Optimierung des Spiralfrasprozesses fuer TC4-Titan Legierung Teile mit grossem Durchmesser
Auf Basis der Spiralfrästechnologie wurden die Titanlegierungsteile einem Spiralfrästest mit einem Durchmesser von 19,05 mm unter Verwendung eines Orthogonal-Tests und einer Bereichsanalyse unterzogen. Die Auswirkungen verschiedener Schnittparameter auf die axiale Schnittkraft, die Porengröße und die Rauheit der Titanlegierung wurden analysiert und die optimalen Prozessparameter als Indikatoren optimiert. Auf dieser Grundlage wurden die Schnittkraft, die Bearbeitungsqualität und der Werkzeugverschleiß mit der Anzahl der Löcher unter den optimalen Parametern untersucht. Die Studie ergab, dass bei der Lochbearbeitung mit großem Durchmesser die Spiralfrästechnologie die Verarbeitungsqualität und die Verarbeitungseffizienz wirksam verbessern kann.
Mit der Entwicklung der Luft- und Raumfahrtindustrie wurde die Anwendung von Titanlegierungen immer umfangreicher, und die Anforderungen an die Präzision und Oberflächenqualität beim Bohren von Löchern werden immer höher. Gegenwärtig ist Titanlegierung nicht nur ein unverzichtbarer Metallwerkstoff in der Luft- und Raumfahrtindustrie, sondern auch weit verbreitet in medizinischen Geräten und Werkzeugen, in der Metallurgie, im Schiffbau und in anderen Industrien. Die Titanlegierung weist jedoch eine hohe Festigkeit, eine hohe Härte und eine geringe Wärmeleitfähigkeit auf, und die Schneidwärme kann nicht leicht abgeleitet werden, was zu einem ernsthaften Werkzeugverschleiß führt, der die Lebensdauer des Werkzeugs ernsthaft beeinträchtigt, die Oberflächenqualität beeinträchtigt und den Wirkungsgrad verringert. Die Werkzeugbewegung beim Spiralfräsen besteht aus drei Aspekten: Werkzeugrotation, Rotation und axialer Vorschub. Das Werkzeugzentrum befindet sich in einer spiralförmigen Bahn und ist ein Riemenbohrvorgang, um die Spanabfuhr und die Wärmeableitung zu erleichtern (siehe Abbildung 1). Diese Technologie kann die Axialkraft erheblich reduzieren, die Qualität der Lochherstellung verbessern und die Lochherstellungseffizienz verbessern. Es kann auch leicht "Einheitsgröße" erreicht werden, indem die Exzentrizität eingestellt wird, die von der Luftfahrtindustrie bevorzugt wird.
Basierend auf dem Schneidprinzip untersuchte die Kangding Company die Spezialwerkzeuge für das Laserschneiden und analysierte die Schneidwirkung von Spezialwerkzeugen. Zweidimensionale Finite-Elemente-Simulation von Werkzeugen unter verschiedenen Winkeln. Ein spezielles Werkzeug für das Spiralfräsen wurde entwickelt, um die dynamischen Eigenschaften von Spiralfräslöchern zu untersuchen. E. A. Rahim untersuchte die Wirkung der Klinge auf die Leistung des Fräsers. Jamal Ahnmad wies darauf hin, dass der Rückwinkel des Spiralfräsers einen großen Einfluss auf die Schnittkraft hat. Ein spiralförmiger Spiralfräser, der von Chatelian et al. Hat eine gute Schneidleistung. Das CFK / Ti6Al4V-Verfahren wurde untersucht und die technischen Vorteile großer Fräsmaschinen vorgeschlagen. Li Dengwan optimierte die Verarbeitungsparameter der Titanlegierung durch ein einheitliches Designverfahren und verbesserte die Schnitteffizienz und Oberflächenqualität. Chen Ertao erstellte ein Optimierungsmodell für Bearbeitungsparameter, das auf Schnittparametern basierte. Wang Fengchao untersuchte die Auswirkungen verschiedener Schnittparameter auf Grathöhe, Öffnungsabweichung und Austrittsrauheit.
