Diseno de tecnologia de procesamiento de torno CNC de eje multiproposito
Resumen: Las partes del eje multipropósito están diseñadas. Este eje tiene un arco circular, una ranura de retracción de proceso, una ranura de retracción del hilo, un hilo, un hilo cónico, un orificio interno y un arco interno. El material es de acero 45. Para este diseño de ejes múltiples, se utilizará el método de torneado "torneado y acabado rotatorio". A saber, las dos caras frontales, el círculo exterior, el hilo, el cono exterior, las ranuras, el arco y los agujeros de perforación se dividen respectivamente en siete pasos para el mecanizado y acabado en bruto.
Este diseño se ocupa principalmente del análisis de procesos de mecanizado CNC y del procesamiento de dibujos de piezas específicas. En primer lugar, se realizó una breve introducción a la tecnología de mecanizado NC, y luego se realizó el análisis de mecanizado NC de acuerdo con el diagrama de piezas.
Primero, de acuerdo con el proceso de mecanizado, la cantidad de corte y otros factores relevantes del material de la pieza, la herramienta, el mango y las características del contorno de las piezas se utilizan para determinar que se requieren 5 herramientas.
En segundo lugar, programe los gráficos del dibujo de la pieza. Esta parte es un eje múltiple, el contorno exterior se compone de una línea recta, un corte inferior, un arco y un hilo. Dentro del extremo izquierdo de la pieza, se perforan un agujero cónico y un arco interior. En el proceso de mecanizado, la pieza de trabajo debe perforar y luego girar el arco interno.
tercero, cuando la configuración de la herramienta taladrar orificio, es necesario volver a referirse al punto de referencia primero. La posición de la herramienta se usa para corregir esto, de modo que la posición de la herramienta y el punto de cambio de herramienta coincidan para determinar el sistema de coordenadas de programación y el origen de programación. Se compiló el programa de mecanizado NC. Finalmente, la simulación y el procesamiento de las partes del eje se realizaron con software de simulación de programación.
Palabras clave: programación CNC, plan de mecanizado, cantidad de corte, programa de mecanizado
Análisis de tecnología de procesamiento de partes
Análisis de tecnología de procesamiento de partes
1.1 Análisis del proceso de dibujo de piezas
como muestra la imagen:
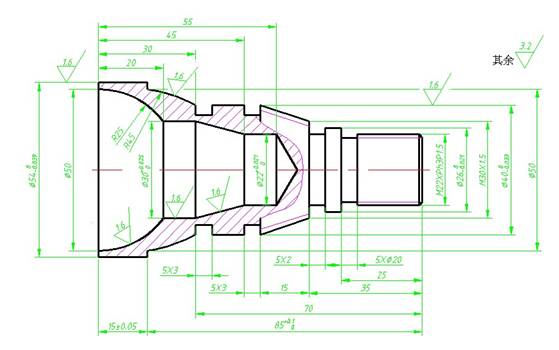
Análisis de estructura de partes:
En el diagrama, podemos ver que esta parte está formada por superficie cilíndrica, orificio interior, superficie interna del cono, superficie circular del arco, ranura, hilo, etc. La forma del contorno de la parte giratoria de la pieza que gira es más compleja y requiere un mecanizado de dos extremos. La precisión de mecanizado y la calidad de la superficie de las piezas son muy altas. Las partes importantes de mecanizado radial de la pieza son c54-0.039 secciones cilíndricas de 0 mm (rugosidad superficial Rɑ = 1,6 μm). R45 está conectado a un arco circular, c40-0.033 0 sección cilíndrica, Ф22 + 0.021 0 y el radio del orificio interior del orificio interior de R25. Las piezas cumplen los requisitos para el dimensionamiento del mecanizado NC, y la descripción del contorno es clara y completa. El material de la pieza es acero No.45 y el espacio en blanco es ф60mm * 110mm.
1.2 Análisis de los requisitos técnicos de las piezas
Programación de condiciones de fabricación de bajo volumen. No está permitido modificar el plano con tela de esmeril y paleta. Este es un requisito para la alta precisión de los aviones. Las tolerancias no especificadas, de acuerdo con GB1804-M, el tratamiento térmico, templado y templado, HRC25-35, no indica la parte rugosidad, el acabado es Ra6.3, el tamaño del embrión es mm60mm * 110mm.
1.3 Análisis de partes en blanco y materiales
(1) Análisis de materiales
En el mecanizado de esta parte del eje, la fuerza de corte entre la herramienta y la pieza de trabajo es grande. La maquinabilidad, resistencia, dureza, plasticidad, corte en frío y las propiedades mecánicas del material de la pieza de trabajo están relacionadas con el material de la pieza de trabajo. Por lo tanto, 45 acero fue seleccionado como el material para el eje. La composición química del acero 45 contiene C0.42% a 0.50%, Si0.17% a 0.37%, Mn0.50 a 0.80%, P≤0.035%, S≤0.035%, Cr≤0.25% y N≤0.25% . Cu≤0.25%. Requisitos de dureza para acero 45 en frío, acero laminado en caliente, diámetro de indentación no inferior a 3,9, dureza Brinell no inferior a 241HB, diámetro de indentación de acero recocido no inferior a 4,4, dureza Brinell no inferior a 187HB, 45 propiedades mecánicas de acero: δs ≥ 335 Mpa, δb ≥ 600 Mpa, ≥ ≥ 40%, Ak ≥ 47J. Herramienta de carburo de acero relativamente mecanizado 45 1.0, herramienta de acero de alta velocidad 1.0, 45 requisitos de herramientas de acero económico razonable también son razonables, 45 de acero es ampliamente utilizado, principalmente para la fabricación de turbinas de vapor, compresores, engranajes de fabricación de piezas de bomba, pin de pistón de eje y otro partes. De acuerdo con los datos anteriores, es adecuado para el mecanizado de este eje.
(2) Análisis de espacios en blanco
Los espacios en blanco de las partes del eje incluyen barras, forjas y piezas fundidas. Forjas: adecuado para piezas con alta resistencia y formas simples. Piezas de gran tamaño debido a las restricciones de los equipos; generalmente se utiliza forjado en matriz abierta; Piezas medianas y pequeñas piezas forjadas opcional; Las piezas rígidas con formas complejas no son adecuadas para el forjado libre y son adecuadas para espacios en blanco con formas complejas. Los espacios en blanco forjados de piezas de acero tienen propiedades mecánicas más altas que las barras de acero y las piezas de fundición de acero. De acuerdo con la forma estructural y el tamaño del contorno exterior de la parte del eje, se utilizan piezas forjadas. El blanco de esta pieza debe adoptar forjado, serrado por barra y forjar en blanco a Φ60X110mm, después de forjar el acero para obtener una estructura fibrosa uniforme, mejorar sus propiedades mecánicas, pero también aumentar la proporción de piezas y espacios en blanco, reduciendo el consumo de material.
