piezas de aleacion de titanio TC4 molienda mecanica personalizadas
Palabras clave: Mecanizado, Piezas de titanio TC4, Propiedades físicas del titanio TC4, Diseño de procesamiento de piezas de titanio TC4, Piezas de titanio personalizadas,
Primero, características de procesamiento:
TC4 tiene las siguientes propiedades físicas / químicas especiales:
1. El TC4 tiene una conductividad térmica baja, lo que hace que la temperatura de la pieza y la herramienta sea más alta durante el procesamiento;
2. El bajo módulo elástico de TC4 produce un gran rebote después de que la carga se deforme, lo que provoca un aumento en el error de mecanizado de la pieza de trabajo, un aumento en el torque de la herramienta de corte, un rápido desgaste del filo y una disminución de la durabilidad.
3, el TC4 tiene una dureza baja y una actividad química alta, lo que resulta en la disolución y difusión del TC4 y el cortador a altas temperaturas, lo que resulta en pegado, quemado y corte.
Basado en el análisis anterior, la tecnología de procesamiento de TC4 debe incluir los siguientes principios:
1, porque TC4 tiene baja conductividad térmica, baja plasticidad y alta tendencia al endurecimiento por trabajo. Durante el proceso de mecanizado, la fuerza de corte es grande y la temperatura de corte alta, lo que hace que la herramienta sea fácil de usar y acorta la vida útil. Por lo tanto, la herramienta debe seleccionarse de materiales con buena resistencia al desgaste, alta dureza al calor y suficiente tenacidad. YG8, YG8W y YG10H se utilizan para desbaste, y YG8W o YP15 (YGRM) se utilizan para el acabado.
2. Optimizar las condiciones de corte, incluidas las herramientas de la máquina, los accesorios, el sistema de herramientas es rígido.
3. Elija una cantidad razonable de corte. En condiciones normales, la velocidad de corte debe ser baja, la profundidad de corte debe ser grande y el corte no puede detenerse durante el proceso de corte.
4. Mejorar el control de viruta y asegurar medidas de ruptura de viruta confiables.
En segundo lugar, el diseño experimental.
Teniendo en cuenta los factores anteriores, el proceso estudió la prueba de factor único y la prueba ortogonal multifactorial, estudió el proceso de corte de TC4 y analizó la integridad de la superficie de las muestras procesadas.
Los indicadores de evaluación incluyen principalmente: rugosidad de la superficie, dureza de procesamiento, tensión residual y microestructura.
(1) Prueba de factor único:
Refiriéndose al rango de parámetros de corte en la producción real, el rango de variación horizontal de cada factor en este experimento se establece de la siguiente manera:
(1) El grado de velocidad de fresado se cambia a 40, 80, 100, 120, 140 m / min, la velocidad de avance es de 50 mm / min, la profundidad de fresado axial es de 1,5 mm y la profundidad de fresado radial es de 28 mm.
(2) El cambio horizontal positivo de la alimentación de cada diente es 0.05, 0.07, 0.09, 0.11, 0.13 mm, la velocidad de fresado es de 40 mm / min, la profundidad de fresado axial es de 0.9 mm y la profundidad de fresado radial es de 8 mm;
(3) La profundidad de fresado axial es 0.4, 0.6, O.8, 1.0, 1.2, 1.5 mm. Mantenga una velocidad de fresado de 40 mm / min, una velocidad de avance de 40.7 mm / min y una profundidad de fresado radial de 8 mm.
(4) La profundidad de fresado radial se cambia a 4, 6, 8, 10, 12, 5, 14, 16 mm. La velocidad de fresado es k = 40 mm / min, la velocidad de avance es de 40,7 mm / min y la profundidad de fresado axial es de 1 mm.
A través de las pruebas anteriores, puede comprender la influencia de los parámetros de fresado en cantidades físicas como la fuerza de fresado, la temperatura de fresado y la calidad de la superficie.
(B), prueba ortogonal multifactorial.
