Perforación de microagujeros en compuestos de placa de circuito
Las especificaciones de las placas de circuito impreso son complejas y hay muchos tipos de productos. El material compuesto a base de resina epoxi más utilizado en placas de circuito impreso es un microagujero (un pequeño agujero con un diámetro de 0.6 mm o menos y un micro agujero con un diámetro de 0.3 mm o menos).
La placa de circuito compuesto tiene alta fragilidad, alta dureza, alta resistencia de la fibra, alta tenacidad, baja resistencia al corte interlaminar, anisotropía, baja conductividad térmica y una gran diferencia en los coeficientes de expansión térmica de las fibras y resinas. Cuando la temperatura de corte es alta, es fácil generar estrés térmico en la interfaz fibra-sustrato alrededor de la zona de corte; Cuando la temperatura es demasiado alta, la resina se derrite y se adhiere al borde de corte, lo que dificulta el procesamiento y la eliminación de virutas.

La fuerza de corte del material compuesto perforado es muy desigual, y es fácil causar defectos tales como delaminación, rebabas y grietas, y la calidad del procesamiento es difícil de garantizar. Este material es extremadamente abrasivo para la herramienta y el desgaste de la herramienta es bastante severo. El desgaste de la herramienta a su vez conduce a mayores fuerzas de corte y generación de calor. Si el calor no se puede disipar a tiempo, causará la fusión del componente de bajo punto de fusión en el material de PCB y se despegará entre la capa compuesta y la capa. Por lo tanto, los materiales compuestos de PCB son difíciles de procesar materiales compuestos no metálicos, y el mecanismo de procesamiento es completamente diferente del de los materiales metálicos.
Al perforar mecánicamente materiales de PCB, la eficiencia del procesamiento es alta, el posicionamiento del orificio es preciso y la calidad de los orificios también es alta. Sin embargo, al perforar un microagujero, el diámetro de la broca es demasiado pequeño y es fácil de romper. Durante el proceso de perforación también pueden ocurrir defectos como la delaminación del material, daños en la pared del pozo, rebabas y manchas.
I. Fuerza de perforación
Varios problemas que ocurren durante la perforación mecánica están directa o indirectamente relacionados con la fuerza axial y el par de corte. Los principales factores que afectan la fuerza axial y el torque son la velocidad de avance, la velocidad de corte, la forma del haz de fibras y la presencia o ausencia de agujeros preformados que también tienen un efecto sobre las fuerzas axiales y el torque. La fuerza axial y el par aumentan al aumentar la velocidad de avance y la velocidad de corte. A medida que aumenta la velocidad de alimentación, aumenta el grosor de la capa de corte, y a medida que aumenta la velocidad de corte, aumenta el número de fibras cortadas por unidad de tiempo, y la cantidad de desgaste de la herramienta aumenta rápidamente, por lo que la fuerza axial y el par aumentan.
La fuerza axial se puede dividir en la fuerza componente estática FS y la fuerza componente dinámica FD. La fuerza componente de la fuerza axial tiene diferentes efectos sobre el borde cortante, y la fuerza componente estática FS de la fuerza axial afecta el corte del borde del cincel. La fuerza del componente dinámico FD afecta principalmente el corte del filo principal, y la fuerza del componente dinámico FD tiene una mayor influencia en la rugosidad de la superficie que la fuerza del componente estático FS. La fuerza axial aumenta con la velocidad de avance, y la influencia de la velocidad de corte en la fuerza axial no es obvia. Además, en el caso de agujeros prefabricados, cuando la abertura es inferior a 0,4 mm, la fuerza del componente estático FS disminuye bruscamente con el aumento de la abertura, mientras que el componente dinámico FD disminuye con una tendencia al aplanamiento.
Debido a las diferentes propiedades de procesamiento de la matriz compuesta y las fibras de refuerzo, la resina de matriz y las fibras tienen diferentes efectos sobre la fuerza axial durante la perforación mecánica. Khashaba estudió los efectos de los tipos de matriz y fibra sobre las fuerzas axiales y el torque:
Se descubrió que la forma del haz de fibras tenía una influencia significativa en la fuerza axial, y el tipo de resina de matriz tenía poco efecto en la fuerza axial.