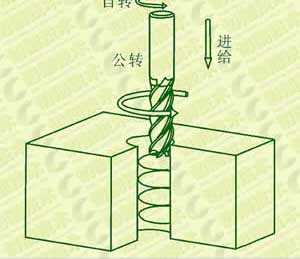
Abbildung 1 Schematische Darstellung des Spiralfräsens der Titanlegierung TC4
Take a 12mm diameter spiral milling cutter as an example. The method of orthogonal milling and extreme value analysis was used to study the 19.05mm (3/4") large diameter spiral milling process of titanium alloy. The influence of different parameters on the processing quality was analyzed, and the optimal processing parameters were optimized. The research is beneficial to promote the application of spiral milling holes in the processing of large diameter holes, and it is also important to improve the efficiency of aircraft assembly and reduce the processing cost.
1. Test equipment and test design
1.1 Prüfmittel und -materialien
Das im Test verwendete Werkzeug war ein Spiralfräser aus unbeschichtetem Hartmetall: Der Durchmesser beträgt 12 mm, die Bearbeitungsöffnung beträgt 19,05 mm, der Spiralwinkel beträgt 35 °, der Spanwinkel beträgt 8 °, der Rückwinkel beträgt 15 ° und die Anzahl der Schneidkanten beträgt 4. Trockenschneiden wird verwendet. Das Testwerkstückmaterial war eine Titanlegierungsplatte mit einer Dicke von 5 mm und einer Größe von 120 × 250 mm. Die physikalischen und mechanischen Eigenschaften der Titanlegierung sind in Tabelle 1 gezeigt.
Maschine. Die Schnittkraft wurde mit einem Dreiwege-Dynamometer Kistler 9257A gemessen. Das erkannte Signal wird vom Ladungsverstärker Kistler 5007A übertragen, von der Datenerfassungskarte erfasst und von der Dynoware Dynamometer-Software in Echtzeit angezeigt. Die Blendendetektion wurde unter Verwendung eines Wenzel LH65-Koordinatenmessgeräts durchgeführt, und für jedes Loch wurden vier Löcher gebohrt, um Blendendaten zu erhalten; Rauheitsmessungen wurden unter Verwendung eines Mitutoyo-Rauheitsprüfers durchgeführt und der Werkzeugverschleiß wurde unter Verwendung eines Ultratiefen Mikroskops beobachtet.
1,2 Ti-6Al-4V Prozessschneidetest Design
Bearbeitung von 3/4 (19,05 mm) Löchern mit einem Werkzeug mit 12 mm großem Durchmesser. Die spezifischen experimentellen Parameter der Drei-Faktor- und Drei-Ebenen-Orthogonal-Tests sind in Tabelle 2 gezeigt. Dabei repräsentiert die Teilung die Abwärtsvorschubstrecke pro Umdrehung des Werkzeugs, und der tangentiale Vorschub jedes Zahns repräsentiert die tangentiale Schnittdicke jeder Schneidkante. In jeder Versuchsreihe wurden zwei Vertiefungen verarbeitet und die gemessenen Parameter gemittelt.
2. Testergebnisse und Analyse
2.1 Einfluss verschiedener Prozessparameter auf die Schnittkraft
Fig. 2 ist eine Variation des fünften Satzes von Schneidparametern, gemessen unter der Bedingung einer kubischen Kurve der Schneidkraft, die als Richtung der z-Achse definiert ist. Aus der Figur ist ersichtlich, dass der Schwankungstrend der Kraft in x-Richtung und der Kraft in y-Richtung derselbe ist und die Axialkraft innerhalb eines bestimmten Bereichs variiert. Die stabile Schneidstufe wurde als effektive Schneidkraft ausgewählt, und die unter jedem Parameter gemessenen Schneidkräfte sind in Tabelle 3 gezeigt.
n = 1800 U / min, Steigung α = 0,25 mm, Tangentialvorschub pro Zahn f = 0,025 mm / z
Bild 2: Schnittkraftsignal über die Zeit gemessen
Abbildung 3. Das Ergebnis der Bereichsanalyse bezieht sich auf die axiale Schnittkraft.
Wie aus der Figur ersichtlich ist, ist die Teilung der Hauptfaktor, der die axiale Schneidkraft des Werkzeugs beeinflusst, gefolgt vom Vorschub pro Zahn in Schneidrichtung. Der minimale Effekt der axialen Schneidkraft ist die Spindeldrehzahl.
