CNC Machining Features and Programming
Main Feature
From the very beginning, CNC machine tools have selected aircraft parts with complex profiles as the processing objects, solving the key problems that are difficult to solve with common machining methods. The most important feature of NC machining is to use perforated tape (or tape) to control machine tools for automatic processing. Because the aircraft, rockets and engine parts have different characteristics: the size of the aircraft and the rocket's zero and component components are large and the profile is complex; Engine parts, components, small size, high precision, Therefore, the numerical control machine tools selected by the aircraft, the rocket manufacturing department and the engine manufacturing department are different. In the manufacturing of aircrafts and rockets, the use of continuously controlled large-scale CNC milling machines is the mainstay. In the manufacture of engines, both continuously controlled CNC machine tools and point-controlled CNC machine tools (such as CNC drilling machines, CNC boring machines, and machining centers) are used.
Process centralization
CNC machine tools generally have tool holders and tool magazines that can automatically change tools. The tool change process is controlled automatically by the program. Therefore, the processes are more centralizatio. Process centralization brings huge economic benefits:
(1) Reduce machine tool area and save plant.
(2) Reduced or no intermediate links (such as intermediate inspections of semi-finished products, temporary storage, etc.) save time and manpower.
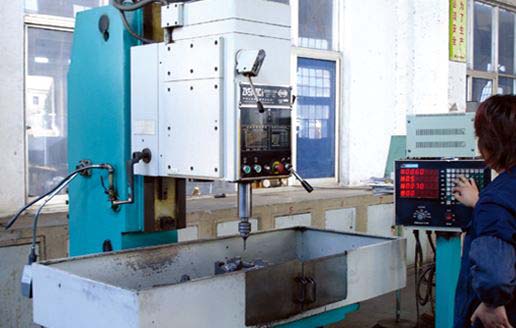
Automation
When CNC machining, No manual control of the tool, a high degree of automation. The benefits are obvious.
⑴ reduce the requirements for operation of the workers:
A senior worker of an ordinary machine tool can not be trained in a short time. A NC worker who does not need to be programmed has a very short training period (for example, a CNC lathe operator needs a week and can write a simple machining program). In addition, the parts machined on CNC machine tools are more accurate than normal workers on traditional machine tools, and the time must be saved.
(2) Reduce the labor intensity of workers:
In the process of machining, CNC workers are excluded from the process most of the time and are very labor-saving.
(3) Product quality is stable:
The automatic processing of CNC machine tools eliminates the fatigue, carelessness, estimation, and other human errors of workers on ordinary machine tools and improves product consistency.
(4) High processing efficiency:
The automatic tool change of CNC machine tools makes the machining process compact and improves labor productivity.
High flexibility
Traditional general-purpose machines, though flexible, have low efficiency;
The traditional machine tools, though highly efficient, have poor adaptability to parts, are rigid and have poor flexibility, and are difficult to adapt to frequent changes in products brought about by fierce competition under market economy. As long as the program is changed, new parts can be processed on the CNC machine tool, and they can be automated. The flexibility and efficiency are high, so the CNC machine tool can adapt to the market competition.
strong ability
The machine tool can accurately process various contours, and some contours cannot be machined on conventional machine tools. CNC machine tools are particularly suitable for the following occasions:
1. Parts that are not allowed to be scrapped.
2, new product development.
3, the urgent need for processing.
NC programming
Program structure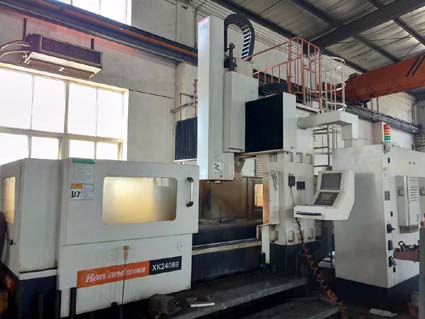
The program segment is a continuous word group that can be processed as a unit. It is actually a program in the numerical control processing program. The main part of the part program consists of several blocks. Most program segments are used to instruct the machine to complete or perform an action. The program segment is composed of size words, non size words and program end instructions. When writing and printing, each program segment generally occupies one line, as does the screen display program.