II. Desgaste y rotura de la broca
El desgaste de micro taladro compuesto de PCB incluye desgaste químico y desgaste por fricción. El desgaste químico es causado por el ataque químico del producto de pirólisis liberado del material de PCB en el aglutinante de Co en el material microperforado de carburo cementado WC-Co. A aproximadamente 300 ° C, esta reacción de erosión se ha vuelto más evidente. A una velocidad de perforación de menos de 150 mm / min, el desgaste químico ya no es la forma principal de desgaste, y la fricción y el desgaste se convierten en la forma principal de desgaste. El desgaste del microperforador de PCB también está relacionado con la relación entre la velocidad de corte, la velocidad de alimentación y el radio de bits con respecto al ancho del haz de fibras. La investigación de Inoue et al. Muestra que: La relación entre el radio del taladro y el ancho del haz de fibras (fibra de vidrio) tiene una gran influencia en la vida útil de la herramienta: cuanto mayor sea la relación, mayor será el ancho del haz de fibras del cortador y mayor será el desgaste de la herramienta.
En aplicaciones prácticas, la nueva broca perfora hasta 2.500 agujeros para rectificar.
Esmerilando la broca por primera vez, perforando hasta 2000 agujeros y volviéndola a pulir.
La segunda rectificación de la broca, que perfora hasta 1500 agujeros, debe rectificarse nuevamente,
La tercera vez que se perforó la broca, se perforaron hasta 1000 agujeros y se desechó la broca.
Durante el procesamiento de microporos de la PCB, la fuerza axial y el par aumentan con el aumento de la velocidad de alimentación y la profundidad de perforación, y la razón principal está relacionada con el estado de eliminación de la viruta. A medida que aumenta la profundidad de perforación, la descarga de la viruta es difícil: En este caso, la temperatura de corte aumenta, el material de resina se funde y une firmemente las fibras de vidrio y las piezas de lámina de cobre para formar un cuerpo de corte resistente. Este cuerpo de corte tiene afinidad con el material de matriz de PCB. Una vez que se produce un cuerpo de corte de este tipo, se detiene la descarga de las virutas, y la fuerza axial y el par aumentan bruscamente, lo que hace que la broca microporosa se rompa. La forma de fractura de la broca de microagujero de PCB tiene pandeo, rotura de torsión y pandeo y rotura de torsión, y generalmente ambos coexisten. La condición de ruptura es principalmente la obstrucción de virutas, que es un factor clave que causa el aumento del par de perforación. Reducir la fuerza axial y el par de corte es la clave para reducir la rotura del taladro de microagujeros.
III. Forma de daño perforado
1, estratificación
Pueden ocurrir varios daños durante la perforación mecánica de laminados GFRP (reforzados con fibra de vidrio). El más grave de estos es la delaminación entre capas, que produce una fuerte caída en las propiedades del material alrededor de las paredes de los poros, y la fuerza axial ejercida por la punta de perforación es la principal causa de la delaminación. Las capas se pueden dividir en delaminación de perforación y delaminación de perforación. La delaminación de perforación es cuando el filo de la broca está en contacto con la placa de laminación, y la fuerza de corte que actúa en la dirección circunferencial en la dirección circunferencial está separada de la capa por la ranura de corte de la broca para formar una región en capas en la superficie de la placa de laminación. Perforar la delaminación es cuando la broca se acerca al fondo del laminado. Dado que el grosor del material sin cortar se hace cada vez más delgado, la capacidad de resistir la deformación se reduce aún más, y la estratificación se produce cuando la carga excede la adhesión entre los laminados. Esto sucedió antes de perforar el laminado. Las fuerzas axiales son la causa principal de la delaminación, y la velocidad de corte, el sustrato y el tipo de haz de fibras también tienen un efecto sobre la delaminación. La perforación y la delaminación de los compuestos epoxídicos disminuye con el aumento de la velocidad de perforación, y el grado de daño por delaminación es mayor que el de la perforación. Las principales medidas para reducir la estratificación son: Se utilizan tecnología de alimentación variable, agujeros guía preestablecidos y relleno. En la perforación no soportada, se usa un amortiguador viscoso o similar.
