Que es el procesamiento de chapa?
El procesamiento de chapa es una tecnología fundamental que los técnicos en chapa deben captar. También es un proceso importante para formar productos de chapa metálica. El procesamiento de chapa metálica incluye métodos convencionales de corte, punzonado, plegado y otros métodos y parámetros de proceso.
También incluye una variedad de estructura de matriz de estampado en frío y parámetros de proceso, varios principios de funcionamiento de los equipos y métodos operativos, incluida la nueva tecnología de estampado y la nueva tecnología. El procesamiento de piezas de chapa se llama procesamiento de chapa metálica.
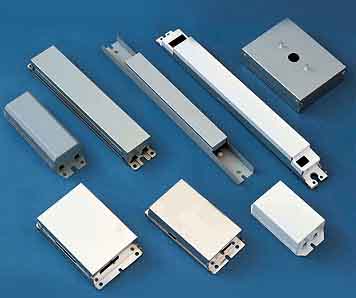
Términos de la industria
Cada industria tiene su propia terminología, y la industria de procesamiento de chapa no es una excepción. Los siguientes 25 son comunes.
(1) Remachado a presión: se refiere al proceso de fijación a presión de la pieza de trabajo a la pieza de trabajo mediante el uso de un punzón o prensa hidráulica para presionar la tuerca remachadora, el tornillo remachador de presión o el sujetador de la columna de la tuerca remachadora.
(2) Remachado: se refiere al avellanado de la pieza de trabajo primero. Luego presione la tuerca de remache firmemente sobre la pieza de trabajo con un punzón o prensa hidráulica.
(3) Tirando de la madre: se refiere al uso de un proceso de remachado similar. El proceso de conectar la tuerca del remache (POP) y otros conectores firmemente a la pieza de trabajo por medio de una pistola de tiro.
(4) Tire de remachado: se refiere a la pistola de remachar como una herramienta, utilizando el perno de tracción dos o más de dos piezas de trabajo estrechamente vinculadas al proceso.
(5) Unión de remache: Un proceso en el cual dos o más piezas de trabajo se unen cara a cara con remaches. Si se remacha avellanado, la pieza de trabajo se debe escariar primero.
(6) Ángulo de corte: se refiere al proceso de corte de la esquina de la pieza de trabajo mediante el uso de un troquel en una punzonadora o una prensa de aceite.
(7) flexión: el proceso de formar una pieza de trabajo desde una máquina dobladora.
(8) formación: se refiere al proceso de usar un molde en un punzón común u otro equipo para deformar la pieza de trabajo.
(9) material de corte: se refiere al material a través de la máquina de corte para obtener el proceso rectangular de la pieza de trabajo.
(10) Corte: se refiere al proceso de la pieza de trabajo después del corte LÁSER o el borrado de la prensa de perforación de control numérico.
(11) Blanking: se refiere al proceso de usar un molde para obtener la forma de un producto en un punzón ordinario u otro equipo.
(12) punzonado: se refiere al proceso de mecanizado de agujeros con punzones y matrices comunes.
(13) casco convexo de perforación: se refiere al proceso de conformación de la forma convexa de la pieza de trabajo en el molde punzonado o prensa hidráulica.
(14) rasgado y rasgado: se refiere al proceso de formar una forma de puente en un punzón o molde de prensa hidráulica.
(15) dibujar agujeros: también llamado "rebordeado", que se refiere al proceso de formación de orificios circulares en la pieza de trabajo mediante el uso de troqueles en punzonadoras ordinarias u otros equipos.
(16) Tapping: se refiere al proceso de mecanizado de roscas internas en la pieza de trabajo.
(17) Nivelación: se refiere a la irregularidad de la pieza de trabajo antes y después del mecanizado, y al uso de otros equipos para aplanar la pieza de trabajo.
(18) dientes posteriores: se refiere a la pieza de trabajo con dientes en el proceso de pre ataque, reparar la segunda veces el hilo.
