Tecnología de mecanizado de piezas de disco de metal
En el mecanizado CNC, ya sea programación manual o automática, analice el proceso de las piezas mecanizadas antes de programar, formule el plan de proceso, seleccione la herramienta adecuada y determine la cantidad de corte. En la programación, también es necesario tratar algunos problemas de proceso (como el punto de ajuste de la herramienta, la ruta de procesamiento, etc.). Por lo tanto, el proceso de programación NC es una tarea muy importante. El objetivo principal de este documento es analizar el proceso de procesamiento de piezas de discos metálicos. Incluye principalmente selección en blanco, selección de referencia, secuencia de procesamiento, método de sujeción, procesamiento de superficie, selección de parámetros y ruta de proceso.
1. El proceso general del diseño del proceso de mecanizado CNC
(1) Seleccione la máquina herramienta CNC adecuada para mecanizar la pieza y determine el contenido del proceso.
(2) Analice los dibujos de piezas mecanizadas, aclare el contenido de procesamiento y los requisitos técnicos, determine el plan de procesamiento y desarrolle la ruta de mecanizado CNC. Tales como la división del proceso, la disposición de la secuencia de procesamiento, la conexión de procesos de mecanizado no CNC, etc. Diseñe procesos de mecanizado CNC, como la división de procesos, la selección de herramientas, el posicionamiento e instalación de accesorios, la determinación de la cantidad de corte, la determinación de la ruta de la cortadora, etc. Debido a la variedad de partes y los contornos y formas de las partes, el material y el tamaño de los espacios en blanco no son los mismos.
Por lo tanto, el diseño del proceso en el mecanizado CNC determina la eficiencia de uso de las máquinas herramienta CNC, la calidad del mecanizado de piezas, el número de herramientas y la economía. Debemos tratar de garantizar un paso de mecanizado centralizado, la ruta más corta y el tiempo de proceso auxiliar de la máquina minimizado.
2. Análisis de la tecnología de mecanizado de piezas de disco.
(1) Selección de materiales de mecanizado. Piezas de disco principalmente de acero, hierro fundido, acero inoxidable, aluminio, latón, bronce o similares como la materia prima principal. Las varillas laminadas en caliente o estiradas en frío generalmente se usan para discos de diámetro pequeño. Diferentes materiales pueden elegir fundición sólida. Se puede usar un agujero previo cuando la abertura es grande. Si se produce en masa, la extrusión en frío opcional y otros procesos de fabricación en blanco avanzados, no solo pueden mejorar la productividad, también pueden ahorrar material.
(2) Selección de estándares de mecanizado.
De acuerdo con las características de las partes, el principio de superposición estándar y evaluación comparativa debe cumplirse tanto como sea posible. La base para la selección suele ser la cara final, el orificio interno y el círculo externo. Cuando la cara final se usa como referencia para las partes del disco, el plano generalmente se usa como referencia. Cuando las partes del disco se basan en el orificio interno, la cara final generalmente es asistida por la cara final; El método de referencia del círculo externo es básicamente el mismo que la selección de referencia con el orificio interno.
(3) Disposición del proceso
Las partes de disco típicas consisten típicamente en caras extremas, agujeros y caras externas (algunas también incluyen agujeros escalonados), y las partes de disco se caracterizan por una dimensión radial mayor que la dimensión axial. Busque la fábrica de piezas de disco Kang Ding, garantía de calidad. Para las piezas de disco, no solo hay requisitos dimensionales, sino también requisitos de rugosidad de la superficie, que generalmente incluyen requisitos de desviación radial, desviación redonda y verticalidad. El redondeo y el redondeo de la cara final son las consideraciones clave al formular el proceso de mecanizado de las piezas del disco. Después de terminar, el círculo exterior, el orificio y la cara final deben terminarse en un proceso de sujeción para evitar una segunda sujeción. Para las piezas que deben sujetarse varias veces, los agujeros se mecanizan primero, y luego el círculo exterior o la cara final se mecanizan a través de los agujeros.