2.4 Selección de equipos de procesamiento de piezas
2.4.1 Tipos de herramientas de máquina
El torno CNC puede completar automáticamente el mecanizado de las superficies cilíndricas internas y externas, superficies cónicas, superficies de arco, etc., en piezas giratorias como ejes o discos, y puede realizar operaciones tales como ranurado, perforación y expansión. De acuerdo con los requisitos técnicos de las piezas, se pueden seleccionar tornos CNC económicos, y generalmente se utilizan servosistemas de lazo semicerrado en forma de motores paso a paso. Estos tornos tienen una estructura simple y un precio relativamente bajo. Este tipo de torno está equipado con un mandril autocentrante de tres mordazas, un contrapunto común o un contrapunto hidráulico controlado numéricamente, que es adecuado para hacer girar piezas de eje más largas. El torno CNC horizontal se selecciona de acuerdo con los requisitos de la configuración del husillo. Los tornos CNC tienen una alta precisión de mecanizado, pueden realizar interpolaciones lineales y circulares, los tornos CNC tienen buena rigidez, alta precisión en la fabricación y configuración de herramientas, y se pueden compensar manual y exactamente de forma manual y automática, y se pueden mecanizar piezas con altos requisitos de precisión dimensional. Puede procesar superficies y tamaños particularmente difíciles con cuerpos de giro difíciles de controlar con formas de contorno, y puede girar fácilmente la superficie cónica del cono y los hilos cilíndricos interno y externo para mantener la precisión del mecanizado y mejorar la eficiencia de producción. Por lo tanto, es muy favorable para el procesamiento.
De acuerdo con la estructura, especificación y precisión de los componentes multieje, la selección de un centro de torneado dará como resultado un cierto desperdicio funcional, por lo que se elige el torno CNC económico, por lo que se selecciona el torno CNC SSCK20 / 500.
2.4.2 Precisión de la máquina herramienta
Los metales comúnmente utilizados, con excepción de los aceros templados con precisión de mecanizado de IT7 a IT8 y Ra 0.8 a Ra 1.6 μm, se pueden completar con dos pasos de desbaste y acabado. Precisión de procesamiento de grado IT5 ~ IT6, Ra0.2 ~ Ra 0.63 μm, además del acero templado de metal comúnmente utilizado, se pueden utilizar tornos CNC de precisión, desbaste → semiacabado → carro fino → procesamiento de programa de carro fino. La precisión de mecanizado es más alta que la de los metales usados comúnmente que no sean los aceros templados como IT5 y Ra <0.08μm, se pueden usar tornos CNC de precisión, y el mecanizado puede realizarse según el desbaste, semiacabado, acabado y torneado de precisión. Para materiales difíciles de girar como el acero endurecido, se puede usar el método de desbaste y semiacabado antes del enfriamiento rápido, y la molienda se realiza después del enfriamiento. Por lo tanto, de acuerdo con los requisitos del plano de piezas, la precisión del torno CNC SSCK20 / 500 es adecuada para la precisión del eje múltiple.
Principales parámetros técnicos del torno CNC SSCK20 / 500
2.5 Determinación del Esquema de Posicionamiento y Fixture de la Pieza de Trabajo
2.5.1 Determinar el esquema de sujeción
Utilice el mandril autocentrante de tres mandíbulas para sujetar el círculo externo áspero de las piezas y determine las partes para extender la longitud adecuada (debe tenerse en cuenta la distancia límite de la máquina herramienta). Las piezas deben mecanizarse en ambos extremos, por lo que se debe considerar la posición de las dos sujeciones, teniendo en cuenta que los pasos en el lado izquierdo de los 54 mm x 15 mm se pueden usar para sujetar. Por lo tanto, el extremo derecho se procesa primero, luego se sujeta el cabezal del hilo de M22 Ph3P1.5 y se mecaniza el arco interno del escalón de 54 mm x 15 mm, el orificio interior 22 y el R25.
2.5.2 Referencia de posicionamiento
El posicionamiento y la referencia de la pieza de trabajo deben ser consistentes con la base de diseño, y se debe evitar el sobre posicionamiento. Lo mejor es elegir "un lado y dos clavijas" como el punto de referencia de la pieza de trabajo con la caja, y el punto de referencia de posición debe ubicarse cuidadosamente en la herramienta de control numérico de la máquina. La pieza de trabajo es un eje sólido con un agujero cónico de 30 grados en el extremo. Debido a que la longitud del eje no es muy larga, la cara extrema derecha de la pieza de trabajo y el círculo exterior de 48 se utilizan como referencia para el posicionamiento. Use un mandril normal de tres garras para sujetar la pieza de trabajo. Tome el centro de la cara frontal derecha de la pieza de trabajo según se coordina el origen de la pieza de trabajo. El punto de la herramienta está en (100.100). Dado que toda la superficie de la pieza necesita ser mecanizada, el círculo exterior y una cara final deben usarse como referencia aproximada, y luego el procesamiento debe realizarse a través del principio de referencia mutua. Siga el principio de "coincidencia de referencia". Seleccione la superficie exterior del lado izquierdo del espacio en blanco al mecanizar el extremo derecho, y seleccione la superficie del círculo externo derecho cuando procese el lado izquierdo, para mostrar que el punto de referencia de posición es la línea central del eje.
2.6 Selección de herramientas de corte y capacidad de corte
2.6.1 Selección de herramienta
El procesamiento de esta parte,
(1) Para el torneado áspero y fino de los extremos exterior y plano, se adopta el cortador de desviación izquierda de carburo cementado de 35 grados.
Elegir orden = evitar la interferencia entre la cara del rastrillo accesorio y el contorno de la pieza de trabajo, el ángulo de desviación auxiliar no debe ser demasiado pequeño. Elija Kr = 35.
(2) cortadores de ranura,
(3) La rosca del tornillo se elige con herramienta de torneado de rosca externa de carburo de 60 grados, y el radio de la punta debe ser menor que el radio de filete mínimo del perfil, tomando re = 0,15 a 0,2 mm.
(4) Mecanizar el agujero izquierdo con un taladro de 22 mm
(5) herramienta de torneado interno.
La elección de la herramienta es uno de los contenidos importantes en el diseño del proceso de control numérico. La elección racional de la herramienta no solo afecta la eficiencia de mecanizado de la máquina herramienta, sino que también afecta la calidad del mecanizado. La elección de la herramienta generalmente considera la capacidad de mecanizado, el contenido del proceso y el material de la pieza de trabajo de la máquina herramienta.
