Titan legierung Precision Lagerteile Drehmaschine Verarbeitung Technologie-Design
Schlüsselwörter: Titanlegierungs-Wellenteile, Drehmaschinen-Bearbeitungstechnik, Grobe Benchmark-Auswahl, Verfahren zur Behandlung der, Lageroberfläche, Achsenbearbeitungsschritte, Titan-Abschrecken und Anlassen
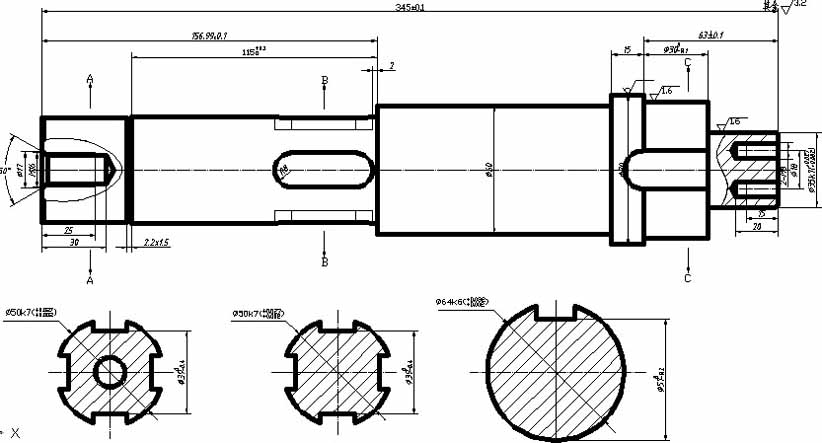
1. Die Rolle der Wellenkomponenten
Die Hauptfunktion der Abtriebswelle der Teildrehmaschine besteht darin, ein Drehmoment zu übertragen, so dass die Spindel der Drehmaschine eine Kraftdrehung erhalten kann. Zweitens trägt es oft die Last der Arbeit. Das dritte sind die tragenden Getriebekomponenten.
2. Teileanalyse
(1) Wie aus der Teilezeichnung ersichtlich ist, handelt es sich bei dem Teil um einen typischen Wellentyp, und sein Aufbau ist relativ einfach. Die Anordnung der Wellenabschnitte ist trapezförmig, die Mitte ist dick und die Enden sind dünn. Es entspricht dem Prinzip der Festigkeit und Form und ist leicht zu installieren und zu demontieren.
(2) Die Hauptbearbeitungsfläche ist 50, 60, 64, 35 und die äußere zylindrische Fläche. Das Innengewindeloch der linken Stirnfläche M16 und das Innengewindeloch M8 der beiden kleinen Stirnflächen.
(3) Wie aus der Abbildung ersichtlich ist, ist die Maßgenauigkeit der Teile sehr hoch und die meisten von ihnen sind IT7. Die Rauheit ist auf der kleinen zylindrischen Oberfläche der Welle angegeben, und die äußere zylindrische Oberfläche von φ64 ist Ra1.6um. Die Endfläche des kleinen Endes ist Ra1.6um und der Rest ist Ra3.2um, was relativ hoch ist;
(4) Die Wärmebehandlung erfordert eine Abschreck- und Anlassbehandlung, HRC 28-30, um die Gleichmäßigkeit aufrechtzuerhalten. Schließlich Oberflächenoxidationsbehandlung
(5) Das Material dieses Teils ist TC4 Ti-6Al-4V.
(6) Die 45 ° -Fase ist am Wellenende für eine einfache Montage bearbeitet.
IV. Auswahl der Rohlinge und Bestimmung der Rohlingsgröße
1. Wählen Sie leer
(1) Der Rohling dieses Teils ist TC4 Ti-6Al-4V, ein typisches Wellenmaterial und eine der am häufigsten verwendeten Titanlegierungen. Nach dem Tempern und Oberflächenhärten kann eine bessere Gesamtleistung erzielt werden.
(2) Aufgrund des einfachen Zustands des Werkstücks kann das Profil TC4 Ti-6Al-4V verwendet werden. Der Rohling wird durch Kaltziehen hergestellt. Da der äußere Kreis von Φ70 angibt, dass das Material nicht entfernt wurde, wird ein Durchmesser von Φ70 mm gewählt. Überprüfen Sie das "Kurzhandbuch für den mechanischen Herstellungsprozess", um die Rohlingsgenauigkeitsklasse IT7 mit der Oberflächenrauheit Ra3.2 bis 1.6 zu erhalten.
