What is CNC machining?
Numerical control machining refers to a processing method for machining parts on a numerically controlled machine tool. The process specifications of numerically-controlled machine tools and conventional machine tools are generally the same, but significant changes have also taken place. A digital machining method for controlling the displacement of parts and tools. It is an effective way to solve the variety of parts, small batches, complex shapes, high precision and high efficiency and automated processing. 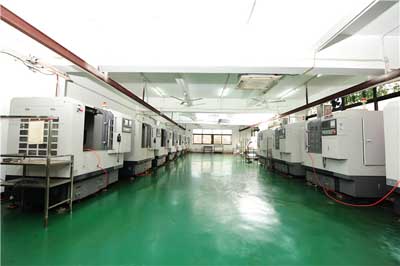
Basic interpretation
CNC machining means that the control system issues commands to make the tool perform various movements that meet the requirements. To represent the shape and dimensions of workpieces in numerical and alphabetical form, and to require the processing required by the machining process. It refers to the process of machining parts on a CNC machine.
CNC machine is a computer controlled machine tool, the computer used to control the machine tool, whether it is a dedicated computer or a general-purpose computer, is collectively referred to as a numerical control system. CNC machine tool movements and actions are controlled by the auxiliary command issued by the NC system. The instructions of the CNC system are compiled by the programmer according to the material of the workpiece, the processing requirements, the characteristics of the machine tool, and the instruction format (CNC language or symbols) specified by the system. The numerical control system sends the operation or the termination information to the servo device and other function parts according to a program instruction to control various movements of the machine tool. When the part's machining program ends, the machine will automatically stop. For any kind of CNC machine tool, if there is no input program instruction in the CNC system, the CNC machine tool cannot work. The controlled motion of the machine tool generally includes starting and stopping of the machine tool;
Spindle start/stop, rotation direction and speed change;
The direction, speed, and mode of the feed movement;
Tool selection, length and radius compensation;
Tool replacement, coolant opening, closing, etc.
Development Background
CNC technology originated from the needs of the aviation industry. In the late 1940s, a helicopter company in the United States proposed it.
The original idea of CNC machine tools, in 1952 the United States MIT developed a three-axis CNC milling machine. In the mid-1950s, this type of CNC milling machine was used to process aircraft parts. In the 1960s, the numerical control system and programming work became increasingly mature and perfect. CNC machine tools have been used in various industrial sectors, but the aerospace industry has always been the largest user of CNC machine tools. Some large aviation factories are equipped with hundreds of CNC machine tools, among which are cutting machines. The CNC machined parts include the aircraft, the rocket's bulkheads, girders, skins, bulkheads, and propellers, as well as the aero-engine casings, shafts, discs, vane mold cavities, and special chambers for liquid rocket engine combustors. Etc. The initial stage of the development of numerically-controlled machine tools was based on continuous-track CNC machine tools and continuous trajectory control.
Continuous trajectory control, also known as contour control, requires the tool to move in a defined trajectory relative to the part. Afterwards, it also vigorously developed point-controlled CNC machine tools. Point control means that the tool moves from one point to another as long as it can reach the target accurately regardless of the route of movement.
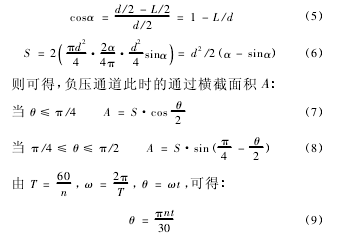
Operation process
NC programming
CNC programming methods are manual programming and automatic programming. Manual programming, the entire contents of the program is written manually by the instruction format specified by the CNC system. Automatic programming is computer programming and can be divided into automatic programming methods based on language and drawing. However, no matter what kind of automatic programming method is adopted, corresponding supporting hardware and software are required. It can be seen that the realization of numerical control machining programming is the key. But programming is not enough, and CNC machining also includes a series of preparations that must be done before programming and the aftermath processing after programming. In general, the NC machining process includes the following contents:
(1) Select and determine the parts and contents for CNC machining;
(2) Process analysis of the numerical control of part drawings;
(3) CNC process design;
(4) Mathematical processing of part drawings;
(5) Preparation of processing procedures;
⑹ programmed to produce a single control medium;
(7) verification and modification of the program;
(8) Sample testing and on-site problem handling;
⑼ stereotypes and archiving digital processing technology file.
