Die perfekte Kombination von In-Schimmel Tapping Technologie in der automatischen Stanzproduktion
Die Stanzindustrie muss Stanzteile zum Umformen von Fäden verarbeiten. Viele Hersteller bleiben immer noch in Einzelstanz- oder Nachprägeprodukten und führen dann Sekundäroperationen wie manuelles Klopfen, aktives Klopfen usw. durch. Dies ist eine Verschwendung von traditioneller Verarbeitungstechnologie. Die In-Mould-Tapping-Fähigkeiten können mit der automatischen Herstellung von Stanzvorrichtungen kombiniert werden, um die Integration von Stanzen und Gewindeschneiden zu erreichen. Ob es darum geht, die Automatisierung zu verbessern, die Effizienz zu steigern oder die Qualität zu verbessern, die Vorteile der In-Mould-Tapping-Technologie für Stanzbetriebe sind enorm.
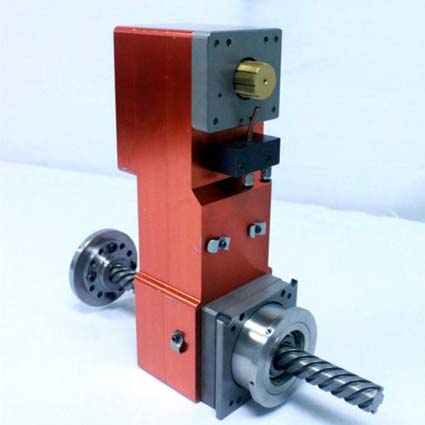
Vergleich zwischen traditionellem Gewindebohren und In-Form-Gewindebohren:
1, traditionelle klopfenproduktion methoden
Die traditionellen Verfahren zur Herstellung von Gewindebohrungen werden im Allgemeinen durch einen einzelnen Stanz- oder automatischen Pressformprozess, Transferprozess, manuellen Gewindebohrprozess oder aktiven Gewindebohrprozess verarbeitet, was zu hohen Produktionskosten, geringer Effizienz und fehlender Gewährleistung der Produktkonsistenz führt.
Die Gesamtkosten umfassen: Prozesskosten für das Stanzen, Überführungskosten und Kosten für das Abgreifen.
2. In-Schimmel-Abstichmethode
Die Produktionsweise des In-Form-Gewindeschneidens wird durch die automatische Integration des Stempelns "Formen + Gewindeschneiden" vervollständigt. Die Produktionsgeschwindigkeit ist schnell, die Effizienz ist hoch und die Fadenqualität ist stabil.
Die Gesamtkosten beinhalten: Stanz-Bearbeitungskosten + Gewindeschneidmaschine-Investition in die Form, während die Form-Gewindeschneidmaschine eine Kapitalinvestition darstellt.
Materialien: Die In-Schimmel Tapping Technology ist für kohlenstoffarmen Stahl, Edelstahl, Aluminium und Aluminiumlegierungen, Messingplatten und Kupferplatten verfügbar.
Die von In-Schimmel Tapping Technology verwendete Gewindebohrer-Kategorie ist ein spanloser Knetgewindebohrer. Das Kneten des Gewindebohrers ist eine neue Art von Gewindeschneidwerkzeug, das das Metall-Kunststoff-Verformungsprinzip verwendet, um das Innengewinde ohne Schneidkante und Spannuten zu bearbeiten. Es gibt jedoch eine oder mehrere glatte Ölnuten, und die Form des Gewindebohrers ist Multi-Diamant, was eine spanlose Bearbeitungstechnologie ist. Die durch den Knetgewindebohrer extrudierten Gewinde haben eine hohe Oberflächengüte, die Metallfasern der Gewindegänge reißen nicht und bilden eine Schicht aus einer abgeschreckten Schicht auf der äußeren Oberfläche, was die Festigkeit und Verschleißfestigkeit der Gewinde verbessern kann. Es löst grundsätzlich das schwierige Problem des Gewindeschneidens, da keine Späneabfuhr mehr förderlich für den Zusammenbau des Gewindes ist. Anstatt Metall während des Gewindeschneidens zu schneiden, werden Gewinde durch Metallplastizität gebildet. Daher ist der Durchmesser größer als der Durchmesser des Gewindes und die Knickform der Gewindeform ist U-förmig.