(19) Perforación: el proceso de taladrar orificios en una pieza de trabajo con un taladro o una fresadora.
(20) Chaflán: se refiere al uso de moldes, herramientas de perforación, rectificadoras, etc., para procesar las esquinas afiladas de la pieza de trabajo.
(21) marca de perforación: se refiere al proceso de usar un molde para perforar caracteres, símbolos u otras impresiones en la pieza de trabajo.
(22) Contrataladre: se refiere al proceso de mecanizado de un agujero cónico en una pieza de trabajo para que coincida con un conector, como un tornillo de cabeza avellanada.
(23) palmada: se refiere a una cierta forma de la pieza de trabajo, la transición a un proceso suave.
(24) malla de perforación: significa perforar un orificio neto en la pieza de trabajo con un troquel con un punzón común o punzón CNC.
(25) escariado: el proceso de mecanizar pequeños agujeros en la pieza de trabajo con un taladro o fresa en agujeros grandes.
Flujo del proceso
Selección de materiales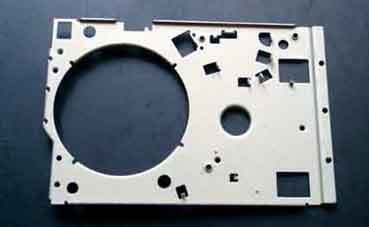
Los materiales comúnmente utilizados para el procesamiento de chapa metálica incluyen chapa laminada en frío (SPCC), chapa laminada en caliente (SHCC), chapa galvanizada (SECC, SGCC), cobre (CU) latón, cobre rojo, cobre de berilio, aluminio (6061, 5052 ) 1010, 1060, 6063, aluminio duro, etc.), acero inoxidable (espejo, superficie cepillada, mate), dependiendo del papel del producto, diferentes materiales, en general, deben considerar el uso del producto y el costo.
1. La placa laminada en frío SPCC, se utiliza principalmente para galvanizar y hornear piezas de pintura, bajo costo, fácil moldeado, espesor del material ≤ 3,2 mm.
2. La chapa laminada en caliente SHCC, material T ≥ 3.0mm, también se utiliza para galvanoplastia, piezas de laca, piezas planas de bajo costo pero difíciles de moldear, principalmente usadas.
3. Hoja galvanizada SECC, SGCC, placa de electrólisis SECC se divide en material N y material P. El material N no se usa para el tratamiento superficial y el costo es alto. El material P se usa para rociar partes.
4. Cobre; principalmente materiales conductivos, el tratamiento superficial es de níquel, cromo o sin tratamiento, de alto costo.
5. Placa de aluminio; uso general de cromato de superficie (J11-A), oxidación (oxidación conductiva, oxidación química), alto costo, plateado, niquelado.
6. Perfiles de aluminio; Estructura de sección transversal de materiales complejos, utilizada en una variedad de caja de enchufe. El tratamiento de superficie es el mismo que el tratamiento de superficie de la placa de aluminio.
7. Acero inoxidable; utilizado principalmente sin ningún tratamiento superficial, alto costo.
Revisión de dibujo
Para escribir el flujo del proceso de la parte, primero debemos entender los diversos requisitos técnicos del dibujo de partes; luego, la revisión del dibujo es la parte más importante de la preparación del flujo del proceso de la parte.
1. Verifique que el dibujo esté completo.
2. La relación entre dibujos y vistas, si las etiquetas son claras y completas, y las unidades de dimensión están marcadas.
3. Las relaciones de la Asamblea, los requisitos de montaje se centran en el tamaño.
4. La diferencia entre los dibujos antiguos y nuevos.
5. Traducción de idiomas extranjeros.
6. Conversión del número de código de la tabla.
7. Mapeo de problemas y comentarios.
8. material
9. Requisitos de calidad y requisitos del proceso
10. Los dibujos de la versión oficial, deberán estar sellados con un capítulo de control de calidad.
También incluye una variedad de estructura de matriz de estampado en frío y parámetros de proceso, varios principios de funcionamiento de los equipos y métodos operativos, incluida la nueva tecnología de estampado y la nueva tecnología. El procesamiento de piezas de chapa se llama procesamiento de chapa metálica.