El estudio de proceso utilizó el diseño ortogonal L16 para estudiar el proceso de fresado de TC4. Los parámetros específicos son los siguientes:
Los parámetros de fresado y la codificación horizontal son:
A través de la prueba ortogonal anterior, se puede comprender el grado de influencia de cada parámetro de procesamiento en la integridad de la superficie de la máquina, y se puede obtener la mejor tecnología de procesamiento.
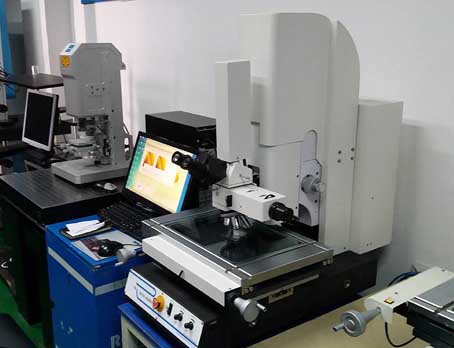
Tercero, análisis y evaluación:
La rugosidad de la superficie se mide con un interferómetro de luz blanca en la superficie mecanizada. Cada prueba se realiza tomando 5 posiciones en la dirección de fresado.
El aumento en el endurecimiento es el resultado de una combinación de campos de tensión no uniformes acoplados térmicamente en la superficie mecanizada de la pieza durante el proceso de corte, que está relacionada con las condiciones de corte y las propiedades mecánicas de la pieza. En este trabajo, se estudió la influencia de los factores de molienda en las leyes de endurecimiento y endurecimiento del trabajo mediante la medición de la dureza de la capa superficial después de la molienda TC4. La dureza de la superficie mecanizada se midió con un comprobador de microdureza Vickers, y el grado de endurecimiento por trabajo se obtuvo comparando la dureza superficial con la dureza de la superficie no mecanizada. Se utilizaron cinco muestras por dirección de molienda para la medición.
Los materiales TC4 son muy sensibles a las condiciones de tensión, especialmente la tensión residual en la superficie mecanizada y su distribución es importante para el uso adecuado de los componentes.
La tensión residual de la superficie mecanizada tiene una diferencia entre la tensión de tracción residual y la tensión de compresión residual. El esfuerzo de tracción residual reduce la resistencia a la fatiga y la vida útil de la pieza, y el esfuerzo de compresión residual a veces aumenta la resistencia a la fatiga y la vida útil de la pieza. La distribución desigual de la tensión residual en cada porción de la superficie mecanizada también hará que la pieza de trabajo se deforme, afectando la forma y la precisión dimensional de la pieza. Por lo tanto, el método de rayos X se utilizó para estudiar la tensión residual de la superficie y su distribución de materiales TC4TC4 durante el fresado a alta velocidad. La microestructura se corta mediante un método de corte de alambre, y la sección transversal en la dirección de alimentación vertical es la superficie de observación. Después del pulido, se seleccionó una solución de grabado apropiada para el grabado de la superficie y se observó por SEM.
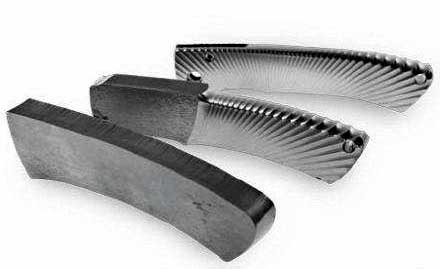
Primero, características de procesamiento:
TC4 tiene las siguientes propiedades físicas / químicas especiales:
1. El TC4 tiene una conductividad térmica baja, lo que hace que la temperatura de la pieza y la herramienta sea más alta durante el procesamiento;
2. El bajo módulo elástico de TC4 produce un gran rebote después de que la carga se deforme, lo que provoca un aumento en el error de mecanizado de la pieza de trabajo, un aumento en el torque de la herramienta de corte, un rápido desgaste del filo y una disminución de la durabilidad.
3, el TC4 tiene una dureza baja y una actividad química alta, lo que resulta en la disolución y difusión del TC4 y el cortador a altas temperaturas, lo que resulta en pegado, quemado y corte.
