Mejora del rendimiento de moldes progresivos
El estampado progresivo de troqueles es un método rentable y seguro para producir componentes. El diseño y la construcción cuidadosos de los troqueles asegurarán un rendimiento óptimo.
Un troquel progresivo realiza una serie de operaciones fundamentales de chapa en dos o más estaciones del troquel durante cada golpe de prensa. Estas operaciones simultáneas producen una parte de una tira de material que se mueve a través de la matriz. Cada estación de trabajo realiza una o más operaciones de troquel, pero la tira debe moverse desde la primera estación a través de cada estación siguiente para producir una pieza completa. Los portadores, que consisten en una o más tiras de material que quedan entre las partes, proporcionan el movimiento de las partes de una estación de troquel a la siguiente. Estas tiras transportadoras están separadas de las partes en la última estación de troquel.
Hay seis elementos que deben abordarse al diseñar y construir un molde progresivo para maximizar su rendimiento:
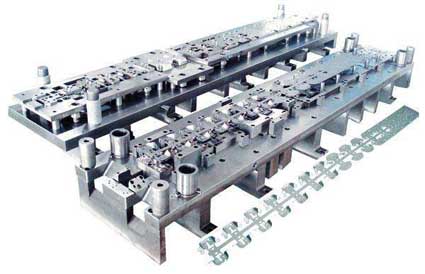
Interpretando la parte impresa
Material de partida en el molde
Elevadores de parte y alimentación de parte
Portadores de piezas flexibles
Almohadillas de presión superior
Conchas dibujadas.
Interpretando la impresión de la pieza
El primer paso en el diseño adecuado de un molde progresivo es analizar correctamente la impresión de la pieza. El diseñador de la herramienta debe interpretar la impresión para determinar la función de la pieza buscando cosas como el tipo de material, las superficies críticas, el tamaño y la ubicación del agujero, la ubicación de las rebabas, los requisitos de dirección del grano, el acabado de la superficie y otros factores.
El diseñador del molde debe comprender bien la pieza, especialmente si tiene formas y contornos irregulares. Sin embargo, las impresiones modernas dibujadas por computadora hacen que esto sea más difícil porque los datos de las piezas dibujadas por computadora se pueden descargar directamente a la computadora de diseño de moldes. Como resultado, el diseñador puede no familiarizarse completamente con las características importantes de las piezas.
Además, muchas partes dibujadas por computadora son más difíciles de entender, porque a menudo, solo se muestra una superficie y puede ser la superficie interior o exterior. Los dibujos por computadora a menudo muestran todas las líneas, incluidas las características ocultas, como líneas continuas en lugar de líneas de puntos. Esto conduce a errores de interpretación, lo que a su vez conduce a errores en la construcción del molde.
Para comprender mejor las formas complejas de las piezas, es útil construir un modelo "a la vista" de la pieza utilizando cera en láminas, revestimientos de goma o modelos de madera. La precisión dimensional no es crítica para estos modelos, ya que se utilizan principalmente para visualizar la pieza. Las pieles de goma y la cera en láminas también se pueden usar para desarrollar formas de preformas y para desarrollar las mejores posiciones para la pieza a medida que pasa a través de cada operación de molde en el molde progresivo.
Material de partida en el molde
Se debe tener cuidado para garantizar que la tira se inicie correctamente en el molde. La ubicación incorrecta del extremo de plomo de la tira hará más daño al molde en los primeros 10 golpes de la prensa que los siguientes 100,000 golpes.
Los medidores de "entrada" deben tener cables grandes y una repisa para soportar el extremo de la tira de la bobina cuando se inserta en el molde. Los cables grandes en los medidores son importantes para que la persona encargada de la configuración del molde no tenga que alcanzar el molde, así como para minimizar el tiempo requerido para comenzar una nueva tira en el molde. Además, un calibre debe ser ajustable para compensar la variación en el ancho de la tira.
La posición del borde de ataque de la tira es crítica para la primera carrera de prensado, y debe determinarse para cada estación de moldeo para asegurar que los punzones perforadores no corten agujeros parciales en el borde de ataque. Esto podría causar la desviación del punzón o provocar un corte parcial con punzones de recorte, lo que puede provocar una carga lateral desequilibrada a medida que la tira pasa a través del molde. Cualquiera de estas condiciones puede dar como resultado un cambio en la relación de punzón a molde que puede causar el cizallamiento de los punzones.
La ubicación inadecuada del borde de ataque de la tira también puede dar como resultado una condición de formación o brida desequilibrada que puede desplazar el molde superior en relación con el molde inferior. Se deben requerir tacones para absorber esta carga lateral, particularmente cuando se forman materiales gruesos.
Una muesca de paso y una parada de paso pueden proporcionar un punto físico para ubicar y controlar el borde de ataque de la tira. Las etiquetas de latón o las ranuras de los marcadores también pueden proporcionar una ubicación visual, pero no son tan precisas ni tan efectivas como una parada de muesca de inclinación. Se puede evitar que la prensa funcione con una alimentación corta o sobrealimentada montando el tope de paso en un pivote y monitoreándolo con un interruptor de límite
Piezas Lifters y piezas de alimentación
Los moldes progresivos a menudo requieren que la tira se levante del nivel normal de trabajo del molde al nivel de alimentación antes de que tenga lugar la alimentación de la tira. Esto puede variar desde una pequeña cantidad, para eliminar las rebabas de corte y perforación, hasta varias pulgadas para permitir que las formas de las piezas eliminen el molde.
