Machining of Stainless Steel Parts
- PRODUCT DETAIL
The CNC machining process of stainless steel refers to the process of turning, milling, and boring stainless steel to obtain the parts required by the drawings. In the process of machining stainless steel, a large number of machine tools, testing instruments and other equipment are needed.
The machined stainless steel materials are mostly SUS303, SUS304, SUS316, and duplex stainless steel. However, due to the high corrosion resistance and toughness of such materials, the problems of heat dissipation, work hardening, and chip sticking to the tool during cutting, make its machinability difficult.
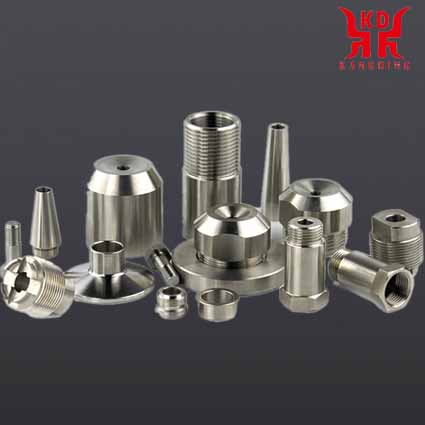
Severe machining hardening
Among stainless steels, the work hardening of austenitic and austenitic + ferritic stainless steels is the most prominent. For example, the strength σb of austenitic stainless steel after hardening reaches 1470~1960 MPa, and with the increase of σb, the yield limit σs increases; The annealed austenitic stainless steel σs does not exceed 30% to 45% of σb, and it reaches 85% to 95% after work hardening. The depth of the work hardened layer can reach 1/3 or more of the cutting depth; The hardness of the hardened layer is 1.4 to 2.2 times higher than the original. Because of the large plasticity of stainless steel, the character is distorted during plastic deformation, and the strengthening coefficient is very large; And the austenite is not stable enough, part of the austenite will be transformed into martensite under the action of turning stress; In addition, under the action of cutting heat, the compound impurities are easy to decompose into a dispersed distribution, so that a hardened layer is produced during turning. The work hardening caused by the previous feed or the previous process seriously affects the smooth progress of the subsequent processes.
High cutting force
Stainless steel has a large plastic deformation during the cutting process, especially austenitic stainless steel (its elongation is more than 1.5 times that of No. 45 steel), which increases the cutting force. At the same time, the work hardening of stainless steel is serious, and the thermal strength is high, which further increases the cutting resistance, and it is also difficult to curl and break the chips. Therefore, the cutting force for processing stainless steel is large. For example, the unit cutting force of turning 1Cr18Ni9Ti is 2450 MPa, which is 25% higher than that of No. 45 steel.
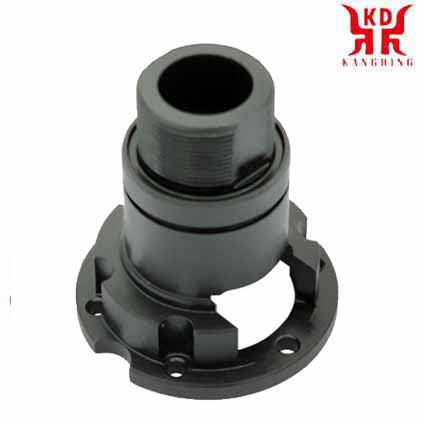
High cutting temperature
Plastic deformation and friction with the tool during cutting are both large, resulting in a lot of cutting heat; In addition, the thermal conductivity of stainless steel is about 1/2 to 1/4 of that of No. 45 steel. A large amount of cutting heat is concentrated on the interface between the cutting area and the tool-chip contact, and the heat dissipation conditions are poor. Under the same conditions, the cutting temperature of 1Cr18Ni9Ti is about 200°C higher than that of No. 45 steel.
Stainless steel chips are not easy to break
The plasticity and toughness of stainless steel are very large, and the chips are continuous during turning, which not only affects the smooth operation of the operation, but also scratches the processed surface. Under high temperature and high pressure, stainless steel has a strong affinity with other metals, and it is easy to produce adhesion phenomena and form built-up tumors, which not only aggravates tool wear, but also tears and deteriorates the processed surface. This feature of martensitic stainless steel with lower carbon content is more obvious.