(4) Selección y uso de accesorios.
El mandril universal de tres mordazas se utiliza para sujetar las piezas de trabajo de pequeñas piezas de disco. El mandril de cuatro mordazas o la placa frontal son adecuados para sujetar piezas de disco medianas y grandes. Para la precisión de la posición tangencial, generalmente se procesa sujetando con un mandril o una placa frontal. Cuando el estándar de posicionamiento de las partes del disco es el orificio mecanizado, para garantizar la coaxialidad del eje del círculo exterior y el eje del orificio, se utiliza el método de mandril para sujetar las partes. También hay muchos tipos de mandriles. Mandril cilíndrico o pequeño mandril cónico, adecuado para posicionamiento con agujeros cilíndricos; Y esos agujeros especiales como los agujeros cónicos y los agujeros de rosca adoptan los conos y mandriles de rosca correspondientes. El mandril cilíndrico sujeta las piezas centrando la superficie cilíndrica exterior y presionando la superficie del extremo. Se utiliza un ajuste libre entre el mandril y el orificio parcial.
Para mejorar la precisión de posicionamiento del huso, a veces el huso se procesa en un pequeño cuerpo vertebral cónico. También hay un disco de fijación común para piezas de funda de disco grandes. El disco está montado en el disco grande del eje del torno. En general, es adecuado para piezas de trabajo de forma irregular, y no se puede utilizar cuando la sujeción general del mandril. Al usar el disco para sujetar la pieza de trabajo, debe estar equilibrado, de lo contrario se generará una fuerza centrífuga, que eventualmente causará vibración y provocará el desgaste del rodamiento del husillo.
(5) Mecanizado de la superficie acabada de las piezas del disco.
Para la superficie giratoria de las partes del disco, el desbaste se realiza girando. Para el acabado, se debe tener más en cuenta el material, los requisitos de mecanizado y la producción para seleccionar métodos de mecanizado, como el torneado de acabado, el acabado de acabado, el rectificado de acabado, etc. Para la superficie no giratoria de las piezas del disco, se pueden utilizar los métodos de mecanizado correspondientes, fresado, electroerosión, etc.
(6) Determinación de los parámetros de corte.
Cuando el programador elige la cantidad de corte, debe considerar completamente varios factores que afectan el corte, seleccionar correctamente las condiciones de corte y determinar razonablemente la cantidad de corte, lo que puede mejorar efectivamente la calidad y eficiencia del mecanizado. Los factores que afectan las condiciones de corte son:
> rigidez de máquina, herramienta y pieza de trabajo;
> velocidad de corte, profundidad de corte, velocidad de avance de corte;
> precisión y rugosidad de la superficie de la pieza de trabajo;
> máxima vida útil de la herramienta y productividad;
> tipos de fluido de corte, método de enfriamiento;
> dureza del tratamiento térmico del material de la pieza de trabajo;
> número de piezas de trabajo;
> vida de la máquina.
Entre los factores anteriores, la velocidad de avance, la velocidad de corte y la profundidad de corte son los factores principales. Analice principalmente estos puntos:
A, la elección de la velocidad de alimentación
Cada revolución de la pieza de trabajo, la distancia que la herramienta se mueve en la dirección de desplazamiento se denomina cantidad de alimentación, y la unidad es mm / r. En teoría, al desbastar, es la alimentación máxima del mecanismo. La velocidad de alimentación está limitada por el tamaño de algunos de los siguientes factores: Resistencia y rigidez de las máquinas herramienta, vástagos, cuchillas, accesorios. El acabado está limitado principalmente por la precisión del mecanizado y la rugosidad de la superficie, y la cantidad de alimentación se selecciona en combinación con el material de la pieza de trabajo, el radio de la punta de la herramienta y la velocidad de corte.