2. Bestimmen Sie die verbleibende Menge des Rohlings
Tabelle 2
V. Gestaltung des Prozessplans
Benchmark-Auswahl
(1) Wählen Sie eine grobe Referenz
Raue Referenz sollte die Positionsgenauigkeit zwischen der Bearbeitungsoberfläche und der nicht arbeitenden Fläche, eine angemessene Zuteilung der einzelnen bearbeiteten Oberfläche das Gleichgewicht zu gewährleisten, werden ausgewählt, und eine genaue Referenz für den nachfolgenden Prozess zur Verfügung zu stellen. Um das Positionieren, Spannen und Bearbeiten zu erleichtern, kann daher die zylindrische Oberfläche der Welle als Referenz ausgewählt werden, oder eine zylindrische Oberfläche und ein Scheitelpunktloch können als Referenz verwendet werden. Beim Positionieren mit einer zylindrischen Oberfläche wird normalerweise das Spannfutter verwendet, da es die Bequemlichkeit der Referenzbearbeitung und -spannung bietet. Um sicherzustellen, dass die zulässige Aufrauung wichtiger Oberflächen gering und gleichmäßig ist, sollte die kleine Endfläche des Teils als grobe Referenz gewählt werden.
(2) Auswahl ausgewählter Benchmarks
Entsprechend den technischen Anforderungen und den Montageanforderungen der Abtriebswelle des Untersetzungsgetriebes sollte die rechte Stirnfläche der Welle als Feinreferenz φ50 + 0,027, 0,002 und die Stirnfläche φ35 + 0,027, 0,002 gewählt werden. Viele Oberflächen des Teils können mit der Endfläche als Referenz bearbeitet werden. Benchmark-Konvertierungsfehler können vermieden und Benchmarking-Prinzipien befolgt werden. Die Mittelachse an beiden Enden ist die Basis für die Konstruktion. Die Mittelachse wird als Referenz ausgewählt, um die endgültige Bearbeitungspositionsgenauigkeit der Oberfläche zu gewährleisten und eine Konsistenz der Konstruktionsbasis und der Prozessreferenz zu erzielen.
2. Bestimmung der Oberflächenbehandlungsmethode des Teils
Entsprechend den Verarbeitungsanforderungen und Materialeigenschaften jeder Oberfläche der Teilezeichnung ist die Welle eine abgestufte Welle, und die spezifische Verarbeitungsmethode jeder Oberfläche der Welle ist in Tabelle 2 gezeigt.
3. Anordnung der Verarbeitungsreihenfolge
(1) Bearbeitung
1> Andere Prinzipien nach der ersten Bezugsebene:
Der Verarbeitungsplan verarbeitet immer zuerst die Positionierungsdaten, daher sollten Sie die Vorbereitung des Folgeprozesses als Basis festlegen. Zunächst wird die Referenzebene vervollständigt und der äußere Kreis des Mittellochs und der rotierenden Fläche gedreht.
2> nach dem prinzip der "erste grob und fein"
Zuerst wird der Schruppvorgang angeordnet, gefolgt vom Endbearbeitungsvorgang. Zunächst wird die Hauptfläche hochpräzise angeordnet und anschließend sortiert.
3> Basierend auf dem Prinzip der Priorität und Priorität:
Die Hauptfläche wird zuerst behandelt, beispielsweise die Außenfläche des Außenkreises, die Endfläche und dergleichen. Hilfsflächen nachbearbeiten, z. B. Passfedernuten fräsen.
4> Zuerst außen und dann innen, zuerst großes und kleines Prinzip:
Zuerst wird der äußere Kreis bearbeitet und dann wird das innere Loch durch den äußeren Kreis positioniert. Bei der Bearbeitung eines gestuften Außenkreises wird zuerst der größere Durchmesser und später der kleinere Durchmesser bearbeitet.
5> Sekundäre Oberflächenbehandlungsanordnung:
Die Bearbeitung von Untergründen wie Keilnuten erfolgt typischerweise nach dem zylindrischen Fertigdrehen. Für das rechte Ende der Achse und das mittlere Ende der Achse sollte eine Oberfläche mit höheren Anforderungen an die Bearbeitungsqualität dahinter angeordnet werden.
6> Die rechte Endfläche der Welle ist 64 mm und die mittlere 35 mm. Die Qualität ist höher und die Rückseite ist angeordnet.