En comparación con el método de torneado tradicional, el torneado CNC tiene un mayor requerimiento de herramientas. No solo requiere alta precisión, buena rigidez, alta durabilidad, sino que también requiere estabilidad dimensional y una fácil instalación y ajuste. Esto requiere el uso de nuevos materiales de alta calidad para fabricar herramientas de mecanizado CNC y optimizar los parámetros de la herramienta.
La herramienta seleccionada se muestra en la figura a continuación:
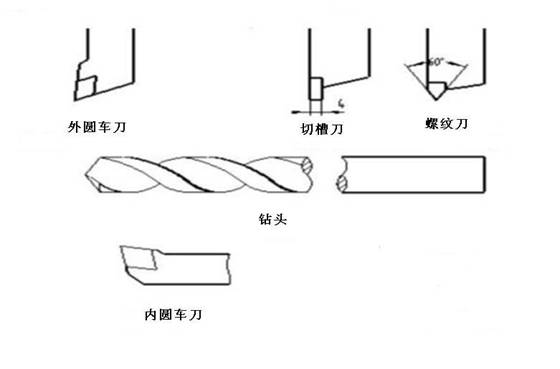
Cylindrical turning tools, grooved knives, thread knives, drill bits, internal turning tools.
Herramientas de torneado cilíndricas, cuchillas acanaladas, cuchillas de rosca, brocas, herramientas de torneado interno.
2.6.2 Elección de la cantidad de corte
La cantidad de corte incluye la velocidad del cabezal, la profundidad de corte y la velocidad de alimentación. Para diferentes métodos de procesamiento, se deben seleccionar diferentes cantidades de corte. El principio de selección de la cantidad de corte es: garantizar la precisión y la rugosidad de la superficie de la pieza, para aprovechar al máximo el rendimiento de corte de la herramienta y garantizar una vida útil razonable de la herramienta; Y aproveche al máximo el rendimiento de las máquinas herramienta para maximizar la productividad y reducir los costos.
(1) Determinación de la velocidad del husillo
La velocidad del husillo debe seleccionarse según la velocidad de corte permitida y el diámetro de la pieza de trabajo (o herramienta). De acuerdo con los requisitos de procesamiento de las piezas, considerando que el material de la pieza es 45 acero, el material de la herramienta es acero al carburo, velocidad de desbaste 500r / min, acabado 1000r / min girando círculo exterior, Considerando que la fuerza de corte del hilo fino es pequeña, el hilo es 400r / min. Debido a la escasa rigidez del orificio interior, el camión crudo se utiliza a 600 rpm, lo que es relativamente fácil de cumplir con los requisitos de procesamiento. La cuchilla de corte es más grande y 350 r / min es más segura.
(2) Selección de velocidad de avance (velocidad de avance) F (mm / r, mm / min)
La velocidad de alimentación es un parámetro importante en la cantidad de corte de máquinas herramienta CNC. Se selecciona principalmente de acuerdo con el programa de procesamiento y los requisitos de rugosidad superficial de las piezas y las propiedades del material de las herramientas y piezas de trabajo. Velocidad de alimentación máxima, limitada por la rigidez de la máquina y el rendimiento del sistema de alimentación. En general, el automóvil de desbaste utiliza una velocidad de alimentación más alta para eliminar el material en bruto rápidamente. El mecanizado final tiene en cuenta los principios de rugosidad superficial y precisión de piezas. Desbaste, ya que no se requiere alta calidad de la superficie de la pieza de trabajo. En este momento, la velocidad de alimentación se selecciona en función de la resistencia y rigidez del mecanismo de alimentación de la máquina herramienta, la resistencia y la rigidez de la barra de herramientas, la material de la herramienta, las dimensiones del vástago de la herramienta y la pieza de trabajo, y la profundidad de corte seleccionada. Durante el acabado, la velocidad de alimentación se selecciona en función de los requisitos de rugosidad de la superficie, la herramienta y el material de la pieza de trabajo y otros factores. La velocidad de alimentación Vf se puede calcular de acuerdo con la fórmula Vf = f × n, donde f representa la alimentación por revolución, generalmente toma 0,3 ~ 0,8 mm / r de desbaste; los autos finos a menudo toman 0.1 ~ 0.3mm / r; El corte a menudo toma 0.05 ~ 0.2mm / r.
De acuerdo con los datos anteriores para seleccionar una velocidad de alimentación más baja, se obtuvo la siguiente tabla:
(3) Determinación de la profundidad de corte
La profundidad de corte está determinada por la rigidez de la máquina, la pieza de trabajo y la herramienta. Cuando se permite la rigidez, la profundidad de corte debe ser igual a la tolerancia de mecanizado (excluyendo la cantidad de torneado de acabado) tanto como sea posible, lo que puede reducir el número de pasadas y aumentar la eficiencia de producción. Para garantizar la calidad de la superficie de mecanizado, puede dejarse una pequeña cantidad de acabado.
La selección de la profundidad de corte de la pieza en base a los datos anteriores es aproximadamente la siguiente:
En resumen, el valor específico de la cantidad de corte debe determinarse por analogía en función del rendimiento de la máquina herramienta, los manuales relacionados y la experiencia práctica. Al mismo tiempo, la velocidad del cabezal, la profundidad de corte y la velocidad de alimentación se pueden adaptar entre sí para formar la cantidad de corte óptima. Cantidad de corte Para diferentes métodos de procesamiento, se requieren diferentes cantidades de corte. La elección razonable de la cantidad de corte tiene una gran influencia en la calidad de la superficie, la precisión y la eficiencia de procesamiento de las piezas.
Método de selección de cantidad de corte:
Al desbastar, debe intentar asegurar una alta tasa de remoción de metal y la vida útil necesaria de la herramienta.
Cuando termina de tornear, los requisitos para la precisión del mecanizado y la rugosidad de la superficie son altos, y el margen de mecanizado no es grande y uniforme. Debe centrarse en cómo garantizar la precisión del procesamiento, y sobre esta base, cómo mejorar la eficiencia del procesamiento. Por lo tanto, se requiere utilizar una profundidad de corte y velocidad de alimentación más pequeñas (pero no demasiado pequeñas) al terminar el torneado, y utilizar materiales de herramientas de alto rendimiento y parámetros geométricos razonables para aumentar la velocidad de corte tanto como sea posible.
