Large Steel Tank Manufacturer
Main type 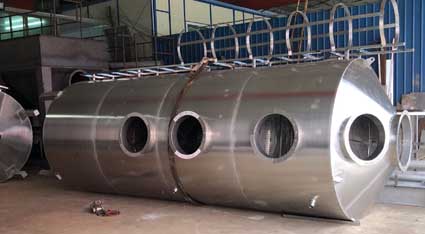
① Vertical cylindrical vault steel tank.
The capacity is generally below 10,000 cubic meters. Wallboard is connected by sleeve type (fillet weld). The inverted method is often used in construction (starting from the top of the tank, the tank wall is installed layer by layer from top to bottom, and the tank body is raised by fan air supply). Compared with the forward loading method (starting from the bottom ring plate of the tank wall and installing the tank wall layer by layer from bottom to top), the operation at high altitude is reduced.
② Vertical cylindrical floating roof steel tank.
It has a double-disc floating roof or a single-disc floating roof that can float up and down. The double-disc floating roof can reduce the influence of heat radiation, and therefore, the oil evaporation loss is small. However, in the case of a large capacity (greater than 10,000 cubic meters), in order to reduce the cost, a single-disc floating roof is generally used. Such oil tanks should pay attention to the selection of a reasonable sealing device, which requires good sealing effect and convenient installation and maintenance. The wall panels are welded by butt welding, and the construction is usually used. The wall panels are butt welded. Formal installation method is commonly used in construction.
③ vertical cylindrical inner floating roof steel tank.
It has both a vault and an inner floating roof. The inner floating roof floats on the liquid surface inside the vault tank and can float up and down. In addition to the characteristics of the floating roof tank, it also ensures the cleanliness of the oil.
④ spherical steel tanks.
It can withstand a working pressure of 0.45 to 3 MPa, and the capacity is generally 50 to 2000 m3), which is commonly used to store liquefied petroleum gas.
④ horizontal steel tanks.
The capacity is generally below 50 m3. It can store petrol and volatile petroleum products.
Calculation principle
① Vertical cylindrical steel tank.
The tank wall thickness t, in millimeters, should satisfy the following formula: where H is calculated: The vertical distance from the bottom edge of a tank wall to the top of the tank wall (when an overflow is provided, to the lower edge of the overflow), in meters;
D is the inner diameter of the tank, in meters;
[σ] is the allowable stress of the tank wall steel at the design temperature, in units of kg/mm 2 ;
γ is the storage bulk density, unit ton / m 3 , Gamma is the weld coefficient, take 0.9;
C0 is the allowable negative deviation of the thickness of the steel plate, in millimeters;
C is the corrosion margin, in millimeters.
The wind-resistant ring and the tank wall reinforcement ring on the wall of the floating roof tank shall be determined by calculation. The vault should first be checked for stability, ie the design external pressure of the vault is less than the allowable critical pressure of the vault. When constructing a tank in an earthquake-protected area, the tank wall must be subjected to seismic verification. When the volume is more than 50,000 m3, if the floating roof steel oil tank is used, the steel plate in the lower part of the tank wall is thicker than 40 mm, and it is not easy to be rolled into a circular arc shape, and the floating roof reinforced concrete oil tank can be used instead.
② Spherical steel tank.
The thickness of the spherical shell, the stability of the strut, the size of the base plate, the tie rods and their connections, and the joints between the strut and the spherical shell should be calculated.
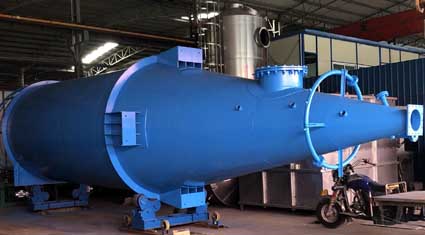
Steel tank foundation
Vertical tanks should be placed on the tar sand insulation to prevent corrosion of the tank floor. If the oil temperature is greater than 80 ° C, a thermal insulation layer should be added to the upper part of the insulation layer.
The lower part is a matt sand or gravel mixed material cushion surrounded by slopes or ring walls. A reinforced concrete ring wall foundation can be used when it is a weak foundation or is in a seismic zone or where the land is restricted. A reinforced concrete independent foundation or a toroidal foundation can be used under the pillars of the spherical oil tank.
Horizontal oil tanks are built on pier-wall foundation. The position and height of the tank body should enable the oil to flow by itself. Although the foundation of the steel tank is allowed to have a larger uniform settlement, in order to offset the settlement value, the foundation should be raised in advance. The uneven settlement of the foundation should be prevented to avoid the damage of the oil tank.
Quality inspection
Steel tank destruction is divided into two categories:
① brittle failure caused by welding residual stress;
② Destruction of foundation.
Therefore, the construction quality of steel tanks must be strictly tested. A reasonable welding sequence should be used during the welding process to control the welding deformation and conduct leak testing and flaw detection. The air tightness test should be carried out for floating roof silos. Vacuum leak test is used for welding seams of floating roof single plate and ship silo bottom plate.
