tecnologia de procesamiento para los engranajes de aleacion de titanio de precision
Palabras clave: Piezas de engranajes de aleación de titanio, Piezas mecanizadas de engranajes, Procesamiento de engranajes, Precisión de la corrección de referencia y acabado del perfil dental.
La Figura 9-17 muestra los engranajes dobles hechos de TC4 Ti-6Al-4V con una precisión de 7-6-6. El proceso de mecanizado se muestra en la Tabla 9-6.
Como se puede ver en la tabla, el proceso de mecanizado de engranajes generalmente pasa por las siguientes etapas: Tratamiento térmico de palanquilla, mecanizado de piezas en bruto de dientes, mecanizado de perfil de dientes, mecanizado de extremos de dientes, tratamiento térmico de superficies de dientes, corrección de referencia fina y acabado de superficies de dientes.
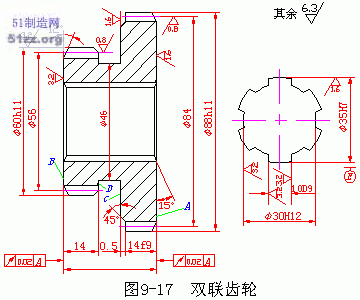
Figura 9-17 Engranaje doble de aleación de titanio.
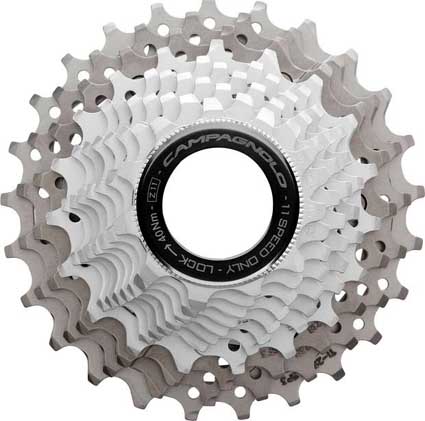
Segundo Superficie principal de mecanizado del engranaje.
1. La superficie principal de mecanizado del engranaje tiene una superficie de diente y una superficie de referencia de engranaje. Este último incluye un agujero de referencia con un engranaje perforado, una cara de extremo de montaje para el proceso de corte y una superficie cilíndrica superior para usar como referencia para medir la posición de la pieza en bruto o medir el grosor del diente.
2. Material del engranaje y pieza en blanco.
Los materiales para engranajes de uso común son los aceros estructurales al carbono, tales como TC4 Ti-6Al-4V, acero 15 y acero 45; Los engranajes de alta velocidad, alta fuerza y alta precisión se utilizan comúnmente en aceros estructurales de aleación como 20Cr, 40Cr, 38CrMoAl, 20CrMnTiA, Ti, etc.
La pieza en bruto del engranaje está determinada por factores tales como el material, la forma estructural, el tamaño, las condiciones de uso y el lote de producción de engranajes. Comúnmente se utilizan aleaciones de titanio, barras, lingotes forjados, lingotes de acero fundido o hierro fundido.
Tres Los principales requisitos técnicos del engranaje recto,
1. Precisión de engranajes y espacio libre.
GBl0095 "Involutar precisión de engranajes cilíndricos" especifica 12 tipos de engranajes y grados de precisión de pares de engranajes.
Entre ellos, los grados 1 a 2 son grados de superprecisión;
Los niveles 3-5 son grados de alta precisión;
Los niveles 6-8 son grados de precisión media;
Los grados 9-12 son grados de baja precisión.
El nivel 7 es el más utilizado en el corte y mecanizado de engranajes. Las tolerancias de los engranajes y las desviaciones de los límites se agrupan en tres grupos de tolerancia (Tabla 13-4) según las características del error del engranaje y su impacto principal en el rendimiento de la transmisión. Dependiendo de los requisitos de uso del engranaje, se pueden usar diferentes niveles de tolerancia para cada grupo de tolerancia.
La holgura del par de engranajes se refiere a la distancia entre las dos caras del diente que no funcionan en la dirección normal cuando el par de engranajes está activado (es decir, el contragolpe normal), y la holgura se utiliza para asegurar el funcionamiento normal del par de engranajes. Al mecanizar engranajes, la desviación límite del grosor del diente se utiliza para controlar y asegurar el tamaño del espacio del lado del engranaje.
