Comparación de diferentes tecnologías de producción y procesamiento de disipadores de calor
¿Qué es un disipador de calor?
Un disipador de calor es un dispositivo que disipa los componentes electrónicos propensos al calor en los aparatos eléctricos y está hecho principalmente de aleación de aluminio, latón o bronce en forma de placa, en forma de lámina o en varias láminas. Por ejemplo, el procesador central de la CPU en la computadora necesita usar un disipador de calor relativamente grande, y el tubo de alimentación, el tubo de línea en el televisor y el tubo del amplificador de potencia en el amplificador deben usar el disipador de calor. En general, el disipador de calor debe recubrirse con una capa de grasa térmica en la superficie de contacto entre los componentes electrónicos y el disipador de calor, de modo que el calor emitido por los componentes se conduzca de manera más efectiva al disipador de calor y luego se irradie al aire circundante a través del disipador de calor. En cuanto al material del disipador de calor, la conductividad térmica de cada material es diferente, y la conductividad térmica se organiza de mayor a menor, que son plata, cobre, aluminio y acero. Sin embargo, si se usa plata como disipador de calor, será demasiado costoso, por lo que la mejor solución es usar cobre. Aunque el aluminio es un disipador de calor mucho más barato, obviamente es menos conductivo térmicamente que el cobre (aproximadamente el 50% del cobre). En la actualidad, los materiales de disipador de calor comúnmente utilizados son el cobre y la aleación de aluminio, cada uno de los cuales tiene sus ventajas y desventajas. El cobre tiene buena conductividad térmica, pero es más costoso, difícil de procesar y tiene sobrepeso (muchos radiadores de cobre puro exceden el límite de peso de la CPU). Tiene una pequeña capacidad de calor y es propenso a la oxidación. El aluminio puro es demasiado blando para usarse directamente. Todas las aleaciones de aluminio utilizadas pueden proporcionar suficiente dureza. Las ventajas de las aleaciones de aluminio son su bajo precio y su peso ligero, pero la conductividad térmica es mucho peor que el cobre. Algunos radiadores tienen sus propias ventajas, y una placa de cobre está incrustada en la base del radiador de aleación de aluminio. Para usuarios comunes, el uso del disipador de calor de aluminio es suficiente para satisfacer las necesidades de disipación de calor. El radiador de calefacción del norte también se llama disipador de calor. El disipador de calor juega un papel importante en la composición del disipador de calor. Además del enfriamiento activo del ventilador, la evaluación de la calidad de un disipador de calor depende en gran medida de la capacidad del disipador de calor para absorber el calor y conducirlo.
Proceso básico de producción del disipador de calor:
Requisitos del producto --- Desarrollo del dibujo --- Fabricación de moldes --- Troquel de prueba (perfil de extrusión de aluminio) --- Corte y procesamiento CNC ) --- Entrada de producción --- Embalaje (inspección) --- Entrega.
1. Disipador de calor extruido de aluminio El material de aluminio se ha utilizado en el mercado de radiadores durante mucho tiempo debido a sus características de procesamiento suaves y fáciles. La tecnología de extrusión de aluminio es simplemente calentar los lingotes de aluminio a alta temperatura y luego dejar que el líquido de aluminio fluya a través del molde de extrusión con ranuras a alta presión para hacer las aletas radiantes. Sin embargo, después de cortar y ranurar las aletas originales del disipador de calor, se hacen los disipadores de calor comunes. El costo del disipador de calor de extrusión de aluminio es bajo y el umbral técnico no es alto. Sin embargo, debido a la limitación del material, la relación de espesor y longitud de las aletas de disipación de calor no puede exceder 1:18. Por lo tanto, es difícil aumentar el área de disipación de calor en un espacio limitado. Por lo tanto, el efecto de disipación de calor del disipador de calor extruido de aluminio es relativamente pobre, y es difícil competir con la CPU de alta frecuencia que está aumentando en la actualidad.
