Auswahl des richtigen Werkzeugs fur die CNC-Bearbeitung
Bei der Programmierung ist es wichtig, das richtige CNC-Werkzeug auszuwählen. Die allgemeinen Anforderungen an CNC-Werkzeuge sind einfache Installation und Einstellung, gute Steifigkeit, hohe Präzision und gute Haltbarkeit. Auf dieser Basis umfassende Betrachtung der Schnittleistung des Werkstückmaterials, der Bearbeitungskapazität der Werkzeugmaschine, der Art des CNC-Bearbeitungsprozesses. Der Schneidumfang und viele Faktoren hängen vom Arbeitsbereich der Werkzeugmaschine und der numerischen Steuerung ab.
1. Faktoren, die die Auswahl der CNC-Werkzeuge beeinflussen
Bei der Auswahl des Typs und der Spezifikation des Werkzeugs werden die Hauptfaktoren berücksichtigt:
(1) Art der Produktion
Die Produktionseigenschaft bezieht sich hier auf die Losgröße der Teile, hauptsächlich unter Berücksichtigung des Einflusses der Bearbeitungskosten auf die Werkzeugauswahl. Beispielsweise kann der Einsatz von Spezialwerkzeugen in der Massenproduktion kostengünstig sein. In der Kleinserienfertigung ist die Auswahl von Standardwerkzeugen besser geeignet.
(2) Maschinentyp
Komplette CNC-Werkzeugmaschinen, die in diesem Schritt verwendet werden, Auswahl des Werkzeugtyps (Bohrer, Drehwerkzeug oder Fräswerkzeug). Werkzeuge mit hoher Produktivität, wie Hochgeschwindigkeitsschneidwerkzeuge und Drehwerkzeuge mit großem Vorschub, sind unter der Bedingung zulässig, dass das Werkstücksystem und das Werkzeugsystem starr sind.
(3) CNC-Bearbeitungsplan
Verschiedene Arten von Werkzeugen können für verschiedene CNC-Bearbeitungslösungen verwendet werden. Beispielsweise kann die Bearbeitung von Löchern mit Bohrern und Reibahlen oder mit Bohrern und Bohrwerkzeugen erfolgen.
(4) Größe und Form des Werkstücks
Die Größe und Form des Werkstücks beeinflusst auch die Wahl des Werkzeugtyps und der Spezifikation. Zum Beispiel werden spezielle Oberflächen mit speziellen Werkzeugen bearbeitet.
(5) Oberflächenrauheit bearbeiten
Die Oberflächenrauheit der bearbeiteten Oberfläche beeinflusst die Strukturform und die Schnittmenge des Werkzeugs. Zum Beispiel können beim Schruppen Schruppfräser und beim Schlichtfräsen Feinfräser eingesetzt werden.
(6) Bearbeitungsgenauigkeit
Die Bearbeitungsgenauigkeit beeinflusst die Art und Form des Endbearbeitungswerkzeugs. Beispielsweise kann die endgültige Bearbeitung des Lochs durch Bohren, Reiben oder Bohren entsprechend der Genauigkeit des Lochs erfolgen.
(7) Werkstückmaterial
Das Werkzeugmaterial hängt mit dem Werkzeugmaterial und der Geometrie des Schneidteils zusammen, das Werkzeugmaterial mit der Bearbeitungsgenauigkeit des Werkstücks und der Materialhärte.
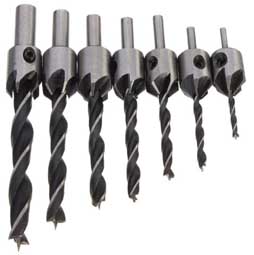
2. Leistungsanforderungen an CNC-Werkzeuge
Da CNC-Werkzeugmaschinen die Eigenschaften einer hohen Bearbeitungsgenauigkeit, einer hohen Bearbeitungseffizienz, eines konzentrierten Bearbeitungsprozesses und weniger Teilespannzeiten aufweisen, werden höhere Anforderungen an die verwendeten CNC-Werkzeuge gestellt.
