Fabricación de Piezas de Chapa
Producción de piezas de chapa: ¿qué métodos se utilizan?
La chapa es un material de estructura, grosor y forma muy diferentes. La chapa también se utiliza en todas partes. Las láminas se utilizan para techos, canalones, elementos de construcción de edificios, máquinas, dispositivos, vehículos y en muchas otras áreas de la economía. La multitud de usos de la chapa está relacionada con muchos métodos de su procesamiento, que permiten que el material se adapte a las necesidades y requisitos individuales del proyecto implementado.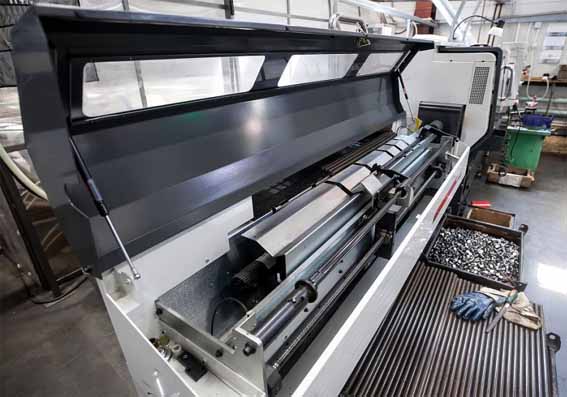
Producción de piezas de chapa de forma moderna
La producción moderna de piezas de chapa se lleva a cabo con la ayuda de máquinas tecnológicamente avanzadas, cuyo trabajo está controlado por computadora. Esto permite dar a las piezas de trabajo la forma, tamaño, textura y otras propiedades funcionales estrictamente definidas, lo que significa la posibilidad de crear un producto final perfectamente adaptado a los requisitos específicos. Las máquinas modernas también permiten realizar los elementos de chapa más complicados y complejos en términos de forma y construcción.Se utilizan muchos métodos diferentes de procesamiento de chapa en la fabricación de piezas de chapa. Uno de los más populares es el corte, que permite obtener una variedad de formas estrictamente definidas. Las hojas se pueden cortar utilizando diversas técnicas y máquinas. Uno de los métodos más eficaces y, al mismo tiempo, más antiguos es el corte con oxígeno con el uso de sopletes. El corte con oxígeno es ideal para mecanizar chapas gruesas. Las láminas más delgadas generalmente se cortan con tecnología láser y tecnología de punzonado. Un método menos común es el corte por arco de plasma o agua, que se lleva a cabo con la ayuda de máquinas debidamente programadas.
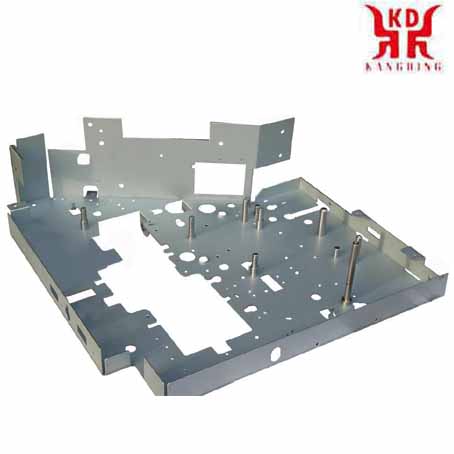
Otros métodos de trabajo de chapa utilizados en la fabricación de piezas de chapa
El método más común de procesamiento de chapa en los últimos años es el corte por láser. El uso de esta tecnología para el corte de chapa permite obtener cualquier forma, incluso las más complejas, y dimensiones perfectamente repetibles, imposible de conseguir con métodos manuales. El corte láser de chapa, sin embargo, requiere programas adecuados y la supervisión de un operador CNC experimentado que vela por el correcto desarrollo de todo el proceso.Otra forma de procesamiento de chapa es el corte con guillotina. Este método tradicional y bastante simple se utiliza para cortes de material simples donde el proceso y el producto no requieren ninguna precisión particular. Cortar con la guillotina no es tan preciso como otros métodos de corte de chapa más modernos. Su uso solo es económico si se producen grandes cantidades y formas simplificadas. Sin embargo, no será adecuado para la producción de piezas pequeñas que deban cortarse con mayor precisión.
La fabricación de piezas de chapa no solo incluye cortar el material en sí, sino también doblar las plegadoras, unir chapas y tratamientos superficiales como el recubrimiento en polvo y la pintura en húmedo. Los siguientes procesos se utilizan para unir láminas de metal: soldadura, soldadura por puntos, soldadura, toxinado, remachado, atornillado, etc. Los más populares son la soldadura por puntos y la soldadura. La soldadura por puntos permite conectar dos o más piezas de chapa metálica entre sí utilizando electricidad y presión.