B, la elección de la velocidad de corte
La velocidad lineal del movimiento principal se llama velocidad de corte y su unidad es III / so III / min. En la producción real, la velocidad de corte generalmente se selecciona en función de la experiencia, y la velocidad de corte más baja generalmente se selecciona para desbaste. Además, es necesario considerar exhaustivamente las propiedades de procesamiento del material, el rendimiento de corte de la herramienta, las condiciones de trabajo y otros factores para determinar razonablemente la velocidad de corte óptima. Relacionado con la velocidad de la máquina, y hay una fórmula de conversión de cálculo:
n = 1000v / dII
Fórmula donde: d es el diámetro de la pieza de trabajo, la velocidad seleccionada n debe estar dentro del rango de la velocidad de rotación del torno.Los parámetros de procesamiento apropiados se seleccionan por experiencia o la fórmula de cálculo anterior.
(7) Formular rutas de mecanizado.
La mayor diferencia entre las partes del disco y las partes del eje es la forma en que se instalan durante el mecanizado. A veces, los diversos requisitos de características de la pieza también dan como resultado un método de mecanizado completamente diferente al de la pieza del eje. Piezas de disco típicas Usualmente usamos las siguientes técnicas de mecanizado: Preparación del tratamiento de tensión de eliminación de la pieza en bruto. ) una inspección de superficie terminada.
Kang Ding empresas de mecanizado son: Tapa giratoria, tornillo, husillo de máquina herramienta, mecanizado de ejes, portaherramientas de alta precisión, portaherramientas, mandril elástico, mecanizado de piezas no estándar, ¡el poste de máquina herramienta es el producto estrella de la compañía!
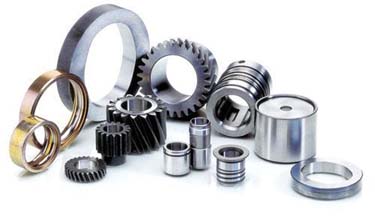
1. El proceso general del diseño del proceso de mecanizado CNC
(1) Seleccione la máquina herramienta CNC adecuada para mecanizar la pieza y determine el contenido del proceso.
(2) Analice los dibujos de piezas mecanizadas, aclare el contenido de procesamiento y los requisitos técnicos, determine el plan de procesamiento y desarrolle la ruta de mecanizado CNC. Tales como la división del proceso, la disposición de la secuencia de procesamiento, la conexión de procesos de mecanizado no CNC, etc. Diseñe procesos de mecanizado CNC, como la división de procesos, la selección de herramientas, el posicionamiento e instalación de accesorios, la determinación de la cantidad de corte, la determinación de la ruta de la cortadora, etc. Debido a la variedad de partes y los contornos y formas de las partes, el material y el tamaño de los espacios en blanco no son los mismos.
Por lo tanto, el diseño del proceso en el mecanizado CNC determina la eficiencia de uso de las máquinas herramienta CNC, la calidad del mecanizado de piezas, el número de herramientas y la economía. Debemos tratar de garantizar un paso de mecanizado centralizado, la ruta más corta y el tiempo de proceso auxiliar de la máquina minimizado.
2. Análisis de la tecnología de mecanizado de piezas de disco.
(1) Selección de materiales de mecanizado. Piezas de disco principalmente de acero, hierro fundido, acero inoxidable, aluminio, latón, bronce o similares como la materia prima principal. Las varillas laminadas en caliente o estiradas en frío generalmente se usan para discos de diámetro pequeño. Diferentes materiales pueden elegir fundición sólida. Se puede usar un agujero previo cuando la abertura es grande. Si se produce en masa, la extrusión en frío opcional y otros procesos de fabricación en blanco avanzados, no solo pueden mejorar la productividad, también pueden ahorrar material.
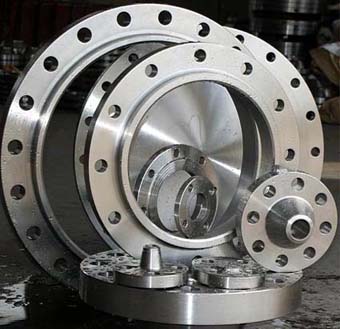
(2) Selección de estándares de mecanizado.