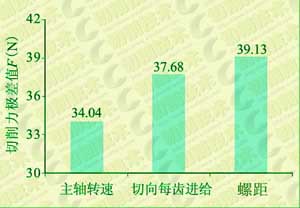
Abbildung 3. Extreme Schnittkraftunterschiede bei Titanlegierungen
Tabelle 3 Testergebnisse für die durchschnittliche axiale Schnittkraft
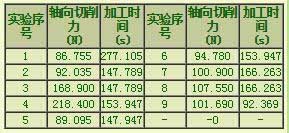
Tabelle 4. Messung der orthogonalen Testapertur
2.2 Einfluss verschiedener Prozessparameter auf die Aperturgenauigkeit
Die Öffnungsgenauigkeit ist einer der wichtigsten Indikatoren für die Porenqualität. Es hat einen wichtigen Einfluss auf die Qualität von Flugzeugbauteilen und die Lebensdauer von Bauteilen: Die Genauigkeit der Lochbearbeitung unter verschiedenen Parametern wird von einem Koordinatenmessgerät untersucht (siehe Tabelle 4).
Anhand der Messergebnisse der Apertur kann geschlossen werden, dass der Toleranzwert der Titanlegierungslochbearbeitung zwischen IT5-IT7 liegt. In der fünften Gruppe haben die Verarbeitungsparameter einen Öffnungsgrad von IT5 und einen minimalen Öffnungsfehler. Der Einfluss von Prozessparametern auf die Porengröße wurde mit dem Entfernungsanalyseverfahren analysiert, und die erhaltenen extremen Unterschiede sind in 4 gezeigt. Spindeldrehzahl und tangentialer Vorschub pro Zahn sind die Hauptfaktoren, die die Blende beeinflussen, und die Steigung wird durch die Blende weniger beeinflusst.
2.3 Einfluss unterschiedlicher Verarbeitungsparameter auf die Rauheit von Titanlegierungsteilen
Die Rauheit ist ein wichtiger Faktor bei der Bewertung der Oberflächenqualität von Ti-6Al-4V.
Für die Montage des Flugzeugs gelten strenge Anforderungen. Die unter verschiedenen Parametern erhaltene Rauheit der Lochwand ist in Tabelle 5 gezeigt.
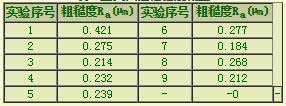
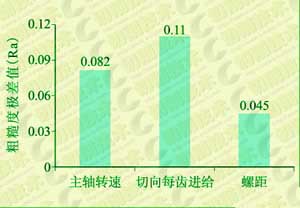
Abb. 5 Extremer Unterschied der Rauheit von Teilen aus Titanlegierung
Wenn beim Spiralfräsen von Titanlegierungsteilen die Rauheit der Öffnungen 0,18 bis 0,42 um beträgt, ist die Wandbeschaffenheit der Löcher ausgezeichnet. Der Einfluss der Verarbeitungsparameter auf die Rauheit wird mit der Entfernungsmethode analysiert, und die erhaltene extreme Differenz ist in Fig. 5 gezeigt. Es ist ersichtlich, dass der wichtigste Faktor, der die Lochwandrauheit beeinflusst, der folgende tangentiale Vorschub pro Zahn ist durch die Spindeldrehzahl und die geringste ist die Steigung.
Zusammenfassend werden die Parameter optimiert, um die axiale Schnittkraft zu verringern, den Öffnungsfehler zu verringern und die Qualität der Lochwand zu verbessern. Die axiale Schnittkraft und der Öffnungsfehler des fünften Satzes von Bearbeitungsparametern sind die kleinsten. Die siebte Gruppe von Parametern weist die kleinste Wandrauheit auf. In Anbetracht dessen, dass der Rauheitswert weit unter dem Flugzeugherstellungsstandard liegt und die Differenz zwischen der fünften Gruppe und der siebten Gruppe nur 0,055 Mikrometer beträgt, wird die fünfte Gruppe von Parametern als optimale Verarbeitungsparameter für Spiralfräslöcher mit großem Durchmesser ausgewählt.
3. Die Variation der Bearbeitungsqualität von Löchern mit großem Durchmesser von Teilen aus Titanlegierung mit der Anzahl der Bearbeitungslöcher
Basierend auf der obigen Analyse wurde die Variation der Schnittkraft, der Bearbeitungsqualität und des Werkzeugverschleißes mit der Anzahl der Bearbeitungslöcher unter den optimalen Bearbeitungsparametern untersucht.