2. Precisión de la superficie de referencia del engranaje.
El error dimensional y el error de posición de la forma del plano de referencia del engranaje afectan directamente la precisión del engranaje y el par de engranajes. Por lo tanto, la tolerancia del espacio en blanco se especifica en el apéndice de GB10095. Para engranajes con una clase de precisión de 6 a 8, las tolerancias dimensionales y las tolerancias de forma de los orificios de referencia de engranajes perforados son IT6-IT7, el diámetro del círculo toroidal utilizado como referencia para la medición es IT8; para engranajes con una clase de precisión de 6 a 8, perforado Las tolerancias dimensionales y las tolerancias de forma de los orificios de referencia de los engranajes son IT6-IT7, y la tolerancia de diámetro del círculo superior utilizado como referencia de medición es IT8. Las tolerancias de desviación circular de la cara radial y del extremo del plano de referencia están entre 11 y 22 μm (engranajes pequeños y medianos, diámetro del círculo exponencial no mayor a 400 mm).
3. rugosidad de la superficie
La rugosidad de la superficie de la cara del diente del engranaje y la superficie de referencia de la muesca del diente tiene cierta influencia en la vida útil del engranaje y el ruido en la transmisión.
Para un engranaje que tiene una precisión de 6 a 8, la rugosidad de la superficie Ra de la superficie del diente suele ser de 0,8 a 3,2 μm. El orificio de referencia es de 0,8-1,6 μm. El diario de referencia es de 0,4-1,6 μm. La cara final de referencia es de 1.6 a 3.2 μm. La superficie superior cilíndrica de los dientes es de 3.2 μm.
En tercer lugar, los principales problemas de proceso de procesamiento de engranajes rectos
1. Referencia de posicionamiento
La selección de la referencia de posicionamiento del mecanizado de engranajes debe ser coherente con el principio de coincidencia de referencia y ser lo más consistente posible con la referencia de montaje y la base de medición. Al mismo tiempo, se deben seleccionar los mismos datos de posicionamiento durante todo el proceso de mecanizado de engranajes (como el encofrado, afeitado, afilado, etc.) para mantener la uniformidad del punto de referencia.
For the ring gear of the perforated gear or the assembled gear, a special mandrel is often used to position the inner bore and the end face of the tooth blank. This method has high positioning accuracy and high productivity, and is suitable for mass production. In the case of single-piece small batch production, the outer circle and the end face are often used as the positioning reference to eliminate the mandrel, but the outer circle is required to have a small radial runout of the hole, and the method has low productivity.
2. Procesamiento de piezas en blanco.
El mecanizado de piezas de engranajes incluye principalmente orificios de engranajes y caras de extremo con orificios.
(1) El esquema principal del procesamiento de la muela dental es el siguiente:
1) Perforación, escariado, escariado e inserción de chaveteros
2) Perforar, escariar, tirar chaveteros y agujeros de pulido
3) Un orificio de inserción o inserción de chavetero para girar o taladrar
(2) El giro se utiliza principalmente para las caras externas y finales de los billetes.
En la producción en serie, las máquinas herramienta de alta productividad se utilizan a menudo para mecanizar piezas de dientes, tales como máquinas semiautomáticas de múltiples ejes, múltiples estaciones y múltiples herramientas. En la producción de lotes simples y pequeños, los tornos de propósito general se usan comúnmente, pero se debe tener cuidado de que el acabado de las caras internas y finales de referencia se realice en un dispositivo y se marque en la cara final de referencia.
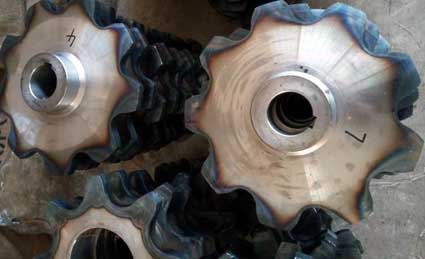
3. Selección del método de corte de la superficie del engranaje.
La elección del método de corte de la superficie del engranaje depende principalmente del grado de precisión del engranaje, el lote de producción, las condiciones de producción y los requisitos de tratamiento térmico.
El encofrado o la configuración de engranajes se pueden usar para cumplir con los requisitos de los engranajes de 7 a 8 de precisión no endurecidos.
El encofrado se puede utilizar para cumplir los requisitos de 6-7 engranajes no endurecidos de precisión.
Cuando el lote de producción es pequeño, se puede usar un engranaje endurecido de grado 6-7.
