Proceso de chapado de plata de Shell de aleacion de aluminio
Resumen: Se estudió el proceso brillante de plateado pretratado mediante la combinación de cincado secundario y galvanizado con cianuración. El flujo del proceso y los parámetros relacionados se introdujeron. Se discutieron los efectos de la preparación de la solución de zinc, la temperatura y el tiempo en el rendimiento del recubrimiento. El recubrimiento obtenido por este proceso es fino, con buena ligereza y fuerte fuerza de unión.
Palabras clave: aleación de aluminio; Lixiviación secundaria de zinc; Cianuro galvanizado; Plateado brillante
1. Introducción
El plateado de aleación de aluminio es ampliamente utilizado en electrónica, comunicaciones, electrodomésticos y otras industrias. Sin embargo, dado que el aluminio es un metal muy activo, tiene una gran afinidad por el oxígeno y forma una película de óxido en la superficie. Al mismo tiempo, el coeficiente de expansión térmica del aluminio y sus aleaciones es muy diferente del de la plata, lo que hace que sea difícil platear las piezas de aluminio.
[1] Cuanto mayor sea el tamaño de la pieza y cuanto más compleja sea la forma, más difícil será el chapado. Muchas partes de un filtro militar son partes plateadas de aleación de aluminio (marca 7R04-Hll2), en las que el plateado de la cavidad del componente principal U, tipo V es el más difícil. El tamaño de la cavidad es de 316 mm × 190 mm × 93 mm, el área de superficie es 40.6 dm2 y el tamaño de la cavidad interna es de l80 mm × 56 mm × 90 mm (profundidad). La forma de la cavidad se muestra en la Fig. L. Se requiere plateado (23 ± 2) μm y pasivación electrolítica.
La pieza tiene un gran volumen y una cavidad profunda. Para obtener una capa plateada con buena adhesión, la clave es el pretratamiento antes del chapado. Muchas investigaciones sobre el pretratamiento del aluminio y sus aleaciones se han llevado a cabo en el país y en el extranjero. El autor realizó una gran cantidad de experimentos sobre la base de resumir estos métodos.
Apagar:
El proceso de pretratamiento combinado con lixiviación secundaria de zinc y galvanización con cloruro de potasio fue replantado con plata, y la mayoría de las cavidades presentaban descamación, formación de ampollas y desprendimiento.
En el proceso de pretratamiento que combina lixiviación secundaria de zinc y galvanización con cianuración, el recubrimiento con cianuro de cobre y plata da como resultado cristales finos, buena ligereza y fuerte poder de unión, que pueden cumplir mejor con los requisitos de calidad de los productos militares.
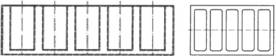
Figura1 Estructura de la carcasa
Palabras clave: aleación de aluminio; Lixiviación secundaria de zinc; Cianuro galvanizado; Plateado brillante
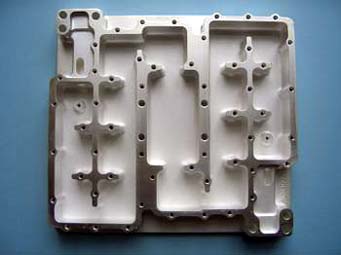
El plateado de aleación de aluminio es ampliamente utilizado en electrónica, comunicaciones, electrodomésticos y otras industrias. Sin embargo, dado que el aluminio es un metal muy activo, tiene una gran afinidad por el oxígeno y forma una película de óxido en la superficie. Al mismo tiempo, el coeficiente de expansión térmica del aluminio y sus aleaciones es muy diferente del de la plata, lo que hace que sea difícil platear las piezas de aluminio.
[1] Cuanto mayor sea el tamaño de la pieza y cuanto más compleja sea la forma, más difícil será el chapado. Muchas partes de un filtro militar son partes plateadas de aleación de aluminio (marca 7R04-Hll2), en las que el plateado de la cavidad del componente principal U, tipo V es el más difícil. El tamaño de la cavidad es de 316 mm × 190 mm × 93 mm, el área de superficie es 40.6 dm2 y el tamaño de la cavidad interna es de l80 mm × 56 mm × 90 mm (profundidad). La forma de la cavidad se muestra en la Fig. L. Se requiere plateado (23 ± 2) μm y pasivación electrolítica.