Al soldar chapa, a su vez, el metal se somete a un tratamiento térmico mediante electricidad y se funde en los bordes donde se une el material sin aplicar presión. La soldadura se puede realizar manualmente o con máquinas o robots controlados por computadora. La soldadura láser también se utiliza para fines de soldadura, lo que permite una costura de soldadura muy estética y fuerte que ya no necesita decolorarse.
Las chapas soldadas suelen someterse a un tratamiento superficial como pintura, galvanizado, anodizado o similar y pueden utilizarse como productos acabados o semipiezas que se ensamblan posteriormente a otras máquinas y sistemas.
Algunos ingenieros tienen dificultades para diseñar correctamente piezas de chapa metálica para la fabricación. Aún así, notamos que hay ciertos problemas que aparecen con frecuencia en los modelos que nos han pedido que citemos. Con estos problemas en mente, ofrecemos esta lista. No es exhaustivo, pero abróchese el cinturón y observe qué hacen mal muchos de sus colegas cuando diseñan para chapa y envían una solicitud de presupuesto.
1. Uso de modelos 3D completos de una pieza sin pliegues
Este es probablemente el problema más básico que vemos. La hoja de metal es plana y debe doblarse, formarse, cortarse, someterse a láser y, a veces, engatusarse para obtener su forma final. Es un proceso muy práctico. Si diseña su pieza de chapa metálica como un objeto sólido, es importante que nos envíe un archivo CAD que parece doblado, pero que muestra dónde deben ir las curvas. En relación con esto, debido a que las materias primas son láminas de metal individuales, toda la pieza debe tener el mismo grosor de material en todas partes. Por ejemplo, si crea una pieza que utiliza aluminio de 0,125 pulgadas (3,175 mm) de grosor, toda la pieza deberá tener el mismo grosor.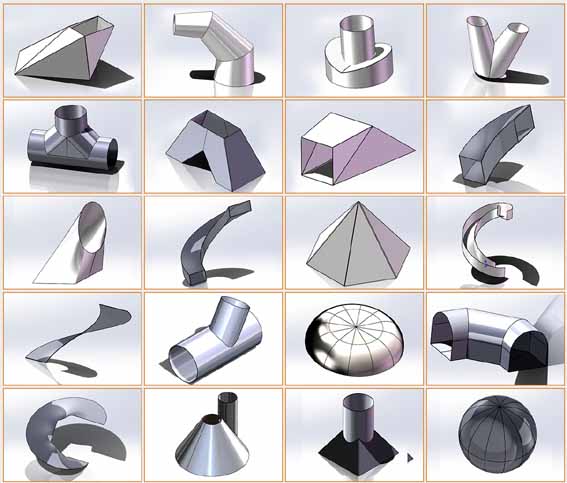
2. Colocación de entidades demasiado cerca de las líneas de plegado
Una forma rápida de crear dificultades durante la fabricación es colocar orificios, pestañas u otras características demasiado cerca de una curva. Entonces, ¿qué tan cerca puedes acercarte? Simplemente siga la regla de las 4T. Mantenga todas las características al menos 4 veces el grosor del material alejadas de las líneas de plegado. Por lo tanto, si su diseño nos dice que usemos cobre de 0.050 pulg. (1.27 mm), dé a su función al menos 0.200 pulg. (5.08 mm) de espacio libre. Si no lo hace, la pieza se deformará torpemente en la plegadora y nadie quiere eso.3. Diseño de esquinas de chapa perfectamente perpendiculares
Cuando se dobla una hoja de metal en una plegadora, la curvatura resultante no forma un ángulo perfecto de 90 grados. En cambio, la herramienta tiene una punta redondeada que agrega un radio a la curva. Si mide la longitud de esa área doblada y la divide por dos, obtendrá el radio de curvatura, una cifra que está definida por la herramienta que la hizo. Si el tamaño de esa curva es importante para usted, asegúrese de especificarlo en su modelo.El radio de curvatura interno más común (y nuestro predeterminado) es de 0,030 pulg. (0,762 mm). Una consideración importante para recordar es que el radio de curvatura externo, el que se forma en el lado de la matriz del juego de herramientas de la plegadora, es igual al grosor del material más el radio de curvatura interno.
A algunos diseñadores les gusta ser sofisticados y crear diferentes radios para cada doblez de una pieza. ¿Quiere ahorrar algo de dinero? Utilice el mismo radio para todas las curvas. Cuando su fabricante no tiene que cambiar las herramientas, eso le ahorra costos de mano de obra.