Program format
Routine machining programs consist of a start character (a single paragraph), a program name (a single paragraph), a program body, and a program end command (generally a single column). At the end of the program, there is a program terminator.
The program start and program end characters are the same character: It is % in ISO code and ER in EIA code. The program end instruction can be M02 (program end) or M30 (end tape end).
CNC machine tools generally use stored programs to run. The common points between M02 and M30 are: After finishing all other instructions in the program segment, it is used to stop the spindle, coolant and feed, and reset the control system.
M02 and M30 are completely equivalent when used on some machine tools (systems), but they are used on other machine tools (systems) as follows: When using M02 to end the program, the cursor will stop at the end of the program after the automatic operation ends. When M3O is used to end the program execution, the cursor and screen display can automatically return to the beginning of the program after the automatic operation ends. Once the start button is pressed, the program can be run again. Although M02 and M30 allow a single program segment to be used in combination with other program words, it is best to list them individually or to share only one program segment with the sequence number.
The program name is located in front of the program body and after the program start character. it is generally a separate line.
There are two types of program names: One is the start of a specified English word (Multiple O) followed by several digits.The maximum allowable number of digits is specified by the specification. Commonly two digits and four digits are used.This form may also be referred to as a program name of the program number.
In another form, the program name consists of a mixture of English words, numbers or English, and numbers. You can also add "-" signs in the middle. This form makes the user naming program more flexible. For example, a flange with part number 215 is machined on the LC30 CNC lathe, and the third process procedure can be named LC30-FIANGE-215-3. This brings great convenience to use, storage and retrieval. Which form the program name uses is determined by the CNC system.
The rules for the arrangement of words, characters, and data in a program segment are called segment formats. CNC has historically used a fixed sequence format and delimiter (HT or TAB) segment format. The format of these two program segments has passed. Both domestic and foreign languages widely use the word address variable segment format, also known as the word address format. In this format, the program word length is not fixed, and the number of program words is also variable. The vast majority of numerical control systems allow the order of program words to be arbitrarily arranged, so it is a program segment format. However, in most cases, program words are used in a certain order in a program segment for the convenience of writing, inputting, checking, and proofreading.
The details of the programming are categorized in the detailed format in the programming manual of the CNC machine tool:
The characters used in the programming, the order of the program words in the program segment, and the word length. E.g:
/ NO3 G02 X+053 Y+053 I0 J+053 F031 S04 T04 M03 LF
The detailed format of the above example is described as follows:
N03 is the block number;
G02 indicates that the machining trajectory is clockwise arc;
X+053, Y+053 indicate the coordinates of the end point of the processed arc;
I0, J+053 indicate the center coordinates of the processed arc;
F031 is the processing feed speed;
S04 is the spindle speed;
T04 is the tool number of the tool used;
M03 is an auxiliary function instruction;
LF block end instruction;
/ Select instructions for skipping.
The role of jump selection instructions is: Under the premise that the program is not changed, the operator can make a choice of execution or non-execution of the program segment in the program with a skip selection instruction. The selected method is usually implemented by skipping the selector switch on the operation panel to ON or OFF, so as to implement a program segment that does not execute or execute a "/".
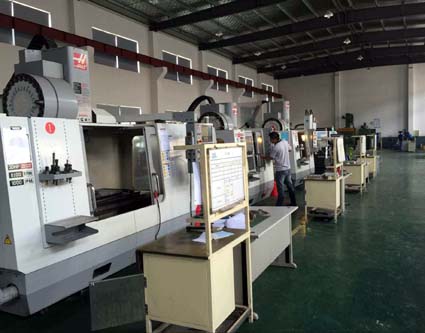
Execute Program
The preparation of processing programs sometimes encounters this situation:
A set of code segments appear multiple times in a program, or you use it in several programs. We can extract this group of programs and store them separately after naming. This group of code segments is a subroutine. A subroutine is a segment of a machining program that can be called by an appropriate machine control command and is generally of independent significance in machining. The machining program in which the instructions of the first level subroutine is called is the main program. The instruction to call a subroutine is also a code segment. It is generally composed of subroutine call instructions, subroutine names, and the number of calls. The specific rules and formats vary from system to system. For example, the same is "call subroutine 55 once," and the FANUC system uses "M98 P55." The United States A-B company system uses "P55x".
