Diseno de estampado continuo de piezas de carcasa metálica
La forma y el tamaño de las piezas de la carcasa del elevador de vidrio de la puerta del automóvil. Como se muestra en la Figura 8.2.1,
El material es 08 placa de acero, placa de espesor 1,5 mm, producción en masa.
Producción de estampado, requiere la preparación de un proceso de estampado.
8.2.1 Análisis de proceso de piezas estampadas
Primero, debe comprender completamente la aplicación y los requisitos técnicos del producto, y realizar un análisis del proceso.
El cristal de la puerta del automóvil es levantado o bajado por el levantador.
El diagrama de ensamblaje de los componentes del elevador se muestra en la Figura 8.2.2. La parte estampada es la carcasa exterior 5 de la misma. El mecanismo de transmisión del elevador está alojado en la carcasa exterior, y está remachado a la placa del asiento de la puerta por tres pequeños agujeros distribuidos uniformemente φ 3.2 mm en la brida de la carcasa exterior. El eje de accionamiento 6 está montado en la porción de soporte del orificio del extremo derecho φ 16.5 mm con la holgura de I T11. El resorte de torsión del freno 3, la pieza de unión 9 y el eje 4 están acoplados con el piñón 11 para balancear la manija 7. El eje de transmisión transmite potencia al piñón y luego impulsa el engranaje grande 12 para empujar el vidrio de la puerta hacia arriba y hacia abajo .
Los estampados están estampados en placas de acero de 1,5 mm para garantizar una rigidez y resistencia adecuadas.
Las dimensiones principales de acoplamiento de la cavidad interna de la carcasa son φ 16,5 mm, φ 22,3 mm y 16 mm son IT11-IT12.
Para garantizar la coaxialidad entre la parte de soporte y el manguito después del remachado y la fijación. la posición relativa entre los tres agujeros pequeños de φ 3.2 mm y φ 16.5 mm es precisa, y el diámetro del círculo central del agujero pequeño es φ 42 ± 0.1 mm. Nivel T10.
Esta parte es un cuerpo giratorio cuya forma se caracteriza por una pieza cilíndrica bridada.
La forma y el tamaño principales se pueden obtener mediante un proceso de dibujo tal como dibujo, rebordeado, punzonado y similares.
Como el tamaño del dibujo, los valores relativos son adecuados, y el proceso de dibujo es mejor.
Los requisitos de tolerancia para φ 22.3 mm y 16 mm son demasiado altos. El radio del filete en la parte inferior y la boca de la pieza de embutición profunda también es pequeño, por lo que se debe agregar después del embutido, y se debe usar el molde con alta precisión y un pequeño espacio.
La precisión del diámetro del círculo central de los tres agujeros pequeños φ 3.2 mm es 42 ± 0.1 mm. Según el análisis técnico de las piezas ciegas, se debe colocar el diámetro interno de φ 22,3 mm y se debe perforar el dado de alta precisión (IT7 o superior) simultáneamente en un proceso.
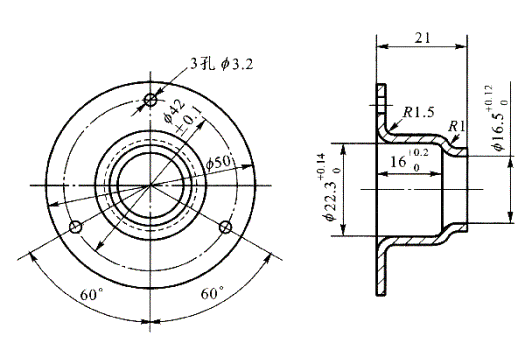
Figura 8.2.1 Carcasa de metal con elevador de vidrio
Figura 8.2.2 Diagrama de ensamblaje de la carcasa del elevador de vidrio
8.2.2 Determinación del proceso de estampado
uno. Análisis y comparación de planes de proceso.
La forma de la carcasa exterior indica que es una pieza de dibujo profunda, por lo que dibujar es un proceso básico.
Los tres pequeños agujeros en la brida se completan mediante un proceso de perforación.
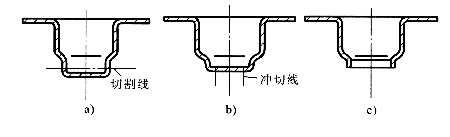
Figura 8.2.3 Esquema de formación en la parte inferior de la carcasa
un corte; b) punzonado; c) brida de perforación
dos. Determinación del plan de proceso.