Normally, all lifters should rise to the same height so that the strip is supported in a level plane during forward feed. The strip must not sag between lifters; otherwise parts will be pulled out of their correct station location spacing. Bar lifters provide good support and are better than spring pins or round lifters notched on one side of the strip.
Normalmente, todos los levantadores deben elevarse a la misma altura para que la tira se sostenga en un plano nivelado durante la alimentación hacia adelante. La tira no debe hundirse entre los levantadores; de lo contrario, las piezas se extraerán del espacio correcto de ubicación de la estación. Los elevadores de barra brindan un buen soporte y son mejores que los pasadores de resorte o los elevadores redondos con muescas en un lado de la tira.
A menudo, un buen sistema elevador de barras permite velocidades de prensa más altas porque se eliminan los problemas de alimentación. Aunque el costo inicial es más que los levantadores redondos, el rendimiento es mejor y se reduce el tiempo de configuración.
Las condiciones de medición y levantamiento pueden simularse durante el diseño del molde cortando un trozo de papel transparente al ancho de la tira. El borde anterior del papel se coloca sobre la vista en planta del diseño del molde en el lugar donde se colocará la tira para el primer golpe de prensado. Luego, el papel se marca con todas las operaciones que se realizarán en la primera estación de moldes, por ejemplo, muescas y perforaciones. La tira de papel luego se mueve a la segunda estación en el dibujo y se marcan las operaciones tanto para la primera como para la segunda estación. Este proceso se repite a través de todas las estaciones de moldes para ilustrar cómo se verá la tira de parte real cuando se inicie en el molde y ayuda a determinar la idoneidad de los medidores y levantadores.
Portadores de piezas flexibles
Para transportar la tira de una estación a la siguiente en un molde progresivo, debe dejarse algo de material entre las partes de la tira. Este material de soporte puede ser sólido en todo el ancho de la tira, o puede ser una o más cintas estrechas de material, vea la barra lateral de los soportes de parte.
Muchas partes requieren que el borde de la pieza en bruto fluya hacia adentro durante las operaciones de embridado, conformado o estirado. Esto puede requerir que el transportador se mueva lateralmente o se flexione verticalmente, o ambos, durante la operación del molde. Se debe proporcionar un bucle flexible en el transportador para permitir la flexión y el movimiento de la pieza sin extraer las partes adyacentes de su posición.
Es importante tener en cuenta la flexión del soporte durante la carrera ascendente de la prensa, así como durante la carrera descendente porque la acción puede ser diferente. Esto se puede simular en la etapa de diseño haciendo un esquema de la sección transversal de la pieza, las almohadillas de presión y los aceros montados en estacionarias en hojas de papel separadas y luego colocando estas hojas una encima de la otra en capas sobre el molde vistas en seccion. Estas hojas se mueven hacia abajo en relación entre sí para simular cómo se cerraría el molde superior durante la carrera descendente de la prensa. Esto mostrará la posición relativa de la pieza a medida que se cierra el molde y durante la acción inversa a medida que se abre el ariete del molde.
Una característica común en todos los moldes de estampado progresivo es el material que transporta las piezas de una estación a otra a medida que pasa a través del molde. Este material es conocido por varios términos, como soporte, banda, banda, corbata, archivo adjunto, etc.
En este caso, utilizaremos el término transportista, del cual existen cinco estilos básicos:
Soporte sólido: todo el trabajo requerido se puede realizar en la pieza sin recortes preliminares. La parte se corta o se deja en blanco en la operación final.
Portador central: se recorta la periferia de la pieza; dejando solo una corbata estrecha cerca del centro de la parte. Esto permite que el trabajo se realice alrededor de la pieza. Un soporte central ancho permite recortar solo a los lados de la pieza.
Lanza y transporta en el centro: la tira se alinea entre las partes, dejando un área estrecha cerca del centro para transportar las piezas.
Esto elimina el material de desecho entre las partes.
Portadores externos: los portadores están unidos a los lados de la pieza para que se pueda trabajar en el centro de la pieza.
Portador de un lado: la parte se transporta completamente o parte del molde a través del molde con el portador solo en un lado. Esto permite trabajar en tres lados de la pieza.
El tipo o la forma del portador variará según lo que requiera la pieza a medida que avanza de una estación a otra en el molde. El ancho del stock se puede dejar sólido si no se requiere movimiento del material de la pieza durante el cierre del molde o se puede hacer una muesca para crear uno, dos o incluso tres portadores entre las piezas.
Los soportes pueden ser rectos, formar un patrón de zig-zag o tener bucles entre las partes dependiendo de dónde estén disponibles los puntos de fijación a la parte o para acomodar cualquier espacio libre que pueda requerir el herramental del molde. A medida que la pieza se forma, brida o dibuja en una carcasa, el portador puede tener que moverse hacia los lados o hacia arriba y hacia abajo a medida que el molde se cierra y se abre.