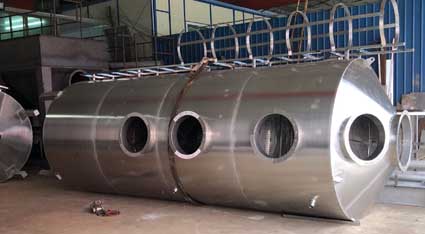
① Vertical cylindrical vault steel tank.
The capacity is generally below 10,000 cubic meters. Wallboard is connected by sleeve type (fillet weld). The inverted method is often used in construction (starting from the top of the tank, the tank wall is installed layer by layer from top to bottom, and the tank body is raised by fan air supply). Compared with the forward loading method (starting from the bottom ring plate of the tank wall and installing the tank wall layer by layer from bottom to top), the operation at high altitude is reduced.
② Vertical cylindrical floating roof steel tank.
It has a double-disc floating roof or a single-disc floating roof that can float up and down. The double-disc floating roof can reduce the influence of heat radiation, and therefore, the oil evaporation loss is small. However, in the case of a large capacity (greater than 10,000 cubic meters), in order to reduce the cost, a single-disc floating roof is generally used. Such oil tanks should pay attention to the selection of a reasonable sealing device, which requires good sealing effect and convenient installation and maintenance. The wall panels are welded by butt welding, and the construction is usually used. The wall panels are butt welded. Formal installation method is commonly used in construction.
③ vertical cylindrical inner floating roof steel tank.
It has both a vault and an inner floating roof. The inner floating roof floats on the liquid surface inside the vault tank and can float up and down. In addition to the characteristics of the floating roof tank, it also ensures the cleanliness of the oil.
④ spherical steel tanks.
It can withstand a working pressure of 0.45 to 3 MPa, and the capacity is generally 50 to 2000 m3), which is commonly used to store liquefied petroleum gas.
④ horizontal steel tanks.
The capacity is generally below 50 m3. It can store petrol and volatile petroleum products.
Calculation principle
① Vertical cylindrical steel tank.
The tank wall thickness t, in millimeters, should satisfy the following formula: where H is calculated: The vertical distance from the bottom edge of a tank wall to the top of the tank wall (when an overflow is provided, to the lower edge of the overflow), in meters;
D is the inner diameter of the tank, in meters;
[σ] is the allowable stress of the tank wall steel at the design temperature, in units of kg/mm 2 ;
γ is the storage bulk density, unit ton / m 3 , Gamma is the weld coefficient, take 0.9;
C0 is the allowable negative deviation of the thickness of the steel plate, in millimeters;
C is the corrosion margin, in millimeters.
The wind-resistant ring and the tank wall reinforcement ring on the wall of the floating roof tank shall be determined by calculation. The vault should first be checked for stability, ie the design external pressure of the vault is less than the allowable critical pressure of the vault. When constructing a tank in an earthquake-protected area, the tank wall must be subjected to seismic verification. When the volume is more than 50,000 m3, if the floating roof steel oil tank is used, the steel plate in the lower part of the tank wall is thicker than 40 mm, and it is not easy to be rolled into a circular arc shape, and the floating roof reinforced concrete oil tank can be used instead.
② Spherical steel tank.
The thickness of the spherical shell, the stability of the strut, the size of the base plate, the tie rods and their connections, and the joints between the strut and the spherical shell should be calculated.
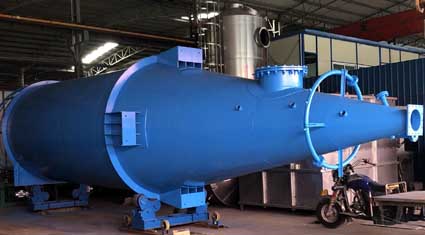
Steel tank foundation
Vertical tanks should be placed on the tar sand insulation to prevent corrosion of the tank floor. If the oil temperature is greater than 80 ° C, a thermal insulation layer should be added to the upper part of the insulation layer.
The lower part is a matt sand or gravel mixed material cushion surrounded by slopes or ring walls. A reinforced concrete ring wall foundation can be used when it is a weak foundation or is in a seismic zone or where the land is restricted. A reinforced concrete independent foundation or a toroidal foundation can be used under the pillars of the spherical oil tank.
Horizontal oil tanks are built on pier-wall foundation. The position and height of the tank body should enable the oil to flow by itself. Although the foundation of the steel tank is allowed to have a larger uniform settlement, in order to offset the settlement value, the foundation should be raised in advance. The uneven settlement of the foundation should be prevented to avoid the damage of the oil tank.
Quality inspection
Steel tank destruction is divided into two categories:
① brittle failure caused by welding residual stress;
② Destruction of foundation.
Therefore, the construction quality of steel tanks must be strictly tested. A reasonable welding sequence should be used during the welding process to control the welding deformation and conduct leak testing and flaw detection. The air tightness test should be carried out for floating roof silos. Vacuum leak test is used for welding seams of floating roof single plate and ship silo bottom plate.