Mecanizado de piezas de aleación dura
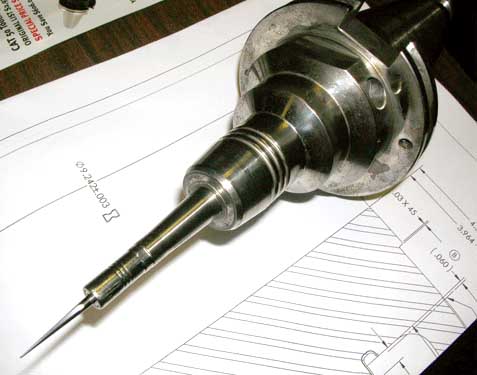
A diferencia de los conceptos tradicionales, no es difícil mecanizar una pieza de trabajo endurecida por temple a 5 μm con la máquina herramienta adecuada y la herramienta adecuada. En la actualidad, los proveedores de herramientas han desarrollado nuevas herramientas que pueden soportar tales condiciones de mecanizado, y los fabricantes de máquinas herramienta también han producido tornos CNC que cumplen con la rigidez requerida para estas nuevas herramientas. Al mismo tiempo, el torneado de material duro puede promover la producción a partir de los siguientes aspectos.
I. El torneado de material duro ahorra tiempo en comparación con la molienda
La especificación del tamaño final consume menos tiempo porque la tasa de corte de metal para torneado es más alta que para el rectificado. Además, después de una pieza de trabajo cargado de fijación abrazadera, puede ser procesada en varios procesos. El operador puede completar todo el mecanizado en una carga y descarga, logrando así una producción justo a tiempo. Reducir costos y ahorrar tiempo es ahorrar dinero. Además, el uso de un torno en lugar de una máquina rectificadora significa una inversión total menor en la máquina herramienta.
El torneado de materiales duros de mejor calidad es mucho mejor que el rectificado en términos de precisión dimensional y rugosidad de la superficie. Puede convertir la mayoría de los materiales duros a una tolerancia total de 5 μm con una rugosidad superficial Ra de 0.1 μm. Por supuesto, una calidad de superficie tan precisa requiere medidas especiales, pero Ra 0.15μm-Ra0.2μm es muy fácil.
Menos proceso de torneado de material duro elimina muchas formas de rectificado, así como pulido y otras operaciones de acabado. No solo ahorra costos de procesamiento, sino que además no requiere subcontratación parcial para ayudar en el procesamiento.
Al desperdiciar materiales menos duros, hay muy poco desperdicio en el torneado. Debido a que el refrigerante utilizado es el mismo que el giro normal, no es necesario agregar refrigerante adicional, lo que genera un pequeño desperdicio. Además, el torneado en seco se puede hacer sin refrigerante para evitar el desperdicio de refrigerante y residuos de piezas de trabajo. El torneado de materiales duros también puede evitar el problema de moler los residuos, es decir, el laborioso y costoso problema de recuperación y eliminación de residuos.
II. Requisitos de potencia y rigidez.
Para lograr los mejores resultados en el torneado de materiales duros, es importante la combinación correcta de máquinas herramienta y herramientas. Por ejemplo, en un proceso de torneado en bruto, cuando se usa una cuchilla de cerámica y se usa una cantidad de corte de 0.28 mm / min y una profundidad de corte de 1.9 mm, es necesario generar una carga del 65% para un motor de 15 kW. El torno gira un extremo de la pieza de acero templado de 50 mm de diámetro a unos 25 mm, mientras que también gira la superficie cónica, el radio del arco y otras formas complejas.
Aunque se requiere alta potencia para una profundidad de corte grande, muchos usuarios encuentran que este no es el caso en la mayoría de los casos. Porque el procesamiento de la mayoría de los materiales duros está terminando. En general, se puede girar en un torno de tornillo común, dejando un margen de 0.25-0.38 mm, y luego terminar con una tecnología de torneado de material duro después del tratamiento térmico. Otro requisito para el torneado de material duro es la rigidez, que puede causar temblores en cualquier parte de la máquina herramienta, herramienta y pieza de trabajo, y la máquina herramienta si carece de rigidez. Para poder lograr precisión y tolerancias dimensionales en comparación con el rectificado, la máquina debe tener una rigidez particularmente alta de la cama. Las camas de hierro fundido tradicionales no son adecuadas para el torneado de materiales duros en comparación con los polímeros de granito. El lecho de polímero de granito es 20 veces más resistente a las vibraciones que el hierro fundido. La vibración en el eje principal es solo 1/3 o menos del eje principal montado en la cama de hierro fundido.
Reducir la cantidad de voladizo es otra forma de reducir la vibración. En teoría, el dispositivo de sujeción de la pieza de trabajo debe mantener la pieza de trabajo lo más cerca posible del cojinete del husillo, y la herramienta debe estar lo más cerca posible del cuerpo de la torreta sin el estado de voladizo. Para este propósito, un torno en el que el portabrocas se puede sujetar directamente en el husillo. El soporte del collar mantiene la pieza de trabajo alejada del rodamiento del husillo, que no solo tiene una pequeña fuerza de sujeción, sino que también aumenta la posibilidad de vibración.
