Tecnología compleja de procesamiento de carcasa de aleación de aluminio: fundición, soldadura y extrusión
En los vehículos eléctricos, el peso de la batería eléctrica representa aproximadamente el 30% de la masa total del vehículo. El peso liviano de los automóviles y la búsqueda inagotable de la densidad energética de los sistemas de baterías de potencia requieren el diseño liviano de la estructura del paquete de baterías. Dentro del sistema de batería, el gabinete como miembro estructural máximo, su peso reducido, la densidad de energía puede mejorarse, no se puede ignorar. Bajo la premisa de optimización estructural y re-optimización, el uso de nuevos materiales es la forma fundamental de reducir el peso de la caja de la batería. Sin mencionar el costo, el costo de lotes pequeños de nuevos productos es relativamente alto, lo cual es un problema que debe resolverse en el seguimiento, no una razón para evitar que las personas consideren la posibilidad de su aplicación.
Según la experiencia obtenida de todo el vehículo, se considera que se utiliza como un nuevo material para los sustitutos del acero en automóviles. Los materiales comunes son:
La aleación de aluminio, la aleación de magnesio, el material compuesto de fibra de carbono, el principal material de aleación de aluminio de la actualidad, es la tecnología relativamente madura entre los tres materiales. En la actualidad, una gran parte del cuerpo puede usar aluminio, como intercambiadores de calor, ruedas y cuerpo, la aleación de aluminio puede lograr un buen efecto de reducción de peso. Este documento organiza los principales tipos de aleaciones de aluminio, así como los principales métodos de procesamiento de las cajas de aleación de aluminio.
Tipo y rendimiento de aleación de aluminio.
El elemento de aluminio es el elemento metálico más abundante en la corteza terrestre, representando aproximadamente el 8.13%. El número atómico de aluminio es 13, el peso atómico es 27, el punto de fusión es 660 ° C y la densidad es 2.7 g / cm ^ 3. La densidad real de las piezas estructurales de aleación de aluminio varía según la tecnología de procesamiento y varía en un rango pequeño. La fundición a presión es de aproximadamente 2.6-2.63 g / cm ^ 3, la extrusión es de 2.68-2.7 g / cm ^ 3 y la forja es de 2.69-2.72 g / cm ^ 3.
Parámetros mecánicos típicos de chapa de aleación de aluminio encontrados en Internet, chapa de aluminio típica de la serie 6, resistencia a la tracción 310 MPa, límite elástico 276 MPa; Las propiedades mecánicas de la serie 5 son más bajas que la serie 6, y la serie 7 es más alta que la serie 6. Parámetros característicos comunes del acero Q235, resistencia a la tracción 375-500 MPa, límite elástico 235 MPa. Comparando acero y aluminio, resistencia a la tracción y límite elástico, el aluminio es ligeramente más bajo.
Tipo de aleación de aluminio
primero, Aplicación de fundición de aleación de aluminio.
Las aleaciones de aluminio fundido se usan ampliamente en la fabricación de automóviles y pueden proporcionar diferentes métodos de fundición de acuerdo con los diferentes requisitos de producción de automóviles. En el mercado original, las aleaciones de aluminio fundido se usaban principalmente para motores, cubos y vigas anticolisión. Caja de batería de aleación de aluminio fundido, el historial de uso también es relativamente largo. Sin embargo, los productos principales originales adoptan el método de fundición tradicional, la superficie de la caja es rugosa, la precisión es baja y la forma es simple, y el grosor de la pared del cuerpo de la caja no puede ser demasiado delgado.
segundo, aplicación de aleación de aluminio deformada.
En comparación con la aleación de aluminio fundido, la aleación de aluminio deformada tiene mayor ventaja de arbitrariedad y resistencia, y su contenido de aleación es relativamente bajo. Generalmente se usa en piezas de molduras automotrices, piezas estructurales, sistemas de disipación de calor y paneles de carrocería. La aleación de aluminio deformada consiste en una serie de láminas de aleación de aluminio, que tienen alta resistencia y buena soldabilidad, y se han utilizado para fabricar cajas y módulos de batería.
Tercero, la aplicación de compuestos de matriz de aluminio.
El tipo de material de aleación de aluminio que tiene una buena estabilidad dimensional, y tiene una densidad más baja, alta resistencia, en aplicaciones de producción automotriz capaces de producir antifatiga, resistencia a la fractura y otras ventajas.