La pieza tiene un gran volumen y una cavidad profunda. Para obtener una capa plateada con buena adhesión, la clave es el pretratamiento antes del chapado. Muchas investigaciones sobre el pretratamiento del aluminio y sus aleaciones se han llevado a cabo en el país y en el extranjero. El autor realizó una gran cantidad de experimentos sobre la base de resumir estos métodos.
Apagar:
El proceso de pretratamiento combinado con lixiviación secundaria de zinc y galvanización con cloruro de potasio fue replantado con plata, y la mayoría de las cavidades presentaban descamación, formación de ampollas y desprendimiento.
En el proceso de pretratamiento que combina lixiviación secundaria de zinc y galvanización con cianuración, el recubrimiento con cianuro de cobre y plata da como resultado cristales finos, buena ligereza y fuerte poder de unión, que pueden cumplir mejor con los requisitos de calidad de los productos militares.
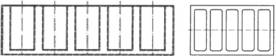
Figura1 Estructura de la carcasa
2 especificaciones de proceso
2.1 Flujo del proceso
Desengrase orgánico, desengrasado químico, corrosión alcalina, grabado ácido, lixiviación de zinc, ácido encurtido, zincado pesado, galvanizado con cianuro, chapado en cobre, plata pretendida, chapado en plata brillante, una pasivación electrolítica secada y secada por soplado.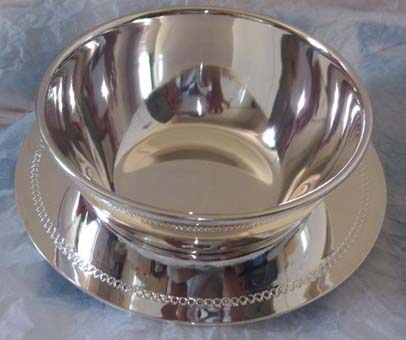
2.2 Fórmulas de solución y condiciones de proceso para cada proceso principal
2.2.1 Desengrase orgánico
A temperatura ambiente, usando gasolina de aviación l80 #.
2.2.2 Desengrase químico
2.2.3 Corrosión alcalina
El objetivo del grabado con álcali es eliminar la película de óxido en la superficie de la pieza de aluminio, para obtener una microrrugosidad ideal, y para eliminar más el aceite, a fin de aumentar la fuerza de unión del revestimiento. La respuesta es más rápida y el tiempo debe ser estrictamente controlado.
2.2.4 Grabado
Después del grabado con álcali, el cobre, el silicio, el manganeso, etc. en aluminio y sus aleaciones no se disuelven en sustancias alcalinas y permanecen en la superficie de la pieza de trabajo y el residuo de corrosión forma una película de adsorción de "cenizas colgantes".
El objetivo del grabado es disolver estos accesorios, dejando la pieza de trabajo expuesta a una superficie brillante y en un buen estado de activación.
(1) Adecuado para piezas de aleación de aluminio en general
(2) adecuado para piezas de aleación de aluminio de silicio
2.2.5 Primera filtración de Zinc
2.2.6 Segunda zincación
El proceso de zincación secundario tiene efectos obvios sobre la mejora de la calidad de la capa impregnada de zinc y la mejora de la fuerza de unión. Esto se debe al hecho de que, por primera vez de inmersión de zinc, Al203 debe disolverse antes de reemplazar Al. La capa de zinc resultante tiene un cristal áspero y suelto, distribución desigual de granos de cristal, gran diferencia de tamaño y mala adhesión de la capa impregnada de zinc. El método secundario de inmersión de zinc puede mejorar la adhesión, la uniformidad y la resistencia a la corrosión de los recubrimientos posteriores. Cuando los granos de cristal de zinc con una pobre unión entre la superficie del aluminio y sus aleaciones se disuelven en ácido nítrico, el gran tamaño de grano de los granos de zinc se vuelve más pequeño y se forma una superficie uniforme y detallada. Los granos expuestos se convierten en los centros de nucleación para la inmersión secundaria de zinc, por lo que la capa de zinc resultante es fina y se mejora la unión con el sustrato.