• Calcular el tamaño en blanco
Antes de calcular el tamaño del blanco, es necesario determinar la forma y el tamaño del producto semiacabado antes del reborde y calcular el grado de deformación del reborde. Con referencia a la FIG. 8.2.1, la dimensión de la altura de las piezas a φ 16.5 mm es: H = 21-16 = 5 mm.
De acuerdo con la fórmula de cálculo del proceso de brida, el coeficiente de brida K es:

La altura de la brida H = 5 mm; diámetro del manguito D = 16.5 + 1.5 = 18 mm; radio de reborde r = 1 mm; espesor del material t = 1.5 mm en la ecuación anterior para obtener la brida del coeficiente:

Diámetro del orificio preperforado d = DK = 11 mm, d / t = 11 / 1.5 = 7.33
Verifique el valor límite del coeficiente de brida. Cuando se perfora el punzón previo con un punzón cilíndrico, el coeficiente límite de rebordeado [K] = 0.5. Ahora 0.61> 0.5, es posible obtener una altura de H = 5 mm bridando directamente después del punzonado. La forma y las dimensiones de las partes dibujadas antes del reborde se muestran en la Figura 8.2.4.
Cuando se realiza un dibujo con el coeficiente de dibujo cercano al límite, es necesario usar un radio mayor para garantizar la calidad del dibujo. En la actualidad, el grosor del material de la pieza es t = 1.5 mm, el radio del filete es r = 2.55 mm, que es aproximadamente 1.5 t, que es demasiado pequeño, y el diámetro de la pieza es pequeño. Es difícil cumplir los requisitos de las piezas mediante dos embutidos profundos. Por lo tanto, es necesario agregar un proceso de modelado después de dos embutidos profundos para obtener un radio de filete inferior y de boca más pequeño.
En aplicaciones prácticas, se pueden utilizar tres procesos de embutición profunda para reducir a su vez el radio del filete. El coeficiente de dibujo total m total = 0.366 se asigna al proceso de dibujo de tres vías, y se puede seleccionar m 1 = 0.56, m 2 = 0.805, m 3 = 0.812.
m 1 × m 2 × m 3 = 0.56 × 0.805 × 0.812 = 0.366
3) Proceso de combinación y determinación de secuencia
Para las piezas de estampado con muchos procesos, como la carcasa exterior, primero se puede determinar el proceso básico de las piezas, y luego se puede considerar la posible combinación de clasificación de todos los procesos básicos. Se analizan y comparan los diversos esquemas de proceso así obtenidos, a partir de los cuales se determina la mejor solución adecuada para la producción real.
El proceso básico de la carcasa exterior es:
Blanking φ 65 mm, primer dibujo,
El segundo dibujo profundo (ver Figura 8-11b),
El tercer dibujo profundo (ver Figura 8.2.5c) y el orificio inferior de φ 11 mm (ver Figura 8.2.5d),
Bridas φ 16.5 mm (ver Figura 8.2.5e),
Perfore tres agujeros pequeños de φ 3.2 mm (consulte la Figura 8.2.5f),
Recorte φ 50 mm (ver Figura 8.2.5g).
Un total de ocho procesos básicos, según los cuales se pueden descargar las siguientes cinco opciones de proceso:
Opción 1: la supresión se combina con el primer dibujo (consulte la Figura 8.2.5a), y el resto se basa en el proceso básico.
Opción II:
La supresión se combina con el primer dibujo, y el orificio inferior de φ 11 mm se combina con la brida (consulte la Figura 8.2.6a). Los tres pequeños orificios de φ 3.2 mm se combinan con el recorte (ver Figura 8.2.6b), y el resto se basa en el proceso básico. .
tercera solución:
La supresión se combina con el primer dibujo, y el orificio inferior de φ 11 mm se combina con los tres orificios pequeños de φ 3,2 mm (consulte la Figura 8.2.7a). El reborde se recorta con el recorte (consulte la Figura 8.2.7b), y el resto se basa en el proceso básico.
Opcion 4:
Blanking, primer embutido profundo y punzonado composite Compuesto de orificio inferior de 11 mm (ver Figura 8.2.8), el resto de acuerdo con el proceso básico. Opción 5: utilice troqueles progresivos o estampados en una prensa automática de varias estaciones.