En resumen, la secuencia de procesamiento de esta parte es la siguiente:
2.7.1 Proceso I: gire la superficie del extremo derecho, convierta los espacios en barras de 102 mm
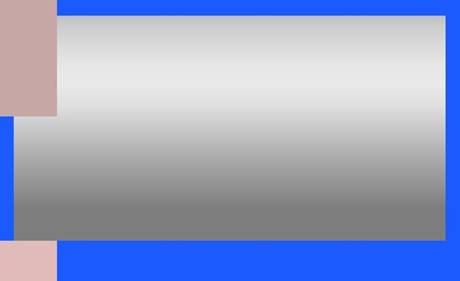
2.7.2 Proceso II: Desbaste, acabado del contorno exterior de la derecha, al tamaño deseado
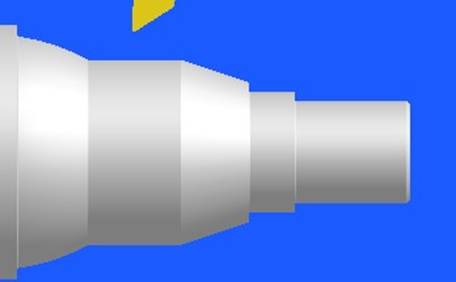
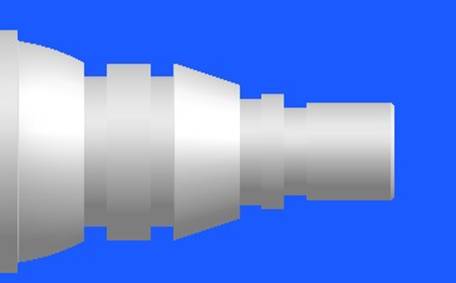
2.7.4 Proceso IV Girar hilo
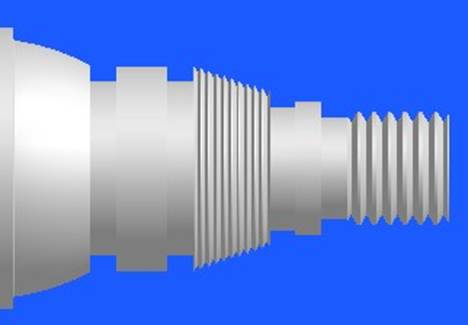
2.7.5 Proceso V Gire la cara del extremo izquierdo a 100 mm
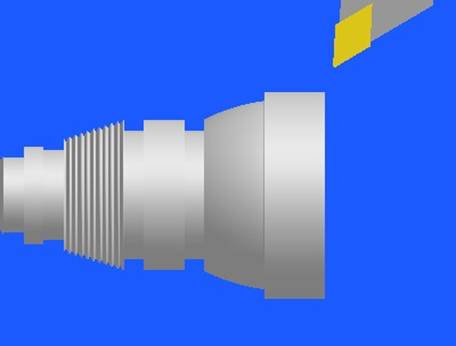
2.7.6 Proceso VI Girando el círculo externo izquierdo
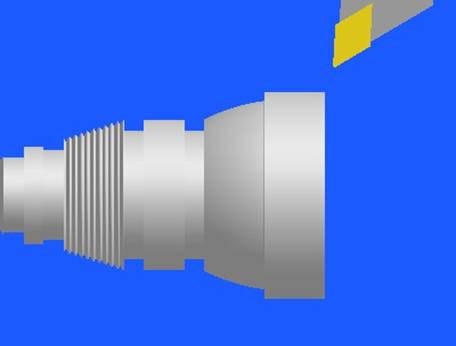
2.7.7 Proceso VII Perforación
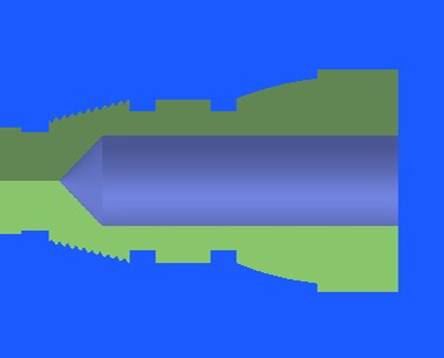
2.7.8 Proceso VIII Círculo interno de torneado grueso y fino
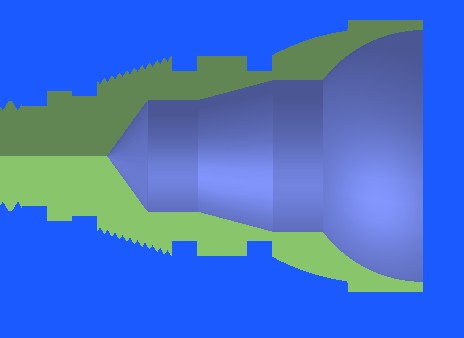
2.10 Métodos para asegurar la precisión del procesamiento
Con el fin de garantizar y mejorar la precisión de mecanizado, de acuerdo con el proceso de producción debe ser la razón principal del error, tomar la prevención de error o compensación de error correspondiente y otros enfoques tecnológicos efectivos para controlar directamente la influencia del error original en la precisión de mecanizado de piezas .
2.10.1 Selección del radio de la herramienta
(1) El radio de herramienta R no se puede mecanizar cuando es más grande que el radio de la esquina de la pieza de trabajo.
(2) Cuando la herramienta es pequeña, no se puede mecanizar con una gran cantidad de corte (rigidez difícil de la herramienta).
2.10.2 Utilice un fluido de corte adecuado
(1) El fluido de corte se usa principalmente para reducir la fricción durante el corte y reducir la temperatura de corte. El uso racional del fluido de corte juega un papel importante en la mejora de la durabilidad de la herramienta, la calidad de la superficie de mecanizado y la precisión del mecanizado.
(2) Fluido de corte no soluble en agua: el aceite de corte, los lubricantes sólidos y los fluidos de corte no solubles juegan principalmente un papel en la lubricación.
(3) Líquido de corte soluble en agua: las soluciones acuosas, las emulsiones y los fluidos de corte solubles en agua tienen buenos efectos de enfriamiento y limpieza. Por lo tanto, este diseño usa una solución acuosa para enfriamiento.
Este diseño se ocupa principalmente del análisis de procesos de mecanizado CNC y del procesamiento de dibujos de piezas específicas. En primer lugar, se realizó una breve introducción a la tecnología de mecanizado NC, y luego se realizó el análisis de mecanizado NC de acuerdo con el diagrama de piezas.
Primero, de acuerdo con el proceso de mecanizado, la cantidad de corte y otros factores relevantes del material de la pieza, la herramienta, el mango y las características del contorno de las piezas se utilizan para determinar que se requieren 5 herramientas.
En segundo lugar, programe los gráficos del dibujo de la pieza. Esta parte es un eje múltiple, el contorno exterior se compone de una línea recta, un corte inferior, un arco y un hilo. Dentro del extremo izquierdo de la pieza, se perforan un agujero cónico y un arco interior. En el proceso de mecanizado, la pieza de trabajo debe perforar y luego girar el arco interno.
tercero, cuando la configuración de la herramienta taladrar orificio, es necesario volver a referirse al punto de referencia primero. La posición de la herramienta se usa para corregir esto, de modo que la posición de la herramienta y el punto de cambio de herramienta coincidan para determinar el sistema de coordenadas de programación y el origen de programación. Se compiló el programa de mecanizado NC. Finalmente, la simulación y el procesamiento de las partes del eje se realizaron con software de simulación de programación.
