Tecnología de mecanizado de piezas de boquillas de acero inoxidable de precisión
El procesamiento compuesto de torneado y fresado de muchas piezas compuestas de precisión pequeña con alta precisión, múltiples lotes y formas complejas plantea un gran desafío para la industria de fabricación mecánica. Con el rápido desarrollo de la industria aeroespacial, hidráulica, comunicaciones, microelectrónica, equipos médicos y otras industrias. Los métodos tradicionales de mecanizado CNC y los procesos de mecanizado no han podido satisfacer las necesidades de mecanizado diverso, individualizado y perfilado. La industria manufacturera se está desarrollando rápidamente en la dirección de alta eficiencia, precisión y composición.
En vista de las características de tales partes, la mayoría de las empresas nacionales adoptan métodos para mejorar el rendimiento del equipo y diseñar nuevas técnicas de procesamiento para satisfacer las necesidades de procesamiento y mejorar la eficiencia de la producción. Este documento toma como ejemplo una parte de boquilla compuesta típica y utiliza las características y ventajas del torno automático de precisión B0326-II. Desde los aspectos de selección de herramientas, desarrollo de procesos de mecanizado, diseño de rutas de mecanizado clave y análisis de problemas de procesamiento de prueba, se llevó a cabo una investigación exhaustiva de la tecnología de procesamiento. Se resuelve el problema del gran tamaño de lote, la baja eficiencia y el procesamiento difícil de tales piezas.
1. Análisis de la tecnología de procesamiento de piezas.
Requerimientos técnicos de piezas
La figura 1 muestra las partes de la boquilla en un dispositivo médico. La producción mensual es de 20,000 piezas, el material es acero inoxidable 1Cr18Ni9Ti, que es un material difícil; Los elementos de mecanizado de esta parte son más, incluyendo girar el círculo exterior y la rosca, fresar la superficie plana; El orificio central de perforación y el orificio inferior, el orificio de perforación, la rosca de rosca, etc. Además, la precisión dimensional y la rugosidad de la superficie de las piezas deben ser altas, y la coaxialidad de los orificios en ambos extremos es de 0.02 mm.
Según el análisis anterior, las dificultades de mecanizado de la pieza:
Garantice la precisión dimensional de los orificios externos e internos, los requisitos de coaxialidad de los dos orificios internos y la producción en masa.
pieza de boquilla de mecanizado
El torno automático de precisión B0326-II se utiliza principalmente para tornear. También tiene perforación, grabado, ranura de fresado, fresado de dientes, roscado, escariado, etc. La máquina herramienta de precisión de mecanizado combinado multiproceso tiene funciones de indexación del eje C y del eje Y, que pueden realizar fresado en plano radial, taladrado, roscado y otros procesos. El sistema de control de doble husillo puede realizar el posicionamiento automático y la alimentación del eje trasero después del procesamiento del lado del husillo, y resolver eficazmente el problema de baja eficiencia y precisión causada por el giro de la pieza de trabajo.
Como se muestra en la Figura 2, según las características de la máquina herramienta, el diseño de la ruta de procesamiento del contorno exterior de la pieza: Lado del husillo → Cara del extremo giratorio → Girar el círculo exterior a 39 mm. → Girar el círculo exterior a 65,1 mm al extremo del automóvil del lado del eje trasero.
Según el análisis anterior, el diseño de procesamiento de las piezas de la boquilla se muestra en la Tabla 1.
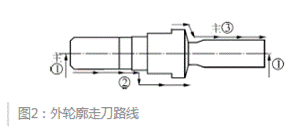
Dibujo de caminos de corte de contorno externo
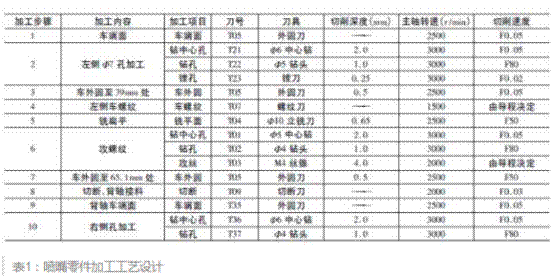
2. El paso clave del proceso de diseño.
Mecanizado de agujeros izquierdos
El orificio del lado izquierdo está mecanizado en el portaherramientas de cinco orificios T31-T35 en el lado del husillo. El portaherramientas de cinco orificios tiene un diseño compacto, lo que reduce el tiempo para que la herramienta pase la cuchilla y tiene una alta eficiencia de procesamiento.
