Herstellung Technologie von Stanzwerkzeug
Bevor wir die Herstellung technologie von Stanzwerkzeugen analysieren, müssen wir zunächst die Zusammensetzung von Stanzwerkzeug komponenten verstehen.
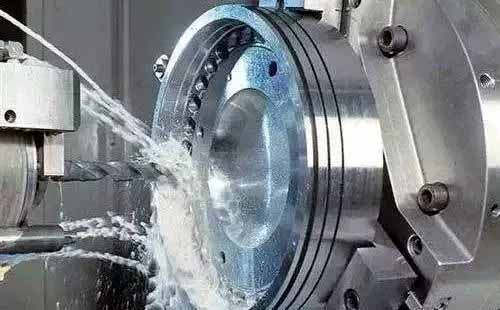
Typ 1
Prozessteile von Stanzwerkzeugen, diese Teile nehmen direkt an der Fertigstellung des Prozesses teil und haben direkten Kontakt mit den Stanzrohlingen. Einschließlich Arbeitsteile, Positionierteile, Entlade- und Pressteile usw.;
Typ 2
Die Strukturteile des Stanzwerkzeugs, solche Teile sind nicht direkt an der Fertigstellung des Prozesses beteiligt und haben auch keinen direkten Kontakt mit dem Rohling. Sie garantiert lediglich den Abschluss des Formprozesses oder verbessert die Funktion der Form. Einschließlich Führungsteile, Befestigungsteile, Normteile und sonstige Teile, wie in Tabelle 1.1.3 dargestellt. Es ist darauf hinzuweisen, dass nicht alle Stanzwerkzeuge die oben genannten sechs Teile aufweisen müssen, insbesondere Einprozess-Stanzwerkzeuge, sondern Arbeitsteile und notwendige Festteile sind unverzichtbar.
Fertigungstechnologie Stanzwerkzeug
Die Modernisierung der Stanzwerkzeug bautechnik ist die Basis für die Entwicklung der Werkzeugindustrie. Mit der Entwicklung von Wissenschaft und Technologie infiltrieren, überschneiden und verschmelzen fortschrittliche Technologien wie Computer technologie, Information technologie und Automatisierung technologie ständig in traditionelle Fertigungstechnologien, transformieren sie und bilden fortschrittliche Fertigungstechnologien. So hat beispielsweise die neue Stanzwerkzeug-Gewindetechnologie viele Stanzhersteller zu Kostensenkungen und einen panischen Kaufboom geführt.Die Entwicklung fortschrittlicher Fertigungstechnologien für Stanzwerkzeuge spiegelt sich hauptsächlich in:
Hochgeschwindigkeitsfräsen
Gewöhnliches Fräsen verwendet einen niedrigen Vorschub und eine große Schnittmenge, während das Hochgeschwindigkeitsfräsen einen hohen Vorschub und eine geringe Schnittmenge verwendet. Im Vergleich zum normalen Fräsen weist das Hochgeschwindigkeitsfräsen folgende Eigenschaften auf:
A. Hohe Effizienz: Die Spindeldrehzahl beim Hochgeschwindigkeitsfräsen beträgt im Allgemeinen 15.000 U / min~40.000 U / min, bis zu 100.000 U / min. Beim Fräsen von Stahl beträgt die Schnittgeschwindigkeit etwa 400 m / min, was 5-10 mal höher ist als bei der herkömmlichen Fräsbearbeitung; Im Vergleich zu herkömmlichen Bearbeitung methoden (traditionelles Fräsen, Erodieren usw.) wird die Effizienz der Bearbeitung von Formkavitäten um das 4- bis 5-fache gesteigert.
B. Hohe Präzision: Die Präzision beim Hochgeschwindigkeitsfräsen beträgt im Allgemeinen 10 μm, und einige Genauigkeiten sind sogar noch höher.
C. Hohe Oberflächenqualität: Aufgrund des geringen Temperaturanstiegs des Werkstücks beim Hochgeschwindigkeitsfräsen (ca. 3°C) gibt es keine metamorphe Schicht und Mikrorisse auf der Oberfläche, und auch die thermische Verformung ist gering. Die beste Oberflächenrauheit Ra liegt unter 1μm, was den Arbeitsaufwand beim anschließenden Schleifen und Polieren reduziert.
D. Hochharte Materialien können Bearbeitung werden: Es kann 50-54HRC-Stahl fräsen und die höchste Fräshärte kann 60HRC erreichen.