2, daño de la pared del agujero
Los microporos se perforan en el PCB compuesto, y varias formas de daño que ocurren alrededor de los agujeros dan como resultado una disminución en el aislamiento entre los agujeros y una ruptura en la capa de cobre de los agujeros después de la metalización de los agujeros. El ángulo relativo entre la dirección de corte y la dirección de la fibra, el grosor del haz de fibra de vidrio en la pared del agujero, la posición del punto de perforación en la tela de vidrio, etc., tienen diferentes efectos sobre el daño de la pared del agujero. El material compuesto de fibra de vidrio / epoxi se perforó con una broca de 1.0 mm de diámetro a una velocidad de 5000 rpm (8 capas de 90 ° escalonadas, 0.2 mm por capa). Las pruebas muestran que el grado de daño alrededor de cada agujero es diferente, y las capas de arrugas de fibra primera, tercera, quinta, séptima y octava son grandes, con una protuberancia máxima de 30 μm; Las 2, 4 y 6 capas de arrugas de fibra son menos prominentes, y el mínimo es inferior a 5 μm. En el área superpuesta del hilo de trama y el hilo de urdimbre, el grosor del haz de fibras es el más grande en el ángulo de la fibra de 45 °, y el ancho de daño de la pared del agujero es el más grande; En la región central, el ancho máximo de daño ocurre en un ángulo de aproximadamente 90 ° con respecto al ángulo de la fibra.
2, daño de la pared del agujero
Perfore microporos en una placa de circuito impreso compuesta. Varias formas de daño que ocurren alrededor de los agujeros dan como resultado una disminución en el aislamiento entre los agujeros y una ruptura en la capa de cobre de los agujeros después de la metalización de los agujeros. El ángulo relativo entre la dirección de corte y la dirección de la fibra, el grosor del haz de fibra de vidrio en la pared del agujero, la posición del punto de perforación en la tela de vidrio, etc., tienen diferentes efectos en el daño de la pared.
El material compuesto de fibra de vidrio / epoxi se perforó con una broca de 1.0 mm de diámetro a una velocidad de 5000 rpm (8 capas de 90 ° escalonadas, 0.2 mm por capa). Las pruebas muestran que el grado de daño alrededor de cada agujero es diferente, y las capas de arrugas de fibra primera, tercera, quinta, séptima y octava son grandes, con una protuberancia máxima de 30 μm; Las 2, 4 y 6 capas de arrugas de fibra son menos prominentes, y el mínimo es inferior a 5 μm. En el área superpuesta del hilo de trama y el hilo de urdimbre, el grosor del haz de fibras es el más grande en el ángulo de la fibra de 45 °, y el ancho de daño de la pared del agujero es el más grande; En la región central, el ancho máximo de daño ocurre en un ángulo de aproximadamente 90 ° con respecto al ángulo de la fibra.
La influencia de la declinación principal de la herramienta en la rugosidad de la superficie de la pared del agujero mecanizado: Cuando la declinación principal es de 30 °, la rugosidad de la superficie de la pared del poro es la más grande, hasta 50 μm.
3, manchas
Mechanical perforación de un material compuesto, ya que el taladro borde de cincel extruye material compuesto, y la fricción entre la pared del agujero cónica invertida. Y incrustado en pequeños chips de borde entre la broca y la pared de agujero de taladro con un gran número de calor de corte giratorio generado por la fricción con la masa fundida de resina. Y adhiérase a la lámina de cobre y a la pared del agujero en la capa intermedia o al agujero del compuesto para formar una mancha. El corte y rectificado adecuados del micro taladro pueden reducir la generación de manchas y reducir el índice de manchas.
4, rebabas
Cuando se perfora un material compuesto, debido a la transferencia de tensión, cuando la broca no alcanza el fondo del orificio, el material de refuerzo y el sustrato frente a la broca generan muchas grietas, de modo que el material de refuerzo se despega del sustrato. Tire del fenómeno se genera, lo que resulta en el material mejorada no se puede cortar a partir de las raíces. Estos materiales de refuerzo que no se cortan desde la raíz no se pueden quitar junto con las astillas cuando se taladran los agujeros, sino que se vierten hacia los bordes de los agujeros. La matriz se ablanda, fluye y se vuelve a condensar en el material de refuerzo vertido en el borde del agujero para formar rebabas. El tamaño de las rebabas de salida se ve afectado principalmente por la fuerza de perforación y la temperatura de perforación. La perforación con brocas de carburo, el cambio de geometrías y estructuras de herramientas, y las técnicas de perforación vibratoria pueden reducir las rebabas en la perforación compuesta.