Cuando las operaciones de molde hacen que el transportador se mueva, generalmente será necesario flexionarlo o estirarlo. Independientemente de la flexión del portador, su función clave es mover las piezas lo suficientemente cerca de la siguiente estación para que los pilotos, medidores y localizadores puedan colocar las piezas en su ubicación precisa a medida que se cierra el molde.
Si el soporte adquiere un estiramiento permanente, las partes pueden avanzar demasiado para caber en la siguiente estación, o en el caso de que el molde tenga dos soportes, un soporte puede desarrollar un estiramiento permanente sin estiramiento en el otro soporte. Esto creará una curvatura en el borde de la tira, haciendo que gire hacia un lado. Esto da como resultado una mala ubicación de la parte.
Un portador estirado se puede acortar a su longitud correcta colocando un hoyuelo en el portador. Si un transportador central o un transportador de un lado desarrolla una curvatura, la tira se puede enderezar al formar hoyuelos o marcar un lado del transportador. Construya los hoyuelos y los golpes de puntuación para que se ajusten fácilmente lateralmente para la posición y verticalmente para la profundidad.
La inclinación del borde del material a medida que se entrega desde la bobina puede hacer que la tira se una a los medidores que guían el material durante el ciclo de alimentación. Esta unión puede hacer que los portadores se doblen, lo que da como resultado alimentaciones cortas. A menudo ayuda a aliviar el borde de guía de los medidores entre estaciones y tener un control más estricto en la estación de trabajo.
Otra opción es eliminar la comba recortando ambos lados del material al comienzo del molde. Al agregar paradas al final de estas muescas de corte, se pueden usar como muescas de control de tono para evitar la sobrealimentación progresiva.
Perfil de operador óptimo
El perfil óptimo del operador se ve afectado por algunas de las siguientes condiciones:
Espacio disponible entre piezas: intente mantener los transportadores dentro del ancho de stock y el paso requerido para el espacio en blanco. Si esto no es posible, entonces el diseñador debe aumentar el ancho y / o la progresión del material para proporcionar un espacio de transporte adecuado.
Puntos de fijación a la parte: Si se usan dos transportadores, trate de mantener el perfil y la longitud de los transportadores algo iguales para que cualquier efecto de flexión del transportador esté cerca de ser equilibrado.
Liquidación para bloques de punzón y troquel: Los bloques de perforación que se extienden por debajo del stock o los bloques de troquel que se extienden por encima del stock cuando se cierra el troquel requerirán autorización en relación con las piezas y los transportadores. Si un bucle del portador interfiere con los bloques, es posible formar el bucle vertical para proporcionar espacio libre.
Espesor del material: Las piezas grandes con material delgado pueden requerir cuentas de refuerzo para agregar resistencia al portador para la alimentación del stock. Otro método de rigidez y guía de la tira es lancear y rebordear el borde del material, que también puede usarse como una muesca de progresión.
El total de la tira: Las piezas pesadas en moldes largos requieren más fuerza para empujar la tira a través del molde. Sin embargo, el peso suele ser material grueso, y el material grueso es más rígido que el material delgado. Como regla general, portadores flexibles para
los materiales de 0.020 pulg. a 0.060 pulg. tienen aproximadamente 3/16 pulg. a 5/16 pulg. de ancho. Para espesores de stock por encima y por debajo de este rango de espesores
ancho es un "mejor juicio".
Dependiendo de todos los factores de moho involucrados, en condiciones normales los portadores deben tener un ancho constante para toda su longitud, pero especialmente en el área de flexión. Como casi todos los alimentadores de existencias empujan el material a través del molde en lugar de tirar del material, el transportador debe ser lo suficientemente fuerte como para empujar las piezas a través del molde.
Un interruptor de detección accionado por una alimentación completa de la tira a la salida del molde puede detectar pandeo. Si la acción del molde durante el cierre o la apertura de la prensa requiere que los soportes se flexionen, diseñe el soporte con bucles que sean lo suficientemente largos como para flexionarse sin romperse, pero aún lo suficientemente fuertes como para alimentar todas las partes a su progresión completa. Si dos portadores flexibles no son lo suficientemente fuertes como para alimentar la tira, considere tres portadores.
Intenta hacer que los radios en bucles flexibles sean tan grandes como sea práctico. Las esquinas afiladas o los radios pequeños concentrarán el estrés de la flexión, lo que lo convierte en el primer punto de fractura durante la flexión del soporte. También evite cualquier escalón o muesca en los bordes del transportador.
Almohadillas de presión superior
Debido al tamaño o la función, muchos moldes progresivos requieren dos o más almohadillas de presión en el molde superior. Cada uno puede requerir una distancia de viaje diferente para realizar el trabajo en la estación de moldeo individual, como recortar, formar o dibujar.
Sin embargo, las almohadillas de presión superiores a menudo se usan para empujar los levantadores de material hacia abajo presionando contra la tira, lo que empuja los levantadores hacia abajo. En esta situación, todas las almohadillas de presión que empujan a los levantadores de material hacia abajo deben tener la misma distancia de recorrido. Si las almohadillas de presión superiores recorren diferentes distancias, la tira no se empujará hacia abajo de manera uniforme. Esto puede extraer partes adyacentes de la progresión, lo que dificulta la ubicación de las partes en su posición de estación adecuada después del ciclo de alimentación.
