Proceso de mecanizado CNC
Principios de procesamiento
(1) el procesamiento del procedimiento de trabajo anterior no puede afectar el posicionamiento y sujeción del siguiente procedimiento de trabajo.
(2) Primero dentro y fuera, Es decir, la cavidad interna (orificio interno) se procesa primero, y luego se procesa la forma externa.
⑶ Los procesos que se procesan con la misma herramienta o la misma herramienta se llevan a cabo preferiblemente de forma continua para reducir los errores causados por la reubicación o el cambio de herramienta.
(4) En la misma instalación, el proceso que tiene poco efecto sobre la rigidez de la pieza de trabajo debe realizarse primero.
Ruta de procesamiento
La ruta de procesamiento de alimentación del torno CNC significa que la herramienta de torneado comienza su movimiento desde el punto de ajuste de la herramienta (o el origen fijo de la máquina herramienta) hasta que vuelve a ese punto y finaliza el programa de mecanizado. Camino de acceso, incluidos cuchillos Cortar, cortar y una ruta de recorrido libre de corte.
La ruta de alimentación para el acabado se lleva a cabo básicamente a lo largo del contorno de sus partes. Por lo tanto, el enfoque principal para determinar la ruta de alimentación es determinar la ruta de alimentación para el desbaste y el recorrido vacío.
En el procesamiento de torno CNC, la determinación de las rutas de procesamiento generalmente sigue los siguientes principios:
1. Se debe garantizar la precisión y la rugosidad de la superficie de la pieza de trabajo a mecanizar.
2. Minimice la ruta de procesamiento, reduzca el tiempo de viaje inactivo y mejore la eficiencia del procesamiento.
3. Simplifique la carga de trabajo del cálculo numérico tanto como sea posible y simplifique el procedimiento de procesamiento.
4. Para algunos programas reutilizables, use subrutinas.
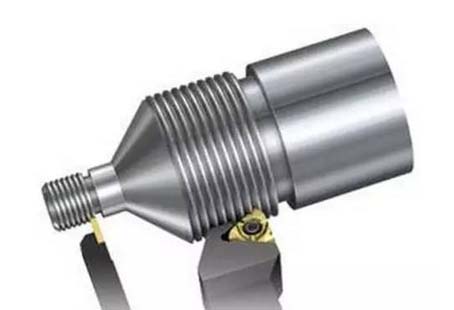
Hacer que el programa de procesamiento tenga la ruta de alimentación más corta no solo ahorra el tiempo de ejecución de todo el proceso de mecanizado, sino que también reduce el consumo innecesario de herramientas y el desgaste de las piezas deslizantes del mecanismo de alimentación de la máquina. El tipo de ruta más corta y su implementación son las siguientes:
(1) La ruta de alimentación de corte más corta. El camino de alimentación de corte más corto puede aumentar efectivamente la eficiencia de producción y reducir el desgaste de la herramienta. Al organizar la ruta de alimentación de corte más corta, también es necesario garantizar la rigidez y la trabajabilidad de la pieza de trabajo.
(2) La ruta de recorrido de corte no corta.
Usando puntos de cuchillo. En general, bucle rectangular, ejemplo de desbaste. El punto A de la herramienta se establece teniendo en cuenta la necesidad de un cambio de herramienta conveniente durante el proceso de acabado, y por lo tanto se establece en una posición alejada del blanco. Al mismo tiempo, el punto de inicio coincide con el punto de la herramienta.
Configure un punto de cambio de herramienta hábilmente. Para considerar la conveniencia y seguridad del cambio de herramienta, a veces el punto de cambio de herramienta también se establece a una distancia de la pieza en blanco.
En la ubicación, entonces, cuando se cambia la segunda cuchilla, el curso de la carrera no cortante durante el acabado debe ser más larga; Si el punto de cambio de herramienta de la segunda cuchilla también se establece en la posición del punto medio, la distancia de recorrido no cortada se puede acortar.
Arregla razonablemente la ruta de "retorno cero". Al compilar manualmente programas complejos de mecanizado de contorno, el proceso de cálculo se simplifica para una fácil verificación. El programador a veces establece el punto final de la herramienta después de procesar cada herramienta. Al ejecutar una instrucción de operación "volver a cero", todas vuelven a la posición del punto de corte de la herramienta y luego se ejecuta el programa subsiguiente. Esto aumentará la distancia de la ruta de alimentación y reducirá la eficiencia de producción. Por lo tanto, la distancia entre el punto final de la cuchilla anterior y el punto inicial de la cuchilla siguiente debe ser lo más corta posible cuando la ruta de "retorno cero" esté razonablemente dispuesta. O cero para cumplir con los requisitos más cortos de la ruta de alimentación. Además, cuando se elige regresar a la instrucción de punto de corte de herramienta, la instrucción bidireccional simultánea de "retorno a cero" del eje xy del eje z se utiliza en la medida de lo posible sin interferencia, y el "retorno" "a cero" la ruta de esta función es la más corta.
(3) Línea de alimentación de corte en escalera grande de margen grande. Se enumeran las rutas de alimentación de corte de dos tipos de espacios en blanco de gran tamaño. Es la línea de corte por pasos incorrecta, cortando en el orden de 1 cuchara 5, la cantidad restante de cada corte es igual, es la ruta de alimentación de corte por pasos correcta. Debido al mismo compromiso de la parte posterior del filo.