In order to improve the degree of automation of production, shorten the programming time and reduce the cost of numerical control processing, a series of advanced numerical control processing technologies have also been developed and used in the aerospace industry. Such as computer numerical control, that is, using a small or micro-computer to replace the controller in the CNC system, and use the software stored in the computer to perform the calculation and control functions, This soft-linked computer numerical control system is gradually replacing the initial state of the numerical control system. The direct numerical control is to use a computer to directly control multiple CNC machine tools, which is suitable for short-period production of small batches of aircraft. The ideal control system is an adaptive control system that can continuously change the processing parameters. Although the system itself is complex and expensive, it can improve the processing efficiency and quality. The development of CNC In addition to the improvement of hardware and CNC systems and machine tools, there is another important aspect is the development of software. Computer-aided programming (also called automatic programming) is a program written by a programmer in a CNC language. It is entered into a computer for translation, and finally a punched tape or tape is automatically output by the computer. The widely used NC language is the APT language. It is roughly divided into main and post-processing programs. The former translates the program written by the programmer and calculates the tool path; The latter edits the tool path into a part machining program for a CNC machine tool. CNC machining is the preparation of a program on a computer in advance before machining the workpiece, and then inputting these programs to a machine tool controlled by a computer program for instructional processing. Or directly on the computer program control machine control panel to write instructions for processing. The process of processing includes: moving knife, changing knife, changing speed, change of direction, parking, etc., all are done automatically. CNC machining is an advanced means of modern mold manufacturing and processing. Of course, the numerical control processing method must also be used not only for the processing of mold parts, but also has a wide range of applications.
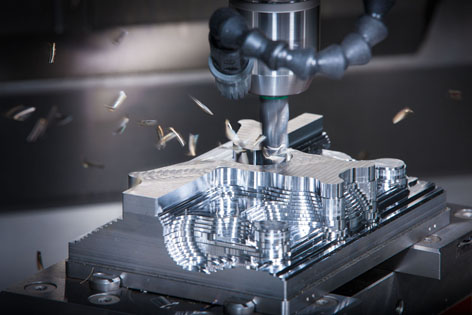
Process analysis
Machined parts CNC machining process involves a wide range of issues, In the following, in conjunction with the possibility and convenience of programming, the main contents that must be analyzed and reviewed are proposed.
1, the dimension should be consistent with the characteristics of CNC machining
In numerical control programming, the size and position of all points, lines, and faces are based on the programming origin. Therefore, it is best to give the coordinate size directly
2. The conditions of geometric elements should be complete and accurate
In programming, the programmer must fully grasp the parameters of the geometric elements that make up the contour of the part and the relationships between the geometric elements. Because all the geometric elements of the part contour are defined during automatic programming, the coordinates of each node are calculated during manual programming. No matter which point is not clear or uncertain, programming cannot be performed. However, due to poor design considerations or neglected by the part designer, the parameters are often incomplete or unclear. Such as: arc and straight, arc and arc are tangent or intersect or apart. So in the review and analysis of drawings, we must be careful, identify problems and timely contact with the designer.
3, reliable positioning
In the numerical control processing, the processing operations are often concentrated, and it is very important to locate the same reference. Therefore, it is often necessary to set up some auxiliary benchmarks. Or add some craft bump on the blank.
4. Uniform geometry type or size
The shape and inner cavity of the part are preferably of a uniform geometry or size, which can reduce the number of tool changes. It is also possible to apply control programs or special programs to shorten the program length. The shape of the part is as symmetrical as possible, and it is easy to program using the mirror processing function of the CNC machine tool to save programming time.
Clamping parts
the basic principles of positioning and installation
When machining parts on CNC machine tools, the basic principle of positioning and installation is to reasonably select the positioning reference and clamping program. The following points should be noted when selecting:
1, seeks to unify the reference design, technology and programming calculations.
