Verfahren zum Drehen von Praezisionswalzen
Die Walze ist der Hauptteil des Walzwerks. Während des tatsächlichen Gebrauchs wird die Oberfläche aufgrund einer bestimmten Aufprallkraft von rotem Hochgeschwindigkeitsstahl mit hoher Temperatur abgerieben. Die Oberfläche muss eine gute Verschleißfestigkeit aufweisen und gleichzeitig eine ausreichende Zähigkeit aufweisen, um ein Brechen durch Aufprall zu verhindern.
In Anbetracht der besonderen Verwendung der Walze wird festgestellt, dass ihr Material Folgendes aufweisen muss:
1. hohe geschwindigkeit verschleißfestigkeit;
2, genug rote Härte;
3. Ausreichende Festigkeit und Zähigkeit.
Für den tatsächlichen Gebrauch ist ca. weißes Gusseisen besser geeignet. Da dieses Material jedoch im Allgemeinen im Gusszustand verwendet wird, sind unvermeidlich Gussfehler vorhanden, und die Härte kann 50 bis 60 HRC erreichen. Zusätzlich hat die Walze (wie in der Zeichnung gezeigt) höhere Koaxialitätsanforderungen, was das Drehen stark erschwert.
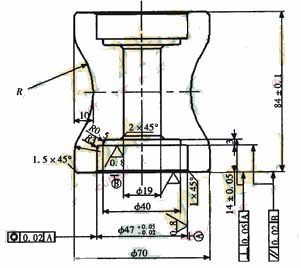
Zeichnen, Rollen
I. Angemessene Auswahl der Werkzeugsorte
Die Festigkeit und Härte des Walzenmaterials haben die Festigkeit und Härte des gewöhnlichen Hartmetallwerkzeugs (YT) erreicht, so dass das gewöhnliche Werkzeug nicht normal schneiden kann. Obwohl die Härte durch Abschrecken und Tempern angemessen verringert werden kann und der Schneidprozess erleichtert wird, sind die Kosten zu groß und der Zyklus ist lang, so dass die direkte Verarbeitung im Gusszustand ausgewählt wird.
Probebearbeitung und wiederholter Vergleich verschiedener Werkzeuge mit hoher Härte, einschließlich Keramikwerkzeugen und importierten Werkzeugen.
Schließlich wird das YS8-Drehwerkzeug mit Härte und Verschleißfestigkeit ausgewählt, das den Schneidanforderungen und dem relativ niedrigen Preis entspricht.
Selbstverständlich ist die Härte der Walze, die nach dem Gebrauch repariert werden muss, extrem hoch, da sie dem Kalthärten und Abschrecken im Prozess entspricht. Falls es nicht möglich ist, mit einem YS8-Werkzeug zu schneiden, verwenden wir eine Keramikklinge für die Reparaturbearbeitung.
II. Angemessene Wahl der Werkzeuggeometrie und der Schnittmenge
Da der Rohling beträchtliche Elemente wie Cr und Mo enthält, ist die Plastizität gut, die Festigkeit und Härte sind hoch, die Verformungsbeständigkeit ist groß und die Schneidkraft ist zwei- bis dreimal höher als die von gewöhnlichem Stahl. Die Schneidwärme steigt ebenfalls an, die Wärmeleitfähigkeit ist niedrig, die Wärmeableitung ist schwierig, die Schneidzonentemperatur ist extrem hoch und das Werkzeug kann leicht beschädigt werden. Außerdem ist der Rohling ein Gussteil, und es gibt Defekte wie harte Oberflächenhaut, Poren, Sandlöcher, ungleichmäßige Bearbeitungszugabe und ungleichmäßige Härte des Materials, was unvermeidlich zu einer Zunahme der Verarbeitungsinstabilität führt. Reduzierte Standzeit, erhöhte Produktionskosten und reduzierte Produktionseffizienz. Für diese Faktoren verbessern wir den Schneidprozess, indem wir die Schneidparameter angemessen auswählen.
1, grobe Verarbeitung
Beim Schruppen ist die Oberfläche der bearbeiteten Oberfläche nicht gleichmäßig und die Oberfläche des Rohlings weist eine harte Haut auf. Daher sollte die maximale Schnitttiefe gewählt werden. Je größer die Schnitttiefe, desto höher die erzeugte Schnittwärme und desto größer die Schnittkraft, der das Werkzeug standhalten kann. Damit das Werkzeug einer ausreichenden Druckspannung standhält, werden der negative Spanwinkel und der negative Spanwinkel (0 ° ~ -5 °) verwendet, um die Steifigkeit des Werkzeugs zu erhöhen.
