Spezifische Anwendung von Titan-Legierung Produkte in der Luft- und Raumfahrt
Debüt in flammhemmender Titanlegierung
Um "Titan-Funken" zu vermeiden, hat Russland flammhemmende Titanlegierungen BTT-1 und BTT-3 mit hoher Kapazität entwickelt, die Kupfer enthalten. Aufgrund ihrer schlechten mechanischen Eigenschaften und Gießeigenschaften wurden sie jedoch noch nicht industrialisiert. Die kürzlich in den USA erfundene flammhemmende Titanlegierung aus Alloyc (Ti-35V-15Cr) wurde erfolgreich für das Hochdruckkompressorgehäuse des F119-Motors, der Leitschaufel und der Vektor-Heckdüse (F / A-22-Antriebseinheit) eingesetzt. Dies ist das neueste Highlight auf dem Gebiet der Hochtemperatur-Titanlegierungen und die erste Titanlegierung und flammhemmende Titanlegierung vom Beta-Typ, die in die Geschichte der Titanlegierungen eingegangen ist.Die Legierung hat drei Flammschutzprinzipien:
Erstens weisen Forschungsergebnisse ausländischer und einiger Forschungsinstitute für Luft- und Raumfahrtmaterialien darauf hin. Wenn die Rotorkomponente und die Statorkomponente durch relative Reibung erwärmt werden, dient das erste Schmelzen des V 2 O 5 mit niedrigem Schmelzpunkt (675C) dazu, Wärme zu absorbieren, zu schmieren und die innere Spannung des Oxidfilms zu verringern.
Zweitens zeigen Experimente des Northwest Institute of Nonferrous Metals, dass die Wärmeleitfähigkeit von Legierungen viel höher ist als die von gewöhnlichen Titanlegierungen.
Drittens zeigen die Ergebnisse des Beijing Nonferrous Metals Research Institute unter Verwendung der CALPHAD-Technologie, dass die Zusammensetzung der Legierung die Anforderungen der "adiabatischen Verbrennungstemperatur" so weit wie möglich erfüllt.
Die vom Northwest Institute of Nonferrous Metals und dem Yihang Materials Research Institute gemeinsam entwickelte flammhemmende Titanlegierung Ti-40 für niedrige Temperaturen wurde entwickelt und installiert und wartet auf Tests. Die Verwendung von Metallinfiltrationstechniken zur Bildung von flammhemmenden Oberflächenlegierungen ist ein weiteres relativ kostengünstiges technisches Verfahren.
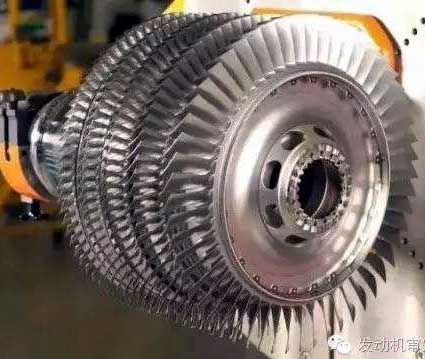
Anfang der Entwicklung von Titanmatrix-Verbundwerkstoffen
Die Welt arbeitet seit vielen Jahren an der Entwicklung von Titan-Verbundwerkstoffen (TMC) und wurde kürzlich für den F119-Motor eingesetzt. Das heißt, der SiC-Faser-Ti-6242S-Verbund wird verwendet, um einen Vektordüsentreiberkolben herzustellen. Vor nicht allzu langer Zeit gab die niederländische Fluggerätentwicklungsfirma SP Aerospace bekannt, dass die Royal Netherlands Air Force die F-16 mit der hinteren Säule des auf Titan basierenden Verbund-Hauptfahrwerks getestet habe. Im Vergleich zum ursprünglichen 300M-Stahl kann das neue Material das Gewicht um 40% reduzieren, und die Kosten liegen nahe an dem Index, den das Design des Jägers kennt. Lockheed Martin beabsichtigt daher, dieses TMC-Material auch für die Herstellung der Fahrwerkskomponenten des gemeinsamen Kampfflugzeugs F-35 zu verwenden. Es wird gesagt, dass die Kosten der Verwendung von TMC anstelle von Ti-6Al-4V-Legierung zur Herstellung von hohlen Lüfterschaufeln mit breiter Sehne geringer sind.