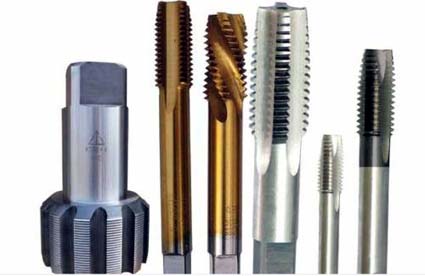
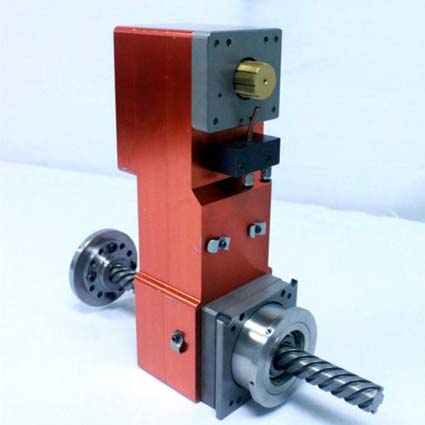
Vergleich zwischen traditionellem Gewindebohren und In-Form-Gewindebohren:
1, traditionelle klopfenproduktion methoden
Die traditionellen Verfahren zur Herstellung von Gewindebohrungen werden im Allgemeinen durch einen einzelnen Stanz- oder automatischen Pressformprozess, Transferprozess, manuellen Gewindebohrprozess oder aktiven Gewindebohrprozess verarbeitet, was zu hohen Produktionskosten, geringer Effizienz und fehlender Gewährleistung der Produktkonsistenz führt.
Die Gesamtkosten umfassen: Prozesskosten für das Stanzen, Überführungskosten und Kosten für das Abgreifen.
2. In-Schimmel-Abstichmethode
Die Produktionsweise des In-Form-Gewindeschneidens wird durch die automatische Integration des Stempelns "Formen + Gewindeschneiden" vervollständigt. Die Produktionsgeschwindigkeit ist schnell, die Effizienz ist hoch und die Fadenqualität ist stabil.
Die Gesamtkosten beinhalten: Stanz-Bearbeitungskosten + Gewindeschneidmaschine-Investition in die Form, während die Form-Gewindeschneidmaschine eine Kapitalinvestition darstellt.
Materialien: Die In-Schimmel Tapping Technology ist für kohlenstoffarmen Stahl, Edelstahl, Aluminium und Aluminiumlegierungen, Messingplatten und Kupferplatten verfügbar.
Die von In-Schimmel Tapping Technology verwendete Gewindebohrer-Kategorie ist ein spanloser Knetgewindebohrer. Das Kneten des Gewindebohrers ist eine neue Art von Gewindeschneidwerkzeug, das das Metall-Kunststoff-Verformungsprinzip verwendet, um das Innengewinde ohne Schneidkante und Spannuten zu bearbeiten. Es gibt jedoch eine oder mehrere glatte Ölnuten, und die Form des Gewindebohrers ist Multi-Diamant, was eine spanlose Bearbeitungstechnologie ist. Die durch den Knetgewindebohrer extrudierten Gewinde haben eine hohe Oberflächengüte, die Metallfasern der Gewindegänge reißen nicht und bilden eine Schicht aus einer abgeschreckten Schicht auf der äußeren Oberfläche, was die Festigkeit und Verschleißfestigkeit der Gewinde verbessern kann. Es löst grundsätzlich das schwierige Problem des Gewindeschneidens, da keine Späneabfuhr mehr förderlich für den Zusammenbau des Gewindes ist. Anstatt Metall während des Gewindeschneidens zu schneiden, werden Gewinde durch Metallplastizität gebildet. Daher ist der Durchmesser größer als der Durchmesser des Gewindes und die Knickform der Gewindeform ist U-förmig.