Der Rückenwinkel liegt in der Regel zwischen 6 ° und 8 °, der Steigungswinkel zwischen 10 ° und 30 ° und die sekundäre Deklination zwischen 10 ° und 15 °. Aufgrund der hohen Härte des Rohlings und der schlechten Wärmeableitung wird beim Schruppen eine niedrige Geschwindigkeit (80 U / min) verwendet. Kleine Vorschubgeschwindigkeit (0,15 mm / r), um die Schnittkraft ordnungsgemäß zu reduzieren; Die Schnitttiefe wird zwischen 2 und 3 mm gewählt.
2, Fertig stellen
Da die Schnittiefe gering ist, ist die Schnittkraft gering und die Schnittwärme gering. Um die Oberflächenqualität zu verbessern, wird ein großer Spanwinkel angenommen, und der Rückwinkel nimmt einen großen Wert von 10 ° an. Minimieren Sie die Reibung und Extrusion des Werkzeugs und des Werkstücks, um die Oberflächenqualität des Werkstücks zu verbessern. Der Steigungswinkel liegt zwischen 10 ° und 30 °, die sekundäre Deklination zwischen 5 ° und 10 °. Um zu vermeiden, dass der Span herausfließt und die bearbeitete Oberfläche zerkratzt, wird der positive Blattneigungswinkel zwischen 0 ° und 5 ° angenommen; Verwenden Sie eine höhere Spindeldrehzahl (120 U / min). Geringe Schnitttiefe (0,2 bis 0,3 mm) und geringer Vorschub von 0,1 mm / r.
3, Arc Oberflächenbearbeitung
Wenn Sie den äußeren Kreis, das innere Loch und die Gesamtlänge drehen, ist es wirtschaftlicher, auf einer gewöhnlichen Drehmaschine zu arbeiten. Es ist jedoch nicht einfach, die kreisförmige Oberfläche auf einer gewöhnlichen Drehmaschine zu gewährleisten, so dass die Bogenoberfläche der Walze durch eine CNC-Drehmaschine vervollständigt wird. Bei ungleichmäßigen Rändern ist das Material hart. Erhöhen Sie beim Programmieren die Anzahl der Durchgänge und stellen Sie die niedrige Spindeldrehzahl und den kleinen Vorschub ein. Für den Fall, dass das Sandloch und das Luftloch leicht zum Abplatzen des Messers führen, wird der Programmstartpunkt jedes Mal vor dem Programmieren des Werkzeugs festgelegt. Das Vermeiden des Prozesses „von vorne anfangen“ nach jedem Messerbruch kann viel Zeit sparen und „unnötige Arbeit“ reduzieren, um die Produktionseffizienz zu steigern.
In Anbetracht der besonderen Verwendung der Walze wird festgestellt, dass ihr Material Folgendes aufweisen muss:
1. hohe geschwindigkeit verschleißfestigkeit;
2, genug rote Härte;
3. Ausreichende Festigkeit und Zähigkeit.
Für den tatsächlichen Gebrauch ist ca. weißes Gusseisen besser geeignet. Da dieses Material jedoch im Allgemeinen im Gusszustand verwendet wird, sind unvermeidlich Gussfehler vorhanden, und die Härte kann 50 bis 60 HRC erreichen. Zusätzlich hat die Walze (wie in der Zeichnung gezeigt) höhere Koaxialitätsanforderungen, was das Drehen stark erschwert.
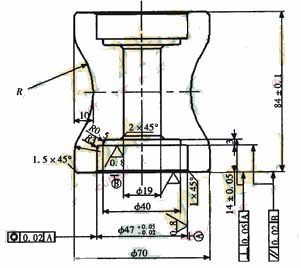
Zeichnen, Rollen
I. Angemessene Auswahl der Werkzeugsorte
Die Festigkeit und Härte des Walzenmaterials haben die Festigkeit und Härte des gewöhnlichen Hartmetallwerkzeugs (YT) erreicht, so dass das gewöhnliche Werkzeug nicht normal schneiden kann. Obwohl die Härte durch Abschrecken und Tempern angemessen verringert werden kann und der Schneidprozess erleichtert wird, sind die Kosten zu groß und der Zyklus ist lang, so dass die direkte Verarbeitung im Gusszustand ausgewählt wird.
Probebearbeitung und wiederholter Vergleich verschiedener Werkzeuge mit hoher Härte, einschließlich Keramikwerkzeugen und importierten Werkzeugen.
Schließlich wird das YS8-Drehwerkzeug mit Härte und Verschleißfestigkeit ausgewählt, das den Schneidanforderungen und dem relativ niedrigen Preis entspricht.