Tool is easy to wear
The affinity effect in the process of cutting stainless steel makes the knife-chips bond and diffuse, so that the tool produces bonding wear and diffusion wear;
As a result, pits are formed on the rake face of the tool, and the cutting edge will also form tiny flaking and nicks;
In addition, the carbides in stainless steel (such as TiC) have a very high hardness. Direct contact with and friction with the tool during cutting, scratching of the tool, and work hardening will all increase the wear of the tool.
Large linear expansion coefficient
The coefficient of linear expansion of stainless steel is about 1.5 times that of carbon steel. Under the action of cutting temperature, the workpiece is prone to thermal deformation, and the dimensional accuracy is difficult to control
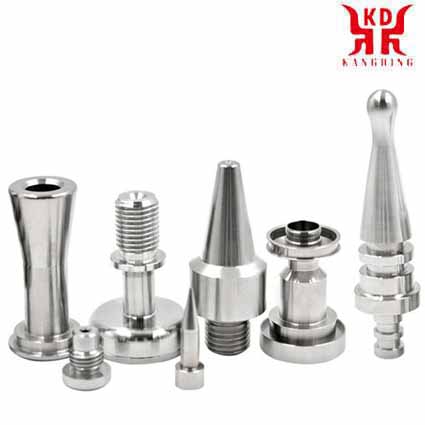
For these reasons, duplex stainless steels are more difficult to machine than 300 series austenitic stainless steels with the same corrosion resistance. Machining of duplex stainless steel generally requires greater cutting forces, and the tool wears faster. When using cemented carbide tools, the degree of difficulty in machining is the most obvious. Figure 16 shows a comparison of the relative machining performance indexes of several duplex stainless steels and 316 stainless steels. Note that compared with 316 stainless steel, duplex stainless steel S32101 has a higher machining difficulty level.
General principles of duplex stainless steel machining
The following machining principles apply to all stainless steels, and for duplex stainless steels, it is particularly important to follow these principles.
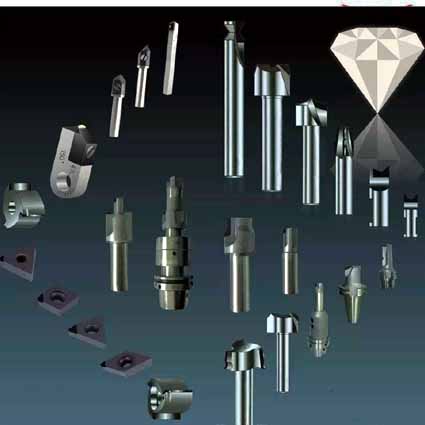
• Use high-power, sturdy equipment, the tool and the workpiece need to be firmly fixed (for the same cutting, the cutting force required for duplex stainless steel is much greater than that of the corresponding austenitic stainless steel);
• Keep the extended part of the tool as short as possible to minimize vibration;
• The tool nose radius is not greater than the necessary value;
• Choose hard knives with sharp shapes, which have both sharp edges and sufficient strength;
• Design the milling sequence of machining so that the depth of cut is always below the hardened layer formed by the first few passes;
• The cutting speed should be large enough, but not too fast, to avoid cutting edges and rapid wear;
• Regularly replace or re-grind the blade of the knife to ensure the sharpness of the blade;
• Use a large flow of coolant/lubricant, use cutting oil or emulsion with extreme pressure (EP) additives;
• Use carbide-coated blades with a chip groove shape.
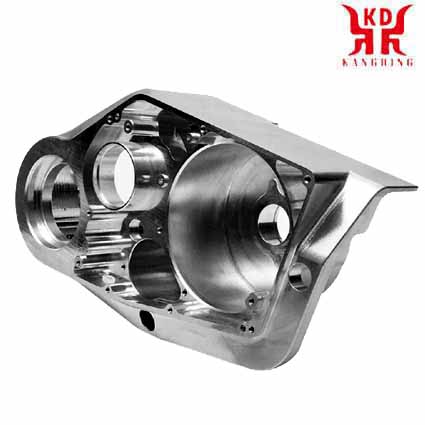
Stainless steel has strong adhesion and fusion, and chips are easy to adhere to the teeth of the milling cutter, which deteriorates the cutting conditions;
When up-milling, the cutter teeth slide on the hardened surface first, which increases the tendency of work hardening;
When milling, the impact and vibration are large, which makes the cutter teeth of the milling cutter easy to chip and wear.
