Duennwandige grossem Durchmesser Titan teile Threading-Technologie
Schlüsselwörter: Titanlegierungsteile aus Ti-6Al-4V, Titanlegierungs-Verarbeitungstechnologie, Großes dünnwandiges Gewinde aus Titanlegierung mit großem Durchmesser, Titan-Gewindedrehen
Dünnwandige rohrförmige Teile aus Ti-6Al-4V-Titanlegierung sind in Abbildung 1 dargestellt: Das Teil hat einen Gewindedurchmesser von M320, eine Steigung von 4 mm, eine Wandstärke von nur 3 mm und ein Durchmesser-zu-Dicke-Verhältnis von 102. Außerdem müssen die Größe und die Konturgenauigkeit des Profils hoch sein, und der Gewindedurchmesser unterliegt Maßkontrollanforderungen. Ti-6Al-4V-Titanlegierung weist eine gute Plastizität und Zähigkeit sowie eine schlechte Wärmeleitfähigkeit auf. Dies ist ein schwer zu bearbeitendes Material, dessen dünnwandige Beschaffenheit es schwierig macht, die Verformung während der Verarbeitung zu kontrollieren.
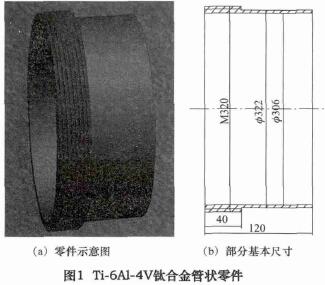
Titanlegierung Ti-6Al-4V rohrförmigen Teils Zeichnungen
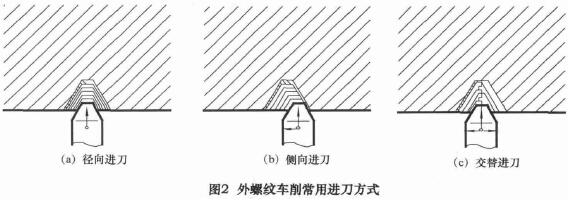
Abbildung 2: Gängige Zuführungsmethoden für Außengewinde aus Titanlegierungen
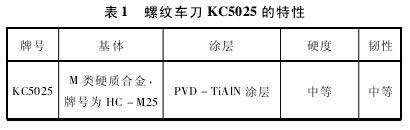
Tabelle 1. Wendemesser anschrauben Eigenschaften von KC5025
Die Menge des verzehrten Messers sollte schrittweise reduziert werden, und das Schruppen, Halbfertigstellen und Fertigstellen sollten schrittweise reduziert werden. Der Werkzeugverbrauch sollte schrittweise reduziert und beim Schruppen, Vorschlichten und Schlichten schrittweise reduziert werden. Da das Drehwerkzeug leicht zu tragen ist, muss es während des Gewindedrehvorgangs gemessen werden.
2, mechanische Analyse und Formgestaltung
The thin-walled tubular thread turning has a large cutting force and a different component force in each direction. The cutting force on-line detection system can detect the component forces in the three directions of X, Y and Z during the machining process. The schematic diagram is shown in Figure 3. Combined with finite element simulation, the force deformation of the tubular part is analyzed, and the clamping condition of the workpiece is improved by the optimized design of the tooling.
2. 1 mechanische Analyse des Gewindedrehens
Beim Schneiden mit dem Gewindedrehwerkzeug KC5025 beträgt die Schnitttiefe 0,3 mm und wird mehrfach verwendet. Beim Hochgeschwindigkeitsschneiden kann das Titanlegierungswerkstück aufgrund der Hitze des Schneidens einer stärkeren Oxidation unterliegen, und der Bearbeitungsprozess wird schwieriger, so dass die Schneidgeschwindigkeit weniger als 60 m / min beträgt. Eine Schnittkraftkomponente mit einer Schnitttiefe von 0,3 m und einer Schnittgeschwindigkeit von 20, 30, 40 und 50 m / min wurde unter Verwendung eines Dreiwege-Dynamometers Kistler 9257B erhalten, wie in Fig. 4 gezeigt.
