Frasen von bearbeiteten Stahlteilen mit zweischneidigen Frasern
Mit der kontinuierlichen Entwicklung von Wissenschaft und Technik, um die speziellen Anforderungen der Leistung von Maschinenteilen, einige neuen Materialien mit hohen Festigkeit, hohen Zähigkeit und hohen Verschleißfestigkeit entstehen gerecht zu werden. Das Schneiden dieser neuen Materialien hat jedoch auch neue Probleme für die Erforschung von Metallschneidwerkzeugen aufgeworfen. Ihre herausragenden Eigenschaften bei der Bearbeitung sind: Hohe Festigkeit, starke Kaltverfestigung, schlechte Oberflächenqualität, hohe Schnitttemperatur, hohe Schnitttemperatur, schneller Werkzeugverschleiß und Schwierigkeiten beim Spanbruch. Beispielsweise wird in dem Material mit hohem Mangangehalt die Austenitstruktur nach der plastischen Verformung zu einer feinkörnigen Martensitstruktur, und die Verarbeitungshärte wird von 180-220 HBS auf 450-500 HBS erhöht, und die Kaltverfestigung ist stark; Die Tiefe der Kühlschicht kann mehr als 0,3 mm betragen. Darüber hinaus ist die Wärmeleitfähigkeit von Gao Meng Stahl 0,25-fache von Stahl No. 45, und die Zähigkeit ist 8-fache von 45 Stahl Nr. Es wird nicht nur die Schneidkraft erhöht, sondern auch die Späne werden nicht leicht zerbrochen. Aus produktionstechnischer und verarbeitungstechnischer Sicht beim Einsatz von Wendeplattenfräsern. Aufgrund der unvernünftigen Auswahl der geometrischen Parameter des Fräsers und die Steuerung von Chip ist Entfernung und Spanbruch nicht gut, es führt oft zu häufig in leistungsfähigen Fräsen Messer-Brech. Zusätzlich wird, wenn die Tiefe des Messers groß ist, ist die axiale Positionierung unzuverlässig, die die Förderung und Anwendung des Wende Fräsers in schwierigen Materialien auswirkt.
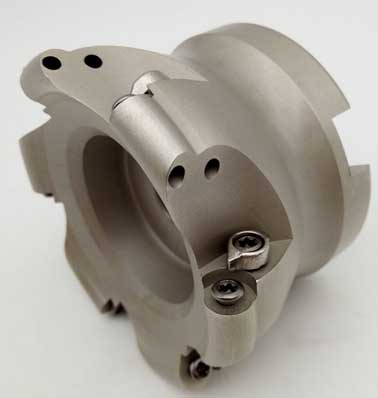
1. Winkel Auswahl
Analyse des Kontaktzustands beim Fräsen Die Wahl des Fräswinkels steht in direktem Zusammenhang mit dem Kontaktzustand beim Fräsen. Ein guter Fräskontaktzustand ist eines der Hauptprobleme bei der Auswahl des kraftvollen Fräserwinkels. Wie in Fig. 1 gezeigt, kann der Kontaktpunkt zwischen der Spanfläche und dem zu schneidenden Werkstück als vier spezielle Punkte (U, V, S, T) angenommen werden, wenn der Fräser in das Werkstück schneidet. Um zu verhindern, dass der Span abplatzt, sollte laut Analyse der Anfangspunkt des Kontakts an dem Punkt oder Punkt gewählt werden, der von der Hauptschneide entfernt ist, und zwar am besten.
