Torneado
¿Qué está cambiando?
El giro se refiere al procesamiento del torno, que es parte del procesamiento mecánico. El mecanizado de torno utiliza principalmente herramientas de torneado para girar la pieza de trabajo. Los tornos se utilizan principalmente para mecanizar ejes, discos, vainas y otras piezas de trabajo con superficies giratorias. Son el tipo de máquina herramienta más utilizado en la fabricación de maquinaria y fábricas de reparación.
El giro se refiere al procesamiento del torno, que es parte del procesamiento mecánico. El mecanizado de torno utiliza principalmente herramientas de torneado para girar la pieza de trabajo. Los tornos se utilizan principalmente para mecanizar ejes, discos, vainas y otras piezas de trabajo con superficies giratorias. Son el tipo de máquina herramienta más utilizado en la fabricación de maquinaria y fábricas de reparación.
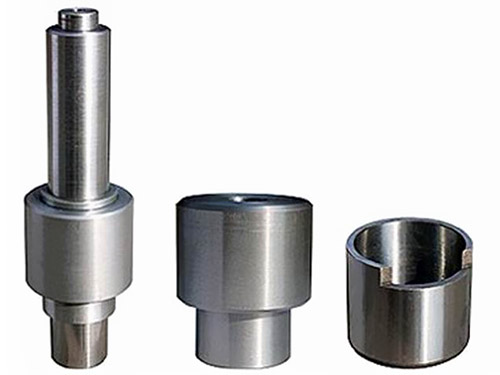
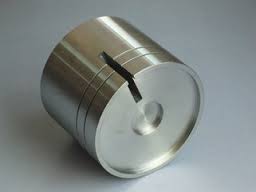
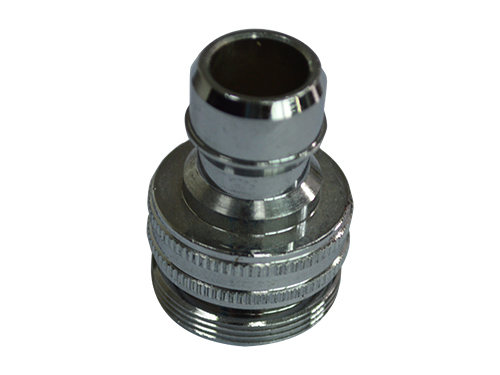
Resumen técnico
Es en el torno que la forma y el tamaño del espacio en blanco cambian por el movimiento de rotación de la pieza de trabajo y el movimiento lineal o curvo de la herramienta, y se procesa para cumplir los requisitos de los dibujos.
El torneado es un método para cortar una pieza de trabajo girando una pieza de trabajo en relación con una herramienta en un torno. La energía de corte del torneado la proporciona principalmente la pieza de trabajo en lugar de la herramienta. El torneado es el método de corte más básico y común y ocupa una posición muy importante en la producción. El torneado es adecuado para mecanizar superficies rotatorias. La mayoría de las piezas de trabajo con superficie giratoria se pueden mecanizar girando. Como las superficies cilíndricas internas y externas, las superficies cónicas internas y externas, las superficies de los extremos, las ranuras, los hilos y las superficies rotatorias de formación, las herramientas utilizadas son principalmente herramientas de torneado. Los tornos son la categoría más utilizada en todo tipo de máquinas herramienta para cortar metales, y representan aproximadamente el 50% del número total de máquinas herramienta. El torno se puede utilizar para hacer girar una pieza de trabajo con una herramienta de torneado, pero también puede usar taladros, escariadores, roscas y herramientas de moleteado para taladrar, escariar, roscar y moletear. De acuerdo con las diferentes características del proceso, el diseño y las características estructurales, los tornos se pueden dividir en tornos horizontales, tornos de tipo piso, tornos verticales, tornos de torreta y tornos de duplicación, la mayoría de los cuales son tornos horizontales.
Problema técnico
El mecanizado de torneado es el tipo más utilizado en la industria de fabricación de maquinaria. La cantidad de tornos es grande, la cantidad de personas es grande y el rango de procesamiento es amplio. Hay muchas herramientas y accesorios utilizados, por lo tanto, la seguridad y los problemas técnicos de torneado son especialmente importantes. Las tareas clave son las siguientes: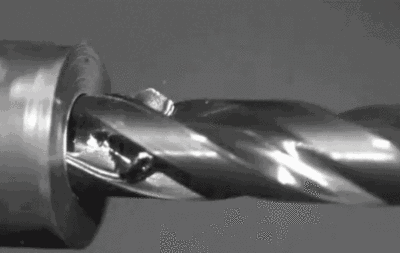
1, daños por viruta y medidas de protección.
Las piezas de acero mecanizadas en el torno son más flexibles, y la viruta producida durante el torneado es de plástico rizado y tiene bordes afilados. En el corte a alta velocidad de piezas de acero, se forman puntos rojos y largos, que son extremadamente fáciles de doler y con frecuencia se enrollan alrededor de las piezas de trabajo, herramientas de torneado y portaherramientas. Por lo tanto, el gancho debe limpiarse o quitarse de manera oportuna en el trabajo. Si es necesario, se debe detener y borrar. Sin embargo, no debe ser eliminado o roto a mano. Con el fin de evitar el daño por viruta, a menudo se adoptan la rotura de virutas, el control del flujo de virutas y diversos deflectores de protección. La medida de ruptura de viruta es rectificar rompevirutas o pasos en la herramienta de torneado; Utilice un rompevirutas apropiado y sujete mecánicamente la herramienta.
2, montaje de la pieza de trabajo.
En el proceso de torneado, hay muchos accidentes, como daños a la máquina herramienta debido a una instalación incorrecta de la pieza de trabajo, a romper o romper la herramienta y a caerse o salir volando de la pieza de trabajo.
Por lo tanto, para garantizar una producción segura de torneado, se debe prestar especial atención al cargar las piezas de trabajo. Para piezas de diferentes tamaños y formas, se deben usar accesorios adecuados, independientemente de la conexión de mandriles de tres mordazas y cuatro garras o accesorios especiales y husillos. Las piezas de trabajo se deben sujetar y sujetar con abrazaderas, y las piezas de trabajo grandes se pueden sujetar con abrazaderas y manguitos.
Cuando la pieza de trabajo se gira a alta velocidad y se aplica la fuerza de corte, no se desplaza, se cae y no se arroja. Si es necesario, puede ser reforzado por el centro superior y el marco central. Bloqueo, inmediatamente después de quitar la llave.
3, operación segura.
Antes del trabajo, debemos inspeccionar completamente la máquina y confirmar que es para usarla. El montaje de la pieza de trabajo y la herramienta garantiza que la posición sea correcta, firme y confiable. Durante el proceso de mecanizado, la herramienta debe detenerse al cambiar la herramienta, al cargar y descargar la pieza de trabajo y al medir la pieza de trabajo. La pieza de trabajo no debe tocarse a mano ni limpiarse con algodón al girar. Para seleccionar correctamente la velocidad de corte, la velocidad de alimentación y la profundidad de tensión, no se permite el mecanizado con sobrecarga. No se deben colocar piezas de trabajo, abrazaderas de trabajo y otros residuos en el soporte de la herramienta y la superficie de la cama. Cuando use un rallador, mueva la herramienta de giro a una posición segura con la mano derecha en la parte delantera y la mano izquierda en la parte posterior para evitar que las mangas se involucren. La máquina herramienta debe tener a alguien responsable del uso y mantenimiento, y otro personal no debe usarla.
