Titanium Processing 6 Key Technologies
In order to meet the performance requirements of stealth, long life, and lightweight structure, titanium alloy structural parts are widely used in modern aircraft design. Titanium alloy aircraft structural parts mainly include frames, beams, sidings, etc., and mainly have structural features such as large outline size, many grooves, deep grooves, thin walls, and often have variable inclined angle theoretical surfaces. In NC machining, the material removal rate is as high as 90% to 95%, and the characteristics of thin-walled and deep-cavity cavities account for more than 80%. It is a typical weak-rigid structure, and the processing state is extremely unstable. Because titanium alloy material has low elastic modulus, large elastic deformation, high cutting temperature, low thermal conductivity, and high chemical activity at high temperature, the sticky knife cutting phenomenon is serious, and it easily exacerbates tool wear and breakage, resulting in poor machining of titanium alloy. .
In the manufacturing process of titanium alloy aircraft monolithic frames, beams and large wall plates, due to the complex structure of parts and components, high requirements for the coordination of the shapes, the number of coordination parts of the parts, the number of intersection holes, and so on, the precision of parts manufacturing is required to be high. The metal removal during processing is relatively large, the relative rigidity is low, and the processing technology is poor. Under the influence of cutting force, cutting vibration, cutting heat and other factors, As a result, problems such as knives, deformations, and vibrations are easily caused during processing, and the quality of the processing is difficult to control. The titanium alloy itself as a typical difficult-to-machine material requires high demands on machine tools, tools, and machining processes. Therefore, the above factors cause the traditional titanium alloy aerospace structural parts to be processed only at a low level of cutting, with a long production cycle and high processing costs. Processing of titanium aerospace structural parts has become a complex manufacturing process problem in aerospace manufacturing.
Key technologies and their development trends
Titanium parts tooling fixture technology
Titanium alloy parts clamping principle is: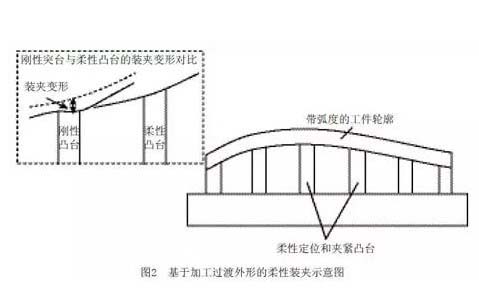
(1) The clamping force during the roughing stage should be large to prevent loosening of the part during large cutting force machining; The clamping force at the finishing stage should be small to prevent the clamping deformation.
(2) The clamping force acts on a rigid place, And the point of application as much as possible.
(3) For the thin-walled structural parts with poor rigidity, appropriate auxiliary devices should be added to increase the rigidity of the entire processing system.
Abroad, a large number of special fixtures with a high degree of automation are used. If hydraulically adjustable tooling is used, the pressure plate is automatically released when the cutting tool approaches the pinch point in the outer contour of the machined part.After the tool is cut, the platen returns to the original position and presses the part.
Some companies use the same materials as the parts being processed to make jigs and press plates that are integrated with the parts when they are mounted. During the cutting process, it is not necessary to consider avoiding fixture clamps and the machining efficiency is significantly improved.
Domestic tooling fixtures for titanium alloy aerospace structural components are lacking in more in-depth research and development, and more are simple mechanical clamping methods. The simple mechanical clamping method is affected by human factors, and the clamping force is not easy to control. There are also some types of planar single-sided structure, the thickness of the smaller parts of the clamping using vacuum adsorption, The vacuum adsorption method has a poor adsorption effect for structural members with large thickness and double-sided structure.
For less rigid workpieces, clamping force is an important factor in the deformation of the part. In the machining, the coupling effect between the clamping force and the cutting force generates a coupling effect, which leads to the redistribution of the machining residual stress and the residual stress of the workpiece, and affects the deformation of the workpiece. In particular, thin-walled parts have poor rigidity, and the elastic deformation of the clips and the pressure during processing will affect the dimensional accuracy, shape, and positional accuracy of the surface. Improper selection of the point of action of the clamping force and supporting force can also cause additional stress. For the numerical control of such parts, the "soft-based fixture based on machining transition shape" method can be used for clamping, that is, by measuring the transition shape in the free state and adjusting the height of the boss and the slope of the top. The flexible boss shape of the clamping system and the transitional shape of the part are completely fitted in a free state to avoid clamping deformation. The distribution of flexible bosses can be adjusted according to the actual situation, so that the clamping force distribution is even.
AVIC Chengfei cooperated with Tsinghua University to explore the design and manufacture of flexible tooling and flexible support components. However, the manufacturing cost and manufacturing cycle of flexible tooling are longer, and in the actual processing and clamping of large-scale titanium alloy structural parts, the “stress-free clamping” method is usually adopted. That is, a gasket is added on the rigid boss to avoid the clamping deformation, and a good application effect is obtained.
Many theoretical and practical application problems in the optimization of the fixture layout of titanium alloy structural components need to be further studied and solved. The major research and development trends in the future include the following two aspects:
The first is the design of a reasonable clamping scheme. The design of a reasonable clamping scheme effectively increases the stiffness of the process system, reduces the deformation of the workpiece, and improves the stability of the cutting process.