Si la parte requiere que se forme una brida, el soporte de la parte debe tener un bucle flexible para permitir la respiración vertical de la parte o proporcionar un punzón / almohadilla presurizada con el mismo recorrido que las otras almohadillas de presión. La fuerza requerida por el punzón / almohadilla presurizada debe ser adecuada para formar las bridas hacia arriba durante la carrera descendente mientras el punzón / almohadilla está en la posición extendida. Esto evita que la tira respire verticalmente cuando se empuja hacia abajo desde el nivel de alimentación hasta el nivel de trabajo normal.
Cuando la tira alcanza el nivel de trabajo, el punzón / almohadilla presurizada detiene su movimiento hacia abajo mientras el molde superior continúa hacia abajo para perforar, recortar, rebordear hacia abajo y otras operaciones. Se pueden usar resortes o cilindros de nitrógeno para la presión en estas estaciones de punzonado / almohadilla presurizadas, pero deben tener suficiente fuerza de precarga para formar las bridas hacia arriba y colapsar la almohadilla de agarre inferior antes de que el punzón / almohadilla superior retroceda.
tracción Instancia
Tracción Instancia se producen cuando se cambia material de banda de un plano a una forma cilíndrica. Durante la operación de extracción, el "diámetro" de la pieza en bruto se reduce a la "circunferencia" de la carcasa. A medida que se reduce la circunferencia durante el flujo de material hacia adentro, la porción externa del material entra en compresión lateral o de borde.
Cuando esta compresión se vuelve demasiado grande para que el material permanezca plano, comienza a doblarse o arrugarse. Para evitar esto, se permite que el material fluya en un espacio controlado entre un anillo de tracción y una almohadilla de presión. Las dos causas principales de falla en el dibujo de una carcasa son exceder el porcentaje de que el blanco (o la carcasa) se reduce en diámetro y un radio de anillo de extracción incorrecto.
Hay un límite de cuánto fluirá el metal hacia adentro cuando se dibuja desde el diámetro de la pieza en bruto hasta el primer diámetro de extracción y desde un diámetro de carcasa estirado a un diámetro de carcasa más pequeño. Esto se expresa como un porcentaje de reducción de sorteo. El porcentaje máximo de reducción está limitado por el flujo de material hacia adentro que hace que el metal entre en compresión, lo que a su vez provoca una resistencia al flujo. Demasiada resistencia causará fracturas cerca de la tapa del caparazón, que es el área más débil en tensión.
El porcentaje de reducción varía con el espesor del metal. Por ejemplo, para una pieza en bruto de acero de embutición profunda, el porcentaje de reducción al primer diámetro de la carcasa de embutición varía del 32 por ciento para 0.015 pulgadas. material grueso al 48 por ciento para 0.125 pulg. material grueso
Hay un radio de extracción mínimo y máximo en el anillo de extracción que controlará el flujo de material. Para piezas de acero de embutición profunda, el radio correcto varía de 5/32 pulg. mínimo a 1/4 pulg. máximo para 0.015 pulg. stock y 11/32 pulg. mínimo a 15/32 pulg. máximo para 0.125 pulg. valores.
Si el radio es demasiado pequeño, el metal no fluirá bien, lo que aumenta la resistencia al flujo, causando adelgazamiento excesivo o fracturas cerca de la tapa de la copa. Si el radio es demasiado grande, el metal se arrugará después de dejar el punto de pellizco entre el anillo de estiramiento y la almohadilla de presión, y antes de que se forme en la pared vertical de la copa.
La tendencia normal es hacer que el radio sea demasiado pequeño porque "es fácil hacer el radio más grande durante la prueba de troquel y es difícil hacer un radio más pequeño". El resultado es que se aplica una tensión innecesaria en la copa, lo que resulta en un adelgazamiento o fractura excesiva. Muchas veces, el problema de un porcentaje incorrecto de reducción o radio de extracción incorrecto en la primera estación de extracción no aparecerá en la primera estación de extracción, sino en una estación de redibujo posterior, con el resultado de que se dedica un tiempo considerable a tratar de arreglar la estación incorrecta .
Un troquel progresivo realiza una serie de operaciones fundamentales de chapa en dos o más estaciones del troquel durante cada golpe de prensa. Estas operaciones simultáneas producen una parte de una tira de material que se mueve a través de la matriz. Cada estación de trabajo realiza una o más operaciones de troquel, pero la tira debe moverse desde la primera estación a través de cada estación siguiente para producir una pieza completa. Los portadores, que consisten en una o más tiras de material que quedan entre las partes, proporcionan el movimiento de las partes de una estación de troquel a la siguiente. Estas tiras transportadoras están separadas de las partes en la última estación de troquel.
