Oil Storage Tank Anti-corrosion Coating Explanation
According to GB13348-92 "Liquid Safety Regulations for Liquid Petroleum Products". GB15599-95 "Safety Regulations for Lightning of Petroleum and Petroleum Facilities", requiring the use of static conductive coatings on the inner wall of crude oil tanks. GB6950-2001 "Technical Indicators of Electrostatic Conductive Coatings for Petroleum Tanks" requires detection according to standard GB/T16906-1997 "Resistivity Measurement Method of Electrostatic Conductive Coatings for Petroleum Tanks". The surface resistivity of the electrostatic storage coating for petroleum storage tanks should be 10 Ω < ps < 10 Ω.
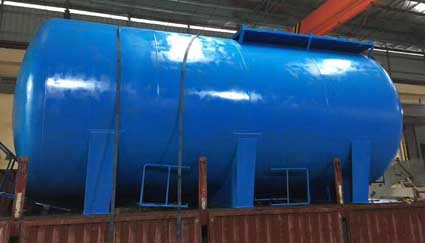
The conductive electrostatic coatings for the inner wall of the oil storage tank are classified according to the conductive medium, and the following are included:
Conductive medium |
Metal powder |
Conductive carbon black and graphite powder |
Conductive composite mica powder (metal oxide coating treatment) |
Performance characteristics |
1. The color is limited by the color of the metal powder. 2. Since the metal powder is easily oxidized, the conductive property of the coating film is lowered, and the inert metal is expensive. 3. If the metal powder whose electrode potential is higher than that of steel is used as conductive medium, electrochemical corrosion will be formed when it contacts directly with the steel substrate, which will accelerate the corrosion of steel as an anode. 4. A metal powder having a lower potential than steel (such as zinc powder) is used as a conductive medium, and the steel has cathodic protection and rust prevention. |
1. The color is limited and can only be made into dark paint. 2. Since the electrode potential is higher than that of the steel, when it is in direct contact with the steel, electrochemical corrosion is formed, and the steel is used as an anode to accelerate corrosion. 3. Because of its high oil absorption, when the conductivity requirement is high, the amount of addition is large, the paint film is loose, and the shielding property and the permeability resistance are decreased. Causes under-film corrosion and poor rust resistance. |
1. Light-colored, it can be made into conductive paints of various colors (limited colors such as gray, red, yellow, green, and blue). 2. The film has good compactness and is superior to the conductive electrostatic coating made of conductive carbon black and graphite powder. 3. The static electricity performance is durable and effective. 4. The price is more expensive. |
Our company's corresponding products |
ZIES213 inorganic zinc rich primer |
EPSP393-1 black epoxy oil resistant antistatic anticorrosive coating EPSP394-1 black epoxy phenolic oil tank coating PU414-1 black polyurethane oil resistant antistatic coating |
EPSP393-2 light epoxy oil resistant antistatic anticorrosive coating |
With the outer wall of anti-corrosion coatings
Considering that the crude oil tank is mostly in the marine atmosphere with strong corrosiveness by the sea, and the tank is used for a long period of time, the coating should have a long anti-corrosion period. Therefore, it is advisable to use a primer with good rust resistance, a good intermediate paint with good shielding, good gloss and color retention, good weather resistance, easy to apply and repair.
The performance characteristics of common coatings on the outer wall of the tank are as follows:
Position |
category |
Coating varieties |
Main performance characteristics |
Aboveground part |
Primer |
Epoxy zinc rich primer Or inorganic zinc-rich primer |
The paint film contains a large amount of zinc powder, has excellent rust prevention and cathodic protection, has excellent oil resistance, fast drying and good compatibility, and is commonly used as a primer in long-acting heavy-duty anti-corrosion systems. |
Intermediate paint |
Epoxy cloud iron intermediate paint |
The paint film contains a large amount of scaly micaceous iron oxide, forming a "fish scale"-like lap joint structure and a "maze" effect, thus having excellent barrier impermeability, effectively blocking the infiltration of corrosive medium and corroding the substrate. Good adhesion to zinc-rich primers and good adhesion to topcoats. |
|
Top coat |
Aliphatic overcoat polyurethane topcoat |
Excellent gloss and color retention performance, anti-powdering, no yellowing, good decorativeness, excellent oil and solvent resistance, good coatingability and unlimited coating time. |
|
Underground part |
Primer |
Epoxy zinc-rich primer or inorganic zinc-rich primer |
Same as above |
Top coat |
Epoxy asphalt mastic paint (summer or winter type with use) |
The paint film has excellent water resistance and rust resistance, good oil resistance and chemical resistance, good adhesion, impact resistance and wear resistance. At the same time, it has good cathodic protection performance, and the winter type can be used between -15-10 degrees. |