Palabras clave: programación CNC, plan de mecanizado, cantidad de corte, programa de mecanizado
Análisis de tecnología de procesamiento de partes
Análisis de tecnología de procesamiento de partes
1.1 Análisis del proceso de dibujo de piezas
como muestra la imagen:
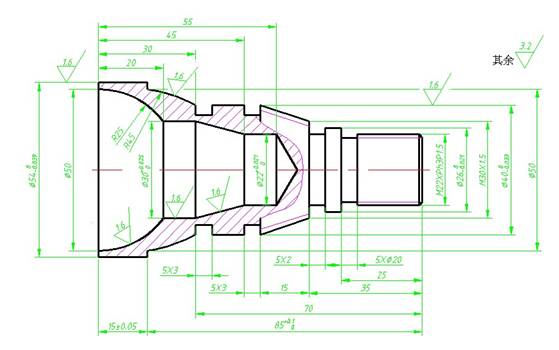
Análisis de estructura de partes:
En el diagrama, podemos ver que esta parte está formada por superficie cilíndrica, orificio interior, superficie interna del cono, superficie circular del arco, ranura, hilo, etc. La forma del contorno de la parte giratoria de la pieza que gira es más compleja y requiere un mecanizado de dos extremos. La precisión de mecanizado y la calidad de la superficie de las piezas son muy altas. Las partes importantes de mecanizado radial de la pieza son c54-0.039 secciones cilíndricas de 0 mm (rugosidad superficial Rɑ = 1,6 μm). R45 está conectado a un arco circular, c40-0.033 0 sección cilíndrica, Ф22 + 0.021 0 y el radio del orificio interior del orificio interior de R25. Las piezas cumplen los requisitos para el dimensionamiento del mecanizado NC, y la descripción del contorno es clara y completa. El material de la pieza es acero No.45 y el espacio en blanco es ф60mm * 110mm.
1.2 Análisis de los requisitos técnicos de las piezas
Programación de condiciones de fabricación de bajo volumen. No está permitido modificar el plano con tela de esmeril y paleta. Este es un requisito para la alta precisión de los aviones. Las tolerancias no especificadas, de acuerdo con GB1804-M, el tratamiento térmico, templado y templado, HRC25-35, no indica la parte rugosidad, el acabado es Ra6.3, el tamaño del embrión es mm60mm * 110mm.
1.3 Análisis de partes en blanco y materiales
(1) Análisis de materiales
En el mecanizado de esta parte del eje, la fuerza de corte entre la herramienta y la pieza de trabajo es grande. La maquinabilidad, resistencia, dureza, plasticidad, corte en frío y las propiedades mecánicas del material de la pieza de trabajo están relacionadas con el material de la pieza de trabajo. Por lo tanto, 45 acero fue seleccionado como el material para el eje. La composición química del acero 45 contiene C0.42% a 0.50%, Si0.17% a 0.37%, Mn0.50 a 0.80%, P≤0.035%, S≤0.035%, Cr≤0.25% y N≤0.25% . Cu≤0.25%. Requisitos de dureza para acero 45 en frío, acero laminado en caliente, diámetro de indentación no inferior a 3,9, dureza Brinell no inferior a 241HB, diámetro de indentación de acero recocido no inferior a 4,4, dureza Brinell no inferior a 187HB, 45 propiedades mecánicas de acero: δs ≥ 335 Mpa, δb ≥ 600 Mpa, ≥ ≥ 40%, Ak ≥ 47J. Herramienta de carburo de acero relativamente mecanizado 45 1.0, herramienta de acero de alta velocidad 1.0, 45 requisitos de herramientas de acero económico razonable también son razonables, 45 de acero es ampliamente utilizado, principalmente para la fabricación de turbinas de vapor, compresores, engranajes de fabricación de piezas de bomba, pin de pistón de eje y otro partes. De acuerdo con los datos anteriores, es adecuado para el mecanizado de este eje.
(2) Análisis de espacios en blanco
Los espacios en blanco de las partes del eje incluyen barras, forjas y piezas fundidas. Forjas: adecuado para piezas con alta resistencia y formas simples. Piezas de gran tamaño debido a las restricciones de los equipos; generalmente se utiliza forjado en matriz abierta; Piezas medianas y pequeñas piezas forjadas opcional; Las piezas rígidas con formas complejas no son adecuadas para el forjado libre y son adecuadas para espacios en blanco con formas complejas. Los espacios en blanco forjados de piezas de acero tienen propiedades mecánicas más altas que las barras de acero y las piezas de fundición de acero. De acuerdo con la forma estructural y el tamaño del contorno exterior de la parte del eje, se utilizan piezas forjadas. El blanco de esta pieza debe adoptar forjado, serrado por barra y forjar en blanco a Φ60X110mm, después de forjar el acero para obtener una estructura fibrosa uniforme, mejorar sus propiedades mecánicas, pero también aumentar la proporción de piezas y espacios en blanco, reduciendo el consumo de material.
2.4 Selección de equipos de procesamiento de piezas
2.4.1 Tipos de herramientas de máquina
El torno CNC puede completar automáticamente el mecanizado de las superficies cilíndricas internas y externas, superficies cónicas, superficies de arco, etc., en piezas giratorias como ejes o discos, y puede realizar operaciones tales como ranurado, perforación y expansión. De acuerdo con los requisitos técnicos de las piezas, se pueden seleccionar tornos CNC económicos, y generalmente se utilizan servosistemas de lazo semicerrado en forma de motores paso a paso. Estos tornos tienen una estructura simple y un precio relativamente bajo. Este tipo de torno está equipado con un mandril autocentrante de tres mordazas, un contrapunto común o un contrapunto hidráulico controlado numéricamente, que es adecuado para hacer girar piezas de eje más largas. El torno CNC horizontal se selecciona de acuerdo con los requisitos de la configuración del husillo. Los tornos CNC tienen una alta precisión de mecanizado, pueden realizar interpolaciones lineales y circulares, los tornos CNC tienen buena rigidez, alta precisión en la fabricación y configuración de herramientas, y se pueden compensar manual y exactamente de forma manual y automática, y se pueden mecanizar piezas con altos requisitos de precisión dimensional. Puede procesar superficies y tamaños particularmente difíciles con cuerpos de giro difíciles de controlar con formas de contorno, y puede girar fácilmente la superficie cónica del cono y los hilos cilíndricos interno y externo para mantener la precisión del mecanizado y mejorar la eficiencia de producción. Por lo tanto, es muy favorable para el procesamiento.