De acuerdo con las características de las partes, el principio de superposición estándar y evaluación comparativa debe cumplirse tanto como sea posible. La base para la selección suele ser la cara final, el orificio interno y el círculo externo. Cuando la cara final se usa como referencia para las partes del disco, el plano generalmente se usa como referencia. Cuando las partes del disco se basan en el orificio interno, la cara final generalmente es asistida por la cara final; El método de referencia del círculo externo es básicamente el mismo que la selección de referencia con el orificio interno.
(3) Disposición del proceso
Las partes de disco típicas consisten típicamente en caras extremas, agujeros y caras externas (algunas también incluyen agujeros escalonados), y las partes de disco se caracterizan por una dimensión radial mayor que la dimensión axial. Busque la fábrica de piezas de disco Kang Ding, garantía de calidad. Para las piezas de disco, no solo hay requisitos dimensionales, sino también requisitos de rugosidad de la superficie, que generalmente incluyen requisitos de desviación radial, desviación redonda y verticalidad. El redondeo y el redondeo de la cara final son las consideraciones clave al formular el proceso de mecanizado de las piezas del disco. Después de terminar, el círculo exterior, el orificio y la cara final deben terminarse en un proceso de sujeción para evitar una segunda sujeción. Para las piezas que deben sujetarse varias veces, los agujeros se mecanizan primero, y luego el círculo exterior o la cara final se mecanizan a través de los agujeros.
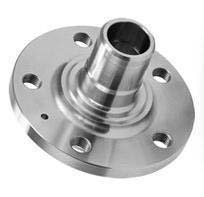
(4) Selección y uso de accesorios.
El mandril universal de tres mordazas se utiliza para sujetar las piezas de trabajo de pequeñas piezas de disco. El mandril de cuatro mordazas o la placa frontal son adecuados para sujetar piezas de disco medianas y grandes. Para la precisión de la posición tangencial, generalmente se procesa sujetando con un mandril o una placa frontal. Cuando el estándar de posicionamiento de las partes del disco es el orificio mecanizado, para garantizar la coaxialidad del eje del círculo exterior y el eje del orificio, se utiliza el método de mandril para sujetar las partes. También hay muchos tipos de mandriles. Mandril cilíndrico o pequeño mandril cónico, adecuado para posicionamiento con agujeros cilíndricos; Y esos agujeros especiales como los agujeros cónicos y los agujeros de rosca adoptan los conos y mandriles de rosca correspondientes. El mandril cilíndrico sujeta las piezas centrando la superficie cilíndrica exterior y presionando la superficie del extremo. Se utiliza un ajuste libre entre el mandril y el orificio parcial.
Para mejorar la precisión de posicionamiento del huso, a veces el huso se procesa en un pequeño cuerpo vertebral cónico. También hay un disco de fijación común para piezas de funda de disco grandes. El disco está montado en el disco grande del eje del torno. En general, es adecuado para piezas de trabajo de forma irregular, y no se puede utilizar cuando la sujeción general del mandril. Al usar el disco para sujetar la pieza de trabajo, debe estar equilibrado, de lo contrario se generará una fuerza centrífuga, que eventualmente causará vibración y provocará el desgaste del rodamiento del husillo.
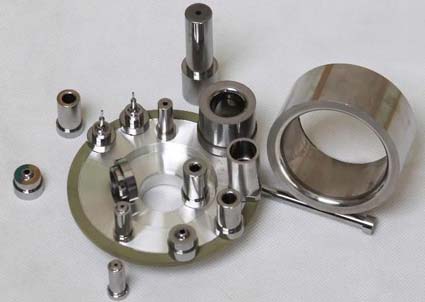
(5) Mecanizado de la superficie acabada de las piezas del disco.
Para la superficie giratoria de las partes del disco, el desbaste se realiza girando. Para el acabado, se debe tener más en cuenta el material, los requisitos de mecanizado y la producción para seleccionar métodos de mecanizado, como el torneado de acabado, el acabado de acabado, el rectificado de acabado, etc. Para la superficie no giratoria de las piezas del disco, se pueden utilizar los métodos de mecanizado correspondientes, fresado, electroerosión, etc.