Gran proceso de moldeo de cajas de aleación de aluminio, que incluye principalmente fundición y soldadura. Entre ellos, se puede realizar una fundición de precisión (o fundición de tamaño neto), es decir, la cavidad interna y la forma de la fundición a menudo requieren una formación única, para que su forma esté cerca de la forma final de la parte o parte, con menos procesamiento o sin procesamiento.
Hay tres tipos principales: fundición antigravedad, fundición de inversión y yeso.
3.1 Fundición
3. La fundición siempre ha sido el proceso principal para la producción en masa de cajas de aleación de aluminio. Cuando la fundición de tamaño neto ha sido ampliamente utilizada, la fundición es el evangelio del procesamiento de piezas de gran tamaño.
Fundición antigravedad
Un método de fundición en el que el líquido de aleación se llena y solidifica desde el fondo en la dirección opuesta a la gravedad por la presión aplicada. El proceso de fundición por gravedad tiene las características principales de llenado estable, velocidad de llenado controlable, distribución de temperatura razonable, solidificación bajo presión y propicio para la solidificación y alimentación de fundiciones. Las piezas fundidas antigravedad tienen buenas propiedades mecánicas, estructura compacta y pocos defectos de fundición.
Según diferentes procesos, la fundición antigravedad se divide en fundición a baja presión, fundición a presión diferencial y fundición reguladora de presión. Durante la Segunda Guerra Mundial, se inventó la tecnología de fundición a baja presión y se usó para fabricar piezas fundidas de bloques de motores refrigerados por aire de aviones; Sobre la base de la fundición a baja presión, se ha desarrollado un proceso de fundición a presión diferencial que combina la fundición a baja presión y la fundición en autoclave para la fabricación de piezas grandes, complejas y de paredes delgadas. El proceso de fundición de regulación de presión se desarrolló sobre la base de fundición a presión diferencial. La mayor diferencia entre la fundición reguladora de presión y la fundición de presión diferencial es que no solo puede realizar un control de presión positiva, sino también realizar un control de presión negativa. Al mismo tiempo, la precisión de control del sistema de control también es mayor.
Fundición de inversión de precisión
El casting de inversión tiene las siguientes ventajas:
Las fundiciones de inversión tienen una alta precisión dimensional y acabado superficial. La precisión dimensional generalmente es de hasta CT4-6 (la fundición en arena es CT10-13 y la fundición a presión es CT5-7); El diseño flexible permite la fundición de fundiciones altamente complejas; Producción limpia, sin aglutinante químico en la arena de moldeo, el material del molde es inofensivo para el medio ambiente a baja temperatura y la tasa de recuperación de la arena vieja es superior al 95%.
Explique "CT4-6", CT es el nivel de tolerancia dimensional de la fundición, cuanto mayor es el número seguido de menor precisión, es decir, mayor es el rango permitido de tamaño de fundición.
de fundición de yeso
El tipo de yeso se puede utilizar para hacer piezas de fundición con alta precisión dimensional y baja rugosidad superficial y baja tensión residual, que tiene muchas características que otras piezas de fundición no tienen: Puede replicar con precisión el patrón, la rugosidad de la superficie de la fundición de aleación de aluminio puede alcanzar 0.8 ~ 3.2μm; La conductividad térmica es baja, la parte de paredes delgadas es fácil de formar por completo y la más delgada se puede moldear en una pared delgada de 0.5 mm; Se pueden fabricar piezas fundidas con formas complejas.
Hay tres tipos principales de yeso de fundición:
Molde de yeso no espumante, molde de yeso espumante y molde de yeso de fundición de inversión. El tipo de yeso no espumado tiene una baja permeabilidad a los gases y utiliza principalmente fundición a baja presión para producir piezas fundidas con requisitos de rendimiento más bajos. El tipo de yeso espumado tiene una cierta permeabilidad a los gases y se puede utilizar para producir piezas de fundición de aleación de aluminio de pared delgada (la más delgada de 0,5 mm) con formas curvas.
En la actualidad, existen muchos métodos de soldadura para el aluminio y sus aleaciones. Sus métodos de soldadura generalmente incluyen soldadura TIG, soldadura MIG, soldadura láser, soldadura por costura, soldadura por resistencia, soldadura por haz de electrones, soldadura por fricción y soldadura por inducción. Los dos primeros tipos de soldadura son ampliamente utilizados: soldadura TIG y soldadura MIG.