Abbildung 4. Schnittkraftdiagramm Abbildung 4. Ergebnisse der Schnittkraftmessung
Wie aus 4 ersichtlich ist, erreichen F2 und F3 eine Spitzengeschwindigkeit von etwa 30 Metern pro Minute und F2 bleibt auf einem niedrigen Niveau von etwa 50 N. Wenn die Schnittgeschwindigkeit 30 m / min beträgt, betragen F2 und F3 822 N bzw. 1213 N. Während des Gewindedrehens schneidet F2 schwer.
Es kann gesagt werden, dass die radiale innere Abstützung der Werkstückbearbeitung unzureichend ist.
2. 2 Optimierung des Werkzeugdesigns
Durch mechanische Prüfung und Verformungsanalyse werden folgende Schlussfolgerungen gezogen: Das rohrförmige Werkstück weist eine große radiale Verformung auf und der innere Träger muss während der Bearbeitung verstärkt werden. Beim eigentlichen Drehvorgang beträgt die Verformung des Durchmessers eines Gewindeendes etwa 0,03 mm, was einen gewissen Verifikationseffekt auf diese Schlussfolgerung hat. Das optimierte Werkzeug ist in Abbildung 6 dargestellt. Die Öffnung der Montageplatte ist konisch und der Keilring und die Druckplatte wirken zusammen, um den Kontakt zwischen dem Werkstück und dem Keilring zu verbessern. Sie stellt sicher, dass die Radialkraft des Werkstücks während des Einfädelvorgangs gleichmäßig ist und dass das Werkstück an verschiedenen Umfangspositionen vom Keilring abgestützt wird.
Das Originalwerkzeug hat keine Keilringe und Druckplatten. Der Montageabschnitt ist zylindrisch und es besteht ein gewisser Spalt zwischen dem Werkstück und der Montageplatte während des Spannvorgangs, der Restspannung und Verformung verursacht.
Das Werkzeug von Fig. 6 löst das Problem der maschinellen Deformation gut, und die Durchmesserverformung eines Endes des Werkstückgewindes wird auf 0,01 mm verringert.
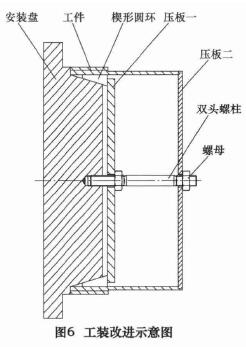
Abbildung 6. Werkzeugverbesserungen
3, Gewindedrehbearbeitungstest
3. 1 Werkzeugverschleißtest
Es wurden drei verschiedene Schnittgeschwindigkeiten (15 m / min, 25 m / min, 35 m / min) gewählt. Der gesamte Faden wurde gemäß dem ermittelten radialen Vorschub geschnitten und der Werkzeugverschleiß unter einem Rasterelektronenmikroskop beobachtet. Die Beziehung zwischen dem Grad des Werkzeugverschleißes und der im Test erhaltenen Schnittgeschwindigkeit ist in Fig. 7 gezeigt.
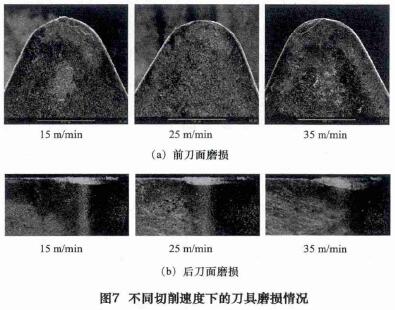
Bild 7 Werkzeugverschleiß bei unterschiedlichen Schnittgeschwindigkeiten
Aus den Testergebnissen ist ersichtlich, dass der Werkzeugverschleiß bei gleichen Werkzeugmaterialbedingungen mit zunehmender Schnittgeschwindigkeit rapide zunimmt. Wenn die Schnittgeschwindigkeit während der eigentlichen Bearbeitung des Gewindes 35 m / min beträgt, beträgt die Werkzeugstandzeit ungefähr eine Bearbeitungszeit des Werkstücks. Wenn die Schnittgeschwindigkeit leicht verringert wird, wird die Werkzeugstandzeit verbessert und die Oberflächenqualität des Gewindes wird verbessert. Für das Gewindedrehen von Ti-6Al-4V-Titanlegierungen ist eine Schnittgeschwindigkeit von 30 m / min besser geeignet.
