Schachtteile Process Plan Analysis
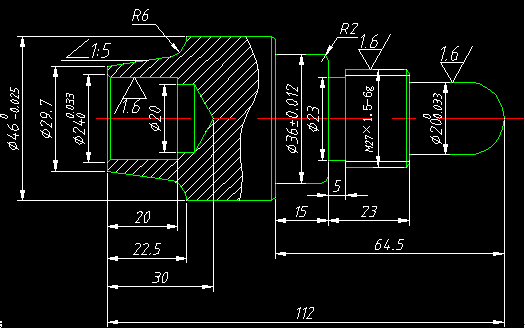
Figure 1-1
(2) Analyse von Teilezeichnungen
Die Oberfläche des Teils besteht aus einem Zylinder, einem geraden Bogen, einem umgekehrten Bogen, einem Kegel, einer Nut, einem Gewinde, einem Loch und dergleichen. Die Dimensionierung ist abgeschlossen. Der Rohling ist 45 # Stahl Φ50mm × 120mm. Wärmebehandlung: Modulationsbehandlung, HRC25-35 hat keine Härteanforderung.
(3) Bestimmen Sie die Verarbeitungsmethode:
Das Prinzip der Wahl des Bearbeitungsverfahrens besteht darin, die Bearbeitungsgenauigkeit und Oberflächenrauhigkeit der bearbeiteten Oberfläche sicherzustellen.
Da es viele Bearbeitungsmethoden gibt, um das gleiche Maß an Präzision und Oberflächenrauhigkeit zu erhalten, müssen bei der tatsächlichen Auswahl umfassende Überlegungen wie die Form, Größe und Toleranzanforderungen der Form und Position der Teile berücksichtigt werden. In der Figur erfordern mehrere Präzisierungen höhere Dimensionen. Da der Toleranzwert klein ist, wird während der Programmierung kein Mittelwert genommen und seine Grundgröße wird verwendet. Es gibt eine Verjüngung von 1: 5 und einen Bogenschnittpunkt auf der Konturlinie, und seine Koordinaten (29.7,0) (34, 16,5) (46, 22,5) werden während der Programmierung benötigt.
Durch die obige Datenanalyse, unter Berücksichtigung der Verarbeitungseffizienz und der wirtschaftlichen Verarbeitung, dreht sich das idealste Bearbeitungsverfahren. Wenn man bedenkt, dass das Teil massenbearbeitet ist, verwendet die Bearbeitungsausrüstung eine CNC-Drehmaschine. Die CJK6032 CNC-Werkzeugmaschine wurde basierend auf den Form- und Materialbedingungen der bearbeiteten Teile ausgewählt.
(4) Bestimmen Sie den Bearbeitungsplan
Eine anspruchsvollere Bearbeitung auf der Werkstückoberfläche wird oft durch Schruppen, Semi-Finishing und Endbearbeitung erreicht. Es reicht nicht aus, nur auf der Grundlage von Qualitätsanforderungen die geeignete Endverarbeitungsmethode für diese Oberflächen auszuwählen. Der Bearbeitungsplan vom Rohling bis zum endgültigen Umformen sollte ebenfalls korrekt ermittelt werden.
Blank zuerst das rechte Ende halten, das linke Ende der Kontur 50mm, die linke Kante Φ46mm, Φ29.7mm, Steigung 1: 5 Steigung, R6 Bogen, Bohrung Φ20mm Bohrung, Bohren Φ20mm Loch und C1.5 Fase drehen.
Heading-Klemmung wurde bearbeitet Φ46mm äußerer Kreis, rechtsseitige Bearbeitung Φ36mm, zurückgeschnittene Lamelle, Bearbeitungsgewinde M27 × 1,5, ø20mm, SΦ20mm und bis auf die Größe.
Die typische Achsenverarbeitungssequenz ist:
Vorbereitung - Drehflächen - Schrupp-Endprofile - Schlichten Drehen End-Profile - Bohren - Schruppbohrungen - Feinbohrlöcher - Werkstückdrehung - Schruppen des rechten Endprofils - Fertigdrehen des rechten Endprofils - Ausschneiden des Einschnitts - grobes Drehgewinde - Finish Gewinde.
(5) Bestimmen Sie die Positionierungsreferenz und die Befestigungsmethode:
(1) Positionierungsdatum: Es wird bestimmt, dass die Billet-Achse und die äußere Kreisebene die Referenz für die Positionierung sind.