Das Wolfram-Argon-Lichtbogenschweißen ist die häufigste Schweißmethode für Aluminiumprodukte. Besonders geeignet zum Schweißen von Aluminium und Aluminiumlegierungen mit einer Dicke von weniger als 5 mm, hauptsächlich aufgrund der Hitzekonzentration beim Schweißen. Der Lichtbogen ist bei der Verbrennung stabil, das Schweißgut ist dicht, die Formgebung ist gut, die Oberfläche ist hell, die Festigkeit und Plastizität der Schweißverbindung sind hoch und die Qualität ist gut; Die Erosion von Argongas in die Schweißzone beschleunigt die Abkühlung der Schweißverbindung und verbessert deren Struktur und Eigenschaften. Die Verbindungsform ist uneingeschränkt und für das Schweißen in allen Positionen geeignet. Diese Methode ist jedoch nicht für den Betrieb im Freien geeignet.
Compared with argon tungsten arc welding, TIG welding (MIG welding) in addition to the above characteristics. It also has high welding efficiency, easy to achieve automatic welding and semi-automatic welding, and is suitable for welding of various thicknesses of aluminum and its alloys. However, due to the limitation of wire feeding system, the wire diameter should not be too large, and the porosity sensitivity of the weld is relatively high.
La soldadura por arco de argón de tungsteno es el método de soldadura más común para productos de aluminio. Especialmente adecuado para soldar aluminio y aleaciones de aluminio con un espesor de menos de 5 mm, principalmente debido a la concentración de calor durante la soldadura. El arco es estable en la combustión, el metal de soldadura es denso, la formación es buena, la superficie es brillante, la resistencia y la plasticidad de la unión soldada son altas y la calidad es buena; La erosión del gas argón hacia la zona de soldadura acelera el enfriamiento de la unión soldada y mejora su estructura y propiedades. La forma de la unión no tiene restricciones y es adecuada para soldar en todas las posiciones. Pero este método no es adecuado para operar en un ambiente al aire libre.
El metal ligero y la aleación ligera tienen buenas propiedades de extrusión, especialmente adecuadas para el procesamiento de extrusión. Como el aluminio y las aleaciones de aluminio, se pueden procesar a través de una variedad de procesos de extrusión y una variedad de estructuras de moldes. La extrusión también tiene limitaciones obvias. Solo es adecuado para productos de igual sección, y la forma no puede ser demasiado complicada.
4 Los defectos en varias técnicas de procesamiento
4.1 Defectos propensos a ocurrir en la fundición
La fundición de inversión tiene las siguientes desventajas: las materias primas son caras y los costos de fundición son altos; El proceso es complicado, el proceso es largo, el ciclo de producción es largo y el rendimiento de fundición generalmente no es alto.
El yeso también tiene sus inconvenientes: El efecto de enfriamiento del molde de yeso es pobre. Cuando el grosor de la pared de las piezas de fundición varía mucho, los defectos como la porosidad de contracción y el orificio de contracción son fáciles de producir en la mayor parte del grosor. El tipo de yeso es extremadamente pobre en permeabilidad a los gases, y la fundición es propensa a defectos como sopletes y fogatas.
Implementado en los tipos específicos de defectos de fundición, la tendencia actual de consenso es esa. Al final de la solidificación, la contracción de solidificación producida por la fase líquida aislada entre las dendritas no se puede compensar efectivamente en la fase líquida, lo que resulta en defectos de fundición, poros y grietas térmicas.
La formación de huecos en la zona de pasta de solidificación de la aleación, con la formación de más fases sólidas, la concentración de gas en la fase líquida en el frente de solidificación alcanza gradualmente el estado de sobresaturación. Al mismo tiempo, debido a la acción capilar entre las dendritas, se reduce la caída de presión local en la región de alta fracción sólida. Cuando la presión parcial del gas sobresaturado en la fase líquida es mayor que la presión de formación de poros, los poros se adherirán a las dendritas, inclusiones o grietas en el molde y a la nucleación en las ranuras. Luego crece y finalmente forma un agujero.