3.2: Untersuchung der Spanform
Drehversuch mit Außengewinde aus Titanlegierung Ti-6Al-4V (M320 mm × 4 mm). Das Einfädeln erfolgt mit mehreren Fräsern. Die Schnittdicke beträgt 0,75 mm, 0,30 mm, 0,20 mm, 0,15 mm, 0,10 mm, 0,075 mm und dergleichen. Abbildung 9 zeigt die Form der Späne bei verschiedenen Werkzeugniveaus.
Es ist zu sehen, dass mit zunehmender Vorschubmenge die Schnittmenge abnimmt und die Verformung der Späne zuerst abnimmt und dann zunimmt. Wenn der Chip klein verformt wird, tritt außerdem eine große ungleichmäßige Verformung auf beiden Seiten des V-förmigen Chips auf.
Das Auswahlprinzip für das Gewindeschneiden rohrförmiger Werkstücke lautet daher wie folgt: Die Schruppwerkzeuggröße beträgt> 0,30 mm und die Schlichtwerkzeuggröße <0,15 mm.
Die Kombination der Gewindedrehparameter des rohrförmigen Werkstücks wird durch den Werkzeugverschleißtest und die Spanform bestimmt als: Die Endbearbeitungsgeschwindigkeit des Endbearbeitungswagens beträgt 30 m / min und das Schneidwerkzeug 0,10 mm, wodurch die Effizienz der Drehbearbeitung sichergestellt und die Oberflächenqualität der Gewindebearbeitung verbessert wird. Die Fertigdrehgeschwindigkeit beträgt 30 m / min und die Schnittstärke 0,10 mm, was die Dreheffizienz gewährleistet und die Oberflächenqualität der Gewindebearbeitung verbessert.
4, Fadenerkennungsmethode
Zur Messung von Drei-Stift, die drei von dem gleichen Durchmesser und der Größe der Nadel in einem geeigneten Mess jeweilige spiralförmige Nuten auf beiden Seiten eines Trapezgewindes angeordnet. Der Abstand zwischen den Scheitelpunkten der beiden Nadeln wird mit einem Mikrometer gemessen und der Fadendurchmesser d2 mit der Formel (2) umgerechnet. Der Nadeldurchmesser sollte nicht zu groß sein. Es ist darauf zu achten, dass der Querschnitt der Messnadel tangential zur Trapezgewindeseite verläuft. Ist der Durchmesser der Messnadel zu klein, sinkt die Messnadel in die Alveolen.
Für Trapezgewinde mit einem Gewindeprofilwinkel von 60 ° beträgt der optimale Wert für den Nadeldurchmesser d0 d0 = 0,577, P = 2,308 mm.
Nach dem Außengewinde ist das rohrförmige Werkstück fertig. Ein Mikrometer mit drei Nadeln plus Außendurchmesser und ein Mikrometer mit Fadendurchmesser werden verwendet, um den Durchmesser zu messen. Wiederholen Sie den Test mit einem hochpräzisen Koordinatenmessgerät. Die vier Sätze von Messergebnissen sind in Tabelle 2 gezeigt.