Angesichts der oben erwähnten Vorteile des Hochgeschwindigkeitsfräsens wird die Hochgeschwindigkeitsbearbeitung in großem Umfang im Formenbau verwendet und ersetzt allmählich einen Teil des Schleifens und des elektrischen Funkens.
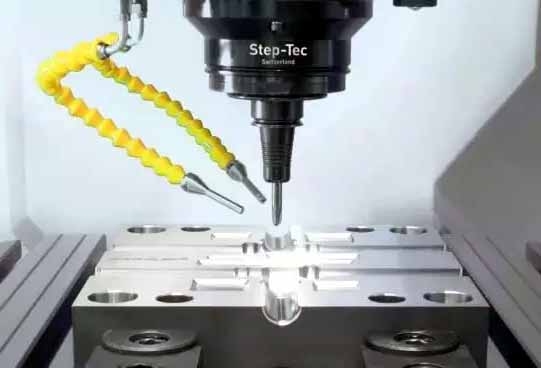
Erodier bearbeitung
Das EDM-Fräsen (auch als EDM-Generatives Bearbeiten bekannt) ist eine wichtige Entwicklung der EDM-Technologie, einer neuen Technologie, die die traditionelle Verwendung von Umformelektroden zur Bearbeitung von Formhohlräumen ersetzt. Ähnlich wie beim CNC-Fräsen verwendet EDM eine schnell rotierende Stabelektrode, um eine zweidimensionale oder dreidimensionale Kontur bearbeitung des Werkstücks durchzuführen, ohne dass komplexe und teure Formelektroden hergestellt werden müssen. Die von der japanischen Mitsubishi Corporation entwickelte Erodier maschine EDSCAN8E ist mit einem automatischen Compensation system für Elektrodenverlust und einem integrierten CAD/CAM-System ausgestattet. Das automatische Online-Mess system und das dynamische Simulation system spiegeln das Niveau heutiger Erodier maschinen wider.Langsame Drahtschneide technologie
Der Entwicklungsstand der CNC-Langsam drahterodiertechnik ist recht hoch, die Funktionen sind recht vollständig und der Automatisierungsgrad hat das Niveau des unbeaufsichtigten Betriebs erreicht. Die maximale Schnittgeschwindigkeit hat 300 mm2/min erreicht, die Bearbeitungsgenauigkeit kann ±1,5 μm erreichen und die Bearbeitung oberflächenrauheit Ra0,1~0,2μm. Die Entwicklung der Dünndraht chneidtechnologie mit einem Durchmesser von 0,03~0,1 mm kann das einmalige Schneiden von konkaven und konvexen Formen realisieren. Sie kann auch schmale Nuten von 0,04 mm und Innenrundungen mit einem Radius von 0,02 mm schneiden. Die Kegelschnitt technologie ist in der Lage, Kegel über 30° präzise zu bearbeiten.Schleif- und Polier bearbeitungstechnik:
Schleif- und Polierprozesse zeichnen sich durch hohe Präzision, gute Oberflächengüte und niedrige Oberflächenrauheitswerte aus. Es wird häufig in der Präzisionsform verarbeitung verwendet. Bei der Herstellung von Präzision formen werden in großem Umfang fortschrittliche Geräte und Technologien wie CNC-Formschleif maschinen, optische CNC-Kurvenschleif maschinen, CNC-Koordinatenschleif maschinen mit kontinuierlicher Spur und automatische Poliermaschinen verwendet.CNC-Messung
Die Komplexität der Produkt struktur führt unweigerlich zu einer Komplexität der Formgebung der Formteile. Herkömmliche geometrische Prüfmethoden können sich nicht mehr an die Herstellung von Formen anpassen. Der moderne Formenbau hat in großem Umfang Drei-Koordinaten-Messmaschine mit numerischer Steuerung verwendet, um die geometrischen Größen von Formteilen zu messen, und auch die Erkennung verfahren der Formen bearbeitung haben große Fortschritte gemacht. Neben der Drei-Koordinaten-CNC-Messmaschine kann sie die Daten komplexer gekrümmter Oberflächen mit hoher Präzision messen. Seine gute Temperatur kompensation, zuverlässiger Schwingungsschutz, strenge Staubentfernung maßnahmen und einfache Bedienschritte ermöglichen eine automatische Erkennung vor Ort.Die Anwendung fortschrittlicher Formenbau technologie hat die traditionelle Formenbau technologie verändert: Die Qualität hängt von menschlichen Faktoren und schwer zu kontrollierenden Bedingungen ab. Die Schimmelqualität hängt von physikalischen und chemischen Faktoren ab, das Gesamtniveau ist leicht zu kontrollieren und die Fähigkeit zur Schimmel produktion ist stark.