(6) Determinación de los parámetros de corte.
Cuando el programador elige la cantidad de corte, debe considerar completamente varios factores que afectan el corte, seleccionar correctamente las condiciones de corte y determinar razonablemente la cantidad de corte, lo que puede mejorar efectivamente la calidad y eficiencia del mecanizado. Los factores que afectan las condiciones de corte son:
> rigidez de máquina, herramienta y pieza de trabajo;
> velocidad de corte, profundidad de corte, velocidad de avance de corte;
> precisión y rugosidad de la superficie de la pieza de trabajo;
> máxima vida útil de la herramienta y productividad;
> tipos de fluido de corte, método de enfriamiento;
> dureza del tratamiento térmico del material de la pieza de trabajo;
> número de piezas de trabajo;
> vida de la máquina.
Entre los factores anteriores, la velocidad de avance, la velocidad de corte y la profundidad de corte son los factores principales. Analice principalmente estos puntos:
A, la elección de la velocidad de alimentación
Cada revolución de la pieza de trabajo, la distancia que la herramienta se mueve en la dirección de desplazamiento se denomina cantidad de alimentación, y la unidad es mm / r. En teoría, al desbastar, es la alimentación máxima del mecanismo. La velocidad de alimentación está limitada por el tamaño de algunos de los siguientes factores: Resistencia y rigidez de las máquinas herramienta, vástagos, cuchillas, accesorios. El acabado está limitado principalmente por la precisión del mecanizado y la rugosidad de la superficie, y la cantidad de alimentación se selecciona en combinación con el material de la pieza de trabajo, el radio de la punta de la herramienta y la velocidad de corte.
B, la elección de la velocidad de corte
La velocidad lineal del movimiento principal se llama velocidad de corte y su unidad es III / so III / min. En la producción real, la velocidad de corte generalmente se selecciona en función de la experiencia, y la velocidad de corte más baja generalmente se selecciona para desbaste. Además, es necesario considerar exhaustivamente las propiedades de procesamiento del material, el rendimiento de corte de la herramienta, las condiciones de trabajo y otros factores para determinar razonablemente la velocidad de corte óptima. Relacionado con la velocidad de la máquina, y hay una fórmula de conversión de cálculo:
n = 1000v / dII
Fórmula donde: d es el diámetro de la pieza de trabajo, la velocidad seleccionada n debe estar dentro del rango de la velocidad de rotación del torno.Los parámetros de procesamiento apropiados se seleccionan por experiencia o la fórmula de cálculo anterior.
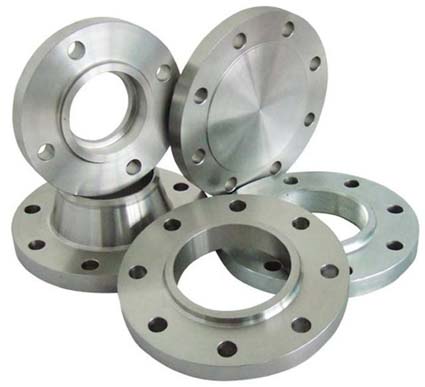
(7) Formular rutas de mecanizado.
La mayor diferencia entre las partes del disco y las partes del eje es la forma en que se instalan durante el mecanizado. A veces, los diversos requisitos de características de la pieza también dan como resultado un método de mecanizado completamente diferente al de la pieza del eje. Piezas de disco típicas Usualmente usamos las siguientes técnicas de mecanizado: Preparación del tratamiento de tensión de eliminación de la pieza en bruto. ) una inspección de superficie terminada.
Kang Ding empresas de mecanizado son: Tapa giratoria, tornillo, husillo de máquina herramienta, mecanizado de ejes, portaherramientas de alta precisión, portaherramientas, mandril elástico, mecanizado de piezas no estándar, ¡el poste de máquina herramienta es el producto estrella de la compañía!