De acuerdo con la estructura, especificación y precisión de los componentes multieje, la selección de un centro de torneado dará como resultado un cierto desperdicio funcional, por lo que se elige el torno CNC económico, por lo que se selecciona el torno CNC SSCK20 / 500.
2.4.2 Precisión de la máquina herramienta
Los metales comúnmente utilizados, con excepción de los aceros templados con precisión de mecanizado de IT7 a IT8 y Ra 0.8 a Ra 1.6 μm, se pueden completar con dos pasos de desbaste y acabado. Precisión de procesamiento de grado IT5 ~ IT6, Ra0.2 ~ Ra 0.63 μm, además del acero templado de metal comúnmente utilizado, se pueden utilizar tornos CNC de precisión, desbaste → semiacabado → carro fino → procesamiento de programa de carro fino. La precisión de mecanizado es más alta que la de los metales usados comúnmente que no sean los aceros templados como IT5 y Ra <0.08μm, se pueden usar tornos CNC de precisión, y el mecanizado puede realizarse según el desbaste, semiacabado, acabado y torneado de precisión. Para materiales difíciles de girar como el acero endurecido, se puede usar el método de desbaste y semiacabado antes del enfriamiento rápido, y la molienda se realiza después del enfriamiento. Por lo tanto, de acuerdo con los requisitos del plano de piezas, la precisión del torno CNC SSCK20 / 500 es adecuada para la precisión del eje múltiple.
Principales parámetros técnicos del torno CNC SSCK20 / 500
Máxima velocidad de giro de la máquina | Ф400mm |
Diámetro de la abrazadera | Ф200mm |
Diámetro máximo de corte | Ф200mm |
Longitud máxima de corte | 500mm |
Rango de velocidad del husillo |
24r / min ~ 2400r / mm (continuo sin escalones)
|
Diámetro del eje | Ф55mm |
Slip saddle maximum longitudinal travel | 550mm |
Máximo recorrido lateral del monopatín | 200mm |
Velocidad de movimiento rápido | X axis 6m/min;Z axis 12m/min |
Número de estación de la torreta | 6 Station |
Especificaciones de herramientas |
herramienta de torneado 20 mm × 20 mm
|
Diámetro del agujero de la herramienta | Ф32mm |
Modo de selección de herramienta | Sentido de las agujas del reloj |
Entrada mínima equivalente | Eje X (diámetro) 0.001 mm; eje Z 0.001 mm |
Diámetro de la manga de la cola | Ф70mm |
Desplazamiento máximo de la manga de contrapunto | 60mm |
Agujero cónico superior | Mode 4 |
Potencia del motor principal | Carga continua 11kw |
Alimentación del servo motor | X axis AC0.6kw;Z axis AC0.6kw |
Potencia del motor de la estación hidráulica | 1.1kw |
Corte de la potencia del motor de fluido | 0.0125kw |
Dimensiones de la máquina (L × W × H) | 2600mm×12400mm×1715mm |
Calidad de red de la máquina herramienta | 2300kg |
2.5 Determinación del Esquema de Posicionamiento y Fixture de la Pieza de Trabajo
2.5.1 Determinar el esquema de sujeción
Utilice el mandril autocentrante de tres mandíbulas para sujetar el círculo externo áspero de las piezas y determine las partes para extender la longitud adecuada (debe tenerse en cuenta la distancia límite de la máquina herramienta). Las piezas deben mecanizarse en ambos extremos, por lo que se debe considerar la posición de las dos sujeciones, teniendo en cuenta que los pasos en el lado izquierdo de los 54 mm x 15 mm se pueden usar para sujetar. Por lo tanto, el extremo derecho se procesa primero, luego se sujeta el cabezal del hilo de M22 Ph3P1.5 y se mecaniza el arco interno del escalón de 54 mm x 15 mm, el orificio interior 22 y el R25.
2.5.2 Referencia de posicionamiento
El posicionamiento y la referencia de la pieza de trabajo deben ser consistentes con la base de diseño, y se debe evitar el sobre posicionamiento. Lo mejor es elegir "un lado y dos clavijas" como el punto de referencia de la pieza de trabajo con la caja, y el punto de referencia de posición debe ubicarse cuidadosamente en la herramienta de control numérico de la máquina. La pieza de trabajo es un eje sólido con un agujero cónico de 30 grados en el extremo. Debido a que la longitud del eje no es muy larga, la cara extrema derecha de la pieza de trabajo y el círculo exterior de 48 se utilizan como referencia para el posicionamiento. Use un mandril normal de tres garras para sujetar la pieza de trabajo. Tome el centro de la cara frontal derecha de la pieza de trabajo según se coordina el origen de la pieza de trabajo. El punto de la herramienta está en (100.100). Dado que toda la superficie de la pieza necesita ser mecanizada, el círculo exterior y una cara final deben usarse como referencia aproximada, y luego el procesamiento debe realizarse a través del principio de referencia mutua. Siga el principio de "coincidencia de referencia". Seleccione la superficie exterior del lado izquierdo del espacio en blanco al mecanizar el extremo derecho, y seleccione la superficie del círculo externo derecho cuando procese el lado izquierdo, para mostrar que el punto de referencia de posición es la línea central del eje.
2.6 Selección de herramientas de corte y capacidad de corte
2.6.1 Selección de herramienta
El procesamiento de esta parte,
(1) Para el torneado áspero y fino de los extremos exterior y plano, se adopta el cortador de desviación izquierda de carburo cementado de 35 grados.
Elegir orden = evitar la interferencia entre la cara del rastrillo accesorio y el contorno de la pieza de trabajo, el ángulo de desviación auxiliar no debe ser demasiado pequeño. Elija Kr = 35.
(2) cortadores de ranura,
(3) La rosca del tornillo se elige con herramienta de torneado de rosca externa de carburo de 60 grados, y el radio de la punta debe ser menor que el radio de filete mínimo del perfil, tomando re = 0,15 a 0,2 mm.
(4) Mecanizar el agujero izquierdo con un taladro de 22 mm
(5) herramienta de torneado interno.
La elección de la herramienta es uno de los contenidos importantes en el diseño del proceso de control numérico. La elección racional de la herramienta no solo afecta la eficiencia de mecanizado de la máquina herramienta, sino que también afecta la calidad del mecanizado. La elección de la herramienta generalmente considera la capacidad de mecanizado, el contenido del proceso y el material de la pieza de trabajo de la máquina herramienta.
En comparación con el método de torneado tradicional, el torneado CNC tiene un mayor requerimiento de herramientas. No solo requiere alta precisión, buena rigidez, alta durabilidad, sino que también requiere estabilidad dimensional y una fácil instalación y ajuste. Esto requiere el uso de nuevos materiales de alta calidad para fabricar herramientas de mecanizado CNC y optimizar los parámetros de la herramienta.