The subroutine can be nested, that is, a layer of one layer. The relationship between the upper layer and the lower layer is the same as the relationship between the main program and the first-level subroutine. The maximum number of layers that can be set is determined by the specific CNC system. The form and composition of subroutines are roughly the same as those of the main program: The first line is the subroutine number (name), and the last line is the "subroutine end" command. Between them is the subroutine body. However, the main program end command function is to end the main program, let the CNC system reset, its instructions have been standardized, each system uses M02 or M30; The end of the subroutine command is to end the subroutine, return to the main program or a subroutine, the command system is not uniform, For example, M99 for the FANUC system, M17 for the Siemens system, and M02 for the system of the American A-B company.
User macros (programs) can be used in NC machining programs.
The so-called macro program is a subroutine containing variables. The instructions for calling a macro program in a program are called user macros. The system can use the custom macro function is called the user macro function.To execute the user macro function, simply write a user macro command.
The biggest feature of user macros is:
● Variables can be used in user macros;
● can use calculus, steering statements and a variety of functions
● You can assign values to variables using custom macro commands.
From the very beginning, CNC machine tools have selected aircraft parts with complex profiles as the processing objects, solving the key problems that are difficult to solve with common machining methods. The most important feature of NC machining is to use perforated tape (or tape) to control machine tools for automatic processing. Because the aircraft, rockets and engine parts have different characteristics: the size of the aircraft and the rocket's zero and component components are large and the profile is complex; Engine parts, components, small size, high precision, Therefore, the numerical control machine tools selected by the aircraft, the rocket manufacturing department and the engine manufacturing department are different. In the manufacturing of aircrafts and rockets, the use of continuously controlled large-scale CNC milling machines is the mainstay. In the manufacture of engines, both continuously controlled CNC machine tools and point-controlled CNC machine tools (such as CNC drilling machines, CNC boring machines, and machining centers) are used.
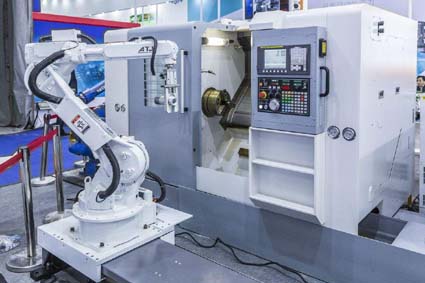
Process centralization
CNC machine tools generally have tool holders and tool magazines that can automatically change tools. The tool change process is controlled automatically by the program. Therefore, the processes are more centralizatio. Process centralization brings huge economic benefits:
(1) Reduce machine tool area and save plant.
(2) Reduced or no intermediate links (such as intermediate inspections of semi-finished products, temporary storage, etc.) save time and manpower.
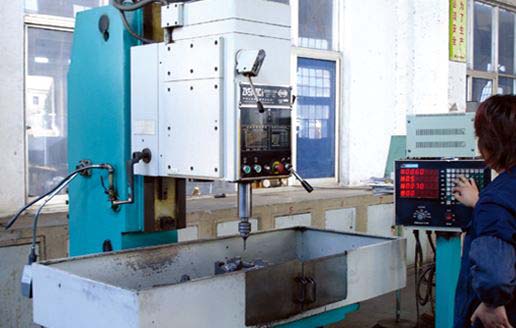
Automation
When CNC machining, No manual control of the tool, a high degree of automation. The benefits are obvious.
⑴ reduce the requirements for operation of the workers:
A senior worker of an ordinary machine tool can not be trained in a short time. A NC worker who does not need to be programmed has a very short training period (for example, a CNC lathe operator needs a week and can write a simple machining program). In addition, the parts machined on CNC machine tools are more accurate than normal workers on traditional machine tools, and the time must be saved.