Las condiciones del proceso son:
2.2.7 Galvanizado de cianuro
Para la forma compleja de la pieza Shell, aunque la inmersión secundaria de zinc, la capa de zinc depositada en el crisol y la depresión profunda es relativamente delgada, y el posterior recubrimiento de cobre es propenso a la disolución debido a la fuerte alcalinidad y la temperatura más alta. De esta manera, se pierde el efecto protector de la capa de zinc sobre la capa superficial de aluminio, y la adhesión de la capa de recubrimiento se reduce severamente. Por lo tanto, es necesario galvanizar antes del cobreado para aumentar el espesor de la capa de zinc.
2.1 Flujo del proceso
Desengrase orgánico, desengrasado químico, corrosión alcalina, grabado ácido, lixiviación de zinc, ácido encurtido, zincado pesado, galvanizado con cianuro, chapado en cobre, plata pretendida, chapado en plata brillante, una pasivación electrolítica secada y secada por soplado.
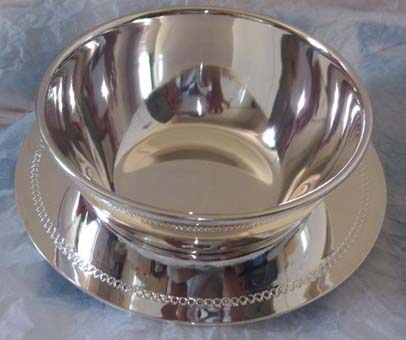
2.2 Fórmulas de solución y condiciones de proceso para cada proceso principal
2.2.1 Desengrase orgánico
A temperatura ambiente, usando gasolina de aviación l80 #.
2.2.2 Desengrase químico
Tipo B 898 desengrasante Ling | 50g/L |
θ | <50℃ |
t | 2~10min |
2.2.3 Corrosión alcalina
El objetivo del grabado con álcali es eliminar la película de óxido en la superficie de la pieza de aluminio, para obtener una microrrugosidad ideal, y para eliminar más el aceite, a fin de aumentar la fuerza de unión del revestimiento. La respuesta es más rápida y el tiempo debe ser estrictamente controlado.
NaOH | 80—100g/L |
θ | 60~700 |
Ct | 0.5~1 min |
Después del grabado con álcali, el cobre, el silicio, el manganeso, etc. en aluminio y sus aleaciones no se disuelven en sustancias alcalinas y permanecen en la superficie de la pieza de trabajo y el residuo de corrosión forma una película de adsorción de "cenizas colgantes".
El objetivo del grabado es disolver estos accesorios, dejando la pieza de trabajo expuesta a una superficie brillante y en un buen estado de activación.
(1) Adecuado para piezas de aleación de aluminio en general
HN03(p=1.639/mL) | 500 mL/L |
t | Temperatura ambiente |
f | 5~10S |
(2) adecuado para piezas de aleación de aluminio de silicio
HN03(p=1.63g/mL) | 500 mL/L |
HF(W≈40%) | 60 mL/L |
θ | Temperatura ambiente |
t | 5~10S |
Zn0 | 100g/L |
NaOH | 500g/L |
NaKC4H406·2H20 |
10g/L |
FeCl3·6H20 | 1g/L |
HF(w≈40%) | 3 mL/L |
θ | 25~30℃ |
t |
45—60S |
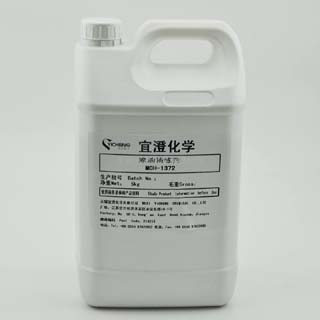
El proceso de zincación secundario tiene efectos obvios sobre la mejora de la calidad de la capa impregnada de zinc y la mejora de la fuerza de unión. Esto se debe al hecho de que, por primera vez de inmersión de zinc, Al203 debe disolverse antes de reemplazar Al. La capa de zinc resultante tiene un cristal áspero y suelto, distribución desigual de granos de cristal, gran diferencia de tamaño y mala adhesión de la capa impregnada de zinc. El método secundario de inmersión de zinc puede mejorar la adhesión, la uniformidad y la resistencia a la corrosión de los recubrimientos posteriores. Cuando los granos de cristal de zinc con una pobre unión entre la superficie del aluminio y sus aleaciones se disuelven en ácido nítrico, el gran tamaño de grano de los granos de zinc se vuelve más pequeño y se forma una superficie uniforme y detallada. Los granos expuestos se convierten en los centros de nucleación para la inmersión secundaria de zinc, por lo que la capa de zinc resultante es fina y se mejora la unión con el sustrato.