The end mills for milling stainless steel can use cemented carbide as the material of the milling cutter teeth, and the other types of milling cutters are all made of high-speed steel. Especially tungsten-molybdenum series and high-vanadium high-speed steel have good results, and the tool durability can be increased by 1-2 times compared with W18Cr4V. Cemented carbide grades suitable for making stainless steel milling cutters are YG8, YW2, 813, 798, YS2T, YS30, YS25, etc.
When milling stainless steel, the cutting edge must be sharp and able to withstand impact, and the chip pocket must be large. Large helix angle milling cutters (cylindrical milling cutters, end milling cutters) can be used, the helix angle b is increased from 20° to 45° (gn=5°), and the tool durability can be increased by more than 2 times. Because the working rake angle g0e of the milling cutter is increased from 11° to more than 27° at this time, the milling is brisk. But the value of b should not be too large, especially for end mills with b≤35°, so as not to weaken the teeth.
Using wave-edge end mills to process stainless steel pipes or thin-walled workpieces, cutting is brisk, vibration is small, chips are fragile, and the workpiece is not deformed. High-speed milling of stainless steel with cemented carbide end mills and indexable end mills can achieve good results.
Milling 1Cr18Ni9Ti with a silver chip (SWC) end mill: Its geometric parameters are gf=5°, gp=15°, af=15°, ap=5°, kr=55°, k′r=35°, g01=-30°, bg=0.4mm, re=6mm ; When Vc=50-90m/min, Vf=630-750mm/min, a′p=2-6mm and the feed per tooth reaches 0.4-0.8mm; The milling force is reduced by 10%-15%, the milling power is reduced by 44%, and the efficiency is greatly improved. The principle is to grind a negative chamfer on the main cutting edge, and artificially generate a built-up edge during milling, so that it can replace the cutting edge for cutting. The front angle gb of the built-up tumor can reach 20~-302. Due to the effect of the entering angle, the built-up edge is subjected to a thrust parallel to the milling edge generated on a rake face and becomes a secondary chip flowing out, thereby taking away the cutting heat and reducing the milling temperature.
When milling stainless steel, down milling should be used as much as possible. The asymmetric down milling method can ensure that the cutting edge is smoothly cut away from the metal, the chip bonding contact area is small, and it is easy to be thrown off under the action of high-speed centrifugal force. In order to avoid chipping when the cutter tooth re-cuts into the workpiece, the chip impacts the rake face, which improves the durability of the cutter.
The spray cooling method has the most significant effect, which can increase the durability of the milling cutter by more than double; If the general 10% emulsion is used for cooling, the cutting fluid flow rate should be ensured to achieve sufficient cooling. When the carbide milling cutter mills stainless steel, take Vc=70-150m/min and Vf=37.5-150mm/min. At the same time, appropriate adjustments should be made according to the alloy grades and workpiece materials. The cutting amount of high-speed steel milling cutter is shown in Table 1
The machined stainless steel materials are mostly SUS303, SUS304, SUS316, and duplex stainless steel. However, due to the high corrosion resistance and toughness of such materials, the problems of heat dissipation, work hardening, and chip sticking to the tool during cutting, make its machinability difficult.
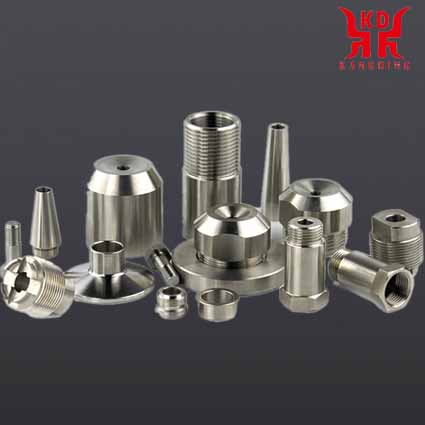
Main properties of stainless steel
The workability of stainless steel is much worse than that of medium carbon steel. Taking the machinability of ordinary No. 45 steel as 100%, the relative machinability of austenitic stainless steel 1Cr18Ni9Ti is 40%; Ferritic stainless steel 1Cr28 is 48%; Martensitic stainless steel 2Cr13 is 55%. Among them, austenitic and austenitic + ferritic stainless steels have the worst machinability.