El orificio Φ7 tiene un mayor requisito de precisión y adopta un proceso aburrido. La profundidad del agujero de 38 mm pertenece al procesamiento de agujeros profundos. La dificultad radica en el enfriamiento del área de corte de la broca durante la perforación del agujero y el problema de la eliminación de virutas. El enfriamiento de aceite a alta presión y el taladro de picoteo G83 pueden prevenir efectivamente la rotura y el enredo de virutas.
Los pasos específicos:
En primer lugar, taladre el orificio central de aproximadamente 2 mm con drill6 taladro central, la profundidad no debe ser demasiado superficial, de lo contrario el chaflán del orificio tendrá rebabas; Luego taladre con una broca de Φ5.8, dejando un margen de mecanizado de aproximadamente 0.5 mm en un lado. Debido a la alta dureza del material de la pieza, la mayor parte de la cantidad restante debe eliminarse en el proceso y debe activarse el enfriamiento de aceite a alta presión; Finalmente, el taladro garantiza el tamaño del orificio, y el modo de corte es de alta velocidad y bajo avance. Se selecciona la barra de mandrinar S25.0G-SVNR12SN, tipo de cuchilla VNBR0620-01, velocidad del husillo 3000r / min, profundidad de corte ap = 0.25 mm, velocidad de avance f = 0.02 mm / r.
Al girar el círculo exterior a 39mm
Este paso es el procesamiento del contorno exterior, centrándose en cómo mejorar la eficiencia del procesamiento y garantizar la calidad de la superficie. Considere las características estructurales de la pieza y las propiedades del material. El diseño de la ruta de la cortadora se muestra en la Figura 3. Este paso 〖LL〗 〖JP2〗 se completa en tres veces. Los dos primeros usan el camino rectangular G90 para eliminar la mayor parte de la asignación y el tercer acabado. En las dos primeras veces, se utilizó el camino de corte rectangular G90 para eliminar la mayor parte de la asignación. El acabado se completa por tercera vez.
Cuando se ejecuta la primera ruta de mecanizado rectangular, se procesa en el punto A, cada vez que la profundidad de corte es de 0,5 mm, la velocidad de avance es de 0,05 mm / r, y se completa con tres cuchillas; Cuando se ejecuta la segunda ruta de mecanizado rectangular, se procesa hasta el punto B, cada vez que la profundidad de corte es de 0.3 mm, la velocidad de avance es de 0.03 mm / r, y se completa el cuchillo de cuatro cuchillas; La profundidad final de acabado es de 0.1 mm y la velocidad de avance es de 0.01 mm / r. Este paso utiliza una cuchilla redonda externa Kyocera SCLCR1616H-12, tipo de hoja CCGT09T304M, la calidad de la superficie de las piezas es mejor.
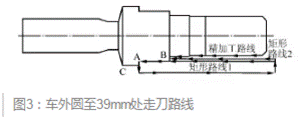
Figura 3. Girando tomando los caminos del cortador
Hilo de giro a la izquierda
Puesto que el hilo de rosca M10 necesita ser emparejado con otras partes de dispositivos médicos, se requiere para controlar el diámetro de la rosca y el valor de rugosidad alcanza Ra0.8.
Para cumplir con los requisitos, gire el hilo en tres pasos:
primer paso, el cuchillo circular exterior girará el diámetro grande en 0.2 mm;
El segundo paso, Después de que el torneado de roscas se ha completado por primera vez, el cuchillo circular exterior se llama de nuevo a girar a lo largo de la superficie de la rosca para eliminar la rebaba parte superior, pero la rebaba se presiona hacia la parte inferior del diente;
tercer paso, Gire los dos últimos cuchillos a lo largo de los hilos con un cortador de hilo, y luego gírelos nuevamente para eliminar las rebabas en la dirección de la parte inferior del diente en el segundo paso.
Fresado plano
El fresado plano utiliza principalmente la función de indexación del eje C del husillo del torno automático de precisión B0326-II para resolver eficazmente el problema de sujeción secundaria. El espesor total de la capa de molienda de este paso es de 2,3 mm, y se puede seleccionar un molino de extremo de gran diámetro para mejorar la eficiencia del procesamiento.