2. Try to reduce the clamping times, as far as possible after a positioning clamping, processing all the surface to be processed.
3, Avoid occupying machine manual adjustment processing plan, in order to give full play to the effectiveness of CNC machine tools.
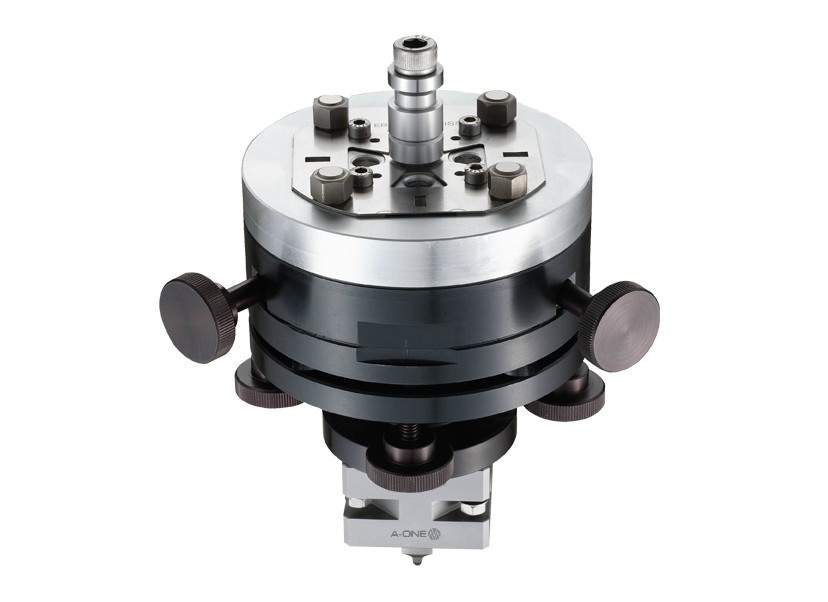
Basic principles of selecting fixture
The characteristics of CNC machining put forward two basic requirements for fixtures:
The first is to ensure that the coordinate direction of the fixture and the coordinate direction of the machine tool are relatively fixed;
The second is to coordinate the dimensional relationship between the parts and the machine coordinate system. In addition, consider the following points:
1, when the parts processing volume is not large, it should try to use combination fixtures, adjustable fixtures and other universal fixtures, in order to shorten the preparation time and save production costs.
2. Consider the use of special fixtures in batch production and strive for a simple structure.
3, the loading and unloading of parts should be fast, convenient and reliable to shorten the pause time of the machine tool.
4. The components on the fixture should not interfere with the machining of the parts on the surface of the part. That is, the fixture should be open, and its positioning and clamping mechanism components can not affect the cutting tool in the process (such as collisions, etc.).
Processing error
CNC machining error △ number is caused by programming error △, machine error △ machine, positioning error △ set, knife error △ knife and other errors formed.
That is: △ number plus = f (△Programming + △ machine + △ set + △ knife)
among them:
1, programming error △ by approximation error δ, Rounding error composition.
The approximation error δ is generated during the process of approximating a non-circular curve with a straight segment or an arc segment, as shown in Figure 1.43. The rounding error is an error generated by rounding off the coordinate values to integer pulse equivalent values during data processing. Pulse equivalent refers to the displacement of the corresponding axis for each unit pulse. Ordinary precision CNC machine tools, the general pulse equivalent value is 0.01mm; The pulse equivalent value of the more precise numerical control machine tool is 0.005mm or 0.001mm.
2. The machine tool error △ is caused by the error of the CNC system and the error of the feed system.
3, positioning error △ When the workpiece is positioned on the fixture, when the clamp is positioned on the machine, it is generated.
4. The tool setting error △ is generated when the relative position between the tool and the workpiece is determined.
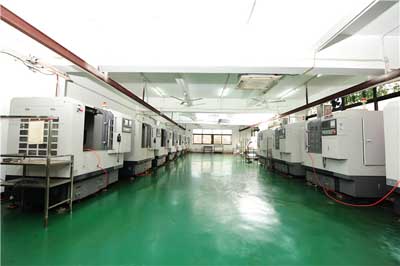
Basic interpretation
CNC machining means that the control system issues commands to make the tool perform various movements that meet the requirements. To represent the shape and dimensions of workpieces in numerical and alphabetical form, and to require the processing required by the machining process. It refers to the process of machining parts on a CNC machine.