Faser / Titan-Laminat
Zwischenschicht-Hybridmaterialien (in Abbildung 3 dargestellt) stießen auf großes Interesse, da sie eine höhere spezifische Festigkeit und Lebensdauer aufweisen als einzelne Metallmaterialien und viel billiger als faserverstärkte Verbundwerkstoffe sind. Seit den 1980er Jahren wurde dieses Material der ersten Generation von ARALL (Aramidfaser-Aluminiumlegierungslaminat) und der zweiten Generation von GLARE (Glasfaser-Aluminiumlegierungslaminat) unterzogen. Das CARE der dritten Generation (Carbonfaser-Aluminiumlegierungslaminat) wurde für das TiGr der vierten Generation (Graphitfaser-Titanlegierungslaminat) entwickelt.Das vom Yihang Materials Research Institute entwickelte ARALL wurde im Ruder des chinesischen J- 8 II eingesetzt, um das Rissausbreitungsproblem des ursprünglichen Ruderniets aus Aluminiumlegierung zu lösen. GLARE wurde häufig in der A380-Rumpfseitenverkleidung und in Heckflossen verwendet, während TiGr für die Herstellung der B7E7-Tragflächen- und Rumpfhaut verwendet wird. TIGR kann auch in Wabensandwichplatten verwendet werden. Die Praxis hat gezeigt, dass die Leistung des automatisch verlegten TiGr-Laminats der des handverlegten TiGr-Laminats überlegen ist. Bis heute hat CARE keine kommerziellen Produkte, da es schwierig ist, das Problem der Kontaktkorrosion zwischen Kohlefaser und Aluminiumlegierung zu lösen. TiGr weist keine elektrochemischen Korrosionsprobleme auf und kann die Gesamtleistung (insbesondere die spezifische Festigkeit und die Hochtemperaturleistung) weiter verbessern.
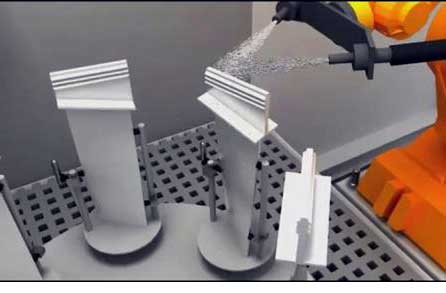
Superplastische Titanlegierung ist einzigartig
Die Überlegenheit fortschrittlicher Technologien wie superplastisches Umformen, isothermes Schmieden und nahezu isothermes Schmieden hat die eigene Entwicklung vorangetrieben. Das Problem des teuren Formenbaus und der Erwärmung durch zu hohe Schmiedetemperaturen wirkt sich jedoch auf die weitere Senkung der Produktkosten und die weitere Anwendung der Prozesstechnologie aus. Daher führte Japan die Legierung SP700 (Ti-4,5Al-3v-2Fe-1Mo) ein. Dies ist die erste Titanlegierung mit SP (Superplastic Abkürzung). Verglichen mit Ti-6Al-4V, superplastisches Formen oder isothermischen Schmieden Temperaturabsenkung 120 ° C (das heißt, von 900 ° C bis 780 ° C), und die Dehnung unter Bedingungen eines optimalen superplastischem verdoppelt (d.h. 1000 %) auf 2000%) erhöht. Im Vergleich zu Ti-6Al-4V weist SP700 auch bessere mechanische Eigenschaften, Wärmebehandlungshärtbarkeit und Kaltverformbarkeit auf. Ein wichtiger Grund, warum SP700 die oben genannten hervorragenden Eigenschaften aufweist, besteht darin, dass SP700 unter den gleichen Prozessbedingungen eine feinere Korngröße von Ti-6Al-4V (2 Mikrometer bzw. 5 Mikrometer) erzielen kann. Daher wurde der SP700 als neue technische Legierung für die Herstellung von Sportartikeln wie Golfschlägern und verstellbaren Schlüsseln verwendet. Es hat auch die Aufmerksamkeit der Luftfahrtgemeinschaft weltweit auf sich gezogen und erwägt die Möglichkeit, es auf Flugzeug- und Triebwerksteile anzuwenden.
Restschallstrahl beim Schmieden von super großen Bauteilen
Um die strukturelle Effizienz zu verbessern, das strukturelle Gewicht zu reduzieren, den Produktionszyklus zu verkürzen und die Produktionskosten zu senken, ist die strukturelle Integration eine wichtige Entwicklungsrichtung für moderne Flugzeuge. Der Rumpfrahmen der F / A-22 weist eine monolithische Struktur auf, die beispiellose große Titanschmiedeteile erfordert, was die Schwierigkeit des Füllens und der Gewebekontrolle erheblich erhöht. Das F / A22-Zwischenprodukt verfügt über vier große einteilige Ti-6Al-4V-Rahmen. Die größten "583" -Rahmenschmiedeteile wiegen 2770 kg und haben eine projizierte Fläche von 5,53 Quadratmetern. Der Motorraumrahmen des hinteren Rumpfes F / A-22 ist ebenfalls groß. Weiman Gordon produziert Gesenkschmiedeteile auf 45.000-Tonnen-Hydraulikpressen. Die Schmiedeteile sind 3,8 Meter lang und 1,7 Meter breit, haben eine projizierte Fläche von 5,2 Quadratmetern und wiegen 1590 Kilogramm. Gemäß der Formschmiedeverformungsbeständigkeit der herkömmlichen Ti-6Al-4V-Legierung ist es unmöglich, eine derart große projizierte Fläche zu schmieden. Die bekannte Situation zeigt, dass das Unternehmen drei Schlüsseltechnologien einsetzt, um die Form und die Mikrostruktur von ultra-großen Titan-Schmiedeteilen sicherzustellen:Verwenden Sie zunächst ein hervorragendes Schmiermittel, um den Widerstand gegen Verformung zu verringern.