La herramienta seleccionada se muestra en la figura a continuación:
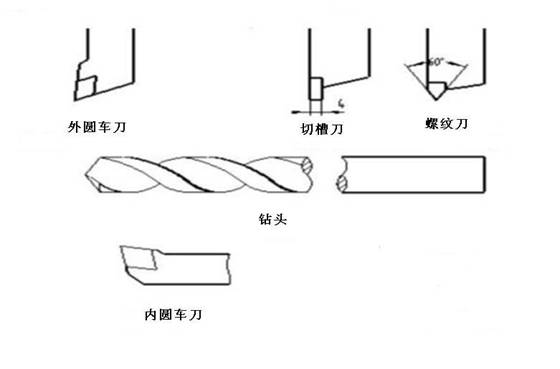
Cylindrical turning tools, grooved knives, thread knives, drill bits, internal turning tools.
Herramientas de torneado cilíndricas, cuchillas acanaladas, cuchillas de rosca, brocas, herramientas de torneado interno.
2.6.2 Elección de la cantidad de corte
La cantidad de corte incluye la velocidad del cabezal, la profundidad de corte y la velocidad de alimentación. Para diferentes métodos de procesamiento, se deben seleccionar diferentes cantidades de corte. El principio de selección de la cantidad de corte es: garantizar la precisión y la rugosidad de la superficie de la pieza, para aprovechar al máximo el rendimiento de corte de la herramienta y garantizar una vida útil razonable de la herramienta; Y aproveche al máximo el rendimiento de las máquinas herramienta para maximizar la productividad y reducir los costos.
(1) Determinación de la velocidad del husillo
La velocidad del husillo debe seleccionarse según la velocidad de corte permitida y el diámetro de la pieza de trabajo (o herramienta). De acuerdo con los requisitos de procesamiento de las piezas, considerando que el material de la pieza es 45 acero, el material de la herramienta es acero al carburo, velocidad de desbaste 500r / min, acabado 1000r / min girando círculo exterior, Considerando que la fuerza de corte del hilo fino es pequeña, el hilo es 400r / min. Debido a la escasa rigidez del orificio interior, el camión crudo se utiliza a 600 rpm, lo que es relativamente fácil de cumplir con los requisitos de procesamiento. La cuchilla de corte es más grande y 350 r / min es más segura.
(2) Selección de velocidad de avance (velocidad de avance) F (mm / r, mm / min)
La velocidad de alimentación es un parámetro importante en la cantidad de corte de máquinas herramienta CNC. Se selecciona principalmente de acuerdo con el programa de procesamiento y los requisitos de rugosidad superficial de las piezas y las propiedades del material de las herramientas y piezas de trabajo. Velocidad de alimentación máxima, limitada por la rigidez de la máquina y el rendimiento del sistema de alimentación. En general, el automóvil de desbaste utiliza una velocidad de alimentación más alta para eliminar el material en bruto rápidamente. El mecanizado final tiene en cuenta los principios de rugosidad superficial y precisión de piezas. Desbaste, ya que no se requiere alta calidad de la superficie de la pieza de trabajo. En este momento, la velocidad de alimentación se selecciona en función de la resistencia y rigidez del mecanismo de alimentación de la máquina herramienta, la resistencia y la rigidez de la barra de herramientas, la material de la herramienta, las dimensiones del vástago de la herramienta y la pieza de trabajo, y la profundidad de corte seleccionada. Durante el acabado, la velocidad de alimentación se selecciona en función de los requisitos de rugosidad de la superficie, la herramienta y el material de la pieza de trabajo y otros factores. La velocidad de alimentación Vf se puede calcular de acuerdo con la fórmula Vf = f × n, donde f representa la alimentación por revolución, generalmente toma 0,3 ~ 0,8 mm / r de desbaste; los autos finos a menudo toman 0.1 ~ 0.3mm / r; El corte a menudo toma 0.05 ~ 0.2mm / r.
De acuerdo con los datos anteriores para seleccionar una velocidad de alimentación más baja, se obtuvo la siguiente tabla:
Áspero | multa | |
Círculo extranjero | 0.5mm/r | 0.2mm/r |
Hilo | 0.08mm/r | 0.03mm/r |
Hoyo interno | 0.4mm/r | 0.2mm/r |
ranura | 0.1mm/r |
(3) Determinación de la profundidad de corte
La profundidad de corte está determinada por la rigidez de la máquina, la pieza de trabajo y la herramienta. Cuando se permite la rigidez, la profundidad de corte debe ser igual a la tolerancia de mecanizado (excluyendo la cantidad de torneado de acabado) tanto como sea posible, lo que puede reducir el número de pasadas y aumentar la eficiencia de producción. Para garantizar la calidad de la superficie de mecanizado, puede dejarse una pequeña cantidad de acabado.
La selección de la profundidad de corte de la pieza en base a los datos anteriores es aproximadamente la siguiente:
Áspero | multa | |
Círculo extranjero | 10(mm) | 0.2-0.5(mm) |
Hilo | 10(mm) | 0.1-0.5(mm) |
Hoyo interno | With the number of feeds in turn decreased | |
ranura | According to knife width, it is performed twice |
Método de selección de cantidad de corte:
Al desbastar, debe intentar asegurar una alta tasa de remoción de metal y la vida útil necesaria de la herramienta.
Cuando termina de tornear, los requisitos para la precisión del mecanizado y la rugosidad de la superficie son altos, y el margen de mecanizado no es grande y uniforme. Debe centrarse en cómo garantizar la precisión del procesamiento, y sobre esta base, cómo mejorar la eficiencia del procesamiento. Por lo tanto, se requiere utilizar una profundidad de corte y velocidad de alimentación más pequeñas (pero no demasiado pequeñas) al terminar el torneado, y utilizar materiales de herramientas de alto rendimiento y parámetros geométricos razonables para aumentar la velocidad de corte tanto como sea posible.