CNC machine is a computer controlled machine tool, the computer used to control the machine tool, whether it is a dedicated computer or a general-purpose computer, is collectively referred to as a numerical control system. CNC machine tool movements and actions are controlled by the auxiliary command issued by the NC system. The instructions of the CNC system are compiled by the programmer according to the material of the workpiece, the processing requirements, the characteristics of the machine tool, and the instruction format (CNC language or symbols) specified by the system. The numerical control system sends the operation or the termination information to the servo device and other function parts according to a program instruction to control various movements of the machine tool. When the part's machining program ends, the machine will automatically stop. For any kind of CNC machine tool, if there is no input program instruction in the CNC system, the CNC machine tool cannot work. The controlled motion of the machine tool generally includes starting and stopping of the machine tool;
Spindle start/stop, rotation direction and speed change;
The direction, speed, and mode of the feed movement;
Tool selection, length and radius compensation;
Tool replacement, coolant opening, closing, etc.
Development Background
CNC technology originated from the needs of the aviation industry. In the late 1940s, a helicopter company in the United States proposed it.
The original idea of CNC machine tools, in 1952 the United States MIT developed a three-axis CNC milling machine. In the mid-1950s, this type of CNC milling machine was used to process aircraft parts. In the 1960s, the numerical control system and programming work became increasingly mature and perfect. CNC machine tools have been used in various industrial sectors, but the aerospace industry has always been the largest user of CNC machine tools. Some large aviation factories are equipped with hundreds of CNC machine tools, among which are cutting machines. The CNC machined parts include the aircraft, the rocket's bulkheads, girders, skins, bulkheads, and propellers, as well as the aero-engine casings, shafts, discs, vane mold cavities, and special chambers for liquid rocket engine combustors. Etc. The initial stage of the development of numerically-controlled machine tools was based on continuous-track CNC machine tools and continuous trajectory control.
Continuous trajectory control, also known as contour control, requires the tool to move in a defined trajectory relative to the part. Afterwards, it also vigorously developed point-controlled CNC machine tools. Point control means that the tool moves from one point to another as long as it can reach the target accurately regardless of the route of movement.
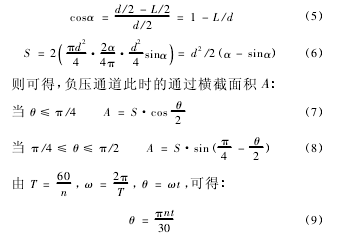
Operation process
NC programming
CNC programming methods are manual programming and automatic programming. Manual programming, the entire contents of the program is written manually by the instruction format specified by the CNC system. Automatic programming is computer programming and can be divided into automatic programming methods based on language and drawing. However, no matter what kind of automatic programming method is adopted, corresponding supporting hardware and software are required. It can be seen that the realization of numerical control machining programming is the key. But programming is not enough, and CNC machining also includes a series of preparations that must be done before programming and the aftermath processing after programming. In general, the NC machining process includes the following contents:
(1) Select and determine the parts and contents for CNC machining;
(2) Process analysis of the numerical control of part drawings;
(3) CNC process design;
(4) Mathematical processing of part drawings;
(5) Preparation of processing procedures;
⑹ programmed to produce a single control medium;
(7) verification and modification of the program;
(8) Sample testing and on-site problem handling;
⑼ stereotypes and archiving digital processing technology file.