4. Olvidar incluir especificaciones detalladas de hardware en su archivo CAD
¿Conoce a alguien que quiera plazos de entrega más largos? Probablemente no. Recuerde siempre informarle a su fabricante qué tipo de hardware desea utilizar al incluir los detalles en la información de ensamblaje de nivel superior. Ya sea que se trate de una tuerca autoajustable como CLS-440-2, espárrago de cabeza empotrada como FHS-M5-15 u otro hardware, esto garantiza que obtendrá exactamente lo que desea en el lugar que espera. Para ahorrar tiempo y problemas, descargue y utilice los modelos de hardware de remache PEM.5. Elegir el acabado incorrecto (o no usar uno cuando lo necesita)
Generalmente, los acabados sirven para dos propósitos. Pueden proteger su pieza o pueden hacer que se vea mejor. Algunos hacen ambas cosas. Los acabados estéticos, los que se centran en la apariencia, no se centran en la protección contra la corrosión. Aún así, el recubrimiento en polvo ofrece cierta protección (a menos que un rasguño llegue al metal debajo). La serigrafía, por otro lado, se usa para agregar texto e imágenes a las partes y no ofrece protección alguna.Los acabados de conversión química están destinados a proteger sus piezas alterando las propiedades de las capas más externas. Por ejemplo, si desea usar acero en un ambiente corrosivo, considere elegir metal galvanizado o galvanizado, que ya tiene un recubrimiento protector de zinc. ¡Pero ten cuidado! No podemos soldar acero galvanizado debido a las peligrosas toxinas que emitiría. En cambio, podemos hacer las piezas de acero y agregar un recubrimiento de zinc después de soldar.
La conversión de cromato puede darle conectividad eléctrica a su pieza y proporciona una capa de imprimación a su pieza si desea pintar. La anodización puede agregar un toque de color metálico a sus piezas al mismo tiempo que las protege. Piense en esa linterna pequeña y colorida que posee.
A continuación, se ofrece un resumen útil de los acabados más comunes para chapa.
6. Selección de la chapa metálica incorrecta para el trabajo
Imagínese fabricar cientos de piezas de acero sin terminar destinadas a su instalación en un entorno marino salado. Sorprendentemente, hemos visto citas que solicitan precisamente eso. Ahórrese el dolor de las quejas de los clientes que recibirá cuando sus piezas se corroan y considere estos factores al seleccionar la chapa adecuada:Desgaste esperado de su parte por el uso diario
Protección contra la corrosión
Manufacturabilidad
Apariencia cosmética
Propiedades mecánicas (resistencia a la tracción, límite elástico, ductilidad, etc.)
Conductividad (para aplicaciones eléctricas)
Esta práctica tabla puede ayudar.
7. No considerar la resistencia del canal en U
Al diseñar canales en U, siempre piense en la resistencia del material que está utilizando y la facilidad con la que se puede doblar. En KANGDING, lo más estrecho no funciona para nosotros debido a nuestras herramientas. Si tuviéramos herramientas más estrechas, podríamos fabricar canales en U más estrechos. La conclusión es que es una buena práctica cuando trabaje con nosotros mantener al menos una relación de ancho a alto de 2: 1 para sus canales en U. Si necesita un canal más estrecho, considere un ensamblaje soldado o remachado.8. Diseño de requisitos de soldadura poco realistas
¿Alguna vez ha intentado soldar una costura dentro de una caja cerrada? ¿No? Nosotros tampoco. Asegúrese de que sus requisitos de soldadura sean alcanzables de manera realista. Es importante recordar que si un soplete de soldadura no puede acceder a una costura, la soldadura no se puede realizar. Recomendamos encarecidamente diseñar de modo que todas las soldaduras se realicen en el exterior de la pieza.El metal se derrite a altas temperaturas, por lo que necesita espesores de material que puedan soportar el calor extremo. El grosor mínimo del material para soldar es de 0.040 pulg. (1.016 mm) para garantizar que la soldadura no termine en un lío impío de metal derretido.
Finalmente, en sus modelos, indique siempre la necesidad de soldaduras mediante una función o nomenclatura de soldadura. Nunca encuadre las esquinas para indicar soldadura.
Ningún consejo de diseño puede cubrir todos los errores de chapa que hemos visto, pero esta colección de "lo mejor de" es un comienzo. Eche un vistazo a nuestras pautas de diseño de chapa metálica para que siga avanzando en la dirección correcta.