Main features of machined stainless steel
Severe machining hardeningAmong stainless steels, the work hardening of austenitic and austenitic + ferritic stainless steels is the most prominent. For example, the strength σb of austenitic stainless steel after hardening reaches 1470~1960 MPa, and with the increase of σb, the yield limit σs increases; The annealed austenitic stainless steel σs does not exceed 30% to 45% of σb, and it reaches 85% to 95% after work hardening. The depth of the work hardened layer can reach 1/3 or more of the cutting depth; The hardness of the hardened layer is 1.4 to 2.2 times higher than the original. Because of the large plasticity of stainless steel, the character is distorted during plastic deformation, and the strengthening coefficient is very large; And the austenite is not stable enough, part of the austenite will be transformed into martensite under the action of turning stress; In addition, under the action of cutting heat, the compound impurities are easy to decompose into a dispersed distribution, so that a hardened layer is produced during turning. The work hardening caused by the previous feed or the previous process seriously affects the smooth progress of the subsequent processes.
High cutting force
Stainless steel has a large plastic deformation during the cutting process, especially austenitic stainless steel (its elongation is more than 1.5 times that of No. 45 steel), which increases the cutting force. At the same time, the work hardening of stainless steel is serious, and the thermal strength is high, which further increases the cutting resistance, and it is also difficult to curl and break the chips. Therefore, the cutting force for processing stainless steel is large. For example, the unit cutting force of turning 1Cr18Ni9Ti is 2450 MPa, which is 25% higher than that of No. 45 steel.
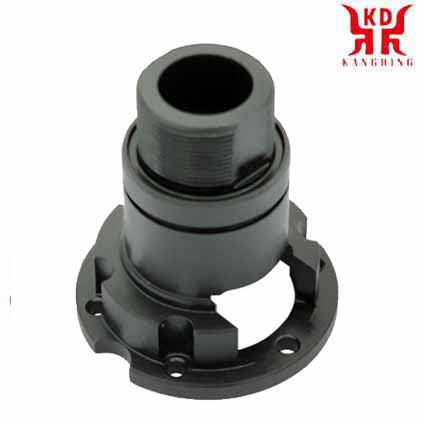
High cutting temperature
Plastic deformation and friction with the tool during cutting are both large, resulting in a lot of cutting heat; In addition, the thermal conductivity of stainless steel is about 1/2 to 1/4 of that of No. 45 steel. A large amount of cutting heat is concentrated on the interface between the cutting area and the tool-chip contact, and the heat dissipation conditions are poor. Under the same conditions, the cutting temperature of 1Cr18Ni9Ti is about 200°C higher than that of No. 45 steel.
Stainless steel chips are not easy to break
The plasticity and toughness of stainless steel are very large, and the chips are continuous during turning, which not only affects the smooth operation of the operation, but also scratches the processed surface. Under high temperature and high pressure, stainless steel has a strong affinity with other metals, and it is easy to produce adhesion phenomena and form built-up tumors, which not only aggravates tool wear, but also tears and deteriorates the processed surface. This feature of martensitic stainless steel with lower carbon content is more obvious.
Tool is easy to wear
The affinity effect in the process of cutting stainless steel makes the knife-chips bond and diffuse, so that the tool produces bonding wear and diffusion wear;
As a result, pits are formed on the rake face of the tool, and the cutting edge will also form tiny flaking and nicks;
In addition, the carbides in stainless steel (such as TiC) have a very high hardness. Direct contact with and friction with the tool during cutting, scratching of the tool, and work hardening will all increase the wear of the tool.