La formación de craqueo térmico, el craqueo térmico es uno de los defectos de fundición más comunes en la producción. Las grietas externas a menudo ocurren en las esquinas, cambios repentinos en el grosor de la sección transversal, condensación local lenta y donde la tensión de tensión se mantiene durante la solidificación. Las grietas internas se producen en la parte de solidificación final de las piezas fundidas y, a menudo, ocurren cerca de los agujeros de contracción.
4.2 Dificultades de soldadura
El aluminio se oxida fácilmente.
El aluminio y sus aleaciones son altamente susceptibles a la oxidación durante el proceso de soldadura, formando una película de Al2O3 densa en la superficie del material. El punto de fusión de Al2O3 es tan alto como 2050 ° C, que es mucho más alto que el punto de fusión del aluminio y la aleación de aluminio (660 ° C de aluminio puro, 595 ° C de aleación de aluminio). Al2O3 es muy estable y difícil de eliminar, lo que dificulta la fusión del metal base durante el proceso de soldadura. Dado que el punto de fusión de la película de Al2O3 es casi tres veces mayor que el del aluminio y la aleación de aluminio, y la densidad es mucho mayor que la del aluminio y la aleación de aluminio, los defectos como la fusión y la inclusión se forman fácilmente durante el proceso de soldadura. Además, la película de óxido tiene buena hidrofilia, lo que hace que la soldadura genere poros durante la soldadura. Por lo tanto, para garantizar la calidad de la soldadura de aleación de aluminio, es necesario limpiar estrictamente la película de óxido en la superficie antes de soldar, y evitar que se vuelva a oxidar o eliminar su película de óxido recién formada durante el proceso de soldadura.
Alta conductividad térmica y gran capacidad calorífica específica.
La capacidad térmica específica y la conductividad térmica de las aleaciones de aluminio son mayores que las del acero. Al soldar, el calor del arco se difunde fácilmente a todos los lados. Por lo tanto, es necesario utilizar una fuente de calor con energía concentrada y aporte de calor. Para aleaciones de aluminio más gruesas, a veces es necesario precalentar la pieza de trabajo. La entrada de calor más alta a menudo forma un sobrecalentamiento, y si es un poco descuidado, es propenso a la deformación del cordón de soldadura, lo que hace que la pieza de trabajo se queme.
Gran coeficiente de expansión lineal y gran tendencia al craqueo térmico.
El aluminio y las aleaciones de aluminio tienen un coeficiente de expansión que es aproximadamente el doble que el del acero. La contracción del volumen en la solidificación es grande (hasta 6.5%, en comparación con 3.5% para el acero). La deformación y la tensión de la soldadura son grandes, y la contracción, el agrietamiento en caliente y la alta tensión interna se generan fácilmente durante la soldadura. En la producción, puede evitarse la aparición de grietas calientes ajustando la composición del alambre de soldadura, seleccionando parámetros razonables de proceso y secuencia de soldadura, y herramientas de soldadura adecuadas.
Sensible al hidrógeno
Los poros son fáciles de producir en la soldadura de aluminio. Dado que el aluminio líquido puede disolver una gran cantidad de hidrógeno, y el aluminio sólido apenas disuelve el hidrógeno, cuando la temperatura de la piscina fundida se enfría y solidifica rápidamente, el hidrógeno no se desborda y es fácil de aglomerar y formar poros en la soldadura. El elemento de hidrógeno en la soldadura proviene principalmente de la humedad en la atmósfera de la columna de arco, el material de soldadura y la humedad adsorbida por la película de óxido en la superficie del metal base; El aluminio tiene una gran conductividad térmica. En las mismas condiciones de proceso, la velocidad de enfriamiento de la zona de fusión de aluminio es 4-7 veces mayor que la del acero, lo que no conduce al escape de burbujas, que también es un factor importante en la formación de poros. En comparación con el acero, el aluminio produce 40 veces más burbujas de hidrógeno que el acero. Por lo tanto, la fuente de hidrógeno debe controlarse estrictamente para evitar la formación de poros; Al mismo tiempo, es necesario limpiar el material base y el alambre de soldadura antes de soldar.
No hay casos publicados de diseño de caja de aleación de aluminio. Disfrutemos por el momento de una carcasa de batería de aluminio fundido de BMW.
