Oberflachenbehandlung von Titan schrauben und Verbindungselementen in verschiedenen Farben
Einleitung: Eigenschaften von Titan und Titanlegierungen, die vor der Oberflächenbehandlung hergestellt wurden. Oberflächenbehandlungstechniken wie chemische Oxidation, Anodisierung, Lichtbogenoxidation, stromloses Plattieren, galvanische Abscheidung, Konversionsfilmbehandlung, elektrochemische Behandlung, elektrophoretische Beschichtung und Nanobehandlung. In Kombination der Anwendungsbeispiele von Titan und Titanlegierung werden die Oberflächenfilmeigenschaften und Anwendungseigenschaften detailliert beschrieben.
Unter Oberflächenbehandlung versteht man das Ausbilden einer Beschichtung auf der Oberfläche eines Werkstücks durch ein Verfahren. Ziel ist es, dem Titanprodukt eine ästhetisch ansprechende Oberfläche und Korrosionsschutzwirkung zu verleihen. Oberflächenbehandlungsmethoden basieren auf den folgenden Methoden:
1, überzug: Die Plattierungsanordnung wird in eine wässrige Lösung getaucht, die die abgeschiedene Metallverbindung enthält, und ein elektrischer Strom wird durch die Plattierungslösung geleitet, um das Plattierungsmetall abzuscheiden und das Plattierungsmetall auf der Anordnung abzuscheiden. Normalerweise umfasst das Galvanisieren: Galvanisieren, Kupfer, Nickel, Chrom, Kupfer-Nickel-Legierung usw., manchmal einschließlich schwarz gekocht (blau), Phosphatieren und dergleichen.
2, Feuerverzinkung: Dies wurde durch Eintauchen des Titanelements in ein geschmolzenes Zinkplattierungsbad bei einer Temperatur von etwa 810 ° C erreicht. Infolgedessen wird die Eisen-Zink-Legierung auf der Oberfläche des Titanelements allmählich zu passiviertem Zink auf der Außenfläche des Produkts.
Das Feueraluminieren ist ein ähnlicher Prozess.
3, mechanische Beschichtung: Die Oberfläche des Produkts wird von metallisierten Partikeln getroffen und die Beschichtung wird kalt mit der Oberfläche des Produkts verschweißt.
4. Sandstrahlen:
Im Allgemeinen wird weißer Korund vorzugsweise zum Strahlen von Titangussteilen verwendet, und der Strahldruck ist niedriger als der von Nichtedelmetallen, der üblicherweise auf 0,45 MPa oder weniger eingestellt wird. Denn wenn der Einspritzdruck zu hoch ist, schlägt der Sand auf die Titanoberfläche auf und erzeugt einen starken Funken, und der Temperaturanstieg reagiert mit der Titanoberfläche, was zu einer sekundären Verschmutzung führt und die Oberflächenqualität beeinträchtigt. Die Zeit beträgt 15 bis 30 Sekunden. Nur der anhaftende Sand, die Sinterschicht und die partielle Oxidschicht auf der Oberfläche des Gussteils können entfernt werden. Die verbleibende Oberflächenstruktur der Reaktionsschicht sollte durch chemisches Beizen schnell entfernt werden.
5. Beizen:
Das Beizen entfernt die Oberflächenreaktionsschicht schnell und gründlich, und die Oberfläche kontaminiert andere Elemente nicht. Zum Beizen von Titan können sowohl HF-HCl- als auch HF-HNO3-Beizlösungen verwendet werden. Die HF-HCl-Säurewäsche weist jedoch eine große Menge an Wasserstoffabsorption auf, während die HF-HNO 3 -Säurewäsche eine kleine Menge an Wasserstoffabsorption aufweist. Es kann die Konzentration von HNO3 steuern, die Absorption von Wasserstoff verringern und die Oberfläche aufhellen. Typischerweise beträgt die Konzentration von HF etwa 3% bis 5% und die Konzentration von HNO 3 etwa 15% bis 30%.