In Bezug auf die Werkzeugleistung sollten CNC-Werkzeuge höher sein als diejenigen, die in normalen Werkzeugmaschinen verwendet werden.
Bei der Auswahl eines CNC-Werkzeugs ist es die erste Wahl, zuerst das Standardwerkzeug zu verwenden. Bei Bedarf können Sie eine Vielzahl von hocheffizienten Verbundwerkzeugen und speziellen Spezialwerkzeugen verwenden. Bei der Auswahl eines Standard-CNC-Werkzeugs sollte dieses mit dem tatsächlichen Werkzeug kombiniert werden Situation, so weit wie möglich, um eine Vielzahl von fortschrittlichen Werkzeugen, wie Wendeplatten, Vollhartmetall-Werkzeuge, Keramik-Werkzeuge zu wählen.
Bei der Auswahl einer CNC-Werkzeugmaschine sollten Sie auch folgende Aspekte berücksichtigen:
(1) Der Typ, die Spezifikation und das Genauigkeitsniveau des CNC-Werkzeugs sollten die Bearbeitungsanforderungen erfüllen und das Werkzeugmaterial sollte mit dem Werkstückmaterial kompatibel sein.
(2) Gute Schneidleistung.
Um sich beim Schruppen oder Bearbeiten von schwer zerspanbaren Werkstoffen an die große Grundfläche und den hohen Vorschub des Werkzeugs anzupassen, sollte das Werkzeug dem Hochgeschwindigkeitsschneiden und dem kraftvollen Schneiden standhalten. Gleichzeitig muss die gleiche Werkzeugcharge hinsichtlich Schneidleistung und Standzeit stabil sein, um einen Werkzeugwechsel entsprechend der Standzeit zu erreichen oder die Standzeit über ein CNC-System zu verwalten.
(3) hohe Präzision.
Um den Anforderungen an hohe Präzision und automatischen Werkzeugwechsel bei der CNC-Bearbeitung gerecht zu werden, muss das Werkzeug eine hohe Präzision aufweisen. Beispielsweise hat der integrierte Schaftfräser eine radiale Maßgenauigkeit von bis zu 0,005 mm.
(4) hohe Zuverlässigkeit.
Es ist darauf zu achten, dass das Werkzeug nicht versehentlich beschädigt wird und mögliche Fehler in der CNC-Bearbeitung auftreten, die den reibungslosen Ablauf der Bearbeitung beeinträchtigen. Es ist erforderlich, dass das Werkzeug und das damit verbundene Zubehör eine gute Zuverlässigkeit und eine starke Anpassungsfähigkeit aufweisen.
(5) Hohe Haltbarkeit.
CNC-Bearbeitungswerkzeuge, ob beim Schruppen oder Schlichten, sollten eine höhere Lebensdauer aufweisen als herkömmliche Werkzeugmaschinen. Minimierung der Anzahl von Austausch- oder Schleifwerkzeugen und der Werkzeugeinstellung, wodurch die Bearbeitungseffizienz von CNC-Werkzeugmaschinen und der Qualitätssicherungsprozess verbessert werden.
(6) Gute Spanbrech- und Spanentfernungsleistung.
Bei der CNC-Bearbeitung werden Spanbruch und Spanabfuhr nicht wie bei normalen Werkzeugmaschinen manuell von Hand ausgeführt. Späne neigen dazu, sich um das Werkzeug und das Werkstück zu wickeln, das Werkzeug zu beschädigen und die bearbeitete Oberfläche zu zerkratzen, und können sogar zu Verletzungen und Unfällen mit Geräten führen. Beeinträchtigt die Qualität der Maschine und den sicheren Betrieb der Werkzeugmaschine, sodass das Werkzeug eine bessere Spanbrech- und Spanabfuhrleistung aufweisen muss.