The second is the study of new auxiliary bearing mounting methods. For thin-walled and complex titanium alloy parts, the traditional method of using auxiliary support to increase the structural rigidity is difficult to meet the high-precision processing requirements, and the operation is complicated and inefficient. Need to break through some new auxiliary support clamping methods.
Titanium machining tool technology
With the development of high-speed cutting technology, great changes have taken place in high-speed cutting tool materials and tool manufacturing technologies, and new materials, new coatings, and new technologies have emerged. However, the current tool technology is still a technical bottleneck that limits the processing efficiency of difficult-to-machine materials such as titanium alloys. Because titanium alloy has low elastic modulus, large elastic deformation, high cutting temperature, low thermal conductivity, and high chemical activity at high temperatures, the sticky knife cutting phenomenon is serious, and it easily exacerbates tool wear and damage. Lead to titanium alloy machining process is poor. Therefore, titanium alloy machining tool technology has become one of the key technologies that restrict the efficient processing of titanium alloys.
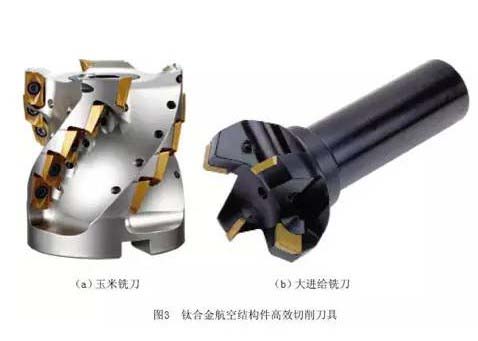
From the viewpoint of improving the metal removal rate, the current high-efficiency rough machining tools for titanium alloy aerostructure parts mainly include corn milling cutters, plug-in milling cutters, large feed milling cutters, and combined cutters . Among them, the use of corn, plunge milling cutters, and combination tools have certain requirements on the power and torque of the machine tool, and the large feed milling cutter has no special requirements on the power, torque and rigidity of the machine tool. Existing processing applications have shown that the use of large feed milling cutters can effectively increase cutting efficiency by more than 50%.
Starting from the precision of the control parts, the high-efficiency finishing tools for titanium aerospace structural parts are mainly spiral end mills. The use of dense-tooth tools (5 to 10 teeth) can significantly improve the machining surface roughness, while the use of unequal-pitch end mills can effectively increase the limit depth of cut.
With the emergence of new types of tool materials and continuous development of new types of tools, a large amount of research work has been done at home and abroad for titanium alloy cutting tools.
For example, T. Kitagawa et al. studied the cutting mechanism of titanium alloys with carbide cutting tools. It was shown that the grain size and Co content of carbide cutting tools directly affect the performance of cutting titanium alloys, and pointed out that YG type hard Alloy tools are more suitable for machining titanium alloys.
J. Vigneau studied the cutting performance of coated cutting tools for titanium alloys. The traditional coatings are mostly TiC and TiCN coatings. In the cutting process, Ti elements tend to have affinity with the workpiece and accelerate tool wear. Because of its high hardness, good heat resistance and high stability, CBN is a good tool for high-speed cutting of titanium alloys. The cost of such tools is relatively expensive, and domestic institutions have not conducted in-depth research.
In terms of tool structure design, G. D. Vasilyuk increased the cutting damping by increasing the radius of the tool tip arc, thus eliminating chatter;
C.R.LIU suppresses chatter by controlling the rake angle, relief angle and cutting edge angle of the tool during the cutting process;
The German scholar V. Sellmeiert conducted experimental and theoretical studies on the stability of unequal-pitch end mills.
Domestically, a large number of studies have also been conducted on titanium alloy cutting tools. Under the support of a number of national basic scientific research projects, Chengdu Chengfei CNC Factory has cooperated with a number of domestic universities in terms of high-speed and high-efficiency cutting tools for titanium alloys. The element diffusion, chemical reaction, and mutual adhesion and melting between the components of the tool and the workpiece were studied. A reasonable matching relationship model and matching design theory for mechanical, physical and chemical properties of cutting tools and titanium alloys were established. The tool wear and breakage mechanism under high-speed cutting conditions, and the effect of different cooling methods on the machining performance and tool life of titanium alloy were studied. A tool life model for high-speed machining of titanium alloy was established. Based on the multi-degree-of-freedom nonlinear dynamic model based on the matching relationship between tool and workpiece stiffness, a high material removal rate and high machined surface quality under flutter-free stable cutting are optimized. A matching relationship model between tool stiffness and workpiece stiffness is established. Through the research on the influence of helix angles and inter-tooth angles on the high-speed machining vibration of cemented carbide end mills, it was found that the use of asymmetrical structure between the changing angles and the deep groove structure can effectively improve the cutting stability of titanium alloys. And independently designed for the efficient processing of titanium alloy solid carbide cutting tools.