Die zweite besteht darin, die Computer-Finite-Elemente-Methode zu verwenden, um die Metallrheologie und die Füllbedingungen im Gesenkschmiedeprozess zu simulieren und den Prozess (einschließlich der Gestaltung der Form und des Vorformlings) zu bestimmen, der die endgültige Form und Größe gewährleisten kann.
Die dritte Aufgabe besteht darin, das Prozessdesign (vom Stanzen bis zum endgültigen Gesenkschmieden) während des gesamten Prozesses durchzuführen, um die strukturellen Eigenschaften des endgültigen Schmiedens sicherzustellen.
Obwohl wir die Schönheit dieses "Konzerts" grob spüren können. Wir verstehen immer noch nicht ganz, warum große Schmiedeteile auf einer 45000-Tonnen-Hydraulikpresse geschmiedet werden können. Wir müssen den Nachhall des Trägers schmecken, um das Geheimnis und andere Möglichkeiten zu erforschen.
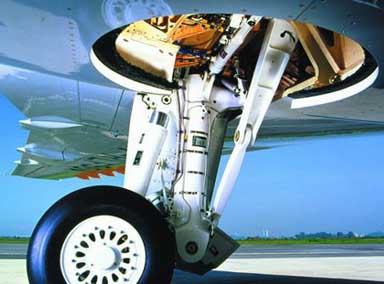
Präzisions-Metall-Gießprozesses wieder eröffnet
Vor langer Zeit wurde die Möglichkeit des Metallgießens (Langzeitgießen) von Titanlegierungen abgelehnt. Die jüngste Praxis von Pratt & Whitney in den USA zeigt jedoch, dass der Metalltyp nicht nur zum Gießen von Titanlegierungen geeignet ist. Darüber hinaus kann es im Vergleich zum Keramiktyp (Schweißdüse) die Kosten um 40% senken, die Umweltverschmutzung verringern, Präzisionsgussteile aus Titanlegierung mit besserer Zugfestigkeit und Ermüdungsfestigkeit erhalten und sogar mit der Leistung von Schmiedeteilen aus Titanlegierung verglichen werden. Pratt & Whitney verwendet Metall-Präzisionsgusstechnologie zur Herstellung flammhemmender Titanlegierungsschaufeln für den vierten und fünften Hochdruckkompressor des F119-Motors. Das Unternehmen beabsichtigt auch, die Möglichkeiten metallischer Präzisionsgussverfahren für die Herstellung von Rotorblättern, einschließlich Lüfterblättern, zu untersuchen.
Der großtechnische strukturelle Gießprozess ist im Aufwind
Titan jüngste Entwicklung der Luftfahrttechnik der schillerndsten „Lichtblick“ ist das Wachsausschmelzverfahren große monolithische Komponenten. Einige moderne Motoren in den USA und in China haben diese Technologie zur Herstellung integraler Gehäuse verwendet. Auffälliger ist: Sechs Arten von großer einheitlicher Struktur, wie beispielsweise die Legierung Ti-6Al-4V hergestellt F / A22 vertikales Ruderstellglied unterstützen und die V22 Kipprotorflugzeug Sitzadapter ist mit diesem neuen Gießvorgang. Nehmen Sie den V-22-Adapter als Beispiel. Es wurde ursprünglich aus 43 Teilen und 536 Verbindungselementen zusammengesetzt. Wenn es einen festen Gußkörper wird, die 32 zusammen aus drei Komponenten und Verbindungselementen zusammengesetzt ist und somit erheblich den Produktionszyklus zu reduzieren (die Verarbeitung und die Installationszeit um 62% reduziert) und reduziert das Strukturgewicht und 30 zu reduzieren, ihre %. Die F / A22 zwei größte Integralgießen ist zwei Linker Ti-6Al-4V, weist einen Flügel auf beiden Seiten des Flügels (Fertiggewichte von 87 kg und 58 kg). Diese Schlüsselkomponenten fett Verwendung von Gussteilen setzen vor allem auf Schlüsseltechnologien und signifikanten Effekt. Drei Schlüsseltechnologien:Eine davon ist eine hochentwickelte und genaue Computersimulationstechnologie.
Die zweite ist die heißisostatische Presstechnologie (einschließlich Großgeräte).
Die dritte ist eine neuartige Beta-Wärmebehandlungstechnologie.
Bemerkenswerte Effekte gleichzeitig erfolgreich werden können, eine präzise Steuerung von großen komplexer Form, Textur und metallurgischer Qualität, Sicherheit und Zuverlässigkeit der zulässigen Spannung entwickelt wird, kann gleichgesetzt und Schmiede- wird.