La placa de circuito compuesto tiene alta fragilidad, alta dureza, alta resistencia de la fibra, alta tenacidad, baja resistencia al corte interlaminar, anisotropía, baja conductividad térmica y una gran diferencia en los coeficientes de expansión térmica de las fibras y resinas. Cuando la temperatura de corte es alta, es fácil generar estrés térmico en la interfaz fibra-sustrato alrededor de la zona de corte; Cuando la temperatura es demasiado alta, la resina se derrite y se adhiere al borde de corte, lo que dificulta el procesamiento y la eliminación de virutas.

La fuerza de corte del material compuesto perforado es muy desigual, y es fácil causar defectos tales como delaminación, rebabas y grietas, y la calidad del procesamiento es difícil de garantizar. Este material es extremadamente abrasivo para la herramienta y el desgaste de la herramienta es bastante severo. El desgaste de la herramienta a su vez conduce a mayores fuerzas de corte y generación de calor. Si el calor no se puede disipar a tiempo, causará la fusión del componente de bajo punto de fusión en el material de PCB y se despegará entre la capa compuesta y la capa. Por lo tanto, los materiales compuestos de PCB son difíciles de procesar materiales compuestos no metálicos, y el mecanismo de procesamiento es completamente diferente del de los materiales metálicos.
Al perforar mecánicamente materiales de PCB, la eficiencia del procesamiento es alta, el posicionamiento del orificio es preciso y la calidad de los orificios también es alta. Sin embargo, al perforar un microagujero, el diámetro de la broca es demasiado pequeño y es fácil de romper. Durante el proceso de perforación también pueden ocurrir defectos como la delaminación del material, daños en la pared del pozo, rebabas y manchas.
I. Fuerza de perforación
Varios problemas que ocurren durante la perforación mecánica están directa o indirectamente relacionados con la fuerza axial y el par de corte. Los principales factores que afectan la fuerza axial y el torque son la velocidad de avance, la velocidad de corte, la forma del haz de fibras y la presencia o ausencia de agujeros preformados que también tienen un efecto sobre las fuerzas axiales y el torque. La fuerza axial y el par aumentan al aumentar la velocidad de avance y la velocidad de corte. A medida que aumenta la velocidad de alimentación, aumenta el grosor de la capa de corte, y a medida que aumenta la velocidad de corte, aumenta el número de fibras cortadas por unidad de tiempo, y la cantidad de desgaste de la herramienta aumenta rápidamente, por lo que la fuerza axial y el par aumentan.
La fuerza axial se puede dividir en la fuerza componente estática FS y la fuerza componente dinámica FD. La fuerza componente de la fuerza axial tiene diferentes efectos sobre el borde cortante, y la fuerza componente estática FS de la fuerza axial afecta el corte del borde del cincel. La fuerza del componente dinámico FD afecta principalmente el corte del filo principal, y la fuerza del componente dinámico FD tiene una mayor influencia en la rugosidad de la superficie que la fuerza del componente estático FS. La fuerza axial aumenta con la velocidad de avance, y la influencia de la velocidad de corte en la fuerza axial no es obvia. Además, en el caso de agujeros prefabricados, cuando la abertura es inferior a 0,4 mm, la fuerza del componente estático FS disminuye bruscamente con el aumento de la abertura, mientras que el componente dinámico FD disminuye con una tendencia al aplanamiento.
Debido a las diferentes propiedades de procesamiento de la matriz compuesta y las fibras de refuerzo, la resina de matriz y las fibras tienen diferentes efectos sobre la fuerza axial durante la perforación mecánica. Khashaba estudió los efectos de los tipos de matriz y fibra sobre las fuerzas axiales y el torque:
Se descubrió que la forma del haz de fibras tenía una influencia significativa en la fuerza axial, y el tipo de resina de matriz tenía poco efecto en la fuerza axial.