Comprehensive technology accumulation and experience summary of high-speed and high-efficiency processing of titanium alloys by Chengdu Chengfei Company's CNC plant. The key technologies needed to achieve high-speed, high-efficiency and high-precision machining of titanium alloys include the following aspects:
Titanium alloy high-speed cutting tool, reducing the cutting force in the direction of direction, to ensure adequate cutting tool cutting process stiffness, to meet the requirements to inhibit cutting chatter; Titanium alloy cutting tool materials and structures need to reduce the adhesion and diffusion wear of titanium alloy during high-speed machining, and increase the tool life; High-speed machining of titanium alloys requires sufficient tool cooling to reduce the cutting temperature and increase tool life.
Surface quality control technology
The surface quality of titanium alloy parts is related to their service life and performance, which is the focus of high-speed and high-efficiency cutting. Due to the requirements of the design structure, aircraft parts often require a variety of tools for machining. Seams between parts of the tool such that the surface quality is unstable, At the same time, due to the lack of systematic research on cutting parameters, it also has a great influence on the quality of surface processing of parts. Research on surface roughness, hardness and residual stress is an important part of surface quality research.
Surface roughness research:
In the cutting process, not only the relative movement of the tool workpiece, the geometric parameters of the tool have influence on the roughness, vibration, tool wear, cutting deformation, cutting heat and other factors can not be ignored. H. Parisn considered the dynamic characteristics of the processing system and established a prediction model for high-speed milling surface roughness. Shandong University Chenjian Ling studied the effects of milling parameters such as roughness, surface microstructure through the test. The geometrical characteristics of the relative movement of the workpiece and the tool were integrated, and a theoretical model of the surface roughness of the titanium alloy milling was established, and the formation mechanism was revealed.
Hardening research:
In the cutting process, due to the combined effect of the plastic deformation and thermal softening of the material, the machined surface is hardened. Work hardening has an effect on the material's fatigue strength and wear resistance. 1950, Oxley and other scholars began work hardening research takes into account the impact of the phenomenon in the processing at right angles to the cutting model. C. R. Li applied the finite element method to study the hardness distribution of the workpiece surface at low speed, and established the model of the machined surface deformation parameters based on the length of the shear surface.
Residual stress research:
The residual stress caused by cutting has an important influence on the part deformation, stress corrosion and fatigue life. N. Fang et al. studied the effect of tool geometry on residual stress. Japanese scholar Migu Mao studied the mechanism of the residual stress on the machined surface of a turning workpiece. The South China University of Science and Technology in the early 20th century from the 1980s to the early 1990s began the cutting process of residual stress generation mechanism of theoretical and experimental research.
In short, the surface quality control technology of titanium alloy structural parts involves many aspects such as machine tools, cutting tools, cutting parameters, cutting path, cooling lubrication, and clamping. At present, Chengfei conducts research on the surface quality control technology of titanium alloy structural parts, mainly through the use of high-performance solid carbide tools, control of the machining allowance, and the use of physical simulation methods to optimize the reduction of cutting forces. To ensure that the surface roughness of parts, work hardening and residual stress meet the design requirements. However, researches on the surface integrity of high-speed milling machining of titanium alloys, especially Ti6Al4V, such as the formation mechanism of roughness, work-hardening and residual stress, and the intrinsic link between them, need to be further studied.
Thin-walled parts processing and knife control
The processing of weak rigid parts is a complex manufacturing process problem. In addition to the difficult-to-machine characteristics of titanium alloy materials, the thin-walled structural characteristics of titanium alloy weak rigid parts make processing more difficult, mainly in:
(1) The dimensional accuracy of the processing is difficult to control. The use of a large number of thin-walled parts, especially large-size thin-walled parts, has the characteristics of thin walls and deep cavity. It is easy to produce processing distortions, and the dimensional accuracy of parts is difficult to guarantee;
(2) The surface quality is difficult to guarantee. The deep cavity thin-walled structural characteristics and the characteristics of the titanium alloy's own materials, resulting in the titanium alloy monolithic structural parts in the processing process is easy to produce chatter, so that the surface quality deterioration;
(3) It is difficult to improve the processing efficiency. The rigidity of the workpiece is weak, and it is easy to produce chatter vibration. As a result, the traditional titanium alloy monolithic component processing can only be performed at a low cutting amount level, and the production cycle is long and the cost is high.
During the machining of thin-walled parts, due to the cutting force, the tool and the workpiece will have a certain degree of elastic deformation. The CAD/CAM system is based on the ideal geometry of the part when planning the tool path and selecting the process parameters, and does not consider factors such as the workpiece and tool deformation, resulting in a deviation between the actual machining surface and the theoretical value. Therefore, the processing is the most prominent process problem in the machining of thin-walled parts. Domestic and foreign scientific research institutions and related companies have invested a lot of effort in predicting and controlling thin-walled parts.
The research abroad mainly focuses on the analysis and prediction of the amount of the knife based on the 3D milling force modeling. Among them, Yusuf Altintas, who conducted research earlier and has a wider impact, built a three-dimensional cutting force model on the basis of finite element analysis. A study was made of the distribution of the knives and their distribution on the surface of the workpiece resulting from the machining of the thin-walled part of the integral cutter. The French Plilippe Depince used the contact point relationship between the tool and the workpiece to study the effect of the elastic deformation characteristics of the tool on the geometrical accuracy of the workpiece surface during machining. It was found that the amount of tooling obtained through the contact point analysis is more consistent with the actual situation than the traditional tool that only considers the tool and the knife yields the tool.