Según el análisis, se selecciona el diámetro mill10 fresa de extremo. Después de frenar el husillo, se divide en tres fresadoras.
primera vez, la profundidad de fresado fue de 0,65 mm.
La segunda vez, la profundidad de fresado es de 0,65 mm.
Por tercera vez, la profundidad de fresado es de 0,35 mm.
Cada vez que la velocidad de avance de fresado es de 50 mm / min, el eje C se indexa 180 ° y se mecaniza el otro lado. Una vez que finaliza el fresado del avión, habrá rebabas en el extremo exterior del avión. En este momento, es mejor usar un cuchillo circular externo para desbarbar a lo largo del círculo exterior de Φ13, y el efecto es mejor.
Girando el círculo exterior a 65.1 mm
La dificultad en el torneado externo aquí es que el área C tiene forma de ranura, lo que limita el ángulo de la herramienta y dificulta el corte de la cuchilla. Las herramientas de corte circular convencionales son fáciles de interferir y colapsar, y la calidad de la superficie de las ranuras es deficiente.
Por lo tanto, el giro se lleva a cabo tres veces, y la ruta del corte se muestra en la Figura 4. Por primera vez, se selecciona el cortador de ranuras con un ancho de 3 mm para cortar hasta el fondo de la ranura con un margen de acabado de 0,1 mm, y la herramienta se alimenta a lo largo de la ruta 1 para proporcionar el espacio de corte para el próximo giro.
Para el segundo tiempo, se selecciona la herramienta de torneado exterior convencional 90 °, y la herramienta se alimenta a lo largo de la ruta 2, y se procesa de acuerdo con la ruta rectangular G90, y se elimina la cantidad total de 6,4 mm;
la tercera vez, use la herramienta de barrido trasero y a lo largo de la ruta 3 para terminar. Debido al pequeño espacio en la ranura, el filo de corte circular exterior de 90 ° es fácil de interferir. El uso de la cuchilla de barrido posterior puede resolver eficazmente el problema y garantizar el valor de rugosidad en la parte inferior de la ranura.
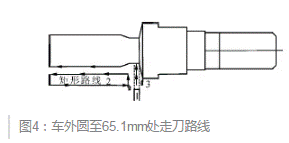
Figura 4. Girando el círculo exterior a 65.1 mm y tomando los caminos de corte
La perforación del orificio de recepción del eje trasero
Como se muestra en la Figura 5. Después de completar todo el mecanizado en el lado del eje principal, la cuchilla de corte se coloca en la posición de corte, el eje posterior se centra con el eje principal, el eje posterior T9900 se sujeta a lo largo de la dirección del eje principal B-B, y el eje posterior principal gira simultáneamente, lo que aumenta considerablemente la rigidez. Corte el eje posterior para recoger el material y use la herramienta T35, T36, T37 del lado posterior para llevar a cabo la cara final y el orificio de perforación. El eje trasero se posiciona automáticamente para ser sujetado con la posición concéntrica del husillo, evitando el error de coaxialidad causado por la re-sujeción, asegurando los requisitos de coaxialidad de los orificios Φ7 y Φ4, y resolviendo el problema del procesamiento de coaxialidad de la pieza.
Figura 5. Croquis de la conexión del eje trasero.
3. Análisis de problemas de procesamiento de prueba
Después de redactar la tecnología de procesamiento, se lleva a cabo la programación. Después de la verificación de simulación repetida, el primer procesamiento de prueba de la pieza mostró una mejora de rebabas en el fondo del orificio Φ7. Orificio de Φ4 sin chaflán de 60 °. Φ7 desviación de profundidad del pozo y otros problemas.
La precisión del tamaño del orificio Φ7 y la calidad de la superficie de esta parte son altas. Cuando se perfora la broca Φ5 en el fondo del agujero, el chip no se descarga a tiempo debido a la extrusión, lo que hace que se levante la rebaba en el fondo del agujero, lo que afecta la calidad de la pieza. Después de varias pruebas, realice los siguientes ajustes: Cuando la broca se perfora hasta el fondo del orificio, el taladro no sale directamente, se levanta 0.1 mm a lo largo del orificio, luego se retrasa 0.2s (es decir, G04U0.2) y luego se sale del fondo del orificio para eliminar la rebaba ascendente .