El volumen de producción es pequeño, 6-7 engranajes endurecidos de precisión. Se puede usar para: tallado - (o piñón) - Tratamiento térmico de la superficie del diente - Solución de pulido, cuando el tamaño del lote de producción es grande, se puede usar el tratamiento térmico de la superficie del diente - raspado - tratamiento de trituración
4. Tecnología de procesamiento de engranajes cilíndricos.
(1) Engranajes que solo requieren tratamiento térmico.
Fabricación de palanquilla - Tratamiento térmico en blanco (normalización) - Desbaste de piezas de engranajes - Temple y revenido - Acabado de piezas de piezas - Desbaste de superficies de dientes - Mecanizado de superficies de dientes.
(2) Engranajes de acero estructural de aleación de titanio y acero estructural de carbono medio cuya superficie debe ser apagada
Fabricación en blanco - estandarización - desbaste de la pieza en bruto - temple y revenido - semiacabado de la pieza en bruto - rugosidad de la superficie del diente (semiacabado) - temple de la superficie del diente - acabado de la superficie del diente - acabado de la superficie del diente.
(3) Engranajes para carburación o nitruración de dientes.
Fabricación de palanquilla - Normalización - Desbaste de piezas en bruto - Normalización o temple - Semiacabado de palanquillas - Desbaste de los flancos de los dientes - Semiacabado de los flancos de los dientes - Carburación y temple o nitruración. Acabado de la pieza del diente. Acabado de la superficie del diente.
La Figura 9-17 muestra los engranajes dobles hechos de TC4 Ti-6Al-4V con una precisión de 7-6-6. El proceso de mecanizado se muestra en la Tabla 9-6.
Como se puede ver en la tabla, el proceso de mecanizado de engranajes generalmente pasa por las siguientes etapas: Tratamiento térmico de palanquilla, mecanizado de piezas en bruto de dientes, mecanizado de perfil de dientes, mecanizado de extremos de dientes, tratamiento térmico de superficies de dientes, corrección de referencia fina y acabado de superficies de dientes.
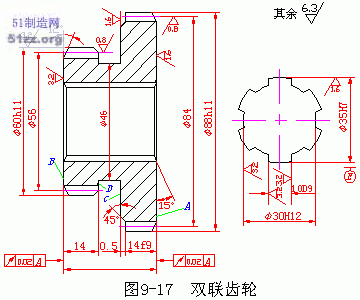
Figura 9-17 Engranaje doble de aleación de titanio.
Número de dientes | Ⅰ | Ⅱ |
Número de dientes
|
Ⅰ | Ⅱ |
Módulo | 2 | 2 | Desviación de la fundación | ±0.016 | ±0.016 |
Número de dientes | 28 | 42 | Tolerancia dental | 0.017 | 0.018 |
Nivel de exactitud | 7GK | 7JL | Tolerancia de la dirección del diente | 0.017 | 0.017 |
Ley pública cambio de longitud | 0.039 | 0.024 | Longitud media de la normalidad común | 21.36 0-0.05 | 27.6 0-0.05 |
Engranaje radial de la corona dentada | 0.050 | 0.042 | Número de dientes cruzados | 4 | 5 |
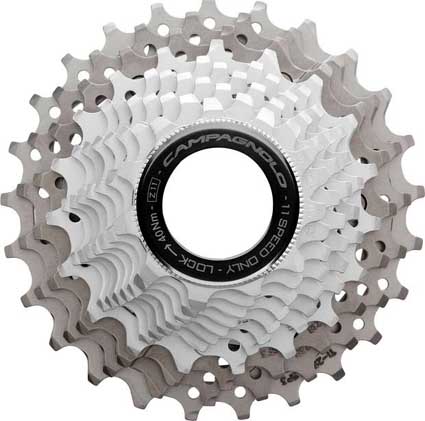
Segundo Superficie principal de mecanizado del engranaje.
1. La superficie principal de mecanizado del engranaje tiene una superficie de diente y una superficie de referencia de engranaje. Este último incluye un agujero de referencia con un engranaje perforado, una cara de extremo de montaje para el proceso de corte y una superficie cilíndrica superior para usar como referencia para medir la posición de la pieza en bruto o medir el grosor del diente.
2. Material del engranaje y pieza en blanco.
Los materiales para engranajes de uso común son los aceros estructurales al carbono, tales como TC4 Ti-6Al-4V, acero 15 y acero 45; Los engranajes de alta velocidad, alta fuerza y alta precisión se utilizan comúnmente en aceros estructurales de aleación como 20Cr, 40Cr, 38CrMoAl, 20CrMnTiA, Ti, etc.