Large linear expansion coefficient
The coefficient of linear expansion of stainless steel is about 1.5 times that of carbon steel. Under the action of cutting temperature, the workpiece is prone to thermal deformation, and the dimensional accuracy is difficult to control
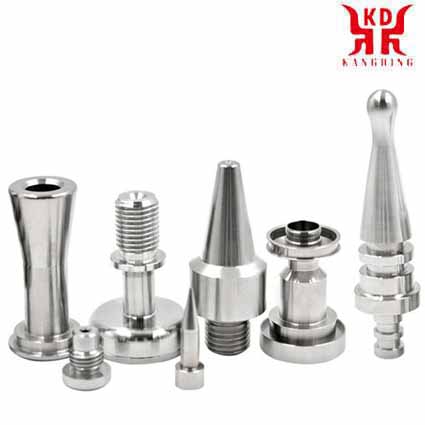
Machining of duplex stainless steel
The yield strength of duplex stainless steels is generally twice that of non-nitrogen alloyed austenitic stainless steels. Their initial work hardening rate is at least equivalent to that of common austenitic stainless steels. The cutting chips of duplex stainless steel are hard, which has a wear effect on the knife, especially the higher alloyed duplex stainless steel. Because the sulfur content in the production of duplex stainless steel is controlled as low as possible, it is not helpful for chip breaking.For these reasons, duplex stainless steels are more difficult to machine than 300 series austenitic stainless steels with the same corrosion resistance. Machining of duplex stainless steel generally requires greater cutting forces, and the tool wears faster. When using cemented carbide tools, the degree of difficulty in machining is the most obvious. Figure 16 shows a comparison of the relative machining performance indexes of several duplex stainless steels and 316 stainless steels. Note that compared with 316 stainless steel, duplex stainless steel S32101 has a higher machining difficulty level.
General principles of duplex stainless steel machining
The following machining principles apply to all stainless steels, and for duplex stainless steels, it is particularly important to follow these principles.
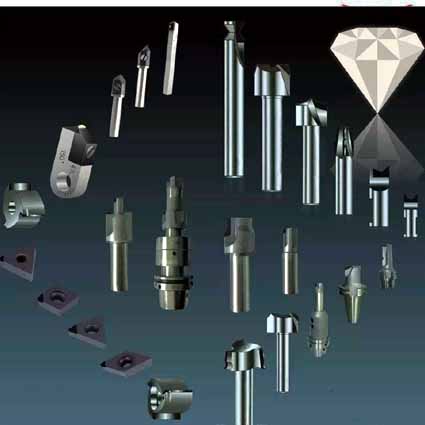
• Use high-power, sturdy equipment, the tool and the workpiece need to be firmly fixed (for the same cutting, the cutting force required for duplex stainless steel is much greater than that of the corresponding austenitic stainless steel);
• Keep the extended part of the tool as short as possible to minimize vibration;
• The tool nose radius is not greater than the necessary value;
• Choose hard knives with sharp shapes, which have both sharp edges and sufficient strength;
• Design the milling sequence of machining so that the depth of cut is always below the hardened layer formed by the first few passes;
• The cutting speed should be large enough, but not too fast, to avoid cutting edges and rapid wear;
• Regularly replace or re-grind the blade of the knife to ensure the sharpness of the blade;
• Use a large flow of coolant/lubricant, use cutting oil or emulsion with extreme pressure (EP) additives;
• Use carbide-coated blades with a chip groove shape.
Turning and face turning of stainless steel
Stainless steel turning and face turning operations involve many variables, so it is impossible to give specific recommendations that apply to all situations. Figure 17 and Table 12 give general guidelines for turning. Carbide tools can be used for turning operations, allowing the use of higher speeds than high-speed tool steels. However, more attention should be paid to the rigidity of the cemented carbide tool and the workpiece, and intermittent cutting should be avoided.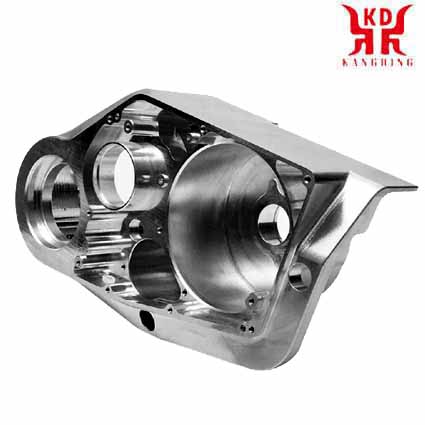
Milling of stainless steel
The characteristics of milling stainless steel are:Stainless steel has strong adhesion and fusion, and chips are easy to adhere to the teeth of the milling cutter, which deteriorates the cutting conditions;
When up-milling, the cutter teeth slide on the hardened surface first, which increases the tendency of work hardening;
When milling, the impact and vibration are large, which makes the cutter teeth of the milling cutter easy to chip and wear.
