Mecanizado de piezas de engranajes de cilíndrico de diente recto 40Cr
Palabras clave: mecanizado de piezas de engranajes, engranajes de 40Cr, engranajes de turbina, rectificado de engranajes, mecanizado de dientes, círculo invertido de dientes, temple de engranajes
El engranaje es un engranaje de dientes rectos de serie con un módulo de m = 3,5 mm, un número de dientes z = 63, y un ángulo de una forma del diente = 20 y ordm. Debido a que es el engranaje en la turbina de vapor de la aeronave, se requiere que su precisión de mecanizado sea alta.
Debido a que los engranajes en la turbina de vapor requieren una superficie de diente duro y un centro de diente duro, se selecciona el blanco forjado; Se usa 40Cr.
(1) Requisitos técnicos principales
1) El nivel de precisión se establece en el primer grupo de tolerancia con 6 niveles de precisión, y el error acumulado del tono del elemento detectado ΔFp; El segundo grupo de tolerancia es la precisión de nivel 5, y el error de perfil de diente del elemento de detección Δff y la desviación de la sección de base Δfpb; El tercer grupo de tolerancia es la precisión de nivel 5, y el elemento detectado error de dirección del diente ΔFβ; Medición de la desviación del grosor del diente Wk midiendo la longitud de la línea normal; Código de desviación M sobre el grosor del diente, código de desviación P bajo el grosor del diente; (En la indicación del nivel de precisión, la desviación del límite del grosor del diente se usa para controlar la reacción, que se indica mediante el código MP).
2) La profundidad de referencia de la superficie de referencia del blanco es la precisión del IT6; Existen requisitos para la desviación circular de la cara final con el eje del orificio interno en ambos extremos.
3) Rugosidad de la superficie Ra El orificio de referencia era de 0,8 μm, las dos caras finales tenían 1,6 μm, la superficie del diente era de 0,8 μm y la superficie cilíndrica superior del diente era de 3,2 μm.
(2) Se elige forjar en blanco para mejorar las propiedades mecánicas del material. La forja libre se usa en la producción de lotes pequeños, y la forja de troqueles se usa en la producción en masa.
(3) La selección de los principales métodos de procesamiento de superficie para el engranaje tiene un mayor nivel de precisión. Los principales métodos de acabado de superficie son los siguientes.
Agujero de referencia: molienda
Cara final: molienda
Superficie del diente: tallado - temple superficial - rectificado
El proceso general de mecanizado de engranajes rectos de turbina de aviones:
Número de documento de piezas y componentes de la tarjeta de proceso Tipo de producto
Nombre del producto Nombre de las piezas del engranaje Página total
No. Contenido del proceso Equipo Cantidad Tiempo de medición Cuota Observaciones
1, corte de la máquina de aserrado 1
2, cara del extremo del coche áspero, agujero interior y coche vertical biselado
3, inspección en blanco detector de defectos no destructivos
4, boca rugosa del coche, chaflán externo y torno frontal
5, horno de caja de tratamiento térmico (templado)
6, agujero interior del coche fino y torno frontal
7. Perforación: perforación vertical
8. Rectificado de la cara del extremo grande: rectificadora de superficie
9, escariado: perforadora
10, llave de extracción: máquina de brochado de ranura
11. Inspección intermedia: calibradores y reglas angulares
12. Hacer estándar de fábrica: banco de banco
13, tallado en bruto: talladora
14. Tallado fino: talladora
15. Procesamiento del extremo del diente: fresadora
16. Limpieza: máquina de limpieza
17. Prueba intermedia
18, Tratamiento térmico (endurecimiento superficial): horno de caja
19. Agujero interior de molienda fina: amoladora interior
20, limpieza: máquina de limpieza
21. Prueba intermedia
22, a juego: máquina de inspección
23, rectificado: rectificadora
24, limpieza: máquina de limpieza
25, a juego: Máquina de inspección
26. Escribe el número de emparejamiento
27, limpieza: máquina de limpieza
28. Prueba final
Aprobación de diseño de revisión
El proceso de procesamiento de engranajes generalmente pasa por las siguientes etapas: Tratamiento térmico de piezas en bruto, mecanizado de piezas en bruto de dientes, mecanizado de perfiles de dientes, mecanizado de extremos de dientes, tratamiento térmico de superficie de dientes, corrección de referencia de precisión y acabado de perfiles de dientes, etc.
La primera etapa de procesamiento es la etapa inicial en la que el blanco se mecaniza inicialmente. Dado que la precisión de la transmisión del engranaje está determinada principalmente por la precisión del perfil del diente y la uniformidad de la distribución del paso del diente, esto tiene una relación directa con la precisión de la referencia de posicionamiento (agujero y cara final) utilizada al cortar el diente. Por lo tanto, esta etapa es principalmente para preparar la referencia fina para la siguiente etapa de mecanizado de la forma del diente, de modo que la precisión del orificio interno y la superficie final del diente cumpla básicamente con los requisitos técnicos especificados. Además de mecanizar los puntos de referencia en esta etapa, el procesamiento de superficies menores que no sean el perfil del diente debe realizarse lo más tarde posible en esta fase.