Auswahl des Schnitttiefenwinkels gp und des Vorschubwinkels gf nach obiger Analyse. Damit der anfängliche Kontaktpunkt beim Schneiden des Fräsers in das Werkstück U-Punkt oder V-Punkt ist, ist die Auswahl des vorderen Winkels des Fräsers entscheidend. Wenn der Vorschubrechenwinkel gf kleiner als der Schneidewinkel d1 ist, ist der Aufprallvorgang beim Schneiden des Schneidwerkzeugs umso langsamer, je länger die Schneidzeit ist. Dadurch wird die Beschädigung des Fräsers verringert, die durch die thermische Rissbildung des Hartmetallfräsers verursacht wird. Der negative Schnitttiefenschlagwinkel gp kann die Schlagfestigkeit des Fräsers verbessern. Der negative Spanwinkel gf kann nicht nur die Schneidkantenfestigkeit verbessern, sondern auch das Aufrollen, Brechen und Beseitigen von Spänen erleichtern. Aus diesem Grund haben wir durch Analyse und experimentellen Vergleich den negativen Spanwinkel des Fräsers gewählt, dh gp = -5 °, gf = -8 °.
Auswahl der Werkzeugspitzenparameter Da sowohl die Schnittiefe als auch der Vorschubwinkel negativ sind, ist die Schneidverformung während des Fräsens groß, die Schneidkraft ist groß und die Frästemperatur ist erhöht. Starkes Schneiden erfordert zwar eine große Schnitt- und Vorschubtiefe, aber die Bildung breiter und dicker Späne kann die Temperatur der Schneidzone verringern. Es ist jedoch auch wichtig, einen vernünftigen Winkel zu wählen. Entsprechend den Verarbeitungsanforderungen des starken Schneidens, unter Berücksichtigung der Systemsteifigkeit und der Verbesserung der Wärmeableitungsbedingungen. Wählen Sie die Hauptdeklination kr = 75 °. Um die Stärke des Spitzenabschnitts zu erhöhen, wird bei dieser Konstruktion eine doppelte sekundäre Schaufelstruktur verwendet (Abb. 2), dh es werden zwei Teilschaufeln mit kr1 '= 5 ° (Schaufel) geschliffen Länge 2 mm) und kr2 '= 15 °. Zusätzlich wird an der Werkzeugspitze ein Bogen mit einem Spitzenradius re = 1,5 ± 0,1 mm geschliffen. Diese Art der Werkzeugspitze verbessert nicht nur die Werkzeugfestigkeit, sondern verringert auch die Reibung des Gegenmessers gegenüber der bearbeiteten Oberfläche, verringert die Schneidkraft, verringert die Schneidetemperatur und verbessert die Werkzeughaltbarkeit.
2. Strukturanalyse
Blattpositionierungsmethode: Die Positionierung der Klinge auf dem Messerkissen erfüllt nicht nur die Anforderungen an die Genauigkeit und Zuverlässigkeit der neuen Klingenpositionierung, sondern gewährleistet auch die Genauigkeit und Zuverlässigkeit der Positionierung, nachdem die Klinge indexiert wurde. Dies ist ein wichtiges Prinzip für die Auswahl der Positionierungsmethode des Messers und der Konstruktionsanforderungen für die Positionierungskomponenten. Dieses Design übernimmt die "Drei-Punkt-Positionierung" -Methode. In Anbetracht der Tatsache, dass das kraftvolle Fräsen eine größere Schneidkraft als das allgemeine Fräsen aufweist, verliert der Positionierungspunkt auf dem Messerkissen die Positionierungsfähigkeit aufgrund einer starken Extrusionsverformung, was die Positionierungsgenauigkeit und die Positionierungszuverlässigkeit beeinträchtigt. Daher wird eine schmale und lange Gesichtspositionierungsstruktur auf beiden Seiten der Klinge angewendet. Um die Zuverlässigkeit der Positionierung zu verbessern, werden an die Positionierfläche des Messerkissens strenge Anforderungen an die Maßhaltigkeit und Positioniergenauigkeit der Bearbeitung gestellt. Um die Stirnfläche der Schneide zu steuern, kann die axiale Richtung der Klinge eingestellt werden.