(2) Klemmschema: Selbstzentrierendes Dreibackenfutter, Zentrierung und Klemmung übernehmen.
(6) Bestimmen Sie die Verarbeitungsreihenfolge und den Transportweg:
Die Verarbeitungssequenz wird von grob bis fein und von nah bis fern bestimmt.
Das heißt, von rechts nach links, Grobdrehen (einen 0,25 mm Finish-Wende-Rand lassen),
Dann drehen Sie von rechts nach links und drehen Sie schließlich das Gewinde.
(7) Werkzeugauswahl
(1) Verwenden Sie einen Φ5mm Zentrierbohrer, um das Mittelloch zu bohren.
(2) Verwenden Sie Φ20mm Hochgeschwindigkeits-Stahl-Spiralbohrer.
(3) Rough Turning und flache Stirnfläche verwenden 90 ° Hartmetall-Drehwerkzeug.
(4) Verwenden Sie ein Schnittmesser mit einer Breite von 5 mm.
(5) Das Gewinde ist aus Hartmetall 60 ° Außengewindedrehwerkzeug hergestellt, und der Radius des Spitzenradius ist kleiner als der minimale Bogenradius und 0,15-0,2 mm ist geeignet. Die ausgewählten Werkzeugparameter werden in die NC-Werkzeugkarte eingegeben (siehe Tabelle), um die Programmierung und das Betriebsmanagement zu vereinfachen.
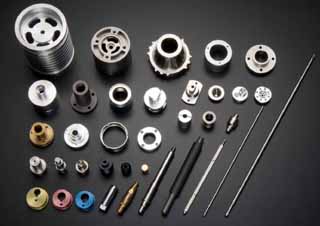
Werkzeugkarte für CNC-Bearbeitung
Produktname oder -code | Teilname | Typische Achse | Artikelnummer | |||
No. | Werkzeugnummer | Name der Werkzeugspezifikation | Anzahl | Bearbeitungsfläche | Note | |
1 | T01 | High-Speed-Stahl Φ5mm Zentrierbohrer | 1 | Loch links bohren | ||
2 | T02 | Hochgeschwindigkeitsstahl Φ20mm Spiralbohrer | 1 | Bohren Sie links Φ20mm Loch | ||
3 | T03 | Hartmetall-Drehwerkzeug 45 ° | 1 | Drehen der äußeren Kontur, Endfläche | ||
4 | T04 | 5mm groovendes Messer | 1 | Einstechen | ||
5 | T05 | Innenbohrungsbohrer | 1 | Feine Bohrung | ||
6 | T06 | 60 ° Außengewindedrehwerkzeug | 1 | Faden drehen | ||
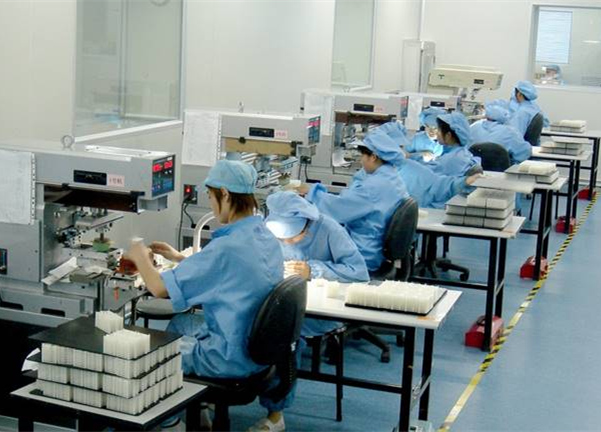
8) Auswahl der Schnittmenge
(1) zurück zu essen Messer Auswahl, Kontur grobe Drehzyklus Auswahl 3mm, Fertigdrehen Auswahl 0,25mm, Gewinde grob drehen Auswahl 0,4 mm, Messer mit Messer zu reduzieren, fertig drehen ist 0,1 mm.
(2) Spindeldrehzahlauswahl, gerade drehen und Bogen, wählen Sie grobe Drehgeschwindigkeit von 90m / min, beenden Sie Drehgeschwindigkeit 120m / min, dann verwenden Sie die Formel, um die Spindeldrehzahl zu berechnen: Grobdrehen: 500r / min, Fertigdrehen: 1200 U / min
(3) Die Auswahl der Vorschubgeschwindigkeit, Nachschlagetabelle wählt Grobdrehen, Fertigdrehvorschub pro Umdrehung und dann gemäß der tatsächlichen Situation der Verarbeitung zum Bestimmen des Grobdrehens pro Umdrehung Vorschub 0,4 mm / r, Fertigdrehen Null pro Umdrehung ist 0,15 mm / r. Schließlich wird das Grobdrehen gemäß der Formel berechnet. Der Fertigdrehvorschub beträgt 200 mm / min bzw. 180 mm / min.
