Soldadura de aleaciones de aluminio y aluminio
■ análisis del material de análisis 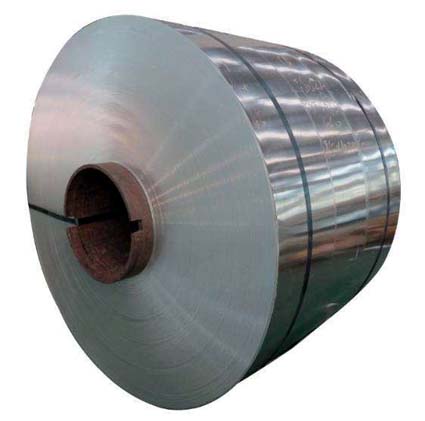
El aluminio puro industrial tiene las características generales de aluminio, baja densidad, buena conductividad eléctrica y térmica, buen rendimiento anticorrosión, buen rendimiento de procesamiento de plástico, puede procesarse en placas, tiras, láminas y productos de extrusión, etc., puede ser soldadura a gas , soldadura por arco de argón, soldadura por puntos. El aluminio industrial puro no puede ser reforzado por calor, puede aumentar la resistencia por deformación en frío, la única forma de tratamiento térmico es el recocido, la temperatura de inicio de la recristalización está relacionada con el contenido de impurezas y el grado de deformación, y generalmente es de alrededor de 200 ° C . La hoja recocida tiene σb = 80 a 100 MPa, σ0.2 = 30 a 50 MPa, ζ = 35% a 40%, y HB = 25 a 30. Después de 60% a 80% de deformación en frío, aunque se puede aumentar a 150 a 180 MPa, la entalpía disminuye a 1% a 1.5%. Aumentar el contenido de hierro y las impurezas de silicio puede aumentar la resistencia pero reducir la plasticidad, la conductividad eléctrica y la resistencia a la corrosión.
La siguiente es la composición química del material original
Tabla 2-1 Composición química del material base (L2) (GB / T3190-1996)
■ Análisis de soldabilidad del aluminio
I. Análisis de propiedades físicas y químicas
El punto de fusión del aluminio puro es bajo (660 ° C). Cuando se derrite, el color no cambia, es difícil observar el estanque fundido y es fácil colapsar y quemar durante la soldadura. La conductividad térmica es tres veces mayor que la del acero con bajo contenido de carbono, la disipación de calor es rápida y no es fácil de derretir al soldar; El coeficiente de expansión lineal es el doble que el del acero con bajo contenido de carbono y se deforma fácilmente durante la soldadura. Se oxida fácilmente en Al2O3 denso, de alto punto de fusión (punto de fusión 2050 ° C) en el aire. Es infusible y no conductivo. Puede causar una soldadura no inestable, inclusión de escoria y soldadura inestable durante la soldadura. Por lo tanto, la soldabilidad del aluminio puro es peor que la del acero bajo en carbono. Por lo tanto, las propiedades de soldadura del aluminio puro incluyen principalmente: fácil oxidación durante el proceso de soldadura, alto consumo de energía, fácil generación de poros (principalmente poros de hidrógeno gaseoso), fácil formación de grietas calientes en soldadura, fácil ablandamiento de juntas soldadas, juntas soldadas resistencia a la corrosión reducida.
1, oxidación fácil
Aluminio 1060 y la afinidad de oxígeno es muy grande, a temperatura ambiente, el aluminio se oxida fácilmente juntos, la formación de una película de Al2O3 densa en la superficie de aluminio, puede evitar la oxidación continua de metal, es beneficioso para la anticorrosión natural, pero ha traído dificultades a la soldadura. Esto se debe al alto punto de fusión de la película de alúmina (aproximadamente 2050 ° C), que supera con creces el punto de fusión del aluminio 1060, y la alta densidad de 3.95-4.10 g / m2, que es aproximadamente 1,4 veces la del aluminio. 1060, más una conductividad térmica muy alta de 1060. Soldadura Es fácil causar fenómenos que no sean de fusión, y también es probable que se conviertan en inclusiones de metal de soldadura y formen defectos de inclusión de escoria. Al mismo tiempo, la película de óxido puede absorber más humedad, la soldadura hará que la soldadura genere poros.
2, agujero de aire fácil de producir
Como el aluminio 1060 no contiene carbono, no hay ninguna condición para la formación de orificios de aire de CO, y el nitrógeno es insoluble en aluminio, por lo que generalmente se cree que la razón principal para que el aluminio 1060 genere agujeros de aire es hidrógeno. El hidrógeno es ampliamente soluble en aluminio líquido y casi insoluble en aluminio sólido. A altas temperaturas de soldadura, la solubilidad del hidrógeno en aluminio líquido disminuye drásticamente. Si el metal del baño se disuelve en hidrógeno sobresaturado, el hidrógeno sobresaturado se precipitará del metal líquido para formar pequeñas burbujas a una cierta velocidad de enfriamiento. La precipitación de hidrógeno en el proceso de solidificación de los depósitos de aluminio fundido forma, por un lado, burbujas nuevas y pequeñas y, por otro lado, se expande en pequeñas burbujas ya formadas y crece. Al mismo tiempo, debido a la pequeña densidad relativa del aluminio 1060, la burbuja flota lentamente. Si la velocidad de enfriamiento es más rápida, las burbujas no escaparán del grupo fundido, dejando el orificio de aire en la soldadura después de la solidificación. Si el proceso de solidificación del grupo fundido es relativamente lento, habrá suficiente tiempo para que las burbujas de hidrógeno escapen del baño fundido y no se formen orificios de aire en la soldadura. Por otro lado, si la velocidad de solidificación del grupo fundido es muy rápida, no se puede precipitar hidrógeno del metal líquido, pero la solución sólida sobresaturada se forma en el aluminio fundido, y el gas no se precipitará para formar un orificio de aire . Se puede ver que la velocidad de enfriamiento es una de las condiciones importantes que afectan la generación de agujeros de aire.
3, soldadura de grietas calientes
Las aleaciones de aluminio 1060 que no fortalecen el calor rara vez producen grietas durante la soldadura por fusión. Las grietas solo pueden ocurrir si el contenido de impurezas excede el rango especificado o si la rigidez es alta. La causa del agrietamiento térmico en aluminio 1060 está relacionada con su composición y tensión de soldadura. Como el aluminio 1060 tiene un coeficiente de expansión lineal que es casi el doble que el del hierro, y su contracción de solidificación es dos veces mayor que la del hierro, el esfuerzo de soldadura de la soldadura de aluminio es grande.
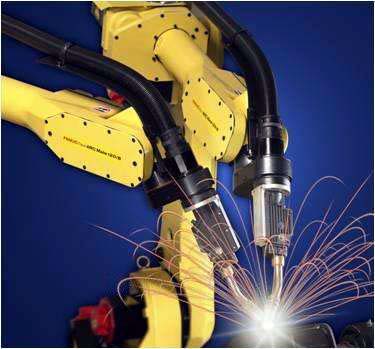
4, alta conductividad y conductividad térmica
La conductividad térmica del aluminio 1060 es muy grande, aproximadamente cuatro veces mayor que la del acero, y su capacidad calorífica es casi el doble que la del acero. Por lo tanto, la soldadura de aluminio 1060 consume más calor que el acero. Para obtener juntas soldadas de alta calidad, es necesario utilizar una fuente de calor con energía concentrada y gran potencia para realizar soldaduras normales, especialmente cuando el grosor de la pieza de trabajo es grande. El aluminio 1060 tiene buena conductividad eléctrica y la soldadura por resistencia requiere más potencia.
5, alta temperatura hace que la fuerza y plasticidad baja
La resistencia y la plasticidad del aluminio 1060 a altas temperaturas es muy baja, como la resistencia a 370 ° C es de aproximadamente 1MPa, a menudo no puede soportar el peso de la piscina de líquidos, la destrucción de la formación de metal de soldadura, a veces también causa el colapso de la soldar metal y quemar.
6, sin cambio de color
Cuando el aluminio 1060 cambia de sólido a líquido, no hay un cambio de color obvio, por lo que no es fácil juzgar la temperatura del baño. Además, cuando la temperatura aumenta, la resistencia del aluminio 1060 disminuye. Por lo tanto, es difícil captar la temperatura de calentamiento durante la soldadura, y a menudo no es posible percibir la combustión debido a una temperatura excesivamente alta.
En general, el aluminio 1060 tiene buena soldabilidad. Siempre que las características de soldadura anteriores se seleccionen correctamente, el método de soldadura, el material de soldadura, el proceso de limpieza previa a la soldadura y el proceso de operación de soldadura se pueden usar adecuadamente para obtener una buena junta soldada.
El grosor de la carcasa de la carcasa es de 16 mm, por lo que antes de la soldadura, para evitar grietas calientes, debe precalentarse con una temperatura de precalentamiento de 120-140 ° C.
(2) métodos de soldadura incorrectos
Por ejemplo, si la energía de la línea de soldadura por arco sumergido es grande, aparecerá una estructura de grano grueso en la zona afectada por el calor de la zona afectada por el calor de soldadura, y se reducirá la dureza de la zona afectada por el calor. La energía de la soldadura electroslag es incluso mayor que la de la soldadura por arco sumergido. Los granos en la zona afectada por el calor son más gruesos y la dureza se reduce más obviamente. Por lo tanto, después de la soldadura automática de arco de argón de aluminio puro, los granos generalmente se refinan mediante la normalización para mejorar la tenacidad.
Plan de proceso de soldadura
El equipo de soldadura es una soldadora MIG NB-500 MIG con un rango de regulación de corriente de 50 a 500A. El diámetro del cable de soldadura es de Φ1.6mm y el gas protector, el argón, tiene una pureza de no menos del 99.96%. La razón de su elección es la siguiente:
(1) Además de la soldadura con gas CO2, casi todos los métodos de soldadura pueden usarse para soldar aluminio y aleaciones de aluminio, pero el aluminio y las aleaciones de aluminio tienen diferente idoneidad para varios métodos de soldadura, y varios métodos de soldadura tienen sus propias aplicaciones.