The end mills for milling stainless steel can use cemented carbide as the material of the milling cutter teeth, and the other types of milling cutters are all made of high-speed steel. Especially tungsten-molybdenum series and high-vanadium high-speed steel have good results, and the tool durability can be increased by 1-2 times compared with W18Cr4V. Cemented carbide grades suitable for making stainless steel milling cutters are YG8, YW2, 813, 798, YS2T, YS30, YS25, etc.
When milling stainless steel, the cutting edge must be sharp and able to withstand impact, and the chip pocket must be large. Large helix angle milling cutters (cylindrical milling cutters, end milling cutters) can be used, the helix angle b is increased from 20° to 45° (gn=5°), and the tool durability can be increased by more than 2 times. Because the working rake angle g0e of the milling cutter is increased from 11° to more than 27° at this time, the milling is brisk. But the value of b should not be too large, especially for end mills with b≤35°, so as not to weaken the teeth.
Using wave-edge end mills to process stainless steel pipes or thin-walled workpieces, cutting is brisk, vibration is small, chips are fragile, and the workpiece is not deformed. High-speed milling of stainless steel with cemented carbide end mills and indexable end mills can achieve good results.
Milling 1Cr18Ni9Ti with a silver chip (SWC) end mill: Its geometric parameters are gf=5°, gp=15°, af=15°, ap=5°, kr=55°, k′r=35°, g01=-30°, bg=0.4mm, re=6mm ; When Vc=50-90m/min, Vf=630-750mm/min, a′p=2-6mm and the feed per tooth reaches 0.4-0.8mm; The milling force is reduced by 10%-15%, the milling power is reduced by 44%, and the efficiency is greatly improved. The principle is to grind a negative chamfer on the main cutting edge, and artificially generate a built-up edge during milling, so that it can replace the cutting edge for cutting. The front angle gb of the built-up tumor can reach 20~-302. Due to the effect of the entering angle, the built-up edge is subjected to a thrust parallel to the milling edge generated on a rake face and becomes a secondary chip flowing out, thereby taking away the cutting heat and reducing the milling temperature.
When milling stainless steel, down milling should be used as much as possible. The asymmetric down milling method can ensure that the cutting edge is smoothly cut away from the metal, the chip bonding contact area is small, and it is easy to be thrown off under the action of high-speed centrifugal force. In order to avoid chipping when the cutter tooth re-cuts into the workpiece, the chip impacts the rake face, which improves the durability of the cutter.
The spray cooling method has the most significant effect, which can increase the durability of the milling cutter by more than double; If the general 10% emulsion is used for cooling, the cutting fluid flow rate should be ensured to achieve sufficient cooling. When the carbide milling cutter mills stainless steel, take Vc=70-150m/min and Vf=37.5-150mm/min. At the same time, appropriate adjustments should be made according to the alloy grades and workpiece materials. The cutting amount of high-speed steel milling cutter is shown in Table 1
Type of milling cutter |
Diameter of the milling cutter d0 (mm) |
Spindle speed n (r/min) |
Feed rate f (mm/min) |
Remark |
End mill | 3-4 | 1180-750 | Manual |
When the cutting width and cutting depth are small, the feed amount f takes a large value; otherwise, it takes a small value When milling 2Cr13 and other martensitic stainless steel, the amount of milling should be adjusted according to the actual hardness of the workpiece material When CNC milling nitric acid resistant stainless steel, the milling speed and feed rate should be appropriately reduced |
5-6 | 750-475 | |||
8-10 | 600-375 | |||
12-14 | 375-235 | 30-37.5 | ||
16-18 | 300-235 | 37.5-47.5 | ||
20-25 | 235-190 | 47.5-60 | ||
32-36 | 190-150 | 47.5-60 | ||
40-50 | 150-118 | 47.5-75 | ||
Wave edge end mill | 36 | 190-150 | 47.5-60 | |
40 | 150-118 | |||
50 | 118-95 | |||
60 | 95-75 | 60-75 | ||
Saw blade milling cutter and three-sided edge milling cutter | 75 | 235-150 | 23.5 or manual | |
110 | 150-75 | |||
150 | 95-60 | |||
200 | 75-37.5 |
PREV:Welding Rose Gold Stainless Steel Screen
NEXT:NONE
NEXT:NONE