En resumen, la secuencia de procesamiento de esta parte es la siguiente:
2.7.1 Proceso I: gire la superficie del extremo derecho, convierta los espacios en barras de 102 mm
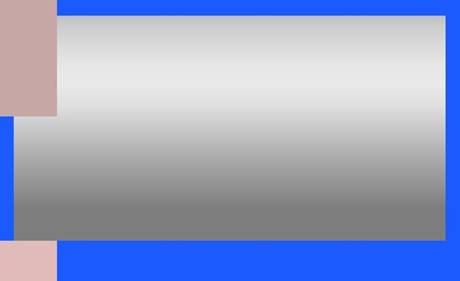
2.7.2 Proceso II: Desbaste, acabado del contorno exterior de la derecha, al tamaño deseado
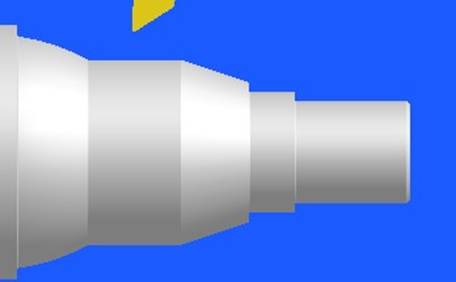
2.7.3 Procesado III Ranurado
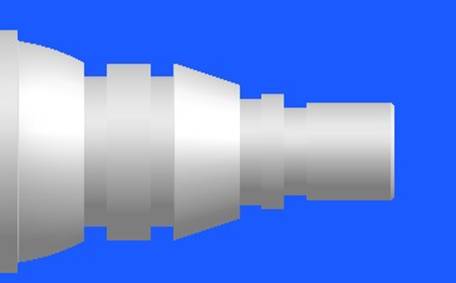
2.7.4 Proceso IV Girar hilo
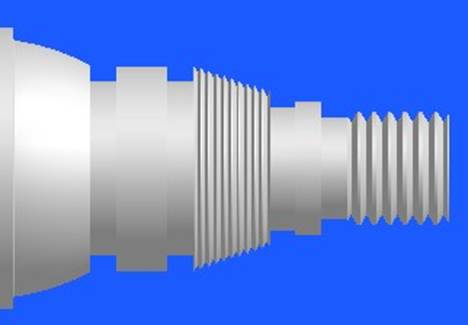
2.7.5 Proceso V Gire la cara del extremo izquierdo a 100 mm
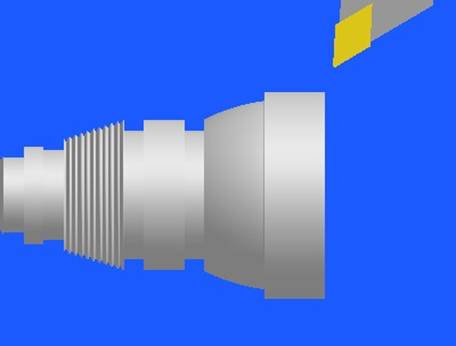
2.7.6 Proceso VI Girando el círculo externo izquierdo
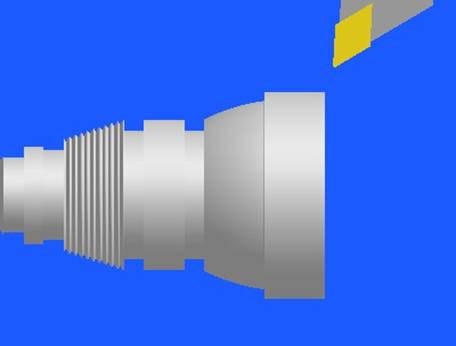
2.7.7 Proceso VII Perforación
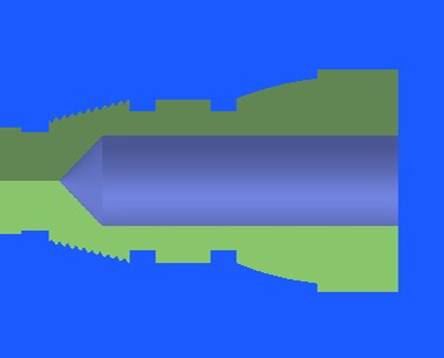
2.7.8 Proceso VIII Círculo interno de torneado grueso y fino
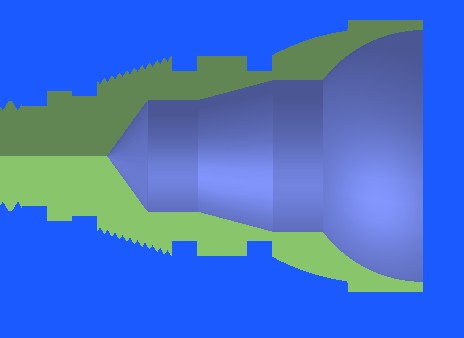
Tarjeta de procesos de mecanizado CNC | ||||||||||||||||||
Nombre de parte | Multieje | Numero de parte | Figura 2 | Nombre del accesorio | Mandril de tres garras | |||||||||||||
Nombre y modelo del equipo | Torno CNC SSCK20 / 500 | |||||||||||||||||
Nombre del material y marca |
45 acero | Dureza | HRC68 | Nombre del proceso | Mecanizado cilíndrico | ID de empleado | Ⅱ | |||||||||||
![]() |
||||||||||||||||||
Número de paso | Contenido paso | Cantidad de corte | Herramientas | Herramienta de medición | ||||||||||||||
n(r/min) | f(mm/r) | ap(mm) | No. | name | nombre | |||||||||||||
1 | Áspero círculo externo | 500 | 0.5 | 10 | T0101 | Herramienta de torneado redondo | Calibre de Vernier | |||||||||||
2 | Fino giro del círculo exterior | 1000 | 0.2 | 0.3 | T0101 | Herramienta de torneado redondo | micrómetro | |||||||||||
3 | Chaflán | 500 | 0.14 | 1.5 | T0101 | Herramienta de torneado redondo | ||||||||||||
4 | Áspero arco externo | 500 | 0.5 | 10 | T0101 | Herramienta de torneado redondo | Calibre de Vernier | |||||||||||
5 | Arco exterior del automóvil fino | 1000 | 0.2 | 0.3 | T0101 | Herramienta de torneado redondo | micrómetro |
2.10 Métodos para asegurar la precisión del procesamiento
Con el fin de garantizar y mejorar la precisión de mecanizado, de acuerdo con el proceso de producción debe ser la razón principal del error, tomar la prevención de error o compensación de error correspondiente y otros enfoques tecnológicos efectivos para controlar directamente la influencia del error original en la precisión de mecanizado de piezas .
2.10.1 Selección del radio de la herramienta
(1) El radio de herramienta R no se puede mecanizar cuando es más grande que el radio de la esquina de la pieza de trabajo.
(2) Cuando la herramienta es pequeña, no se puede mecanizar con una gran cantidad de corte (rigidez difícil de la herramienta).
2.10.2 Utilice un fluido de corte adecuado
(1) El fluido de corte se usa principalmente para reducir la fricción durante el corte y reducir la temperatura de corte. El uso racional del fluido de corte juega un papel importante en la mejora de la durabilidad de la herramienta, la calidad de la superficie de mecanizado y la precisión del mecanizado.
(2) Fluido de corte no soluble en agua: el aceite de corte, los lubricantes sólidos y los fluidos de corte no solubles juegan principalmente un papel en la lubricación.
(3) Líquido de corte soluble en agua: las soluciones acuosas, las emulsiones y los fluidos de corte solubles en agua tienen buenos efectos de enfriamiento y limpieza. Por lo tanto, este diseño usa una solución acuosa para enfriamiento.