Las condiciones del proceso son:
Zn(NO)2 | 30g/L |
NaOH | 200g/L |
C6H807 | 40g/L |
FeCl3·6H20 | 1g/L |
θ | 15~30℃ |
Ct | 30~60S |
Para la forma compleja de la pieza Shell, aunque la inmersión secundaria de zinc, la capa de zinc depositada en el crisol y la depresión profunda es relativamente delgada, y el posterior recubrimiento de cobre es propenso a la disolución debido a la fuerte alcalinidad y la temperatura más alta. De esta manera, se pierde el efecto protector de la capa de zinc sobre la capa superficial de aluminio, y la adhesión de la capa de recubrimiento se reduce severamente. Por lo tanto, es necesario galvanizar antes del cobreado para aumentar el espesor de la capa de zinc.
Zn0 | 35~459/L |
NaCN | 70~90g/L |
NaOH | 60~70g/L |
95 galvanizado y agente de apertura de cianuro | 5 mL/L |
95 cianuro de chapado de zinc abrillantador | 3~5 mL/L |
θ | 5~30℃, |
J | O.5~3 A/dm2 |
t | 2~5 min |
2.2.8 Enchapado de cobre
2.2.9 Plata pretendida
CuCN | 55~85g/L |
NaCN (gratis) | 10~15g/L |
991 Brillante | l0~12mL/L |
θ | 55~65℃, |
J | 1~3 A/dm2 |
t | 10~15 min |
Método de agitación | Movimiento cátodo |
Ag(以KAg(CN)2加入) | 1~2g/L |
KCN | l00g/L |
ánodo | Plato de acero inoxidable |
J | 1~2 A/dm2 |
θ | 10~30℃ |
Ct | 5~10S |
2.2.10 plateado
Se descubrió en el experimento que si se usa un cátodo protector durante la electrodeposición de plata, el revestimiento en la superficie de Shell se cristaliza con finura y uniformidad; De lo contrario, el revestimiento en la esquina externa de la carcasa queda chamuscado. Cuando el ánodo auxiliar se usa para galvanizar plata, el grosor del revestimiento del armazón dentro de la cubierta es uniforme, de lo contrario, el revestimiento exterior del armazón es más delgado en las esquinas agudas, lo que afecta la calidad del recubrimiento. Por lo tanto, en el plateado brillante, por un lado, se usa un cátodo protector y, por otro lado, se suspende un ánodo auxiliar dentro del armazón. Los ánodos auxiliares están hechos de tiras de plata y debe haber suficientes ánodos en cada cavidad. El ánodo de plata está parcialmente pegado con cinta aislante para evitar cortocircuitar el ánodo plateado con la carcasa.
5. Conclusión
Se utiliza un proceso de pretratamiento combinado de zinc galvanizado y galvanizado para obtener un plateado brillante en la superficie del aluminio y sus aleaciones, que se caracteriza por cristales finos, buen brillo y una fuerte fuerza de unión.