Los métodos de soldadura por arco y electrodo de gas son simples y fáciles de operar. La soldadura a gas se puede utilizar para reparar soldaduras de placas de aluminio delgadas y piezas fundidas que no requieren una alta calidad de soldadura. La soldadura por arco con electrodo de soldadura se puede usar para soldar piezas de aleación de aluminio. La soldadura con protección de gas inerte es soldadura TIG y soldadura MIG, son los métodos de soldadura de aluminio y aleación de aluminio más ampliamente utilizados. Desde la función de "limpieza del cátodo" y la corriente máxima de tungsteno, generalmente se utiliza la soldadura de arco de tungsteno. Debido a que está bajo la buena protección de la soldadura de argón, el grupo fundido puede protegerse del oxígeno, el hidrógeno y otros gases nocivos. La corriente de soldadura de arco de argón es estable, el calor se concentra, el tejido de soldadura es compacto, la apariencia es hermosa, la resistencia y la plasticidad son altas y la deformación de la pieza de trabajo es pequeña.
Sin embargo, debido a la limitada corriente de tungsteno, la fuerza de penetración del arco es pequeña y la productividad es baja. Por lo tanto, generalmente se usa para soldar placas delgadas con un grosor de 6 mm o menos.
La potencia de arco MIG, la concentración de calor, la zona afectada por el calor es pequeña, la productividad puede ser más de tres veces más que la soldadura TIG. Por lo tanto, es adecuado para la soldadura de estructuras de placas gruesas. Puede soldar placas de aluminio y aleaciones de aluminio por debajo de 50 mm. La soldadura de placas de aluminio de 30 mm de espesor puede realizarse sin precalentamiento. La soldadura MIG semiautomática se utiliza principalmente para soldadura por puntos, soldaduras pequeñas e intermitentes y soldadura de piezas de forma irregular.
(2) La conductividad térmica y la capacidad de calor específica del aluminio y sus aleaciones son más de dos veces más bajas que las del acero al carbono y acero de baja aleación. La conductividad térmica del aluminio es más de diez veces mayor que la del acero inoxidable austenítico. En el proceso de soldadura, una gran cantidad de energía térmica se transfiere rápidamente al interior de la matriz metálica. Por lo tanto, al soldar aluminio y aleaciones de aluminio, la energía se consume en el depósito de metal fundido y se consume más calor en otras partes del metal.
Este tipo de consumo de energía inútil es más importante que la soldadura de acero. Para obtener juntas soldadas de alta calidad, debería ser posible utilizar energía concentrada, energía de alta potencia y precalentamiento y otras medidas tecnológicas.
Soldadura MIG en comparación con soldadura TIG, soldadura MIG del área mínima de calentamiento de 10-4cm2, la densidad de potencia máxima de 104 ~ 105w • cm-2, el área mínima de calentamiento de la soldadura TIG es de 10-3cm2, y la densidad máxima de potencia es 1.5-104w • cm-2. Por lo tanto, es mejor usar soldadura MIG.
(3) Selección de alambre de soldadura de aluminio y aleación de aluminio Además de considerar un buen rendimiento del proceso de soldadura, la resistencia a la tracción y la plasticidad (mediante prueba de flexión) de la unión a tope deben cumplir los requisitos especificados de acuerdo con los requisitos del contenedor. Para buques con requisitos de resistencia a la corrosión, la resistencia a la corrosión de las uniones soldadas también debe ser igual o cercana a la del metal principal. Por lo tanto, la selección de alambre de soldadura se basa principalmente en los siguientes principios:
1. La pureza del alambre de soldadura de aluminio puro generalmente no es menor que la del metal original;
2. La composición química del alambre de soldadura de aleación de aluminio generalmente corresponde a o es similar al metal principal;
3. El contenido de elementos resistentes a la corrosión (magnesio, manganeso, silicio, etc.) en alambre de soldadura de aleación de aluminio generalmente no es inferior al del metal original;
4. Cuando el aluminio diferente está soldado, el alambre de soldadura debe seleccionarse de acuerdo con el material original con alta resistencia a la corrosión y alta resistencia;
5. Las aleaciones de aluminio de alta resistencia que no requieren resistencia a la corrosión (aleaciones de aluminio reforzado con tratamiento térmico) pueden usar alambres de aleación diferentes, como SAlSi-1, que tiene buena resistencia al agrietamiento y pueden tener una resistencia menor que el metal base.
De acuerdo con el uso de tanques de almacenamiento de aluminio, de acuerdo con los principios anteriores (resistencia igual, etc.), el cable ahora se selecciona como SAl-2, cuyo contenido de aluminio es superior a 1060 (L2) aluminio puro industrial, con el fin de asegurar la resistencia a la corrosión de las uniones soldadas. .
(4) Selección de gas de protección
Soldadura MIG de aluminio y aleación de aluminio, utilizando únicamente gas inerte argón o helio, no se utiliza gas reactivo. Aunque el argón o helio es un gas protector, sus propiedades físicas son diferentes y, por lo tanto, su rendimiento en el proceso también es diferente. La densidad del argón es aproximadamente 1,4 veces la del aire, más pesada que el aire; La densidad del helio es aproximadamente 0,14 veces mayor que la del aire, más ligera que el aire. Al soldar en la posición de soldadura plana, el gas de argón se hunde y aleja el aire. Esto protege el arco y cubre la zona de soldadura. Si se selecciona protección contra el gas helio, se obtiene el mismo efecto protector. El flujo y consumo de gas helio es aproximadamente de 2 a 3 veces mayor que el del gas argón.
Además, la conductividad térmica del helio es más alta que la del argón, y se puede generar un plasma de arco con una distribución de energía más uniforme. El plasma de arco de argón tiene una energía central alta de la columna de arco, y su energía periférica es baja. Por lo tanto, la forma de la soldadura durante la soldadura MIG de arco Xenon se caracteriza por una penetración profunda y una fusión amplia, y la parte inferior de la soldadura es un arco circular. Sin embargo, el centro de la soldadura MIG de soldadura de argón tiene una penetración "similar a un dedo" estrecha y profunda, con una penetración menos profunda en ambos lados.
El potencial de ionización del helio es más alto que el del argón. Cuando la longitud del arco y la corriente de soldadura son constantes, el voltaje de arco de la protección del gas helio es más alto que el del arco de argón. Por lo tanto, soldadura MIG protectora de helio puro, es difícil lograr una transición de chorro axial. A menudo ocurren salpicaduras frecuentes y superficies de soldadura más rugosas. La soldadura MIG protegida con argón es más fácil de lograr la transición de chorro.
Debido al bajo voltaje de arco y la baja densidad de energía de arco de la soldadura de arco de argón MIG, el arco es estable y tiene muy pocas salpicaduras, por lo que es adecuado para soldar piezas delgadas. La soldadura de arco de xenón MIG tiene una alta densidad de energía y es adecuada para soldar piezas gruesas, pero el arco no es lo suficientemente estable y el helio es costoso.
El grosor máximo de la pared de este producto es de 16 mm, por lo tanto, use argón como gas protector.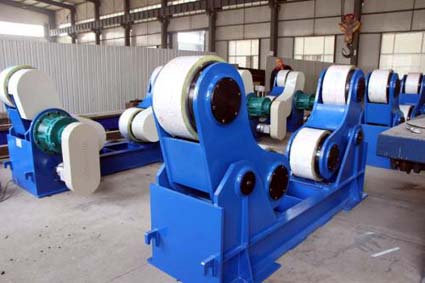
3. Preparación antes de soldar
(1) Forma de surco, forma conjunta y tamaño
La forma del surco, la forma y el tamaño de la unión dependen del espesor de la soldadura de aluminio, la posición de soldadura, la forma de transferencia de gotitas y el proceso de soldadura.
Cuando se fijan el espesor de la soldadura, la posición de soldadura y el proceso de soldadura, la forma de transferencia de gotas es una condición importante para determinar la forma de la ranura y los parámetros del proceso de soldadura.
La forma de transferencia de gotitas en soldadura MIG y la estabilidad de su proceso son la clave para la idoneidad del método de soldadura MIG. Cuando la corriente de soldadura aumenta de pequeña a grande, la transición de la gota desde la transición de cortocircuito, transición tipo gota, a la dirección de transición de inyección (transición de gota de disparo, transición de chorro). La transición de cortocircuito solo es aplicable a la soldadura MIG de piezas de pared delgada con un grosor de material de 1 a 2 mm. El proceso de transición de inyección es relativamente estable y se puede usar para la soldadura MIG de diversos materiales de aluminio de espesor. Entre la transición de cortocircuito y la transición de chorro, hay una zona de transición de chorro bajo donde no se produce un cortocircuito a pesar de la corta longitud del arco. Incluso si la longitud del arco cambia, la corriente y la tensión pueden permanecer sin cambios. Incluso con una fuente de corriente constante (características externas de caída profunda), el arco puede autorregularse, el proceso de soldadura es estable y la soldadura tiene una forma uniforme y hermosa. La experiencia práctica muestra que cuando se usa la soldadura MIG de transición bajo chorro de aluminio, la eficiencia de la soldadura es mayor y la calidad de la soldadura es mejor. La soldadura MIG, el uso general de la conexión inversa de CC, no utiliza soldadura CC positiva o alterna, soldadura automática y soldadura semiautomática de dos maneras.
Empleado en la forma de transición de chorro, el tiempo de transición de la inyección, la soldadura de dedos estrechos y profundos presenta fácilmente la penetración de los dedos, la soldadura de ambos lados de la penetración deficiente, grietas de porosidad y otros defectos. Cuando se utilizan transiciones de subimpulso, la longitud del arco es más corta, el voltaje del arco es más bajo, el arco se detona levemente y las gotas en el extremo del cable crecen para igualar el diámetro del cable a medida que pasa al grupo fundido a lo largo del eje. Puede haber un cortocircuito instantáneo durante este período. En la soldadura MIG de transición bajo chorro, el área de atomización del cátodo es grande, el efecto de protección del baño es bueno, la costura de soldadura está bien formada y los defectos de la costura de soldadura son pequeños. Por esta razón, los tanques de almacenamiento de aluminio deben considerar completamente los problemas anteriores en la selección de los parámetros de soldadura y el diseño de la ranura.
(2) Limpieza antes de soldar
La película de óxido y los contaminantes en la superficie de la soldadura de aluminio y el alambre pueden hacer que la curva estática del arco se mueva hacia abajo durante el proceso de soldadura MIG. Como resultado, la corriente de la soldadura aumenta repentinamente, la velocidad de fusión del cable aumenta y el arco se alarga.