(4) Ruta de alimentación de corte continuo para el acabado del contorno de parte. El acabado de los contornos de las partes se puede organizar con una o varias operaciones de acabado de cuchillas. Su perfil terminado debe mecanizarse continuamente desde la última cuchilla. En este momento, la posición de la herramienta se debe seleccionar correctamente. Trate de no arreglar el corte y corte o cambiar herramientas y pausas en contornos continuos. Para evitar cambios repentinos en la fuerza de corte y destruir el equilibrio de los sistemas de proceso. Esto ocasiona arañazos, cambios bruscos de forma o estancamiento de las piezas en el contorno de la pieza.
(5) Rutas de alimentación especiales. En torneado CNC, en circunstancias normales. La alimentación longitudinal de la herramienta se alimenta a lo largo de la dirección negativa de las coordenadas. Sin embargo, a veces no es razonable organizar una ruta de alimentación en su dirección negativa habitual. Incluso puede dañar la pieza de trabajo.
Ventajas y desventajas
El mecanizado CNC tiene las siguientes ventajas:
1. La cantidad de vestidos es muy reducida, y las partes con formas complejas no requieren vestidos complicados. Si desea cambiar la forma y el tamaño de las piezas, solo necesita modificar el programa de procesamiento de piezas, que es adecuado para el desarrollo y modificación de nuevos productos.
2. La calidad de procesamiento es estable, la precisión del procesamiento es alta y la precisión de repetición es alta, y puede cumplir los requisitos de procesamiento de la aeronave.
3. La alta eficiencia de producción en el caso de la producción de lotes múltiples y pequeños puede reducir el tiempo de preparación de la producción, el ajuste de la máquina herramienta y la inspección del proceso, y reduce el tiempo de corte debido al uso de la cantidad de corte óptima.
4. Las superficies complejas mecanizables que son difíciles de procesar con métodos convencionales se pueden mecanizar e incluso se pueden mecanizar piezas que no se pueden observar.n La desventaja del mecanizado CNC es que el equipo de la máquina herramienta es costoso y requiere que el personal de mantenimiento tenga un alto nivel.
Selección de herramientas
1, elija el principio de herramienta CNC
La vida útil de la herramienta está estrechamente relacionada con la cantidad de corte. Al establecer la cantidad de corte, se debe seleccionar primero una vida útil razonable de la herramienta y se debe determinar una vida útil razonable de acuerdo con el objetivo de optimización. Generalmente se divide en la vida útil de la herramienta de mayor productividad y la vida útil de la herramienta de menor costo. El primero se determina en función del objetivo con la menor cantidad de tiempo de trabajo por unidad y el último se determina en función del objetivo con el menor costo de proceso.
La vida útil de la herramienta depende de la complejidad de la herramienta, la fabricación y el costo de afilado.
La vida útil de la herramienta compleja y de alta precisión se debe seleccionar para que sea más alta que la herramienta de un solo filo. Para la máquina herramienta con herramientas indexables, debido al corto tiempo de cambio de la herramienta, para poder aprovechar al máximo su rendimiento de corte y mejorar la eficiencia de producción, la vida útil de la herramienta puede seleccionarse para ser menor, por lo general demorar entre 15 y 30 minutos.
Para herramientas de cuchilla múltiple, máquina herramienta y mecanizado automático que son más complejas para cargar herramientas, cambiar herramientas y ajustar herramientas. La vida útil de la herramienta debe seleccionarse más alto y, en particular, debe garantizarse la fiabilidad de la herramienta.
Cuando la productividad de un determinado proceso en un taller limita la productividad de todo el taller, la vida útil de la herramienta del proceso se selecciona para que sea más baja. Cuando el gasto de la planta completa compartida por un cierto tiempo de unidad de la unidad de proceso es relativamente grande, la vida útil de la herramienta también debe seleccionarse más baja.
En el caso del acabado a gran escala, para garantizar que se realice al menos una pasada para evitar el cambio a mitad de la herramienta durante el corte, la vida útil de la herramienta debe determinarse de acuerdo con la precisión de la pieza y la rugosidad de la superficie.
Comparado con el método de procesamiento de máquina-herramienta común, el procesamiento de control numérico presenta mayores requisitos en la herramienta, no solo necesita una buena y alta precisión, sino que también requiere un tamaño estable, alta durabilidad. La desconexión y el rendimiento de la fila también requieren una fácil instalación y ajuste para cumplir con los requisitos de alta eficiencia de máquinas herramienta CNC. Las herramientas seleccionadas para máquinas herramienta CNC se utilizan a menudo para materiales de herramientas de corte de alta velocidad (como acero de alta velocidad, carburo de grano ultrafino) y utilizan insertos indexables.
2, elija la herramienta para torneado CNC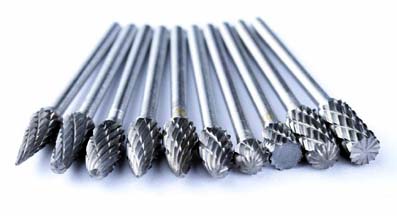
Herramienta de torneado de torno CNC de uso general puntos generales: herramienta de torno que forma, herramienta de giro afilado, herramienta de torneado de arco y cinco tipos.