Hochfester Stahl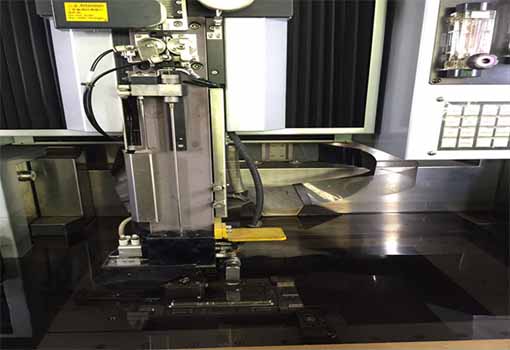
Stanzwerkzeug aus hochfestem StahlDie heutigen hochfesten Stähle und ultrahochfesten Stähle haben das Leichtgewicht von Fahrzeugen erreicht und die Kollision festigkeit und Sicherheitsleistung von Fahrzeugen verbessert, sodass sie zu einer wichtigen Entwicklungsrichtung von Automobilstahl geworden sind. Mit zunehmender Festigkeit der Bleche neigt das traditionelle Kaltumformverfahren jedoch zu Rissbildungen während des Umformprozesses, die den Verarbeitungsanforderungen hochfester Stahlbleche nicht gerecht werden können. Unter der Bedingung, dass die Umformbedingungen nicht eingehalten werden können, wurde die Warm umformtechnologie von ultrahochfesten Stahlblechen sukzessive international untersucht. Bei dieser Technologie handelt es sich um ein neues Verfahren, das Umformung, Wärmeübertragung und Strukturp hasenumwandlung integriert und hauptsächlich die Eigenschaften einer erhöhten Plastizität von Blechen und einer verringerten Streckgrenze im Zustand von Hoch temperatur austenit sowie den Prozess der Umformung durch Formen nutzt. Das Thermoformen erfordert jedoch eine eingehende Untersuchung der Prozessbedingungen, des Metall phasenübergangs und der CAE-Analyse technologie Diese Technologie wird von ausländischen Herstellern monopolisiert und hat eine langsame Entwicklung im Inland.
Früher glaubte jeder beim Ziehen oder Umstanzen von Werkstücken, dass EP-Schmierstoffe die beste Wahl für den Werkzeugschutz seien. Schwefel- und Chlor-EP-Additive wurden in reines Öl eingemischt, um die Lebensdauer der Form zu verlängern. Mit dem Aufkommen eines neuen Metalls – hochfester Stahl und strenge Umweltschutzauflagen – hat der Wert von Schmierstoffen auf EP-Ölbasis jedoch abgenommen und sogar den Markt verloren.
Beim Formen von hochfestem Stahl bei hohen Temperaturen verlieren Schmierstoffe auf EP-Ölbasis ihre Leistung und können bei extremen Temperatur anwendungen keine physikalische Form schutzmembran bieten. Das IRMCO High Solid Polymer-Schmiermittel für extreme Temperaturen kann den notwendigen Schutz bieten. Wenn sich das Metall im Stanzwerkzeug verformt und die Temperatur weiter ansteigt, wird der Schmierstoff auf EP-Ölbasis dünner und erreicht in einigen Fällen den Flammpunkt oder brennt (Rauch). IRMCO Polymer schmierstoffe haben beim Aufsprühen in der Regel eine deutlich geringere Konsistenz. Mit steigender Temperatur während des Umformprozesses wird es dicker und zäher. Tatsächlich haben hochmolekulare Polymer-Schmiermittel für extreme Temperaturen "Wärmesuche" und haften am Metall, wodurch eine Membran gebildet wird, die die Reibung reduzieren kann. Diese Schutzbarriere kann es dem Werkstück ermöglichen, sich ohne Risse und Verklebungen auszudehnen, wenn das anspruchsvollste Werkstück geformt wird, wodurch Reibung und Metallfluss kontrolliert werden. Es schützt die Form effektiv, verlängert die Lebensdauer der Form und verbessert die Stanzfestigkeit.