Según la experiencia obtenida de todo el vehículo, se considera que se utiliza como un nuevo material para los sustitutos del acero en automóviles. Los materiales comunes son:
La aleación de aluminio, la aleación de magnesio, el material compuesto de fibra de carbono, el principal material de aleación de aluminio de la actualidad, es la tecnología relativamente madura entre los tres materiales. En la actualidad, una gran parte del cuerpo puede usar aluminio, como intercambiadores de calor, ruedas y cuerpo, la aleación de aluminio puede lograr un buen efecto de reducción de peso. Este documento organiza los principales tipos de aleaciones de aluminio, así como los principales métodos de procesamiento de las cajas de aleación de aluminio.
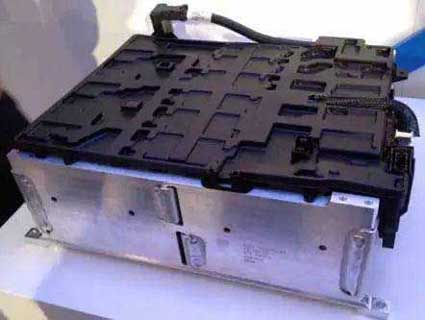
Tipo y rendimiento de aleación de aluminio.
El elemento de aluminio es el elemento metálico más abundante en la corteza terrestre, representando aproximadamente el 8.13%. El número atómico de aluminio es 13, el peso atómico es 27, el punto de fusión es 660 ° C y la densidad es 2.7 g / cm ^ 3. La densidad real de las piezas estructurales de aleación de aluminio varía según la tecnología de procesamiento y varía en un rango pequeño. La fundición a presión es de aproximadamente 2.6-2.63 g / cm ^ 3, la extrusión es de 2.68-2.7 g / cm ^ 3 y la forja es de 2.69-2.72 g / cm ^ 3.
Parámetros mecánicos típicos de chapa de aleación de aluminio encontrados en Internet, chapa de aluminio típica de la serie 6, resistencia a la tracción 310 MPa, límite elástico 276 MPa; Las propiedades mecánicas de la serie 5 son más bajas que la serie 6, y la serie 7 es más alta que la serie 6. Parámetros característicos comunes del acero Q235, resistencia a la tracción 375-500 MPa, límite elástico 235 MPa. Comparando acero y aluminio, resistencia a la tracción y límite elástico, el aluminio es ligeramente más bajo.
Tipo de aleación de aluminio
primero, Aplicación de fundición de aleación de aluminio.
Las aleaciones de aluminio fundido se usan ampliamente en la fabricación de automóviles y pueden proporcionar diferentes métodos de fundición de acuerdo con los diferentes requisitos de producción de automóviles. En el mercado original, las aleaciones de aluminio fundido se usaban principalmente para motores, cubos y vigas anticolisión. Caja de batería de aleación de aluminio fundido, el historial de uso también es relativamente largo. Sin embargo, los productos principales originales adoptan el método de fundición tradicional, la superficie de la caja es rugosa, la precisión es baja y la forma es simple, y el grosor de la pared del cuerpo de la caja no puede ser demasiado delgado.
segundo, aplicación de aleación de aluminio deformada.
En comparación con la aleación de aluminio fundido, la aleación de aluminio deformada tiene mayor ventaja de arbitrariedad y resistencia, y su contenido de aleación es relativamente bajo. Generalmente se usa en piezas de molduras automotrices, piezas estructurales, sistemas de disipación de calor y paneles de carrocería. La aleación de aluminio deformada consiste en una serie de láminas de aleación de aluminio, que tienen alta resistencia y buena soldabilidad, y se han utilizado para fabricar cajas y módulos de batería.
Tercero, la aplicación de compuestos de matriz de aluminio.
El tipo de material de aleación de aluminio que tiene una buena estabilidad dimensional, y tiene una densidad más baja, alta resistencia, en aplicaciones de producción automotriz capaces de producir antifatiga, resistencia a la fractura y otras ventajas.
Tecnología típica de procesamiento de cajas de aleación de aluminio
Gran proceso de moldeo de cajas de aleación de aluminio, que incluye principalmente fundición y soldadura. Entre ellos, se puede realizar una fundición de precisión (o fundición de tamaño neto), es decir, la cavidad interna y la forma de la fundición a menudo requieren una formación única, para que su forma esté cerca de la forma final de la parte o parte, con menos procesamiento o sin procesamiento.
Hay tres tipos principales: fundición antigravedad, fundición de inversión y yeso.