3. Werkzeugauswahlmethode
Die Wahl des Werkzeugs ist einer der wichtigen Inhalte im CNC-Bearbeitungsprozess, der nicht nur die Bearbeitungseffizienz der Werkzeugmaschine beeinflusst, sondern auch die Bearbeitungsqualität des Teils direkt beeinflusst. Weil die Spindeldrehzahl und der Bereich der CNC-Werkzeugmaschinen viel höher sind als bei normalen Werkzeugmaschinen und die Ausgangsleistung der Spindel groß ist. Daher werden im Vergleich zu herkömmlichen Bearbeitungsverfahren höhere Anforderungen an das CNC-Bearbeitungswerkzeug gestellt, einschließlich hoher Präzision, hoher Festigkeit, guter Steifigkeit, hoher Haltbarkeit, stabiler Größe und bequemer Installation und Einstellung. Dies erfordert eine angemessene Struktur des Werkzeugs, eine Standardisierung der geometrischen Parameter und eine Serialisierung. CNC-Werkzeuge sind eine der Voraussetzungen für die Verbesserung der Bearbeitungseffizienz. Die Auswahl hängt von der Geometrie des zu bearbeitenden Teils, dem Materialzustand, der Steifigkeit der Vorrichtung und dem für die Maschine ausgewählten Werkzeug ab.
Folgende Aspekte sollten beachtet werden:
(1) Wählen Sie das Werkzeug entsprechend der Schneidleistung des Teilematerials aus. Zum Drehen oder Fräsen von hochfesten Stahl-, Titanlegierungs- und Edelstahlteilen wird empfohlen, ein Wendeplattenwerkzeug mit guter Verschleißfestigkeit zu wählen.
(2) Wählen Sie das Werkzeug entsprechend der Bearbeitungsstufe des Teils aus.
Das heißt, die Schruppstufe dient hauptsächlich zum Entfernen des Randes, und das Werkzeug mit besserer Steifigkeit und geringerer Präzision sollte ausgewählt werden. Um die Bearbeitungsgenauigkeit und Produktqualität der Teile zu gewährleisten, sollten in der Vorschlicht- und Endbearbeitungsphase Werkzeuge mit hoher Haltbarkeit und hoher Präzision ausgewählt werden. Das in der Schruppstufe eingesetzte Werkzeug hat die geringste Präzision und das in der Schlichtstufe eingesetzte Werkzeug die höchste Präzision. Wenn für die Schrupp- und Schlichtbearbeitung dasselbe Werkzeug ausgewählt ist, wird empfohlen, das aus der Schlichtbearbeitung ausgeschlossene Werkzeug für die Schruppbearbeitung auszuwählen. Da der Zustand des Werkzeugverschleißes beim Schlichten meistens der geringe Verschleiß der Klinge ist, verschleißt und repariert die Beschichtung das Licht, und der kontinuierliche Gebrauch beeinträchtigt die Verarbeitungsqualität des Schlichtens, aber der Einfluss auf das Schruppen ist gering.
(3) Die Werkzeug- und Geometrieparameter werden gemäß den Eigenschaften des Bearbeitungsbereichs ausgewählt. Ein Werkzeug mit großem Durchmesser und kleinem Seitenverhältnis sollte verwendet werden, wenn die Teilestruktur dies zulässt. Die mittlere Schneidkante eines dünnwandigen, ultradünnen Wandteils sollte einen ausreichenden Zentripetalwinkel aufweisen, um die Schneidkraft des Werkzeugs und des Schneidteils zu verringern. Bei der Bearbeitung von Teilen wie Aluminium und Kupfer sollten Sie einen Schaftfräser mit einer etwas größeren vorderen Ecke wählen und die Zähnezahl sollte 4 Zähne nicht überschreiten.