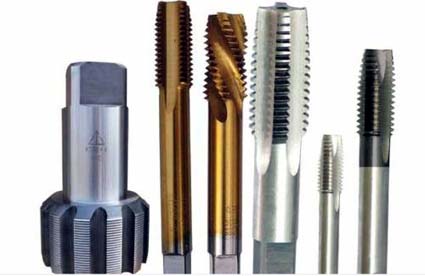
In-Schimmel Tapping Funktionen:
(1) Gewindebohrer Ersatz ist schnell und kann in nur 1 min abgeschlossen werden.
(2) Die Gewindebohrvorrichtung ist in drei Methoden unterteilt: fest, schwimmend und hängend. Das Gerät kann exakt nach Kundenwunsch positioniert werden.
Festgelegter Typ
(1) Das Links- oder Rechtsgewinde kann entsprechend den Produktanforderungen geformt werden.
(2) Die konzentrische Sechspunkt-Aufsammeltechnologie gewährleistet die hohe Präzision der Gewindeformung.
(3) Auswahl der Form-Klopfvorrichtung Doppelschutzversicherung, das Stanzen sicher und schnell klopfend.
Schwimmend
(1) Gewindebohrer und Zerstäubungskühl- und -glättungssystem WD-10 für Geräte- und Stempelsynchronisationssignale mit gutem Kraftstoffverbrauch und Kühlwirkung.
(2) Schnelle Klopfgeschwindigkeit, bis zu 120 Löcher / Minute, hohe Effizienz.
(3) Nach dem Austausch von Leitungsanordnungen unterschiedlicher Standards können unterschiedliche Gewindeabmessungen auf demselben Körper gebildet werden.
Art der Aufhängung
(1) Das Modell ist vorzüglich, nimmt den Formraum nicht ein, beeinflußt nicht die Modellkosten, die elastische Vorrichtungsplanung.
(2) Geschlossene und glatte Zirkulation, bequeme Operation und Wartung.
(3) Es gibt Einloch-, poröse, horizontale, kombinierte und servogetriebene Serienmodelle, die verschiedene Einsatzbedingungen erfüllen können.
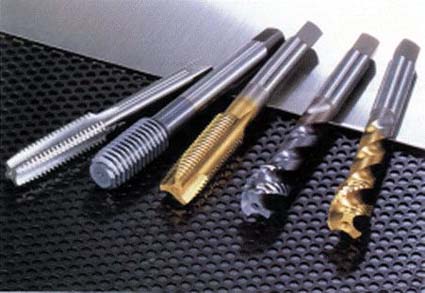
Beeinflussende Faktoren
Wenn Sie die Faktoren wie die Produkttechnologie nicht berücksichtigen, sind die Hauptfaktoren, die die In-Schimmel Tapping-Rolle beeinflussen, die Gewindeschneidgeschwindigkeit, die Gewindebohrerstandzeit, die Werkzeugplanung und -ausrüstung sowie die Ölauswahl.
(1) Abgreifgeschwindigkeit.
Folgende Faktoren beeinflussen die In-Mold-Abstichgeschwindigkeit: Gewindegrundloch, Gewindeschneidtiefe, Speisepunkt, Produktrohmaterial, Gewindebohrerqualität, Kühlwirkung.
(2) Gewindebohrerlebensdauer.
Die wichtigsten Faktoren, die die Lebensdauer des Gewindebohrers beeinflussen, sind die folgenden neun:
Gewindebohrung, Gewindetiefe, Gewindeschneidgeschwindigkeit, Produktrohmaterial, Vorschubgenauigkeit, Gewindebohrerqualität, Kühlwirkung, korrekte Vorrichtung, nationaler Standard.