II. Desgaste y rotura de la broca
El desgaste de micro taladro compuesto de PCB incluye desgaste químico y desgaste por fricción. El desgaste químico es causado por el ataque químico del producto de pirólisis liberado del material de PCB en el aglutinante de Co en el material microperforado de carburo cementado WC-Co. A aproximadamente 300 ° C, esta reacción de erosión se ha vuelto más evidente. A una velocidad de perforación de menos de 150 mm / min, el desgaste químico ya no es la forma principal de desgaste, y la fricción y el desgaste se convierten en la forma principal de desgaste. El desgaste del microperforador de PCB también está relacionado con la relación entre la velocidad de corte, la velocidad de alimentación y el radio de bits con respecto al ancho del haz de fibras. La investigación de Inoue et al. Muestra que: La relación entre el radio del taladro y el ancho del haz de fibras (fibra de vidrio) tiene una gran influencia en la vida útil de la herramienta: cuanto mayor sea la relación, mayor será el ancho del haz de fibras del cortador y mayor será el desgaste de la herramienta.
En aplicaciones prácticas, la nueva broca perfora hasta 2.500 agujeros para rectificar.
Esmerilando la broca por primera vez, perforando hasta 2000 agujeros y volviéndola a pulir.
La segunda rectificación de la broca, que perfora hasta 1500 agujeros, debe rectificarse nuevamente,
La tercera vez que se perforó la broca, se perforaron hasta 1000 agujeros y se desechó la broca.
Durante el procesamiento de microporos de la PCB, la fuerza axial y el par aumentan con el aumento de la velocidad de alimentación y la profundidad de perforación, y la razón principal está relacionada con el estado de eliminación de la viruta. A medida que aumenta la profundidad de perforación, la descarga de la viruta es difícil: En este caso, la temperatura de corte aumenta, el material de resina se funde y une firmemente las fibras de vidrio y las piezas de lámina de cobre para formar un cuerpo de corte resistente. Este cuerpo de corte tiene afinidad con el material de matriz de PCB. Una vez que se produce un cuerpo de corte de este tipo, se detiene la descarga de las virutas, y la fuerza axial y el par aumentan bruscamente, lo que hace que la broca microporosa se rompa. La forma de fractura de la broca de microagujero de PCB tiene pandeo, rotura de torsión y pandeo y rotura de torsión, y generalmente ambos coexisten. La condición de ruptura es principalmente la obstrucción de virutas, que es un factor clave que causa el aumento del par de perforación. Reducir la fuerza axial y el par de corte es la clave para reducir la rotura del taladro de microagujeros.
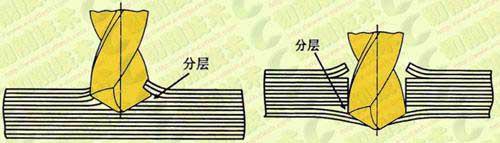
III. Forma de daño perforado
1, estratificación
Pueden ocurrir varios daños durante la perforación mecánica de laminados GFRP (reforzados con fibra de vidrio). El más grave de estos es la delaminación entre capas, que produce una fuerte caída en las propiedades del material alrededor de las paredes de los poros, y la fuerza axial ejercida por la punta de perforación es la principal causa de la delaminación. Las capas se pueden dividir en delaminación de perforación y delaminación de perforación. La delaminación de perforación es cuando el filo de la broca está en contacto con la placa de laminación, y la fuerza de corte que actúa en la dirección circunferencial en la dirección circunferencial está separada de la capa por la ranura de corte de la broca para formar una región en capas en la superficie de la placa de laminación. Perforar la delaminación es cuando la broca se acerca al fondo del laminado. Dado que el grosor del material sin cortar se hace cada vez más delgado, la capacidad de resistir la deformación se reduce aún más, y la estratificación se produce cuando la carga excede la adhesión entre los laminados. Esto sucedió antes de perforar el laminado. Las fuerzas axiales son la causa principal de la delaminación, y la velocidad de corte, el sustrato y el tipo de haz de fibras también tienen un efecto sobre la delaminación. La perforación y la delaminación de los compuestos epoxídicos disminuye con el aumento de la velocidad de perforación, y el grado de daño por delaminación es mayor que el de la perforación. Las principales medidas para reducir la estratificación son: Se utilizan tecnología de alimentación variable, agujeros guía preestablecidos y relleno. En la perforación no soportada, se usa un amortiguador viscoso o similar.