Klemmmechanismus: Der Spannmechanismus wird durch einen vorderen Druckkeil gespannt. Um die Anforderungen an ein zuverlässiges Spannen und eine bequeme Bedienung zu erfüllen, wird der Keilwinkel des Keils mit 12 ° gewählt. Wenn der Klemmkraftpunkt im oberen Teil der Klinge liegt, wird ein Spalt zwischen der Klinge und der Positionierungsfläche der Klinge gebildet, wodurch die Positionierungszuverlässigkeit der Klinge verschlechtert wird. Um dieses Phänomen zu vermeiden, wird die Klinge eng mit der Positionierungsfläche der Klinge verbunden, und der Einfluss der Hauptschneidkraft (Fz) auf die Positionierungsgenauigkeit der Klinge kann überwunden werden. Die Klemmkraft wird bei 1/2 der Klinge und dann 1 mm nach oben (Fj in Fig. 3 gezeigt) gewählt, und die Praxis hat sich als wirksam erwiesen.
Bearbeitung von Frästaschen:
Das Bearbeiten von Frästaschen ist einer der Schlüsselprozesse in der Fräserfertigung. Dies erfordert nicht nur eine hohe Bearbeitungsgenauigkeit der Lamelle selbst, sondern auch eine hohe Teilgenauigkeit zwischen den Lamellen. Wenn die Planiergenauigkeit der Lamelle nicht hoch ist, ist die Toleranz für das Einstechen ungleichmäßig. Um das Ausmaß der Wärmebehandlungsverformung nach dem Abschrecken des Fräsers zu steuern, wird zunächst nach der Grobbearbeitung des Fräserkörpers die Abschreck- und Anlassbehandlung durchgeführt, um die Struktur für das Abschrecken vorzubereiten. Die zweite Möglichkeit ist die Verwendung eines abgestuften Abschreckverfahrens, um Verformungen und Risse bei der Wärmebehandlung wirksam zu vermeiden. Um die Genauigkeit der Lamellenindizierung zu verbessern, wird im Schleifnutenprozess die spezielle Nut für die Schleifnut verwendet, um die konstruktiven Anforderungen an die Präzision der Lamellenherstellung und die Indizierungsgenauigkeit zu gewährleisten.
3. Dosierung Auswahl
Entsprechend den Zerspanungseigenschaften schwer zerspanbarer Werkstoffe wird beim Fräsen von manganreichem Stahl, gehärtetem Stahl, Gusseisen und anderen Werkstoffen, insbesondere beim kraftvollen Fräsen von Stahlteilen, in der Regel folgende Fräsdosis gewählt: Die Fräsgeschwindigkeit ist etwas niedriger, um die Frästemperatur zu senken, den Werkzeugverschleiß zu verringern und die Werkzeughaltbarkeit zu verbessern. Die Frästiefe und der Vorschub werden entsprechend erhöht, um sicherzustellen, dass das Werkzeug die Tiefe der arbeitshärtenden Schicht überschreitet und den Werkzeugverschleiß und das Absplittern verringert. Es ist jedoch auch zu berücksichtigen, dass die Fräskraft aufgrund der erhöhten Frästiefe und Vorschubgeschwindigkeit zunimmt, was zu Vibrationen beim Fräsen und dem Problem führt, dass die Späne nicht leicht zerbrechen.
4. Experimente zum Mahlen
Versuchsbedingung
Werkzeugmaschine: X5020;
Werkstück: ZGMn13 180 ~ 200HB
Fräser: d0 = 315 z = 16 YT798 Doppelschneidenfräser;
Dosierung: Vc = 25 m / min, ap fz = 0,2 mm / z.
Versuchsergebnisse 96 Teile des Werkstücks wurden kontinuierlich gefräst, und zwei Schichten wurden ohne abnormalen Verschleiß wie Abplatzen, Schneiden von Messern und Heißrissbildung gefräst. Im Vergleich zu anderen Fräsern erhöht sich die Produktivität fast um das Dreifache und die Werkzeughaltbarkeit um das 1,5-fache.
