlegendsten technischen Anforderungen aussortieren und mit Ihnen teilen.
Grundtyp der Motorbasis
● Je nachdem, ob die Basis magnetisch ist oder nicht, kann sie in magnetische und nichtmagnetische magnetische Basen unterteilt werden. Der Magnetfuß wird für Gleichstrommotoren und Schwenksynchronmotoren verwendet. Nichtmagnetische Gehäuse werden in Asynchronmotoren, Rotationssynchronmotoren und anderen Motoren mit laminierten Statorkernen verwendet.
● Je nach den unterschiedlichen Zuschnitten des Sockels kann dieser in Schweiß- und Gusssockel unterteilt werden. Die Schweißbasis ist aus Stahl geschweißt. Die Gussbasis kann in Stahlguss, Gusseisen oder Aluminiumlegierung gegossen werden; Das magnetisch durchlässige Stativ ist fast immer mit Stahl oder Stahl verschweißt.
● Nichtmagnetische Motorgehäuse bestehen in der Regel aus Grauguss. Die Motorbasis aus Gusseisen ist kostengünstig und bequem zu verarbeiten und ihre mechanische Festigkeit kann die Anforderungen allgemeiner kleiner und mittlerer Motoren erfüllen. Hochfeste Gusseisen- oder Stahlguss-Motorsitze werden nur in Anwendungen verwendet, in denen eine hohe mechanische Festigkeit erforderlich ist, z. B. bei explosionsgeschützten Motoren und Schiffsmotoren.
● Kleine Wechselstrommotoren und Mikromotoren. In den letzten Jahren wurden Aluminium-Silizium-Legierungen oder Aluminium-Magnesium-Legierungen zum Druckgießen von Motorsitzen verwendet. Die Struktur ist dadurch gekennzeichnet, dass die Aluminiumlegierung direkt auf den Statorkern gegossen werden kann, der innere Kreis des Motorsitzes nicht bearbeitet werden muss, einige Befestigungselemente weggelassen werden und der kleine Motor leichter gemacht werden kann. Der Nachteil ist, dass der Materialpreis der Aluminiumlegierung relativ hoch ist, die mechanische Festigkeit schwach ist und die Verschleißfestigkeit schlecht ist.
● Bei großen Motoren wurden aufgrund der geringen Leistung und des hohen Gewichts des Motors häufig geschweißte Sitze aus Profilstahl und Stahlblech verwendet. Im Vergleich zu Gusseisenständern ist das Gewicht des Schweißbodens bei gleicher mechanischer Festigkeit und struktureller Steifigkeit geringer. Beim Schweißen ist keine spezielle Form erforderlich und die Kosten sind relativ gering, der Produktionszyklus kann verkürzt werden und die individuelle Form des Motors kann erfüllt werden.
● Je nach Struktur der Basis kann diese in einen integralen Rahmen und einen separaten Rahmen unterteilt werden. Die strukturelle Steifigkeit des separaten Rahmens ist schwach und die Verarbeitungszeit ist länger. Wenn die Montage nicht korrekt ist, entspricht die gesamte Maschine nicht den Anforderungen. Die einzigartigen Vorteile liegen jedoch in der bequemen Installation und Wartung. Wenn das Design angemessen ist, sind die Montagegenauigkeit und die strukturelle Steifigkeit nicht länger die Einschränkungen.
Entsprechend den verschiedenen Schutz- und Kühlmethoden kann der Motorsitz in offene, schützende, geschlossene und explosionssichere Typen unterteilt werden. Die äußere Oberfläche des geschlossenen und explosionsgeschützten Motorsockels hat normalerweise einen Kühlkörper, während die anderen Motorsockel keinen Kühlkörper haben. Je nach Vorhandensein oder Nichtvorhandensein von Füßen kann es in Motorbasen mit Füßen (wie B3 und B35) und ohne Füße (wie V1 und B5) unterteilt werden.
Technische Anforderungen an die Motorbasis verarbeitung
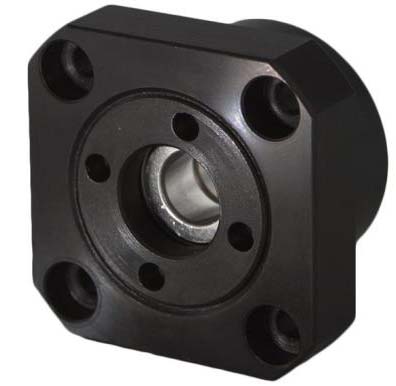
Die Teile, die von der Motorbasis bearbeitet werden sollen, umfassen hauptsächlich die Endanschläge, die Endflächen, den inneren Kreis, die Fußebene, das Bodenloch, die feste Endabdeckung, den Auslasskasten und die Bolzen zum Anheben. Für den Trenntyp muss die Maschinenbasis auch die geteilte Oberfläche, das Schraubenloch und das Stiftloch bearbeiten. Die technischen Anforderungen, die bei der Bearbeitung der Basis erfüllt sein müssen, lassen sich wie folgt zusammenfassen.