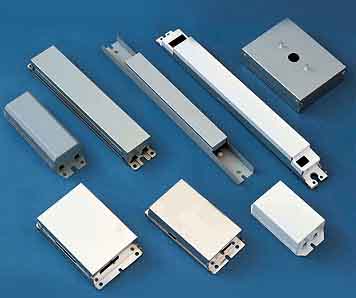
Términos de la industria
Cada industria tiene su propia terminología, y la industria de procesamiento de chapa no es una excepción. Los siguientes 25 son comunes.
(1) Remachado a presión: se refiere al proceso de fijación a presión de la pieza de trabajo a la pieza de trabajo mediante el uso de un punzón o prensa hidráulica para presionar la tuerca remachadora, el tornillo remachador de presión o el sujetador de la columna de la tuerca remachadora.
(2) Remachado: se refiere al avellanado de la pieza de trabajo primero. Luego presione la tuerca de remache firmemente sobre la pieza de trabajo con un punzón o prensa hidráulica.
(3) Tirando de la madre: se refiere al uso de un proceso de remachado similar. El proceso de conectar la tuerca del remache (POP) y otros conectores firmemente a la pieza de trabajo por medio de una pistola de tiro.
(4) Tire de remachado: se refiere a la pistola de remachar como una herramienta, utilizando el perno de tracción dos o más de dos piezas de trabajo estrechamente vinculadas al proceso.
(5) Unión de remache: Un proceso en el cual dos o más piezas de trabajo se unen cara a cara con remaches. Si se remacha avellanado, la pieza de trabajo se debe escariar primero.
(6) Ángulo de corte: se refiere al proceso de corte de la esquina de la pieza de trabajo mediante el uso de un troquel en una punzonadora o una prensa de aceite.
(7) flexión: el proceso de formar una pieza de trabajo desde una máquina dobladora.
(8) formación: se refiere al proceso de usar un molde en un punzón común u otro equipo para deformar la pieza de trabajo.
(9) material de corte: se refiere al material a través de la máquina de corte para obtener el proceso rectangular de la pieza de trabajo.
(10) Corte: se refiere al proceso de la pieza de trabajo después del corte LÁSER o el borrado de la prensa de perforación de control numérico.
(11) Blanking: se refiere al proceso de usar un molde para obtener la forma de un producto en un punzón ordinario u otro equipo.
(12) punzonado: se refiere al proceso de mecanizado de agujeros con punzones y matrices comunes.
(13) casco convexo de perforación: se refiere al proceso de conformación de la forma convexa de la pieza de trabajo en el molde punzonado o prensa hidráulica.
(14) rasgado y rasgado: se refiere al proceso de formar una forma de puente en un punzón o molde de prensa hidráulica.
(15) dibujar agujeros: también llamado "rebordeado", que se refiere al proceso de formación de orificios circulares en la pieza de trabajo mediante el uso de troqueles en punzonadoras ordinarias u otros equipos.
(16) Tapping: se refiere al proceso de mecanizado de roscas internas en la pieza de trabajo.
(17) Nivelación: se refiere a la irregularidad de la pieza de trabajo antes y después del mecanizado, y al uso de otros equipos para aplanar la pieza de trabajo.
(18) dientes posteriores: se refiere a la pieza de trabajo con dientes en el proceso de pre ataque, reparar la segunda veces el hilo.
(19) Perforación: el proceso de taladrar orificios en una pieza de trabajo con un taladro o una fresadora.
(20) Chaflán: se refiere al uso de moldes, herramientas de perforación, rectificadoras, etc., para procesar las esquinas afiladas de la pieza de trabajo.