In recent years, more in-depth studies have been conducted on the cutting force modeling of thin-walled parts, the stability of the cutting process, the prediction and control of the geometric accuracy of the workpiece surface, and the elastic deformation of the tool. Among them, AVIC Chengdu Aircraft Industry (Group) Co., Ltd. has become a high-performance cutting process system by integrating machine tools, tooling, cutting tools, and machining processes, making the machining efficiency of titanium alloy thin-walled parts increase by 20% in the past 5 years. There are very few domestic aviation companies that have the capacity to produce thin-walled titanium alloy components. With funding from the National 863 “High-speed Cutting Technology and Application of Titanium Alloy Thin-walled Parts”, Chengdu Chengfei Co., Ltd. and Shandong University have established a system process method based on paraffin-base composite materials to assist titanium steel thin-walled parts in high-efficiency machining. Formed a complete set of processes including wax-based composite formulations, paraffin-based composites melting, filling, recycling, etc. The new titanium alloy thin-walled paraffin-assisted reinforcement device developed and applied for national invention patents. Can effectively solve the titanium alloy structural parts processing problems, to achieve processing molding, reduce the titanium alloy thin-walled parts in the process of vibration.
The experimental data show that: with paraffin-based composite reinforcement, the vibration acceleration of titanium alloy thin-walled parts is reduced by 86.4% compared with that without reinforcement measures, and the web deformation is reduced by 58.6%, effectively increasing the ultra-small size. Size thin-walled structure processing capacity.
Research and Application of Deformation Control Technology
Aerostructure deformation can be divided into two categories:
Local deformation of the structure and overall deformation of the profile. The local deformation of the structure occurs mainly in the cutting process, usually manifested as the knife, local bending, etc. Its scale is limited to the vicinity of the contact area between the tool and the workpiece. The overall contour deformation is mainly represented by the overall bending and twisting after the cutting process is completed (such as after the fixture is removed), as well as the elongation and shortening during the part placement process, and the deformation amount is proportional to the outline size of the structural component. The large-size monolithic structural parts are often represented by the overall deformation of the contour after processing, which is mainly caused by the re-equilibrium distribution of internal stress after massive removal of materials. Thermal expansion and contraction caused by temperature changes and natural aging during placement are also important factors that cause deformation of the overall profile.
In view of the complexity of the deformation of the titanium alloy monolithic structural parts, follow-up studies have the following issues to note:
(1) The deformation of the titanium aerospace aeronautical structural part is the result of a combination of multiple factors, including the initial residual stress of the blank, the characteristics of the workpiece structure, the material properties, and the technological process, etc. Systematic analysis should be carried out on different structural parts to identify the key factors leading to the deformation of the process and to take targeted control measures.
(2) Most of the researches on the deformation of thin-walled parts are based on the finite element method. Some laws of processing and deformation of thin-walled structural parts have been obtained, and corresponding deformation control measures have been proposed, which lack systematic theoretical basis. In the analysis process, only the single factor that causes the deformation is often considered and has a certain degree of one-sidedness.
Research and Application of Cooling Lubrication Technology
In the process of NC machining of titanium alloy structural parts, the high temperature, high pressure, and high frequency impact of the knife/work friction contact area pose severe tests on the tool performance. The sharp wear of the tool is often the key factor restricting the improvement of the cutting efficiency. Facing the high requirements of modern manufacturing technology in terms of “high efficiency, low energy consumption, and environmental protection”, How to choose a reasonable and effective cooling lubrication method to improve the knife/work friction state and inhibit tool wear, thereby improving the processing quality and processing efficiency, At the same time, the processing process is environmentally friendly, and it is an important technical element that must be taken into consideration when optimizing the selection of the cooling lubrication method for numerical control machining of titanium aerospace structural parts.
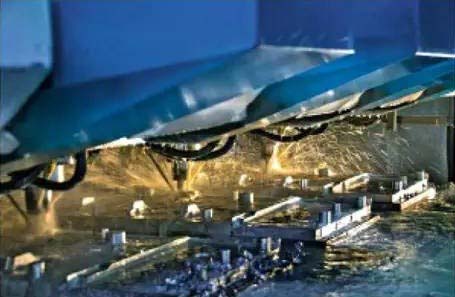
To solve the cutting problem of titanium alloy materials requires the use of high-temperature-resistant high-performance tools and effective cooling and lubrication of the cutting tools. In the conventional speed cutting of titanium alloys, wet cutting is generally adopted so as to reduce the temperature in the cutting zone and thus extend the service life of the cutter. However, the manufacturing, use, treatment, and discharge of cutting fluids consume large amounts of energy and resources and cause environmental pollution. If high-speed wet cutting titanium alloys such as emulsions are used, tool life is extremely low due to thermal fatigue damage. At present, in the high-speed processing of titanium alloys, cooling lubrication methods such as air-cooling and micro-lubrication under normal or low temperature conditions are mainly used, and the gaseous media mainly include air, N2, and CO2. In addition, the use of liquid nitrogen cooling high-speed processing of titanium alloy, can effectively extend the tool life, but the tool cooling device requirements are higher, it is not easy to promote the application.