Precauciones
El proceso de mecanizado con torno CNC es similar al de los tornos ordinarios. Sin embargo, debido a que el torno CNC se instala una vez y todas las operaciones de torneado se completan automáticamente, se deben tener en cuenta los siguientes aspectos.
1. Elección razonable de la cantidad de corte:
Para el corte de metales de alta eficiencia, los materiales a mecanizar, las herramientas de corte y las condiciones de corte son tres factores principales. Estos determinan el tiempo de procesamiento, la vida útil de la herramienta y la calidad del procesamiento. El método de procesamiento económico y efectivo debe ser una elección razonable de las condiciones de corte. Los tres elementos de las condiciones de corte: velocidad de corte, velocidad de avance y profundidad de corte causan daño a la herramienta directamente. Con el aumento de la velocidad de corte, la temperatura de la punta de la herramienta aumentará y producirá desgaste mecánico, químico y térmico. La velocidad de corte aumentó en un 20%, la vida de la herramienta se reducirá en 1/2. La condición de alimentación y el desgaste detrás de la herramienta se producen dentro de un rango muy pequeño. Sin embargo, la velocidad de alimentación es grande, la temperatura de corte aumenta y el desgaste posterior es grande. Tiene menos influencia en la herramienta que la velocidad de corte. El efecto del corte profundo en la herramienta de corte Aunque no hay velocidad de corte y cantidad de alimentación, cuando la profundidad de corte es pequeña, el material a cortar tiene una capa endurecida, lo que también afecta la vida útil de la herramienta de corte. El usuario selecciona la velocidad de corte que se utilizará en función del material que se va a procesar, la dureza, las condiciones de corte, el tipo de material, la cantidad de alimentación, la profundidad de corte y similares. La selección de las condiciones de procesamiento más adecuadas se selecciona sobre la base de estos factores. El desgaste regular y estable es la condición ideal para alcanzar la esperanza de vida. Sin embargo, en la operación real, la elección de la vida útil de la herramienta está relacionada con el desgaste de la herramienta, el tamaño de la máquina que se procesa, la calidad de la superficie, el ruido de corte y el calor de procesamiento. Al determinar las condiciones de procesamiento, es necesario realizar una investigación de acuerdo con las condiciones reales. Para materiales difíciles de mecanizar como acero inoxidable y aleaciones resistentes al calor, se pueden usar refrigerantes o cuchillas rígidas.
2. Elección razonable de herramientas:
(1) Al desbastar, seleccione una herramienta con alta resistencia y buena durabilidad para cumplir con los requisitos de una gran profundidad de corte y una gran cantidad de avance durante el desbaste.
(2) Cuando termine de girar, es necesario seleccionar herramientas con alta precisión y buena durabilidad para garantizar la precisión del procesamiento.
(3) Para reducir el tiempo de cambio de la herramienta y facilitar el ajuste de la herramienta, la abrazadera y la cuchilla deben usarse lo más lejos posible.
3. Razonablemente seleccione el accesorio: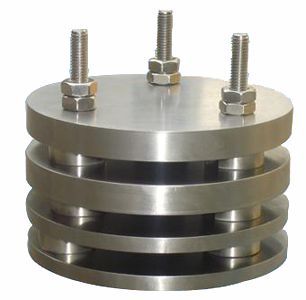
(1) Intente usar un accesorio universal para sujetar la pieza de trabajo para evitar el uso de accesorios especiales;
(2) La referencia de posicionamiento de la pieza coincide para reducir el error de posicionamiento.
4. Determine la ruta de procesamiento:
La ruta de procesamiento es la trayectoria y la dirección de la herramienta con respecto a la pieza en el proceso de mecanizado de herramienta de máquina controlada por índice.
(1) Debe ser capaz de garantizar la precisión del procesamiento y los requisitos de rugosidad de la superficie;
(2) La ruta de procesamiento debe acortarse tanto como sea posible para reducir el tiempo de viaje inactivo de la herramienta.
5. Ruta de procesamiento y asignación de mecanizado:
Bajo la condición de que los tornos CNC no hayan alcanzado un uso universal, generalmente, la tolerancia excesiva para los espacios en blanco, especialmente la tolerancia para forjar y fundir la cubierta dura, debe mecanizarse en tornos comunes. Si debe utilizar el procesamiento del torno CNC, debe prestar atención a la disposición flexible del programa.
6. Puntos de instalación del artefacto:
La conexión entre el plato hidráulico y el cilindro de sujeción hidráulico se logra mediante la barra de tracción. Los puntos clave de la sujeción del mandril hidráulico son los siguientes:
Primero quite la tuerca del cilindro hidráulico con una mano, retire el tubo de extracción y retire el portabrocas del extremo trasero del eje. Luego quite el tornillo de fijación del portabrocas para quitar el portabrocas.
Reglas generales
Procedimientos generales de procesamiento de torneado (JB / T9168.2-1998)
Configuración de herramientas
1) El mango de la herramienta se extiende fuera del portaherramientas y no debe ser demasiado largo. La longitud general no debe exceder 1,5 veces la altura de la barra de herramientas (a excepción del orificio, ranura, etc.)
2) La línea central del portaherramientas del torno debe ser perpendicular o paralela a la dirección de corte.
3) Ajuste de la altura de la punta del cuchillo:
(1) Al girar una cara, girar una superficie cónica, girar roscas, girar una superficie de formación y cortar una pieza de trabajo sólida, el borde de corte debería estar a la misma altura que el eje de la pieza de trabajo.
(2) La rueda de desbaste, el orificio de acabado y la punta de la herramienta generalmente deben ser un poco más altos que el eje de la pieza de trabajo.
(3) Cuando se cortan el eje delgado, el agujero áspero y la pieza de trabajo hueca, la punta de la herramienta generalmente debe ser un poco más baja que el eje de la pieza de trabajo.
4) La bisectriz del ángulo de rosca de la herramienta de torneado de roscas debe ser perpendicular al eje de la pieza de trabajo.
5) Al insertar la herramienta de torneado, la arandela debajo de la barra de herramientas debe ser pequeña y plana, y el tornillo que presiona la herramienta de torneado debe apretarse.
Montaje de la pieza de trabajo
1) Cuando se utiliza un mandril autocentrante de tres mordazas para sujetar piezas de trabajo para desbaste o acabado, si el diámetro de la pieza de trabajo es inferior a 30 mm, la longitud del voladizo no debe ser mayor de 5 veces el diámetro. Si el diámetro de la pieza de trabajo es mayor a 30 mm, su longitud de saliente no debe ser más de 3 veces el diámetro.
2) Cuando se utiliza un portabrocas de una sola acción, placa frontal, ángulo de hierro (placa de doblez), etc. de cuatro mordazas para sujetar piezas pesadas de forma irregular, se debe agregar peso.
3) Al mecanizar una pieza de trabajo de eje en la punta del eje, ajuste el eje central del contrapunto para que coincida con el eje del eje del torno antes de girar.
4) Al mecanizar ejes delgados entre los dos centros superiores, se debe usar un portaherramientas o un marco central. En el proceso de procesamiento, se debe prestar atención al ajuste de la rigidez superior. El centro muerto superior y el marco central deben prestar atención a la lubricación.
5) Cuando se usa el contrapunto, la manga debe extenderse lo más corto posible para reducir la vibración.