La segunda etapa es el procesamiento de la forma del diente del engranaje.
Para engranajes que no requieren enfriamiento, esta etapa es generalmente la etapa de mecanizado final del engranaje. Después de esta etapa, los engranajes que cumplan completamente los requisitos de los dibujos deben ser mecanizados. Para los engranajes que requieren endurecimiento, la precisión del perfil del diente requerida para cumplir con el acabado final del perfil del diente debe mecanizarse en esta etapa, por lo que el mecanizado en esta etapa es una etapa crítica para garantizar la precisión del mecanizado del engranaje.
Se debe prestar especial atención.
Procesamiento final del diente:
A) círculo invertido
B) punta invertida
C) biselado
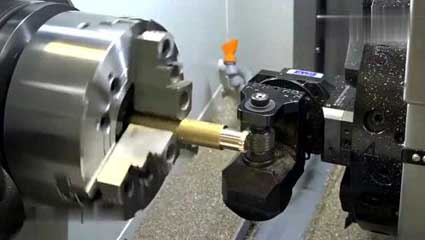
Figura 1 procesamiento final del diente del engranaje
Los métodos de mecanizado del extremo del engranaje son: Hay cuatro formas de círculo invertido, punto invertido, borde biselado y desbarbado. El engranaje después de achaflanado, achaflanado y achaflanado (Fig. 1). Es fácil participar cuando se mueve a lo largo del eje. El achaflanado del extremo del diente es el más utilizado. La figura 2 muestra el principio del achaflanado de la fresa. Cuando se redondea, el engranaje gira lentamente, y la cortadora de dedos se mueve alternativamente linealmente a lo largo del eje del engranaje mientras gira a alta velocidad. Cada vez que el engranaje gira un diente, la fresa se corresponde una vez, y los dos extremos completan el redondeo del extremo del diente en movimiento relativo. El procesamiento del extremo del diente debe organizarse antes del enfriamiento del perfil del diente.
La tercera etapa del procesamiento es la etapa de tratamiento térmico. En esta etapa, el tratamiento de temple de la superficie del diente se realiza principalmente para lograr el requisito de dureza especificado de la superficie del diente.
La etapa final del mecanizado es la fase de acabado del perfil del diente.
El propósito de esta etapa es corregir la deformación del perfil del diente causada por el enfriamiento del engranaje, mejorar aún más la precisión del perfil del diente y reducir la rugosidad de la superficie para lograr los requisitos de precisión final. En esta etapa, el datum de posicionamiento (agujero y cara final) debe recortarse primero, y el agujero interno y la cara final del engranaje se deformarán después del enfriamiento. Si el acabado en forma de agujero se realiza directamente usando tales agujeros y caras finales después del enfriamiento, es difícil lograr la precisión del engranaje. El acabado dentado con el posicionamiento de la superficie de referencia recortada hace que el posicionamiento sea preciso y confiable, y la distribución del equilibrio es relativamente uniforme, para lograr el propósito del acabado. El procesamiento del extremo del diente debe organizarse antes del enfriamiento del engranaje, generalmente después de fresar (insertar) los dientes.
El orificio de la base del engranaje se deforma después del enfriamiento. Para garantizar la calidad del acabado del perfil del diente, se debe corregir el orificio de la base.
La corrección del engranaje cilíndrico del orificio se puede usar para empujar orificios o rectificar agujeros, y el orificio de empuje tiene una alta productividad, y a menudo se usa para engranajes sin endurecer; Alta precisión de molienda, pero baja productividad. Para engranajes con alta dureza interna y alta dureza después del enfriamiento rápido, o engranajes con mayor diámetro interno y grosor más delgado, es mejor usar agujeros de rectificado.
Al rectificar agujeros, el círculo de indexación del engranaje generalmente está centrado, de modo que la desviación radial del anillo del engranaje después de los agujeros de rectificado es más pequeña, lo que es beneficioso para el rectificado o pulido posterior. Con el fin de mejorar la productividad, algunas fábricas también han logrado buenos resultados al reemplazar los orificios de rectificado con perforación de diamante.
El engranaje es un engranaje de dientes rectos de serie con un módulo de m = 3,5 mm, un número de dientes z = 63, y un ángulo de una forma del diente = 20 y ordm. Debido a que es el engranaje en la turbina de vapor de la aeronave, se requiere que su precisión de mecanizado sea alta.