In view of the research on the cooling lubrication methods of difficult-to-machine materials such as titanium alloys, many tool manufacturers and colleges and universities at home and abroad have carried out a large number of experimental studies. In Germany, especially institutions such as Darmstadt University of Technology, Aachen University of Technology, Braunschweig University of Technology and Dortmund University of Technology, in the titanium alloy cutting mechanism, finite element model analysis, simulation, cutting test and adoption A series of studies have been carried out on different cooling methods. Among them, the Machine Tool Laboratory (WZL) of Aachen University of Technology also works with cutting tools such as Iscar, Kennametal, Seco Tools and Sandvik. Close cooperation has been carried out with research including high-pressure cooling and other technologies. From the information provided by Iscar, you can learn about the chip formation when turning titanium alloys under different cooling lubrication pressures. When large-flow external cooling is performed with a pressure of 2 MPa, long-winding-shaped chips are generated; When internal cooling with 8MPa pressure is used, the chips are broken into small arc-shaped chips under high-pressure impact; If 30 MPa ultra high pressure is used for internal cooling, needle-shaped chips will be changed. It is not difficult to see from the above examples that high-pressure cooling can control chip formation, improve the reliability of the cutting process, and increase the amount of cutting.
In recent years, China has made great progress in the theoretical research and application of titanium alloy cooling lubrication. It has been shown that in the high-speed cutting of titanium alloys, the use of ordinary cutting fluids will exacerbate the spalling frequency of the titanium alloy material on the bonding surface of the tool, and increase the bond peeling of the tool coating. Therefore, the general cutting fluid has the tendency of aggravating the wear of the composite coating tool, and the traditional cutting fluid will also cause the cooling stroke of the milling tool to be quenched during the processing of the titanium alloy. As a result, the thermal stress gradient of the tool is aggravated, and the formation of thermal cracks on the surface of the tool aggravates tool wear and damage. Therefore, when using a diamond tool to cut titanium alloy parts, a new type of processing technology using carbon dioxide, water and vegetable oil atomized mist mixture as a cooling medium can be used to achieve the purpose of cooling, lubricating, and protecting diamond tools. In addition, the use of low-temperature nitrogen gas jet combined with micro-lubrication of high-speed milling of titanium alloys can effectively reduce the milling force and suppress tool wear. Under low-temperature nitrogen jet conditions, as long as the formation and expansion of thermal cracking does not cause tool chipping and flaking of the blade surface, further reduction of the temperature of the cryogenic nitrogen gas will increase the service life of the tool.
In the manufacturing process of titanium alloy aircraft monolithic frames, beams and large wall plates, due to the complex structure of parts and components, high requirements for the coordination of the shapes, the number of coordination parts of the parts, the number of intersection holes, and so on, the precision of parts manufacturing is required to be high. The metal removal during processing is relatively large, the relative rigidity is low, and the processing technology is poor. Under the influence of cutting force, cutting vibration, cutting heat and other factors, As a result, problems such as knives, deformations, and vibrations are easily caused during processing, and the quality of the processing is difficult to control. The titanium alloy itself as a typical difficult-to-machine material requires high demands on machine tools, tools, and machining processes. Therefore, the above factors cause the traditional titanium alloy aerospace structural parts to be processed only at a low level of cutting, with a long production cycle and high processing costs. Processing of titanium aerospace structural parts has become a complex manufacturing process problem in aerospace manufacturing.
Key technologies and their development trends
Titanium parts tooling fixture technology
Titanium alloy parts clamping principle is:
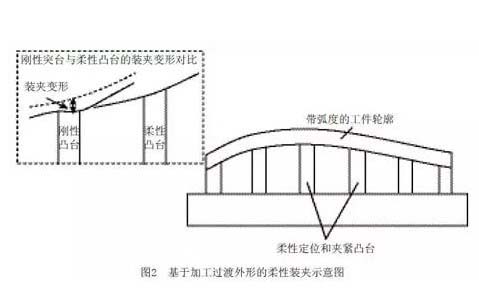
(1) The clamping force during the roughing stage should be large to prevent loosening of the part during large cutting force machining; The clamping force at the finishing stage should be small to prevent the clamping deformation.
(2) The clamping force acts on a rigid place, And the point of application as much as possible.
(3) For the thin-walled structural parts with poor rigidity, appropriate auxiliary devices should be added to increase the rigidity of the entire processing system.
Abroad, a large number of special fixtures with a high degree of automation are used. If hydraulically adjustable tooling is used, the pressure plate is automatically released when the cutting tool approaches the pinch point in the outer contour of the machined part.After the tool is cut, the platen returns to the original position and presses the part.
Some companies use the same materials as the parts being processed to make jigs and press plates that are integrated with the parts when they are mounted. During the cutting process, it is not necessary to consider avoiding fixture clamps and the machining efficiency is significantly improved.
Domestic tooling fixtures for titanium alloy aerospace structural components are lacking in more in-depth research and development, and more are simple mechanical clamping methods. The simple mechanical clamping method is affected by human factors, and the clamping force is not easy to control. There are also some types of planar single-sided structure, the thickness of the smaller parts of the clamping using vacuum adsorption, The vacuum adsorption method has a poor adsorption effect for structural members with large thickness and double-sided structure.