6) Cuando se sujeta el torno vertical, la superficie de apoyo es pequeña y la altura de la pieza de trabajo es alta, se debe usar la uña elevada y la pieza de trabajo debe presionarse en el lugar apropiado con una barra de tracción o placa de presión.
7) Al girar ruedas y forjados de fundición, la superficie sin terminar debe corregirse para garantizar un espesor de pared uniforme después del procesamiento.
Torneado
1) Al girar el eje del escalón, para garantizar la rigidez durante el torneado, generalmente la parte de mayor diámetro debe girarse primero, y la parte de menor diámetro debe girarse más tarde.
2) cuando el eje tiene ranuras de corte en una pieza de trabajo, a realizar antes del acabado, a fin de evitar la deformación de la pieza de trabajo.
3) Cuando está bien girar un eje roscado,
Después de enhebrar, la parte no roscada se gira con precisión.
4) antes de taladrar, la cara final de la pieza de trabajo debe estar plana. Taladre el orificio central primero si es necesario.
5) Cuando se perforan orificios profundos, el orificio piloto generalmente se perfora primero.
6) Al girar agujeros (Φ10-Φ20) mm, el diámetro del vástago de la herramienta debe ser de 0.6-0.7 veces el diámetro del orificio mecanizado; Cuando el diámetro del orificio es mayor que 20 mm, se debe usar el portacuchillas con cabeza de sujeción.
7) Al girar un tornillo de cabezales múltiples o de cabezales múltiples, después de ajustar los engranajes de cambio, realice un corte de prueba.
8) Cuando utilice el torno automático, ajuste la posición relativa de la herramienta y la pieza de trabajo de acuerdo con la tarjeta de ajuste de la máquina herramienta. Después del ajuste, es necesario llevar a cabo el giro de prueba. Después de calificar la primera pieza, puede procesarse; Durante el proceso de mecanizado, el desgaste de la herramienta, el tamaño de la pieza de trabajo y la rugosidad de la superficie siempre se tienen en cuenta.
9) Al encender un torno vertical, la viga no debe moverse libremente cuando se ajusta el portacuchillas. Al encender el torno vertical, cuando se ajusta el soporte de la herramienta, no se permite mover el travesaño a voluntad.
10) Cuando la superficie relevante de la pieza de trabajo tiene tolerancias posicionales, el giro se realiza en una sola sujeción tanto como sea posible.
11) Al girar un diente de dientes rectos, el orificio y la cara del extremo de referencia se deben mecanizar en una sujeción. Si es necesario, la línea de marcado debe dibujarse cerca del final del círculo de indexación del engranaje.
Error de compensación
La tecnología moderna de fabricación de maquinaria se está moviendo hacia la alta eficiencia, alta calidad, alta precisión, alta integración y alta inteligencia. La tecnología de mecanizado de precisión y ultraprecisión se ha convertido en el componente y la dirección de desarrollo más importante en la fabricación de maquinaria moderna, y se ha convertido en una tecnología clave para mejorar la competitividad internacional. El error de mecanizado por torneado se ha convertido en un tema candente de investigación con la extensa aplicación del mecanizado de precisión. Dado que los errores térmicos y los errores geométricos representan la mayoría de los diversos errores en la máquina herramienta, la reducción de estos dos errores, en particular los errores térmicos, se ha convertido en el objetivo principal. La Tecnología de Compensación de Errores (ECT) surgió con el desarrollo continuo de la ciencia y la tecnología. Las pérdidas causadas por la deformación térmica de la máquina herramienta son considerables. Por lo tanto, es extremadamente necesario desarrollar un sistema de compensación de errores térmicos de alta precisión y bajo costo que pueda cumplir con los requisitos de producción reales de la fábrica para corregir los errores térmicos entre el husillo (o la pieza de trabajo) y la herramienta de corte. Para mejorar la precisión de las máquinas herramienta, reduzca los desechos, aumente la eficiencia de la producción y los beneficios económicos.
Definición básica
La definición básica de compensación de error es crear artificialmente un nuevo error para cancelar o reducir en gran medida el error original que es actualmente un problema. A través del análisis, estadísticas, inducción y dominio de las características y leyes del error original, se estableció el modelo matemático de error para tratar de hacer que el error creado artificialmente sea igual al error original y en la dirección opuesta, reduciendo así el error de mecanizado y mejorando la precisión dimensional de la parte.
La compensación de errores más temprana se logró mediante hardware. La compensación de hardware es una compensación fija mecánica. Para cambiar la cantidad de compensación cuando el error de la herramienta de la máquina cambia, debe volver a crear las piezas, las reglas de calibración o reajustar el mecanismo de compensación. La compensación de hardware también tiene la desventaja de no ser capaz de resolver errores aleatorios y falta de flexibilidad.
[1] El desarrollo de la compensación de software se caracteriza por el uso integral de la tecnología avanzada y la tecnología de control computarizado de diversas disciplinas para mejorar la precisión de las máquinas herramienta sin ningún cambio en la máquina herramienta. La compensación de software supera muchas de las dificultades y desventajas de la compensación de hardware y coloca la tecnología de compensación en una nueva etapa.
Característica
La compensación de errores (tecnología) tiene dos características principales: científico e ingeniería.
El rápido desarrollo de la tecnología científica de compensación de errores ha enriquecido enormemente la teoría del diseño mecánico de precisión, la medición de precisión y toda la ingeniería de precisión, y se ha convertido en una rama importante de esta disciplina. Las técnicas relacionadas con la compensación de errores incluyen tecnología de detección, tecnología de detección, tecnología de procesamiento de señal, tecnología fotoeléctrica, tecnología de materiales, tecnología informática y tecnología de control. Como una nueva rama tecnológica, la tecnología de compensación de errores tiene su propio contenido y características independientes. La investigación adicional sobre técnicas de compensación de errores para que sean teóricas y sistemáticas tendrá una importancia científica muy importante.
La importancia de ingeniería de la tecnología de compensación de error de ingeniería es muy significativa, contiene tres capas de significado:
En primer lugar, el uso de la tecnología de compensación de errores puede alcanzar fácilmente el nivel de precisión que puede costar alcanzar la "tecnología dura";
El segundo es el uso de técnicas de compensación de errores que pueden resolver el nivel de precisión que la "tecnología dura" normalmente no puede lograr;
En tercer lugar, si la tecnología de compensación de errores se adopta bajo ciertos requisitos de precisión, el costo de la fabricación de instrumentos y equipos puede reducirse considerablemente, lo que tiene beneficios económicos muy significativos.
Torneado de generación y clasificación de errores térmicos
Con la mejora adicional de los requisitos de precisión de la máquina herramienta, la proporción de errores térmicos en el error total continuará aumentando. La deformación térmica de la máquina herramienta se ha convertido en un obstáculo importante para mejorar la precisión del mecanizado. El error térmico de la máquina herramienta se debe principalmente a la deformación térmica de los componentes de la máquina causada por fuentes de calor dentro y fuera de la máquina, como motores, cojinetes, piezas de transmisión, sistemas hidráulicos, temperatura ambiente y refrigerante. El error de geometría de la máquina herramienta proviene de los defectos de fabricación de la máquina herramienta, el error de coincidencia entre los componentes de la máquina herramienta, el desplazamiento dinámico y estático de los componentes de la máquina herramienta, y así sucesivamente.