3.1 Änderungen der axialen Schnittkraft
Mit der Entwicklung der Luft- und Raumfahrtindustrie wurde die Anwendung von Titanlegierungen immer umfangreicher, und die Anforderungen an die Präzision und Oberflächenqualität beim Bohren von Löchern werden immer höher. Gegenwärtig ist Titanlegierung nicht nur ein unverzichtbarer Metallwerkstoff in der Luft- und Raumfahrtindustrie, sondern auch weit verbreitet in medizinischen Geräten und Werkzeugen, in der Metallurgie, im Schiffbau und in anderen Industrien. Die Titanlegierung weist jedoch eine hohe Festigkeit, eine hohe Härte und eine geringe Wärmeleitfähigkeit auf, und die Schneidwärme kann nicht leicht abgeleitet werden, was zu einem ernsthaften Werkzeugverschleiß führt, der die Lebensdauer des Werkzeugs ernsthaft beeinträchtigt, die Oberflächenqualität beeinträchtigt und den Wirkungsgrad verringert. Die Werkzeugbewegung beim Spiralfräsen besteht aus drei Aspekten: Werkzeugrotation, Rotation und axialer Vorschub. Das Werkzeugzentrum befindet sich in einer spiralförmigen Bahn und ist ein Riemenbohrvorgang, um die Spanabfuhr und die Wärmeableitung zu erleichtern (siehe Abbildung 1). Diese Technologie kann die Axialkraft erheblich reduzieren, die Qualität der Lochherstellung verbessern und die Lochherstellungseffizienz verbessern. Es kann auch leicht "Einheitsgröße" erreicht werden, indem die Exzentrizität eingestellt wird, die von der Luftfahrtindustrie bevorzugt wird.
Basierend auf dem Schneidprinzip untersuchte die Kangding Company die Spezialwerkzeuge für das Laserschneiden und analysierte die Schneidwirkung von Spezialwerkzeugen. Zweidimensionale Finite-Elemente-Simulation von Werkzeugen unter verschiedenen Winkeln. Ein spezielles Werkzeug für das Spiralfräsen wurde entwickelt, um die dynamischen Eigenschaften von Spiralfräslöchern zu untersuchen. E. A. Rahim untersuchte die Wirkung der Klinge auf die Leistung des Fräsers. Jamal Ahnmad wies darauf hin, dass der Rückwinkel des Spiralfräsers einen großen Einfluss auf die Schnittkraft hat. Ein spiralförmiger Spiralfräser, der von Chatelian et al. Hat eine gute Schneidleistung. Das CFK / Ti6Al4V-Verfahren wurde untersucht und die technischen Vorteile großer Fräsmaschinen vorgeschlagen. Li Dengwan optimierte die Verarbeitungsparameter der Titanlegierung durch ein einheitliches Designverfahren und verbesserte die Schnitteffizienz und Oberflächenqualität. Chen Ertao erstellte ein Optimierungsmodell für Bearbeitungsparameter, das auf Schnittparametern basierte. Wang Fengchao untersuchte die Auswirkungen verschiedener Schnittparameter auf Grathöhe, Öffnungsabweichung und Austrittsrauheit.
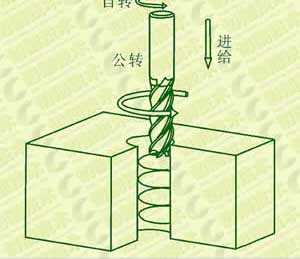
Abbildung 1 Schematische Darstellung des Spiralfräsens der Titanlegierung TC4
In der Flugzeugmontage ist die Anzahl der Löcher mit einem Durchmesser von 1/2 "oder weniger am größten, weshalb sich die Forschung zur Spiralfrästechnologie hauptsächlich hier konzentriert. Es gibt jedoch eine Reihe von Löchern mit großem Durchmesser in kritischen Lagerkomponenten, die sehr schwer zu bearbeiten sind. Derzeit werden bei der Lochbearbeitung mit großem Durchmesser in der Regel mehrere Prozesse wie Bohren, Reiben und Reiben verwendet. Der Prozess ist komplex, erfordert Dutzende von Werkzeugen, hohe Bearbeitungskosten und eine extrem niedrige Bearbeitungseffizienz, was schon immer eine der Schwierigkeiten bei der Flugzeugmontage darstellte.
Take a 12mm diameter spiral milling cutter as an example. The method of orthogonal milling and extreme value analysis was used to study the 19.05mm (3/4") large diameter spiral milling process of titanium alloy. The influence of different parameters on the processing quality was analyzed, and the optimal processing parameters were optimized. The research is beneficial to promote the application of spiral milling holes in the processing of large diameter holes, and it is also important to improve the efficiency of aircraft assembly and reduce the processing cost.