Der leistungsstarke Doppelschneiden-Schaftfräser verfügt über vernünftige Parameter und Strukturen, zuverlässiges Spannen und Positionieren, große Fräsmenge, gute Steifigkeit, hohe Produktionseffizienz und lange Lebensdauer. Es eignet sich besonders zum Schruppen und Vorschlichten von schwer zerspanbaren Werkstoffen wie Manganstahl, gehärtetem Stahl und hochlegiertem Stahl. Bei der von der National Knife Association organisierten Ausstellung für das Schneiden von Werkzeugen wurde der zweischneidige, leistungsstarke Fräser bei der Bearbeitung von Werkstoffen aus hochmanganhaltigem Stahl gut angenommen. Es wurde weit verbreitet in großen Unternehmen wie Second Automobile und Dalian Diesel Engine Factory eingesetzt.
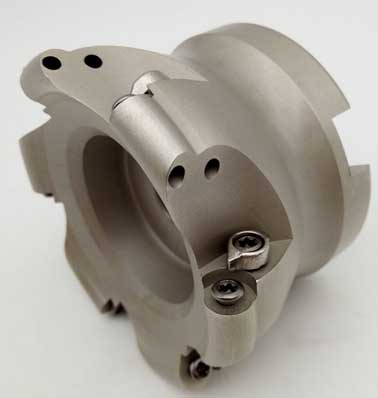
1. Winkel Auswahl
Analyse des Kontaktzustands beim Fräsen Die Wahl des Fräswinkels steht in direktem Zusammenhang mit dem Kontaktzustand beim Fräsen. Ein guter Fräskontaktzustand ist eines der Hauptprobleme bei der Auswahl des kraftvollen Fräserwinkels. Wie in Fig. 1 gezeigt, kann der Kontaktpunkt zwischen der Spanfläche und dem zu schneidenden Werkstück als vier spezielle Punkte (U, V, S, T) angenommen werden, wenn der Fräser in das Werkstück schneidet. Um zu verhindern, dass der Span abplatzt, sollte laut Analyse der Anfangspunkt des Kontakts an dem Punkt oder Punkt gewählt werden, der von der Hauptschneide entfernt ist, und zwar am besten.
Auswahl des Schnitttiefenwinkels gp und des Vorschubwinkels gf nach obiger Analyse. Damit der anfängliche Kontaktpunkt beim Schneiden des Fräsers in das Werkstück U-Punkt oder V-Punkt ist, ist die Auswahl des vorderen Winkels des Fräsers entscheidend. Wenn der Vorschubrechenwinkel gf kleiner als der Schneidewinkel d1 ist, ist der Aufprallvorgang beim Schneiden des Schneidwerkzeugs umso langsamer, je länger die Schneidzeit ist. Dadurch wird die Beschädigung des Fräsers verringert, die durch die thermische Rissbildung des Hartmetallfräsers verursacht wird. Der negative Schnitttiefenschlagwinkel gp kann die Schlagfestigkeit des Fräsers verbessern. Der negative Spanwinkel gf kann nicht nur die Schneidkantenfestigkeit verbessern, sondern auch das Aufrollen, Brechen und Beseitigen von Spänen erleichtern. Aus diesem Grund haben wir durch Analyse und experimentellen Vergleich den negativen Spanwinkel des Fräsers gewählt, dh gp = -5 °, gf = -8 °.
Auswahl der Werkzeugspitzenparameter Da sowohl die Schnittiefe als auch der Vorschubwinkel negativ sind, ist die Schneidverformung während des Fräsens groß, die Schneidkraft ist groß und die Frästemperatur ist erhöht. Starkes Schneiden erfordert zwar eine große Schnitt- und Vorschubtiefe, aber die Bildung breiter und dicker Späne kann die Temperatur der Schneidzone verringern. Es ist jedoch auch wichtig, einen vernünftigen Winkel zu wählen. Entsprechend den Verarbeitungsanforderungen des starken Schneidens, unter Berücksichtigung der Systemsteifigkeit und der Verbesserung der Wärmeableitungsbedingungen. Wählen Sie die Hauptdeklination kr = 75 °. Um die Stärke des Spitzenabschnitts zu erhöhen, wird bei dieser Konstruktion eine doppelte sekundäre Schaufelstruktur verwendet (Abb. 2), dh es werden zwei Teilschaufeln mit kr1 '= 5 ° (Schaufel) geschliffen Länge 2 mm) und kr2 '= 15 °. Zusätzlich wird an der Werkzeugspitze ein Bogen mit einem Spitzenradius re = 1,5 ± 0,1 mm geschliffen. Diese Art der Werkzeugspitze verbessert nicht nur die Werkzeugfestigkeit, sondern verringert auch die Reibung des Gegenmessers gegenüber der bearbeiteten Oberfläche, verringert die Schneidkraft, verringert die Schneidetemperatur und verbessert die Werkzeughaltbarkeit.