En este punto, el sonido del arco también cambió del rítmico zumbido al rudo sonido de llamada. Por lo tanto, las partes de soldadura MIG y la superficie del alambre deben limpiarse estrictamente, la calidad de su limpieza afectará directamente la calidad de los procesos de soldadura y las juntas, como la tendencia de la porosidad de la soldadura y las propiedades mecánicas. Soldaduras y cableado Limpieza de la superficie de soldadura MIG, a menudo utilizando limpieza química y métodos de limpieza mecánica. Al mismo tiempo, es mejor utilizar alambre de soldadura de aluminio y aleación de aluminio con un alambre de soldadura liviano, liso y brillante con tratamiento superficial especial.
1. Limpieza química
Alta eficiencia de limpieza química, calidad estable, adecuado para soldadura de alambre limpio y de pequeño tamaño, producción por lotes de piezas de trabajo. Método de inmersión disponible y método de limpieza dos. Puede usarse acetona, gasolina, queroseno y otros solventes orgánicos en la superficie del aceite, con 40 ° C ~ 70 ° C 5% ~ 10% solución de NaOH lavado alcalino 3min ~ 7min (un poco más largo pero no más de 20min de aluminio puro ), enjuague con agua, luego se decapa con una solución de HNO3 al 30% a temperatura ambiente a 60 ° C durante 1 minuto a 3 minutos, se enjuaga con agua corriente, se seca al aire o se seca a baja temperatura.
2. limpieza mecánica
La limpieza mecánica se usa a menudo cuando la pieza de trabajo tiene un tamaño grande, un ciclo de producción largo, soldadura de múltiples capas o limpieza química. Primero use acetona, gasolina y otros solventes orgánicos para limpiar la superficie para eliminar el aceite, luego use directamente un cepillo de alambre de cobre con un diámetro de 0.15mm a 0.20mm o un cepillo de alambre de acero inoxidable para cepillar hasta que el brillo metálico quede expuesto. En general, no es adecuado moler con muela o papel de lija ordinario, a fin de evitar que las partículas de arena queden sobre la superficie del metal, y los defectos como la inclusión de escoria se generarán al soldar. Además, la superficie a soldar se puede limpiar con una espátula, un archivo o similar.
Después de limpiar y limpiar la pieza de trabajo y el alambre de soldadura, se regenerará una película de óxido durante el almacenamiento. Especialmente en un ambiente húmedo, la película de óxido crece más rápido en un ambiente contaminado por ácidos, álcalis y otros vapores. Por lo tanto, después de limpiar y limpiar las piezas de trabajo y el alambre de soldadura, el tiempo de almacenamiento antes de la soldadura debe acortarse tanto como sea posible. En climas húmedos, la soldadura generalmente debe realizarse dentro de las 4 horas de la limpieza. Después de la limpieza, si el tiempo de almacenamiento es demasiado largo (como más de 24 horas), debe volver a tratarse.
El plan de limpieza adoptado por este tanque es:
Los óxidos y otros desechos a 50 mm de la ranura y su periferia deben limpiarse. Primero use una rueda de alambre de acero inoxidable con un diámetro de menos de 0,2 mm para limpiar y luego limpiar con productos químicos. El alambre de soldadura solo se limpia químicamente. La ranura limpia debe soldarse en 2 horas, y el cable expuesto en la atmósfera después del lavado y secado no debe exceder las 4 horas.
Los parámetros de limpieza química de los tanques de aluminio se muestran en la Tabla 1:
4. Preparación del equipo de proceso
El equipo de proceso requerido para la soldadura MIG incluye carros de soldadura y rieles, manipuladores, posicionadores, transportadores de rodillos y abrazaderas para soldaduras. Las costuras de soldadura principales para los tanques de almacenamiento de aluminio son soldadura de un solo lado y paso único con ranura en forma de V. Con el fin de asegurar la penetración y evitar la fuga de metal en la piscina fundida, se adopta un método para agregar una junta de superficie inversa. Aquí solo la selección principal de herramientas.
(1) Liners
La soldadura MIG, como la soldadura TIG, a veces requiere una soldadura trasera, porque la potencia de soldadura MIG es mayor, la capacidad de penetración es más fuerte. La almohadilla trasera no solo es beneficiosa para evitar fugas de metal en el baño, sino que también ayuda a reducir el tamaño de la junta . Las condiciones de operación son más relajadas, y los requisitos para las habilidades de operación se pueden reducir apropiadamente. Las soldaduras longitudinales y circunferenciales del tanque de almacenamiento de aluminio están hechas de almohadillas temporales, y el material es el mismo que el del metal base, que no solo puede contaminar el baño fundido sino también facilitar la disipación del calor. La junta trasera está instalada en el accesorio para neumáticos de la soldadura, corresponde a la posición de costura de soldadura y está unida fuertemente a los lados opuestos de las dos partes. Después de soldar, se separa de la soldadura.
(2) carro de rodillos
El carro de rodillos es un equipo de proceso comúnmente utilizado para la fabricación de recipientes a presión. El bastidor del rodillo de soldadura impulsa el rodillo a través del motor y utiliza la fricción entre el rodillo de accionamiento y la pieza de soldadura para accionar la máquina de desplazamiento que gira la pieza de soldadura tubular a una velocidad determinada. El marco del rodillo de soldadura utilizado en la producción de soldadura generalmente se compone de un par de bastidores de rodillos activos y un par de bastidores de rodillos pasivos.
El marco del rodillo de soldadura se utiliza principalmente para el ensamblaje y la soldadura de cilindros cilíndricos. Cuando se realiza la soldadura de circunferencia tubular, dado que el cilindro gira sobre el rodillo, la soldadura en toda posición de la soldadura anular se cambia a soldadura plana, lo que es favorable para mejorar la calidad de la soldadura y la productividad de la soldadura. Cuando las alturas de instalación del soporte del rodillo activo y el soporte del rodillo pasivo son diferentes, también se puede realizar el montaje y la soldadura del cono y la soldadura del cilindro de diámetro desigual. Para soldaduras de sección rectangular y soldaduras de forma irregular, pueden montarse en abrazaderas anulares especiales o en carros de rodillos.
El marco del rodillo de soldadura se puede dividir en:
El bastidor de rodillo de soldadura de tipo universal y el bastidor de rodillo de soldadura especial están ahora disponibles en tipo universal. Los carros de rodillo de soldadura universales más comúnmente utilizados en la producción industrial se pueden dividir en dos categorías: uno es un bastidor de rodillo de soldadura autoajustable y el otro es un rodillo de soldadura ajustable fra
El marco del rodillo de soldadura se puede dividir en:
El bastidor de rodillo de soldadura de tipo universal y el bastidor de rodillo de soldadura especial son ahora de tipo universal ... Los carros de rodillo de soldadura universales más comúnmente utilizados en la producción industrial se pueden dividir en dos categorías: uno es un bastidor de rodillo de soldadura autoajustable y el otro es un marco de rodillo de soldadura ajustable.
La característica del bastidor de rodillo de soldadura autoajustable es que cada bastidor de rodillo consta de dos juegos de rodillos dobles. Cada grupo de soportes de rodillos puede rotar centrado en su fulcro para que pueda adaptarse a diferentes diámetros de soldaduras en un rango relativamente amplio sin cambiar la distancia entre los dos juegos de rodillos. Sin embargo, al soldar soldaduras de pequeño diámetro, el círculo exterior de la soldadura solo puede estar en contacto con los dos rodillos de cada par de bastidores de rodillos, y la capacidad de carga del bastidor del rodillo se reducirá al 75% de la carga nominal en consecuencia .
El bastidor de rodillo de soldadura autoajustable generalmente adopta el modo de transmisión dual. El motor transmite el par a los dos juegos de rodillos a través del reductor secundario y el eje de conexión para lograr una velocidad de rotación suave. El motor de accionamiento puede usar regulación electromagnética de velocidad continua o regulación de velocidad continua de inversor.
La característica del bastidor de rodillo de soldadura ajustable es que la distancia entre los rodillos de cada bastidor de rodillo es ajustable para adaptarse a piezas de soldadura de diferentes diámetros. El espaciado entre rodillos puede ajustarse por varios métodos. El método más simple es perforar dos filas de orificios de pernos con el mismo espaciado de orificios en la superficie del rodamiento del marco del rodillo. El asiento del rodillo se instala en la posición del orificio correspondiente de acuerdo con el diámetro de la soldadura. Bolt reparado. Cuando el diámetro de la pieza a soldar cambia constantemente, el paso del tornillo se puede utilizar para ajustar el paso de la rueda. Para el campo de aplicación con una pequeña gama de diámetros de soldadura, el mecanismo de conexión se puede utilizar para ajustar el espaciado entre ruedas, lo cual es muy simple y ahorra tiempo auxiliar.
El bastidor de rodillo de soldadura ajustable usualmente usa un par de bastidor de rodillo activo y un par de bastidor de rodillo pasivo para realizar operaciones de ensamblaje y soldadura. El carro de rodillos activo se puede dividir en una sola unidad y doble unidad. Ambos motores se pueden iniciar de forma sincronizada a través de circuitos electrónicos. La ventaja de la unidad dual es que la soldadura gira suavemente y elimina el rebote. China ha desarrollado el estándar de la industria JB / T9187-1999 para carritos de rodillos de soldadura. Desde el punto de vista de la seguridad, y teniendo en cuenta la elección razonable de la potencia de la rueda, el estándar industrial JB / T9187 también especifica que el ángulo de envoltura α del centro de la rueda al centro de la soldadura debe controlarse dentro del rango de 45 ° a 110 °. En la producción de soldadura real, el procedimiento de selección del marco del rodillo de soldadura es el siguiente:
1. De acuerdo con la especificación y el peso de la soldadura especificada en el programa de producción de la fábrica, y la capacidad de producción mensual, las especificaciones del bastidor del rodillo de soldadura, la capacidad de carga nominal y la cantidad a equipar se determinan tentativamente.
2. La estructura del rodillo se determina de acuerdo con el peso de la pieza soldada y el tipo de material. Para recipientes a presión de acero inoxidable, aleación de titanio y aleación de aluminio, se deben usar ruedas de caucho o poliuretano.
3. De acuerdo con el método de proceso de soldadura a ser adoptado, determine los requisitos para el rango de velocidad del marco del rodillo de soldadura y otras características técnicas.