1. Test equipment and test design
Table 1 Physical properties and mechanical properties of titanium alloys
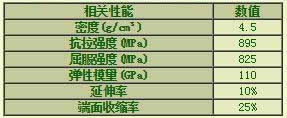
1.1 Prüfmittel und -materialien
Das im Test verwendete Werkzeug war ein Spiralfräser aus unbeschichtetem Hartmetall: Der Durchmesser beträgt 12 mm, die Bearbeitungsöffnung beträgt 19,05 mm, der Spiralwinkel beträgt 35 °, der Spanwinkel beträgt 8 °, der Rückwinkel beträgt 15 ° und die Anzahl der Schneidkanten beträgt 4. Trockenschneiden wird verwendet. Das Testwerkstückmaterial war eine Titanlegierungsplatte mit einer Dicke von 5 mm und einer Größe von 120 × 250 mm. Die physikalischen und mechanischen Eigenschaften der Titanlegierung sind in Tabelle 1 gezeigt.
Maschine. Die Schnittkraft wurde mit einem Dreiwege-Dynamometer Kistler 9257A gemessen. Das erkannte Signal wird vom Ladungsverstärker Kistler 5007A übertragen, von der Datenerfassungskarte erfasst und von der Dynoware Dynamometer-Software in Echtzeit angezeigt. Die Blendendetektion wurde unter Verwendung eines Wenzel LH65-Koordinatenmessgeräts durchgeführt, und für jedes Loch wurden vier Löcher gebohrt, um Blendendaten zu erhalten; Rauheitsmessungen wurden unter Verwendung eines Mitutoyo-Rauheitsprüfers durchgeführt und der Werkzeugverschleiß wurde unter Verwendung eines Ultratiefen Mikroskops beobachtet.
Tabelle 2 Tabelle der orthogonalen Prüfparameter der fünfachsigen DMC75Vlinear-CNC-Werkzeugmaschine
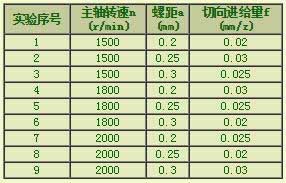
1,2 Ti-6Al-4V Prozessschneidetest Design
Bearbeitung von 3/4 (19,05 mm) Löchern mit einem Werkzeug mit 12 mm großem Durchmesser. Die spezifischen experimentellen Parameter der Drei-Faktor- und Drei-Ebenen-Orthogonal-Tests sind in Tabelle 2 gezeigt. Dabei repräsentiert die Teilung die Abwärtsvorschubstrecke pro Umdrehung des Werkzeugs, und der tangentiale Vorschub jedes Zahns repräsentiert die tangentiale Schnittdicke jeder Schneidkante. In jeder Versuchsreihe wurden zwei Vertiefungen verarbeitet und die gemessenen Parameter gemittelt.
2. Testergebnisse und Analyse
2.1 Einfluss verschiedener Prozessparameter auf die Schnittkraft
Fig. 2 ist eine Variation des fünften Satzes von Schneidparametern, gemessen unter der Bedingung einer kubischen Kurve der Schneidkraft, die als Richtung der z-Achse definiert ist. Aus der Figur ist ersichtlich, dass der Schwankungstrend der Kraft in x-Richtung und der Kraft in y-Richtung derselbe ist und die Axialkraft innerhalb eines bestimmten Bereichs variiert. Die stabile Schneidstufe wurde als effektive Schneidkraft ausgewählt, und die unter jedem Parameter gemessenen Schneidkräfte sind in Tabelle 3 gezeigt.
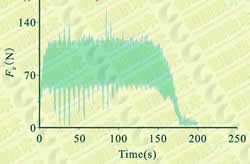
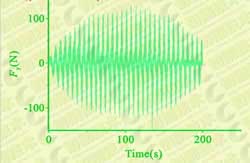
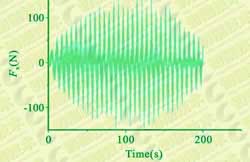
n = 1800 U / min, Steigung α = 0,25 mm, Tangentialvorschub pro Zahn f = 0,025 mm / z
Bild 2: Schnittkraftsignal über die Zeit gemessen
Abbildung 3. Das Ergebnis der Bereichsanalyse bezieht sich auf die axiale Schnittkraft.
Wie aus der Figur ersichtlich ist, ist die Teilung der Hauptfaktor, der die axiale Schneidkraft des Werkzeugs beeinflusst, gefolgt vom Vorschub pro Zahn in Schneidrichtung. Der minimale Effekt der axialen Schneidkraft ist die Spindeldrehzahl.