Bei der Auswahl eines Werkzeugs sollte die Größe des Werkzeugs an die Oberflächengröße des zu bearbeitenden Werkstücks angepasst werden. Bei der Herstellung wird die Umfangskontur der Hobelteile häufig mit einem Schaftfräser bearbeitet; Beim Fräsen der Ebene sollte der Hartmetalleinsatzfräser gewählt werden; Wählen Sie beim Bearbeiten von Vorsprüngen und Nuten Schnellarbeitsstahl-Schaftfräser aus. Bei der Bearbeitung der Oberfläche des Rohlings oder beim Schruppen des Lochs kann ein Maisfräser mit Hartmetalleinsatz gewählt werden. Für die Bearbeitung einiger dreidimensionaler und winkelvariabler Konturen werden häufig Kugelkopffräser, Ringfräser, Kegelfräser und Scheibenfräser eingesetzt.
Bei der Freiformflächenbearbeitung ist da die Schnittgeschwindigkeit des Endes des Kugelkopfwerkzeugs Null. um die bearbeitungsgenauigkeit zu gewährleisten, ist die schneideteilung in der regel klein, so dass der kugelfräser zum schlichten der gewölbten oberfläche geeignet ist.
Der Schaftfräser ist dem Kugelschaftfräser in Bezug auf Oberflächenqualität und Bearbeitungseffizienz weit überlegen. Wählen Sie daher den Schaftfräser, wenn beim Schruppen und Vorschlichten der Oberfläche sichergestellt werden soll, dass die Teile nicht geschnitten werden. Darüber hinaus sind die Haltbarkeit und Genauigkeit des Werkzeugs stark vom Werkzeugpreis abhängig und müssen beachtet werden.
In den meisten Fällen erhöht die Wahl eines guten Werkzeugs die Kosten des Werkzeugs, aber die sich daraus ergebende Erhöhung der Verarbeitungsqualität und der Verarbeitungseffizienz kann die Gesamtverarbeitungskosten erheblich senken.
Im Bearbeitungszentrum sind alle Werkzeuge im Werkzeugmagazin vorinstalliert und der entsprechende Werkzeugwechsel erfolgt über die Befehle Werkzeuganwahl und Werkzeugwechsel des NC-Programms. Der entsprechende Standardschaft für die Systemspezifikation der Werkzeugmaschine muss ausgewählt werden, damit das CNC-Bearbeitungswerkzeug schnell und genau auf der Maschinenspindel montiert oder in das Werkzeugmagazin zurückgeführt werden kann. Der Programmierer sollte in der Lage sein, die Strukturgröße, die Einstellmethode und den Einstellbereich des in der Werkzeugmaschine verwendeten Werkzeughalters zu verstehen, um sicherzustellen, dass die radialen und axialen Abmessungen des Werkzeugs während der Programmierung bestimmt werden und die Reihenfolge der Werkzeuge angemessen angeordnet ist .
1. Faktoren, die die Auswahl der CNC-Werkzeuge beeinflussen
Bei der Auswahl des Typs und der Spezifikation des Werkzeugs werden die Hauptfaktoren berücksichtigt:
(1) Art der Produktion
Die Produktionseigenschaft bezieht sich hier auf die Losgröße der Teile, hauptsächlich unter Berücksichtigung des Einflusses der Bearbeitungskosten auf die Werkzeugauswahl. Beispielsweise kann der Einsatz von Spezialwerkzeugen in der Massenproduktion kostengünstig sein. In der Kleinserienfertigung ist die Auswahl von Standardwerkzeugen besser geeignet.
(2) Maschinentyp
Komplette CNC-Werkzeugmaschinen, die in diesem Schritt verwendet werden, Auswahl des Werkzeugtyps (Bohrer, Drehwerkzeug oder Fräswerkzeug). Werkzeuge mit hoher Produktivität, wie Hochgeschwindigkeitsschneidwerkzeuge und Drehwerkzeuge mit großem Vorschub, sind unter der Bedingung zulässig, dass das Werkstücksystem und das Werkzeugsystem starr sind.