Como se muestra en la Figura 6. El chaflán de hole4 agujeros se mecaniza a partir de un taladro central de Φ6. El no orificio del orificio se juzga ya que el orificio central se perfora demasiado profundo. y la superficie del cono ha excedido los 60 ° en la parte inferior del taladro central, y la compensación de desgaste +0.5 en el lado del eje trasero T36 puede resolver el problema.
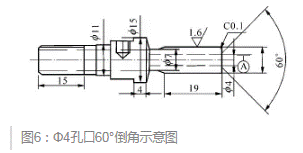
Figura 6. Diagrama de achaflanado de 4 agujeros de 60 °
Cuando se probó el primer producto, se descubrió que la profundidad del agujero Φ7 era de 37.8 mm, que era 0.2 mm más pequeña que el tamaño real. La razón del análisis es principalmente la herramienta de perforación T23 en el lado del husillo, y hay una desviación en la configuración de la herramienta. En el lado del husillo, la herramienta de perforación T23 vuelve a alinear la herramienta con precisión, y la entrada de compensación de desgaste T23 +0.2. Después de la depuración repetida, las piezas de la boquilla cumplen con los requisitos de aceptación, y las boquillas de mecanizado se muestran en la Figura 7.
4. Resumen
Después de la puesta en marcha de las piezas de la boquilla, la máquina herramienta está equipada con un alimentador automático. La alimentación, el procesamiento, la recepción y la descarga están completamente automatizados, y se realiza la demanda de procesamiento de 20,000 piezas por mes. Resuelve los problemas de miniaturización, multi-variedad, alto volumen y alta precisión que ocurren en los procesos de fabricación modernos.
A través de la investigación del torno automático de precisión B0326-II, tecnología de procesamiento de piezas de eje compuesto pequeño. Proporciona una base técnica para la promoción de un nuevo tipo de tecnología de mecanizado combinado de torneado y fresado, y también proporciona referencias y referencias para el procesamiento de piezas similares.
En vista de las características de tales partes, la mayoría de las empresas nacionales adoptan métodos para mejorar el rendimiento del equipo y diseñar nuevas técnicas de procesamiento para satisfacer las necesidades de procesamiento y mejorar la eficiencia de la producción. Este documento toma como ejemplo una parte de boquilla compuesta típica y utiliza las características y ventajas del torno automático de precisión B0326-II. Desde los aspectos de selección de herramientas, desarrollo de procesos de mecanizado, diseño de rutas de mecanizado clave y análisis de problemas de procesamiento de prueba, se llevó a cabo una investigación exhaustiva de la tecnología de procesamiento. Se resuelve el problema del gran tamaño de lote, la baja eficiencia y el procesamiento difícil de tales piezas.
1. Análisis de la tecnología de procesamiento de piezas.
Requerimientos técnicos de piezas
La figura 1 muestra las partes de la boquilla en un dispositivo médico. La producción mensual es de 20,000 piezas, el material es acero inoxidable 1Cr18Ni9Ti, que es un material difícil; Los elementos de mecanizado de esta parte son más, incluyendo girar el círculo exterior y la rosca, fresar la superficie plana; El orificio central de perforación y el orificio inferior, el orificio de perforación, la rosca de rosca, etc. Además, la precisión dimensional y la rugosidad de la superficie de las piezas deben ser altas, y la coaxialidad de los orificios en ambos extremos es de 0.02 mm.
Según el análisis anterior, las dificultades de mecanizado de la pieza:
Garantice la precisión dimensional de los orificios externos e internos, los requisitos de coaxialidad de los dos orificios internos y la producción en masa.
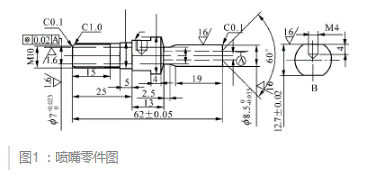
pieza de boquilla de mecanizado
El torno automático de precisión B0326-II se utiliza principalmente para tornear. También tiene perforación, grabado, ranura de fresado, fresado de dientes, roscado, escariado, etc. La máquina herramienta de precisión de mecanizado combinado multiproceso tiene funciones de indexación del eje C y del eje Y, que pueden realizar fresado en plano radial, taladrado, roscado y otros procesos. El sistema de control de doble husillo puede realizar el posicionamiento automático y la alimentación del eje trasero después del procesamiento del lado del husillo, y resolver eficazmente el problema de baja eficiencia y precisión causada por el giro de la pieza de trabajo.