4. De acuerdo con los requisitos de calidad de la soldadura, se debe proponer la precisión de control de la velocidad de la línea del rodillo del bastidor del rodillo de soldadura.
5. debería considerar el ambiente de trabajo.
Teniendo en cuenta la versatilidad, el tanque de almacenamiento de aluminio adopta un marco de rodillo de soldadura ajustable tipo EB-10TN, sus parámetros técnicos son:
Carga máxima 5t, capacidad de rotación máxima 10t, velocidad de la línea de rodillos 70-1200mm / min,
Diámetro de la pieza de trabajo 150-4000 mm, número de ruedas de goma 6, distancia entre las ruedas 410 a 1810,
Dimensiones: rueda motriz 3300 × 890, rueda motriz 2600 × 500 × 515, diámetro del rodillo (rueda de goma 350),
Peso: rueda motriz 600, rueda pasiva 400.
(3) manipulador de soldadura
La soldadora, también llamada posicionador de máquina de soldadura, entrega con precisión el cabezal de soldadura y lo mantiene en la posición para soldarlo. O a la velocidad de soldadura seleccionada, el cabezal de soldadura se mueve a lo largo de la trayectoria especificada, y la máquina de desplazamiento del cabezal de soldadura que completa la operación de soldadura se corresponde. Utilizado en conjunto con el posicionador de soldadura, se puede utilizar para completar una variedad de soldaduras, como la soldadura automática de juntas longitudinales, juntas anulares, juntas a tope, soldaduras en ángulo y soldaduras en curva arbitrarias. También es posible llevar a cabo procesos automáticos de superficie y corte en la superficie de la pieza de trabajo.
Existen muchos tipos de manipuladores de soldadura, y los siguientes tipos son comunes: manipuladores tipo plataforma, manipuladores en voladizo, manipuladores de brazos telescópicos, manipuladores de puertas y puentes, etc.
El manipulador de plataforma se utiliza principalmente para la soldadura de costuras longitudinales exteriores y costuras anulares exteriores de recipientes cilíndricos. El manipulador en voladizo se usa principalmente para soldar la costura longitudinal interna y la costura anular interna del contenedor. El tipo de brazo telescópico tiene muchas ventajas. Además del uso de los dos primeros, también puede completar operaciones tales como corte, rectificado y detección de defectos. Se propone utilizar un manipulador de brazo telescópico.
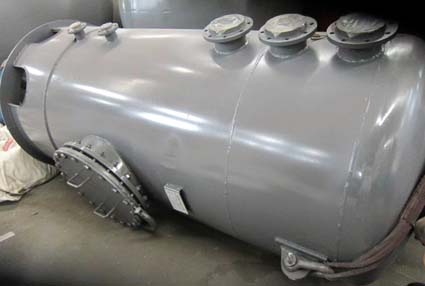
5. Montaje y soldadura
El tanque de almacenamiento de aluminio se compone de un cuerpo de cilindro, un cabezal de sellado y un tubo de conexión. El tanque de almacenamiento de aluminio se ensambla y suelda por separado, y luego el cuerpo del cilindro, el cabezal de sellado y el tubo de conexión se sueldan entre sí.
Pero el elemento de fuerza principal es la cabeza y el cilindro. A continuación, explicaremos el proceso de fabricación del tanque de almacenamiento de aluminio mediante el proceso específico de producción de cabeza y cilindro.
(1) fabricación de la cabeza
El tanque de aluminio usa una estructura de cabeza ovalada. De acuerdo con el tamaño, la lámina de aluminio puro 1060 (L2) con un tamaño de -16 × 2000 × 5800 mm se puede usar para la conformación por presión. El proceso específico es el siguiente:
Selección de material → Volver a realizar pruebas → Nivelación → Dibujo → Debajo del material → Formando → Grabado secundario → Corte del equilibrio del cabezal → Procesamiento de surco anular → Desplazamiento (agujeros) → Mecanizado de orificios → dimensiones de reexamen → limpieza antes de la soldadura → montaje.
La calidad de la lámina de aluminio puro 1060 (L2) debe cumplir con la calidad requerida por los estándares nacionales.
La cabeza elíptica es redonda antes de presionarla. De acuerdo con la fórmula Dp = k (Dn + δ) + 2h, el tamaño desarrollado es Φ1258mm. Después de considerar la reducción y el margen de mecanizado, el tamaño de corte es de Φ1270 mm. El tamaño de la cabeza antes del moldeo por compresión presiona el borde recto pulido, seguido por la prensa, con un punzón y prensa de moldeado.
El cabezal formado también se procesa en el borde para facilitar el ensamblaje del barril. Es decir, en la plataforma, una línea de posición de procesamiento que garantiza que se dibuja la altura del borde recto, y se selecciona para completar la cantidad restante de corte y procesamiento de bisel al mismo tiempo en el vehículo vertical ordinario para cumplir con los requisitos de dibujos de diseño. Después de terminar la cabeza, se debe inspeccionar la superficie interna de la cabeza. El método es verificar la plantilla interna con una longitud de cuerda igual a 3 / 4Di del diámetro interior de la cabeza.
El espacio libre máximo no debe ser mayor que 1.25% del flujo interno del cabezal. Al verificar, la plantilla debe ser perpendicular a la superficie que se va a medir.
Para el cabezal con salida de líquido, se requieren dos procesos de grabado de orificios de Ø100 mm y procesamiento de orificios después del proceso de corte del reposacabezas y el proceso de inspección.
(2) Fabricación de secciones de tubo
El tanque de almacenamiento de aluminio se compone de 3 secciones de barril. Las secciones de 3 barriles están hechas de dos piezas de 6 × 1888 × 786 mm placa de aluminio puro 1060 (L2). Cada sección tiene un agujero pero diferentes diámetros de orificio. Al ensamblar, es necesario asegurarse de que los tres orificios estén directamente sobre el cilindro, y que las juntas longitudinales de las tres secciones del cilindro en el cilindro estén escalonadas a una distancia suficiente. Por lo tanto, se debe prestar atención al tamaño de posicionamiento del orificio cuando corte material. Para más detalles, vea la tarjeta de proceso de la sección del tubo.
El proceso de fabricación de la sección del tubo es el siguiente:
Selección de material → Volver a probar → Nivelación → Escribano → Comprobar → Corte → Procesamiento de surco → Limpieza antes de soldar → Montaje de remiendo → Soldadura de remiendo → Formación de rollo → Limpieza antes de soldar → Montaje de costura longitudinal → Soldadura de costura longitudinal → Inspección de soldadura → Enderezar → Revisar dimensiones → Montaje .
Elija placas de aluminio puro 1060 (L2) de 6 × 1000 × 2000 mm, y la calidad debe cumplir con la calidad requerida por las normas nacionales. La sección del tubo generalmente se enrolla en una máquina de bobinado. Dado que el diámetro interno de la sección del tubo es mucho más grande que el espesor de la pared, por lo tanto, la longitud de desarrollo L del tubo en blanco se calcula como el diámetro promedio Dp de la sección del tubo.
Es decir, L = πDp = π (Dg + δ) = 3787mm Dg - el diámetro interno de la sección del tubo δ - el espesor de la pared de la sección del tubo
Después de desplegar la sección del tubo, es rectangular, y su tamaño de borrado también debe considerar la contracción y el margen de mecanizado, y observar que la dirección de despliegue de la sección del tubo es consistente con la dirección de la fibra rodante del tablero. La línea incluye la línea de posición de corte, la línea de borde, la línea central del agujero y la línea de posición, y la marca está marcada. También debería verificar la diagonal rectangular, error ≤ 2 mm.
El trabajo de limpieza debe realizarse antes de la soldadura, y cuando se realiza la soldadura de ensamblaje, la soldadura se coloca en la parte frontal de la ranura. La soldadura debe ser delgada, y la longitud de la soldadura por puntos es generalmente de 40-60 mm.
Las secciones de tubo se pueden laminar en frío en máquinas de bobinado de tres o cuatro rodillos. En el proceso de rodadura, a menudo debe verificar la curvatura con una plantilla. La cantidad de desalineación longitudinal y desalineación longitudinal en la costura longitudinal del círculo enrollado deberá cumplir los requisitos técnicos. (Espacio de soldadura de tachuela de ensamblaje 0 ~ 2 mm; lado incorrecto <1 mm; elipticidad ≤ 1 mm)
Después de enrollar la sección del tubo, las juntas longitudinales deben montarse antes de la soldadura longitudinal. Apalancamiento: tensores de tornillo, caballos de presión en espiral y otros accesorios para eliminar los problemas de calidad después del laminado. Cumpla con los requisitos de tecnología de ensamblaje para uniones a tope de juntas longitudinales para garantizar la calidad de la soldadura. La soldadura con cremallera se realiza después del ensamblaje. La ranura longitudinal de la sección del tubo se procesa antes de enrollarla, y se debe observar la limpieza en ambos lados de la ranura antes de soldar.
Se requiere que la calidad de soldadura de las juntas longitudinales de la sección del tubo sea alta. Durante la soldadura, se realizó la placa de prueba de soldadura del tanque de almacenamiento de aluminio.
Al mismo tiempo, debido a la mala calidad de la soldadura por arco y la extinción de arco, se montaron placas de soldadura por arco y placas de plomo con una longitud de 100 mm, un ancho de 80 mm y una pieza de trabajo en ambos extremos de la soldadura longitudinal antes de soldar Ver FIG. 2 para las condiciones de montaje. Después de soldar las juntas longitudinales de la sección tubular, se deben llevar a cabo inspecciones no destructivas según se requiera, y luego se deben enderezar para cumplir con los requisitos de redondez antes de enviarlas al conjunto.