2, daño de la pared del agujero
Los microporos se perforan en el PCB compuesto, y varias formas de daño que ocurren alrededor de los agujeros dan como resultado una disminución en el aislamiento entre los agujeros y una ruptura en la capa de cobre de los agujeros después de la metalización de los agujeros. El ángulo relativo entre la dirección de corte y la dirección de la fibra, el grosor del haz de fibra de vidrio en la pared del agujero, la posición del punto de perforación en la tela de vidrio, etc., tienen diferentes efectos sobre el daño de la pared del agujero. El material compuesto de fibra de vidrio / epoxi se perforó con una broca de 1.0 mm de diámetro a una velocidad de 5000 rpm (8 capas de 90 ° escalonadas, 0.2 mm por capa). Las pruebas muestran que el grado de daño alrededor de cada agujero es diferente, y las capas de arrugas de fibra primera, tercera, quinta, séptima y octava son grandes, con una protuberancia máxima de 30 μm; Las 2, 4 y 6 capas de arrugas de fibra son menos prominentes, y el mínimo es inferior a 5 μm. En el área superpuesta del hilo de trama y el hilo de urdimbre, el grosor del haz de fibras es el más grande en el ángulo de la fibra de 45 °, y el ancho de daño de la pared del agujero es el más grande; En la región central, el ancho máximo de daño ocurre en un ángulo de aproximadamente 90 ° con respecto al ángulo de la fibra.
2, daño de la pared del agujero
Perfore microporos en una placa de circuito impreso compuesta. Varias formas de daño que ocurren alrededor de los agujeros dan como resultado una disminución en el aislamiento entre los agujeros y una ruptura en la capa de cobre de los agujeros después de la metalización de los agujeros. El ángulo relativo entre la dirección de corte y la dirección de la fibra, el grosor del haz de fibra de vidrio en la pared del agujero, la posición del punto de perforación en la tela de vidrio, etc., tienen diferentes efectos en el daño de la pared.
El material compuesto de fibra de vidrio / epoxi se perforó con una broca de 1.0 mm de diámetro a una velocidad de 5000 rpm (8 capas de 90 ° escalonadas, 0.2 mm por capa). Las pruebas muestran que el grado de daño alrededor de cada agujero es diferente, y las capas de arrugas de fibra primera, tercera, quinta, séptima y octava son grandes, con una protuberancia máxima de 30 μm; Las 2, 4 y 6 capas de arrugas de fibra son menos prominentes, y el mínimo es inferior a 5 μm. En el área superpuesta del hilo de trama y el hilo de urdimbre, el grosor del haz de fibras es el más grande en el ángulo de la fibra de 45 °, y el ancho de daño de la pared del agujero es el más grande; En la región central, el ancho máximo de daño ocurre en un ángulo de aproximadamente 90 ° con respecto al ángulo de la fibra.
La influencia de la declinación principal de la herramienta en la rugosidad de la superficie de la pared del agujero mecanizado: Cuando la declinación principal es de 30 °, la rugosidad de la superficie de la pared del poro es la más grande, hasta 50 μm.
3, manchas
Mechanical perforación de un material compuesto, ya que el taladro borde de cincel extruye material compuesto, y la fricción entre la pared del agujero cónica invertida. Y incrustado en pequeños chips de borde entre la broca y la pared de agujero de taladro con un gran número de calor de corte giratorio generado por la fricción con la masa fundida de resina. Y adhiérase a la lámina de cobre y a la pared del agujero en la capa intermedia o al agujero del compuesto para formar una mancha. El corte y rectificado adecuados del micro taladro pueden reducir la generación de manchas y reducir el índice de manchas.
4, rebabas
Cuando se perfora un material compuesto, debido a la transferencia de tensión, cuando la broca no alcanza el fondo del orificio, el material de refuerzo y el sustrato frente a la broca generan muchas grietas, de modo que el material de refuerzo se despega del sustrato. Tire del fenómeno se genera, lo que resulta en el material mejorada no se puede cortar a partir de las raíces. Estos materiales de refuerzo que no se cortan desde la raíz no se pueden quitar junto con las astillas cuando se taladran los agujeros, sino que se vierten hacia los bordes de los agujeros. La matriz se ablanda, fluye y se vuelve a condensar en el material de refuerzo vertido en el borde del agujero para formar rebabas. El tamaño de las rebabas de salida se ve afectado principalmente por la fuerza de perforación y la temperatura de perforación. La perforación con brocas de carburo, el cambio de geometrías y estructuras de herramientas, y las técnicas de perforación vibratoria pueden reducir las rebabas en la perforación compuesta.