7> Prinzip der ersten Seite und des hinteren Lochs:
Zuerst werden die Stirnseiten bearbeitet, dann die Keilnut gefräst und die Gewindelöcher gebohrt.
2) Anordnung des Wärmebehandlungsprozesses
Es wird empfohlen, vor dem Schneiden eine Normalisierung durchzuführen, die die Härte des Schafts erhöhen, die innere Spannung des Rohlings beseitigen und die Schneidleistung verbessern kann. Nach dem Schruppen kann das Abschrecken und Anlassen die Gesamtleistung der Welle verbessern. Die abschließende Wärmebehandlung nach dem Halbfinish verbessert die Materialfestigkeit, Oberflächenhärte und Verschleißfestigkeit.
Nach dem Schruppen und der Wärmebehandlung wird der Richtvorgang angeordnet. Entgratungs- und Zwischenprüfungsverfahren werden nach dem Halbfinish vereinbart. Nach Fertigstellung Entgraten, Reinigen und Endkontrolle veranlassen.
Zusammenfassend ist die Betriebsreihenfolge der Achsen:
Benchmarking_Hauptoberflächenaufrauen_Wärmebehandlung_Halbschlichten der Hauptoberfläche_Bearbeiten der Hauptoberfläche (Schleifen) _Fräsen von Passfedernuten und Gewindebohren_Entgraten, abschließende Wärmebehandlung usw.
4. Bestimmen Sie die technische Route der Welle
Basierend auf der Analyse des obigen Prozesses wird der Prozessweg der Komponente bestimmt, wie in Tabelle 4 gezeigt.
5. Bearbeitungszugabe, Bestimmung der Prozessgröße
Um die Bearbeitungsmaße der Zylinderfläche zu bestimmen, beziehen sich die Bearbeitungsmaße der Zylinderfläche für die Mehrfachbearbeitung nur auf die Bearbeitungszugabe. Die Gesamtbearbeitungszugabe (Rohlingsrand) für jede zylindrische Oberfläche wurde zuvor bestimmt, und die Rohlingszugabe sollte in die Bearbeitungszugabe für jeden Prozess unterteilt werden, und dann werden die Prozessabmessungen von hinten nach vorne berechnet. Die Toleranz der Zwischenabmessungen des Prozesses wird durch die wirtschaftliche Genauigkeit der Verarbeitungsmethode bestimmt. Die Prozesstoleranzen, Prozessabmessungen und -toleranzen sowie die Oberflächenrauheit jeder zylindrischen Oberfläche des Teils sind wie folgt:
Tabelle 5 äußere zylindrische Fläche φ50
Berechnung der Bearbeitungszugabe für die Achse
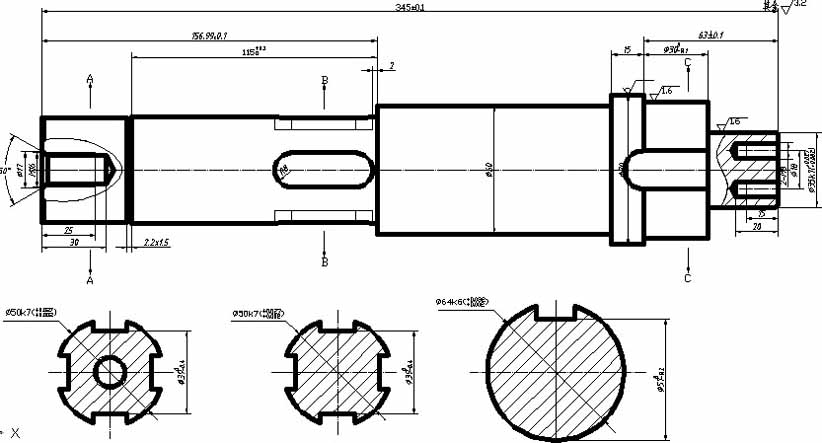
1. Die Rolle der Wellenkomponenten
Die Hauptfunktion der Abtriebswelle der Teildrehmaschine besteht darin, ein Drehmoment zu übertragen, so dass die Spindel der Drehmaschine eine Kraftdrehung erhalten kann. Zweitens trägt es oft die Last der Arbeit. Das dritte sind die tragenden Getriebekomponenten.