(2) Reduce the labor intensity of workers:
In the process of machining, CNC workers are excluded from the process most of the time and are very labor-saving.
(3) Product quality is stable:
The automatic processing of CNC machine tools eliminates the fatigue, carelessness, estimation, and other human errors of workers on ordinary machine tools and improves product consistency.
(4) High processing efficiency:
The automatic tool change of CNC machine tools makes the machining process compact and improves labor productivity.
High flexibility
Traditional general-purpose machines, though flexible, have low efficiency;
The traditional machine tools, though highly efficient, have poor adaptability to parts, are rigid and have poor flexibility, and are difficult to adapt to frequent changes in products brought about by fierce competition under market economy. As long as the program is changed, new parts can be processed on the CNC machine tool, and they can be automated. The flexibility and efficiency are high, so the CNC machine tool can adapt to the market competition.
strong ability
The machine tool can accurately process various contours, and some contours cannot be machined on conventional machine tools. CNC machine tools are particularly suitable for the following occasions:
1. Parts that are not allowed to be scrapped.
2, new product development.
3, the urgent need for processing.
NC programming
Program structure
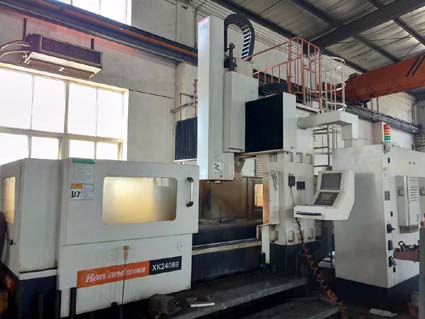
The program segment is a continuous word group that can be processed as a unit. It is actually a program in the numerical control processing program. The main part of the part program consists of several blocks. Most program segments are used to instruct the machine to complete or perform an action. The program segment is composed of size words, non size words and program end instructions. When writing and printing, each program segment generally occupies one line, as does the screen display program.
Program format
Routine machining programs consist of a start character (a single paragraph), a program name (a single paragraph), a program body, and a program end command (generally a single column). At the end of the program, there is a program terminator.
The program start and program end characters are the same character: It is % in ISO code and ER in EIA code. The program end instruction can be M02 (program end) or M30 (end tape end).
CNC machine tools generally use stored programs to run. The common points between M02 and M30 are: After finishing all other instructions in the program segment, it is used to stop the spindle, coolant and feed, and reset the control system.
M02 and M30 are completely equivalent when used on some machine tools (systems), but they are used on other machine tools (systems) as follows: When using M02 to end the program, the cursor will stop at the end of the program after the automatic operation ends. When M3O is used to end the program execution, the cursor and screen display can automatically return to the beginning of the program after the automatic operation ends. Once the start button is pressed, the program can be run again. Although M02 and M30 allow a single program segment to be used in combination with other program words, it is best to list them individually or to share only one program segment with the sequence number.
The program name is located in front of the program body and after the program start character. it is generally a separate line.
There are two types of program names: One is the start of a specified English word (Multiple O) followed by several digits.The maximum allowable number of digits is specified by the specification. Commonly two digits and four digits are used.This form may also be referred to as a program name of the program number.
In another form, the program name consists of a mixture of English words, numbers or English, and numbers. You can also add "-" signs in the middle. This form makes the user naming program more flexible. For example, a flange with part number 215 is machined on the LC30 CNC lathe, and the third process procedure can be named LC30-FIANGE-215-3. This brings great convenience to use, storage and retrieval. Which form the program name uses is determined by the CNC system.