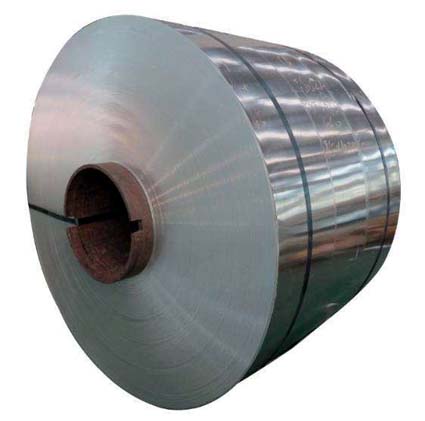
El aluminio puro industrial tiene las características generales de aluminio, baja densidad, buena conductividad eléctrica y térmica, buen rendimiento anticorrosión, buen rendimiento de procesamiento de plástico, puede procesarse en placas, tiras, láminas y productos de extrusión, etc., puede ser soldadura a gas , soldadura por arco de argón, soldadura por puntos. El aluminio industrial puro no puede ser reforzado por calor, puede aumentar la resistencia por deformación en frío, la única forma de tratamiento térmico es el recocido, la temperatura de inicio de la recristalización está relacionada con el contenido de impurezas y el grado de deformación, y generalmente es de alrededor de 200 ° C . La hoja recocida tiene σb = 80 a 100 MPa, σ0.2 = 30 a 50 MPa, ζ = 35% a 40%, y HB = 25 a 30. Después de 60% a 80% de deformación en frío, aunque se puede aumentar a 150 a 180 MPa, la entalpía disminuye a 1% a 1.5%. Aumentar el contenido de hierro y las impurezas de silicio puede aumentar la resistencia pero reducir la plasticidad, la conductividad eléctrica y la resistencia a la corrosión.
La siguiente es la composición química del material original
Tabla 2-1 Composición química del material base (L2) (GB / T3190-1996)
Grado | Al | Si | Mn | Fe | Cu |
L2 | 99.6 | 0.25 | 0.03 |
0.35 |
0.05 |
■ Análisis de soldabilidad del aluminio
I. Análisis de propiedades físicas y químicas
El punto de fusión del aluminio puro es bajo (660 ° C). Cuando se derrite, el color no cambia, es difícil observar el estanque fundido y es fácil colapsar y quemar durante la soldadura. La conductividad térmica es tres veces mayor que la del acero con bajo contenido de carbono, la disipación de calor es rápida y no es fácil de derretir al soldar; El coeficiente de expansión lineal es el doble que el del acero con bajo contenido de carbono y se deforma fácilmente durante la soldadura. Se oxida fácilmente en Al2O3 denso, de alto punto de fusión (punto de fusión 2050 ° C) en el aire. Es infusible y no conductivo. Puede causar una soldadura no inestable, inclusión de escoria y soldadura inestable durante la soldadura. Por lo tanto, la soldabilidad del aluminio puro es peor que la del acero bajo en carbono. Por lo tanto, las propiedades de soldadura del aluminio puro incluyen principalmente: fácil oxidación durante el proceso de soldadura, alto consumo de energía, fácil generación de poros (principalmente poros de hidrógeno gaseoso), fácil formación de grietas calientes en soldadura, fácil ablandamiento de juntas soldadas, juntas soldadas resistencia a la corrosión reducida.
1, oxidación fácil
Aluminio 1060 y la afinidad de oxígeno es muy grande, a temperatura ambiente, el aluminio se oxida fácilmente juntos, la formación de una película de Al2O3 densa en la superficie de aluminio, puede evitar la oxidación continua de metal, es beneficioso para la anticorrosión natural, pero ha traído dificultades a la soldadura. Esto se debe al alto punto de fusión de la película de alúmina (aproximadamente 2050 ° C), que supera con creces el punto de fusión del aluminio 1060, y la alta densidad de 3.95-4.10 g / m2, que es aproximadamente 1,4 veces la del aluminio. 1060, más una conductividad térmica muy alta de 1060. Soldadura Es fácil causar fenómenos que no sean de fusión, y también es probable que se conviertan en inclusiones de metal de soldadura y formen defectos de inclusión de escoria. Al mismo tiempo, la película de óxido puede absorber más humedad, la soldadura hará que la soldadura genere poros.
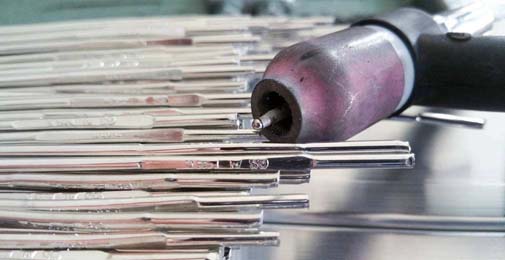
Como el aluminio 1060 no contiene carbono, no hay ninguna condición para la formación de orificios de aire de CO, y el nitrógeno es insoluble en aluminio, por lo que generalmente se cree que la razón principal para que el aluminio 1060 genere agujeros de aire es hidrógeno. El hidrógeno es ampliamente soluble en aluminio líquido y casi insoluble en aluminio sólido. A altas temperaturas de soldadura, la solubilidad del hidrógeno en aluminio líquido disminuye drásticamente. Si el metal del baño se disuelve en hidrógeno sobresaturado, el hidrógeno sobresaturado se precipitará del metal líquido para formar pequeñas burbujas a una cierta velocidad de enfriamiento. La precipitación de hidrógeno en el proceso de solidificación de los depósitos de aluminio fundido forma, por un lado, burbujas nuevas y pequeñas y, por otro lado, se expande en pequeñas burbujas ya formadas y crece. Al mismo tiempo, debido a la pequeña densidad relativa del aluminio 1060, la burbuja flota lentamente. Si la velocidad de enfriamiento es más rápida, las burbujas no escaparán del grupo fundido, dejando el orificio de aire en la soldadura después de la solidificación. Si el proceso de solidificación del grupo fundido es relativamente lento, habrá suficiente tiempo para que las burbujas de hidrógeno escapen del baño fundido y no se formen orificios de aire en la soldadura. Por otro lado, si la velocidad de solidificación del grupo fundido es muy rápida, no se puede precipitar hidrógeno del metal líquido, pero la solución sólida sobresaturada se forma en el aluminio fundido, y el gas no se precipitará para formar un orificio de aire . Se puede ver que la velocidad de enfriamiento es una de las condiciones importantes que afectan la generación de agujeros de aire.
3, soldadura de grietas calientes
Las aleaciones de aluminio 1060 que no fortalecen el calor rara vez producen grietas durante la soldadura por fusión. Las grietas solo pueden ocurrir si el contenido de impurezas excede el rango especificado o si la rigidez es alta. La causa del agrietamiento térmico en aluminio 1060 está relacionada con su composición y tensión de soldadura. Como el aluminio 1060 tiene un coeficiente de expansión lineal que es casi el doble que el del hierro, y su contracción de solidificación es dos veces mayor que la del hierro, el esfuerzo de soldadura de la soldadura de aluminio es grande.
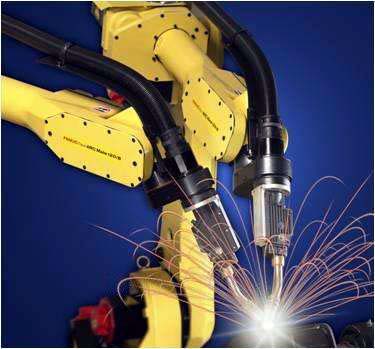
4, alta conductividad y conductividad térmica
La conductividad térmica del aluminio 1060 es muy grande, aproximadamente cuatro veces mayor que la del acero, y su capacidad calorífica es casi el doble que la del acero. Por lo tanto, la soldadura de aluminio 1060 consume más calor que el acero. Para obtener juntas soldadas de alta calidad, es necesario utilizar una fuente de calor con energía concentrada y gran potencia para realizar soldaduras normales, especialmente cuando el grosor de la pieza de trabajo es grande. El aluminio 1060 tiene buena conductividad eléctrica y la soldadura por resistencia requiere más potencia.
5, alta temperatura hace que la fuerza y plasticidad baja
La resistencia y la plasticidad del aluminio 1060 a altas temperaturas es muy baja, como la resistencia a 370 ° C es de aproximadamente 1MPa, a menudo no puede soportar el peso de la piscina de líquidos, la destrucción de la formación de metal de soldadura, a veces también causa el colapso de la soldar metal y quemar.
6, sin cambio de color
Cuando el aluminio 1060 cambia de sólido a líquido, no hay un cambio de color obvio, por lo que no es fácil juzgar la temperatura del baño. Además, cuando la temperatura aumenta, la resistencia del aluminio 1060 disminuye. Por lo tanto, es difícil captar la temperatura de calentamiento durante la soldadura, y a menudo no es posible percibir la combustión debido a una temperatura excesivamente alta.
En general, el aluminio 1060 tiene buena soldabilidad. Siempre que las características de soldadura anteriores se seleccionen correctamente, el método de soldadura, el material de soldadura, el proceso de limpieza previa a la soldadura y el proceso de operación de soldadura se pueden usar adecuadamente para obtener una buena junta soldada.
El grosor de la carcasa de la carcasa es de 16 mm, por lo que antes de la soldadura, para evitar grietas calientes, debe precalentarse con una temperatura de precalentamiento de 120-140 ° C.
(2) métodos de soldadura incorrectos
Por ejemplo, si la energía de la línea de soldadura por arco sumergido es grande, aparecerá una estructura de grano grueso en la zona afectada por el calor de la zona afectada por el calor de soldadura, y se reducirá la dureza de la zona afectada por el calor. La energía de la soldadura electroslag es incluso mayor que la de la soldadura por arco sumergido. Los granos en la zona afectada por el calor son más gruesos y la dureza se reduce más obviamente. Por lo tanto, después de la soldadura automática de arco de argón de aluminio puro, los granos generalmente se refinan mediante la normalización para mejorar la tenacidad.
Plan de proceso de soldadura
El equipo de soldadura es una soldadora MIG NB-500 MIG con un rango de regulación de corriente de 50 a 500A. El diámetro del cable de soldadura es de Φ1.6mm y el gas protector, el argón, tiene una pureza de no menos del 99.96%. La razón de su elección es la siguiente:
(1) Además de la soldadura con gas CO2, casi todos los métodos de soldadura pueden usarse para soldar aluminio y aleaciones de aluminio, pero el aluminio y las aleaciones de aluminio tienen diferente idoneidad para varios métodos de soldadura, y varios métodos de soldadura tienen sus propias aplicaciones.