Hay seis elementos que deben abordarse al diseñar y construir un molde progresivo para maximizar su rendimiento:
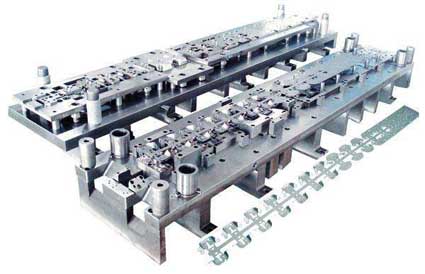
Interpretando la parte impresa
Material de partida en el molde
Elevadores de parte y alimentación de parte
Portadores de piezas flexibles
Almohadillas de presión superior
Conchas dibujadas.
Interpretando la impresión de la pieza
El primer paso en el diseño adecuado de un molde progresivo es analizar correctamente la impresión de la pieza. El diseñador de la herramienta debe interpretar la impresión para determinar la función de la pieza buscando cosas como el tipo de material, las superficies críticas, el tamaño y la ubicación del agujero, la ubicación de las rebabas, los requisitos de dirección del grano, el acabado de la superficie y otros factores.
El diseñador del molde debe comprender bien la pieza, especialmente si tiene formas y contornos irregulares. Sin embargo, las impresiones modernas dibujadas por computadora hacen que esto sea más difícil porque los datos de las piezas dibujadas por computadora se pueden descargar directamente a la computadora de diseño de moldes. Como resultado, el diseñador puede no familiarizarse completamente con las características importantes de las piezas.
Además, muchas partes dibujadas por computadora son más difíciles de entender, porque a menudo, solo se muestra una superficie y puede ser la superficie interior o exterior. Los dibujos por computadora a menudo muestran todas las líneas, incluidas las características ocultas, como líneas continuas en lugar de líneas de puntos. Esto conduce a errores de interpretación, lo que a su vez conduce a errores en la construcción del molde.
Para comprender mejor las formas complejas de las piezas, es útil construir un modelo "a la vista" de la pieza utilizando cera en láminas, revestimientos de goma o modelos de madera. La precisión dimensional no es crítica para estos modelos, ya que se utilizan principalmente para visualizar la pieza. Las pieles de goma y la cera en láminas también se pueden usar para desarrollar formas de preformas y para desarrollar las mejores posiciones para la pieza a medida que pasa a través de cada operación de molde en el molde progresivo.
Material de partida en el molde
Se debe tener cuidado para garantizar que la tira se inicie correctamente en el molde. La ubicación incorrecta del extremo de plomo de la tira hará más daño al molde en los primeros 10 golpes de la prensa que los siguientes 100,000 golpes.
Los medidores de "entrada" deben tener cables grandes y una repisa para soportar el extremo de la tira de la bobina cuando se inserta en el molde. Los cables grandes en los medidores son importantes para que la persona encargada de la configuración del molde no tenga que alcanzar el molde, así como para minimizar el tiempo requerido para comenzar una nueva tira en el molde. Además, un calibre debe ser ajustable para compensar la variación en el ancho de la tira.
La posición del borde de ataque de la tira es crítica para la primera carrera de prensado, y debe determinarse para cada estación de moldeo para asegurar que los punzones perforadores no corten agujeros parciales en el borde de ataque. Esto podría causar la desviación del punzón o provocar un corte parcial con punzones de recorte, lo que puede provocar una carga lateral desequilibrada a medida que la tira pasa a través del molde. Cualquiera de estas condiciones puede dar como resultado un cambio en la relación de punzón a molde que puede causar el cizallamiento de los punzones.
La ubicación inadecuada del borde de ataque de la tira también puede dar como resultado una condición de formación o brida desequilibrada que puede desplazar el molde superior en relación con el molde inferior. Se deben requerir tacones para absorber esta carga lateral, particularmente cuando se forman materiales gruesos.
Una muesca de paso y una parada de paso pueden proporcionar un punto físico para ubicar y controlar el borde de ataque de la tira. Las etiquetas de latón o las ranuras de los marcadores también pueden proporcionar una ubicación visual, pero no son tan precisas ni tan efectivas como una parada de muesca de inclinación. Se puede evitar que la prensa funcione con una alimentación corta o sobrealimentada montando el tope de paso en un pivote y monitoreándolo con un interruptor de límite
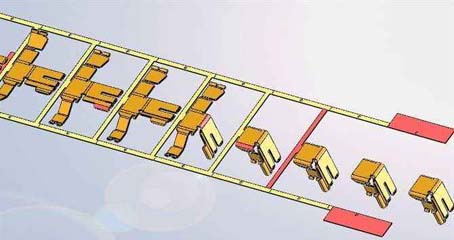
Piezas Lifters y piezas de alimentación
Los moldes progresivos a menudo requieren que la tira se levante del nivel normal de trabajo del molde al nivel de alimentación antes de que tenga lugar la alimentación de la tira. Esto puede variar desde una pequeña cantidad, para eliminar las rebabas de corte y perforación, hasta varias pulgadas para permitir que las formas de las piezas eliminen el molde.
Normally, all lifters should rise to the same height so that the strip is supported in a level plane during forward feed. The strip must not sag between lifters; otherwise parts will be pulled out of their correct station location spacing. Bar lifters provide good support and are better than spring pins or round lifters notched on one side of the strip.