● Die Maßhaltigkeit und Rauheit jedes Bearbeitungsteils muss den Zeichnungen entsprechen. Die Genauigkeits- und Rauheitsanforderungen der beiden Endanschläge und des inneren Kreises sind beide hoch, und die mittlere hohe Maßgenauigkeit ist ebenfalls genau.
● Die geometrischen Toleranzen jeder Bearbeitungsfläche müssen den Zeichnungen entsprechen. Die Koaxialität zwischen den beiden Enden des Anschlags und dem Innenkreis sowie der stirnseitige Kreissprung der beiden der Achslinie zugewandten Enden sind der Schlüssel für die Bearbeitung der Basis. Mit besonderem Schwerpunkt auf: Wenn die geometrische Toleranz nicht angegeben ist, müssen die Maximal- und Minimalwerte innerhalb der Maßtoleranz liegen; Die Fußebene sollte parallel zur Achse des Schafts sein.
● Der Abstand zwischen dem Fußloch und der Mittellinie der Basis sollte symmetrisch sein und die angegebenen Toleranzen einhalten.
● Nach der Bearbeitung der magnetischen Maschinenbasis sollte die Dicke jedes Teils des Jochs gleichmäßig sein. Die Pole der Pole sollten gleich sein und ihre Position muss den Zeichnungen entsprechen.
● Die geteilte Oberfläche des separaten Rahmens erfordert eine stabile Verbindung und eine zuverlässige Positionierung und kann im zusammengebauten Zustand die ursprünglichen Anforderungen erfüllen.
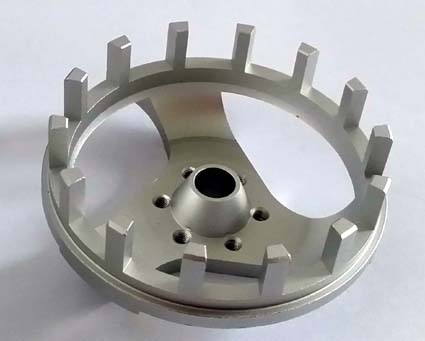
● Je nachdem, ob die Basis magnetisch ist oder nicht, kann sie in magnetische und nichtmagnetische magnetische Basen unterteilt werden. Der Magnetfuß wird für Gleichstrommotoren und Schwenksynchronmotoren verwendet. Nichtmagnetische Gehäuse werden in Asynchronmotoren, Rotationssynchronmotoren und anderen Motoren mit laminierten Statorkernen verwendet.
● Je nach den unterschiedlichen Zuschnitten des Sockels kann dieser in Schweiß- und Gusssockel unterteilt werden. Die Schweißbasis ist aus Stahl geschweißt. Die Gussbasis kann in Stahlguss, Gusseisen oder Aluminiumlegierung gegossen werden; Das magnetisch durchlässige Stativ ist fast immer mit Stahl oder Stahl verschweißt.
● Nichtmagnetische Motorgehäuse bestehen in der Regel aus Grauguss. Die Motorbasis aus Gusseisen ist kostengünstig und bequem zu verarbeiten und ihre mechanische Festigkeit kann die Anforderungen allgemeiner kleiner und mittlerer Motoren erfüllen. Hochfeste Gusseisen- oder Stahlguss-Motorsitze werden nur in Anwendungen verwendet, in denen eine hohe mechanische Festigkeit erforderlich ist, z. B. bei explosionsgeschützten Motoren und Schiffsmotoren.
● Kleine Wechselstrommotoren und Mikromotoren. In den letzten Jahren wurden Aluminium-Silizium-Legierungen oder Aluminium-Magnesium-Legierungen zum Druckgießen von Motorsitzen verwendet. Die Struktur ist dadurch gekennzeichnet, dass die Aluminiumlegierung direkt auf den Statorkern gegossen werden kann, der innere Kreis des Motorsitzes nicht bearbeitet werden muss, einige Befestigungselemente weggelassen werden und der kleine Motor leichter gemacht werden kann. Der Nachteil ist, dass der Materialpreis der Aluminiumlegierung relativ hoch ist, die mechanische Festigkeit schwach ist und die Verschleißfestigkeit schlecht ist.