Como se muestra en la Figura 2, según las características de la máquina herramienta, el diseño de la ruta de procesamiento del contorno exterior de la pieza: Lado del husillo → Cara del extremo giratorio → Girar el círculo exterior a 39 mm. → Girar el círculo exterior a 65,1 mm al extremo del automóvil del lado del eje trasero.
Según el análisis anterior, el diseño de procesamiento de las piezas de la boquilla se muestra en la Tabla 1.
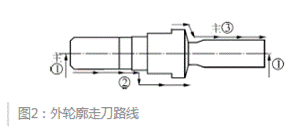
Dibujo de caminos de corte de contorno externo
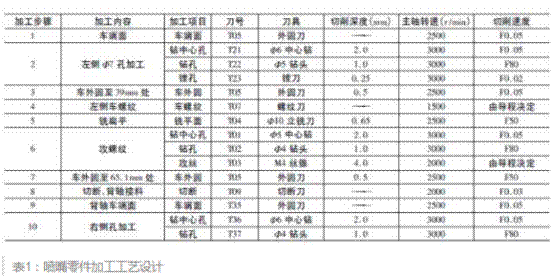
Tabla de proceso de diseño de procesamiento de piezas de boquilla
2. El paso clave del proceso de diseño.
Mecanizado de agujeros izquierdos
El orificio del lado izquierdo está mecanizado en el portaherramientas de cinco orificios T31-T35 en el lado del husillo. El portaherramientas de cinco orificios tiene un diseño compacto, lo que reduce el tiempo para que la herramienta pase la cuchilla y tiene una alta eficiencia de procesamiento.
El orificio Φ7 tiene un mayor requisito de precisión y adopta un proceso aburrido. La profundidad del agujero de 38 mm pertenece al procesamiento de agujeros profundos. La dificultad radica en el enfriamiento del área de corte de la broca durante la perforación del agujero y el problema de la eliminación de virutas. El enfriamiento de aceite a alta presión y el taladro de picoteo G83 pueden prevenir efectivamente la rotura y el enredo de virutas.
Los pasos específicos:
En primer lugar, taladre el orificio central de aproximadamente 2 mm con drill6 taladro central, la profundidad no debe ser demasiado superficial, de lo contrario el chaflán del orificio tendrá rebabas; Luego taladre con una broca de Φ5.8, dejando un margen de mecanizado de aproximadamente 0.5 mm en un lado. Debido a la alta dureza del material de la pieza, la mayor parte de la cantidad restante debe eliminarse en el proceso y debe activarse el enfriamiento de aceite a alta presión; Finalmente, el taladro garantiza el tamaño del orificio, y el modo de corte es de alta velocidad y bajo avance. Se selecciona la barra de mandrinar S25.0G-SVNR12SN, tipo de cuchilla VNBR0620-01, velocidad del husillo 3000r / min, profundidad de corte ap = 0.25 mm, velocidad de avance f = 0.02 mm / r.
Al girar el círculo exterior a 39mm
Este paso es el procesamiento del contorno exterior, centrándose en cómo mejorar la eficiencia del procesamiento y garantizar la calidad de la superficie. Considere las características estructurales de la pieza y las propiedades del material. El diseño de la ruta de la cortadora se muestra en la Figura 3. Este paso 〖LL〗 〖JP2〗 se completa en tres veces. Los dos primeros usan el camino rectangular G90 para eliminar la mayor parte de la asignación y el tercer acabado. En las dos primeras veces, se utilizó el camino de corte rectangular G90 para eliminar la mayor parte de la asignación. El acabado se completa por tercera vez.