Análisis y comparación de los cinco esquemas anteriores, se puede ver que en el esquema 2, el orificio de perforación de φ 11 mm se combina con la brida, debido al pequeño grosor de la pared del molde
mm, es más pequeño que el espesor mínimo de la pared de 3,8 mm entre los moldes convexo y cóncavo, y el molde se daña fácilmente. Al perforar tres pequeños agujeros de φ 3.2 mm combinados con recortes, también existe el problema de que la pared del molde es demasiado delgada. en este momento
mm, por lo tanto, no debe usarse.
En la opción tres,
Aunque resuelve la contradicción de que la pared del molde anterior es demasiado delgada. Sin embargo, cuando el orificio inferior de φ 11 mm se combina con los tres orificios pequeños de φ 3.2 mm y se combinan la brida y la moldura, sus bordes de corte no están en el mismo plano y la velocidad de desgaste es diferente. Esto puede causar inconvenientes en la molienda y es difícil mantener la posición relativa después de la molienda.
En la opción cuatro,
Blanking, primer embutido profundo y punzonado composite Compuesto de orificio inferior de 11 mm, matriz de punzonado y punzón embutido profundo integrados, lo que también causará dificultad en el rectificado. En particular, después de perforar el orificio inferior dos y tres veces, una vez que el diámetro del orificio cambia, afectará la dimensión de altura de la brida y la calidad de la porción de brida.
El quinto esquema adopta un troquel progresivo o un dispositivo de alimentación automática de múltiples estaciones, que tiene una alta eficiencia de producción. La estructura del molde es compleja, el ciclo de fabricación es largo y el costo es alto. Por lo tanto, solo es adecuado para la producción en masa.
El esquema 1 no tiene las deficiencias mencionadas anteriormente, pero el grado de composición es bajo y la eficiencia de producción es baja. Sin embargo, el molde de proceso único tiene una estructura simple y un bajo costo de fabricación, lo cual es razonable en la producción de lotes pequeños y medianos, por lo que se decide adoptar el primer esquema. En el tercer proceso de embutición profunda y embridado, cuando la carrera de estampado está llegando al final, el molde puede presionarse rígidamente contra la pieza de trabajo para formar un efecto de conformación, por lo que no se requiere un proceso de conformación adicional.
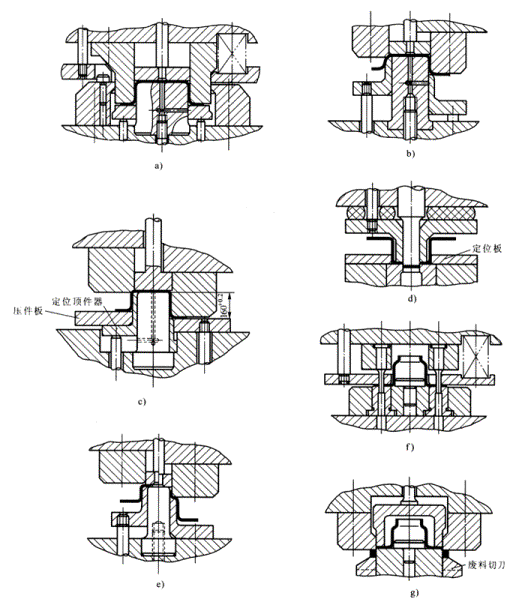
Figura 8.2.5 Estampado de diseño Estructura de molde de cada proceso
El material es 08 placa de acero, placa de espesor 1,5 mm, producción en masa.
Producción de estampado, requiere la preparación de un proceso de estampado.
8.2.1 Análisis de proceso de piezas estampadas
Primero, debe comprender completamente la aplicación y los requisitos técnicos del producto, y realizar un análisis del proceso.
El cristal de la puerta del automóvil es levantado o bajado por el levantador.
El diagrama de ensamblaje de los componentes del elevador se muestra en la Figura 8.2.2. La parte estampada es la carcasa exterior 5 de la misma. El mecanismo de transmisión del elevador está alojado en la carcasa exterior, y está remachado a la placa del asiento de la puerta por tres pequeños agujeros distribuidos uniformemente φ 3.2 mm en la brida de la carcasa exterior. El eje de accionamiento 6 está montado en la porción de soporte del orificio del extremo derecho φ 16.5 mm con la holgura de I T11. El resorte de torsión del freno 3, la pieza de unión 9 y el eje 4 están acoplados con el piñón 11 para balancear la manija 7. El eje de transmisión transmite potencia al piñón y luego impulsa el engranaje grande 12 para empujar el vidrio de la puerta hacia arriba y hacia abajo .
Los estampados están estampados en placas de acero de 1,5 mm para garantizar una rigidez y resistencia adecuadas.