Los métodos de soldadura por arco y electrodo de gas son simples y fáciles de operar. La soldadura a gas se puede utilizar para reparar soldaduras de placas de aluminio delgadas y piezas fundidas que no requieren una alta calidad de soldadura. La soldadura por arco con electrodo de soldadura se puede usar para soldar piezas de aleación de aluminio. La soldadura con protección de gas inerte es soldadura TIG y soldadura MIG, son los métodos de soldadura de aluminio y aleación de aluminio más ampliamente utilizados. Desde la función de "limpieza del cátodo" y la corriente máxima de tungsteno, generalmente se utiliza la soldadura de arco de tungsteno. Debido a que está bajo la buena protección de la soldadura de argón, el grupo fundido puede protegerse del oxígeno, el hidrógeno y otros gases nocivos. La corriente de soldadura de arco de argón es estable, el calor se concentra, el tejido de soldadura es compacto, la apariencia es hermosa, la resistencia y la plasticidad son altas y la deformación de la pieza de trabajo es pequeña.
Sin embargo, debido a la limitada corriente de tungsteno, la fuerza de penetración del arco es pequeña y la productividad es baja. Por lo tanto, generalmente se usa para soldar placas delgadas con un grosor de 6 mm o menos.
La potencia de arco MIG, la concentración de calor, la zona afectada por el calor es pequeña, la productividad puede ser más de tres veces más que la soldadura TIG. Por lo tanto, es adecuado para la soldadura de estructuras de placas gruesas. Puede soldar placas de aluminio y aleaciones de aluminio por debajo de 50 mm. La soldadura de placas de aluminio de 30 mm de espesor puede realizarse sin precalentamiento. La soldadura MIG semiautomática se utiliza principalmente para soldadura por puntos, soldaduras pequeñas e intermitentes y soldadura de piezas de forma irregular.
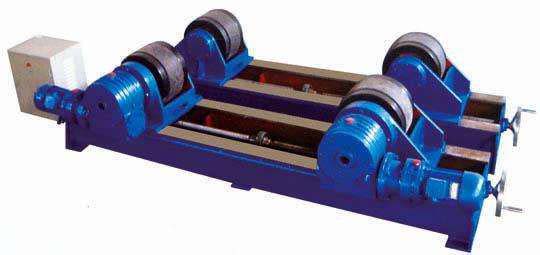
Este tipo de consumo de energía inútil es más importante que la soldadura de acero. Para obtener juntas soldadas de alta calidad, debería ser posible utilizar energía concentrada, energía de alta potencia y precalentamiento y otras medidas tecnológicas.
Soldadura MIG en comparación con soldadura TIG, soldadura MIG del área mínima de calentamiento de 10-4cm2, la densidad de potencia máxima de 104 ~ 105w • cm-2, el área mínima de calentamiento de la soldadura TIG es de 10-3cm2, y la densidad máxima de potencia es 1.5-104w • cm-2. Por lo tanto, es mejor usar soldadura MIG.
(3) Selección de alambre de soldadura de aluminio y aleación de aluminio Además de considerar un buen rendimiento del proceso de soldadura, la resistencia a la tracción y la plasticidad (mediante prueba de flexión) de la unión a tope deben cumplir los requisitos especificados de acuerdo con los requisitos del contenedor. Para buques con requisitos de resistencia a la corrosión, la resistencia a la corrosión de las uniones soldadas también debe ser igual o cercana a la del metal principal. Por lo tanto, la selección de alambre de soldadura se basa principalmente en los siguientes principios:
1. La pureza del alambre de soldadura de aluminio puro generalmente no es menor que la del metal original;
2. La composición química del alambre de soldadura de aleación de aluminio generalmente corresponde a o es similar al metal principal;
3. El contenido de elementos resistentes a la corrosión (magnesio, manganeso, silicio, etc.) en alambre de soldadura de aleación de aluminio generalmente no es inferior al del metal original;
4. Cuando el aluminio diferente está soldado, el alambre de soldadura debe seleccionarse de acuerdo con el material original con alta resistencia a la corrosión y alta resistencia;
5. Las aleaciones de aluminio de alta resistencia que no requieren resistencia a la corrosión (aleaciones de aluminio reforzado con tratamiento térmico) pueden usar alambres de aleación diferentes, como SAlSi-1, que tiene buena resistencia al agrietamiento y pueden tener una resistencia menor que el metal base.
De acuerdo con el uso de tanques de almacenamiento de aluminio, de acuerdo con los principios anteriores (resistencia igual, etc.), el cable ahora se selecciona como SAl-2, cuyo contenido de aluminio es superior a 1060 (L2) aluminio puro industrial, con el fin de asegurar la resistencia a la corrosión de las uniones soldadas. .
(4) Selección de gas de protección
Soldadura MIG de aluminio y aleación de aluminio, utilizando únicamente gas inerte argón o helio, no se utiliza gas reactivo. Aunque el argón o helio es un gas protector, sus propiedades físicas son diferentes y, por lo tanto, su rendimiento en el proceso también es diferente. La densidad del argón es aproximadamente 1,4 veces la del aire, más pesada que el aire; La densidad del helio es aproximadamente 0,14 veces mayor que la del aire, más ligera que el aire. Al soldar en la posición de soldadura plana, el gas de argón se hunde y aleja el aire. Esto protege el arco y cubre la zona de soldadura. Si se selecciona protección contra el gas helio, se obtiene el mismo efecto protector. El flujo y consumo de gas helio es aproximadamente de 2 a 3 veces mayor que el del gas argón.
Además, la conductividad térmica del helio es más alta que la del argón, y se puede generar un plasma de arco con una distribución de energía más uniforme. El plasma de arco de argón tiene una energía central alta de la columna de arco, y su energía periférica es baja. Por lo tanto, la forma de la soldadura durante la soldadura MIG de arco Xenon se caracteriza por una penetración profunda y una fusión amplia, y la parte inferior de la soldadura es un arco circular. Sin embargo, el centro de la soldadura MIG de soldadura de argón tiene una penetración "similar a un dedo" estrecha y profunda, con una penetración menos profunda en ambos lados.
El potencial de ionización del helio es más alto que el del argón. Cuando la longitud del arco y la corriente de soldadura son constantes, el voltaje de arco de la protección del gas helio es más alto que el del arco de argón. Por lo tanto, soldadura MIG protectora de helio puro, es difícil lograr una transición de chorro axial. A menudo ocurren salpicaduras frecuentes y superficies de soldadura más rugosas. La soldadura MIG protegida con argón es más fácil de lograr la transición de chorro.
Debido al bajo voltaje de arco y la baja densidad de energía de arco de la soldadura de arco de argón MIG, el arco es estable y tiene muy pocas salpicaduras, por lo que es adecuado para soldar piezas delgadas. La soldadura de arco de xenón MIG tiene una alta densidad de energía y es adecuada para soldar piezas gruesas, pero el arco no es lo suficientemente estable y el helio es costoso.
El grosor máximo de la pared de este producto es de 16 mm, por lo tanto, use argón como gas protector.
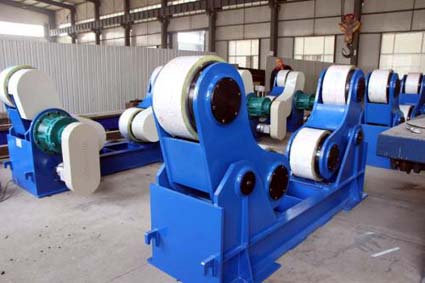
3. Preparación antes de soldar
(1) Forma de surco, forma conjunta y tamaño
La forma del surco, la forma y el tamaño de la unión dependen del espesor de la soldadura de aluminio, la posición de soldadura, la forma de transferencia de gotitas y el proceso de soldadura.
Cuando se fijan el espesor de la soldadura, la posición de soldadura y el proceso de soldadura, la forma de transferencia de gotas es una condición importante para determinar la forma de la ranura y los parámetros del proceso de soldadura.
La forma de transferencia de gotitas en soldadura MIG y la estabilidad de su proceso son la clave para la idoneidad del método de soldadura MIG. Cuando la corriente de soldadura aumenta de pequeña a grande, la transición de la gota desde la transición de cortocircuito, transición tipo gota, a la dirección de transición de inyección (transición de gota de disparo, transición de chorro). La transición de cortocircuito solo es aplicable a la soldadura MIG de piezas de pared delgada con un grosor de material de 1 a 2 mm. El proceso de transición de inyección es relativamente estable y se puede usar para la soldadura MIG de diversos materiales de aluminio de espesor. Entre la transición de cortocircuito y la transición de chorro, hay una zona de transición de chorro bajo donde no se produce un cortocircuito a pesar de la corta longitud del arco. Incluso si la longitud del arco cambia, la corriente y la tensión pueden permanecer sin cambios. Incluso con una fuente de corriente constante (características externas de caída profunda), el arco puede autorregularse, el proceso de soldadura es estable y la soldadura tiene una forma uniforme y hermosa. La experiencia práctica muestra que cuando se usa la soldadura MIG de transición bajo chorro de aluminio, la eficiencia de la soldadura es mayor y la calidad de la soldadura es mejor. La soldadura MIG, el uso general de la conexión inversa de CC, no utiliza soldadura CC positiva o alterna, soldadura automática y soldadura semiautomática de dos maneras.
Empleado en la forma de transición de chorro, el tiempo de transición de la inyección, la soldadura de dedos estrechos y profundos presenta fácilmente la penetración de los dedos, la soldadura de ambos lados de la penetración deficiente, grietas de porosidad y otros defectos. Cuando se utilizan transiciones de subimpulso, la longitud del arco es más corta, el voltaje del arco es más bajo, el arco se detona levemente y las gotas en el extremo del cable crecen para igualar el diámetro del cable a medida que pasa al grupo fundido a lo largo del eje. Puede haber un cortocircuito instantáneo durante este período. En la soldadura MIG de transición bajo chorro, el área de atomización del cátodo es grande, el efecto de protección del baño es bueno, la costura de soldadura está bien formada y los defectos de la costura de soldadura son pequeños. Por esta razón, los tanques de almacenamiento de aluminio deben considerar completamente los problemas anteriores en la selección de los parámetros de soldadura y el diseño de la ranura.
(2) Limpieza antes de soldar
La película de óxido y los contaminantes en la superficie de la soldadura de aluminio y el alambre pueden hacer que la curva estática del arco se mueva hacia abajo durante el proceso de soldadura MIG. Como resultado, la corriente de la soldadura aumenta repentinamente, la velocidad de fusión del cable aumenta y el arco se alarga.