For less rigid workpieces, clamping force is an important factor in the deformation of the part. In the machining, the coupling effect between the clamping force and the cutting force generates a coupling effect, which leads to the redistribution of the machining residual stress and the residual stress of the workpiece, and affects the deformation of the workpiece. In particular, thin-walled parts have poor rigidity, and the elastic deformation of the clips and the pressure during processing will affect the dimensional accuracy, shape, and positional accuracy of the surface. Improper selection of the point of action of the clamping force and supporting force can also cause additional stress. For the numerical control of such parts, the "soft-based fixture based on machining transition shape" method can be used for clamping, that is, by measuring the transition shape in the free state and adjusting the height of the boss and the slope of the top. The flexible boss shape of the clamping system and the transitional shape of the part are completely fitted in a free state to avoid clamping deformation. The distribution of flexible bosses can be adjusted according to the actual situation, so that the clamping force distribution is even.
AVIC Chengfei cooperated with Tsinghua University to explore the design and manufacture of flexible tooling and flexible support components. However, the manufacturing cost and manufacturing cycle of flexible tooling are longer, and in the actual processing and clamping of large-scale titanium alloy structural parts, the “stress-free clamping” method is usually adopted. That is, a gasket is added on the rigid boss to avoid the clamping deformation, and a good application effect is obtained.
Many theoretical and practical application problems in the optimization of the fixture layout of titanium alloy structural components need to be further studied and solved. The major research and development trends in the future include the following two aspects:
The first is the design of a reasonable clamping scheme. The design of a reasonable clamping scheme effectively increases the stiffness of the process system, reduces the deformation of the workpiece, and improves the stability of the cutting process.
The second is the study of new auxiliary bearing mounting methods. For thin-walled and complex titanium alloy parts, the traditional method of using auxiliary support to increase the structural rigidity is difficult to meet the high-precision processing requirements, and the operation is complicated and inefficient. Need to break through some new auxiliary support clamping methods.
Titanium machining tool technology
With the development of high-speed cutting technology, great changes have taken place in high-speed cutting tool materials and tool manufacturing technologies, and new materials, new coatings, and new technologies have emerged. However, the current tool technology is still a technical bottleneck that limits the processing efficiency of difficult-to-machine materials such as titanium alloys. Because titanium alloy has low elastic modulus, large elastic deformation, high cutting temperature, low thermal conductivity, and high chemical activity at high temperatures, the sticky knife cutting phenomenon is serious, and it easily exacerbates tool wear and damage. Lead to titanium alloy machining process is poor. Therefore, titanium alloy machining tool technology has become one of the key technologies that restrict the efficient processing of titanium alloys.
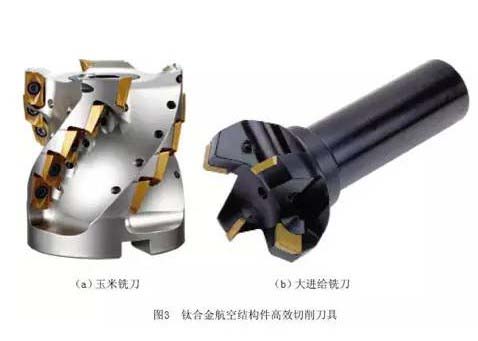
From the viewpoint of improving the metal removal rate, the current high-efficiency rough machining tools for titanium alloy aerostructure parts mainly include corn milling cutters, plug-in milling cutters, large feed milling cutters, and combined cutters . Among them, the use of corn, plunge milling cutters, and combination tools have certain requirements on the power and torque of the machine tool, and the large feed milling cutter has no special requirements on the power, torque and rigidity of the machine tool. Existing processing applications have shown that the use of large feed milling cutters can effectively increase cutting efficiency by more than 50%.
Starting from the precision of the control parts, the high-efficiency finishing tools for titanium aerospace structural parts are mainly spiral end mills. The use of dense-tooth tools (5 to 10 teeth) can significantly improve the machining surface roughness, while the use of unequal-pitch end mills can effectively increase the limit depth of cut.
With the emergence of new types of tool materials and continuous development of new types of tools, a large amount of research work has been done at home and abroad for titanium alloy cutting tools.
For example, T. Kitagawa et al. studied the cutting mechanism of titanium alloys with carbide cutting tools. It was shown that the grain size and Co content of carbide cutting tools directly affect the performance of cutting titanium alloys, and pointed out that YG type hard Alloy tools are more suitable for machining titanium alloys.
J. Vigneau studied the cutting performance of coated cutting tools for titanium alloys. The traditional coatings are mostly TiC and TiCN coatings. In the cutting process, Ti elements tend to have affinity with the workpiece and accelerate tool wear. Because of its high hardness, good heat resistance and high stability, CBN is a good tool for high-speed cutting of titanium alloys. The cost of such tools is relatively expensive, and domestic institutions have not conducted in-depth research.
In terms of tool structure design, G. D. Vasilyuk increased the cutting damping by increasing the radius of the tool tip arc, thus eliminating chatter;
C.R.LIU suppresses chatter by controlling the rake angle, relief angle and cutting edge angle of the tool during the cutting process;
The German scholar V. Sellmeiert conducted experimental and theoretical studies on the stability of unequal-pitch end mills.