Debido a que los engranajes en la turbina de vapor requieren una superficie de diente duro y un centro de diente duro, se selecciona el blanco forjado; Se usa 40Cr.
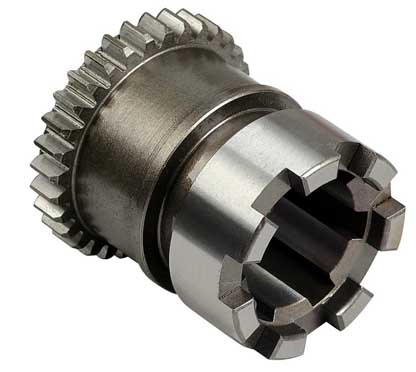
(1) Requisitos técnicos principales
1) El nivel de precisión se establece en el primer grupo de tolerancia con 6 niveles de precisión, y el error acumulado del tono del elemento detectado ΔFp; El segundo grupo de tolerancia es la precisión de nivel 5, y el error de perfil de diente del elemento de detección Δff y la desviación de la sección de base Δfpb; El tercer grupo de tolerancia es la precisión de nivel 5, y el elemento detectado error de dirección del diente ΔFβ; Medición de la desviación del grosor del diente Wk midiendo la longitud de la línea normal; Código de desviación M sobre el grosor del diente, código de desviación P bajo el grosor del diente; (En la indicación del nivel de precisión, la desviación del límite del grosor del diente se usa para controlar la reacción, que se indica mediante el código MP).
2) La profundidad de referencia de la superficie de referencia del blanco es la precisión del IT6; Existen requisitos para la desviación circular de la cara final con el eje del orificio interno en ambos extremos.
3) Rugosidad de la superficie Ra El orificio de referencia era de 0,8 μm, las dos caras finales tenían 1,6 μm, la superficie del diente era de 0,8 μm y la superficie cilíndrica superior del diente era de 3,2 μm.
(2) Se elige forjar en blanco para mejorar las propiedades mecánicas del material. La forja libre se usa en la producción de lotes pequeños, y la forja de troqueles se usa en la producción en masa.
(3) La selección de los principales métodos de procesamiento de superficie para el engranaje tiene un mayor nivel de precisión. Los principales métodos de acabado de superficie son los siguientes.
Agujero de referencia: molienda
Cara final: molienda
Superficie del diente: tallado - temple superficial - rectificado
El proceso general de mecanizado de engranajes rectos de turbina de aviones:
Número de documento de piezas y componentes de la tarjeta de proceso Tipo de producto
Nombre del producto Nombre de las piezas del engranaje Página total
No. Contenido del proceso Equipo Cantidad Tiempo de medición Cuota Observaciones
1, corte de la máquina de aserrado 1
2, cara del extremo del coche áspero, agujero interior y coche vertical biselado
3, inspección en blanco detector de defectos no destructivos
4, boca rugosa del coche, chaflán externo y torno frontal
5, horno de caja de tratamiento térmico (templado)
6, agujero interior del coche fino y torno frontal
7. Perforación: perforación vertical
8. Rectificado de la cara del extremo grande: rectificadora de superficie
9, escariado: perforadora
10, llave de extracción: máquina de brochado de ranura
11. Inspección intermedia: calibradores y reglas angulares
12. Hacer estándar de fábrica: banco de banco
13, tallado en bruto: talladora
14. Tallado fino: talladora
15. Procesamiento del extremo del diente: fresadora
16. Limpieza: máquina de limpieza
17. Prueba intermedia
18, Tratamiento térmico (endurecimiento superficial): horno de caja
19. Agujero interior de molienda fina: amoladora interior
20, limpieza: máquina de limpieza
21. Prueba intermedia
22, a juego: máquina de inspección
23, rectificado: rectificadora
24, limpieza: máquina de limpieza
25, a juego: Máquina de inspección
26. Escribe el número de emparejamiento
27, limpieza: máquina de limpieza
28. Prueba final
Aprobación de diseño de revisión
El proceso de procesamiento de engranajes generalmente pasa por las siguientes etapas: Tratamiento térmico de piezas en bruto, mecanizado de piezas en bruto de dientes, mecanizado de perfiles de dientes, mecanizado de extremos de dientes, tratamiento térmico de superficie de dientes, corrección de referencia de precisión y acabado de perfiles de dientes, etc.
La primera etapa de procesamiento es la etapa inicial en la que el blanco se mecaniza inicialmente. Dado que la precisión de la transmisión del engranaje está determinada principalmente por la precisión del perfil del diente y la uniformidad de la distribución del paso del diente, esto tiene una relación directa con la precisión de la referencia de posicionamiento (agujero y cara final) utilizada al cortar el diente. Por lo tanto, esta etapa es principalmente para preparar la referencia fina para la siguiente etapa de mecanizado de la forma del diente, de modo que la precisión del orificio interno y la superficie final del diente cumpla básicamente con los requisitos técnicos especificados. Además de mecanizar los puntos de referencia en esta etapa, el procesamiento de superficies menores que no sean el perfil del diente debe realizarse lo más tarde posible en esta fase.