La pieza en bruto del engranaje está determinada por factores tales como el material, la forma estructural, el tamaño, las condiciones de uso y el lote de producción de engranajes. Comúnmente se utilizan aleaciones de titanio, barras, lingotes forjados, lingotes de acero fundido o hierro fundido.
Tres Los principales requisitos técnicos del engranaje recto,
1. Precisión de engranajes y espacio libre.
GBl0095 "Involutar precisión de engranajes cilíndricos" especifica 12 tipos de engranajes y grados de precisión de pares de engranajes.
Entre ellos, los grados 1 a 2 son grados de superprecisión;
Los niveles 3-5 son grados de alta precisión;
Los niveles 6-8 son grados de precisión media;
Los grados 9-12 son grados de baja precisión.
El nivel 7 es el más utilizado en el corte y mecanizado de engranajes. Las tolerancias de los engranajes y las desviaciones de los límites se agrupan en tres grupos de tolerancia (Tabla 13-4) según las características del error del engranaje y su impacto principal en el rendimiento de la transmisión. Dependiendo de los requisitos de uso del engranaje, se pueden usar diferentes niveles de tolerancia para cada grupo de tolerancia.
La holgura del par de engranajes se refiere a la distancia entre las dos caras del diente que no funcionan en la dirección normal cuando el par de engranajes está activado (es decir, el contragolpe normal), y la holgura se utiliza para asegurar el funcionamiento normal del par de engranajes. Al mecanizar engranajes, la desviación límite del grosor del diente se utiliza para controlar y asegurar el tamaño del espacio del lado del engranaje.
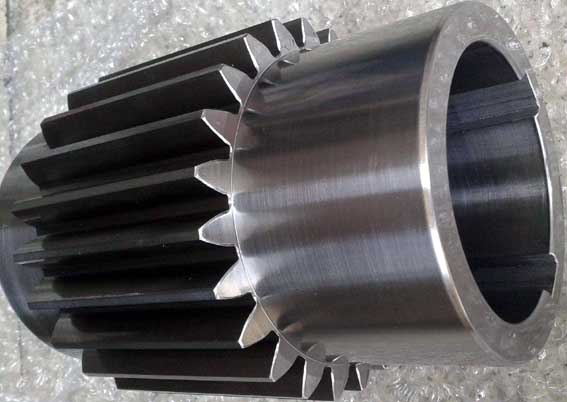
2. Precisión de la superficie de referencia del engranaje.
El error dimensional y el error de posición de la forma del plano de referencia del engranaje afectan directamente la precisión del engranaje y el par de engranajes. Por lo tanto, la tolerancia del espacio en blanco se especifica en el apéndice de GB10095. Para engranajes con una clase de precisión de 6 a 8, las tolerancias dimensionales y las tolerancias de forma de los orificios de referencia de engranajes perforados son IT6-IT7, el diámetro del círculo toroidal utilizado como referencia para la medición es IT8; para engranajes con una clase de precisión de 6 a 8, perforado Las tolerancias dimensionales y las tolerancias de forma de los orificios de referencia de los engranajes son IT6-IT7, y la tolerancia de diámetro del círculo superior utilizado como referencia de medición es IT8. Las tolerancias de desviación circular de la cara radial y del extremo del plano de referencia están entre 11 y 22 μm (engranajes pequeños y medianos, diámetro del círculo exponencial no mayor a 400 mm).
3. rugosidad de la superficie
La rugosidad de la superficie de la cara del diente del engranaje y la superficie de referencia de la muesca del diente tiene cierta influencia en la vida útil del engranaje y el ruido en la transmisión.
Para un engranaje que tiene una precisión de 6 a 8, la rugosidad de la superficie Ra de la superficie del diente suele ser de 0,8 a 3,2 μm. El orificio de referencia es de 0,8-1,6 μm. El diario de referencia es de 0,4-1,6 μm. La cara final de referencia es de 1.6 a 3.2 μm. La superficie superior cilíndrica de los dientes es de 3.2 μm.