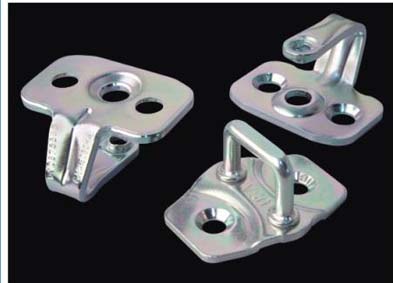
Ag(以KAg(CN)2 Join) | 20~40g/L |
KCN(free) | 90~150g/L |
KOH | 5~10g/L |
Abrillantador de plata A | 30mL/L |
Abrillantador de plata B | 15 mL/L |
θ | 10~30℃ |
J | 0.5~1.5 |
Método de agitación | Movimiento cátodo |
2.2.11 pasivación de la electrólisis
3. prueba de rendimiento de placas
3.1 Prueba de Apariencia
El método de observación visual observa la suavidad del revestimiento, la uniformidad del color y si hay imperfecciones como peladuras, ampollas, desprendimientos, picaduras, manchas y quemaduras.
3.2 prueba de fuerza vinculante
3.2.1 Método de corte transversal
En la muestra, use una cuchilla de acero para dibujar varios cuadrados con un lado de 1 mm × 1 mm. Observe si el recubrimiento en esta área se está formando ampollas o se está cayendo.
3.2.2 método de ciclo caliente y frío
Coloque la muestra en un horno eléctrico a 200 ° C e incube durante 1 h. Inmediatamente después de la eliminación, se coloca en un agua de 18 ° C a 25 ° C para que se enfríe, y se comprueba si el revestimiento se forma ampollas o se cae.
4. Factores que afectan el rendimiento de recubrimiento
4.1 Aguafuerte alcalina y ácida
El experimento encontró que la temperatura del grabado alcalino es demasiado alta y el tiempo es demasiado largo, y la superficie de la cubierta se sobregraba fácilmente; Cuando la temperatura es demasiado baja y el tiempo es demasiado corto, la película de óxido desigual en la superficie de la carcasa no se elimina por completo, lo que da como resultado una disminución en la adhesión del recubrimiento. Además, para eliminar la mezcla de tri-alúmina, elementos de aleación de silicio y sus óxidos formados después del grabado alcalino de la superficie de la carcasa, la pieza de trabajo está en un buen estado activado. Los diferentes componentes de aleación de aluminio generalmente usan diferentes soluciones de grabado ácido. que tienen un mayor impacto en la fuerza de unión del recubrimiento.
4.2 Pretratamiento
La Tabla 1 muestra el efecto de diferentes combinaciones de procesos de pretratamiento sobre la calidad del recubrimiento. Se puede ver en la tabla que solo el proceso de pretratamiento de la combinación de inmersión secundaria de zinc y galvanizado proporciona un cristal con grano fino, fuerte fuerza de unión, buena ligereza y buena calidad de recubrimiento. Shell tiene una pequeña parte de formación de ampollas debido a la falta de agua durante la operación.
Tabla 1 Efecto del proceso de pretratamiento en la calidad del recubrimiento
4.3 La temperatura de la solución de inmersión de zinc
La temperatura de la solución de inmersión de zinc tiene una gran influencia en la calidad del recubrimiento. En el proceso de deposición de zinc, para el mismo sustrato de aluminio, si la temperatura es diferente, la tasa de deposición también es diferente, y la temperatura del zinc cristaliza más rápidamente cuando se aumenta la temperatura. Si la temperatura es demasiado alta, la reacción es demasiado rápida, la capa de zinc es gruesa, los cristales son ásperos, la vida de la solución es corta, la fuerza de adhesión del recubrimiento es pobre y la tasa de aprobación del lote es baja; Si la temperatura es demasiado baja, la reacción es lenta, la capa de zinc es delgada, se descompone fácilmente durante el preenplacado y la fuerza de unión es pobre. Se sabe por el experimento que la inmersión en zinc debe llevarse a cabo a 25-30 ° C. El revestimiento resultante es uniforme, denso, con buena fuerza de unión y una alta velocidad de transferencia de lote.