Basado en el análisis anterior, la tecnología de procesamiento de TC4 debe incluir los siguientes principios:
1, porque TC4 tiene baja conductividad térmica, baja plasticidad y alta tendencia al endurecimiento por trabajo. Durante el proceso de mecanizado, la fuerza de corte es grande y la temperatura de corte alta, lo que hace que la herramienta sea fácil de usar y acorta la vida útil. Por lo tanto, la herramienta debe seleccionarse de materiales con buena resistencia al desgaste, alta dureza al calor y suficiente tenacidad. YG8, YG8W y YG10H se utilizan para desbaste, y YG8W o YP15 (YGRM) se utilizan para el acabado.
2. Optimizar las condiciones de corte, incluidas las herramientas de la máquina, los accesorios, el sistema de herramientas es rígido.
3. Elija una cantidad razonable de corte. En condiciones normales, la velocidad de corte debe ser baja, la profundidad de corte debe ser grande y el corte no puede detenerse durante el proceso de corte.
4. Mejorar el control de viruta y asegurar medidas de ruptura de viruta confiables.
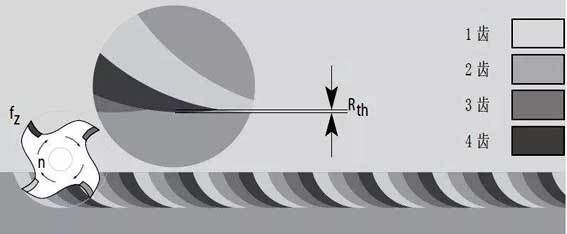
En segundo lugar, el diseño experimental.
Teniendo en cuenta los factores anteriores, el proceso estudió la prueba de factor único y la prueba ortogonal multifactorial, estudió el proceso de corte de TC4 y analizó la integridad de la superficie de las muestras procesadas.
Los indicadores de evaluación incluyen principalmente: rugosidad de la superficie, dureza de procesamiento, tensión residual y microestructura.
(1) Prueba de factor único:
Refiriéndose al rango de parámetros de corte en la producción real, el rango de variación horizontal de cada factor en este experimento se establece de la siguiente manera:
(1) El grado de velocidad de fresado se cambia a 40, 80, 100, 120, 140 m / min, la velocidad de avance es de 50 mm / min, la profundidad de fresado axial es de 1,5 mm y la profundidad de fresado radial es de 28 mm.
(2) El cambio horizontal positivo de la alimentación de cada diente es 0.05, 0.07, 0.09, 0.11, 0.13 mm, la velocidad de fresado es de 40 mm / min, la profundidad de fresado axial es de 0.9 mm y la profundidad de fresado radial es de 8 mm;
(3) La profundidad de fresado axial es 0.4, 0.6, O.8, 1.0, 1.2, 1.5 mm. Mantenga una velocidad de fresado de 40 mm / min, una velocidad de avance de 40.7 mm / min y una profundidad de fresado radial de 8 mm.
(4) La profundidad de fresado radial se cambia a 4, 6, 8, 10, 12, 5, 14, 16 mm. La velocidad de fresado es k = 40 mm / min, la velocidad de avance es de 40,7 mm / min y la profundidad de fresado axial es de 1 mm.
A través de las pruebas anteriores, puede comprender la influencia de los parámetros de fresado en cantidades físicas como la fuerza de fresado, la temperatura de fresado y la calidad de la superficie.
(B), prueba ortogonal multifactorial.