Domestically, a large number of studies have also been conducted on titanium alloy cutting tools. Under the support of a number of national basic scientific research projects, Chengdu Chengfei CNC Factory has cooperated with a number of domestic universities in terms of high-speed and high-efficiency cutting tools for titanium alloys. The element diffusion, chemical reaction, and mutual adhesion and melting between the components of the tool and the workpiece were studied. A reasonable matching relationship model and matching design theory for mechanical, physical and chemical properties of cutting tools and titanium alloys were established. The tool wear and breakage mechanism under high-speed cutting conditions, and the effect of different cooling methods on the machining performance and tool life of titanium alloy were studied. A tool life model for high-speed machining of titanium alloy was established. Based on the multi-degree-of-freedom nonlinear dynamic model based on the matching relationship between tool and workpiece stiffness, a high material removal rate and high machined surface quality under flutter-free stable cutting are optimized. A matching relationship model between tool stiffness and workpiece stiffness is established. Through the research on the influence of helix angles and inter-tooth angles on the high-speed machining vibration of cemented carbide end mills, it was found that the use of asymmetrical structure between the changing angles and the deep groove structure can effectively improve the cutting stability of titanium alloys. And independently designed for the efficient processing of titanium alloy solid carbide cutting tools.
Comprehensive technology accumulation and experience summary of high-speed and high-efficiency processing of titanium alloys by Chengdu Chengfei Company's CNC plant. The key technologies needed to achieve high-speed, high-efficiency and high-precision machining of titanium alloys include the following aspects:
Titanium alloy high-speed cutting tool, reducing the cutting force in the direction of direction, to ensure adequate cutting tool cutting process stiffness, to meet the requirements to inhibit cutting chatter; Titanium alloy cutting tool materials and structures need to reduce the adhesion and diffusion wear of titanium alloy during high-speed machining, and increase the tool life; High-speed machining of titanium alloys requires sufficient tool cooling to reduce the cutting temperature and increase tool life.
Surface quality control technology
The surface quality of titanium alloy parts is related to their service life and performance, which is the focus of high-speed and high-efficiency cutting. Due to the requirements of the design structure, aircraft parts often require a variety of tools for machining. Seams between parts of the tool such that the surface quality is unstable, At the same time, due to the lack of systematic research on cutting parameters, it also has a great influence on the quality of surface processing of parts. Research on surface roughness, hardness and residual stress is an important part of surface quality research.
Surface roughness research:
In the cutting process, not only the relative movement of the tool workpiece, the geometric parameters of the tool have influence on the roughness, vibration, tool wear, cutting deformation, cutting heat and other factors can not be ignored. H. Parisn considered the dynamic characteristics of the processing system and established a prediction model for high-speed milling surface roughness. Shandong University Chenjian Ling studied the effects of milling parameters such as roughness, surface microstructure through the test. The geometrical characteristics of the relative movement of the workpiece and the tool were integrated, and a theoretical model of the surface roughness of the titanium alloy milling was established, and the formation mechanism was revealed.
Hardening research:
In the cutting process, due to the combined effect of the plastic deformation and thermal softening of the material, the machined surface is hardened. Work hardening has an effect on the material's fatigue strength and wear resistance. 1950, Oxley and other scholars began work hardening research takes into account the impact of the phenomenon in the processing at right angles to the cutting model. C. R. Li applied the finite element method to study the hardness distribution of the workpiece surface at low speed, and established the model of the machined surface deformation parameters based on the length of the shear surface.
Residual stress research:
The residual stress caused by cutting has an important influence on the part deformation, stress corrosion and fatigue life. N. Fang et al. studied the effect of tool geometry on residual stress. Japanese scholar Migu Mao studied the mechanism of the residual stress on the machined surface of a turning workpiece. The South China University of Science and Technology in the early 20th century from the 1980s to the early 1990s began the cutting process of residual stress generation mechanism of theoretical and experimental research.
In short, the surface quality control technology of titanium alloy structural parts involves many aspects such as machine tools, cutting tools, cutting parameters, cutting path, cooling lubrication, and clamping. At present, Chengfei conducts research on the surface quality control technology of titanium alloy structural parts, mainly through the use of high-performance solid carbide tools, control of the machining allowance, and the use of physical simulation methods to optimize the reduction of cutting forces. To ensure that the surface roughness of parts, work hardening and residual stress meet the design requirements. However, researches on the surface integrity of high-speed milling machining of titanium alloys, especially Ti6Al4V, such as the formation mechanism of roughness, work-hardening and residual stress, and the intrinsic link between them, need to be further studied.
Thin-walled parts processing and knife control
The processing of weak rigid parts is a complex manufacturing process problem. In addition to the difficult-to-machine characteristics of titanium alloy materials, the thin-walled structural characteristics of titanium alloy weak rigid parts make processing more difficult, mainly in:
(1) The dimensional accuracy of the processing is difficult to control. The use of a large number of thin-walled parts, especially large-size thin-walled parts, has the characteristics of thin walls and deep cavity. It is easy to produce processing distortions, and the dimensional accuracy of parts is difficult to guarantee;
(2) The surface quality is difficult to guarantee. The deep cavity thin-walled structural characteristics and the characteristics of the titanium alloy's own materials, resulting in the titanium alloy monolithic structural parts in the processing process is easy to produce chatter, so that the surface quality deterioration;
(3) It is difficult to improve the processing efficiency. The rigidity of the workpiece is weak, and it is easy to produce chatter vibration. As a result, the traditional titanium alloy monolithic component processing can only be performed at a low cutting amount level, and the production cycle is long and the cost is high.