4.4 Preparación de la solución de inmersión de zinc
Lashmore propuso que la adición de iones de hierro trivalentes tiene una gran influencia en la reacción de lixiviación de zinc. Por lo tanto, para cristalizar la capa de inmersión de zinc, se debe agregar FeCl3 a la solución. Los resultados experimentales muestran que el orden de adición de iones férricos también afecta seriamente el rendimiento del recubrimiento. La adición de FeCl3 y NaKC4H406 tiene un efecto significativo sobre la reacción. Si se agrega cloruro férrico directamente a la solución de hidróxido de sodio, el revestimiento resultante se espumea y se desprende. Esto se debe a que en condiciones alcalinas, los iones de hierro tienden a formar precipitados, lo que reduce la concentración efectiva de hierro en la solución. El cloruro férrico debe disolverse primero en solución de tartrato de potasio y sodio, óxido de zinc disuelto en solución de hidróxido de sodio y luego mezclarse, lo que da como resultado una buena unión del revestimiento, la tasa de aprobación del lote es alta.
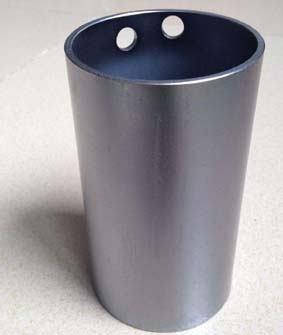
4.5 Tiempo de inmersión de zinc
Cuando el tiempo de inmersión de zinc es más de 60 s, la capa de zinc es gruesa, el cristal es rugoso, la potencia de unión es pobre y la tasa de aprobación del lote es baja. Cuando el primer tiempo de inmersión de zinc es inferior a 45 segundos y el segundo tiempo de inmersión de zinc es inferior a 30 segundos, la capa de zinc resultante es delgada, fácil de romper durante el prelaminado, y la adhesión del recubrimiento es deficiente. Por lo tanto, la primera inmersión de zinc debe controlarse a 45-60S, y el segundo tiempo de inmersión de zinc debe ser de 30-60 s. El recubrimiento obtenido es uniforme, denso, con alta fuerza de unión y alto paso de lotes
4.6 Densidad de la corriente del cátodo en la galjanoplastia del cobre del cianuro
La densidad actual de cobreado de cianuro tiene una influencia importante en la calidad del recubrimiento. Con diferentes densidades de corriente del cátodo, la fuerza de unión del recubrimiento varía enormemente. Los experimentos muestran que la densidad de corriente debe limitarse al valor permitido dentro de un corto período de tiempo después del inicio de la activación y luego reducirse a cerca del límite inferior para la galvanoplastia. De esta forma, todas las partes de la pieza de trabajo pueden depositarse con cobre para mejorar la adhesión de la capa de recubrimiento de plata subsiguiente; De lo contrario, la pieza de trabajo no se depositará en el crisol o en el hueco profundo, y la capa de recubrimiento plateado tendrá poca adhesión. Además, cuando se aplica cobreado con cianuro, las piezas deben cargarse debajo de la ranura para evitar el reemplazo de la capa de cobre.
4.7 Cátodos auxiliares para chapado de plata brillanteKECr204 | 8~10g/L |
K2C03 | 6~8g/L |
pH | 9~10 |
θ | 10~35℃ |
J | 0.5~1 A/dm2 |
t | 2~5 min |
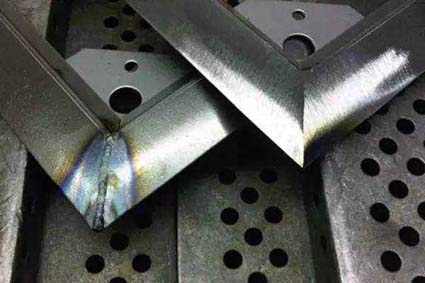
3.1 Prueba de Apariencia
El método de observación visual observa la suavidad del revestimiento, la uniformidad del color y si hay imperfecciones como peladuras, ampollas, desprendimientos, picaduras, manchas y quemaduras.