Las herramientas de torneado de moldeo también se denominan herramientas de torneado modelo. La forma del contorno de las piezas de mecanizado está completamente determinada por la forma y el tamaño del borde de giro de la herramienta de torneado. En torneado CNC, las herramientas de torneado comunes incluyen cortadores de arco de pequeño radio, cortadores de ranura no rectangulares y cortadores de hilo. En CNC Mecanizado, la herramienta de moldeo debe usarse lo menos posible.
La herramienta de giro afilado es una herramienta de torneado caracterizada por un filo recto. La punta de una herramienta de torneado de este tipo consiste en bordes cortantes principales y auxiliares rectos. La herramienta de torneado interna y externa 900, las herramientas de torneado, ranurado (corte) de la cara izquierda y derecha del extremo derecho y una variedad de punta pequeña biselada y las herramientas de orificio cilíndrico. El método de selección de los parámetros geométricos (principalmente ángulos geométricos) del torneado agudo la herramienta es básicamente la misma que la del giro ordinario.
Sin embargo, se deben tener en cuenta las características del mecanizado CNC (como las rutas de procesamiento, la interferencia de procesamiento, etc.) y se debe tener en cuenta la resistencia de la punta de la herramienta.
3, seleccione la herramienta para fresado CNC
En el mecanizado de control numérico, los contornos internos y externos de las partes del plano de fresado y el plano de fresado son comúnmente utilizados molinos de fondo plano. Los datos empíricos de los parámetros relevantes de la herramienta son los siguientes:
Una es que el radio del cortador RD debe ser más pequeño que el radio mínimo de curvatura Rmin de la superficie del contorno interno de la pieza, generalmente tomando RD = (0.8-0.9) Rmin.
El segundo es la altura de procesamiento de la parte H <(1 / 4-1 / 6) RD para asegurar que la cuchilla tenga suficiente rigidez.
En tercer lugar, al fresar la parte inferior de la ranura interna con una fresa de fondo plano, el borde inferior de la ranura debe superponerse mediante dos pasadas, y el radio del borde cortante de la herramienta Re = Rr, es decir, el el diámetro es d = 2Re = 2 (Rr), el radio de la herramienta se toma como Re = 0.95 (Rr) cuando se programa.
Para un procesamiento tridimensional de superficies y perfiles de ángulos variables, se utilizan con frecuencia fresas esféricas, fresas de anillo, fresas de tambor, fresas cónicas y fresas de disco.
(1) el procesamiento del procedimiento de trabajo anterior no puede afectar el posicionamiento y sujeción del siguiente procedimiento de trabajo.
(2) Primero dentro y fuera, Es decir, la cavidad interna (orificio interno) se procesa primero, y luego se procesa la forma externa.
⑶ Los procesos que se procesan con la misma herramienta o la misma herramienta se llevan a cabo preferiblemente de forma continua para reducir los errores causados por la reubicación o el cambio de herramienta.
(4) En la misma instalación, el proceso que tiene poco efecto sobre la rigidez de la pieza de trabajo debe realizarse primero.
Ruta de procesamiento
La ruta de procesamiento de alimentación del torno CNC significa que la herramienta de torneado comienza su movimiento desde el punto de ajuste de la herramienta (o el origen fijo de la máquina herramienta) hasta que vuelve a ese punto y finaliza el programa de mecanizado. Camino de acceso, incluidos cuchillos Cortar, cortar y una ruta de recorrido libre de corte.
La ruta de alimentación para el acabado se lleva a cabo básicamente a lo largo del contorno de sus partes. Por lo tanto, el enfoque principal para determinar la ruta de alimentación es determinar la ruta de alimentación para el desbaste y el recorrido vacío.
En el procesamiento de torno CNC, la determinación de las rutas de procesamiento generalmente sigue los siguientes principios:
1. Se debe garantizar la precisión y la rugosidad de la superficie de la pieza de trabajo a mecanizar.
2. Minimice la ruta de procesamiento, reduzca el tiempo de viaje inactivo y mejore la eficiencia del procesamiento.
3. Simplifique la carga de trabajo del cálculo numérico tanto como sea posible y simplifique el procedimiento de procesamiento.
4. Para algunos programas reutilizables, use subrutinas.
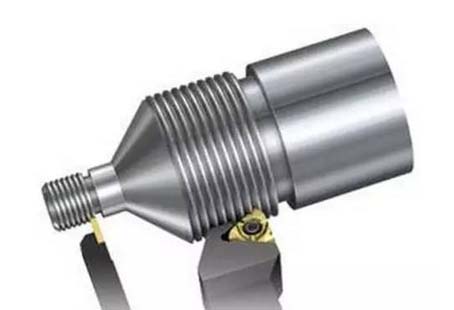
Hacer que el programa de procesamiento tenga la ruta de alimentación más corta no solo ahorra el tiempo de ejecución de todo el proceso de mecanizado, sino que también reduce el consumo innecesario de herramientas y el desgaste de las piezas deslizantes del mecanismo de alimentación de la máquina. El tipo de ruta más corta y su implementación son las siguientes:
(1) La ruta de alimentación de corte más corta. El camino de alimentación de corte más corto puede aumentar efectivamente la eficiencia de producción y reducir el desgaste de la herramienta. Al organizar la ruta de alimentación de corte más corta, también es necesario garantizar la rigidez y la trabajabilidad de la pieza de trabajo.