2. Teileanalyse
(1) Wie aus der Teilezeichnung ersichtlich ist, handelt es sich bei dem Teil um einen typischen Wellentyp, und sein Aufbau ist relativ einfach. Die Anordnung der Wellenabschnitte ist trapezförmig, die Mitte ist dick und die Enden sind dünn. Es entspricht dem Prinzip der Festigkeit und Form und ist leicht zu installieren und zu demontieren.
(2) Die Hauptbearbeitungsfläche ist 50, 60, 64, 35 und die äußere zylindrische Fläche. Das Innengewindeloch der linken Stirnfläche M16 und das Innengewindeloch M8 der beiden kleinen Stirnflächen.
(3) Wie aus der Abbildung ersichtlich ist, ist die Maßgenauigkeit der Teile sehr hoch und die meisten von ihnen sind IT7. Die Rauheit ist auf der kleinen zylindrischen Oberfläche der Welle angegeben, und die äußere zylindrische Oberfläche von φ64 ist Ra1.6um. Die Endfläche des kleinen Endes ist Ra1.6um und der Rest ist Ra3.2um, was relativ hoch ist;
(4) Die Wärmebehandlung erfordert eine Abschreck- und Anlassbehandlung, HRC 28-30, um die Gleichmäßigkeit aufrechtzuerhalten. Schließlich Oberflächenoxidationsbehandlung
(5) Das Material dieses Teils ist TC4 Ti-6Al-4V.
(6) Die 45 ° -Fase ist am Wellenende für eine einfache Montage bearbeitet.
IV. Auswahl der Rohlinge und Bestimmung der Rohlingsgröße
1. Wählen Sie leer
(1) Der Rohling dieses Teils ist TC4 Ti-6Al-4V, ein typisches Wellenmaterial und eine der am häufigsten verwendeten Titanlegierungen. Nach dem Tempern und Oberflächenhärten kann eine bessere Gesamtleistung erzielt werden.
(2) Aufgrund des einfachen Zustands des Werkstücks kann das Profil TC4 Ti-6Al-4V verwendet werden. Der Rohling wird durch Kaltziehen hergestellt. Da der äußere Kreis von Φ70 angibt, dass das Material nicht entfernt wurde, wird ein Durchmesser von Φ70 mm gewählt. Überprüfen Sie das "Kurzhandbuch für den mechanischen Herstellungsprozess", um die Rohlingsgenauigkeitsklasse IT7 mit der Oberflächenrauheit Ra3.2 bis 1.6 zu erhalten.
2. Bestimmen Sie die verbleibende Menge des Rohlings
Tabelle 2
Produktübersicht | Oberflächencode wird verarbeitet | Die Grundmaße | Bearbeitungszugabe | Bearbeitungszugabe |
Beschreibung
|
![]() |
D1 | 50 | IT7 | 20 | |
D2 | 50 | IT7 | 20 | ||
D3 | 60 | IT7 | 10 | ||
D4 | 70 | IT7 | |||
D5 | 64 | IT7 | 6 | ||
D6 | 35 | IT7 | 35 | ||
D7 | |||||
D8 |
V. Gestaltung des Prozessplans
Benchmark-Auswahl
(1) Wählen Sie eine grobe Referenz
Raue Referenz sollte die Positionsgenauigkeit zwischen der Bearbeitungsoberfläche und der nicht arbeitenden Fläche, eine angemessene Zuteilung der einzelnen bearbeiteten Oberfläche das Gleichgewicht zu gewährleisten, werden ausgewählt, und eine genaue Referenz für den nachfolgenden Prozess zur Verfügung zu stellen. Um das Positionieren, Spannen und Bearbeiten zu erleichtern, kann daher die zylindrische Oberfläche der Welle als Referenz ausgewählt werden, oder eine zylindrische Oberfläche und ein Scheitelpunktloch können als Referenz verwendet werden. Beim Positionieren mit einer zylindrischen Oberfläche wird normalerweise das Spannfutter verwendet, da es die Bequemlichkeit der Referenzbearbeitung und -spannung bietet. Um sicherzustellen, dass die zulässige Aufrauung wichtiger Oberflächen gering und gleichmäßig ist, sollte die kleine Endfläche des Teils als grobe Referenz gewählt werden.