Las dimensiones principales de acoplamiento de la cavidad interna de la carcasa son φ 16,5 mm, φ 22,3 mm y 16 mm son IT11-IT12.
Para garantizar la coaxialidad entre la parte de soporte y el manguito después del remachado y la fijación. la posición relativa entre los tres agujeros pequeños de φ 3.2 mm y φ 16.5 mm es precisa, y el diámetro del círculo central del agujero pequeño es φ 42 ± 0.1 mm. Nivel T10.
Esta parte es un cuerpo giratorio cuya forma se caracteriza por una pieza cilíndrica bridada.
La forma y el tamaño principales se pueden obtener mediante un proceso de dibujo tal como dibujo, rebordeado, punzonado y similares.
Como el tamaño del dibujo, los valores relativos son adecuados, y el proceso de dibujo es mejor.
Los requisitos de tolerancia para φ 22.3 mm y 16 mm son demasiado altos. El radio del filete en la parte inferior y la boca de la pieza de embutición profunda también es pequeño, por lo que se debe agregar después del embutido, y se debe usar el molde con alta precisión y un pequeño espacio.
La precisión del diámetro del círculo central de los tres agujeros pequeños φ 3.2 mm es 42 ± 0.1 mm. Según el análisis técnico de las piezas ciegas, se debe colocar el diámetro interno de φ 22,3 mm y se debe perforar el dado de alta precisión (IT7 o superior) simultáneamente en un proceso.
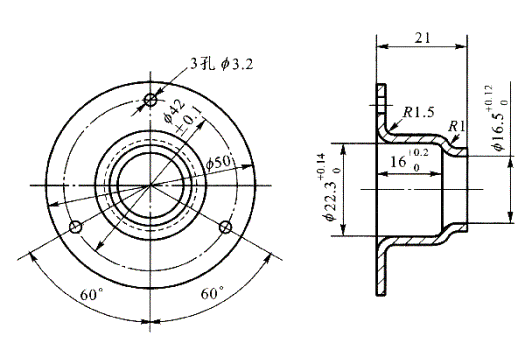
Figura 8.2.1 Carcasa de metal con elevador de vidrio
Figura 8.2.2 Diagrama de ensamblaje de la carcasa del elevador de vidrio
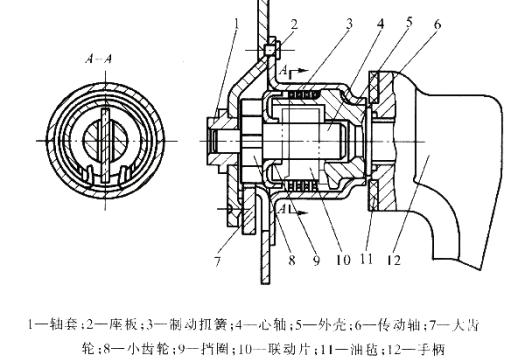
1, bujes. 2, placa de asiento. 3, muelle de torsión de freno. 4, el mandril. 5, la carcasa exterior. 6, el eje impulsor. 7, equipo grande. 8, piñón. 9, el anillo de retención. 10, película de enlace 11, linóleo. 12, el mango
8.2.2 Determinación del proceso de estampado
uno. Análisis y comparación de planes de proceso.
La forma de la carcasa exterior indica que es una pieza de dibujo profunda, por lo que dibujar es un proceso básico.
Los tres pequeños agujeros en la brida se completan mediante un proceso de perforación.
La formación de la pieza φ 16.5 mm (ver el lado derecho de la Figura 8.2.1) se puede hacer de tres maneras:
1, puede usar el paso de dibujo profundo, girando hacia abajo
2, después de que se puede utilizar el dibujo profundo de Step, el estampado elimina la parte inferior;
3, puede usar el método de dibujo, perforar el agujero inferior y luego hacer bridas. (Ver Figura 8.2.3)
El primer método tiene una mayor calidad en la parte inferior del torneado pero tiene una menor productividad. No es fácil de usar cuando la parte inferior de la pieza no está alta.
El segundo método requiere que el radio del filete del fondo esté cerca de cero antes de estampar para quitar el fondo, por lo que se requiere un proceso de modelado adicional y la calidad no se garantiza fácilmente.
El tercer método, aunque la calidad del extremo de la brida no es tan buena como las dos primeras, pero la eficiencia de producción es alta y el material se guarda.
Dado que la tolerancia de la dimensión de la altura de la carcasa de 21 mm no es alta, el proceso de brida puede garantizar completamente los requisitos técnicos de las piezas, por lo que es razonable utilizar el método de embutición profunda y luego punzonado y brida.