El estudio de proceso utilizó el diseño ortogonal L16 para estudiar el proceso de fresado de TC4. Los parámetros específicos son los siguientes:
Los parámetros de fresado y la codificación horizontal son:
Profundidad de fresado (mm) |
Velocidad de fresado (m/min) |
Alimentación por diente (mm) |
Ancho de fresado
|
|
Nivel superior (3) | 1.4 | 120 | 0.14 | 14 |
Nivel subordinado (1) | 1 | 100 | 0.1 | 11 |
Siguiente nivel (-1) | 0.6 | 80 | 0.06 | 18 |
Nivel inferior (3) | 0.2 | 60 | 0.02 | 5 |
Tabla de prueba ortogonal:
Profundidad de fresado (mm) |
Velocidad de fresado (m/min) |
Alimentación por diente (mm) |
Ancho de fresado (mm) |
|
1 | 1.4 | 100 | 0.06 | 11 |
2 | 1.4 | 80 | 0.14 | 5 |
3 | 1.4 | 120 | 0.02 | 8 |
4 | 1.4 | 60 | 0.1 | 14 |
5 | 1 | 60 | 0.06 | 8 |
6 | 1 | 120 | 0.14 | 14 |
7 | 1 | 80 | 0.02 | 11 |
8 | 1 | 100 | 0.1 | 5 |
9 | 0.6 | 60 | 0.14 | 11 |
10 | 0.6 | 120 | 0.06 | 5 |
11 | 0.6 | 80 | 0.1 | 8 |
12 | 0.6 | 100 | 0.02 | 14 |
13 | 0.2 | 100 | 0.14 | 8 |
14 | 0.2 | 80 | 0.06 | 14 |
15 | 0.2 | 120 | 0.1 | 11 |
16 | 0.2 | 60 | 0.02 | 5 |
A través de la prueba ortogonal anterior, se puede comprender el grado de influencia de cada parámetro de procesamiento en la integridad de la superficie de la máquina, y se puede obtener la mejor tecnología de procesamiento.
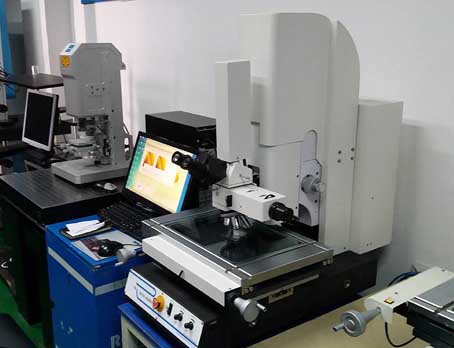
Tercero, análisis y evaluación:
La rugosidad de la superficie se mide con un interferómetro de luz blanca en la superficie mecanizada. Cada prueba se realiza tomando 5 posiciones en la dirección de fresado.
El aumento en el endurecimiento es el resultado de una combinación de campos de tensión no uniformes acoplados térmicamente en la superficie mecanizada de la pieza durante el proceso de corte, que está relacionada con las condiciones de corte y las propiedades mecánicas de la pieza. En este trabajo, se estudió la influencia de los factores de molienda en las leyes de endurecimiento y endurecimiento del trabajo mediante la medición de la dureza de la capa superficial después de la molienda TC4. La dureza de la superficie mecanizada se midió con un comprobador de microdureza Vickers, y el grado de endurecimiento por trabajo se obtuvo comparando la dureza superficial con la dureza de la superficie no mecanizada. Se utilizaron cinco muestras por dirección de molienda para la medición.
Los materiales TC4 son muy sensibles a las condiciones de tensión, especialmente la tensión residual en la superficie mecanizada y su distribución es importante para el uso adecuado de los componentes.
La tensión residual de la superficie mecanizada tiene una diferencia entre la tensión de tracción residual y la tensión de compresión residual. El esfuerzo de tracción residual reduce la resistencia a la fatiga y la vida útil de la pieza, y el esfuerzo de compresión residual a veces aumenta la resistencia a la fatiga y la vida útil de la pieza. La distribución desigual de la tensión residual en cada porción de la superficie mecanizada también hará que la pieza de trabajo se deforme, afectando la forma y la precisión dimensional de la pieza. Por lo tanto, el método de rayos X se utilizó para estudiar la tensión residual de la superficie y su distribución de materiales TC4TC4 durante el fresado a alta velocidad. La microestructura se corta mediante un método de corte de alambre, y la sección transversal en la dirección de alimentación vertical es la superficie de observación. Después del pulido, se seleccionó una solución de grabado apropiada para el grabado de la superficie y se observó por SEM.
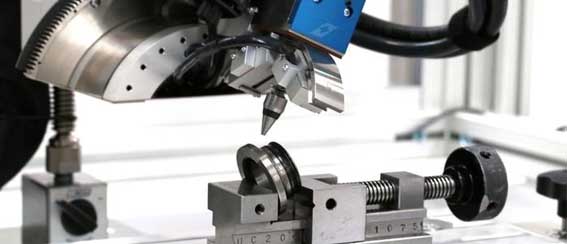