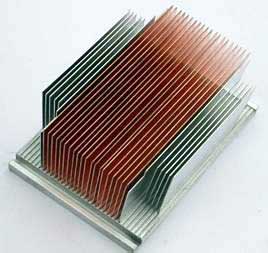
2. Enchufe los disipadores de calor de cobre Los principales materiales utilizados en los disipadores de calor principales del mercado son el aluminio y el cobre. El proceso de tapón de cobre es el producto de las ventajas combinadas de aluminio y cobre. El proceso del tapón de cobre se completa con el principio de expansión y contracción térmica. Después de calentar el disipador de calor extruido de aluminio, el núcleo de cobre se inserta en el mismo y luego se realiza el enfriamiento general. Debido a que no se utiliza dieléctrico de terceros, el proceso de taponamiento de cobre puede reducir en gran medida la resistencia térmica entre las superficies de contacto. No solo garantiza la estanqueidad de la unión cobre-aluminio, sino que también utiliza plenamente las características de la rápida disipación de calor del aluminio y la rápida absorción de calor del cobre. Este proceso de taponamiento de cobre tiene un costo moderado y un buen efecto de disipación de calor, y es el tipo principal de disipador de calor en el mercado.

3. El método de compactación es apilar una gran cantidad de láminas de cobre o aluminio, luego presionar en ambos lados y pulir la sección. Esta sección está en contacto con el núcleo de la CPU, y el otro lado se extiende para servir como aleta para el disipador de calor. El disipador de calor hecho por el método de compactación se caracteriza porque el número de aletas se puede hacer mucho. Y no requiere un proceso alto para garantizar que cada aleta pueda mantener un buen contacto (o cierre) con el núcleo de la CPU. Las aletas también tienen contacto cercano mediante compresión, y la pérdida de conducción de calor entre ellas se reducirá significativamente. Precisamente porque el disipador de calor hecho por el método de compactación tiene muchas aletas, el efecto de disipación de calor de este tipo de disipador de calor a menudo es bueno y el peso es mucho más liviano que el disipador de calor tradicional.
4. El proceso de forja del disipador de calor de forja se forma calentando el bloque de aluminio y llenando el molde con alta presión. Su ventaja es que la altura de la aleta puede alcanzar más de 50 mm y el grosor es inferior a 1 mm. Puede obtener el área de disipación de calor más grande en el mismo volumen, y es fácil obtener una buena precisión dimensional y un acabado superficial en la forja. Sin embargo, debido a la baja plasticidad del metal durante la forja, es fácil que se produzcan grietas durante la deformación, y la resistencia a la deformación es grande, lo que requiere maquinaria de forja de gran tonelaje (más de 500 toneladas). También es debido al alto costo del equipo y los moldes que el costo del producto es extremadamente alto, e incluso muchos entusiastas del overclocking no pueden permitírselo.