Thread-Checking-Experimente zeigen, dass: Der Fehler des mittleren Durchmessers, gemessen mit dem Mikrometer mit drei Nadeln plus Außendurchmesser, ist gering, und der Fehler der Größe des mittleren Durchmessers, direkt gemessen mit dem Mikrometer mit dem Fadendurchmesser, weist einen großen Fehler von 0,01 mm auf. Daher ist die Methode der Messung mit einem Drei-Nadel- und einem Außendurchmesser-Mikrometer sinnvoller.
5. Fazit
Durch die Untersuchung der Gewindeverarbeitungstechnologie mit großem Durchmesser für Titanlegierungen aus Ti-6Al-4V werden folgende Schlussfolgerungen gezogen:
(1) Ein beschichtetes spiralförmiges Schneidwerkzeug KC5025 mit der gleichen Härte und Zähigkeit wird verwendet und das Werkzeug wird durch radialen Vorschub zugeführt.
(2) Unter Verwendung des Analyseverfahrens der Schnittkrafterkennung und der Finite-Elemente-Simulation wird das Werkzeugdesign optimiert und die Durchmesserverformung während der Gewindebearbeitung von 0,03 mm auf 0,01 mm verringert.
(3) Die Schnittgeschwindigkeit beim Gewindedrehen beträgt 30 m / min, die Schruppmenge beträgt> 0,30 mm und die Endbearbeitungsmenge beträgt <0,15 mm.
(4) Bei der Fadendetektionsmethode ist die Genauigkeit der Drei-Nadel-Messung höher als die Genauigkeit der direkten Verwendung des Durchmessermikrometers.
Dünnwandige rohrförmige Teile aus Ti-6Al-4V-Titanlegierung sind in Abbildung 1 dargestellt: Das Teil hat einen Gewindedurchmesser von M320, eine Steigung von 4 mm, eine Wandstärke von nur 3 mm und ein Durchmesser-zu-Dicke-Verhältnis von 102. Außerdem müssen die Größe und die Konturgenauigkeit des Profils hoch sein, und der Gewindedurchmesser unterliegt Maßkontrollanforderungen. Ti-6Al-4V-Titanlegierung weist eine gute Plastizität und Zähigkeit sowie eine schlechte Wärmeleitfähigkeit auf. Dies ist ein schwer zu bearbeitendes Material, dessen dünnwandige Beschaffenheit es schwierig macht, die Verformung während der Verarbeitung zu kontrollieren.
Titanlegierung Großgewinde Verarbeitungstechnologie ist noch nicht ausgereift, aber der Preis ist relativ teuer, ist es notwendig, die Verarbeitungstechnologie zu optimieren, um die Produktionsdurchlaufrate zu gewährleisten. Für das Drehen dünnwandiger Rohrteile wird in diesem Artikel die konstruktive Optimierung von Werkzeugen unter dem Gesichtspunkt der mechanischen Analyse und Simulation vervollständigt. In Kombination mit dem Werkzeugverschleißtest und der Spanformstudie wird eine sinnvolle Kombination von Schneidparametern erhalten und die geeignete Erkennungsmethode in Kombination mit dem Ergebnis der Gewindedetektion ausgewählt.
1, die Wahl der Fütterungsmethode
Zum Drehen von Titanlegierungsteilen aus Ti-6Al-4V benötigt das Werkzeugmaterial aufgrund der guten Plastizität des Werkstückmaterials eine ausreichende Festigkeit und Zähigkeit. Der Gewindeschneidprozess verwendet den von Kenner hergestellten Gewindeschneider KC5025. Die Eigenschaften sind in Tabelle 1 aufgeführt.
1, die Wahl der Fütterungsmethode
Zum Drehen von Titanlegierungsteilen aus Ti-6Al-4V benötigt das Werkzeugmaterial aufgrund der guten Plastizität des Werkstückmaterials eine ausreichende Festigkeit und Zähigkeit. Der Gewindeschneidprozess verwendet den von Kenner hergestellten Gewindeschneider KC5025. Die Eigenschaften sind in Tabelle 1 aufgeführt.