1, puede usar el paso de dibujo profundo, girando hacia abajo
2, después de que se puede utilizar el dibujo profundo de Step, el estampado elimina la parte inferior;
3, puede usar el método de dibujo, perforar el agujero inferior y luego hacer bridas. (Ver Figura 8.2.3)
El primer método tiene una mayor calidad en la parte inferior del torneado pero tiene una menor productividad. No es fácil de usar cuando la parte inferior de la pieza no está alta.
El segundo método requiere que el radio del filete del fondo esté cerca de cero antes de estampar para quitar el fondo, por lo que se requiere un proceso de modelado adicional y la calidad no se garantiza fácilmente.
El tercer método, aunque la calidad del extremo de la brida no es tan buena como las dos primeras, pero la eficiencia de producción es alta y el material se guarda.
Dado que la tolerancia de la dimensión de la altura de la carcasa de 21 mm no es alta, el proceso de brida puede garantizar completamente los requisitos técnicos de las piezas, por lo que es razonable utilizar el método de embutición profunda y luego punzonado y brida.
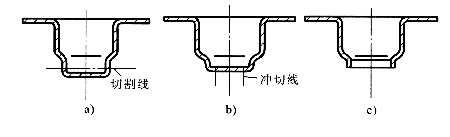
Figura 8.2.3 Esquema de formación en la parte inferior de la carcasa
un corte; b) punzonado; c) brida de perforación
dos. Determinación del plan de proceso.
• Calcular el tamaño en blanco
Antes de calcular el tamaño del blanco, es necesario determinar la forma y el tamaño del producto semiacabado antes del reborde y calcular el grado de deformación del reborde. Con referencia a la FIG. 8.2.1, la dimensión de la altura de las piezas a φ 16.5 mm es: H = 21-16 = 5 mm.
De acuerdo con la fórmula de cálculo del proceso de brida, el coeficiente de brida K es:

La altura de la brida H = 5 mm; diámetro del manguito D = 16.5 + 1.5 = 18 mm; radio de reborde r = 1 mm; espesor del material t = 1.5 mm en la ecuación anterior para obtener la brida del coeficiente:

Diámetro del orificio preperforado d = DK = 11 mm, d / t = 11 / 1.5 = 7.33
Verifique el valor límite del coeficiente de brida. Cuando se perfora el punzón previo con un punzón cilíndrico, el coeficiente límite de rebordeado [K] = 0.5. Ahora 0.61> 0.5, es posible obtener una altura de H = 5 mm bridando directamente después del punzonado. La forma y las dimensiones de las partes dibujadas antes del reborde se muestran en la Figura 8.2.4.
Cuando se realiza un dibujo con el coeficiente de dibujo cercano al límite, es necesario usar un radio mayor para garantizar la calidad del dibujo. En la actualidad, el grosor del material de la pieza es t = 1.5 mm, el radio del filete es r = 2.55 mm, que es aproximadamente 1.5 t, que es demasiado pequeño, y el diámetro de la pieza es pequeño. Es difícil cumplir los requisitos de las piezas mediante dos embutidos profundos. Por lo tanto, es necesario agregar un proceso de modelado después de dos embutidos profundos para obtener un radio de filete inferior y de boca más pequeño.
En aplicaciones prácticas, se pueden utilizar tres procesos de embutición profunda para reducir a su vez el radio del filete. El coeficiente de dibujo total m total = 0.366 se asigna al proceso de dibujo de tres vías, y se puede seleccionar m 1 = 0.56, m 2 = 0.805, m 3 = 0.812.
m 1 × m 2 × m 3 = 0.56 × 0.805 × 0.812 = 0.366
3) Proceso de combinación y determinación de secuencia
Para las piezas de estampado con muchos procesos, como la carcasa exterior, primero se puede determinar el proceso básico de las piezas, y luego se puede considerar la posible combinación de clasificación de todos los procesos básicos. Se analizan y comparan los diversos esquemas de proceso así obtenidos, a partir de los cuales se determina la mejor solución adecuada para la producción real.
El proceso básico de la carcasa exterior es:
Blanking φ 65 mm, primer dibujo,
El segundo dibujo profundo (ver Figura 8-11b),
El tercer dibujo profundo (ver Figura 8.2.5c) y el orificio inferior de φ 11 mm (ver Figura 8.2.5d),
Bridas φ 16.5 mm (ver Figura 8.2.5e),
Perfore tres agujeros pequeños de φ 3.2 mm (consulte la Figura 8.2.5f),
Recorte φ 50 mm (ver Figura 8.2.5g).