Normalmente, todos los levantadores deben elevarse a la misma altura para que la tira se sostenga en un plano nivelado durante la alimentación hacia adelante. La tira no debe hundirse entre los levantadores; de lo contrario, las piezas se extraerán del espacio correcto de ubicación de la estación. Los elevadores de barra brindan un buen soporte y son mejores que los pasadores de resorte o los elevadores redondos con muescas en un lado de la tira.
A menudo, un buen sistema elevador de barras permite velocidades de prensa más altas porque se eliminan los problemas de alimentación. Aunque el costo inicial es más que los levantadores redondos, el rendimiento es mejor y se reduce el tiempo de configuración.
Las condiciones de medición y levantamiento pueden simularse durante el diseño del molde cortando un trozo de papel transparente al ancho de la tira. El borde anterior del papel se coloca sobre la vista en planta del diseño del molde en el lugar donde se colocará la tira para el primer golpe de prensado. Luego, el papel se marca con todas las operaciones que se realizarán en la primera estación de moldes, por ejemplo, muescas y perforaciones. La tira de papel luego se mueve a la segunda estación en el dibujo y se marcan las operaciones tanto para la primera como para la segunda estación. Este proceso se repite a través de todas las estaciones de moldes para ilustrar cómo se verá la tira de parte real cuando se inicie en el molde y ayuda a determinar la idoneidad de los medidores y levantadores.
Portadores de piezas flexibles
Para transportar la tira de una estación a la siguiente en un molde progresivo, debe dejarse algo de material entre las partes de la tira. Este material de soporte puede ser sólido en todo el ancho de la tira, o puede ser una o más cintas estrechas de material, vea la barra lateral de los soportes de parte.
Muchas partes requieren que el borde de la pieza en bruto fluya hacia adentro durante las operaciones de embridado, conformado o estirado. Esto puede requerir que el transportador se mueva lateralmente o se flexione verticalmente, o ambos, durante la operación del molde. Se debe proporcionar un bucle flexible en el transportador para permitir la flexión y el movimiento de la pieza sin extraer las partes adyacentes de su posición.
Otra preocupación es la "respiración" vertical de las piezas en las estaciones de moldes durante el cierre y la apertura del molde en la carrera de la prensa. Por ejemplo, la respiración vertical tiene lugar entre las estaciones de extracción de partes que requieren más de una extracción para completar la parte. La respiración vertical también se produce cuando se forma una brida "hacia arriba" en una estación de moldeo progresiva adyacente a estaciones que usan almohadillas de presión superiores para mantener presionadas las partes adyacentes.
Es importante tener en cuenta la flexión del soporte durante la carrera ascendente de la prensa, así como durante la carrera descendente porque la acción puede ser diferente. Esto se puede simular en la etapa de diseño haciendo un esquema de la sección transversal de la pieza, las almohadillas de presión y los aceros montados en estacionarias en hojas de papel separadas y luego colocando estas hojas una encima de la otra en capas sobre el molde vistas en seccion. Estas hojas se mueven hacia abajo en relación entre sí para simular cómo se cerraría el molde superior durante la carrera descendente de la prensa. Esto mostrará la posición relativa de la pieza a medida que se cierra el molde y durante la acción inversa a medida que se abre el ariete del molde.
Una característica común en todos los moldes de estampado progresivo es el material que transporta las piezas de una estación a otra a medida que pasa a través del molde. Este material es conocido por varios términos, como soporte, banda, banda, corbata, archivo adjunto, etc.
En este caso, utilizaremos el término transportista, del cual existen cinco estilos básicos:
Soporte sólido: todo el trabajo requerido se puede realizar en la pieza sin recortes preliminares. La parte se corta o se deja en blanco en la operación final.
Portador central: se recorta la periferia de la pieza; dejando solo una corbata estrecha cerca del centro de la parte. Esto permite que el trabajo se realice alrededor de la pieza. Un soporte central ancho permite recortar solo a los lados de la pieza.
Lanza y transporta en el centro: la tira se alinea entre las partes, dejando un área estrecha cerca del centro para transportar las piezas.
Esto elimina el material de desecho entre las partes.
Portadores externos: los portadores están unidos a los lados de la pieza para que se pueda trabajar en el centro de la pieza.
Portador de un lado: la parte se transporta completamente o parte del molde a través del molde con el portador solo en un lado. Esto permite trabajar en tres lados de la pieza.
El tipo o la forma del portador variará según lo que requiera la pieza a medida que avanza de una estación a otra en el molde. El ancho del stock se puede dejar sólido si no se requiere movimiento del material de la pieza durante el cierre del molde o se puede hacer una muesca para crear uno, dos o incluso tres portadores entre las piezas.
Los soportes pueden ser rectos, formar un patrón de zig-zag o tener bucles entre las partes dependiendo de dónde estén disponibles los puntos de fijación a la parte o para acomodar cualquier espacio libre que pueda requerir el herramental del molde. A medida que la pieza se forma, brida o dibuja en una carcasa, el portador puede tener que moverse hacia los lados o hacia arriba y hacia abajo a medida que el molde se cierra y se abre.