(3) Formenplanung und Installationen.
Voraussetzung für die Einführung von In-Schimmel Tapping-Skills ist, dass der Geräteplatz benötigt wird. Dies erfordert von allen Herstellern, die diese Fähigkeit importieren, eine Änderung des Produktionsprozesses, aber auch die Erneuerung bestehender Formen. Neuentwickelte sukzessive Metallformen, der Formkern wird bei der Planung in zwei Teile geteilt, der Bauraum bleibt, die Originalform hat den Planungs- und Reparaturraum für die Vorbereitung der Prozesspositionen, modifizierte oder Multi-Prozess-Form mit geplanten Reservepositionen, kann in das Gerät In-Schimmel Tapping Fähigkeiten eingeführt werden.
(4) Auswahl des Abstichöls.
Entsprechende Gewindeöle sollten entsprechend den Materialien in der Produktion ausgewählt werden. Wenn tiefe Löcher bearbeitet werden, können wir außerdem die Anzahl der glatten Ölnuten auf dem Knethahn hinzufügen, um die Glätte zu verbessern.
Der Einsatz von In-Schimmel Tapping Fähigkeiten in der Hobelproduktion
Der Produktionsprozeß der inländischen Hobelmesserfirmen ist nur in den künstlich kombinierten halbautomatischen Verarbeitungsbedingungen geblieben. Seine traditionellen Verarbeitungsmethoden und zahlreiche Prozesse verbrauchen viele Ressourcen und profitablen Platz. Langsamer Produktionsfortschritt und instabile Qualität. Als Reaktion auf diese Situation haben viele Unternehmen mit der technologischen Innovation begonnen und hervorragende Ergebnisse erzielt. Original Hobelmesser Produkte, Produkt Dicke 3,8 mm, Rohstoff Q235. Seine Verarbeitungsverfahren sind zahlreich und der Prozess ist chaotisch.
Der Einsatz der In-Schimmel Tapping Technologie zur Automatisierung des Stanz-Integrationssystems erfordert nur zwei Stanz-Produktionsprozesse, um die Verarbeitung des Produktes zu vervollständigen. Nachdem das In-Schimmel Tapping dental auto Stanzsystem das Aufwickelmaterial zum Ausstanzen und Ausschneiden des Blanks ausgewählt hat, wird das Roboterschweißgerät verwendet, um das Rohembryoschweißen der Klingen in das Produkt durchzuführen. Automatisierte Produktionslinien (Stanzen + In-Mold-Tapping) vervollständigen die Produktion von Fertigprodukten.
Nachdem der neue Prozess ausgewählt wurde, beträgt die Änderung der Längenabmessung des Produkts nach dem Stanzen weniger als 0,2 mm, die mäanderförmige Menge der Seitenbiegung (eingesetzte Stahlkante) weniger als 0,1 mm (Änderungsbetrag vor und nach dem Stanzen) und die Ebene Zickzack ist weniger als 0,2 mm. Der Stanzabschnitt jedes Lochs, die minimale 1/3 glatte Oberfläche, um die Datendicke sicherzustellen, 2/3 Abschnitt, keine Aussehensdefekte wie das Reißen, das Anhaften, von usw. Die Höhe der gestempelten Ecke ist weniger als 0.3mm und das Die Threads sind nach dem Threading voll. Keine Zähne, Zähne und andere Bedingungen. Seine normale Massenproduktion erreicht 6000 Stück / 8 Stunden oder mehr, weit höher als die 1500 Stücke / 8 Stunden des alten Handwerks. Die Produktionskapazität wurde erheblich erhöht, die Produktionskosten und der Ressourcenverbrauch wurden gut kontrolliert, und die Produktwettbewerbsfähigkeit des Unternehmens wurde weiter verbessert.
Nach dem tatsächlichen Vergleich der alten und neuen Technologien und der Produktion Rückkehr Besuch, egal wie das Aussehen des Produkts, Maßstab Genauigkeit, Produktionsleistung, Stabilität und Werkstatt Produktionsumgebung sind immer noch Geräteschutz Operationen haben eine neue Stufe der Fähigkeiten erreicht.