En tercer lugar, los principales problemas de proceso de procesamiento de engranajes rectos
1. Referencia de posicionamiento
La selección de la referencia de posicionamiento del mecanizado de engranajes debe ser coherente con el principio de coincidencia de referencia y ser lo más consistente posible con la referencia de montaje y la base de medición. Al mismo tiempo, se deben seleccionar los mismos datos de posicionamiento durante todo el proceso de mecanizado de engranajes (como el encofrado, afeitado, afilado, etc.) para mantener la uniformidad del punto de referencia.
For the ring gear of the perforated gear or the assembled gear, a special mandrel is often used to position the inner bore and the end face of the tooth blank. This method has high positioning accuracy and high productivity, and is suitable for mass production. In the case of single-piece small batch production, the outer circle and the end face are often used as the positioning reference to eliminate the mandrel, but the outer circle is required to have a small radial runout of the hole, and the method has low productivity.
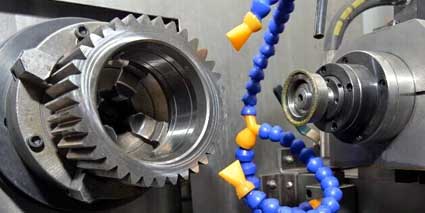
2. Procesamiento de piezas en blanco.
El mecanizado de piezas de engranajes incluye principalmente orificios de engranajes y caras de extremo con orificios.
(1) El esquema principal del procesamiento de la muela dental es el siguiente:
1) Perforación, escariado, escariado e inserción de chaveteros
2) Perforar, escariar, tirar chaveteros y agujeros de pulido
3) Un orificio de inserción o inserción de chavetero para girar o taladrar
(2) El giro se utiliza principalmente para las caras externas y finales de los billetes.
En la producción en serie, las máquinas herramienta de alta productividad se utilizan a menudo para mecanizar piezas de dientes, tales como máquinas semiautomáticas de múltiples ejes, múltiples estaciones y múltiples herramientas. En la producción de lotes simples y pequeños, los tornos de propósito general se usan comúnmente, pero se debe tener cuidado de que el acabado de las caras internas y finales de referencia se realice en un dispositivo y se marque en la cara final de referencia.
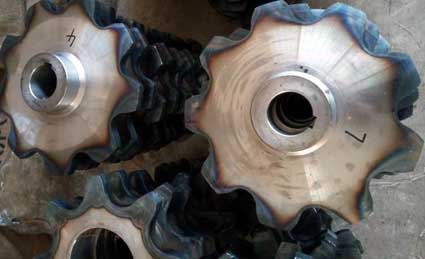
3. Selección del método de corte de la superficie del engranaje.
La elección del método de corte de la superficie del engranaje depende principalmente del grado de precisión del engranaje, el lote de producción, las condiciones de producción y los requisitos de tratamiento térmico.
El encofrado o la configuración de engranajes se pueden usar para cumplir con los requisitos de los engranajes de 7 a 8 de precisión no endurecidos.
El encofrado se puede utilizar para cumplir los requisitos de 6-7 engranajes no endurecidos de precisión.
Cuando el lote de producción es pequeño, se puede usar un engranaje endurecido de grado 6-7.
El volumen de producción es pequeño, 6-7 engranajes endurecidos de precisión. Se puede usar para: tallado - (o piñón) - Tratamiento térmico de la superficie del diente - Solución de pulido, cuando el tamaño del lote de producción es grande, se puede usar el tratamiento térmico de la superficie del diente - raspado - tratamiento de trituración
4. Tecnología de procesamiento de engranajes cilíndricos.
(1) Engranajes que solo requieren tratamiento térmico.
Fabricación de palanquilla - Tratamiento térmico en blanco (normalización) - Desbaste de piezas de engranajes - Temple y revenido - Acabado de piezas de piezas - Desbaste de superficies de dientes - Mecanizado de superficies de dientes.
(2) Engranajes de acero estructural de aleación de titanio y acero estructural de carbono medio cuya superficie debe ser apagada
Fabricación en blanco - estandarización - desbaste de la pieza en bruto - temple y revenido - semiacabado de la pieza en bruto - rugosidad de la superficie del diente (semiacabado) - temple de la superficie del diente - acabado de la superficie del diente - acabado de la superficie del diente.
(3) Engranajes para carburación o nitruración de dientes.
Fabricación de palanquilla - Normalización - Desbaste de piezas en bruto - Normalización o temple - Semiacabado de palanquillas - Desbaste de los flancos de los dientes - Semiacabado de los flancos de los dientes - Carburación y temple o nitruración. Acabado de la pieza del diente. Acabado de la superficie del diente.