(21) marca de perforación: se refiere al proceso de usar un molde para perforar caracteres, símbolos u otras impresiones en la pieza de trabajo.
(22) Contrataladre: se refiere al proceso de mecanizado de un agujero cónico en una pieza de trabajo para que coincida con un conector, como un tornillo de cabeza avellanada.
(23) palmada: se refiere a una cierta forma de la pieza de trabajo, la transición a un proceso suave.
(24) malla de perforación: significa perforar un orificio neto en la pieza de trabajo con un troquel con un punzón común o punzón CNC.
(25) escariado: el proceso de mecanizar pequeños agujeros en la pieza de trabajo con un taladro o fresa en agujeros grandes.
Flujo del proceso
Selección de materiales
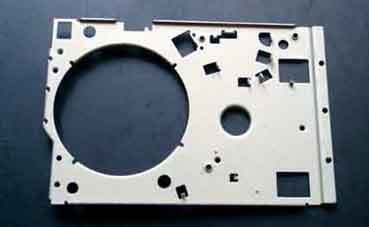
Los materiales comúnmente utilizados para el procesamiento de chapa metálica incluyen chapa laminada en frío (SPCC), chapa laminada en caliente (SHCC), chapa galvanizada (SECC, SGCC), cobre (CU) latón, cobre rojo, cobre de berilio, aluminio (6061, 5052 ) 1010, 1060, 6063, aluminio duro, etc.), acero inoxidable (espejo, superficie cepillada, mate), dependiendo del papel del producto, diferentes materiales, en general, deben considerar el uso del producto y el costo.
1. La placa laminada en frío SPCC, se utiliza principalmente para galvanizar y hornear piezas de pintura, bajo costo, fácil moldeado, espesor del material ≤ 3,2 mm.
2. La chapa laminada en caliente SHCC, material T ≥ 3.0mm, también se utiliza para galvanoplastia, piezas de laca, piezas planas de bajo costo pero difíciles de moldear, principalmente usadas.
3. Hoja galvanizada SECC, SGCC, placa de electrólisis SECC se divide en material N y material P. El material N no se usa para el tratamiento superficial y el costo es alto. El material P se usa para rociar partes.
4. Cobre; principalmente materiales conductivos, el tratamiento superficial es de níquel, cromo o sin tratamiento, de alto costo.
5. Placa de aluminio; uso general de cromato de superficie (J11-A), oxidación (oxidación conductiva, oxidación química), alto costo, plateado, niquelado.
6. Perfiles de aluminio; Estructura de sección transversal de materiales complejos, utilizada en una variedad de caja de enchufe. El tratamiento de superficie es el mismo que el tratamiento de superficie de la placa de aluminio.
7. Acero inoxidable; utilizado principalmente sin ningún tratamiento superficial, alto costo.
Revisión de dibujo
Para escribir el flujo del proceso de la parte, primero debemos entender los diversos requisitos técnicos del dibujo de partes; luego, la revisión del dibujo es la parte más importante de la preparación del flujo del proceso de la parte.
1. Verifique que el dibujo esté completo.
2. La relación entre dibujos y vistas, si las etiquetas son claras y completas, y las unidades de dimensión están marcadas.
3. Las relaciones de la Asamblea, los requisitos de montaje se centran en el tamaño.
4. La diferencia entre los dibujos antiguos y nuevos.
5. Traducción de idiomas extranjeros.
6. Conversión del número de código de la tabla.
7. Mapeo de problemas y comentarios.
8. material
9. Requisitos de calidad y requisitos del proceso
10. Los dibujos de la versión oficial, deberán estar sellados con un capítulo de control de calidad.
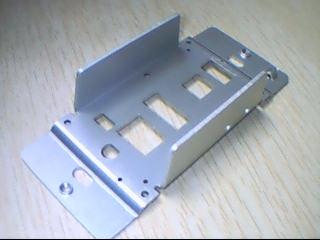