3.1 Fundición
3. La fundición siempre ha sido el proceso principal para la producción en masa de cajas de aleación de aluminio. Cuando la fundición de tamaño neto ha sido ampliamente utilizada, la fundición es el evangelio del procesamiento de piezas de gran tamaño.
Fundición antigravedad
Un método de fundición en el que el líquido de aleación se llena y solidifica desde el fondo en la dirección opuesta a la gravedad por la presión aplicada. El proceso de fundición por gravedad tiene las características principales de llenado estable, velocidad de llenado controlable, distribución de temperatura razonable, solidificación bajo presión y propicio para la solidificación y alimentación de fundiciones. Las piezas fundidas antigravedad tienen buenas propiedades mecánicas, estructura compacta y pocos defectos de fundición.
Según diferentes procesos, la fundición antigravedad se divide en fundición a baja presión, fundición a presión diferencial y fundición reguladora de presión. Durante la Segunda Guerra Mundial, se inventó la tecnología de fundición a baja presión y se usó para fabricar piezas fundidas de bloques de motores refrigerados por aire de aviones; Sobre la base de la fundición a baja presión, se ha desarrollado un proceso de fundición a presión diferencial que combina la fundición a baja presión y la fundición en autoclave para la fabricación de piezas grandes, complejas y de paredes delgadas. El proceso de fundición de regulación de presión se desarrolló sobre la base de fundición a presión diferencial. La mayor diferencia entre la fundición reguladora de presión y la fundición de presión diferencial es que no solo puede realizar un control de presión positiva, sino también realizar un control de presión negativa. Al mismo tiempo, la precisión de control del sistema de control también es mayor.
Fundición de inversión de precisión
El casting de inversión tiene las siguientes ventajas:
Las fundiciones de inversión tienen una alta precisión dimensional y acabado superficial. La precisión dimensional generalmente es de hasta CT4-6 (la fundición en arena es CT10-13 y la fundición a presión es CT5-7); El diseño flexible permite la fundición de fundiciones altamente complejas; Producción limpia, sin aglutinante químico en la arena de moldeo, el material del molde es inofensivo para el medio ambiente a baja temperatura y la tasa de recuperación de la arena vieja es superior al 95%.
Explique "CT4-6", CT es el nivel de tolerancia dimensional de la fundición, cuanto mayor es el número seguido de menor precisión, es decir, mayor es el rango permitido de tamaño de fundición.
de fundición de yeso
El tipo de yeso se puede utilizar para hacer piezas de fundición con alta precisión dimensional y baja rugosidad superficial y baja tensión residual, que tiene muchas características que otras piezas de fundición no tienen: Puede replicar con precisión el patrón, la rugosidad de la superficie de la fundición de aleación de aluminio puede alcanzar 0.8 ~ 3.2μm; La conductividad térmica es baja, la parte de paredes delgadas es fácil de formar por completo y la más delgada se puede moldear en una pared delgada de 0.5 mm; Se pueden fabricar piezas fundidas con formas complejas.
Hay tres tipos principales de yeso de fundición:
Molde de yeso no espumante, molde de yeso espumante y molde de yeso de fundición de inversión. El tipo de yeso no espumado tiene una baja permeabilidad a los gases y utiliza principalmente fundición a baja presión para producir piezas fundidas con requisitos de rendimiento más bajos. El tipo de yeso espumado tiene una cierta permeabilidad a los gases y se puede utilizar para producir piezas de fundición de aleación de aluminio de pared delgada (la más delgada de 0,5 mm) con formas curvas.
3.2 soldadura
En la actualidad, existen muchos métodos de soldadura para el aluminio y sus aleaciones. Sus métodos de soldadura generalmente incluyen soldadura TIG, soldadura MIG, soldadura láser, soldadura por costura, soldadura por resistencia, soldadura por haz de electrones, soldadura por fricción y soldadura por inducción. Los dos primeros tipos de soldadura son ampliamente utilizados: soldadura TIG y soldadura MIG.
Das Wolfram-Argon-Lichtbogenschweißen ist die häufigste Schweißmethode für Aluminiumprodukte. Besonders geeignet zum Schweißen von Aluminium und Aluminiumlegierungen mit einer Dicke von weniger als 5 mm, hauptsächlich aufgrund der Hitzekonzentration beim Schweißen. Der Lichtbogen ist bei der Verbrennung stabil, das Schweißgut ist dicht, die Formgebung ist gut, die Oberfläche ist hell, die Festigkeit und Plastizität der Schweißverbindung sind hoch und die Qualität ist gut; Die Erosion von Argongas in die Schweißzone beschleunigt die Abkühlung der Schweißverbindung und verbessert deren Struktur und Eigenschaften. Die Verbindungsform ist uneingeschränkt und für das Schweißen in allen Positionen geeignet. Diese Methode ist jedoch nicht für den Betrieb im Freien geeignet.