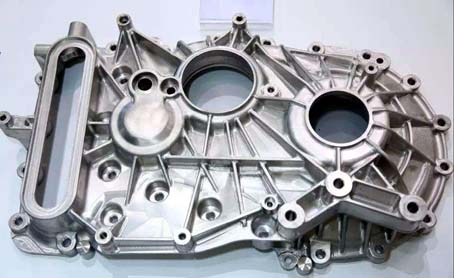
● Bei großen Motoren wurden aufgrund der geringen Leistung und des hohen Gewichts des Motors häufig geschweißte Sitze aus Profilstahl und Stahlblech verwendet. Im Vergleich zu Gusseisenständern ist das Gewicht des Schweißbodens bei gleicher mechanischer Festigkeit und struktureller Steifigkeit geringer. Beim Schweißen ist keine spezielle Form erforderlich und die Kosten sind relativ gering, der Produktionszyklus kann verkürzt werden und die individuelle Form des Motors kann erfüllt werden.
● Je nach Struktur der Basis kann diese in einen integralen Rahmen und einen separaten Rahmen unterteilt werden. Die strukturelle Steifigkeit des separaten Rahmens ist schwach und die Verarbeitungszeit ist länger. Wenn die Montage nicht korrekt ist, entspricht die gesamte Maschine nicht den Anforderungen. Die einzigartigen Vorteile liegen jedoch in der bequemen Installation und Wartung. Wenn das Design angemessen ist, sind die Montagegenauigkeit und die strukturelle Steifigkeit nicht länger die Einschränkungen.
Die integrale Motorbasis wird relativ häufig verwendet, und der Abschnitt ist im Allgemeinen zylindrisch gestaltet. Im unteren Teil der Motorbasis befinden sich zwei oder vier Fuß, und die Stromversorgung ist installiert. Die zylindrische Motorbasis weist die beste Verarbeitbarkeit auf. Wenn jedoch bei einigen Motoren die Außenabmessungen durch bestimmte Bedingungen begrenzt sind und die Leistung so hoch wie möglich sein muss, wird der Querschnitt der Motorbasis häufig als Polygon ausgeführt, um die räumliche Position voll auszunutzen. Polygonale Motorlager sind in der Herstellung komplexer und die Verarbeitungskosten sind ebenfalls erhöht.
● Andere Klassifizierungsmethoden.
● Andere Klassifizierungsmethoden.
Technische Anforderungen an die Motorbasis verarbeitung
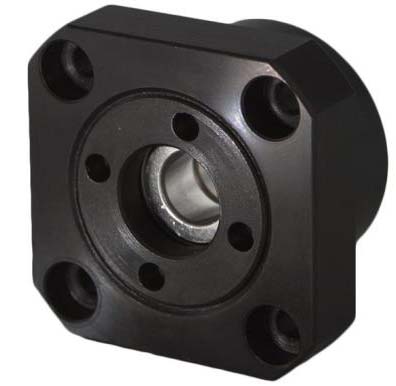
Die Teile, die von der Motorbasis bearbeitet werden sollen, umfassen hauptsächlich die Endanschläge, die Endflächen, den inneren Kreis, die Fußebene, das Bodenloch, die feste Endabdeckung, den Auslasskasten und die Bolzen zum Anheben. Für den Trenntyp muss die Maschinenbasis auch die geteilte Oberfläche, das Schraubenloch und das Stiftloch bearbeiten. Die technischen Anforderungen, die bei der Bearbeitung der Basis erfüllt sein müssen, lassen sich wie folgt zusammenfassen.
● Die Maßhaltigkeit und Rauheit jedes Bearbeitungsteils muss den Zeichnungen entsprechen. Die Genauigkeits- und Rauheitsanforderungen der beiden Endanschläge und des inneren Kreises sind beide hoch, und die mittlere hohe Maßgenauigkeit ist ebenfalls genau.
● Die geometrischen Toleranzen jeder Bearbeitungsfläche müssen den Zeichnungen entsprechen. Die Koaxialität zwischen den beiden Enden des Anschlags und dem Innenkreis sowie der stirnseitige Kreissprung der beiden der Achslinie zugewandten Enden sind der Schlüssel für die Bearbeitung der Basis. Mit besonderem Schwerpunkt auf: Wenn die geometrische Toleranz nicht angegeben ist, müssen die Maximal- und Minimalwerte innerhalb der Maßtoleranz liegen; Die Fußebene sollte parallel zur Achse des Schafts sein.
● Der Abstand zwischen dem Fußloch und der Mittellinie der Basis sollte symmetrisch sein und die angegebenen Toleranzen einhalten.
● Nach der Bearbeitung der magnetischen Maschinenbasis sollte die Dicke jedes Teils des Jochs gleichmäßig sein. Die Pole der Pole sollten gleich sein und ihre Position muss den Zeichnungen entsprechen.
● Die geteilte Oberfläche des separaten Rahmens erfordert eine stabile Verbindung und eine zuverlässige Positionierung und kann im zusammengebauten Zustand die ursprünglichen Anforderungen erfüllen.