3.2 prueba de fuerza vinculante
3.2.1 Método de corte transversal
En la muestra, use una cuchilla de acero para dibujar varios cuadrados con un lado de 1 mm × 1 mm. Observe si el recubrimiento en esta área se está formando ampollas o se está cayendo.
3.2.2 método de ciclo caliente y frío
Coloque la muestra en un horno eléctrico a 200 ° C e incube durante 1 h. Inmediatamente después de la eliminación, se coloca en un agua de 18 ° C a 25 ° C para que se enfríe, y se comprueba si el revestimiento se forma ampollas o se cae.
4. Factores que afectan el rendimiento de recubrimiento
4.1 Aguafuerte alcalina y ácida
El experimento encontró que la temperatura del grabado alcalino es demasiado alta y el tiempo es demasiado largo, y la superficie de la cubierta se sobregraba fácilmente; Cuando la temperatura es demasiado baja y el tiempo es demasiado corto, la película de óxido desigual en la superficie de la carcasa no se elimina por completo, lo que da como resultado una disminución en la adhesión del recubrimiento. Además, para eliminar la mezcla de tri-alúmina, elementos de aleación de silicio y sus óxidos formados después del grabado alcalino de la superficie de la carcasa, la pieza de trabajo está en un buen estado activado. Los diferentes componentes de aleación de aluminio generalmente usan diferentes soluciones de grabado ácido. que tienen un mayor impacto en la fuerza de unión del recubrimiento.
4.2 Pretratamiento
La Tabla 1 muestra el efecto de diferentes combinaciones de procesos de pretratamiento sobre la calidad del recubrimiento. Se puede ver en la tabla que solo el proceso de pretratamiento de la combinación de inmersión secundaria de zinc y galvanizado proporciona un cristal con grano fino, fuerte fuerza de unión, buena ligereza y buena calidad de recubrimiento. Shell tiene una pequeña parte de formación de ampollas debido a la falta de agua durante la operación.
Tabla 1 Efecto del proceso de pretratamiento en la calidad del recubrimiento
Proceso de pretratamiento | Calidad de chapado |
una vez que el zinc se filtra | Cristales gruesos, luz pobre, la mayoría de Shell de la piel, ampollas, pérdida |
Dos veces lixiviación de zinc | La superficie exterior es clara como el cristal con buena ligereza, y la superficie interna de la carcasa tiene peladuras y ampollas. |
Inmersión combinada de zinc secundario y galvanizado | Cristalizado, buena luz, muy pocas conchas tienen ampollas |
Dip de aleación de zinc y níquel | La superficie exterior de la superficie está chamuscada, y la superficie interna de la carcasa está pelada, ampollada y despegada. |
Pregalvanizado | Pobre brillo, peladura de la superficie de la cáscara, formación de ampollas, derramamiento |
4.3 La temperatura de la solución de inmersión de zinc
La temperatura de la solución de inmersión de zinc tiene una gran influencia en la calidad del recubrimiento. En el proceso de deposición de zinc, para el mismo sustrato de aluminio, si la temperatura es diferente, la tasa de deposición también es diferente, y la temperatura del zinc cristaliza más rápidamente cuando se aumenta la temperatura. Si la temperatura es demasiado alta, la reacción es demasiado rápida, la capa de zinc es gruesa, los cristales son ásperos, la vida de la solución es corta, la fuerza de adhesión del recubrimiento es pobre y la tasa de aprobación del lote es baja; Si la temperatura es demasiado baja, la reacción es lenta, la capa de zinc es delgada, se descompone fácilmente durante el preenplacado y la fuerza de unión es pobre. Se sabe por el experimento que la inmersión en zinc debe llevarse a cabo a 25-30 ° C. El revestimiento resultante es uniforme, denso, con buena fuerza de unión y una alta velocidad de transferencia de lote.