Cuando las operaciones de molde hacen que el transportador se mueva, generalmente será necesario flexionarlo o estirarlo. Independientemente de la flexión del portador, su función clave es mover las piezas lo suficientemente cerca de la siguiente estación para que los pilotos, medidores y localizadores puedan colocar las piezas en su ubicación precisa a medida que se cierra el molde.
Si el soporte adquiere un estiramiento permanente, las partes pueden avanzar demasiado para caber en la siguiente estación, o en el caso de que el molde tenga dos soportes, un soporte puede desarrollar un estiramiento permanente sin estiramiento en el otro soporte. Esto creará una curvatura en el borde de la tira, haciendo que gire hacia un lado. Esto da como resultado una mala ubicación de la parte.
Un portador estirado se puede acortar a su longitud correcta colocando un hoyuelo en el portador. Si un transportador central o un transportador de un lado desarrolla una curvatura, la tira se puede enderezar al formar hoyuelos o marcar un lado del transportador. Construya los hoyuelos y los golpes de puntuación para que se ajusten fácilmente lateralmente para la posición y verticalmente para la profundidad.
La inclinación del borde del material a medida que se entrega desde la bobina puede hacer que la tira se una a los medidores que guían el material durante el ciclo de alimentación. Esta unión puede hacer que los portadores se doblen, lo que da como resultado alimentaciones cortas. A menudo ayuda a aliviar el borde de guía de los medidores entre estaciones y tener un control más estricto en la estación de trabajo.
Otra opción es eliminar la comba recortando ambos lados del material al comienzo del molde. Al agregar paradas al final de estas muescas de corte, se pueden usar como muescas de control de tono para evitar la sobrealimentación progresiva.
Perfil de operador óptimo
El perfil óptimo del operador se ve afectado por algunas de las siguientes condiciones:
Espacio disponible entre piezas: intente mantener los transportadores dentro del ancho de stock y el paso requerido para el espacio en blanco. Si esto no es posible, entonces el diseñador debe aumentar el ancho y / o la progresión del material para proporcionar un espacio de transporte adecuado.
Puntos de fijación a la parte: Si se usan dos transportadores, trate de mantener el perfil y la longitud de los transportadores algo iguales para que cualquier efecto de flexión del transportador esté cerca de ser equilibrado.
Liquidación para bloques de punzón y troquel: Los bloques de perforación que se extienden por debajo del stock o los bloques de troquel que se extienden por encima del stock cuando se cierra el troquel requerirán autorización en relación con las piezas y los transportadores. Si un bucle del portador interfiere con los bloques, es posible formar el bucle vertical para proporcionar espacio libre.
Espesor del material: Las piezas grandes con material delgado pueden requerir cuentas de refuerzo para agregar resistencia al portador para la alimentación del stock. Otro método de rigidez y guía de la tira es lancear y rebordear el borde del material, que también puede usarse como una muesca de progresión.
El total de la tira: Las piezas pesadas en moldes largos requieren más fuerza para empujar la tira a través del molde. Sin embargo, el peso suele ser material grueso, y el material grueso es más rígido que el material delgado. Como regla general, portadores flexibles para
los materiales de 0.020 pulg. a 0.060 pulg. tienen aproximadamente 3/16 pulg. a 5/16 pulg. de ancho. Para espesores de stock por encima y por debajo de este rango de espesores
ancho es un "mejor juicio".
Dependiendo de todos los factores de moho involucrados, en condiciones normales los portadores deben tener un ancho constante para toda su longitud, pero especialmente en el área de flexión. Como casi todos los alimentadores de existencias empujan el material a través del molde en lugar de tirar del material, el transportador debe ser lo suficientemente fuerte como para empujar las piezas a través del molde.
Un interruptor de detección accionado por una alimentación completa de la tira a la salida del molde puede detectar pandeo. Si la acción del molde durante el cierre o la apertura de la prensa requiere que los soportes se flexionen, diseñe el soporte con bucles que sean lo suficientemente largos como para flexionarse sin romperse, pero aún lo suficientemente fuertes como para alimentar todas las partes a su progresión completa. Si dos portadores flexibles no son lo suficientemente fuertes como para alimentar la tira, considere tres portadores.
Intenta hacer que los radios en bucles flexibles sean tan grandes como sea práctico. Las esquinas afiladas o los radios pequeños concentrarán el estrés de la flexión, lo que lo convierte en el primer punto de fractura durante la flexión del soporte. También evite cualquier escalón o muesca en los bordes del transportador.
Almohadillas de presión superior
Debido al tamaño o la función, muchos moldes progresivos requieren dos o más almohadillas de presión en el molde superior. Cada uno puede requerir una distancia de viaje diferente para realizar el trabajo en la estación de moldeo individual, como recortar, formar o dibujar.
Sin embargo, las almohadillas de presión superiores a menudo se usan para empujar los levantadores de material hacia abajo presionando contra la tira, lo que empuja los levantadores hacia abajo. En esta situación, todas las almohadillas de presión que empujan a los levantadores de material hacia abajo deben tener la misma distancia de recorrido. Si las almohadillas de presión superiores recorren diferentes distancias, la tira no se empujará hacia abajo de manera uniforme. Esto puede extraer partes adyacentes de la progresión, lo que dificulta la ubicación de las partes en su posición de estación adecuada después del ciclo de alimentación.