(2) La ruta de recorrido de corte no corta.
Usando puntos de cuchillo. En general, bucle rectangular, ejemplo de desbaste. El punto A de la herramienta se establece teniendo en cuenta la necesidad de un cambio de herramienta conveniente durante el proceso de acabado, y por lo tanto se establece en una posición alejada del blanco. Al mismo tiempo, el punto de inicio coincide con el punto de la herramienta.
Configure un punto de cambio de herramienta hábilmente. Para considerar la conveniencia y seguridad del cambio de herramienta, a veces el punto de cambio de herramienta también se establece a una distancia de la pieza en blanco.
En la ubicación, entonces, cuando se cambia la segunda cuchilla, el curso de la carrera no cortante durante el acabado debe ser más larga; Si el punto de cambio de herramienta de la segunda cuchilla también se establece en la posición del punto medio, la distancia de recorrido no cortada se puede acortar.
Arregla razonablemente la ruta de "retorno cero". Al compilar manualmente programas complejos de mecanizado de contorno, el proceso de cálculo se simplifica para una fácil verificación. El programador a veces establece el punto final de la herramienta después de procesar cada herramienta. Al ejecutar una instrucción de operación "volver a cero", todas vuelven a la posición del punto de corte de la herramienta y luego se ejecuta el programa subsiguiente. Esto aumentará la distancia de la ruta de alimentación y reducirá la eficiencia de producción. Por lo tanto, la distancia entre el punto final de la cuchilla anterior y el punto inicial de la cuchilla siguiente debe ser lo más corta posible cuando la ruta de "retorno cero" esté razonablemente dispuesta. O cero para cumplir con los requisitos más cortos de la ruta de alimentación. Además, cuando se elige regresar a la instrucción de punto de corte de herramienta, la instrucción bidireccional simultánea de "retorno a cero" del eje xy del eje z se utiliza en la medida de lo posible sin interferencia, y el "retorno" "a cero" la ruta de esta función es la más corta.
(3) Línea de alimentación de corte en escalera grande de margen grande. Se enumeran las rutas de alimentación de corte de dos tipos de espacios en blanco de gran tamaño. Es la línea de corte por pasos incorrecta, cortando en el orden de 1 cuchara 5, la cantidad restante de cada corte es igual, es la ruta de alimentación de corte por pasos correcta. Debido al mismo compromiso de la parte posterior del filo.
(4) Ruta de alimentación de corte continuo para el acabado del contorno de parte. El acabado de los contornos de las partes se puede organizar con una o varias operaciones de acabado de cuchillas. Su perfil terminado debe mecanizarse continuamente desde la última cuchilla. En este momento, la posición de la herramienta se debe seleccionar correctamente. Trate de no arreglar el corte y corte o cambiar herramientas y pausas en contornos continuos. Para evitar cambios repentinos en la fuerza de corte y destruir el equilibrio de los sistemas de proceso. Esto ocasiona arañazos, cambios bruscos de forma o estancamiento de las piezas en el contorno de la pieza.
(5) Rutas de alimentación especiales. En torneado CNC, en circunstancias normales. La alimentación longitudinal de la herramienta se alimenta a lo largo de la dirección negativa de las coordenadas. Sin embargo, a veces no es razonable organizar una ruta de alimentación en su dirección negativa habitual. Incluso puede dañar la pieza de trabajo.
Ventajas y desventajas
El mecanizado CNC tiene las siguientes ventajas:
1. La cantidad de vestidos es muy reducida, y las partes con formas complejas no requieren vestidos complicados. Si desea cambiar la forma y el tamaño de las piezas, solo necesita modificar el programa de procesamiento de piezas, que es adecuado para el desarrollo y modificación de nuevos productos.
2. La calidad de procesamiento es estable, la precisión del procesamiento es alta y la precisión de repetición es alta, y puede cumplir los requisitos de procesamiento de la aeronave.
3. La alta eficiencia de producción en el caso de la producción de lotes múltiples y pequeños puede reducir el tiempo de preparación de la producción, el ajuste de la máquina herramienta y la inspección del proceso, y reduce el tiempo de corte debido al uso de la cantidad de corte óptima.
4. Las superficies complejas mecanizables que son difíciles de procesar con métodos convencionales se pueden mecanizar e incluso se pueden mecanizar piezas que no se pueden observar.n La desventaja del mecanizado CNC es que el equipo de la máquina herramienta es costoso y requiere que el personal de mantenimiento tenga un alto nivel.
Selección de herramientas
1, elija el principio de herramienta CNC
La vida útil de la herramienta está estrechamente relacionada con la cantidad de corte. Al establecer la cantidad de corte, se debe seleccionar primero una vida útil razonable de la herramienta y se debe determinar una vida útil razonable de acuerdo con el objetivo de optimización. Generalmente se divide en la vida útil de la herramienta de mayor productividad y la vida útil de la herramienta de menor costo. El primero se determina en función del objetivo con la menor cantidad de tiempo de trabajo por unidad y el último se determina en función del objetivo con el menor costo de proceso.