(2) Auswahl ausgewählter Benchmarks
Entsprechend den technischen Anforderungen und den Montageanforderungen der Abtriebswelle des Untersetzungsgetriebes sollte die rechte Stirnfläche der Welle als Feinreferenz φ50 + 0,027, 0,002 und die Stirnfläche φ35 + 0,027, 0,002 gewählt werden. Viele Oberflächen des Teils können mit der Endfläche als Referenz bearbeitet werden. Benchmark-Konvertierungsfehler können vermieden und Benchmarking-Prinzipien befolgt werden. Die Mittelachse an beiden Enden ist die Basis für die Konstruktion. Die Mittelachse wird als Referenz ausgewählt, um die endgültige Bearbeitungspositionsgenauigkeit der Oberfläche zu gewährleisten und eine Konsistenz der Konstruktionsbasis und der Prozessreferenz zu erzielen.
2. Bestimmung der Oberflächenbehandlungsmethode des Teils
Entsprechend den Verarbeitungsanforderungen und Materialeigenschaften jeder Oberfläche der Teilezeichnung ist die Welle eine abgestufte Welle, und die spezifische Verarbeitungsmethode jeder Oberfläche der Welle ist in Tabelle 2 gezeigt.
Bearbeitete Oberfläche | Maßgenauigkeitsgrad | Oberflächenrauheit Ra (μm) | Verarbeitungsmethode |
Linke und rechte Stirnfläche | IT12 | 12.5 | Schruppdrehmaschinen |
Φ50 0,027, +0.002 äußere kreisförmige Oberfläche | IT7 | 3.2 | Grobdrehen_Halbendrehen |
Φ60 äußere kreisförmige Oberfläche | IT7 | 3.2 | Grobdrehen _ Halbfertigdrehen |
Φ64 0,032, +0.002 äußere kreisförmige Oberfläche | IT7 | 1.6 | Grobdrehen _ Halbfertigdrehen _ Schlichten |
Φ35 0,027, +0.002 äußere kreisförmige Oberfläche | IT7 | 1.6 | Grobdrehen _ Halbfertigdrehen _ Feindrehen |
Entnahmerille | IT12 | 12.5 | Feines Drehen |
Splin | IT7 | 3.2 | Grobfräsen _ Halbfeinfräsen |
Flacher Schlüssel | IT7 | 3.2 | Grobfräsen _ Halbfeinfräsen |
Kleines Ende Gewindebohrung | IT12 | 12.5 | Bohren _ Gewindebohren |
Großes Ende Gewindebohrung | IT12 | 12.5 | Bohren _ Gewindebohren |
3. Anordnung der Verarbeitungsreihenfolge
(1) Bearbeitung
1> Andere Prinzipien nach der ersten Bezugsebene:
Der Verarbeitungsplan verarbeitet immer zuerst die Positionierungsdaten, daher sollten Sie die Vorbereitung des Folgeprozesses als Basis festlegen. Zunächst wird die Referenzebene vervollständigt und der äußere Kreis des Mittellochs und der rotierenden Fläche gedreht.
2> nach dem prinzip der "erste grob und fein"
Zuerst wird der Schruppvorgang angeordnet, gefolgt vom Endbearbeitungsvorgang. Zunächst wird die Hauptfläche hochpräzise angeordnet und anschließend sortiert.
3> Basierend auf dem Prinzip der Priorität und Priorität:
Die Hauptfläche wird zuerst behandelt, beispielsweise die Außenfläche des Außenkreises, die Endfläche und dergleichen. Hilfsflächen nachbearbeiten, z. B. Passfedernuten fräsen.
4> Zuerst außen und dann innen, zuerst großes und kleines Prinzip:
Zuerst wird der äußere Kreis bearbeitet und dann wird das innere Loch durch den äußeren Kreis positioniert. Bei der Bearbeitung eines gestuften Außenkreises wird zuerst der größere Durchmesser und später der kleinere Durchmesser bearbeitet.
5> Sekundäre Oberflächenbehandlungsanordnung:
Die Bearbeitung von Untergründen wie Keilnuten erfolgt typischerweise nach dem zylindrischen Fertigdrehen. Für das rechte Ende der Achse und das mittlere Ende der Achse sollte eine Oberfläche mit höheren Anforderungen an die Bearbeitungsqualität dahinter angeordnet werden.
6> Die rechte Endfläche der Welle ist 64 mm und die mittlere 35 mm. Die Qualität ist höher und die Rückseite ist angeordnet.
7> Prinzip der ersten Seite und des hinteren Lochs:
Zuerst werden die Stirnseiten bearbeitet, dann die Keilnut gefräst und die Gewindelöcher gebohrt.