Si la parte requiere que se forme una brida, el soporte de la parte debe tener un bucle flexible para permitir la respiración vertical de la parte o proporcionar un punzón / almohadilla presurizada con el mismo recorrido que las otras almohadillas de presión. La fuerza requerida por el punzón / almohadilla presurizada debe ser adecuada para formar las bridas hacia arriba durante la carrera descendente mientras el punzón / almohadilla está en la posición extendida. Esto evita que la tira respire verticalmente cuando se empuja hacia abajo desde el nivel de alimentación hasta el nivel de trabajo normal.
Cuando la tira alcanza el nivel de trabajo, el punzón / almohadilla presurizada detiene su movimiento hacia abajo mientras el molde superior continúa hacia abajo para perforar, recortar, rebordear hacia abajo y otras operaciones. Se pueden usar resortes o cilindros de nitrógeno para la presión en estas estaciones de punzonado / almohadilla presurizadas, pero deben tener suficiente fuerza de precarga para formar las bridas hacia arriba y colapsar la almohadilla de agarre inferior antes de que el punzón / almohadilla superior retroceda.
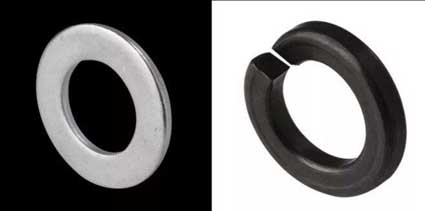
tracción Instancia
Tracción Instancia se producen cuando se cambia material de banda de un plano a una forma cilíndrica. Durante la operación de extracción, el "diámetro" de la pieza en bruto se reduce a la "circunferencia" de la carcasa. A medida que se reduce la circunferencia durante el flujo de material hacia adentro, la porción externa del material entra en compresión lateral o de borde.
Cuando esta compresión se vuelve demasiado grande para que el material permanezca plano, comienza a doblarse o arrugarse. Para evitar esto, se permite que el material fluya en un espacio controlado entre un anillo de tracción y una almohadilla de presión. Las dos causas principales de falla en el dibujo de una carcasa son exceder el porcentaje de que el blanco (o la carcasa) se reduce en diámetro y un radio de anillo de extracción incorrecto.
Hay un límite de cuánto fluirá el metal hacia adentro cuando se dibuja desde el diámetro de la pieza en bruto hasta el primer diámetro de extracción y desde un diámetro de carcasa estirado a un diámetro de carcasa más pequeño. Esto se expresa como un porcentaje de reducción de sorteo. El porcentaje máximo de reducción está limitado por el flujo de material hacia adentro que hace que el metal entre en compresión, lo que a su vez provoca una resistencia al flujo. Demasiada resistencia causará fracturas cerca de la tapa del caparazón, que es el área más débil en tensión.
El porcentaje de reducción varía con el espesor del metal. Por ejemplo, para una pieza en bruto de acero de embutición profunda, el porcentaje de reducción al primer diámetro de la carcasa de embutición varía del 32 por ciento para 0.015 pulgadas. material grueso al 48 por ciento para 0.125 pulg. material grueso
Hay un radio de extracción mínimo y máximo en el anillo de extracción que controlará el flujo de material. Para piezas de acero de embutición profunda, el radio correcto varía de 5/32 pulg. mínimo a 1/4 pulg. máximo para 0.015 pulg. stock y 11/32 pulg. mínimo a 15/32 pulg. máximo para 0.125 pulg. valores.
Si el radio es demasiado pequeño, el metal no fluirá bien, lo que aumenta la resistencia al flujo, causando adelgazamiento excesivo o fracturas cerca de la tapa de la copa. Si el radio es demasiado grande, el metal se arrugará después de dejar el punto de pellizco entre el anillo de estiramiento y la almohadilla de presión, y antes de que se forme en la pared vertical de la copa.
La tendencia normal es hacer que el radio sea demasiado pequeño porque "es fácil hacer el radio más grande durante la prueba de troquel y es difícil hacer un radio más pequeño". El resultado es que se aplica una tensión innecesaria en la copa, lo que resulta en un adelgazamiento o fractura excesiva. Muchas veces, el problema de un porcentaje incorrecto de reducción o radio de extracción incorrecto en la primera estación de extracción no aparecerá en la primera estación de extracción, sino en una estación de redibujo posterior, con el resultado de que se dedica un tiempo considerable a tratar de arreglar la estación incorrecta .
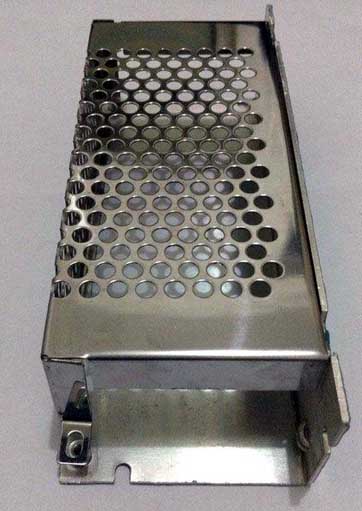