Método básico de compensación de error
En resumen y referencias relacionadas, se puede ver que el error de giro generalmente es causado por los siguientes factores:
Error de deformación térmica de la máquina herramienta;
Errores geométricos en partes y estructuras de la máquina herramienta;
Error inducido por la fuerza de corte;
Error de desgaste de la herramienta;
Otras fuentes de error, como errores de servo en los ejes de la máquina herramienta, errores del algoritmo de interpolación del CNC, etc.
Hay dos métodos básicos para mejorar la precisión de la máquina herramienta: método de prevención de errores y método de compensación de errores.
El método de prevención de errores intenta eliminar o reducir posibles fuentes de error a través de los enfoques de diseño y fabricación. El método de prevención de errores es eficaz para reducir el aumento de temperatura de la fuente de calor, ecualizar el campo de temperatura y reducir la deformación térmica de la máquina herramienta hasta cierto punto. Sin embargo, es imposible eliminar completamente la deformación térmica, y el costo es muy caro; La aplicación de la ley de compensación de error térmico abre una forma efectiva y económica de mejorar la precisión de las máquinas herramienta.
Conclusiones relacionadas
La investigación de errores de torneado de mecanizado es el componente y la dirección más importantes del desarrollo en la fabricación de maquinaria moderna, y se ha convertido en una tecnología clave para mejorar la competitividad internacional. El error se produce de muchas maneras. El análisis y la investigación sobre error térmico es útil para mejorar la precisión de giro y los requisitos técnicos.
La tecnología de compensación de errores puede cumplir con la alta precisión y bajo costo de los requisitos de producción reales de la fábrica. La tecnología de compensación térmica de errores puede corregir el error de deriva térmica entre el husillo (o la pieza de trabajo) y la herramienta de corte, mejorar la precisión de mecanizado de la máquina herramienta, reducir los productos de desecho, aumentar la eficiencia de producción y los beneficios económicos.
problema comun
Cuando el torno ordinario gira un hilo de paso grande, a veces se produce vibración en el asiento, y la superficie de mecanizado está corrugada, y la pesada está fracturando los cuchillos.
Y cuando se cortan, los trabajadores a menudo tienen un cuchillo de corbata o un cuchillo de corte.
Hay muchos motivos para los problemas anteriores. Ahora discutimos principalmente el fenómeno y las soluciones analizando las condiciones de fuerza de las herramientas.
1. La causa del problema y sus causas
sabemos:
Al girar un hilo con un paso pequeño, generalmente se adopta un método de corte recto del cuchillo (un avance recto en la dirección perpendicular al eje de la pieza de trabajo);
Al girar un hilo con un paso grande, a menudo se usan métodos de corte de cuchilla izquierdo y derecho para reducir la fuerza de corte. (Al mover la patineta pequeña para hacer que la herramienta de tornear hilo corte con los bordes de corte izquierdo y derecho, respectivamente).
Al girar el hilo, el movimiento del sillín se logra mediante la rotación del tornillo largo para impulsar el movimiento de la tuerca de apertura y cierre. Hay una holgura axial en el cojinete del tornillo largo, y también hay un juego axial entre el tornillo largo y la tuerca de apertura. Cuando el filo principal derecho del tornillo diestro derecho se mecaniza con fuerza mediante el método de corte de préstamo izquierda-derecha, la herramienta se somete a la fuerza P que le da la pieza de trabajo (ignorando la fricción entre el chip y la cara del rastrillo) , y la fuerza P se descompone en un componente axial Px y un componente radial, donde el componente axial Px y la alimentación de la herramienta En la misma dirección, la herramienta pasa este componente axial Px al sillín. Por lo tanto, la silla de cama se empuja hacia el lado del espacio para hacer movimientos rápidos y rápidos hacia adelante y hacia atrás. Como resultado, la herramienta se mueve hacia adelante y hacia atrás, y la superficie de mecanizado está corrugada e incluso rota. Sin embargo, al cortar con el borde de corte principal izquierdo, no hay tal fenómeno. Al cortar con el borde de corte principal izquierdo, la fuerza de componente axial Px de la herramienta es opuesta a la dirección de alimentación, y se elimina la dirección de espacio libre. En este momento, el sillín se mueve a una velocidad uniforme. .
Al cortar, el movimiento de la placa deslizante del medio se logra mediante la rotación del tornillo de la platina deslizante del medio que impulsa la tuerca. Hay un juego axial en el cojinete del eje del tornillo y un juego axial entre el eje del tornillo y la tuerca. Al cortar en un torno, la cara de rastrillo de la herramienta (con la esquina frontal) está sujeta a la fuerza P dada por la pieza de trabajo (ignorando la fricción entre el chip y la cara del rastrillo), Descompone la fuerza P en fuerza Pz y fuerza radial El componente radial es igual a la dirección de corte de la herramienta de corte. Señala la pieza de trabajo y empuja la herramienta hacia la pieza de trabajo. Esto hará que la diapositiva central se mueva en la dirección de la holgura, causando la flexión (rotura) de la cuchilla o la pieza de trabajo.
Al cortar, el movimiento de la placa deslizante del medio se logra mediante la rotación del tornillo de la platina deslizante del medio que impulsa la tuerca. Hay un juego axial en el cojinete del eje del tornillo y un juego axial entre el eje del tornillo y la tuerca. Al cortar en un torno, la cara de rastrillo de la herramienta (con la esquina frontal) está sujeta a la fuerza P dada por la pieza de trabajo (ignorando la fricción entre el chip y la cara del rastrillo), Descompone la fuerza P en fuerza Pz y fuerza radial El componente radial es igual a la dirección de corte de la herramienta de corte. Señala la pieza de trabajo y empuja la herramienta hacia la pieza de trabajo. Esto hará que la diapositiva central se mueva en la dirección de la holgura, causando la flexión (rotura) de la cuchilla o la pieza de trabajo.
2. Solución
Cuando el tono de giro es más grande y se utiliza el hilo del método de corte de préstamo izquierdo y derecho, además de ajustar los parámetros relevantes del torno, la separación entre el sillín y el riel de la cama debe ajustarse para que quede un poco más apretado. Para aumentar la fricción durante el movimiento, se reduce la posibilidad de turbulencias en el sillín, pero este espacio no se puede ajustar demasiado apretado para que sea apropiado sacudir el sillín constantemente.
Ajuste la separación de la patineta media para minimizar la brecha; Ajuste la rigidez de la patineta pequeña para que quede un poco más ajustada para evitar el giro de la herramienta de giro al girar. La longitud de la pieza de trabajo y la barra de herramientas debe acortarse tanto como sea posible, y la hoja principal izquierda debe usarse lo más posible; Al cortar con la cuchilla principal derecha, es necesario reducir la cantidad de cuchilla trasera; Aumente el ángulo de inclinación del borde de corte principal derecho. El borde del filo debe ser recto y afilado para reducir la fuerza de componente axial Px de la herramienta. En teoría, cuanto mayor sea el ángulo de inclinación de la hoja principal derecha, mejor.
Es en el torno que la forma y el tamaño del espacio en blanco cambian por el movimiento de rotación de la pieza de trabajo y el movimiento lineal o curvo de la herramienta, y se procesa para cumplir los requisitos de los dibujos.