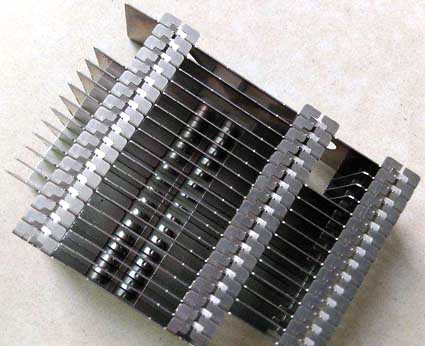
5. Disipadores de calor de tipo unión Debido a que los disipadores de calor de extrusión de aluminio tradicionales no pueden romper el límite del grosor y la longitud de las aletas, son disipadores de calor combinados. Este tipo de disipador de calor está hecho primero de aluminio o placa de cobre, y luego se combina en un disipador de calor con ranuras utilizando pasta o soldadura termoconductora. Las características del disipador térmico combinado son que las aletas rompen el límite proporcional original, y el efecto de disipación de calor es bueno, y se pueden usar diferentes materiales como aletas. Por supuesto, las deficiencias también son obvias, es decir, el uso de pasta térmica y soldadura para conectar las aletas y la base tendrá un problema de impedancia de interfaz. Esto afecta la disipación del calor. Para mejorar estas deficiencias, se han utilizado dos nuevas tecnologías en el campo de los disipadores de calor. La primera es la tecnología de conformación de engranajes: utiliza una presión de más de 60 toneladas para combinar la lámina de aluminio en la base de la lámina de cobre, y no se utiliza ningún medio entre el aluminio y el cobre. Desde una perspectiva microscópica, los átomos de aluminio y cobre están conectados entre sí en cierta medida, evitando por completo las desventajas de la resistencia térmica causadas por la combinación tradicional de cobre y aluminio y mejorando en gran medida la capacidad de transferencia de calor del producto. El segundo es la tecnología de soldadura por reflujo. El mayor problema del disipador de calor de unión tradicional es el problema de la impedancia de la interfaz, y la tecnología de soldadura por reflujo es una mejora en este problema. De hecho, el proceso de soldadura por reflujo es casi el mismo que el disipador de calor del tipo de unión tradicional, excepto que se utiliza un horno de reflujo especial, que puede establecer con precisión los parámetros de temperatura y tiempo de soldadura. La soldadura utiliza aleación de plomo-estaño para hacer que la soldadura y el metal entren en contacto por completo, evitando así la falta de soldadura y la soldadura vacía. Asegúrese de que la conexión entre la aleta y la base esté lo más cerca posible, minimice la resistencia térmica de la interfaz y controle el tiempo de fusión y la temperatura del cobre de cada junta de soldadura para garantizar la uniformidad de todas las juntas de soldadura. Sin embargo, este horno de reflujo especial es muy costoso. Los fabricantes de placas base usan más, pero los fabricantes de radiadores rara vez lo usan.
6. En comparación con las aletas extruidas de aluminio, el proceso de corte resuelve la limitación de la relación espesor-longitud de las aletas. El proceso de corte consiste en utilizar herramientas especiales para cortar todo el material en capas de aletas, que pueden ser tan delgadas como 0,5 mm. Además, las aletas del disipador de calor y la base están integradas, por lo que no hay problema de impedancia de interfaz. Sin embargo, el efecto de este proceso de corte en el proceso de producción es un alto desperdicio y una baja tasa de calidad, lo que hace que el costo sea alto, por lo que el proceso de corte está sesgado principalmente al disipador de calor de cobre.
Un disipador de calor es un dispositivo que disipa los componentes electrónicos propensos al calor en los aparatos eléctricos y está hecho principalmente de aleación de aluminio, latón o bronce en forma de placa, en forma de lámina o en varias láminas. Por ejemplo, el procesador central de la CPU en la computadora necesita usar un disipador de calor relativamente grande, y el tubo de alimentación, el tubo de línea en el televisor y el tubo del amplificador de potencia en el amplificador deben usar el disipador de calor. En general, el disipador de calor debe recubrirse con una capa de grasa térmica en la superficie de contacto entre los componentes electrónicos y el disipador de calor, de modo que el calor emitido por los componentes se conduzca de manera más efectiva al disipador de calor y luego se irradie al aire circundante a través del disipador de calor. En cuanto al material del disipador de calor, la conductividad térmica de cada material es diferente, y la conductividad térmica se organiza de mayor a menor, que son plata, cobre, aluminio y acero. Sin embargo, si se usa plata como disipador de calor, será demasiado costoso, por lo que la mejor solución es usar cobre. Aunque el aluminio es un disipador de calor mucho más barato, obviamente es menos conductivo térmicamente que el cobre (aproximadamente el 50% del cobre). En la actualidad, los materiales de disipador de calor comúnmente utilizados son el cobre y la aleación de aluminio, cada uno de los cuales tiene sus ventajas y desventajas. El cobre tiene buena conductividad térmica, pero es más costoso, difícil de procesar y tiene sobrepeso (muchos radiadores de cobre puro exceden el límite de peso de la CPU). Tiene una pequeña capacidad de calor y es propenso a la oxidación. El aluminio puro es demasiado blando para usarse directamente. Todas las aleaciones de aluminio utilizadas pueden proporcionar suficiente dureza. Las ventajas de las aleaciones de aluminio son su bajo precio y su peso ligero, pero la conductividad térmica es mucho peor que el cobre. Algunos radiadores tienen sus propias ventajas, y una placa de cobre está incrustada en la base del radiador de aleación de aluminio. Para usuarios comunes, el uso del disipador de calor de aluminio es suficiente para satisfacer las necesidades de disipación de calor. El radiador de calefacción del norte también se llama disipador de calor. El disipador de calor juega un papel importante en la composición del disipador de calor. Además del enfriamiento activo del ventilador, la evaluación de la calidad de un disipador de calor depende en gran medida de la capacidad del disipador de calor para absorber el calor y conducirlo.