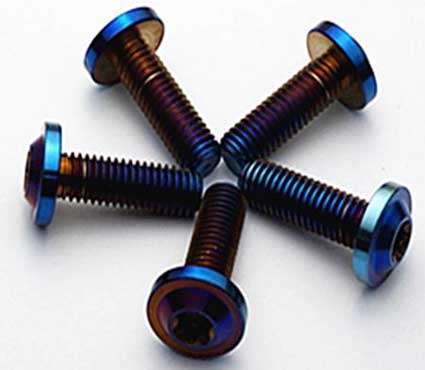
Zweitens, titan oberflächenbehandlung qualitätskontrolle:
Die Beschichtungsqualität wird hauptsächlich an der Korrosionsbeständigkeit gemessen, gefolgt vom Aussehen. Korrosionsbeständigkeit ist eine Arbeitsumgebung, die das Produkt nachahmt, den Testbedingungen entspricht und einem Korrosionstest unterzogen wird. Die Qualität der galvanisierten Produkte wird kontrolliert durch:
1. Aussehen: Die Oberfläche des Titanprodukts darf keine partielle Beschichtung, Brennen, Rauheit, Grau, Abblättern, Schalenbeschaffenheit und deutliche Streifen aufweisen. Lochfraß, schwarze Schlacke, lockerer Passivierungsfilm, Risse, Abplatzungen und starke Passivierung sind nicht zulässig.
2, Überzugstärke: Die Lebensdauer von Verbindungselementen in korrosiver Umgebung ist proportional zur Dicke der Beschichtung. Die empfohlene wirtschaftliche Schichtdicke beträgt 0,00015 bis 0,0005 Zoll (4 bis 12 um).
Feuerverzinkung: Die durchschnittliche Standarddicke beträgt 54 Mikrometer (Nenndurchmesser ≤ 3/8 beträgt 43 Mikrometer) und die Mindestdicke beträgt 43 Mikrometer (Nenndurchmesser ≤ 3/8 beträgt 37 Mikrometer).
3. Plating Verteilung: Das Muster der Aggregation der Beschichtung auf der Oberfläche des Befestigungselements unterscheidet sich auch unter Verwendung verschiedener Abscheidungsverfahren. Während des Galvanisierens wird das plattierte Metall ungleichmäßig auf der Umfangskante abgeschieden und an den Ecken wird eine dickere Beschichtung erhalten. Im Gewindeabschnitt des Befestigungselements befindet sich die dickste Beschichtung am oberen Ende des Gewindes, verjüngt sich entlang der Seiten des Gewindes und lagert die dünnste Beschichtung am unteren Ende des Zahns ab. Feuerverzinkung ist genau das Gegenteil. Eine dickere Beschichtung wird auf der Innen- und Unterseite des Fadens aufgebracht. Mechanisch plattierte elektroplattierte Metalle neigen dazu, sich als Heißtauchbeschichtungen abzuscheiden, sind jedoch glatter und gleichmäßiger über die gesamte Oberfläche.
4, Wasserstoffversprödung:
Bei der Verarbeitung und Handhabung von Verbindungselementen, insbesondere beim Beizen und Ätzen vor dem Galvanisieren und anschließenden Galvanisieren, nimmt die Oberfläche Wasserstoffatome auf und die abgeschiedene Metallbeschichtung nimmt dann Wasserstoff auf. Wenn das Befestigungselement angezogen wird, wird Wasserstoff auf den am stärksten konzentrierten Teil der Beanspruchung übertragen, wodurch der Druck über die Festigkeit des Grundmetalls hinaus ansteigt und ein geringfügiger Oberflächenriss verursacht wird. Wasserstoff ist besonders aktiv und dringt schnell in neu gebildete Risse ein. Dieser Druckbruch - der Permeationszyklus setzt sich fort, bis das Befestigungselement bricht. Sie tritt normalerweise innerhalb weniger Stunden nach dem ersten Druck auf.
Um die Gefahr der Wasserstoffversprödung auszuschließen, werden die Verbindungselemente nach dem Plattieren so schnell wie möglich erhitzt und eingebrannt, damit Wasserstoff aus der Beschichtung austreten kann. Das Backen wird typischerweise 3–24 Stunden lang bei 375–4000 ° F (176–190 ° C) durchgeführt.