El torneado es un método para cortar una pieza de trabajo girando una pieza de trabajo en relación con una herramienta en un torno. La energía de corte del torneado la proporciona principalmente la pieza de trabajo en lugar de la herramienta. El torneado es el método de corte más básico y común y ocupa una posición muy importante en la producción. El torneado es adecuado para mecanizar superficies rotatorias. La mayoría de las piezas de trabajo con superficie giratoria se pueden mecanizar girando. Como las superficies cilíndricas internas y externas, las superficies cónicas internas y externas, las superficies de los extremos, las ranuras, los hilos y las superficies rotatorias de formación, las herramientas utilizadas son principalmente herramientas de torneado. Los tornos son la categoría más utilizada en todo tipo de máquinas herramienta para cortar metales, y representan aproximadamente el 50% del número total de máquinas herramienta. El torno se puede utilizar para hacer girar una pieza de trabajo con una herramienta de torneado, pero también puede usar taladros, escariadores, roscas y herramientas de moleteado para taladrar, escariar, roscar y moletear. De acuerdo con las diferentes características del proceso, el diseño y las características estructurales, los tornos se pueden dividir en tornos horizontales, tornos de tipo piso, tornos verticales, tornos de torreta y tornos de duplicación, la mayoría de los cuales son tornos horizontales.
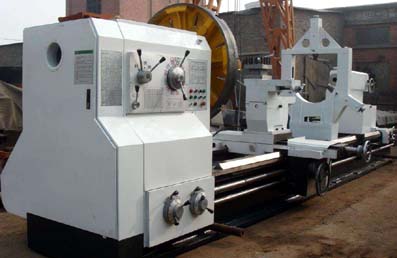
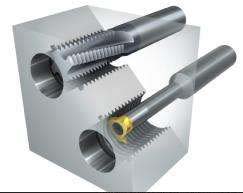
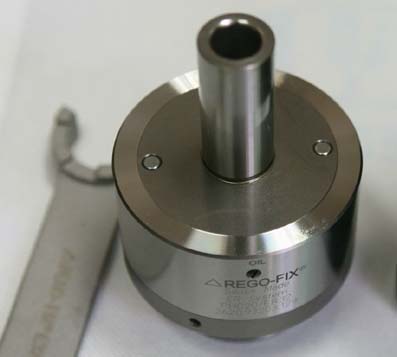
Problema técnico
El mecanizado de torneado es el tipo más utilizado en la industria de fabricación de maquinaria. La cantidad de tornos es grande, la cantidad de personas es grande y el rango de procesamiento es amplio. Hay muchas herramientas y accesorios utilizados, por lo tanto, la seguridad y los problemas técnicos de torneado son especialmente importantes. Las tareas clave son las siguientes:
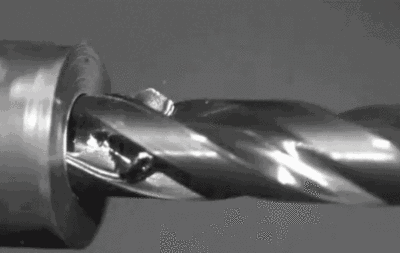
1, daños por viruta y medidas de protección.
Las piezas de acero mecanizadas en el torno son más flexibles, y la viruta producida durante el torneado es de plástico rizado y tiene bordes afilados. En el corte a alta velocidad de piezas de acero, se forman puntos rojos y largos, que son extremadamente fáciles de doler y con frecuencia se enrollan alrededor de las piezas de trabajo, herramientas de torneado y portaherramientas. Por lo tanto, el gancho debe limpiarse o quitarse de manera oportuna en el trabajo. Si es necesario, se debe detener y borrar. Sin embargo, no debe ser eliminado o roto a mano. Con el fin de evitar el daño por viruta, a menudo se adoptan la rotura de virutas, el control del flujo de virutas y diversos deflectores de protección. La medida de ruptura de viruta es rectificar rompevirutas o pasos en la herramienta de torneado; Utilice un rompevirutas apropiado y sujete mecánicamente la herramienta.
2, montaje de la pieza de trabajo.
En el proceso de torneado, hay muchos accidentes, como daños a la máquina herramienta debido a una instalación incorrecta de la pieza de trabajo, a romper o romper la herramienta y a caerse o salir volando de la pieza de trabajo.
Por lo tanto, para garantizar una producción segura de torneado, se debe prestar especial atención al cargar las piezas de trabajo. Para piezas de diferentes tamaños y formas, se deben usar accesorios adecuados, independientemente de la conexión de mandriles de tres mordazas y cuatro garras o accesorios especiales y husillos. Las piezas de trabajo se deben sujetar y sujetar con abrazaderas, y las piezas de trabajo grandes se pueden sujetar con abrazaderas y manguitos.
Cuando la pieza de trabajo se gira a alta velocidad y se aplica la fuerza de corte, no se desplaza, se cae y no se arroja. Si es necesario, puede ser reforzado por el centro superior y el marco central. Bloqueo, inmediatamente después de quitar la llave.
3, operación segura.
Antes del trabajo, debemos inspeccionar completamente la máquina y confirmar que es para usarla. El montaje de la pieza de trabajo y la herramienta garantiza que la posición sea correcta, firme y confiable. Durante el proceso de mecanizado, la herramienta debe detenerse al cambiar la herramienta, al cargar y descargar la pieza de trabajo y al medir la pieza de trabajo. La pieza de trabajo no debe tocarse a mano ni limpiarse con algodón al girar. Para seleccionar correctamente la velocidad de corte, la velocidad de alimentación y la profundidad de tensión, no se permite el mecanizado con sobrecarga. No se deben colocar piezas de trabajo, abrazaderas de trabajo y otros residuos en el soporte de la herramienta y la superficie de la cama. Cuando use un rallador, mueva la herramienta de giro a una posición segura con la mano derecha en la parte delantera y la mano izquierda en la parte posterior para evitar que las mangas se involucren. La máquina herramienta debe tener a alguien responsable del uso y mantenimiento, y otro personal no debe usarla.
Precauciones
El proceso de mecanizado con torno CNC es similar al de los tornos ordinarios. Sin embargo, debido a que el torno CNC se instala una vez y todas las operaciones de torneado se completan automáticamente, se deben tener en cuenta los siguientes aspectos.
1. Elección razonable de la cantidad de corte:
Para el corte de metales de alta eficiencia, los materiales a mecanizar, las herramientas de corte y las condiciones de corte son tres factores principales. Estos determinan el tiempo de procesamiento, la vida útil de la herramienta y la calidad del procesamiento. El método de procesamiento económico y efectivo debe ser una elección razonable de las condiciones de corte. Los tres elementos de las condiciones de corte: velocidad de corte, velocidad de avance y profundidad de corte causan daño a la herramienta directamente. Con el aumento de la velocidad de corte, la temperatura de la punta de la herramienta aumentará y producirá desgaste mecánico, químico y térmico. La velocidad de corte aumentó en un 20%, la vida de la herramienta se reducirá en 1/2. La condición de alimentación y el desgaste detrás de la herramienta se producen dentro de un rango muy pequeño. Sin embargo, la velocidad de alimentación es grande, la temperatura de corte aumenta y el desgaste posterior es grande. Tiene menos influencia en la herramienta que la velocidad de corte. El efecto del corte profundo en la herramienta de corte Aunque no hay velocidad de corte y cantidad de alimentación, cuando la profundidad de corte es pequeña, el material a cortar tiene una capa endurecida, lo que también afecta la vida útil de la herramienta de corte. El usuario selecciona la velocidad de corte que se utilizará en función del material que se va a procesar, la dureza, las condiciones de corte, el tipo de material, la cantidad de alimentación, la profundidad de corte y similares. La selección de las condiciones de procesamiento más adecuadas se selecciona sobre la base de estos factores. El desgaste regular y estable es la condición ideal para alcanzar la esperanza de vida. Sin embargo, en la operación real, la elección de la vida útil de la herramienta está relacionada con el desgaste de la herramienta, el tamaño de la máquina que se procesa, la calidad de la superficie, el ruido de corte y el calor de procesamiento. Al determinar las condiciones de procesamiento, es necesario realizar una investigación de acuerdo con las condiciones reales. Para materiales difíciles de mecanizar como acero inoxidable y aleaciones resistentes al calor, se pueden usar refrigerantes o cuchillas rígidas.