In order to improve the degree of automation of production, shorten the programming time and reduce the cost of numerical control processing, a series of advanced numerical control processing technologies have also been developed and used in the aerospace industry. Such as computer numerical control, that is, using a small or micro-computer to replace the controller in the CNC system, and use the software stored in the computer to perform the calculation and control functions, This soft-linked computer numerical control system is gradually replacing the initial state of the numerical control system. The direct numerical control is to use a computer to directly control multiple CNC machine tools, which is suitable for short-period production of small batches of aircraft. The ideal control system is an adaptive control system that can continuously change the processing parameters. Although the system itself is complex and expensive, it can improve the processing efficiency and quality. The development of CNC In addition to the improvement of hardware and CNC systems and machine tools, there is another important aspect is the development of software. Computer-aided programming (also called automatic programming) is a program written by a programmer in a CNC language. It is entered into a computer for translation, and finally a punched tape or tape is automatically output by the computer. The widely used NC language is the APT language. It is roughly divided into main and post-processing programs. The former translates the program written by the programmer and calculates the tool path; The latter edits the tool path into a part machining program for a CNC machine tool. CNC machining is the preparation of a program on a computer in advance before machining the workpiece, and then inputting these programs to a machine tool controlled by a computer program for instructional processing. Or directly on the computer program control machine control panel to write instructions for processing. The process of processing includes: moving knife, changing knife, changing speed, change of direction, parking, etc., all are done automatically. CNC machining is an advanced means of modern mold manufacturing and processing. Of course, the numerical control processing method must also be used not only for the processing of mold parts, but also has a wide range of applications.
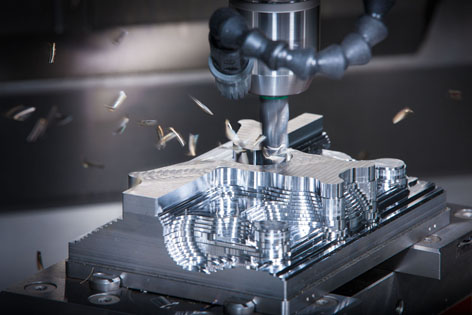
Process analysis
Machined parts CNC machining process involves a wide range of issues, In the following, in conjunction with the possibility and convenience of programming, the main contents that must be analyzed and reviewed are proposed.
1, the dimension should be consistent with the characteristics of CNC machining
In numerical control programming, the size and position of all points, lines, and faces are based on the programming origin. Therefore, it is best to give the coordinate size directly
2. The conditions of geometric elements should be complete and accurate
In programming, the programmer must fully grasp the parameters of the geometric elements that make up the contour of the part and the relationships between the geometric elements. Because all the geometric elements of the part contour are defined during automatic programming, the coordinates of each node are calculated during manual programming. No matter which point is not clear or uncertain, programming cannot be performed. However, due to poor design considerations or neglected by the part designer, the parameters are often incomplete or unclear. Such as: arc and straight, arc and arc are tangent or intersect or apart. So in the review and analysis of drawings, we must be careful, identify problems and timely contact with the designer.
3, reliable positioning
In the numerical control processing, the processing operations are often concentrated, and it is very important to locate the same reference. Therefore, it is often necessary to set up some auxiliary benchmarks. Or add some craft bump on the blank.
4. Uniform geometry type or size
The shape and inner cavity of the part are preferably of a uniform geometry or size, which can reduce the number of tool changes. It is also possible to apply control programs or special programs to shorten the program length. The shape of the part is as symmetrical as possible, and it is easy to program using the mirror processing function of the CNC machine tool to save programming time.
Clamping parts
the basic principles of positioning and installation
When machining parts on CNC machine tools, the basic principle of positioning and installation is to reasonably select the positioning reference and clamping program. The following points should be noted when selecting:
1, seeks to unify the reference design, technology and programming calculations.
2. Try to reduce the clamping times, as far as possible after a positioning clamping, processing all the surface to be processed.
3, Avoid occupying machine manual adjustment processing plan, in order to give full play to the effectiveness of CNC machine tools.