La vida útil de la herramienta depende de la complejidad de la herramienta, la fabricación y el costo de afilado.
La vida útil de la herramienta compleja y de alta precisión se debe seleccionar para que sea más alta que la herramienta de un solo filo. Para la máquina herramienta con herramientas indexables, debido al corto tiempo de cambio de la herramienta, para poder aprovechar al máximo su rendimiento de corte y mejorar la eficiencia de producción, la vida útil de la herramienta puede seleccionarse para ser menor, por lo general demorar entre 15 y 30 minutos.
Para herramientas de cuchilla múltiple, máquina herramienta y mecanizado automático que son más complejas para cargar herramientas, cambiar herramientas y ajustar herramientas. La vida útil de la herramienta debe seleccionarse más alto y, en particular, debe garantizarse la fiabilidad de la herramienta.
Cuando la productividad de un determinado proceso en un taller limita la productividad de todo el taller, la vida útil de la herramienta del proceso se selecciona para que sea más baja. Cuando el gasto de la planta completa compartida por un cierto tiempo de unidad de la unidad de proceso es relativamente grande, la vida útil de la herramienta también debe seleccionarse más baja.
En el caso del acabado a gran escala, para garantizar que se realice al menos una pasada para evitar el cambio a mitad de la herramienta durante el corte, la vida útil de la herramienta debe determinarse de acuerdo con la precisión de la pieza y la rugosidad de la superficie.
Comparado con el método de procesamiento de máquina-herramienta común, el procesamiento de control numérico presenta mayores requisitos en la herramienta, no solo necesita una buena y alta precisión, sino que también requiere un tamaño estable, alta durabilidad. La desconexión y el rendimiento de la fila también requieren una fácil instalación y ajuste para cumplir con los requisitos de alta eficiencia de máquinas herramienta CNC. Las herramientas seleccionadas para máquinas herramienta CNC se utilizan a menudo para materiales de herramientas de corte de alta velocidad (como acero de alta velocidad, carburo de grano ultrafino) y utilizan insertos indexables.
2, elija la herramienta para torneado CNC
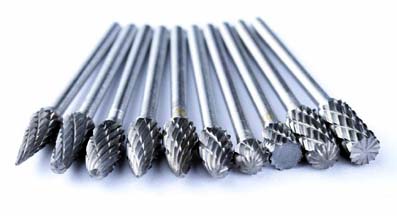
Herramienta de torneado de torno CNC de uso general puntos generales: herramienta de torno que forma, herramienta de giro afilado, herramienta de torneado de arco y cinco tipos.
Las herramientas de torneado de moldeo también se denominan herramientas de torneado modelo. La forma del contorno de las piezas de mecanizado está completamente determinada por la forma y el tamaño del borde de giro de la herramienta de torneado. En torneado CNC, las herramientas de torneado comunes incluyen cortadores de arco de pequeño radio, cortadores de ranura no rectangulares y cortadores de hilo. En CNC Mecanizado, la herramienta de moldeo debe usarse lo menos posible.
La herramienta de giro afilado es una herramienta de torneado caracterizada por un filo recto. La punta de una herramienta de torneado de este tipo consiste en bordes cortantes principales y auxiliares rectos. La herramienta de torneado interna y externa 900, las herramientas de torneado, ranurado (corte) de la cara izquierda y derecha del extremo derecho y una variedad de punta pequeña biselada y las herramientas de orificio cilíndrico. El método de selección de los parámetros geométricos (principalmente ángulos geométricos) del torneado agudo la herramienta es básicamente la misma que la del giro ordinario.
Sin embargo, se deben tener en cuenta las características del mecanizado CNC (como las rutas de procesamiento, la interferencia de procesamiento, etc.) y se debe tener en cuenta la resistencia de la punta de la herramienta.
3, seleccione la herramienta para fresado CNC
En el mecanizado de control numérico, los contornos internos y externos de las partes del plano de fresado y el plano de fresado son comúnmente utilizados molinos de fondo plano. Los datos empíricos de los parámetros relevantes de la herramienta son los siguientes:
Una es que el radio del cortador RD debe ser más pequeño que el radio mínimo de curvatura Rmin de la superficie del contorno interno de la pieza, generalmente tomando RD = (0.8-0.9) Rmin.
El segundo es la altura de procesamiento de la parte H <(1 / 4-1 / 6) RD para asegurar que la cuchilla tenga suficiente rigidez.
En tercer lugar, al fresar la parte inferior de la ranura interna con una fresa de fondo plano, el borde inferior de la ranura debe superponerse mediante dos pasadas, y el radio del borde cortante de la herramienta Re = Rr, es decir, el el diámetro es d = 2Re = 2 (Rr), el radio de la herramienta se toma como Re = 0.95 (Rr) cuando se programa.
Para un procesamiento tridimensional de superficies y perfiles de ángulos variables, se utilizan con frecuencia fresas esféricas, fresas de anillo, fresas de tambor, fresas cónicas y fresas de disco.