Compared with argon tungsten arc welding, TIG welding (MIG welding) in addition to the above characteristics. It also has high welding efficiency, easy to achieve automatic welding and semi-automatic welding, and is suitable for welding of various thicknesses of aluminum and its alloys. However, due to the limitation of wire feeding system, the wire diameter should not be too large, and the porosity sensitivity of the weld is relatively high.
3.3 Extrusion molding
Extrusion forming is to exert strong pressure on the metal blank placed in the die cavity (or extrusion cylinder). A plastic working method for forcing a metal blank to produce a directionally plastic deformation, which is extruded from a die hole of an extrusion die, thereby obtaining a part or a semi-finished product having a desired sectional shape and size and having a certain mechanical property. Extrusion moulding is usually used with other technological means in the process of battery case processing.La soldadura por arco de argón de tungsteno es el método de soldadura más común para productos de aluminio. Especialmente adecuado para soldar aluminio y aleaciones de aluminio con un espesor de menos de 5 mm, principalmente debido a la concentración de calor durante la soldadura. El arco es estable en la combustión, el metal de soldadura es denso, la formación es buena, la superficie es brillante, la resistencia y la plasticidad de la unión soldada son altas y la calidad es buena; La erosión del gas argón hacia la zona de soldadura acelera el enfriamiento de la unión soldada y mejora su estructura y propiedades. La forma de la unión no tiene restricciones y es adecuada para soldar en todas las posiciones. Pero este método no es adecuado para operar en un ambiente al aire libre.
El metal ligero y la aleación ligera tienen buenas propiedades de extrusión, especialmente adecuadas para el procesamiento de extrusión. Como el aluminio y las aleaciones de aluminio, se pueden procesar a través de una variedad de procesos de extrusión y una variedad de estructuras de moldes. La extrusión también tiene limitaciones obvias. Solo es adecuado para productos de igual sección, y la forma no puede ser demasiado complicada.
4 Los defectos en varias técnicas de procesamiento
La fundición de inversión tiene las siguientes desventajas: las materias primas son caras y los costos de fundición son altos; El proceso es complicado, el proceso es largo, el ciclo de producción es largo y el rendimiento de fundición generalmente no es alto.
El yeso también tiene sus inconvenientes: El efecto de enfriamiento del molde de yeso es pobre. Cuando el grosor de la pared de las piezas de fundición varía mucho, los defectos como la porosidad de contracción y el orificio de contracción son fáciles de producir en la mayor parte del grosor. El tipo de yeso es extremadamente pobre en permeabilidad a los gases, y la fundición es propensa a defectos como sopletes y fogatas.
Implementado en los tipos específicos de defectos de fundición, la tendencia actual de consenso es esa. Al final de la solidificación, la contracción de solidificación producida por la fase líquida aislada entre las dendritas no se puede compensar efectivamente en la fase líquida, lo que resulta en defectos de fundición, poros y grietas térmicas.
La formación de huecos en la zona de pasta de solidificación de la aleación, con la formación de más fases sólidas, la concentración de gas en la fase líquida en el frente de solidificación alcanza gradualmente el estado de sobresaturación. Al mismo tiempo, debido a la acción capilar entre las dendritas, se reduce la caída de presión local en la región de alta fracción sólida. Cuando la presión parcial del gas sobresaturado en la fase líquida es mayor que la presión de formación de poros, los poros se adherirán a las dendritas, inclusiones o grietas en el molde y a la nucleación en las ranuras. Luego crece y finalmente forma un agujero.
La formación de craqueo térmico, el craqueo térmico es uno de los defectos de fundición más comunes en la producción. Las grietas externas a menudo ocurren en las esquinas, cambios repentinos en el grosor de la sección transversal, condensación local lenta y donde la tensión de tensión se mantiene durante la solidificación. Las grietas internas se producen en la parte de solidificación final de las piezas fundidas y, a menudo, ocurren cerca de los agujeros de contracción.