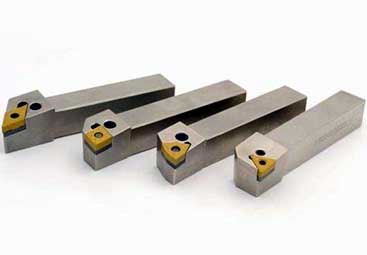
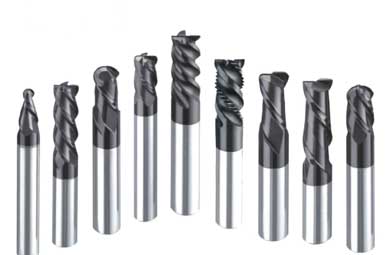
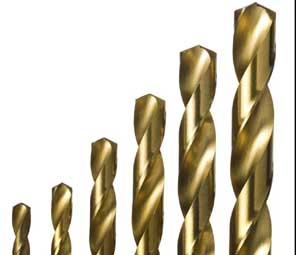
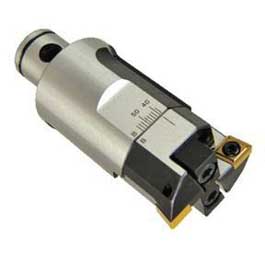
(3) CNC-Bearbeitungsplan
Verschiedene Arten von Werkzeugen können für verschiedene CNC-Bearbeitungslösungen verwendet werden. Beispielsweise kann die Bearbeitung von Löchern mit Bohrern und Reibahlen oder mit Bohrern und Bohrwerkzeugen erfolgen.
(4) Größe und Form des Werkstücks
Die Größe und Form des Werkstücks beeinflusst auch die Wahl des Werkzeugtyps und der Spezifikation. Zum Beispiel werden spezielle Oberflächen mit speziellen Werkzeugen bearbeitet.
(5) Oberflächenrauheit bearbeiten
Die Oberflächenrauheit der bearbeiteten Oberfläche beeinflusst die Strukturform und die Schnittmenge des Werkzeugs. Zum Beispiel können beim Schruppen Schruppfräser und beim Schlichtfräsen Feinfräser eingesetzt werden.
(6) Bearbeitungsgenauigkeit
Die Bearbeitungsgenauigkeit beeinflusst die Art und Form des Endbearbeitungswerkzeugs. Beispielsweise kann die endgültige Bearbeitung des Lochs durch Bohren, Reiben oder Bohren entsprechend der Genauigkeit des Lochs erfolgen.
(7) Werkstückmaterial
Das Werkzeugmaterial hängt mit dem Werkzeugmaterial und der Geometrie des Schneidteils zusammen, das Werkzeugmaterial mit der Bearbeitungsgenauigkeit des Werkstücks und der Materialhärte.
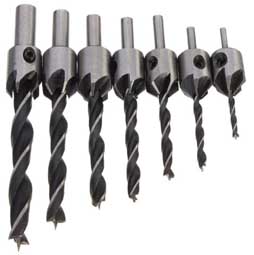
2. Leistungsanforderungen an CNC-Werkzeuge
Da CNC-Werkzeugmaschinen die Eigenschaften einer hohen Bearbeitungsgenauigkeit, einer hohen Bearbeitungseffizienz, eines konzentrierten Bearbeitungsprozesses und weniger Teilespannzeiten aufweisen, werden höhere Anforderungen an die verwendeten CNC-Werkzeuge gestellt.
In Bezug auf die Werkzeugleistung sollten CNC-Werkzeuge höher sein als diejenigen, die in normalen Werkzeugmaschinen verwendet werden.