III. Nueva variedad de herramientas.
Es bueno mecanizar acero duro con cuchillos de cerámica y herramientas de nitruro de boro cúbico (CBN). Estas herramientas se han desarrollado rápidamente en un corto período de tiempo, y algunos fabricantes de herramientas afirman que:
Siempre que la máquina se use correctamente, su herramienta puede reducir el tiempo en un 300% más que el rectificado y mejorar la precisión de corte.
Los cuchillos de cerámica recomendados por estos proveedores tienen un ángulo de inclinación negativo y un gran chaflán en T que agrega presión solo en la interfaz de la herramienta y la pieza de trabajo. Por el contrario, el CBN puede tener o no un chaflán en T tan desfavorable dependiendo de las condiciones específicas de la pieza de trabajo. Por ejemplo, cuando se usa CBN para el corte interrumpido, se requiere un gran chaflán en T para resistir la vibración.
El uso de herramientas de cerámica se está volviendo más común que el CBN debido a su menor costo y debido a sus filos de corte más grandes. Sin embargo, son extremadamente susceptibles a la fisuración por calor. Además, si la cuchilla no está correctamente rectificada, no es aconsejable realizar cortes interrumpidos. Aunque CBN es mucho más costoso que la cerámica, tiene un rendimiento de corte mucho mejor, una mayor precisión de procesamiento y una vida útil más larga.
Elegir entre estos dos materiales de herramienta es cómo adaptar el material de la pieza de trabajo, la geometría y la velocidad de corte y la velocidad de avance. Algunos usuarios generalmente no se apegan a la comparación uno por uno, sino al costo del mismo procesamiento para la herramienta y el principio de cuánto beneficio puede generarse. Estos usuarios usan un cuchillo de cerámica barato para cortar las escamas y las escamas que quedan en el tratamiento térmico. Luego, termine con una mejor herramienta CBN. En general, si la profundidad de endurecimiento es mayor que la profundidad del material a cuidar, es mejor usar CBN.
IV. Elija el método de procesamiento correcto
Desde un punto de vista práctico, el torneado de material duro es un proceso estrechamente relacionado con las características de la pieza de trabajo. Es especialmente adecuado para cortar piezas de trabajo con geometrías complejas como arcos intrincados, ángulos y radios. Puede utilizar un método de torneado de programación de punta única para completar el mecanizado de forma rápida y económica sin tener que comprar una rueda de formación para este propósito. Como regla general, la mayoría del torneado de material duro se realiza a una velocidad de corte de 91-150 m / min y una velocidad de avance de 0.05-0.13 mm / min. La profundidad de la cuchilla de corte es generalmente de 0.08-0.5 mm. Por lo tanto, cómo controlar la pureza del material, así como los procesos de tratamiento térmico, desbaste y formación antes del torneado, es el factor determinante de la precisión que se puede lograr con este procesamiento. Si la dureza de la pieza de trabajo fluctúa solo tres valores de dureza Rockwell (por ejemplo), la presión de corte de la herramienta cambiará lo suficiente como para garantizar que no pueda garantizar la precisión dimensional de 5 μm. La rigidez inestable y la profundidad de corte desigual pueden dañar este proceso. Por lo tanto, se deben usar materiales calificados para mantener una tasa constante de remoción de metales y para asegurar que la dureza del tratamiento térmico esté dentro de ± 1 o ± 2 HRC.
La relación longitud / diámetro de la pieza de trabajo también afecta la capacidad de la máquina para mantener la precisión de la tolerancia. Un torno horizontal típico generalmente logra una precisión bastante estricta cuando el contrapunto se usa para una pieza de trabajo blanda con una relación de longitud a diámetro de 5: 1 a 6: 1. Debido a la dureza de la pieza de trabajo, el ángulo de inclinación negativo de la herramienta y el chaflán en T necesario para cortar el material duro, la presión sobre la herramienta es bastante grande. Por lo tanto, cuando la pieza de trabajo se apoya sin contrapunto, la relación longitud / diámetro de la pieza de trabajo debe limitarse a 3: 1-4: 1.
Por supuesto, esta limitación variará con el proceso del proceso, es decir, con los requisitos de material, dureza y rugosidad y precisión de la pieza de trabajo. No hemos usado el soporte del contrapunto antes, y girar la pieza de trabajo con un diámetro de 13 mm y una longitud de 64 mm es una precisión muy pobre.
El contrapunto puede desempeñar un papel, pero es una panacea para todos los problemas. Por ejemplo, la punta no puede evitar el ruido de una pieza de trabajo que tiene un diámetro de 25 mm y una longitud de 300 mm. Para este tipo de pieza de trabajo, solo puede usar rectificado. Para garantizar tolerancias más estrictas que 0.005 mm, es mejor utilizar el proceso de molienda. Aunque el torneado de material duro no puede reemplazar por completo el rectificado. Pero puede reemplazar una parte considerable. En particular, piezas de trabajo con una pequeña relación de longitud y diámetro y una forma complicada.