En este punto, el sonido del arco también cambió del rítmico zumbido al rudo sonido de llamada. Por lo tanto, las partes de soldadura MIG y la superficie del alambre deben limpiarse estrictamente, la calidad de su limpieza afectará directamente la calidad de los procesos de soldadura y las juntas, como la tendencia de la porosidad de la soldadura y las propiedades mecánicas. Soldaduras y cableado Limpieza de la superficie de soldadura MIG, a menudo utilizando limpieza química y métodos de limpieza mecánica. Al mismo tiempo, es mejor utilizar alambre de soldadura de aluminio y aleación de aluminio con un alambre de soldadura liviano, liso y brillante con tratamiento superficial especial.
1. Limpieza química
Alta eficiencia de limpieza química, calidad estable, adecuado para soldadura de alambre limpio y de pequeño tamaño, producción por lotes de piezas de trabajo. Método de inmersión disponible y método de limpieza dos. Puede usarse acetona, gasolina, queroseno y otros solventes orgánicos en la superficie del aceite, con 40 ° C ~ 70 ° C 5% ~ 10% solución de NaOH lavado alcalino 3min ~ 7min (un poco más largo pero no más de 20min de aluminio puro ), enjuague con agua, luego se decapa con una solución de HNO3 al 30% a temperatura ambiente a 60 ° C durante 1 minuto a 3 minutos, se enjuaga con agua corriente, se seca al aire o se seca a baja temperatura.
2. limpieza mecánica
La limpieza mecánica se usa a menudo cuando la pieza de trabajo tiene un tamaño grande, un ciclo de producción largo, soldadura de múltiples capas o limpieza química. Primero use acetona, gasolina y otros solventes orgánicos para limpiar la superficie para eliminar el aceite, luego use directamente un cepillo de alambre de cobre con un diámetro de 0.15mm a 0.20mm o un cepillo de alambre de acero inoxidable para cepillar hasta que el brillo metálico quede expuesto. En general, no es adecuado moler con muela o papel de lija ordinario, a fin de evitar que las partículas de arena queden sobre la superficie del metal, y los defectos como la inclusión de escoria se generarán al soldar. Además, la superficie a soldar se puede limpiar con una espátula, un archivo o similar.
Después de limpiar y limpiar la pieza de trabajo y el alambre de soldadura, se regenerará una película de óxido durante el almacenamiento. Especialmente en un ambiente húmedo, la película de óxido crece más rápido en un ambiente contaminado por ácidos, álcalis y otros vapores. Por lo tanto, después de limpiar y limpiar las piezas de trabajo y el alambre de soldadura, el tiempo de almacenamiento antes de la soldadura debe acortarse tanto como sea posible. En climas húmedos, la soldadura generalmente debe realizarse dentro de las 4 horas de la limpieza. Después de la limpieza, si el tiempo de almacenamiento es demasiado largo (como más de 24 horas), debe volver a tratarse.
El plan de limpieza adoptado por este tanque es:
Los óxidos y otros desechos a 50 mm de la ranura y su periferia deben limpiarse. Primero use una rueda de alambre de acero inoxidable con un diámetro de menos de 0,2 mm para limpiar y luego limpiar con productos químicos. El alambre de soldadura solo se limpia químicamente. La ranura limpia debe soldarse en 2 horas, y el cable expuesto en la atmósfera después del lavado y secado no debe exceder las 4 horas.
Los parámetros de limpieza química de los tanques de aluminio se muestran en la Tabla 1:
Tabla 1 Parámetros del proceso de limpieza química de la ranura del tanque de aluminio | ||||
Secuencia y contenido de limpieza | Nombre de la solución | Concentración de solución /% | Temperatura de la solución / ° C | Tiempo de limpieza / min |
Limpieza de ranura y alambre | NaOH | 5 | 50~60 | 1~1.5 |
Lavado | Agua del grifo | — | >10 | 2~3 |
Limpieza de ranura y alambre | NaOH | 25~30 | >10 | 1~2 |
Lavado | Agua del grifo | — | >10 | 2~3 |
El secado | La pieza de trabajo se seca con aire caliente libre de aceite y el cable se seca y se seca a 200 ° C durante 1 hora. |
4. Preparación del equipo de proceso
El equipo de proceso requerido para la soldadura MIG incluye carros de soldadura y rieles, manipuladores, posicionadores, transportadores de rodillos y abrazaderas para soldaduras. Las costuras de soldadura principales para los tanques de almacenamiento de aluminio son soldadura de un solo lado y paso único con ranura en forma de V. Con el fin de asegurar la penetración y evitar la fuga de metal en la piscina fundida, se adopta un método para agregar una junta de superficie inversa. Aquí solo la selección principal de herramientas.
(1) Liners
La soldadura MIG, como la soldadura TIG, a veces requiere una soldadura trasera, porque la potencia de soldadura MIG es mayor, la capacidad de penetración es más fuerte. La almohadilla trasera no solo es beneficiosa para evitar fugas de metal en el baño, sino que también ayuda a reducir el tamaño de la junta . Las condiciones de operación son más relajadas, y los requisitos para las habilidades de operación se pueden reducir apropiadamente. Las soldaduras longitudinales y circunferenciales del tanque de almacenamiento de aluminio están hechas de almohadillas temporales, y el material es el mismo que el del metal base, que no solo puede contaminar el baño fundido sino también facilitar la disipación del calor. La junta trasera está instalada en el accesorio para neumáticos de la soldadura, corresponde a la posición de costura de soldadura y está unida fuertemente a los lados opuestos de las dos partes. Después de soldar, se separa de la soldadura.
(2) carro de rodillos
El carro de rodillos es un equipo de proceso comúnmente utilizado para la fabricación de recipientes a presión. El bastidor del rodillo de soldadura impulsa el rodillo a través del motor y utiliza la fricción entre el rodillo de accionamiento y la pieza de soldadura para accionar la máquina de desplazamiento que gira la pieza de soldadura tubular a una velocidad determinada. El marco del rodillo de soldadura utilizado en la producción de soldadura generalmente se compone de un par de bastidores de rodillos activos y un par de bastidores de rodillos pasivos.
El marco del rodillo de soldadura se utiliza principalmente para el ensamblaje y la soldadura de cilindros cilíndricos. Cuando se realiza la soldadura de circunferencia tubular, dado que el cilindro gira sobre el rodillo, la soldadura en toda posición de la soldadura anular se cambia a soldadura plana, lo que es favorable para mejorar la calidad de la soldadura y la productividad de la soldadura. Cuando las alturas de instalación del soporte del rodillo activo y el soporte del rodillo pasivo son diferentes, también se puede realizar el montaje y la soldadura del cono y la soldadura del cilindro de diámetro desigual. Para soldaduras de sección rectangular y soldaduras de forma irregular, pueden montarse en abrazaderas anulares especiales o en carros de rodillos.
El marco del rodillo de soldadura se puede dividir en:
El bastidor de rodillo de soldadura de tipo universal y el bastidor de rodillo de soldadura especial están ahora disponibles en tipo universal. Los carros de rodillo de soldadura universales más comúnmente utilizados en la producción industrial se pueden dividir en dos categorías: uno es un bastidor de rodillo de soldadura autoajustable y el otro es un rodillo de soldadura ajustable fra
El marco del rodillo de soldadura se puede dividir en:
El bastidor de rodillo de soldadura de tipo universal y el bastidor de rodillo de soldadura especial son ahora de tipo universal ... Los carros de rodillo de soldadura universales más comúnmente utilizados en la producción industrial se pueden dividir en dos categorías: uno es un bastidor de rodillo de soldadura autoajustable y el otro es un marco de rodillo de soldadura ajustable.
La característica del bastidor de rodillo de soldadura autoajustable es que cada bastidor de rodillo consta de dos juegos de rodillos dobles. Cada grupo de soportes de rodillos puede rotar centrado en su fulcro para que pueda adaptarse a diferentes diámetros de soldaduras en un rango relativamente amplio sin cambiar la distancia entre los dos juegos de rodillos. Sin embargo, al soldar soldaduras de pequeño diámetro, el círculo exterior de la soldadura solo puede estar en contacto con los dos rodillos de cada par de bastidores de rodillos, y la capacidad de carga del bastidor del rodillo se reducirá al 75% de la carga nominal en consecuencia .
El bastidor de rodillo de soldadura autoajustable generalmente adopta el modo de transmisión dual. El motor transmite el par a los dos juegos de rodillos a través del reductor secundario y el eje de conexión para lograr una velocidad de rotación suave. El motor de accionamiento puede usar regulación electromagnética de velocidad continua o regulación de velocidad continua de inversor.
La característica del bastidor de rodillo de soldadura ajustable es que la distancia entre los rodillos de cada bastidor de rodillo es ajustable para adaptarse a piezas de soldadura de diferentes diámetros. El espaciado entre rodillos puede ajustarse por varios métodos. El método más simple es perforar dos filas de orificios de pernos con el mismo espaciado de orificios en la superficie del rodamiento del marco del rodillo. El asiento del rodillo se instala en la posición del orificio correspondiente de acuerdo con el diámetro de la soldadura. Bolt reparado. Cuando el diámetro de la pieza a soldar cambia constantemente, el paso del tornillo se puede utilizar para ajustar el paso de la rueda. Para el campo de aplicación con una pequeña gama de diámetros de soldadura, el mecanismo de conexión se puede utilizar para ajustar el espaciado entre ruedas, lo cual es muy simple y ahorra tiempo auxiliar.
El bastidor de rodillo de soldadura ajustable usualmente usa un par de bastidor de rodillo activo y un par de bastidor de rodillo pasivo para realizar operaciones de ensamblaje y soldadura. El carro de rodillos activo se puede dividir en una sola unidad y doble unidad. Ambos motores se pueden iniciar de forma sincronizada a través de circuitos electrónicos. La ventaja de la unidad dual es que la soldadura gira suavemente y elimina el rebote. China ha desarrollado el estándar de la industria JB / T9187-1999 para carritos de rodillos de soldadura. Desde el punto de vista de la seguridad, y teniendo en cuenta la elección razonable de la potencia de la rueda, el estándar industrial JB / T9187 también especifica que el ángulo de envoltura α del centro de la rueda al centro de la soldadura debe controlarse dentro del rango de 45 ° a 110 °. En la producción de soldadura real, el procedimiento de selección del marco del rodillo de soldadura es el siguiente:
1. De acuerdo con la especificación y el peso de la soldadura especificada en el programa de producción de la fábrica, y la capacidad de producción mensual, las especificaciones del bastidor del rodillo de soldadura, la capacidad de carga nominal y la cantidad a equipar se determinan tentativamente.