Da die mechanische Verzinkung nicht elektrolytisch ist, ist die Gefahr der Wasserstoffversprödung praktisch ausgeschlossen. Darüber hinaus ist aufgrund technischer Standards das Feuerverzinken von Verbindungselementen mit einer höheren Härte als HRC35 (Zoll Gr8, metrisch 10,9 oder höher) verboten. Daher sind feuerverzinkte Verbindungselemente selten einer Wasserstoffversprödung ausgesetzt.
Unter Oberflächenbehandlung versteht man das Ausbilden einer Beschichtung auf der Oberfläche eines Werkstücks durch ein Verfahren. Ziel ist es, dem Titanprodukt eine ästhetisch ansprechende Oberfläche und Korrosionsschutzwirkung zu verleihen. Oberflächenbehandlungsmethoden basieren auf den folgenden Methoden:
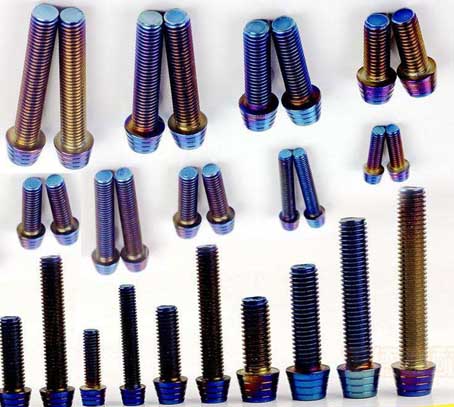
2, Feuerverzinkung: Dies wurde durch Eintauchen des Titanelements in ein geschmolzenes Zinkplattierungsbad bei einer Temperatur von etwa 810 ° C erreicht. Infolgedessen wird die Eisen-Zink-Legierung auf der Oberfläche des Titanelements allmählich zu passiviertem Zink auf der Außenfläche des Produkts.
Das Feueraluminieren ist ein ähnlicher Prozess.
3, mechanische Beschichtung: Die Oberfläche des Produkts wird von metallisierten Partikeln getroffen und die Beschichtung wird kalt mit der Oberfläche des Produkts verschweißt.
4. Sandstrahlen:
Im Allgemeinen wird weißer Korund vorzugsweise zum Strahlen von Titangussteilen verwendet, und der Strahldruck ist niedriger als der von Nichtedelmetallen, der üblicherweise auf 0,45 MPa oder weniger eingestellt wird. Denn wenn der Einspritzdruck zu hoch ist, schlägt der Sand auf die Titanoberfläche auf und erzeugt einen starken Funken, und der Temperaturanstieg reagiert mit der Titanoberfläche, was zu einer sekundären Verschmutzung führt und die Oberflächenqualität beeinträchtigt. Die Zeit beträgt 15 bis 30 Sekunden. Nur der anhaftende Sand, die Sinterschicht und die partielle Oxidschicht auf der Oberfläche des Gussteils können entfernt werden. Die verbleibende Oberflächenstruktur der Reaktionsschicht sollte durch chemisches Beizen schnell entfernt werden.
5. Beizen:
Das Beizen entfernt die Oberflächenreaktionsschicht schnell und gründlich, und die Oberfläche kontaminiert andere Elemente nicht. Zum Beizen von Titan können sowohl HF-HCl- als auch HF-HNO3-Beizlösungen verwendet werden. Die HF-HCl-Säurewäsche weist jedoch eine große Menge an Wasserstoffabsorption auf, während die HF-HNO 3 -Säurewäsche eine kleine Menge an Wasserstoffabsorption aufweist. Es kann die Konzentration von HNO3 steuern, die Absorption von Wasserstoff verringern und die Oberfläche aufhellen. Typischerweise beträgt die Konzentration von HF etwa 3% bis 5% und die Konzentration von HNO 3 etwa 15% bis 30%.