4.4 Preparación de la solución de inmersión de zinc
Lashmore propuso que la adición de iones de hierro trivalentes tiene una gran influencia en la reacción de lixiviación de zinc. Por lo tanto, para cristalizar la capa de inmersión de zinc, se debe agregar FeCl3 a la solución. Los resultados experimentales muestran que el orden de adición de iones férricos también afecta seriamente el rendimiento del recubrimiento. La adición de FeCl3 y NaKC4H406 tiene un efecto significativo sobre la reacción. Si se agrega cloruro férrico directamente a la solución de hidróxido de sodio, el revestimiento resultante se espumea y se desprende. Esto se debe a que en condiciones alcalinas, los iones de hierro tienden a formar precipitados, lo que reduce la concentración efectiva de hierro en la solución. El cloruro férrico debe disolverse primero en solución de tartrato de potasio y sodio, óxido de zinc disuelto en solución de hidróxido de sodio y luego mezclarse, lo que da como resultado una buena unión del revestimiento, la tasa de aprobación del lote es alta.
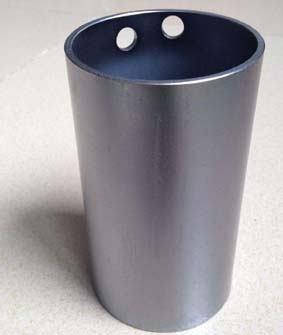
4.5 Tiempo de inmersión de zinc
Cuando el tiempo de inmersión de zinc es más de 60 s, la capa de zinc es gruesa, el cristal es rugoso, la potencia de unión es pobre y la tasa de aprobación del lote es baja. Cuando el primer tiempo de inmersión de zinc es inferior a 45 segundos y el segundo tiempo de inmersión de zinc es inferior a 30 segundos, la capa de zinc resultante es delgada, fácil de romper durante el prelaminado, y la adhesión del recubrimiento es deficiente. Por lo tanto, la primera inmersión de zinc debe controlarse a 45-60S, y el segundo tiempo de inmersión de zinc debe ser de 30-60 s. El recubrimiento obtenido es uniforme, denso, con alta fuerza de unión y alto paso de lotes
4.6 Densidad de la corriente del cátodo en la galjanoplastia del cobre del cianuro
La densidad actual de cobreado de cianuro tiene una influencia importante en la calidad del recubrimiento. Con diferentes densidades de corriente del cátodo, la fuerza de unión del recubrimiento varía enormemente. Los experimentos muestran que la densidad de corriente debe limitarse al valor permitido dentro de un corto período de tiempo después del inicio de la activación y luego reducirse a cerca del límite inferior para la galvanoplastia. De esta forma, todas las partes de la pieza de trabajo pueden depositarse con cobre para mejorar la adhesión de la capa de recubrimiento de plata subsiguiente; De lo contrario, la pieza de trabajo no se depositará en el crisol o en el hueco profundo, y la capa de recubrimiento plateado tendrá poca adhesión. Además, cuando se aplica cobreado con cianuro, las piezas deben cargarse debajo de la ranura para evitar el reemplazo de la capa de cobre.
Se descubrió en el experimento que si se usa un cátodo protector durante la electrodeposición de plata, el revestimiento en la superficie de Shell se cristaliza con finura y uniformidad; De lo contrario, el revestimiento en la esquina externa de la carcasa queda chamuscado. Cuando el ánodo auxiliar se usa para galvanizar plata, el grosor del revestimiento del armazón dentro de la cubierta es uniforme, de lo contrario, el revestimiento exterior del armazón es más delgado en las esquinas agudas, lo que afecta la calidad del recubrimiento. Por lo tanto, en el plateado brillante, por un lado, se usa un cátodo protector y, por otro lado, se suspende un ánodo auxiliar dentro del armazón. Los ánodos auxiliares están hechos de tiras de plata y debe haber suficientes ánodos en cada cavidad. El ánodo de plata está parcialmente pegado con cinta aislante para evitar cortocircuitar el ánodo plateado con la carcasa.
5. Conclusión
Se utiliza un proceso de pretratamiento combinado de zinc galvanizado y galvanizado para obtener un plateado brillante en la superficie del aluminio y sus aleaciones, que se caracteriza por cristales finos, buen brillo y una fuerte fuerza de unión.