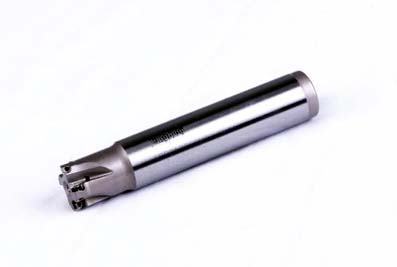
La mayoría de las máquinas herramienta CNC utilizan herramientas serializadas y estandarizadas, y los modelos estándar y serializados nacionales están disponibles para los portaherramientas y cabezas de corte de las máquinas herramienta indexables, como la herramienta de torneado externo y la herramienta de torneado frontal. Para centros de mecanizado y máquinas herramienta con cambiador automático de herramientas, los portaherramientas se han serializado y estandarizado. Por ejemplo, el código estándar para el sistema de herramientas de mango cónico es TSG-JT, y el código estándar para el sistema de herramientas de mango recto es DSG-JZ.
Además, para la herramienta seleccionada, el tamaño de la herramienta debe medirse estrictamente para obtener datos precisos antes de su uso. El operador introduce estos datos en el sistema de datos y completa el proceso de mecanizado llamando al programa, produciendo así una pieza de trabajo calificada.
Punto de cuchillo
¿Desde dónde comenzó la herramienta a moverse a la posición especificada?
Por lo tanto, al comienzo de la ejecución del programa, se debe determinar la posición de la herramienta en el sistema de coordenadas de la pieza. Esta posición es el punto de partida de la herramienta en relación con la pieza de trabajo durante la ejecución del programa. Por lo tanto, se llama el punto de partida del programa o el punto del cuchillo.
Este punto de partida generalmente está determinado por el cuchillo, por lo que este punto también se llama punto de cuchilla. Cuando se programa, es necesario seleccionar correctamente la posición del punto de la herramienta. El principio de establecer puntos de herramienta es facilitar el procesamiento numérico y simplificar la programación. Fácil de corregir y fácil de controlar durante el procesamiento; lo que resulta en pequeños errores de mecanizado. El punto de corte de la herramienta se puede configurar en la pieza mecanizada, o en el accesorio o la herramienta de la máquina. Para mejorar la precisión del mecanizado de la pieza, el punto de corte de la herramienta debe establecerse lo más posible en la base de diseño de la pieza o la base del proceso.
Cuando la máquina herramienta funciona realmente, la posición de la cuchilla de la herramienta se puede colocar en el punto de ajuste de la herramienta ajustando manualmente la herramienta. Es decir, la "ubicación del cuchillo" y el "punto de corte" coinciden.
La denominada "ubicación de la cuchilla" se refiere al punto de referencia de posicionamiento de la herramienta. La ubicación de la herramienta de torneado es la punta de la herramienta o el centro del arco de la punta de la herramienta.
La fresa de punta plana es el punto de intersección del eje de la herramienta y la superficie inferior de la herramienta; la fresa de punta esférica es el centro de la esfera de la bola, y la broca es la punta de la broca.
Con el funcionamiento manual de la cuchilla, la precisión de la herramienta es baja y la eficiencia es baja. Algunas fábricas utilizan una herramienta de alineación óptica, un alineador de herramienta y un dispositivo de configuración automática de herramientas para reducir el tiempo de configuración de la herramienta y aumentar la precisión de la configuración de la herramienta.
Cuando se requiere un cambio de herramienta durante el mecanizado, debe especificarse el punto de cambio de herramienta. El llamado "punto de cambio de herramienta" se refiere a la posición de cambio de herramienta cuando se gira el soporte, el cambio de herramienta debe ubicarse fuera de la pieza de trabajo o accesorio, no tocar la pieza de trabajo y el otro a los componentes de cambio de herramienta debe prevalecer.
Cantidad de corte
En la programación de NC, el programador debe determinar la cantidad de corte para cada proceso y escribir el programa en forma de instrucciones. Las tasas de corte incluyen la velocidad del husillo, la profundidad de corte y la velocidad de avance. Para diferentes métodos de procesamiento, se deben seleccionar diferentes cantidades de corte. El principio de selección de la cantidad de corte es garantizar la precisión y la rugosidad de la superficie de la pieza y aprovechar al máximo el rendimiento de corte de la herramienta. Garantice una vida útil razonable de la herramienta y aproveche al máximo el rendimiento de la máquina, maximice la productividad y reduzca los costos.
1, determinar la velocidad del eje
La velocidad del husillo debe seleccionarse según la velocidad de corte permitida y el diámetro de la pieza de trabajo (o herramienta). Su fórmula de cálculo es: n = 1000 v / 7 1D Tipo: v? Velocidad de corte, unidad m / m en movimiento, decidida por la durabilidad de la herramienta; n Una velocidad de husillo, en r / min, D es el diámetro de la pieza de trabajo o el diámetro de la herramienta en mm. Calcule la velocidad del husillo, n, y finalmente seleccione la velocidad propia o más cercana de la máquina.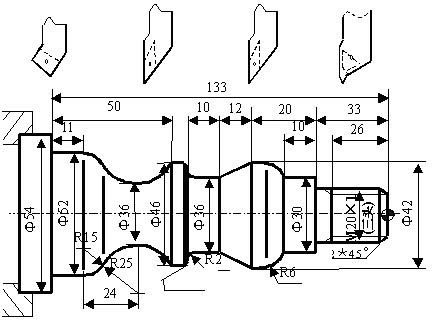
2, determinar la velocidad de alimentación
La velocidad de alimentación es un parámetro importante en la cantidad de corte de máquinas herramienta CNC. Se selecciona principalmente en función de la precisión del mecanizado y los requisitos de rugosidad de la superficie de las piezas y las propiedades del material de las herramientas y piezas de trabajo. La velocidad máxima de alimentación está limitada por la rigidez de la máquina y el rendimiento del sistema de alimentación.