2. Strukturanalyse
Blattpositionierungsmethode: Die Positionierung der Klinge auf dem Messerkissen erfüllt nicht nur die Anforderungen an die Genauigkeit und Zuverlässigkeit der neuen Klingenpositionierung, sondern gewährleistet auch die Genauigkeit und Zuverlässigkeit der Positionierung, nachdem die Klinge indexiert wurde. Dies ist ein wichtiges Prinzip für die Auswahl der Positionierungsmethode des Messers und der Konstruktionsanforderungen für die Positionierungskomponenten. Dieses Design übernimmt die "Drei-Punkt-Positionierung" -Methode. In Anbetracht der Tatsache, dass das kraftvolle Fräsen eine größere Schneidkraft als das allgemeine Fräsen aufweist, verliert der Positionierungspunkt auf dem Messerkissen die Positionierungsfähigkeit aufgrund einer starken Extrusionsverformung, was die Positionierungsgenauigkeit und die Positionierungszuverlässigkeit beeinträchtigt. Daher wird eine schmale und lange Gesichtspositionierungsstruktur auf beiden Seiten der Klinge angewendet. Um die Zuverlässigkeit der Positionierung zu verbessern, werden an die Positionierfläche des Messerkissens strenge Anforderungen an die Maßhaltigkeit und Positioniergenauigkeit der Bearbeitung gestellt. Um die Stirnfläche der Schneide zu steuern, kann die axiale Richtung der Klinge eingestellt werden.
Klemmmechanismus: Der Spannmechanismus wird durch einen vorderen Druckkeil gespannt. Um die Anforderungen an ein zuverlässiges Spannen und eine bequeme Bedienung zu erfüllen, wird der Keilwinkel des Keils mit 12 ° gewählt. Wenn der Klemmkraftpunkt im oberen Teil der Klinge liegt, wird ein Spalt zwischen der Klinge und der Positionierungsfläche der Klinge gebildet, wodurch die Positionierungszuverlässigkeit der Klinge verschlechtert wird. Um dieses Phänomen zu vermeiden, wird die Klinge eng mit der Positionierungsfläche der Klinge verbunden, und der Einfluss der Hauptschneidkraft (Fz) auf die Positionierungsgenauigkeit der Klinge kann überwunden werden. Die Klemmkraft wird bei 1/2 der Klinge und dann 1 mm nach oben (Fj in Fig. 3 gezeigt) gewählt, und die Praxis hat sich als wirksam erwiesen.
Bearbeitung von Frästaschen:
Das Bearbeiten von Frästaschen ist einer der Schlüsselprozesse in der Fräserfertigung. Dies erfordert nicht nur eine hohe Bearbeitungsgenauigkeit der Lamelle selbst, sondern auch eine hohe Teilgenauigkeit zwischen den Lamellen. Wenn die Planiergenauigkeit der Lamelle nicht hoch ist, ist die Toleranz für das Einstechen ungleichmäßig. Um das Ausmaß der Wärmebehandlungsverformung nach dem Abschrecken des Fräsers zu steuern, wird zunächst nach der Grobbearbeitung des Fräserkörpers die Abschreck- und Anlassbehandlung durchgeführt, um die Struktur für das Abschrecken vorzubereiten. Die zweite Möglichkeit ist die Verwendung eines abgestuften Abschreckverfahrens, um Verformungen und Risse bei der Wärmebehandlung wirksam zu vermeiden. Um die Genauigkeit der Lamellenindizierung zu verbessern, wird im Schleifnutenprozess die spezielle Nut für die Schleifnut verwendet, um die konstruktiven Anforderungen an die Präzision der Lamellenherstellung und die Indizierungsgenauigkeit zu gewährleisten.