(1) Gewindebohrer Ersatz ist schnell und kann in nur 1 min abgeschlossen werden.
(2) Die Gewindebohrvorrichtung ist in drei Methoden unterteilt: fest, schwimmend und hängend. Das Gerät kann exakt nach Kundenwunsch positioniert werden.
Festgelegter Typ
(1) Das Links- oder Rechtsgewinde kann entsprechend den Produktanforderungen geformt werden.
(2) Die konzentrische Sechspunkt-Aufsammeltechnologie gewährleistet die hohe Präzision der Gewindeformung.
(3) Auswahl der Form-Klopfvorrichtung Doppelschutzversicherung, das Stanzen sicher und schnell klopfend.
Schwimmend
(1) Gewindebohrer und Zerstäubungskühl- und -glättungssystem WD-10 für Geräte- und Stempelsynchronisationssignale mit gutem Kraftstoffverbrauch und Kühlwirkung.
(2) Schnelle Klopfgeschwindigkeit, bis zu 120 Löcher / Minute, hohe Effizienz.
(3) Nach dem Austausch von Leitungsanordnungen unterschiedlicher Standards können unterschiedliche Gewindeabmessungen auf demselben Körper gebildet werden.
Art der Aufhängung
(1) Das Modell ist vorzüglich, nimmt den Formraum nicht ein, beeinflußt nicht die Modellkosten, die elastische Vorrichtungsplanung.
(2) Geschlossene und glatte Zirkulation, bequeme Operation und Wartung.
(3) Es gibt Einloch-, poröse, horizontale, kombinierte und servogetriebene Serienmodelle, die verschiedene Einsatzbedingungen erfüllen können.
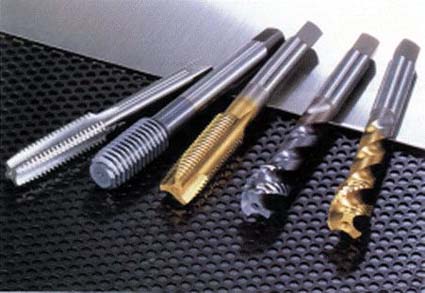
Beeinflussende Faktoren
Wenn Sie die Faktoren wie die Produkttechnologie nicht berücksichtigen, sind die Hauptfaktoren, die die In-Schimmel Tapping-Rolle beeinflussen, die Gewindeschneidgeschwindigkeit, die Gewindebohrerstandzeit, die Werkzeugplanung und -ausrüstung sowie die Ölauswahl.
(1) Abgreifgeschwindigkeit.
Folgende Faktoren beeinflussen die In-Mold-Abstichgeschwindigkeit: Gewindegrundloch, Gewindeschneidtiefe, Speisepunkt, Produktrohmaterial, Gewindebohrerqualität, Kühlwirkung.
(2) Gewindebohrerlebensdauer.
Die wichtigsten Faktoren, die die Lebensdauer des Gewindebohrers beeinflussen, sind die folgenden neun:
Gewindebohrung, Gewindetiefe, Gewindeschneidgeschwindigkeit, Produktrohmaterial, Vorschubgenauigkeit, Gewindebohrerqualität, Kühlwirkung, korrekte Vorrichtung, nationaler Standard.
(3) Formenplanung und Installationen.
Voraussetzung für die Einführung von In-Schimmel Tapping-Skills ist, dass der Geräteplatz benötigt wird. Dies erfordert von allen Herstellern, die diese Fähigkeit importieren, eine Änderung des Produktionsprozesses, aber auch die Erneuerung bestehender Formen. Neuentwickelte sukzessive Metallformen, der Formkern wird bei der Planung in zwei Teile geteilt, der Bauraum bleibt, die Originalform hat den Planungs- und Reparaturraum für die Vorbereitung der Prozesspositionen, modifizierte oder Multi-Prozess-Form mit geplanten Reservepositionen, kann in das Gerät In-Schimmel Tapping Fähigkeiten eingeführt werden.