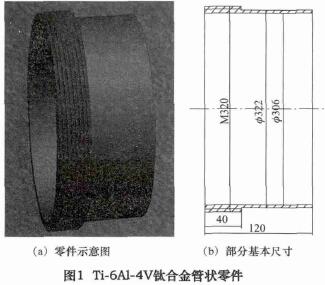
Titanlegierung Ti-6Al-4V rohrförmigen Teils Zeichnungen
Das Gewindedrehen ist eine Form des Drehens. Da das Gewindedrehwerkzeug in keilförmigem Kontakt mit dem rohrförmigen Werkstück steht, nimmt die Länge der am Schneiden beteiligten Schneidkante mit zunehmender Schnitttiefe stark zu. Die Hauptschneide und die Nebenschneide nehmen gleichzeitig am Schneiden teil, und die starke Plastizität des Werkstückmaterials erhöht den Reibungskoeffizienten, so dass der Drehzustand der Bearbeitung des Titanlegierungsrohraußengewindes relativ schlecht ist. Beim Drehen von Außengewinden werden normalerweise die folgenden drei Vorschubmodi verwendet (Abbildung 2):
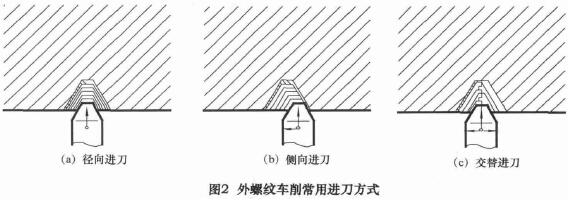
Abbildung 2: Gängige Zuführungsmethoden für Außengewinde aus Titanlegierungen
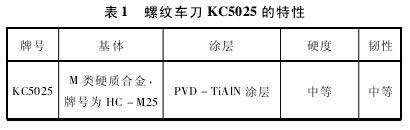
Tabelle 1. Wendemesser anschrauben Eigenschaften von KC5025
(1) Radialvorschub: Das Zuführungsverfahren ist einfach und es werden V-förmige Späne erzeugt, was die Steuerung schwierig macht.
(2) Die Seitliche füttern: Durch die einseitige Kantenbearbeitung verschleißt die Schneide und das Gewindeprofil wird ungenauer.
(3) Alternatives Futter: Die Werkzeugstandzeit kann durch abwechselndes Vorschieben an beiden Seiten des Gewindeprofils verbessert werden. Es ist zum Schneiden von Gewinden mit großer Steigung geeignet und erfordert eine spezielle Programmierung von CNC-Maschinen. Bei dem Schneidtest der Gewindebearbeitung mit großem Durchmesser wird ein radiales Vorschubverfahren angewendet.
Diese Methode wird am häufigsten zum Gewindedrehen verwendet und bietet folgende Vorteile: Die beidseitig der Gewindeschneidkante versetzte Axialschneidkraft kann die durch die Axialschneidkraft verursachte Abweichung beim Drehen teilweise überwinden und den Konturfehler des Gewindes verringern.
Die Nachteile sind: Die Schneidkanten auf beiden Seiten des Drehwerkzeugs sind gleichzeitig am Schneiden beteiligt, und die von beiden Seiten ausgegebenen Späne werden zusammengedrückt, und der Spanauswurf ist schwierig, und gleichzeitig sind die Leistung und die Wärme des Gewindedrehwerkzeugs ernst und die Schneidkante ist leicht zu tragen. Wenn die Menge des Messers groß ist, kann leicht ein "Perforationsmesser" -Phänomen erzeugt werden, das das Werkzeug sehr leicht beschädigt und die Qualität des Gewindes beeinträchtigt.(2) Die Seitliche füttern: Durch die einseitige Kantenbearbeitung verschleißt die Schneide und das Gewindeprofil wird ungenauer.