Bei der Auswahl eines CNC-Werkzeugs ist es die erste Wahl, zuerst das Standardwerkzeug zu verwenden. Bei Bedarf können Sie eine Vielzahl von hocheffizienten Verbundwerkzeugen und speziellen Spezialwerkzeugen verwenden. Bei der Auswahl eines Standard-CNC-Werkzeugs sollte dieses mit dem tatsächlichen Werkzeug kombiniert werden Situation, so weit wie möglich, um eine Vielzahl von fortschrittlichen Werkzeugen, wie Wendeplatten, Vollhartmetall-Werkzeuge, Keramik-Werkzeuge zu wählen.
Bei der Auswahl einer CNC-Werkzeugmaschine sollten Sie auch folgende Aspekte berücksichtigen:
(1) Der Typ, die Spezifikation und das Genauigkeitsniveau des CNC-Werkzeugs sollten die Bearbeitungsanforderungen erfüllen und das Werkzeugmaterial sollte mit dem Werkstückmaterial kompatibel sein.
(2) Gute Schneidleistung.
Um sich beim Schruppen oder Bearbeiten von schwer zerspanbaren Werkstoffen an die große Grundfläche und den hohen Vorschub des Werkzeugs anzupassen, sollte das Werkzeug dem Hochgeschwindigkeitsschneiden und dem kraftvollen Schneiden standhalten. Gleichzeitig muss die gleiche Werkzeugcharge hinsichtlich Schneidleistung und Standzeit stabil sein, um einen Werkzeugwechsel entsprechend der Standzeit zu erreichen oder die Standzeit über ein CNC-System zu verwalten.
(3) hohe Präzision.
Um den Anforderungen an hohe Präzision und automatischen Werkzeugwechsel bei der CNC-Bearbeitung gerecht zu werden, muss das Werkzeug eine hohe Präzision aufweisen. Beispielsweise hat der integrierte Schaftfräser eine radiale Maßgenauigkeit von bis zu 0,005 mm.
(4) hohe Zuverlässigkeit.
Es ist darauf zu achten, dass das Werkzeug nicht versehentlich beschädigt wird und mögliche Fehler in der CNC-Bearbeitung auftreten, die den reibungslosen Ablauf der Bearbeitung beeinträchtigen. Es ist erforderlich, dass das Werkzeug und das damit verbundene Zubehör eine gute Zuverlässigkeit und eine starke Anpassungsfähigkeit aufweisen.
(5) Hohe Haltbarkeit.
CNC-Bearbeitungswerkzeuge, ob beim Schruppen oder Schlichten, sollten eine höhere Lebensdauer aufweisen als herkömmliche Werkzeugmaschinen. Minimierung der Anzahl von Austausch- oder Schleifwerkzeugen und der Werkzeugeinstellung, wodurch die Bearbeitungseffizienz von CNC-Werkzeugmaschinen und der Qualitätssicherungsprozess verbessert werden.
(6) Gute Spanbrech- und Spanentfernungsleistung.
Bei der CNC-Bearbeitung werden Spanbruch und Spanabfuhr nicht wie bei normalen Werkzeugmaschinen manuell von Hand ausgeführt. Späne neigen dazu, sich um das Werkzeug und das Werkstück zu wickeln, das Werkzeug zu beschädigen und die bearbeitete Oberfläche zu zerkratzen, und können sogar zu Verletzungen und Unfällen mit Geräten führen. Beeinträchtigt die Qualität der Maschine und den sicheren Betrieb der Werkzeugmaschine, sodass das Werkzeug eine bessere Spanbrech- und Spanabfuhrleistung aufweisen muss.