El principio de determinar la velocidad de avance: Cuando se pueden garantizar los requisitos de calidad de la pieza de trabajo, para aumentar la eficiencia de producción, se puede seleccionar una velocidad de alimentación más alta. Generalmente dentro del rango de 100 a 200 mm / min;
Al cortar, procesar orificios profundos o mecanizar con herramientas de acero de alta velocidad, se deben seleccionar velocidades de alimentación más bajas, generalmente dentro del rango de 20 a 50 mm / min;
Cuando los requisitos de precisión de procesamiento y rugosidad de la superficie son altos, la velocidad de alimentación debe elegirse más pequeña, generalmente dentro del rango de 20--50 mm / min;
Cuando la herramienta está inactiva, especialmente cuando está "regresando a cero" a una distancia larga, se puede establecer el avance más alto establecido por el sistema de control numérico de la máquina.
3, determinar la profundidad de corte
La profundidad de corte está determinada por la rigidez de la máquina, la pieza de trabajo y la herramienta. Cuando la rigidez lo permite, la profundidad de corte debe ser igual a la tolerancia de mecanizado de la pieza de trabajo tanto como sea posible, lo que puede reducir el número de pasadas y aumentar la eficiencia de producción. Para garantizar la calidad de la superficie mecanizada, se puede dejar una pequeña cantidad de margen de acabado, generalmente de 0,2 a 0,5 mm. En resumen, el valor específico de la cantidad de corte debe determinarse por analogía en función del rendimiento de la máquina herramienta, los manuales relacionados y la experiencia práctica.
Al mismo tiempo, la velocidad del cabezal, la profundidad de corte y la velocidad de alimentación se pueden adaptar entre sí para formar la cantidad de corte óptima.
La cantidad de corte no solo es un parámetro importante que debe determinarse antes de ajustar la máquina herramienta, sino también si el valor es razonable o no tiene una influencia muy importante en la calidad del procesamiento, la eficiencia del procesamiento y el costo de producción.
La denominada cantidad de corte "razonable" se refiere al uso completo del rendimiento de corte de la herramienta y rendimiento de potencia de la máquina (potencia, par), bajo la premisa de garantizar la calidad, obtener alta productividad y bajos costos de procesamiento de la cantidad de corte.
Además, para la herramienta seleccionada, el tamaño de la herramienta debe medirse estrictamente para obtener datos precisos antes de su uso. El operador introduce estos datos en el sistema de datos y completa el proceso de mecanizado llamando al programa, produciendo así una pieza de trabajo calificada.
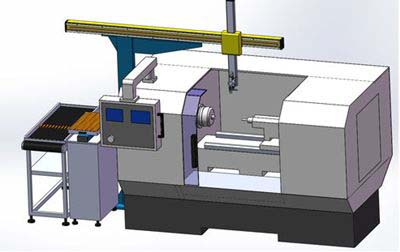
Punto de cuchillo
¿Desde dónde comenzó la herramienta a moverse a la posición especificada?
Por lo tanto, al comienzo de la ejecución del programa, se debe determinar la posición de la herramienta en el sistema de coordenadas de la pieza. Esta posición es el punto de partida de la herramienta en relación con la pieza de trabajo durante la ejecución del programa. Por lo tanto, se llama el punto de partida del programa o el punto del cuchillo.
Este punto de partida generalmente está determinado por el cuchillo, por lo que este punto también se llama punto de cuchilla. Cuando se programa, es necesario seleccionar correctamente la posición del punto de la herramienta. El principio de establecer puntos de herramienta es facilitar el procesamiento numérico y simplificar la programación. Fácil de corregir y fácil de controlar durante el procesamiento; lo que resulta en pequeños errores de mecanizado. El punto de corte de la herramienta se puede configurar en la pieza mecanizada, o en el accesorio o la herramienta de la máquina. Para mejorar la precisión del mecanizado de la pieza, el punto de corte de la herramienta debe establecerse lo más posible en la base de diseño de la pieza o la base del proceso.
Cuando la máquina herramienta funciona realmente, la posición de la cuchilla de la herramienta se puede colocar en el punto de ajuste de la herramienta ajustando manualmente la herramienta. Es decir, la "ubicación del cuchillo" y el "punto de corte" coinciden.
La denominada "ubicación de la cuchilla" se refiere al punto de referencia de posicionamiento de la herramienta. La ubicación de la herramienta de torneado es la punta de la herramienta o el centro del arco de la punta de la herramienta.
La fresa de punta plana es el punto de intersección del eje de la herramienta y la superficie inferior de la herramienta; la fresa de punta esférica es el centro de la esfera de la bola, y la broca es la punta de la broca.