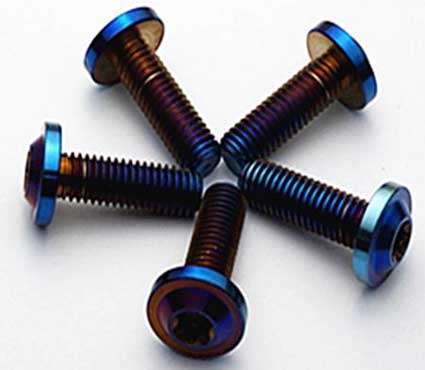
Zweitens, titan oberflächenbehandlung qualitätskontrolle:
Die Beschichtungsqualität wird hauptsächlich an der Korrosionsbeständigkeit gemessen, gefolgt vom Aussehen. Korrosionsbeständigkeit ist eine Arbeitsumgebung, die das Produkt nachahmt, den Testbedingungen entspricht und einem Korrosionstest unterzogen wird. Die Qualität der galvanisierten Produkte wird kontrolliert durch:
1. Aussehen: Die Oberfläche des Titanprodukts darf keine partielle Beschichtung, Brennen, Rauheit, Grau, Abblättern, Schalenbeschaffenheit und deutliche Streifen aufweisen. Lochfraß, schwarze Schlacke, lockerer Passivierungsfilm, Risse, Abplatzungen und starke Passivierung sind nicht zulässig.
2, Überzugstärke: Die Lebensdauer von Verbindungselementen in korrosiver Umgebung ist proportional zur Dicke der Beschichtung. Die empfohlene wirtschaftliche Schichtdicke beträgt 0,00015 bis 0,0005 Zoll (4 bis 12 um).
Feuerverzinkung: Die durchschnittliche Standarddicke beträgt 54 Mikrometer (Nenndurchmesser ≤ 3/8 beträgt 43 Mikrometer) und die Mindestdicke beträgt 43 Mikrometer (Nenndurchmesser ≤ 3/8 beträgt 37 Mikrometer).
3. Plating Verteilung: Das Muster der Aggregation der Beschichtung auf der Oberfläche des Befestigungselements unterscheidet sich auch unter Verwendung verschiedener Abscheidungsverfahren. Während des Galvanisierens wird das plattierte Metall ungleichmäßig auf der Umfangskante abgeschieden und an den Ecken wird eine dickere Beschichtung erhalten. Im Gewindeabschnitt des Befestigungselements befindet sich die dickste Beschichtung am oberen Ende des Gewindes, verjüngt sich entlang der Seiten des Gewindes und lagert die dünnste Beschichtung am unteren Ende des Zahns ab. Feuerverzinkung ist genau das Gegenteil. Eine dickere Beschichtung wird auf der Innen- und Unterseite des Fadens aufgebracht. Mechanisch plattierte elektroplattierte Metalle neigen dazu, sich als Heißtauchbeschichtungen abzuscheiden, sind jedoch glatter und gleichmäßiger über die gesamte Oberfläche.
4, Wasserstoffversprödung:
Bei der Verarbeitung und Handhabung von Verbindungselementen, insbesondere beim Beizen und Ätzen vor dem Galvanisieren und anschließenden Galvanisieren, nimmt die Oberfläche Wasserstoffatome auf und die abgeschiedene Metallbeschichtung nimmt dann Wasserstoff auf. Wenn das Befestigungselement angezogen wird, wird Wasserstoff auf den am stärksten konzentrierten Teil der Beanspruchung übertragen, wodurch der Druck über die Festigkeit des Grundmetalls hinaus ansteigt und ein geringfügiger Oberflächenriss verursacht wird. Wasserstoff ist besonders aktiv und dringt schnell in neu gebildete Risse ein. Dieser Druckbruch - der Permeationszyklus setzt sich fort, bis das Befestigungselement bricht. Sie tritt normalerweise innerhalb weniger Stunden nach dem ersten Druck auf.
Um die Gefahr der Wasserstoffversprödung auszuschließen, werden die Verbindungselemente nach dem Plattieren so schnell wie möglich erhitzt und eingebrannt, damit Wasserstoff aus der Beschichtung austreten kann. Das Backen wird typischerweise 3–24 Stunden lang bei 375–4000 ° F (176–190 ° C) durchgeführt.
Da die mechanische Verzinkung nicht elektrolytisch ist, ist die Gefahr der Wasserstoffversprödung praktisch ausgeschlossen. Darüber hinaus ist aufgrund technischer Standards das Feuerverzinken von Verbindungselementen mit einer höheren Härte als HRC35 (Zoll Gr8, metrisch 10,9 oder höher) verboten. Daher sind feuerverzinkte Verbindungselemente selten einer Wasserstoffversprödung ausgesetzt.