Cuando se ejecuta la primera ruta de mecanizado rectangular, se procesa en el punto A, cada vez que la profundidad de corte es de 0,5 mm, la velocidad de avance es de 0,05 mm / r, y se completa con tres cuchillas; Cuando se ejecuta la segunda ruta de mecanizado rectangular, se procesa hasta el punto B, cada vez que la profundidad de corte es de 0.3 mm, la velocidad de avance es de 0.03 mm / r, y se completa el cuchillo de cuatro cuchillas; La profundidad final de acabado es de 0.1 mm y la velocidad de avance es de 0.01 mm / r. Este paso utiliza una cuchilla redonda externa Kyocera SCLCR1616H-12, tipo de hoja CCGT09T304M, la calidad de la superficie de las piezas es mejor.
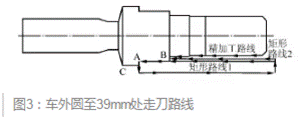
Figura 3. Girando tomando los caminos del cortador
Hilo de giro a la izquierda
Puesto que el hilo de rosca M10 necesita ser emparejado con otras partes de dispositivos médicos, se requiere para controlar el diámetro de la rosca y el valor de rugosidad alcanza Ra0.8.
Para cumplir con los requisitos, gire el hilo en tres pasos:
primer paso, el cuchillo circular exterior girará el diámetro grande en 0.2 mm;
tercer paso, Gire los dos últimos cuchillos a lo largo de los hilos con un cortador de hilo, y luego gírelos nuevamente para eliminar las rebabas en la dirección de la parte inferior del diente en el segundo paso.
Fresado plano
El fresado plano utiliza principalmente la función de indexación del eje C del husillo del torno automático de precisión B0326-II para resolver eficazmente el problema de sujeción secundaria. El espesor total de la capa de molienda de este paso es de 2,3 mm, y se puede seleccionar un molino de extremo de gran diámetro para mejorar la eficiencia del procesamiento.
Según el análisis, se selecciona el diámetro mill10 fresa de extremo. Después de frenar el husillo, se divide en tres fresadoras.
primera vez, la profundidad de fresado fue de 0,65 mm.
La segunda vez, la profundidad de fresado es de 0,65 mm.
Por tercera vez, la profundidad de fresado es de 0,35 mm.
Cada vez que la velocidad de avance de fresado es de 50 mm / min, el eje C se indexa 180 ° y se mecaniza el otro lado. Una vez que finaliza el fresado del avión, habrá rebabas en el extremo exterior del avión. En este momento, es mejor usar un cuchillo circular externo para desbarbar a lo largo del círculo exterior de Φ13, y el efecto es mejor.
Girando el círculo exterior a 65.1 mm
La dificultad en el torneado externo aquí es que el área C tiene forma de ranura, lo que limita el ángulo de la herramienta y dificulta el corte de la cuchilla. Las herramientas de corte circular convencionales son fáciles de interferir y colapsar, y la calidad de la superficie de las ranuras es deficiente.
Por lo tanto, el giro se lleva a cabo tres veces, y la ruta del corte se muestra en la Figura 4. Por primera vez, se selecciona el cortador de ranuras con un ancho de 3 mm para cortar hasta el fondo de la ranura con un margen de acabado de 0,1 mm, y la herramienta se alimenta a lo largo de la ruta 1 para proporcionar el espacio de corte para el próximo giro.
Para el segundo tiempo, se selecciona la herramienta de torneado exterior convencional 90 °, y la herramienta se alimenta a lo largo de la ruta 2, y se procesa de acuerdo con la ruta rectangular G90, y se elimina la cantidad total de 6,4 mm;
la tercera vez, use la herramienta de barrido trasero y a lo largo de la ruta 3 para terminar. Debido al pequeño espacio en la ranura, el filo de corte circular exterior de 90 ° es fácil de interferir. El uso de la cuchilla de barrido posterior puede resolver eficazmente el problema y garantizar el valor de rugosidad en la parte inferior de la ranura.