Proceso básico de producción del disipador de calor:
Requisitos del producto --- Desarrollo del dibujo --- Fabricación de moldes --- Troquel de prueba (perfil de extrusión de aluminio) --- Corte y procesamiento CNC ) --- Entrada de producción --- Embalaje (inspección) --- Entrega.
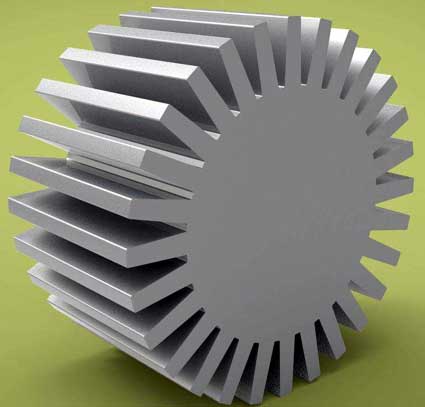
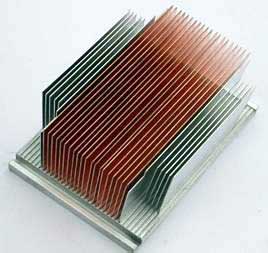
2. Enchufe los disipadores de calor de cobre Los principales materiales utilizados en los disipadores de calor principales del mercado son el aluminio y el cobre. El proceso de tapón de cobre es el producto de las ventajas combinadas de aluminio y cobre. El proceso del tapón de cobre se completa con el principio de expansión y contracción térmica. Después de calentar el disipador de calor extruido de aluminio, el núcleo de cobre se inserta en el mismo y luego se realiza el enfriamiento general. Debido a que no se utiliza dieléctrico de terceros, el proceso de taponamiento de cobre puede reducir en gran medida la resistencia térmica entre las superficies de contacto. No solo garantiza la estanqueidad de la unión cobre-aluminio, sino que también utiliza plenamente las características de la rápida disipación de calor del aluminio y la rápida absorción de calor del cobre. Este proceso de taponamiento de cobre tiene un costo moderado y un buen efecto de disipación de calor, y es el tipo principal de disipador de calor en el mercado.

3. El método de compactación es apilar una gran cantidad de láminas de cobre o aluminio, luego presionar en ambos lados y pulir la sección. Esta sección está en contacto con el núcleo de la CPU, y el otro lado se extiende para servir como aleta para el disipador de calor. El disipador de calor hecho por el método de compactación se caracteriza porque el número de aletas se puede hacer mucho. Y no requiere un proceso alto para garantizar que cada aleta pueda mantener un buen contacto (o cierre) con el núcleo de la CPU. Las aletas también tienen contacto cercano mediante compresión, y la pérdida de conducción de calor entre ellas se reducirá significativamente. Precisamente porque el disipador de calor hecho por el método de compactación tiene muchas aletas, el efecto de disipación de calor de este tipo de disipador de calor a menudo es bueno y el peso es mucho más liviano que el disipador de calor tradicional.