2. Elección razonable de herramientas:
(1) Al desbastar, seleccione una herramienta con alta resistencia y buena durabilidad para cumplir con los requisitos de una gran profundidad de corte y una gran cantidad de avance durante el desbaste.
(2) Cuando termine de girar, es necesario seleccionar herramientas con alta precisión y buena durabilidad para garantizar la precisión del procesamiento.
(3) Para reducir el tiempo de cambio de la herramienta y facilitar el ajuste de la herramienta, la abrazadera y la cuchilla deben usarse lo más lejos posible.
3. Razonablemente seleccione el accesorio:
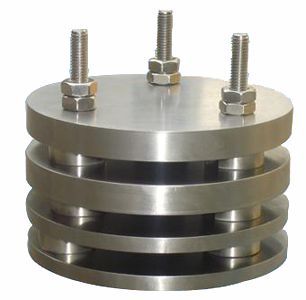
(1) Intente usar un accesorio universal para sujetar la pieza de trabajo para evitar el uso de accesorios especiales;
(2) La referencia de posicionamiento de la pieza coincide para reducir el error de posicionamiento.
4. Determine la ruta de procesamiento:
La ruta de procesamiento es la trayectoria y la dirección de la herramienta con respecto a la pieza en el proceso de mecanizado de herramienta de máquina controlada por índice.
(1) Debe ser capaz de garantizar la precisión del procesamiento y los requisitos de rugosidad de la superficie;
(2) La ruta de procesamiento debe acortarse tanto como sea posible para reducir el tiempo de viaje inactivo de la herramienta.
5. Ruta de procesamiento y asignación de mecanizado:
Bajo la condición de que los tornos CNC no hayan alcanzado un uso universal, generalmente, la tolerancia excesiva para los espacios en blanco, especialmente la tolerancia para forjar y fundir la cubierta dura, debe mecanizarse en tornos comunes. Si debe utilizar el procesamiento del torno CNC, debe prestar atención a la disposición flexible del programa.
6. Puntos de instalación del artefacto:
La conexión entre el plato hidráulico y el cilindro de sujeción hidráulico se logra mediante la barra de tracción. Los puntos clave de la sujeción del mandril hidráulico son los siguientes:
Primero quite la tuerca del cilindro hidráulico con una mano, retire el tubo de extracción y retire el portabrocas del extremo trasero del eje. Luego quite el tornillo de fijación del portabrocas para quitar el portabrocas.
Reglas generales
Procedimientos generales de procesamiento de torneado (JB / T9168.2-1998)
Configuración de herramientas
1) El mango de la herramienta se extiende fuera del portaherramientas y no debe ser demasiado largo. La longitud general no debe exceder 1,5 veces la altura de la barra de herramientas (a excepción del orificio, ranura, etc.)
2) La línea central del portaherramientas del torno debe ser perpendicular o paralela a la dirección de corte.
3) Ajuste de la altura de la punta del cuchillo:
(1) Al girar una cara, girar una superficie cónica, girar roscas, girar una superficie de formación y cortar una pieza de trabajo sólida, el borde de corte debería estar a la misma altura que el eje de la pieza de trabajo.
(2) La rueda de desbaste, el orificio de acabado y la punta de la herramienta generalmente deben ser un poco más altos que el eje de la pieza de trabajo.
(3) Cuando se cortan el eje delgado, el agujero áspero y la pieza de trabajo hueca, la punta de la herramienta generalmente debe ser un poco más baja que el eje de la pieza de trabajo.
4) La bisectriz del ángulo de rosca de la herramienta de torneado de roscas debe ser perpendicular al eje de la pieza de trabajo.
5) Al insertar la herramienta de torneado, la arandela debajo de la barra de herramientas debe ser pequeña y plana, y el tornillo que presiona la herramienta de torneado debe apretarse.
Montaje de la pieza de trabajo
1) Cuando se utiliza un mandril autocentrante de tres mordazas para sujetar piezas de trabajo para desbaste o acabado, si el diámetro de la pieza de trabajo es inferior a 30 mm, la longitud del voladizo no debe ser mayor de 5 veces el diámetro. Si el diámetro de la pieza de trabajo es mayor a 30 mm, su longitud de saliente no debe ser más de 3 veces el diámetro.
2) Cuando se utiliza un portabrocas de una sola acción, placa frontal, ángulo de hierro (placa de doblez), etc. de cuatro mordazas para sujetar piezas pesadas de forma irregular, se debe agregar peso.
3) Al mecanizar una pieza de trabajo de eje en la punta del eje, ajuste el eje central del contrapunto para que coincida con el eje del eje del torno antes de girar.
4) Al mecanizar ejes delgados entre los dos centros superiores, se debe usar un portaherramientas o un marco central. En el proceso de procesamiento, se debe prestar atención al ajuste de la rigidez superior. El centro muerto superior y el marco central deben prestar atención a la lubricación.
5) Cuando se usa el contrapunto, la manga debe extenderse lo más corto posible para reducir la vibración.
6) Cuando se sujeta el torno vertical, la superficie de apoyo es pequeña y la altura de la pieza de trabajo es alta, se debe usar la uña elevada y la pieza de trabajo debe presionarse en el lugar apropiado con una barra de tracción o placa de presión.
7) Al girar ruedas y forjados de fundición, la superficie sin terminar debe corregirse para garantizar un espesor de pared uniforme después del procesamiento.
Torneado
1) Al girar el eje del escalón, para garantizar la rigidez durante el torneado, generalmente la parte de mayor diámetro debe girarse primero, y la parte de menor diámetro debe girarse más tarde.
2) cuando el eje tiene ranuras de corte en una pieza de trabajo, a realizar antes del acabado, a fin de evitar la deformación de la pieza de trabajo.
3) Cuando está bien girar un eje roscado,
Después de enhebrar, la parte no roscada se gira con precisión.
4) antes de taladrar, la cara final de la pieza de trabajo debe estar plana. Taladre el orificio central primero si es necesario.
5) Cuando se perforan orificios profundos, el orificio piloto generalmente se perfora primero.
6) Al girar agujeros (Φ10-Φ20) mm, el diámetro del vástago de la herramienta debe ser de 0.6-0.7 veces el diámetro del orificio mecanizado; Cuando el diámetro del orificio es mayor que 20 mm, se debe usar el portacuchillas con cabeza de sujeción.
7) Al girar un tornillo de cabezales múltiples o de cabezales múltiples, después de ajustar los engranajes de cambio, realice un corte de prueba.
8) Cuando utilice el torno automático, ajuste la posición relativa de la herramienta y la pieza de trabajo de acuerdo con la tarjeta de ajuste de la máquina herramienta. Después del ajuste, es necesario llevar a cabo el giro de prueba. Después de calificar la primera pieza, puede procesarse; Durante el proceso de mecanizado, el desgaste de la herramienta, el tamaño de la pieza de trabajo y la rugosidad de la superficie siempre se tienen en cuenta.