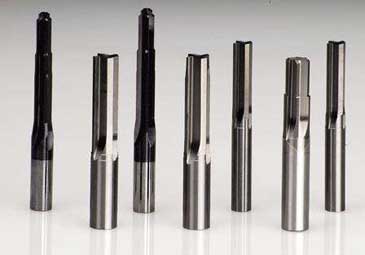
3. Werkzeugauswahlmethode
Die Wahl des Werkzeugs ist einer der wichtigen Inhalte im CNC-Bearbeitungsprozess, der nicht nur die Bearbeitungseffizienz der Werkzeugmaschine beeinflusst, sondern auch die Bearbeitungsqualität des Teils direkt beeinflusst. Weil die Spindeldrehzahl und der Bereich der CNC-Werkzeugmaschinen viel höher sind als bei normalen Werkzeugmaschinen und die Ausgangsleistung der Spindel groß ist. Daher werden im Vergleich zu herkömmlichen Bearbeitungsverfahren höhere Anforderungen an das CNC-Bearbeitungswerkzeug gestellt, einschließlich hoher Präzision, hoher Festigkeit, guter Steifigkeit, hoher Haltbarkeit, stabiler Größe und bequemer Installation und Einstellung. Dies erfordert eine angemessene Struktur des Werkzeugs, eine Standardisierung der geometrischen Parameter und eine Serialisierung. CNC-Werkzeuge sind eine der Voraussetzungen für die Verbesserung der Bearbeitungseffizienz. Die Auswahl hängt von der Geometrie des zu bearbeitenden Teils, dem Materialzustand, der Steifigkeit der Vorrichtung und dem für die Maschine ausgewählten Werkzeug ab.
Folgende Aspekte sollten beachtet werden:
(1) Wählen Sie das Werkzeug entsprechend der Schneidleistung des Teilematerials aus. Zum Drehen oder Fräsen von hochfesten Stahl-, Titanlegierungs- und Edelstahlteilen wird empfohlen, ein Wendeplattenwerkzeug mit guter Verschleißfestigkeit zu wählen.
(2) Wählen Sie das Werkzeug entsprechend der Bearbeitungsstufe des Teils aus.
Das heißt, die Schruppstufe dient hauptsächlich zum Entfernen des Randes, und das Werkzeug mit besserer Steifigkeit und geringerer Präzision sollte ausgewählt werden. Um die Bearbeitungsgenauigkeit und Produktqualität der Teile zu gewährleisten, sollten in der Vorschlicht- und Endbearbeitungsphase Werkzeuge mit hoher Haltbarkeit und hoher Präzision ausgewählt werden. Das in der Schruppstufe eingesetzte Werkzeug hat die geringste Präzision und das in der Schlichtstufe eingesetzte Werkzeug die höchste Präzision. Wenn für die Schrupp- und Schlichtbearbeitung dasselbe Werkzeug ausgewählt ist, wird empfohlen, das aus der Schlichtbearbeitung ausgeschlossene Werkzeug für die Schruppbearbeitung auszuwählen. Da der Zustand des Werkzeugverschleißes beim Schlichten meistens der geringe Verschleiß der Klinge ist, verschleißt und repariert die Beschichtung das Licht, und der kontinuierliche Gebrauch beeinträchtigt die Verarbeitungsqualität des Schlichtens, aber der Einfluss auf das Schruppen ist gering.
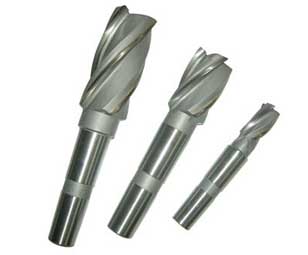
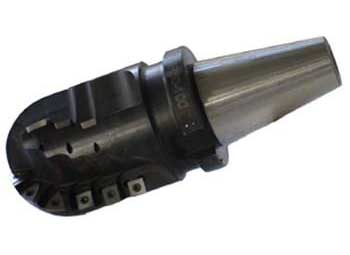
(3) Die Werkzeug- und Geometrieparameter werden gemäß den Eigenschaften des Bearbeitungsbereichs ausgewählt. Ein Werkzeug mit großem Durchmesser und kleinem Seitenverhältnis sollte verwendet werden, wenn die Teilestruktur dies zulässt. Die mittlere Schneidkante eines dünnwandigen, ultradünnen Wandteils sollte einen ausreichenden Zentripetalwinkel aufweisen, um die Schneidkraft des Werkzeugs und des Schneidteils zu verringern. Bei der Bearbeitung von Teilen wie Aluminium und Kupfer sollten Sie einen Schaftfräser mit einer etwas größeren vorderen Ecke wählen und die Zähnezahl sollte 4 Zähne nicht überschreiten.