Analysieren Sie umfassend die verschiedenen Inhalte der bisherigen Analyse und füllen Sie diese in die NC-Prozesskarte ein. Dies ist die wesentliche Grundlage für die Erstellung des Bearbeitungsprogramms und der Leitfäden für die NC-Bearbeitung durch den Bediener.
Zu den wichtigsten Inhalten gehören: die Reihenfolge der Arbeitsschritte, der Inhalt der Arbeitsschritte, die Schneidwerkzeuge und die Schnittmenge, die für jeden Arbeitsschritt verwendet werden.
CNC-Bearbeitungskarte
Kangding Metall |
CNC-Bearbeitungsprozess Karte |
Produktname oder -code |
Achse |
Materialien |
Artikelnummer |
||||||||||||||
Beispiele für CNC-Drehtechnologie |
Typische Wellenteile |
45 # Stahl |
|
||||||||||||||||
Angestellten ID |
Programmnummer |
Geräte-Nummer |
Verwenden Sie Ausrüstung |
|
Werkstatt |
||||||||||||||
|
|
|
CK6140 |
|
CNC-Zentrum
|
||||||||||||||
Schrittnummer |
Schritt Inhalt |
Werkzeugnummer |
Werkzeugspezifikationen (mm) | Spindeldrehzahl (U / min) |
Vorschubgeschwindigkeit f / (mm / r) |
Zurück Essen Messer ap / mm |
Hinweis |
||||||||||||
1 |
Flache Endfläche (linkes Ende) | T03 |
25×25 |
350 |
|
1 |
Manuell |
||||||||||||
2 |
Zentrierbohrung bohren |
T01 |
Ø5 |
800 |
|
2 |
Manuell |
||||||||||||
3 |
Bohren |
T02 |
Ø 20 |
200 |
|
15 |
Manuell |
||||||||||||
4 |
Schwerer Bohrlochkreis (invertierter) Winkel und Steigung |
T05 |
20×20 |
500 |
40 |
0.8 |
automatisch |
||||||||||||
5 |
Right boring inner hole fillet and bevel, guaranteed slope (1:5), Ra6 |
T05 |
20×20 |
800 |
40 |
0.2 |
automatisch |
||||||||||||
6 |
Biegen Sie die linke Kontur auf 50 mm und lassen Sie 0,25 mm Rand für den Außendurchmesser |
T03 |
25×25 |
500 |
40 |
2 |
automatisch | ||||||||||||
7 |
Endbearbeitung der äußeren Oberfläche |
T03 |
25×25 |
1200 |
15 |
0.25 |
automatisch | ||||||||||||
8 |
Drehen Sie die andere Seite des Autos, um die Länge zu gewährleisten |
T03 |
25×25 |
500 |
|
|
Manuell |
||||||||||||
9 |
Rough Drehen der äußeren Oberfläche, so dass 0,25 mm Marge |
T03 |
25×25 |
500 |
40 |
2 |
automatisch |
||||||||||||
10 |
Endbearbeitung der äußeren Oberfläche |
T03 |
25×25 |
1200 |
15 |
0.25 |
automatisch | ||||||||||||
11 |
Einstechen |
T05 |
16×16 |
400 |
20 |
2 |
automatisch |
||||||||||||
8 |
Grobdrehen eines Außengewindes |
T06 |
16×16 |
500 |
|
0.4 |
automatisch |
||||||||||||
9 |
Beenden Sie das Drehen des Außengewindes |
T06 |
16×16 |
800 |
|
0.1 |
automatisch |
||||||||||||
hergestellt von |
Liu Xin |
Rezension |
|
Genehmigt |
|
Insgesamt eine Seite |
Erste Seite |
||||||||||||
Table 4-2
(9) Manuelle Programmierung von Wellenteilen
Linkes Bearbeitungsprogramm:
O0020 Programmnummer
N001 G21 G99 G97 G40; Initialisierungsprozedur
N002 M03 S500 T0303; Spindeldrehung, Geschwindigkeit 500, Nr. 3 Messer und Werkzeugkompensation