Un total de ocho procesos básicos, según los cuales se pueden descargar las siguientes cinco opciones de proceso:
Opción 1: la supresión se combina con el primer dibujo (consulte la Figura 8.2.5a), y el resto se basa en el proceso básico.
Opción II:
La supresión se combina con el primer dibujo, y el orificio inferior de φ 11 mm se combina con la brida (consulte la Figura 8.2.6a). Los tres pequeños orificios de φ 3.2 mm se combinan con el recorte (ver Figura 8.2.6b), y el resto se basa en el proceso básico. .
tercera solución:
La supresión se combina con el primer dibujo, y el orificio inferior de φ 11 mm se combina con los tres orificios pequeños de φ 3,2 mm (consulte la Figura 8.2.7a). El reborde se recorta con el recorte (consulte la Figura 8.2.7b), y el resto se basa en el proceso básico.
Opcion 4:
Blanking, primer embutido profundo y punzonado composite Compuesto de orificio inferior de 11 mm (ver Figura 8.2.8), el resto de acuerdo con el proceso básico. Opción 5: utilice troqueles progresivos o estampados en una prensa automática de varias estaciones.
Análisis y comparación de los cinco esquemas anteriores, se puede ver que en el esquema 2, el orificio de perforación de φ 11 mm se combina con la brida, debido al pequeño grosor de la pared del molde
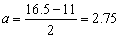
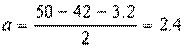
En la opción tres,
Aunque resuelve la contradicción de que la pared del molde anterior es demasiado delgada. Sin embargo, cuando el orificio inferior de φ 11 mm se combina con los tres orificios pequeños de φ 3.2 mm y se combinan la brida y la moldura, sus bordes de corte no están en el mismo plano y la velocidad de desgaste es diferente. Esto puede causar inconvenientes en la molienda y es difícil mantener la posición relativa después de la molienda.
En la opción cuatro,
Blanking, primer embutido profundo y punzonado composite Compuesto de orificio inferior de 11 mm, matriz de punzonado y punzón embutido profundo integrados, lo que también causará dificultad en el rectificado. En particular, después de perforar el orificio inferior dos y tres veces, una vez que el diámetro del orificio cambia, afectará la dimensión de altura de la brida y la calidad de la porción de brida.
El quinto esquema adopta un troquel progresivo o un dispositivo de alimentación automática de múltiples estaciones, que tiene una alta eficiencia de producción. La estructura del molde es compleja, el ciclo de fabricación es largo y el costo es alto. Por lo tanto, solo es adecuado para la producción en masa.
El esquema 1 no tiene las deficiencias mencionadas anteriormente, pero el grado de composición es bajo y la eficiencia de producción es baja. Sin embargo, el molde de proceso único tiene una estructura simple y un bajo costo de fabricación, lo cual es razonable en la producción de lotes pequeños y medianos, por lo que se decide adoptar el primer esquema. En el tercer proceso de embutición profunda y embridado, cuando la carrera de estampado está llegando al final, el molde puede presionarse rígidamente contra la pieza de trabajo para formar un efecto de conformación, por lo que no se requiere un proceso de conformación adicional.
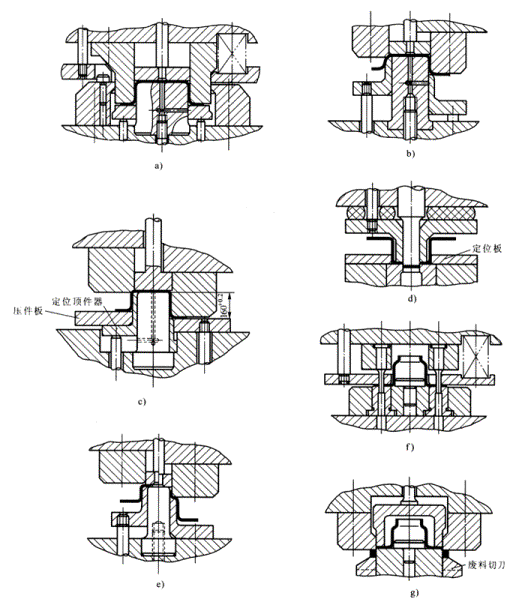
Figura 8.2.5 Estampado de diseño Estructura de molde de cada proceso