2. La estructura del rodillo se determina de acuerdo con el peso de la pieza soldada y el tipo de material. Para recipientes a presión de acero inoxidable, aleación de titanio y aleación de aluminio, se deben usar ruedas de caucho o poliuretano.
3. De acuerdo con el método de proceso de soldadura a ser adoptado, determine los requisitos para el rango de velocidad del marco del rodillo de soldadura y otras características técnicas.
4. De acuerdo con los requisitos de calidad de la soldadura, se debe proponer la precisión de control de la velocidad de la línea del rodillo del bastidor del rodillo de soldadura.
5. debería considerar el ambiente de trabajo.
Teniendo en cuenta la versatilidad, el tanque de almacenamiento de aluminio adopta un marco de rodillo de soldadura ajustable tipo EB-10TN, sus parámetros técnicos son:
Carga máxima 5t, capacidad de rotación máxima 10t, velocidad de la línea de rodillos 70-1200mm / min,
Diámetro de la pieza de trabajo 150-4000 mm, número de ruedas de goma 6, distancia entre las ruedas 410 a 1810,
Dimensiones: rueda motriz 3300 × 890, rueda motriz 2600 × 500 × 515, diámetro del rodillo (rueda de goma 350),
Peso: rueda motriz 600, rueda pasiva 400.
(3) manipulador de soldadura
La soldadora, también llamada posicionador de máquina de soldadura, entrega con precisión el cabezal de soldadura y lo mantiene en la posición para soldarlo. O a la velocidad de soldadura seleccionada, el cabezal de soldadura se mueve a lo largo de la trayectoria especificada, y la máquina de desplazamiento del cabezal de soldadura que completa la operación de soldadura se corresponde. Utilizado en conjunto con el posicionador de soldadura, se puede utilizar para completar una variedad de soldaduras, como la soldadura automática de juntas longitudinales, juntas anulares, juntas a tope, soldaduras en ángulo y soldaduras en curva arbitrarias. También es posible llevar a cabo procesos automáticos de superficie y corte en la superficie de la pieza de trabajo.
Existen muchos tipos de manipuladores de soldadura, y los siguientes tipos son comunes: manipuladores tipo plataforma, manipuladores en voladizo, manipuladores de brazos telescópicos, manipuladores de puertas y puentes, etc.
El manipulador de plataforma se utiliza principalmente para la soldadura de costuras longitudinales exteriores y costuras anulares exteriores de recipientes cilíndricos. El manipulador en voladizo se usa principalmente para soldar la costura longitudinal interna y la costura anular interna del contenedor. El tipo de brazo telescópico tiene muchas ventajas. Además del uso de los dos primeros, también puede completar operaciones tales como corte, rectificado y detección de defectos. Se propone utilizar un manipulador de brazo telescópico.
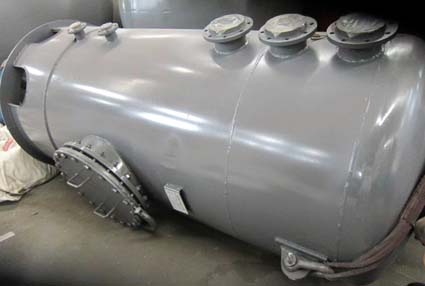
5. Montaje y soldadura
El tanque de almacenamiento de aluminio se compone de un cuerpo de cilindro, un cabezal de sellado y un tubo de conexión. El tanque de almacenamiento de aluminio se ensambla y suelda por separado, y luego el cuerpo del cilindro, el cabezal de sellado y el tubo de conexión se sueldan entre sí.
Pero el elemento de fuerza principal es la cabeza y el cilindro. A continuación, explicaremos el proceso de fabricación del tanque de almacenamiento de aluminio mediante el proceso específico de producción de cabeza y cilindro.
(1) fabricación de la cabeza
El tanque de aluminio usa una estructura de cabeza ovalada. De acuerdo con el tamaño, la lámina de aluminio puro 1060 (L2) con un tamaño de -16 × 2000 × 5800 mm se puede usar para la conformación por presión. El proceso específico es el siguiente:
Selección de material → Volver a realizar pruebas → Nivelación → Dibujo → Debajo del material → Formando → Grabado secundario → Corte del equilibrio del cabezal → Procesamiento de surco anular → Desplazamiento (agujeros) → Mecanizado de orificios → dimensiones de reexamen → limpieza antes de la soldadura → montaje.
La calidad de la lámina de aluminio puro 1060 (L2) debe cumplir con la calidad requerida por los estándares nacionales.
La cabeza elíptica es redonda antes de presionarla. De acuerdo con la fórmula Dp = k (Dn + δ) + 2h, el tamaño desarrollado es Φ1258mm. Después de considerar la reducción y el margen de mecanizado, el tamaño de corte es de Φ1270 mm. El tamaño de la cabeza antes del moldeo por compresión presiona el borde recto pulido, seguido por la prensa, con un punzón y prensa de moldeado.
El cabezal formado también se procesa en el borde para facilitar el ensamblaje del barril. Es decir, en la plataforma, una línea de posición de procesamiento que garantiza que se dibuja la altura del borde recto, y se selecciona para completar la cantidad restante de corte y procesamiento de bisel al mismo tiempo en el vehículo vertical ordinario para cumplir con los requisitos de dibujos de diseño. Después de terminar la cabeza, se debe inspeccionar la superficie interna de la cabeza. El método es verificar la plantilla interna con una longitud de cuerda igual a 3 / 4Di del diámetro interior de la cabeza.
El espacio libre máximo no debe ser mayor que 1.25% del flujo interno del cabezal. Al verificar, la plantilla debe ser perpendicular a la superficie que se va a medir.
Para el cabezal con salida de líquido, se requieren dos procesos de grabado de orificios de Ø100 mm y procesamiento de orificios después del proceso de corte del reposacabezas y el proceso de inspección.
(2) Fabricación de secciones de tubo
El tanque de almacenamiento de aluminio se compone de 3 secciones de barril. Las secciones de 3 barriles están hechas de dos piezas de 6 × 1888 × 786 mm placa de aluminio puro 1060 (L2). Cada sección tiene un agujero pero diferentes diámetros de orificio. Al ensamblar, es necesario asegurarse de que los tres orificios estén directamente sobre el cilindro, y que las juntas longitudinales de las tres secciones del cilindro en el cilindro estén escalonadas a una distancia suficiente. Por lo tanto, se debe prestar atención al tamaño de posicionamiento del orificio cuando corte material. Para más detalles, vea la tarjeta de proceso de la sección del tubo.
El proceso de fabricación de la sección del tubo es el siguiente:
Selección de material → Volver a probar → Nivelación → Escribano → Comprobar → Corte → Procesamiento de surco → Limpieza antes de soldar → Montaje de remiendo → Soldadura de remiendo → Formación de rollo → Limpieza antes de soldar → Montaje de costura longitudinal → Soldadura de costura longitudinal → Inspección de soldadura → Enderezar → Revisar dimensiones → Montaje .
Elija placas de aluminio puro 1060 (L2) de 6 × 1000 × 2000 mm, y la calidad debe cumplir con la calidad requerida por las normas nacionales. La sección del tubo generalmente se enrolla en una máquina de bobinado. Dado que el diámetro interno de la sección del tubo es mucho más grande que el espesor de la pared, por lo tanto, la longitud de desarrollo L del tubo en blanco se calcula como el diámetro promedio Dp de la sección del tubo.
Es decir, L = πDp = π (Dg + δ) = 3787mm Dg - el diámetro interno de la sección del tubo δ - el espesor de la pared de la sección del tubo
Después de desplegar la sección del tubo, es rectangular, y su tamaño de borrado también debe considerar la contracción y el margen de mecanizado, y observar que la dirección de despliegue de la sección del tubo es consistente con la dirección de la fibra rodante del tablero. La línea incluye la línea de posición de corte, la línea de borde, la línea central del agujero y la línea de posición, y la marca está marcada. También debería verificar la diagonal rectangular, error ≤ 2 mm.
El trabajo de limpieza debe realizarse antes de la soldadura, y cuando se realiza la soldadura de ensamblaje, la soldadura se coloca en la parte frontal de la ranura. La soldadura debe ser delgada, y la longitud de la soldadura por puntos es generalmente de 40-60 mm.
Las secciones de tubo se pueden laminar en frío en máquinas de bobinado de tres o cuatro rodillos. En el proceso de rodadura, a menudo debe verificar la curvatura con una plantilla. La cantidad de desalineación longitudinal y desalineación longitudinal en la costura longitudinal del círculo enrollado deberá cumplir los requisitos técnicos. (Espacio de soldadura de tachuela de ensamblaje 0 ~ 2 mm; lado incorrecto <1 mm; elipticidad ≤ 1 mm)
Después de enrollar la sección del tubo, las juntas longitudinales deben montarse antes de la soldadura longitudinal. Apalancamiento: tensores de tornillo, caballos de presión en espiral y otros accesorios para eliminar los problemas de calidad después del laminado. Cumpla con los requisitos de tecnología de ensamblaje para uniones a tope de juntas longitudinales para garantizar la calidad de la soldadura. La soldadura con cremallera se realiza después del ensamblaje. La ranura longitudinal de la sección del tubo se procesa antes de enrollarla, y se debe observar la limpieza en ambos lados de la ranura antes de soldar.
Se requiere que la calidad de soldadura de las juntas longitudinales de la sección del tubo sea alta. Durante la soldadura, se realizó la placa de prueba de soldadura del tanque de almacenamiento de aluminio.
Al mismo tiempo, debido a la mala calidad de la soldadura por arco y la extinción de arco, se montaron placas de soldadura por arco y placas de plomo con una longitud de 100 mm, un ancho de 80 mm y una pieza de trabajo en ambos extremos de la soldadura longitudinal antes de soldar Ver FIG. 2 para las condiciones de montaje. Después de soldar las juntas longitudinales de la sección tubular, se deben llevar a cabo inspecciones no destructivas según se requiera, y luego se deben enderezar para cumplir con los requisitos de redondez antes de enviarlas al conjunto.