Con el funcionamiento manual de la cuchilla, la precisión de la herramienta es baja y la eficiencia es baja. Algunas fábricas utilizan una herramienta de alineación óptica, un alineador de herramienta y un dispositivo de configuración automática de herramientas para reducir el tiempo de configuración de la herramienta y aumentar la precisión de la configuración de la herramienta.
Cuando se requiere un cambio de herramienta durante el mecanizado, debe especificarse el punto de cambio de herramienta. El llamado "punto de cambio de herramienta" se refiere a la posición de cambio de herramienta cuando se gira el soporte, el cambio de herramienta debe ubicarse fuera de la pieza de trabajo o accesorio, no tocar la pieza de trabajo y el otro a los componentes de cambio de herramienta debe prevalecer.
Cantidad de corte
En la programación de NC, el programador debe determinar la cantidad de corte para cada proceso y escribir el programa en forma de instrucciones. Las tasas de corte incluyen la velocidad del husillo, la profundidad de corte y la velocidad de avance. Para diferentes métodos de procesamiento, se deben seleccionar diferentes cantidades de corte. El principio de selección de la cantidad de corte es garantizar la precisión y la rugosidad de la superficie de la pieza y aprovechar al máximo el rendimiento de corte de la herramienta. Garantice una vida útil razonable de la herramienta y aproveche al máximo el rendimiento de la máquina, maximice la productividad y reduzca los costos.
1, determinar la velocidad del eje
La velocidad del husillo debe seleccionarse según la velocidad de corte permitida y el diámetro de la pieza de trabajo (o herramienta). Su fórmula de cálculo es: n = 1000 v / 7 1D Tipo: v? Velocidad de corte, unidad m / m en movimiento, decidida por la durabilidad de la herramienta; n Una velocidad de husillo, en r / min, D es el diámetro de la pieza de trabajo o el diámetro de la herramienta en mm. Calcule la velocidad del husillo, n, y finalmente seleccione la velocidad propia o más cercana de la máquina.
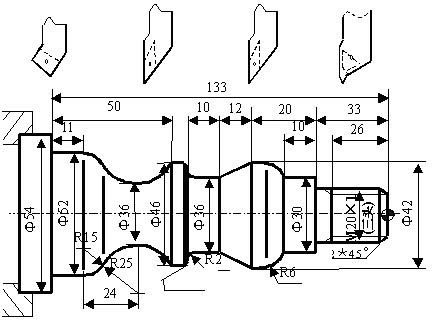
2, determinar la velocidad de alimentación
La velocidad de alimentación es un parámetro importante en la cantidad de corte de máquinas herramienta CNC. Se selecciona principalmente en función de la precisión del mecanizado y los requisitos de rugosidad de la superficie de las piezas y las propiedades del material de las herramientas y piezas de trabajo. La velocidad máxima de alimentación está limitada por la rigidez de la máquina y el rendimiento del sistema de alimentación.
El principio de determinar la velocidad de avance: Cuando se pueden garantizar los requisitos de calidad de la pieza de trabajo, para aumentar la eficiencia de producción, se puede seleccionar una velocidad de alimentación más alta. Generalmente dentro del rango de 100 a 200 mm / min;
Al cortar, procesar orificios profundos o mecanizar con herramientas de acero de alta velocidad, se deben seleccionar velocidades de alimentación más bajas, generalmente dentro del rango de 20 a 50 mm / min;
Cuando los requisitos de precisión de procesamiento y rugosidad de la superficie son altos, la velocidad de alimentación debe elegirse más pequeña, generalmente dentro del rango de 20--50 mm / min;
Cuando la herramienta está inactiva, especialmente cuando está "regresando a cero" a una distancia larga, se puede establecer el avance más alto establecido por el sistema de control numérico de la máquina.
3, determinar la profundidad de corte
La profundidad de corte está determinada por la rigidez de la máquina, la pieza de trabajo y la herramienta. Cuando la rigidez lo permite, la profundidad de corte debe ser igual a la tolerancia de mecanizado de la pieza de trabajo tanto como sea posible, lo que puede reducir el número de pasadas y aumentar la eficiencia de producción. Para garantizar la calidad de la superficie mecanizada, se puede dejar una pequeña cantidad de margen de acabado, generalmente de 0,2 a 0,5 mm. En resumen, el valor específico de la cantidad de corte debe determinarse por analogía en función del rendimiento de la máquina herramienta, los manuales relacionados y la experiencia práctica.
Al mismo tiempo, la velocidad del cabezal, la profundidad de corte y la velocidad de alimentación se pueden adaptar entre sí para formar la cantidad de corte óptima.
La cantidad de corte no solo es un parámetro importante que debe determinarse antes de ajustar la máquina herramienta, sino también si el valor es razonable o no tiene una influencia muy importante en la calidad del procesamiento, la eficiencia del procesamiento y el costo de producción.
La denominada cantidad de corte "razonable" se refiere al uso completo del rendimiento de corte de la herramienta y rendimiento de potencia de la máquina (potencia, par), bajo la premisa de garantizar la calidad, obtener alta productividad y bajos costos de procesamiento de la cantidad de corte.