9) Al encender un torno vertical, la viga no debe moverse libremente cuando se ajusta el portacuchillas. Al encender el torno vertical, cuando se ajusta el soporte de la herramienta, no se permite mover el travesaño a voluntad.
10) Cuando la superficie relevante de la pieza de trabajo tiene tolerancias posicionales, el giro se realiza en una sola sujeción tanto como sea posible.
11) Al girar un diente de dientes rectos, el orificio y la cara del extremo de referencia se deben mecanizar en una sujeción. Si es necesario, la línea de marcado debe dibujarse cerca del final del círculo de indexación del engranaje.
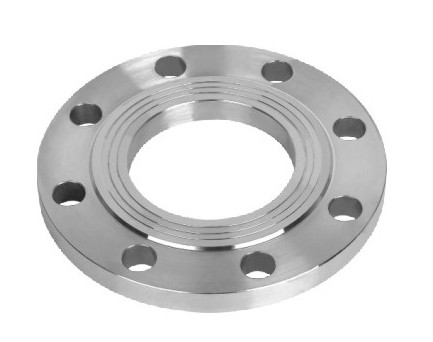
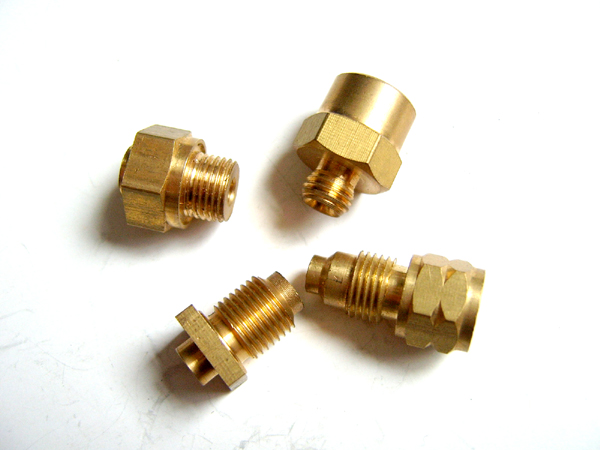
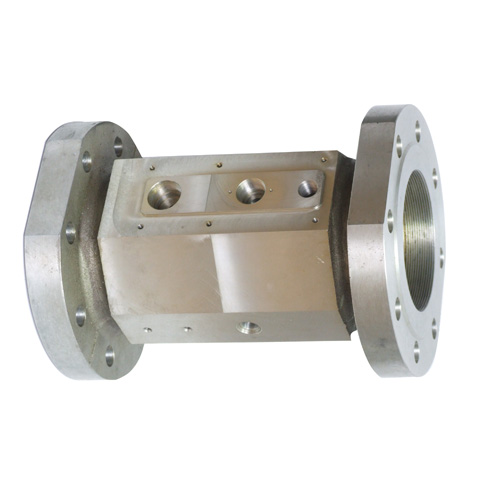
La tecnología moderna de fabricación de maquinaria se está moviendo hacia la alta eficiencia, alta calidad, alta precisión, alta integración y alta inteligencia. La tecnología de mecanizado de precisión y ultraprecisión se ha convertido en el componente y la dirección de desarrollo más importante en la fabricación de maquinaria moderna, y se ha convertido en una tecnología clave para mejorar la competitividad internacional. El error de mecanizado por torneado se ha convertido en un tema candente de investigación con la extensa aplicación del mecanizado de precisión. Dado que los errores térmicos y los errores geométricos representan la mayoría de los diversos errores en la máquina herramienta, la reducción de estos dos errores, en particular los errores térmicos, se ha convertido en el objetivo principal. La Tecnología de Compensación de Errores (ECT) surgió con el desarrollo continuo de la ciencia y la tecnología. Las pérdidas causadas por la deformación térmica de la máquina herramienta son considerables. Por lo tanto, es extremadamente necesario desarrollar un sistema de compensación de errores térmicos de alta precisión y bajo costo que pueda cumplir con los requisitos de producción reales de la fábrica para corregir los errores térmicos entre el husillo (o la pieza de trabajo) y la herramienta de corte. Para mejorar la precisión de las máquinas herramienta, reduzca los desechos, aumente la eficiencia de la producción y los beneficios económicos.
Definición básica
La definición básica de compensación de error es crear artificialmente un nuevo error para cancelar o reducir en gran medida el error original que es actualmente un problema. A través del análisis, estadísticas, inducción y dominio de las características y leyes del error original, se estableció el modelo matemático de error para tratar de hacer que el error creado artificialmente sea igual al error original y en la dirección opuesta, reduciendo así el error de mecanizado y mejorando la precisión dimensional de la parte.
La compensación de errores más temprana se logró mediante hardware. La compensación de hardware es una compensación fija mecánica. Para cambiar la cantidad de compensación cuando el error de la herramienta de la máquina cambia, debe volver a crear las piezas, las reglas de calibración o reajustar el mecanismo de compensación. La compensación de hardware también tiene la desventaja de no ser capaz de resolver errores aleatorios y falta de flexibilidad.
[1] El desarrollo de la compensación de software se caracteriza por el uso integral de la tecnología avanzada y la tecnología de control computarizado de diversas disciplinas para mejorar la precisión de las máquinas herramienta sin ningún cambio en la máquina herramienta. La compensación de software supera muchas de las dificultades y desventajas de la compensación de hardware y coloca la tecnología de compensación en una nueva etapa.
Característica
La compensación de errores (tecnología) tiene dos características principales: científico e ingeniería.
El rápido desarrollo de la tecnología científica de compensación de errores ha enriquecido enormemente la teoría del diseño mecánico de precisión, la medición de precisión y toda la ingeniería de precisión, y se ha convertido en una rama importante de esta disciplina. Las técnicas relacionadas con la compensación de errores incluyen tecnología de detección, tecnología de detección, tecnología de procesamiento de señal, tecnología fotoeléctrica, tecnología de materiales, tecnología informática y tecnología de control. Como una nueva rama tecnológica, la tecnología de compensación de errores tiene su propio contenido y características independientes. La investigación adicional sobre técnicas de compensación de errores para que sean teóricas y sistemáticas tendrá una importancia científica muy importante.
La importancia de ingeniería de la tecnología de compensación de error de ingeniería es muy significativa, contiene tres capas de significado:
En primer lugar, el uso de la tecnología de compensación de errores puede alcanzar fácilmente el nivel de precisión que puede costar alcanzar la "tecnología dura";
El segundo es el uso de técnicas de compensación de errores que pueden resolver el nivel de precisión que la "tecnología dura" normalmente no puede lograr;
En tercer lugar, si la tecnología de compensación de errores se adopta bajo ciertos requisitos de precisión, el costo de la fabricación de instrumentos y equipos puede reducirse considerablemente, lo que tiene beneficios económicos muy significativos.
Torneado de generación y clasificación de errores térmicos
Con la mejora adicional de los requisitos de precisión de la máquina herramienta, la proporción de errores térmicos en el error total continuará aumentando. La deformación térmica de la máquina herramienta se ha convertido en un obstáculo importante para mejorar la precisión del mecanizado. El error térmico de la máquina herramienta se debe principalmente a la deformación térmica de los componentes de la máquina causada por fuentes de calor dentro y fuera de la máquina, como motores, cojinetes, piezas de transmisión, sistemas hidráulicos, temperatura ambiente y refrigerante. El error de geometría de la máquina herramienta proviene de los defectos de fabricación de la máquina herramienta, el error de coincidencia entre los componentes de la máquina herramienta, el desplazamiento dinámico y estático de los componentes de la máquina herramienta, y así sucesivamente.