La segunda etapa es el procesamiento de la forma del diente del engranaje.
Para engranajes que no requieren enfriamiento, esta etapa es generalmente la etapa de mecanizado final del engranaje. Después de esta etapa, los engranajes que cumplan completamente los requisitos de los dibujos deben ser mecanizados. Para los engranajes que requieren endurecimiento, la precisión del perfil del diente requerida para cumplir con el acabado final del perfil del diente debe mecanizarse en esta etapa, por lo que el mecanizado en esta etapa es una etapa crítica para garantizar la precisión del mecanizado del engranaje.
Se debe prestar especial atención.
Procesamiento final del diente:
A) círculo invertido
B) punta invertida
C) biselado
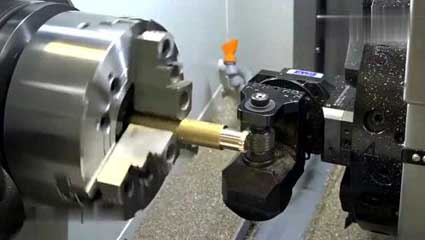
Figura 1 procesamiento final del diente del engranaje
Los métodos de mecanizado del extremo del engranaje son: Hay cuatro formas de círculo invertido, punto invertido, borde biselado y desbarbado. El engranaje después de achaflanado, achaflanado y achaflanado (Fig. 1). Es fácil participar cuando se mueve a lo largo del eje. El achaflanado del extremo del diente es el más utilizado. La figura 2 muestra el principio del achaflanado de la fresa. Cuando se redondea, el engranaje gira lentamente, y la cortadora de dedos se mueve alternativamente linealmente a lo largo del eje del engranaje mientras gira a alta velocidad. Cada vez que el engranaje gira un diente, la fresa se corresponde una vez, y los dos extremos completan el redondeo del extremo del diente en movimiento relativo. El procesamiento del extremo del diente debe organizarse antes del enfriamiento del perfil del diente.
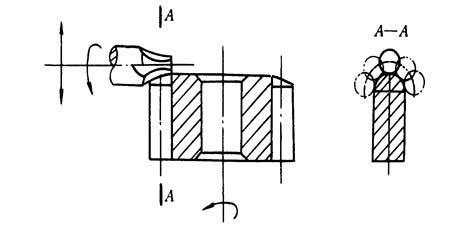
Figura 2 Círculo de punta de diente de engranaje
La tercera etapa del procesamiento es la etapa de tratamiento térmico. En esta etapa, el tratamiento de temple de la superficie del diente se realiza principalmente para lograr el requisito de dureza especificado de la superficie del diente.
La etapa final del mecanizado es la fase de acabado del perfil del diente.
El propósito de esta etapa es corregir la deformación del perfil del diente causada por el enfriamiento del engranaje, mejorar aún más la precisión del perfil del diente y reducir la rugosidad de la superficie para lograr los requisitos de precisión final. En esta etapa, el datum de posicionamiento (agujero y cara final) debe recortarse primero, y el agujero interno y la cara final del engranaje se deformarán después del enfriamiento. Si el acabado en forma de agujero se realiza directamente usando tales agujeros y caras finales después del enfriamiento, es difícil lograr la precisión del engranaje. El acabado dentado con el posicionamiento de la superficie de referencia recortada hace que el posicionamiento sea preciso y confiable, y la distribución del equilibrio es relativamente uniforme, para lograr el propósito del acabado. El procesamiento del extremo del diente debe organizarse antes del enfriamiento del engranaje, generalmente después de fresar (insertar) los dientes.
El orificio de la base del engranaje se deforma después del enfriamiento. Para garantizar la calidad del acabado del perfil del diente, se debe corregir el orificio de la base.
La corrección del engranaje cilíndrico del orificio se puede usar para empujar orificios o rectificar agujeros, y el orificio de empuje tiene una alta productividad, y a menudo se usa para engranajes sin endurecer; Alta precisión de molienda, pero baja productividad. Para engranajes con alta dureza interna y alta dureza después del enfriamiento rápido, o engranajes con mayor diámetro interno y grosor más delgado, es mejor usar agujeros de rectificado.
Al rectificar agujeros, el círculo de indexación del engranaje generalmente está centrado, de modo que la desviación radial del anillo del engranaje después de los agujeros de rectificado es más pequeña, lo que es beneficioso para el rectificado o pulido posterior. Con el fin de mejorar la productividad, algunas fábricas también han logrado buenos resultados al reemplazar los orificios de rectificado con perforación de diamante.