Bei der Auswahl eines Werkzeugs sollte die Größe des Werkzeugs an die Oberflächengröße des zu bearbeitenden Werkstücks angepasst werden. Bei der Herstellung wird die Umfangskontur der Hobelteile häufig mit einem Schaftfräser bearbeitet; Beim Fräsen der Ebene sollte der Hartmetalleinsatzfräser gewählt werden; Wählen Sie beim Bearbeiten von Vorsprüngen und Nuten Schnellarbeitsstahl-Schaftfräser aus. Bei der Bearbeitung der Oberfläche des Rohlings oder beim Schruppen des Lochs kann ein Maisfräser mit Hartmetalleinsatz gewählt werden. Für die Bearbeitung einiger dreidimensionaler und winkelvariabler Konturen werden häufig Kugelkopffräser, Ringfräser, Kegelfräser und Scheibenfräser eingesetzt.
Bei der Freiformflächenbearbeitung ist da die Schnittgeschwindigkeit des Endes des Kugelkopfwerkzeugs Null. um die bearbeitungsgenauigkeit zu gewährleisten, ist die schneideteilung in der regel klein, so dass der kugelfräser zum schlichten der gewölbten oberfläche geeignet ist.
Der Schaftfräser ist dem Kugelschaftfräser in Bezug auf Oberflächenqualität und Bearbeitungseffizienz weit überlegen. Wählen Sie daher den Schaftfräser, wenn beim Schruppen und Vorschlichten der Oberfläche sichergestellt werden soll, dass die Teile nicht geschnitten werden. Darüber hinaus sind die Haltbarkeit und Genauigkeit des Werkzeugs stark vom Werkzeugpreis abhängig und müssen beachtet werden.
In den meisten Fällen erhöht die Wahl eines guten Werkzeugs die Kosten des Werkzeugs, aber die sich daraus ergebende Erhöhung der Verarbeitungsqualität und der Verarbeitungseffizienz kann die Gesamtverarbeitungskosten erheblich senken.
Im Bearbeitungszentrum sind alle Werkzeuge im Werkzeugmagazin vorinstalliert und der entsprechende Werkzeugwechsel erfolgt über die Befehle Werkzeuganwahl und Werkzeugwechsel des NC-Programms. Der entsprechende Standardschaft für die Systemspezifikation der Werkzeugmaschine muss ausgewählt werden, damit das CNC-Bearbeitungswerkzeug schnell und genau auf der Maschinenspindel montiert oder in das Werkzeugmagazin zurückgeführt werden kann. Der Programmierer sollte in der Lage sein, die Strukturgröße, die Einstellmethode und den Einstellbereich des in der Werkzeugmaschine verwendeten Werkzeughalters zu verstehen, um sicherzustellen, dass die radialen und axialen Abmessungen des Werkzeugs während der Programmierung bestimmt werden und die Reihenfolge der Werkzeuge angemessen angeordnet ist .
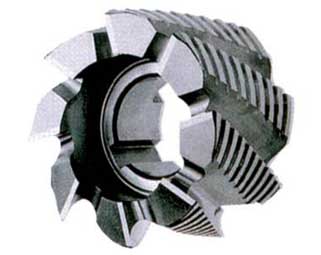
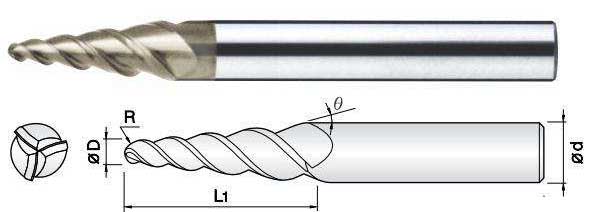