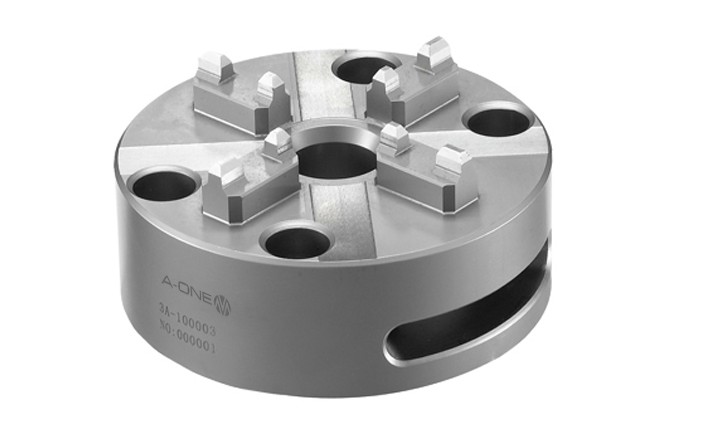
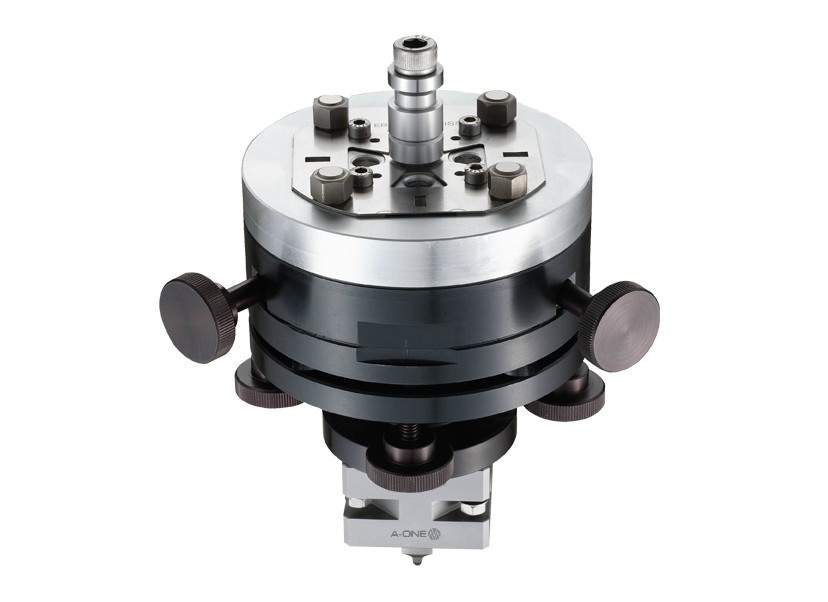
Basic principles of selecting fixture
The characteristics of CNC machining put forward two basic requirements for fixtures:
The first is to ensure that the coordinate direction of the fixture and the coordinate direction of the machine tool are relatively fixed;
The second is to coordinate the dimensional relationship between the parts and the machine coordinate system. In addition, consider the following points:
1, when the parts processing volume is not large, it should try to use combination fixtures, adjustable fixtures and other universal fixtures, in order to shorten the preparation time and save production costs.
2. Consider the use of special fixtures in batch production and strive for a simple structure.
3, the loading and unloading of parts should be fast, convenient and reliable to shorten the pause time of the machine tool.
4. The components on the fixture should not interfere with the machining of the parts on the surface of the part. That is, the fixture should be open, and its positioning and clamping mechanism components can not affect the cutting tool in the process (such as collisions, etc.).
Processing error
CNC machining error △ number is caused by programming error △, machine error △ machine, positioning error △ set, knife error △ knife and other errors formed.
That is: △ number plus = f (△Programming + △ machine + △ set + △ knife)
among them:
1, programming error △ by approximation error δ, Rounding error composition.
The approximation error δ is generated during the process of approximating a non-circular curve with a straight segment or an arc segment, as shown in Figure 1.43. The rounding error is an error generated by rounding off the coordinate values to integer pulse equivalent values during data processing. Pulse equivalent refers to the displacement of the corresponding axis for each unit pulse. Ordinary precision CNC machine tools, the general pulse equivalent value is 0.01mm; The pulse equivalent value of the more precise numerical control machine tool is 0.005mm or 0.001mm.
2. The machine tool error △ is caused by the error of the CNC system and the error of the feed system.
3, positioning error △ When the workpiece is positioned on the fixture, when the clamp is positioned on the machine, it is generated.
4. The tool setting error △ is generated when the relative position between the tool and the workpiece is determined.