N003 G00 X52 Z2; schneller Positionierzyklus Start (52,2)
N004 G71 U1.0 R0.5; grobe äußere Kontur
N005 G71 P006 Q010U0.3 W0.1 F0.15; Grobdrehen, X-Richtung Rand 0,3 mm, Z-Richtung Rand 0,1 mm
N006 G01 X29,7 Z0; Gerader Weg zum Punkt (29.7,0)
N007 X40 Z-16.5; Gerader Weg zum Punkt (40, -16.5)
N008 G02 U6 W-6 R6; Im Uhrzeigersinn auf (46 ,, - 22.5) mit Radius R6 mm drehen
N009 G01 Z-50; Gerade zu (46, -50)
N010 U2; Gerade zu (48, 16.5)
N011 G00 X31 Z2; Schnelle Positionierung zum Startpunkt des Zyklus
N012 G70 P006 Q010 F0.15; Endbearbeitung der äußeren Kontur
N013 G00 X100 Z50; Zum Werkzeugwechselpunkt zurückfahren
N014 MO3; Spindel steht fest
N015 M05; Programm gestoppt
Nach dem Umdrehen der rechten Seite des Bearbeitungsprogramms:
O0021 Programmnummer
N001 G21 G99 G97 G40; Initialisierungsprozedur
N002 M03 S500 T0303; Spindeldrehung, Geschwindigkeit 500, Nr. 3 Messer und Werkzeugkompensation
N003 G00 X52 Z2; schneller Positionierzyklus Start (52,2)
N004 G71 U1.0 R0.5; grobe äußere Kontur
N005 G71 P006 Q018U0.3 W0.1 F0.15; Grobdrehen, X-Richtung Rand 0,3 mm, Z-Richtung Rand 0,1 mm
N006 G01 X0 Z2; Geradeausfahrt zum Zyklusstartpunkt (0,2)
N007 G03 X20 Z-10 R10; Messer gegen den Uhrzeigersinn drehen bis zum Punkt (20, -10); R6
N008 G01 Z-26.5; Gerader Weg zum Punkt (20, -26.5)
N009 X25; Gerader Weg zum Punkt (25, -26.5)
N010 U2, Z-1; Gerade zu Punkt (27, -27.5)
N011 W-22; Gerade zu Punkt (25, -49,5)
N012 X32; Gerade zu Punkt (32, -49,5)
N013 G03 U4 W-2 R2; Gegen den Uhrzeigersinn zum Punkt (36, -51.5); R2
N014 G01 W-13; Geradeaus zum Punkt (36, -64,5)
N015 X44; Gerade zu Punkt (44, -64.5)
N016 U2 W-1; Geradeaus zum Punkt (46, -65,5)
N017 Z-68; Gerader Weg zum Punkt (46, -68.5)
N018 G00 X100 Z50; Schnelle Positionierung zum Werkzeugwechselpunkt
N019 X0 Z2 Schnelle Positionierung zum Startpunkt des Zyklus
N020 G70 P006 Q018F0.15; Endbearbeitung der äußeren Kontur
N021 G00 X100 Z50; Schnelle Positionierung zum Werkzeugwechselpunkt
N022 G21 G99 G97 G40; Initialisierungsprozedur
N023 M03 S500 T0505; Spindel positive Rotation, Geschwindigkeit 500, Nr. 5 Messer und Werkzeugkompensation
N024 G00 X38 Z-49,5; Positionierung zum schnellen Einstecken
N025 G01 X23; Einstechen
N026 X38; Zurück zum Punkt (38, -49.5)
N027 G00 X100 Z50; Schnelle Positionierung zum Werkzeugwechselpunkt
N028 G21 G99 G97 G40; Initialisierungsprozedur
N029 M03 S800 T0606; Spindeldrehung, Geschwindigkeit 800, Nr. 6 Messer und Werkzeugkompensation
N030 G00 X30 Z-25; Schnelle Positionierung zum Punkt (30, -25)
N031 G92 X26.2 Z-47 F1.5; Bearbeiteter Faden
N032 X 25,7; Bearbeiteter Faden
N033 X25,4; Bearbeiteter Faden
N034 X25.2; Bearbeiteter Faden
N035 X25.05; Bearbeitungsgarn
N036 G00 X100 Z50; Schnelle Positionierung zum Werkzeugwechselpunkt
N037 MO3; Spindel stoppen
N038 M05; Programm gestoppt