4.2 Dificultades de soldadura
El aluminio se oxida fácilmente.
El aluminio y sus aleaciones son altamente susceptibles a la oxidación durante el proceso de soldadura, formando una película de Al2O3 densa en la superficie del material. El punto de fusión de Al2O3 es tan alto como 2050 ° C, que es mucho más alto que el punto de fusión del aluminio y la aleación de aluminio (660 ° C de aluminio puro, 595 ° C de aleación de aluminio). Al2O3 es muy estable y difícil de eliminar, lo que dificulta la fusión del metal base durante el proceso de soldadura. Dado que el punto de fusión de la película de Al2O3 es casi tres veces mayor que el del aluminio y la aleación de aluminio, y la densidad es mucho mayor que la del aluminio y la aleación de aluminio, los defectos como la fusión y la inclusión se forman fácilmente durante el proceso de soldadura. Además, la película de óxido tiene buena hidrofilia, lo que hace que la soldadura genere poros durante la soldadura. Por lo tanto, para garantizar la calidad de la soldadura de aleación de aluminio, es necesario limpiar estrictamente la película de óxido en la superficie antes de soldar, y evitar que se vuelva a oxidar o eliminar su película de óxido recién formada durante el proceso de soldadura.
Alta conductividad térmica y gran capacidad calorífica específica.
La capacidad térmica específica y la conductividad térmica de las aleaciones de aluminio son mayores que las del acero. Al soldar, el calor del arco se difunde fácilmente a todos los lados. Por lo tanto, es necesario utilizar una fuente de calor con energía concentrada y aporte de calor. Para aleaciones de aluminio más gruesas, a veces es necesario precalentar la pieza de trabajo. La entrada de calor más alta a menudo forma un sobrecalentamiento, y si es un poco descuidado, es propenso a la deformación del cordón de soldadura, lo que hace que la pieza de trabajo se queme.
Gran coeficiente de expansión lineal y gran tendencia al craqueo térmico.
El aluminio y las aleaciones de aluminio tienen un coeficiente de expansión que es aproximadamente el doble que el del acero. La contracción del volumen en la solidificación es grande (hasta 6.5%, en comparación con 3.5% para el acero). La deformación y la tensión de la soldadura son grandes, y la contracción, el agrietamiento en caliente y la alta tensión interna se generan fácilmente durante la soldadura. En la producción, puede evitarse la aparición de grietas calientes ajustando la composición del alambre de soldadura, seleccionando parámetros razonables de proceso y secuencia de soldadura, y herramientas de soldadura adecuadas.
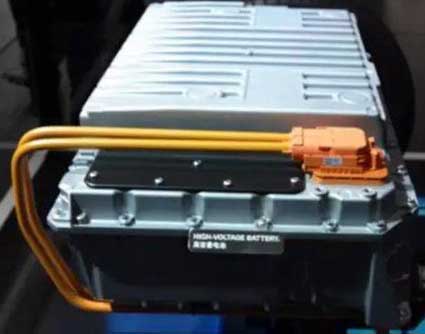
Sensible al hidrógeno
Los poros son fáciles de producir en la soldadura de aluminio. Dado que el aluminio líquido puede disolver una gran cantidad de hidrógeno, y el aluminio sólido apenas disuelve el hidrógeno, cuando la temperatura de la piscina fundida se enfría y solidifica rápidamente, el hidrógeno no se desborda y es fácil de aglomerar y formar poros en la soldadura. El elemento de hidrógeno en la soldadura proviene principalmente de la humedad en la atmósfera de la columna de arco, el material de soldadura y la humedad adsorbida por la película de óxido en la superficie del metal base; El aluminio tiene una gran conductividad térmica. En las mismas condiciones de proceso, la velocidad de enfriamiento de la zona de fusión de aluminio es 4-7 veces mayor que la del acero, lo que no conduce al escape de burbujas, que también es un factor importante en la formación de poros. En comparación con el acero, el aluminio produce 40 veces más burbujas de hidrógeno que el acero. Por lo tanto, la fuente de hidrógeno debe controlarse estrictamente para evitar la formación de poros; Al mismo tiempo, es necesario limpiar el material base y el alambre de soldadura antes de soldar.
No hay casos publicados de diseño de caja de aleación de aluminio. Disfrutemos por el momento de una carcasa de batería de aluminio fundido de BMW.