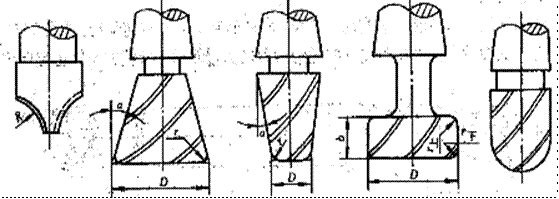
3. Dosierung Auswahl
Entsprechend den Zerspanungseigenschaften schwer zerspanbarer Werkstoffe wird beim Fräsen von manganreichem Stahl, gehärtetem Stahl, Gusseisen und anderen Werkstoffen, insbesondere beim kraftvollen Fräsen von Stahlteilen, in der Regel folgende Fräsdosis gewählt: Die Fräsgeschwindigkeit ist etwas niedriger, um die Frästemperatur zu senken, den Werkzeugverschleiß zu verringern und die Werkzeughaltbarkeit zu verbessern. Die Frästiefe und der Vorschub werden entsprechend erhöht, um sicherzustellen, dass das Werkzeug die Tiefe der arbeitshärtenden Schicht überschreitet und den Werkzeugverschleiß und das Absplittern verringert. Es ist jedoch auch zu berücksichtigen, dass die Fräskraft aufgrund der erhöhten Frästiefe und Vorschubgeschwindigkeit zunimmt, was zu Vibrationen beim Fräsen und dem Problem führt, dass die Späne nicht leicht zerbrechen.
4. Experimente zum Mahlen
Versuchsbedingung
Werkzeugmaschine: X5020;
Werkstück: ZGMn13 180 ~ 200HB
Fräser: d0 = 315 z = 16 YT798 Doppelschneidenfräser;
Dosierung: Vc = 25 m / min, ap fz = 0,2 mm / z.
Versuchsergebnisse 96 Teile des Werkstücks wurden kontinuierlich gefräst, und zwei Schichten wurden ohne abnormalen Verschleiß wie Abplatzen, Schneiden von Messern und Heißrissbildung gefräst. Im Vergleich zu anderen Fräsern erhöht sich die Produktivität fast um das Dreifache und die Werkzeughaltbarkeit um das 1,5-fache.
Der leistungsstarke Doppelschneiden-Schaftfräser verfügt über vernünftige Parameter und Strukturen, zuverlässiges Spannen und Positionieren, große Fräsmenge, gute Steifigkeit, hohe Produktionseffizienz und lange Lebensdauer. Es eignet sich besonders zum Schruppen und Vorschlichten von schwer zerspanbaren Werkstoffen wie Manganstahl, gehärtetem Stahl und hochlegiertem Stahl. Bei der von der National Knife Association organisierten Ausstellung für das Schneiden von Werkzeugen wurde der zweischneidige, leistungsstarke Fräser bei der Bearbeitung von Werkstoffen aus hochmanganhaltigem Stahl gut angenommen. Es wurde weit verbreitet in großen Unternehmen wie Second Automobile und Dalian Diesel Engine Factory eingesetzt.
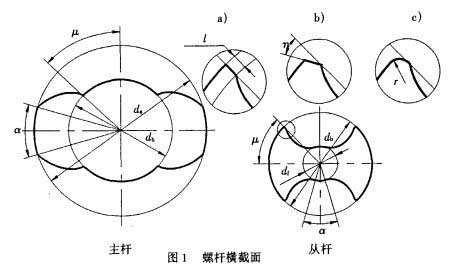
PREV:Auswahl des richtigen Werkzeugs fur die CNC-Bearbeitung
NEXT:NONE
NEXT:NONE