(3) Alternatives Futter: Die Werkzeugstandzeit kann durch abwechselndes Vorschieben an beiden Seiten des Gewindeprofils verbessert werden. Es ist zum Schneiden von Gewinden mit großer Steigung geeignet und erfordert eine spezielle Programmierung von CNC-Maschinen. Bei dem Schneidtest der Gewindebearbeitung mit großem Durchmesser wird ein radiales Vorschubverfahren angewendet.
Diese Methode wird am häufigsten zum Gewindedrehen verwendet und bietet folgende Vorteile: Die beidseitig der Gewindeschneidkante versetzte Axialschneidkraft kann die durch die Axialschneidkraft verursachte Abweichung beim Drehen teilweise überwinden und den Konturfehler des Gewindes verringern.
Die Menge des verzehrten Messers sollte schrittweise reduziert werden, und das Schruppen, Halbfertigstellen und Fertigstellen sollten schrittweise reduziert werden. Der Werkzeugverbrauch sollte schrittweise reduziert und beim Schruppen, Vorschlichten und Schlichten schrittweise reduziert werden. Da das Drehwerkzeug leicht zu tragen ist, muss es während des Gewindedrehvorgangs gemessen werden.
2, mechanische Analyse und Formgestaltung
The thin-walled tubular thread turning has a large cutting force and a different component force in each direction. The cutting force on-line detection system can detect the component forces in the three directions of X, Y and Z during the machining process. The schematic diagram is shown in Figure 3. Combined with finite element simulation, the force deformation of the tubular part is analyzed, and the clamping condition of the workpiece is improved by the optimized design of the tooling.
2. 1 mechanische Analyse des Gewindedrehens
Beim Schneiden mit dem Gewindedrehwerkzeug KC5025 beträgt die Schnitttiefe 0,3 mm und wird mehrfach verwendet. Beim Hochgeschwindigkeitsschneiden kann das Titanlegierungswerkstück aufgrund der Hitze des Schneidens einer stärkeren Oxidation unterliegen, und der Bearbeitungsprozess wird schwieriger, so dass die Schneidgeschwindigkeit weniger als 60 m / min beträgt. Eine Schnittkraftkomponente mit einer Schnitttiefe von 0,3 m und einer Schnittgeschwindigkeit von 20, 30, 40 und 50 m / min wurde unter Verwendung eines Dreiwege-Dynamometers Kistler 9257B erhalten, wie in Fig. 4 gezeigt.
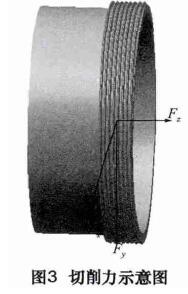
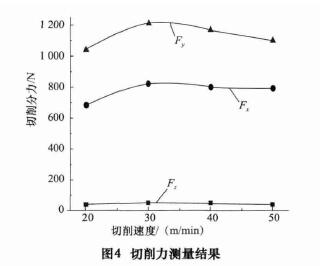
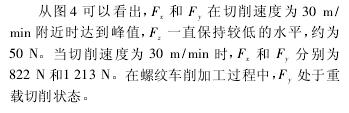
Wie aus 4 ersichtlich ist, erreichen F2 und F3 eine Spitzengeschwindigkeit von etwa 30 Metern pro Minute und F2 bleibt auf einem niedrigen Niveau von etwa 50 N. Wenn die Schnittgeschwindigkeit 30 m / min beträgt, betragen F2 und F3 822 N bzw. 1213 N. Während des Gewindedrehens schneidet F2 schwer.
Es kann gesagt werden, dass die radiale innere Abstützung der Werkstückbearbeitung unzureichend ist.