%
O1001
N0 G92 X0 Y0 Z0
N5 G91 G00 X50 Y35 S500 MO3
N10 G43 Z-25 T01.01
N15 G01 G007 Z-12
N20 G00 Z12
N25 X40
N30 G01 Z-17
N35 G00 G44 Z42 M05
N40 G90 X0 Y0
N45 M30
%
Segment formatO1001
N0 G92 X0 Y0 Z0
N5 G91 G00 X50 Y35 S500 MO3
N10 G43 Z-25 T01.01
N15 G01 G007 Z-12
N20 G00 Z12
N25 X40
N30 G01 Z-17
N35 G00 G44 Z42 M05
N40 G90 X0 Y0
N45 M30
%
The rules for the arrangement of words, characters, and data in a program segment are called segment formats. CNC has historically used a fixed sequence format and delimiter (HT or TAB) segment format. The format of these two program segments has passed. Both domestic and foreign languages widely use the word address variable segment format, also known as the word address format. In this format, the program word length is not fixed, and the number of program words is also variable. The vast majority of numerical control systems allow the order of program words to be arbitrarily arranged, so it is a program segment format. However, in most cases, program words are used in a certain order in a program segment for the convenience of writing, inputting, checking, and proofreading.
The details of the programming are categorized in the detailed format in the programming manual of the CNC machine tool:
The characters used in the programming, the order of the program words in the program segment, and the word length. E.g:
/ NO3 G02 X+053 Y+053 I0 J+053 F031 S04 T04 M03 LF
The detailed format of the above example is described as follows:
N03 is the block number;
G02 indicates that the machining trajectory is clockwise arc;
X+053, Y+053 indicate the coordinates of the end point of the processed arc;
I0, J+053 indicate the center coordinates of the processed arc;
F031 is the processing feed speed;
S04 is the spindle speed;
T04 is the tool number of the tool used;
M03 is an auxiliary function instruction;
LF block end instruction;
/ Select instructions for skipping.
The role of jump selection instructions is: Under the premise that the program is not changed, the operator can make a choice of execution or non-execution of the program segment in the program with a skip selection instruction. The selected method is usually implemented by skipping the selector switch on the operation panel to ON or OFF, so as to implement a program segment that does not execute or execute a "/".
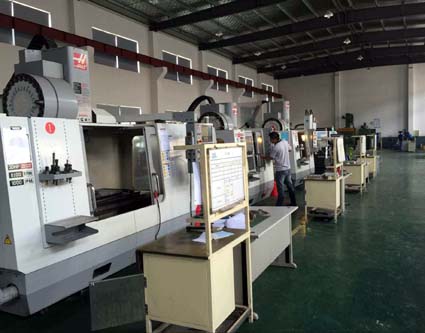
Execute Program
The preparation of processing programs sometimes encounters this situation:
A set of code segments appear multiple times in a program, or you use it in several programs. We can extract this group of programs and store them separately after naming. This group of code segments is a subroutine. A subroutine is a segment of a machining program that can be called by an appropriate machine control command and is generally of independent significance in machining. The machining program in which the instructions of the first level subroutine is called is the main program. The instruction to call a subroutine is also a code segment. It is generally composed of subroutine call instructions, subroutine names, and the number of calls. The specific rules and formats vary from system to system. For example, the same is "call subroutine 55 once," and the FANUC system uses "M98 P55." The United States A-B company system uses "P55x".
The subroutine can be nested, that is, a layer of one layer. The relationship between the upper layer and the lower layer is the same as the relationship between the main program and the first-level subroutine. The maximum number of layers that can be set is determined by the specific CNC system. The form and composition of subroutines are roughly the same as those of the main program: The first line is the subroutine number (name), and the last line is the "subroutine end" command. Between them is the subroutine body. However, the main program end command function is to end the main program, let the CNC system reset, its instructions have been standardized, each system uses M02 or M30; The end of the subroutine command is to end the subroutine, return to the main program or a subroutine, the command system is not uniform, For example, M99 for the FANUC system, M17 for the Siemens system, and M02 for the system of the American A-B company.
User macros (programs) can be used in NC machining programs.
The so-called macro program is a subroutine containing variables. The instructions for calling a macro program in a program are called user macros. The system can use the custom macro function is called the user macro function.To execute the user macro function, simply write a user macro command.
The biggest feature of user macros is:
● Variables can be used in user macros;
● can use calculus, steering statements and a variety of functions
● You can assign values to variables using custom macro commands.