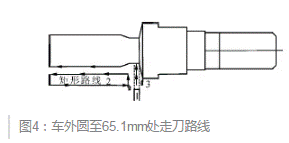
Figura 4. Girando el círculo exterior a 65.1 mm y tomando los caminos de corte
La perforación del orificio de recepción del eje trasero
Como se muestra en la Figura 5. Después de completar todo el mecanizado en el lado del eje principal, la cuchilla de corte se coloca en la posición de corte, el eje posterior se centra con el eje principal, el eje posterior T9900 se sujeta a lo largo de la dirección del eje principal B-B, y el eje posterior principal gira simultáneamente, lo que aumenta considerablemente la rigidez. Corte el eje posterior para recoger el material y use la herramienta T35, T36, T37 del lado posterior para llevar a cabo la cara final y el orificio de perforación. El eje trasero se posiciona automáticamente para ser sujetado con la posición concéntrica del husillo, evitando el error de coaxialidad causado por la re-sujeción, asegurando los requisitos de coaxialidad de los orificios Φ7 y Φ4, y resolviendo el problema del procesamiento de coaxialidad de la pieza.
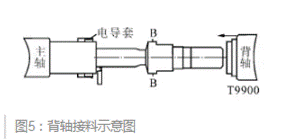
Figura 5. Croquis de la conexión del eje trasero.
3. Análisis de problemas de procesamiento de prueba
Después de redactar la tecnología de procesamiento, se lleva a cabo la programación. Después de la verificación de simulación repetida, el primer procesamiento de prueba de la pieza mostró una mejora de rebabas en el fondo del orificio Φ7. Orificio de Φ4 sin chaflán de 60 °. Φ7 desviación de profundidad del pozo y otros problemas.
La precisión del tamaño del orificio Φ7 y la calidad de la superficie de esta parte son altas. Cuando se perfora la broca Φ5 en el fondo del agujero, el chip no se descarga a tiempo debido a la extrusión, lo que hace que se levante la rebaba en el fondo del agujero, lo que afecta la calidad de la pieza. Después de varias pruebas, realice los siguientes ajustes: Cuando la broca se perfora hasta el fondo del orificio, el taladro no sale directamente, se levanta 0.1 mm a lo largo del orificio, luego se retrasa 0.2s (es decir, G04U0.2) y luego se sale del fondo del orificio para eliminar la rebaba ascendente .
Como se muestra en la Figura 6. El chaflán de hole4 agujeros se mecaniza a partir de un taladro central de Φ6. El no orificio del orificio se juzga ya que el orificio central se perfora demasiado profundo. y la superficie del cono ha excedido los 60 ° en la parte inferior del taladro central, y la compensación de desgaste +0.5 en el lado del eje trasero T36 puede resolver el problema.
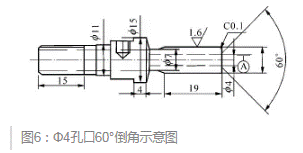
Figura 6. Diagrama de achaflanado de 4 agujeros de 60 °
Cuando se probó el primer producto, se descubrió que la profundidad del agujero Φ7 era de 37.8 mm, que era 0.2 mm más pequeña que el tamaño real. La razón del análisis es principalmente la herramienta de perforación T23 en el lado del husillo, y hay una desviación en la configuración de la herramienta. En el lado del husillo, la herramienta de perforación T23 vuelve a alinear la herramienta con precisión, y la entrada de compensación de desgaste T23 +0.2. Después de la depuración repetida, las piezas de la boquilla cumplen con los requisitos de aceptación, y las boquillas de mecanizado se muestran en la Figura 7.
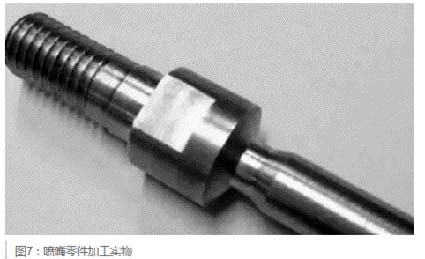
Figura 7. inoxidable partes de boquilla de acero procesamiento físico
4. Resumen
Después de la puesta en marcha de las piezas de la boquilla, la máquina herramienta está equipada con un alimentador automático. La alimentación, el procesamiento, la recepción y la descarga están completamente automatizados, y se realiza la demanda de procesamiento de 20,000 piezas por mes. Resuelve los problemas de miniaturización, multi-variedad, alto volumen y alta precisión que ocurren en los procesos de fabricación modernos.
A través de la investigación del torno automático de precisión B0326-II, tecnología de procesamiento de piezas de eje compuesto pequeño. Proporciona una base técnica para la promoción de un nuevo tipo de tecnología de mecanizado combinado de torneado y fresado, y también proporciona referencias y referencias para el procesamiento de piezas similares.