Método básico de compensación de error
En resumen y referencias relacionadas, se puede ver que el error de giro generalmente es causado por los siguientes factores:
Error de deformación térmica de la máquina herramienta;
Errores geométricos en partes y estructuras de la máquina herramienta;
Error inducido por la fuerza de corte;
Error de desgaste de la herramienta;
Otras fuentes de error, como errores de servo en los ejes de la máquina herramienta, errores del algoritmo de interpolación del CNC, etc.
Hay dos métodos básicos para mejorar la precisión de la máquina herramienta: método de prevención de errores y método de compensación de errores.
El método de prevención de errores intenta eliminar o reducir posibles fuentes de error a través de los enfoques de diseño y fabricación. El método de prevención de errores es eficaz para reducir el aumento de temperatura de la fuente de calor, ecualizar el campo de temperatura y reducir la deformación térmica de la máquina herramienta hasta cierto punto. Sin embargo, es imposible eliminar completamente la deformación térmica, y el costo es muy caro; La aplicación de la ley de compensación de error térmico abre una forma efectiva y económica de mejorar la precisión de las máquinas herramienta.
Conclusiones relacionadas
La investigación de errores de torneado de mecanizado es el componente y la dirección más importantes del desarrollo en la fabricación de maquinaria moderna, y se ha convertido en una tecnología clave para mejorar la competitividad internacional. El error se produce de muchas maneras. El análisis y la investigación sobre error térmico es útil para mejorar la precisión de giro y los requisitos técnicos.
La tecnología de compensación de errores puede cumplir con la alta precisión y bajo costo de los requisitos de producción reales de la fábrica. La tecnología de compensación térmica de errores puede corregir el error de deriva térmica entre el husillo (o la pieza de trabajo) y la herramienta de corte, mejorar la precisión de mecanizado de la máquina herramienta, reducir los productos de desecho, aumentar la eficiencia de producción y los beneficios económicos.
problema comun
Cuando el torno ordinario gira un hilo de paso grande, a veces se produce vibración en el asiento, y la superficie de mecanizado está corrugada, y la pesada está fracturando los cuchillos.
Y cuando se cortan, los trabajadores a menudo tienen un cuchillo de corbata o un cuchillo de corte.
Hay muchos motivos para los problemas anteriores. Ahora discutimos principalmente el fenómeno y las soluciones analizando las condiciones de fuerza de las herramientas.
1. La causa del problema y sus causas
sabemos:
Al girar un hilo con un paso pequeño, generalmente se adopta un método de corte recto del cuchillo (un avance recto en la dirección perpendicular al eje de la pieza de trabajo);
Al girar un hilo con un paso grande, a menudo se usan métodos de corte de cuchilla izquierdo y derecho para reducir la fuerza de corte. (Al mover la patineta pequeña para hacer que la herramienta de tornear hilo corte con los bordes de corte izquierdo y derecho, respectivamente).
Al girar el hilo, el movimiento del sillín se logra mediante la rotación del tornillo largo para impulsar el movimiento de la tuerca de apertura y cierre. Hay una holgura axial en el cojinete del tornillo largo, y también hay un juego axial entre el tornillo largo y la tuerca de apertura. Cuando el filo principal derecho del tornillo diestro derecho se mecaniza con fuerza mediante el método de corte de préstamo izquierda-derecha, la herramienta se somete a la fuerza P que le da la pieza de trabajo (ignorando la fricción entre el chip y la cara del rastrillo) , y la fuerza P se descompone en un componente axial Px y un componente radial, donde el componente axial Px y la alimentación de la herramienta En la misma dirección, la herramienta pasa este componente axial Px al sillín. Por lo tanto, la silla de cama se empuja hacia el lado del espacio para hacer movimientos rápidos y rápidos hacia adelante y hacia atrás. Como resultado, la herramienta se mueve hacia adelante y hacia atrás, y la superficie de mecanizado está corrugada e incluso rota. Sin embargo, al cortar con el borde de corte principal izquierdo, no hay tal fenómeno. Al cortar con el borde de corte principal izquierdo, la fuerza de componente axial Px de la herramienta es opuesta a la dirección de alimentación, y se elimina la dirección de espacio libre. En este momento, el sillín se mueve a una velocidad uniforme. .
Al cortar, el movimiento de la placa deslizante del medio se logra mediante la rotación del tornillo de la platina deslizante del medio que impulsa la tuerca. Hay un juego axial en el cojinete del eje del tornillo y un juego axial entre el eje del tornillo y la tuerca. Al cortar en un torno, la cara de rastrillo de la herramienta (con la esquina frontal) está sujeta a la fuerza P dada por la pieza de trabajo (ignorando la fricción entre el chip y la cara del rastrillo), Descompone la fuerza P en fuerza Pz y fuerza radial El componente radial es igual a la dirección de corte de la herramienta de corte. Señala la pieza de trabajo y empuja la herramienta hacia la pieza de trabajo. Esto hará que la diapositiva central se mueva en la dirección de la holgura, causando la flexión (rotura) de la cuchilla o la pieza de trabajo.
Al cortar, el movimiento de la placa deslizante del medio se logra mediante la rotación del tornillo de la platina deslizante del medio que impulsa la tuerca. Hay un juego axial en el cojinete del eje del tornillo y un juego axial entre el eje del tornillo y la tuerca. Al cortar en un torno, la cara de rastrillo de la herramienta (con la esquina frontal) está sujeta a la fuerza P dada por la pieza de trabajo (ignorando la fricción entre el chip y la cara del rastrillo), Descompone la fuerza P en fuerza Pz y fuerza radial El componente radial es igual a la dirección de corte de la herramienta de corte. Señala la pieza de trabajo y empuja la herramienta hacia la pieza de trabajo. Esto hará que la diapositiva central se mueva en la dirección de la holgura, causando la flexión (rotura) de la cuchilla o la pieza de trabajo.
2. Solución
Cuando el tono de giro es más grande y se utiliza el hilo del método de corte de préstamo izquierdo y derecho, además de ajustar los parámetros relevantes del torno, la separación entre el sillín y el riel de la cama debe ajustarse para que quede un poco más apretado. Para aumentar la fricción durante el movimiento, se reduce la posibilidad de turbulencias en el sillín, pero este espacio no se puede ajustar demasiado apretado para que sea apropiado sacudir el sillín constantemente.
Ajuste la separación de la patineta media para minimizar la brecha; Ajuste la rigidez de la patineta pequeña para que quede un poco más ajustada para evitar el giro de la herramienta de giro al girar. La longitud de la pieza de trabajo y la barra de herramientas debe acortarse tanto como sea posible, y la hoja principal izquierda debe usarse lo más posible; Al cortar con la cuchilla principal derecha, es necesario reducir la cantidad de cuchilla trasera; Aumente el ángulo de inclinación del borde de corte principal derecho. El borde del filo debe ser recto y afilado para reducir la fuerza de componente axial Px de la herramienta. En teoría, cuanto mayor sea el ángulo de inclinación de la hoja principal derecha, mejor.