2. 2 Optimierung des Werkzeugdesigns
Durch mechanische Prüfung und Verformungsanalyse werden folgende Schlussfolgerungen gezogen: Das rohrförmige Werkstück weist eine große radiale Verformung auf und der innere Träger muss während der Bearbeitung verstärkt werden. Beim eigentlichen Drehvorgang beträgt die Verformung des Durchmessers eines Gewindeendes etwa 0,03 mm, was einen gewissen Verifikationseffekt auf diese Schlussfolgerung hat. Das optimierte Werkzeug ist in Abbildung 6 dargestellt. Die Öffnung der Montageplatte ist konisch und der Keilring und die Druckplatte wirken zusammen, um den Kontakt zwischen dem Werkstück und dem Keilring zu verbessern. Sie stellt sicher, dass die Radialkraft des Werkstücks während des Einfädelvorgangs gleichmäßig ist und dass das Werkstück an verschiedenen Umfangspositionen vom Keilring abgestützt wird.
Das Originalwerkzeug hat keine Keilringe und Druckplatten. Der Montageabschnitt ist zylindrisch und es besteht ein gewisser Spalt zwischen dem Werkstück und der Montageplatte während des Spannvorgangs, der Restspannung und Verformung verursacht.
Das Werkzeug von Fig. 6 löst das Problem der maschinellen Deformation gut, und die Durchmesserverformung eines Endes des Werkstückgewindes wird auf 0,01 mm verringert.
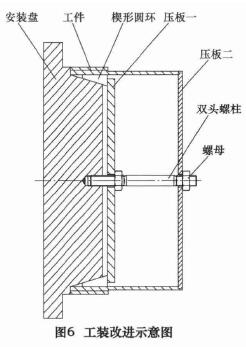
Abbildung 6. Werkzeugverbesserungen
3, Gewindedrehbearbeitungstest
3. 1 Werkzeugverschleißtest
Es wurden drei verschiedene Schnittgeschwindigkeiten (15 m / min, 25 m / min, 35 m / min) gewählt. Der gesamte Faden wurde gemäß dem ermittelten radialen Vorschub geschnitten und der Werkzeugverschleiß unter einem Rasterelektronenmikroskop beobachtet. Die Beziehung zwischen dem Grad des Werkzeugverschleißes und der im Test erhaltenen Schnittgeschwindigkeit ist in Fig. 7 gezeigt.
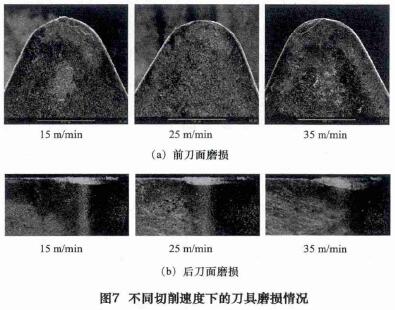
Bild 7 Werkzeugverschleiß bei unterschiedlichen Schnittgeschwindigkeiten
Aus den Testergebnissen ist ersichtlich, dass der Werkzeugverschleiß bei gleichen Werkzeugmaterialbedingungen mit zunehmender Schnittgeschwindigkeit rapide zunimmt. Wenn die Schnittgeschwindigkeit während der eigentlichen Bearbeitung des Gewindes 35 m / min beträgt, beträgt die Werkzeugstandzeit ungefähr eine Bearbeitungszeit des Werkstücks. Wenn die Schnittgeschwindigkeit leicht verringert wird, wird die Werkzeugstandzeit verbessert und die Oberflächenqualität des Gewindes wird verbessert. Für das Gewindedrehen von Ti-6Al-4V-Titanlegierungen ist eine Schnittgeschwindigkeit von 30 m / min besser geeignet.
3.2: Untersuchung der Spanform
Drehversuch mit Außengewinde aus Titanlegierung Ti-6Al-4V (M320 mm × 4 mm). Das Einfädeln erfolgt mit mehreren Fräsern. Die Schnittdicke beträgt 0,75 mm, 0,30 mm, 0,20 mm, 0,15 mm, 0,10 mm, 0,075 mm und dergleichen. Abbildung 9 zeigt die Form der Späne bei verschiedenen Werkzeugniveaus.