2) Anordnung des Wärmebehandlungsprozesses
Es wird empfohlen, vor dem Schneiden eine Normalisierung durchzuführen, die die Härte des Schafts erhöhen, die innere Spannung des Rohlings beseitigen und die Schneidleistung verbessern kann. Nach dem Schruppen kann das Abschrecken und Anlassen die Gesamtleistung der Welle verbessern. Die abschließende Wärmebehandlung nach dem Halbfinish verbessert die Materialfestigkeit, Oberflächenhärte und Verschleißfestigkeit.
Nach dem Schruppen und der Wärmebehandlung wird der Richtvorgang angeordnet. Entgratungs- und Zwischenprüfungsverfahren werden nach dem Halbfinish vereinbart. Nach Fertigstellung Entgraten, Reinigen und Endkontrolle veranlassen.
Zusammenfassend ist die Betriebsreihenfolge der Achsen:
Benchmarking_Hauptoberflächenaufrauen_Wärmebehandlung_Halbschlichten der Hauptoberfläche_Bearbeiten der Hauptoberfläche (Schleifen) _Fräsen von Passfedernuten und Gewindebohren_Entgraten, abschließende Wärmebehandlung usw.
4. Bestimmen Sie die technische Route der Welle
Basierend auf der Analyse des obigen Prozesses wird der Prozessweg der Komponente bestimmt, wie in Tabelle 4 gezeigt.
Prozess-ID | Prozessname | Werkzeugmaschinenausstattung | Werkzeug | Messwerkzeug |
01 |
Linke und rechte Stirnfläche grob drehen und 45 ° anfasen
|
CA6140 | 45 ° Messer | Messschieber |
02 | Mittelloch bohren | CA6140 | Wendelbohrer | Bremssattel |
03 | Rauer Außenring | CA6140 | 60° Messer | Messschieber |
04 | Anlassen und Anlassen HRC28 ~ 30 | |||
05 | Halbfertig gedrehter Außenring φ50, φ60, φ64, φ35 | CA6140 | 60°Messer | Messschieber und Messgeräte |
06 | Fein drehender Außenring φ64, φ35 | CA6140 | 60° Messer | Messschieber |
07 | Drehen Sie die 2,2 x 1,5-Steckplätze | CA6140 | Gewöhnliches Einstechmesser | Messschieber |
08 | Passfedernut fräsen | Fräsmaschine X083 | Fräser | Messschieber |
09 | M16, 2-M8-Gewindeloch bohren | Bohrmaschine Z515 | bohren | Messschieber |
10 | Monteur klopfen | Zapfhahn | ||
11 | Entgraten | Handhammer | ||
12 | Endwärmebehandlung (Oberflächenoxidation) und Reinigung | |||
13 | Überprüfen Sie | Caliper Stecker |
5. Bearbeitungszugabe, Bestimmung der Prozessgröße
Um die Bearbeitungsmaße der Zylinderfläche zu bestimmen, beziehen sich die Bearbeitungsmaße der Zylinderfläche für die Mehrfachbearbeitung nur auf die Bearbeitungszugabe. Die Gesamtbearbeitungszugabe (Rohlingsrand) für jede zylindrische Oberfläche wurde zuvor bestimmt, und die Rohlingszugabe sollte in die Bearbeitungszugabe für jeden Prozess unterteilt werden, und dann werden die Prozessabmessungen von hinten nach vorne berechnet. Die Toleranz der Zwischenabmessungen des Prozesses wird durch die wirtschaftliche Genauigkeit der Verarbeitungsmethode bestimmt. Die Prozesstoleranzen, Prozessabmessungen und -toleranzen sowie die Oberflächenrauheit jeder zylindrischen Oberfläche des Teils sind wie folgt:
Tabelle 5 äußere zylindrische Fläche φ50
Berechnung der Bearbeitungszugabe für die Achse
Prozessname | Prozessvolumen / mm | Programm | Grundmaß / mm verarbeiten |
Beschriftungsprozess Maßtoleranz / mm |
|
Wirtschaftliche Genauigkeit / mm | Oberflächenrauheit Ra / μm | ||||
Leer | 10 | ±2 | 0 | 60 | Φ60±2 |
Raues Auto | 9 | IT10 | 12.5 | 51.027 | 51.027 0 +0.12 |
Semi-Finishing-Drehen | 1 | IT7 | 3.2 | 50.027 | Φ50.027 0 +027 |