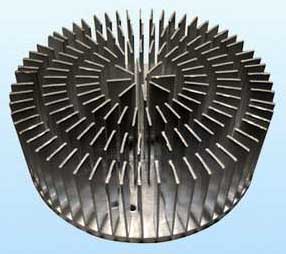
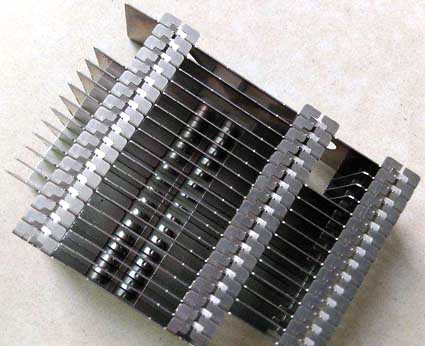
5. Disipadores de calor de tipo unión Debido a que los disipadores de calor de extrusión de aluminio tradicionales no pueden romper el límite del grosor y la longitud de las aletas, son disipadores de calor combinados. Este tipo de disipador de calor está hecho primero de aluminio o placa de cobre, y luego se combina en un disipador de calor con ranuras utilizando pasta o soldadura termoconductora. Las características del disipador térmico combinado son que las aletas rompen el límite proporcional original, y el efecto de disipación de calor es bueno, y se pueden usar diferentes materiales como aletas. Por supuesto, las deficiencias también son obvias, es decir, el uso de pasta térmica y soldadura para conectar las aletas y la base tendrá un problema de impedancia de interfaz. Esto afecta la disipación del calor. Para mejorar estas deficiencias, se han utilizado dos nuevas tecnologías en el campo de los disipadores de calor. La primera es la tecnología de conformación de engranajes: utiliza una presión de más de 60 toneladas para combinar la lámina de aluminio en la base de la lámina de cobre, y no se utiliza ningún medio entre el aluminio y el cobre. Desde una perspectiva microscópica, los átomos de aluminio y cobre están conectados entre sí en cierta medida, evitando por completo las desventajas de la resistencia térmica causadas por la combinación tradicional de cobre y aluminio y mejorando en gran medida la capacidad de transferencia de calor del producto. El segundo es la tecnología de soldadura por reflujo. El mayor problema del disipador de calor de unión tradicional es el problema de la impedancia de la interfaz, y la tecnología de soldadura por reflujo es una mejora en este problema. De hecho, el proceso de soldadura por reflujo es casi el mismo que el disipador de calor del tipo de unión tradicional, excepto que se utiliza un horno de reflujo especial, que puede establecer con precisión los parámetros de temperatura y tiempo de soldadura. La soldadura utiliza aleación de plomo-estaño para hacer que la soldadura y el metal entren en contacto por completo, evitando así la falta de soldadura y la soldadura vacía. Asegúrese de que la conexión entre la aleta y la base esté lo más cerca posible, minimice la resistencia térmica de la interfaz y controle el tiempo de fusión y la temperatura del cobre de cada junta de soldadura para garantizar la uniformidad de todas las juntas de soldadura. Sin embargo, este horno de reflujo especial es muy costoso. Los fabricantes de placas base usan más, pero los fabricantes de radiadores rara vez lo usan.
6. En comparación con las aletas extruidas de aluminio, el proceso de corte resuelve la limitación de la relación espesor-longitud de las aletas. El proceso de corte consiste en utilizar herramientas especiales para cortar todo el material en capas de aletas, que pueden ser tan delgadas como 0,5 mm. Además, las aletas del disipador de calor y la base están integradas, por lo que no hay problema de impedancia de interfaz. Sin embargo, el efecto de este proceso de corte en el proceso de producción es un alto desperdicio y una baja tasa de calidad, lo que hace que el costo sea alto, por lo que el proceso de corte está sesgado principalmente al disipador de calor de cobre.