Das Auswahlprinzip für das Gewindeschneiden rohrförmiger Werkstücke lautet daher wie folgt: Die Schruppwerkzeuggröße beträgt> 0,30 mm und die Schlichtwerkzeuggröße <0,15 mm.
Die Kombination der Gewindedrehparameter des rohrförmigen Werkstücks wird durch den Werkzeugverschleißtest und die Spanform bestimmt als: Die Endbearbeitungsgeschwindigkeit des Endbearbeitungswagens beträgt 30 m / min und das Schneidwerkzeug 0,10 mm, wodurch die Effizienz der Drehbearbeitung sichergestellt und die Oberflächenqualität der Gewindebearbeitung verbessert wird. Die Fertigdrehgeschwindigkeit beträgt 30 m / min und die Schnittstärke 0,10 mm, was die Dreheffizienz gewährleistet und die Oberflächenqualität der Gewindebearbeitung verbessert.
4, Fadenerkennungsmethode
Zur Messung von Drei-Stift, die drei von dem gleichen Durchmesser und der Größe der Nadel in einem geeigneten Mess jeweilige spiralförmige Nuten auf beiden Seiten eines Trapezgewindes angeordnet. Der Abstand zwischen den Scheitelpunkten der beiden Nadeln wird mit einem Mikrometer gemessen und der Fadendurchmesser d2 mit der Formel (2) umgerechnet. Der Nadeldurchmesser sollte nicht zu groß sein. Es ist darauf zu achten, dass der Querschnitt der Messnadel tangential zur Trapezgewindeseite verläuft. Ist der Durchmesser der Messnadel zu klein, sinkt die Messnadel in die Alveolen.
Für Trapezgewinde mit einem Gewindeprofilwinkel von 60 ° beträgt der optimale Wert für den Nadeldurchmesser d0 d0 = 0,577, P = 2,308 mm.
Nach dem Außengewinde ist das rohrförmige Werkstück fertig. Ein Mikrometer mit drei Nadeln plus Außendurchmesser und ein Mikrometer mit Fadendurchmesser werden verwendet, um den Durchmesser zu messen. Wiederholen Sie den Test mit einem hochpräzisen Koordinatenmessgerät. Die vier Sätze von Messergebnissen sind in Tabelle 2 gezeigt.
Thread-Checking-Experimente zeigen, dass: Der Fehler des mittleren Durchmessers, gemessen mit dem Mikrometer mit drei Nadeln plus Außendurchmesser, ist gering, und der Fehler der Größe des mittleren Durchmessers, direkt gemessen mit dem Mikrometer mit dem Fadendurchmesser, weist einen großen Fehler von 0,01 mm auf. Daher ist die Methode der Messung mit einem Drei-Nadel- und einem Außendurchmesser-Mikrometer sinnvoller.
5. Fazit
Durch die Untersuchung der Gewindeverarbeitungstechnologie mit großem Durchmesser für Titanlegierungen aus Ti-6Al-4V werden folgende Schlussfolgerungen gezogen:
(1) Ein beschichtetes spiralförmiges Schneidwerkzeug KC5025 mit der gleichen Härte und Zähigkeit wird verwendet und das Werkzeug wird durch radialen Vorschub zugeführt.
(2) Unter Verwendung des Analyseverfahrens der Schnittkrafterkennung und der Finite-Elemente-Simulation wird das Werkzeugdesign optimiert und die Durchmesserverformung während der Gewindebearbeitung von 0,03 mm auf 0,01 mm verringert.
(3) Die Schnittgeschwindigkeit beim Gewindedrehen beträgt 30 m / min, die Schruppmenge beträgt> 0,30 mm und die Endbearbeitungsmenge beträgt <0,15 mm.
(4) Bei der Fadendetektionsmethode ist die Genauigkeit der Drei-Nadel-Messung höher als die Genauigkeit der direkten Verwendung des Durchmessermikrometers.