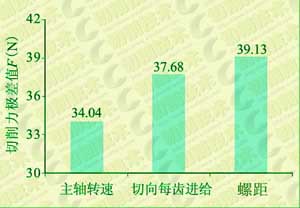
Abbildung 3. Extreme Schnittkraftunterschiede bei Titanlegierungen
Tabelle 3 Testergebnisse für die durchschnittliche axiale Schnittkraft
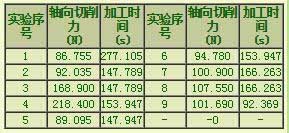
Tabelle 4. Messung der orthogonalen Testapertur
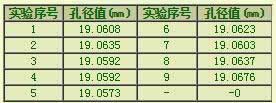
2.2 Einfluss verschiedener Prozessparameter auf die Aperturgenauigkeit
Die Öffnungsgenauigkeit ist einer der wichtigsten Indikatoren für die Porenqualität. Es hat einen wichtigen Einfluss auf die Qualität von Flugzeugbauteilen und die Lebensdauer von Bauteilen: Die Genauigkeit der Lochbearbeitung unter verschiedenen Parametern wird von einem Koordinatenmessgerät untersucht (siehe Tabelle 4).
Anhand der Messergebnisse der Apertur kann geschlossen werden, dass der Toleranzwert der Titanlegierungslochbearbeitung zwischen IT5-IT7 liegt. In der fünften Gruppe haben die Verarbeitungsparameter einen Öffnungsgrad von IT5 und einen minimalen Öffnungsfehler. Der Einfluss von Prozessparametern auf die Porengröße wurde mit dem Entfernungsanalyseverfahren analysiert, und die erhaltenen extremen Unterschiede sind in 4 gezeigt. Spindeldrehzahl und tangentialer Vorschub pro Zahn sind die Hauptfaktoren, die die Blende beeinflussen, und die Steigung wird durch die Blende weniger beeinflusst.
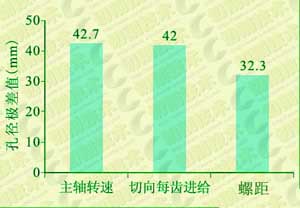
Abb. 4 Extremer Unterschied der Porengröße von Titanlegierungsteilen
2.3 Einfluss unterschiedlicher Verarbeitungsparameter auf die Rauheit von Titanlegierungsteilen
Die Rauheit ist ein wichtiger Faktor bei der Bewertung der Oberflächenqualität von Ti-6Al-4V.
Für die Montage des Flugzeugs gelten strenge Anforderungen. Die unter verschiedenen Parametern erhaltene Rauheit der Lochwand ist in Tabelle 5 gezeigt.
Tabelle 5 Messung der orthogonalen Testrauheit
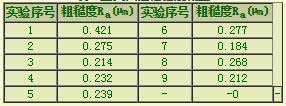
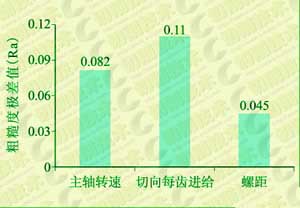
Abb. 5 Extremer Unterschied der Rauheit von Teilen aus Titanlegierung
Zusammenfassend werden die Parameter optimiert, um die axiale Schnittkraft zu verringern, den Öffnungsfehler zu verringern und die Qualität der Lochwand zu verbessern. Die axiale Schnittkraft und der Öffnungsfehler des fünften Satzes von Bearbeitungsparametern sind die kleinsten. Die siebte Gruppe von Parametern weist die kleinste Wandrauheit auf. In Anbetracht dessen, dass der Rauheitswert weit unter dem Flugzeugherstellungsstandard liegt und die Differenz zwischen der fünften Gruppe und der siebten Gruppe nur 0,055 Mikrometer beträgt, wird die fünfte Gruppe von Parametern als optimale Verarbeitungsparameter für Spiralfräslöcher mit großem Durchmesser ausgewählt.
3. Die Variation der Bearbeitungsqualität von Löchern mit großem Durchmesser von Teilen aus Titanlegierung mit der Anzahl der Bearbeitungslöcher
Basierend auf der obigen Analyse wurde die Variation der Schnittkraft, der Bearbeitungsqualität und des Werkzeugverschleißes mit der Anzahl der Bearbeitungslöcher unter den optimalen Bearbeitungsparametern untersucht.
3.1 Änderungen der axialen Schnittkraft