Selbstverständlich ist die Härte der Walze, die nach dem Gebrauch repariert werden muss, extrem hoch, da sie dem Kalthärten und Abschrecken im Prozess entspricht. Falls es nicht möglich ist, mit einem YS8-Werkzeug zu schneiden, verwenden wir eine Keramikklinge für die Reparaturbearbeitung.
II. Angemessene Wahl der Werkzeuggeometrie und der Schnittmenge
Da der Rohling beträchtliche Elemente wie Cr und Mo enthält, ist die Plastizität gut, die Festigkeit und Härte sind hoch, die Verformungsbeständigkeit ist groß und die Schneidkraft ist zwei- bis dreimal höher als die von gewöhnlichem Stahl. Die Schneidwärme steigt ebenfalls an, die Wärmeleitfähigkeit ist niedrig, die Wärmeableitung ist schwierig, die Schneidzonentemperatur ist extrem hoch und das Werkzeug kann leicht beschädigt werden. Außerdem ist der Rohling ein Gussteil, und es gibt Defekte wie harte Oberflächenhaut, Poren, Sandlöcher, ungleichmäßige Bearbeitungszugabe und ungleichmäßige Härte des Materials, was unvermeidlich zu einer Zunahme der Verarbeitungsinstabilität führt. Reduzierte Standzeit, erhöhte Produktionskosten und reduzierte Produktionseffizienz. Für diese Faktoren verbessern wir den Schneidprozess, indem wir die Schneidparameter angemessen auswählen.
1, grobe Verarbeitung
Beim Schruppen ist die Oberfläche der bearbeiteten Oberfläche nicht gleichmäßig und die Oberfläche des Rohlings weist eine harte Haut auf. Daher sollte die maximale Schnitttiefe gewählt werden. Je größer die Schnitttiefe, desto höher die erzeugte Schnittwärme und desto größer die Schnittkraft, der das Werkzeug standhalten kann. Damit das Werkzeug einer ausreichenden Druckspannung standhält, werden der negative Spanwinkel und der negative Spanwinkel (0 ° ~ -5 °) verwendet, um die Steifigkeit des Werkzeugs zu erhöhen.
Der Rückenwinkel liegt in der Regel zwischen 6 ° und 8 °, der Steigungswinkel zwischen 10 ° und 30 ° und die sekundäre Deklination zwischen 10 ° und 15 °. Aufgrund der hohen Härte des Rohlings und der schlechten Wärmeableitung wird beim Schruppen eine niedrige Geschwindigkeit (80 U / min) verwendet. Kleine Vorschubgeschwindigkeit (0,15 mm / r), um die Schnittkraft ordnungsgemäß zu reduzieren; Die Schnitttiefe wird zwischen 2 und 3 mm gewählt.
2, Fertig stellen
Da die Schnittiefe gering ist, ist die Schnittkraft gering und die Schnittwärme gering. Um die Oberflächenqualität zu verbessern, wird ein großer Spanwinkel angenommen, und der Rückwinkel nimmt einen großen Wert von 10 ° an. Minimieren Sie die Reibung und Extrusion des Werkzeugs und des Werkstücks, um die Oberflächenqualität des Werkstücks zu verbessern. Der Steigungswinkel liegt zwischen 10 ° und 30 °, die sekundäre Deklination zwischen 5 ° und 10 °. Um zu vermeiden, dass der Span herausfließt und die bearbeitete Oberfläche zerkratzt, wird der positive Blattneigungswinkel zwischen 0 ° und 5 ° angenommen; Verwenden Sie eine höhere Spindeldrehzahl (120 U / min). Geringe Schnitttiefe (0,2 bis 0,3 mm) und geringer Vorschub von 0,1 mm / r.
3, Arc Oberflächenbearbeitung
Wenn Sie den äußeren Kreis, das innere Loch und die Gesamtlänge drehen, ist es wirtschaftlicher, auf einer gewöhnlichen Drehmaschine zu arbeiten. Es ist jedoch nicht einfach, die kreisförmige Oberfläche auf einer gewöhnlichen Drehmaschine zu gewährleisten, so dass die Bogenoberfläche der Walze durch eine CNC-Drehmaschine vervollständigt wird. Bei ungleichmäßigen Rändern ist das Material hart. Erhöhen Sie beim Programmieren die Anzahl der Durchgänge und stellen Sie die niedrige Spindeldrehzahl und den kleinen Vorschub ein. Für den Fall, dass das Sandloch und das Luftloch leicht zum Abplatzen des Messers führen, wird der Programmstartpunkt jedes Mal vor dem Programmieren des Werkzeugs festgelegt. Das Vermeiden des Prozesses „von vorne anfangen“ nach jedem Messerbruch kann viel Zeit sparen und „unnötige Arbeit“ reduzieren, um die Produktionseffizienz zu steigern.