(4) Auswahl des Abstichöls.
Entsprechende Gewindeöle sollten entsprechend den Materialien in der Produktion ausgewählt werden. Wenn tiefe Löcher bearbeitet werden, können wir außerdem die Anzahl der glatten Ölnuten auf dem Knethahn hinzufügen, um die Glätte zu verbessern.
Der Einsatz von In-Schimmel Tapping Fähigkeiten in der Hobelproduktion
Der Produktionsprozeß der inländischen Hobelmesserfirmen ist nur in den künstlich kombinierten halbautomatischen Verarbeitungsbedingungen geblieben. Seine traditionellen Verarbeitungsmethoden und zahlreiche Prozesse verbrauchen viele Ressourcen und profitablen Platz. Langsamer Produktionsfortschritt und instabile Qualität. Als Reaktion auf diese Situation haben viele Unternehmen mit der technologischen Innovation begonnen und hervorragende Ergebnisse erzielt. Original Hobelmesser Produkte, Produkt Dicke 3,8 mm, Rohstoff Q235. Seine Verarbeitungsverfahren sind zahlreich und der Prozess ist chaotisch.
Der Einsatz der In-Schimmel Tapping Technologie zur Automatisierung des Stanz-Integrationssystems erfordert nur zwei Stanz-Produktionsprozesse, um die Verarbeitung des Produktes zu vervollständigen. Nachdem das In-Schimmel Tapping dental auto Stanzsystem das Aufwickelmaterial zum Ausstanzen und Ausschneiden des Blanks ausgewählt hat, wird das Roboterschweißgerät verwendet, um das Rohembryoschweißen der Klingen in das Produkt durchzuführen. Automatisierte Produktionslinien (Stanzen + In-Mold-Tapping) vervollständigen die Produktion von Fertigprodukten.
Nachdem der neue Prozess ausgewählt wurde, beträgt die Änderung der Längenabmessung des Produkts nach dem Stanzen weniger als 0,2 mm, die mäanderförmige Menge der Seitenbiegung (eingesetzte Stahlkante) weniger als 0,1 mm (Änderungsbetrag vor und nach dem Stanzen) und die Ebene Zickzack ist weniger als 0,2 mm. Der Stanzabschnitt jedes Lochs, die minimale 1/3 glatte Oberfläche, um die Datendicke sicherzustellen, 2/3 Abschnitt, keine Aussehensdefekte wie das Reißen, das Anhaften, von usw. Die Höhe der gestempelten Ecke ist weniger als 0.3mm und das Die Threads sind nach dem Threading voll. Keine Zähne, Zähne und andere Bedingungen. Seine normale Massenproduktion erreicht 6000 Stück / 8 Stunden oder mehr, weit höher als die 1500 Stücke / 8 Stunden des alten Handwerks. Die Produktionskapazität wurde erheblich erhöht, die Produktionskosten und der Ressourcenverbrauch wurden gut kontrolliert, und die Produktwettbewerbsfähigkeit des Unternehmens wurde weiter verbessert.
Nach dem tatsächlichen Vergleich der alten und neuen Technologien und der Produktion Rückkehr Besuch, egal wie das Aussehen des Produkts, Maßstab Genauigkeit, Produktionsleistung, Stabilität und Werkstatt Produktionsumgebung sind immer noch Geräteschutz Operationen haben eine neue Stufe der Fähigkeiten erreicht.
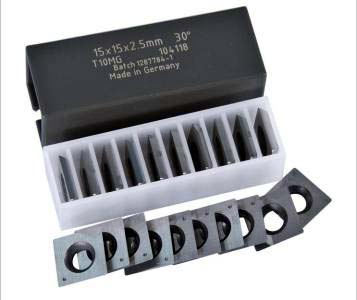