During the machining of thin-walled parts, due to the cutting force, the tool and the workpiece will have a certain degree of elastic deformation. The CAD/CAM system is based on the ideal geometry of the part when planning the tool path and selecting the process parameters, and does not consider factors such as the workpiece and tool deformation, resulting in a deviation between the actual machining surface and the theoretical value. Therefore, the processing is the most prominent process problem in the machining of thin-walled parts. Domestic and foreign scientific research institutions and related companies have invested a lot of effort in predicting and controlling thin-walled parts.
The research abroad mainly focuses on the analysis and prediction of the amount of the knife based on the 3D milling force modeling. Among them, Yusuf Altintas, who conducted research earlier and has a wider impact, built a three-dimensional cutting force model on the basis of finite element analysis. A study was made of the distribution of the knives and their distribution on the surface of the workpiece resulting from the machining of the thin-walled part of the integral cutter. The French Plilippe Depince used the contact point relationship between the tool and the workpiece to study the effect of the elastic deformation characteristics of the tool on the geometrical accuracy of the workpiece surface during machining. It was found that the amount of tooling obtained through the contact point analysis is more consistent with the actual situation than the traditional tool that only considers the tool and the knife yields the tool.
In recent years, more in-depth studies have been conducted on the cutting force modeling of thin-walled parts, the stability of the cutting process, the prediction and control of the geometric accuracy of the workpiece surface, and the elastic deformation of the tool. Among them, AVIC Chengdu Aircraft Industry (Group) Co., Ltd. has become a high-performance cutting process system by integrating machine tools, tooling, cutting tools, and machining processes, making the machining efficiency of titanium alloy thin-walled parts increase by 20% in the past 5 years. There are very few domestic aviation companies that have the capacity to produce thin-walled titanium alloy components. With funding from the National 863 “High-speed Cutting Technology and Application of Titanium Alloy Thin-walled Parts”, Chengdu Chengfei Co., Ltd. and Shandong University have established a system process method based on paraffin-base composite materials to assist titanium steel thin-walled parts in high-efficiency machining. Formed a complete set of processes including wax-based composite formulations, paraffin-based composites melting, filling, recycling, etc. The new titanium alloy thin-walled paraffin-assisted reinforcement device developed and applied for national invention patents. Can effectively solve the titanium alloy structural parts processing problems, to achieve processing molding, reduce the titanium alloy thin-walled parts in the process of vibration.
The experimental data show that: with paraffin-based composite reinforcement, the vibration acceleration of titanium alloy thin-walled parts is reduced by 86.4% compared with that without reinforcement measures, and the web deformation is reduced by 58.6%, effectively increasing the ultra-small size. Size thin-walled structure processing capacity.
Research and Application of Deformation Control Technology
Aerostructure deformation can be divided into two categories:
Local deformation of the structure and overall deformation of the profile. The local deformation of the structure occurs mainly in the cutting process, usually manifested as the knife, local bending, etc. Its scale is limited to the vicinity of the contact area between the tool and the workpiece. The overall contour deformation is mainly represented by the overall bending and twisting after the cutting process is completed (such as after the fixture is removed), as well as the elongation and shortening during the part placement process, and the deformation amount is proportional to the outline size of the structural component. The large-size monolithic structural parts are often represented by the overall deformation of the contour after processing, which is mainly caused by the re-equilibrium distribution of internal stress after massive removal of materials. Thermal expansion and contraction caused by temperature changes and natural aging during placement are also important factors that cause deformation of the overall profile.
In view of the complexity of the deformation of the titanium alloy monolithic structural parts, follow-up studies have the following issues to note:
(1) The deformation of the titanium aerospace aeronautical structural part is the result of a combination of multiple factors, including the initial residual stress of the blank, the characteristics of the workpiece structure, the material properties, and the technological process, etc. Systematic analysis should be carried out on different structural parts to identify the key factors leading to the deformation of the process and to take targeted control measures.
(2) Most of the researches on the deformation of thin-walled parts are based on the finite element method. Some laws of processing and deformation of thin-walled structural parts have been obtained, and corresponding deformation control measures have been proposed, which lack systematic theoretical basis. In the analysis process, only the single factor that causes the deformation is often considered and has a certain degree of one-sidedness.
Research and Application of Cooling Lubrication Technology
In the process of NC machining of titanium alloy structural parts, the high temperature, high pressure, and high frequency impact of the knife/work friction contact area pose severe tests on the tool performance. The sharp wear of the tool is often the key factor restricting the improvement of the cutting efficiency. Facing the high requirements of modern manufacturing technology in terms of “high efficiency, low energy consumption, and environmental protection”, How to choose a reasonable and effective cooling lubrication method to improve the knife/work friction state and inhibit tool wear, thereby improving the processing quality and processing efficiency, At the same time, the processing process is environmentally friendly, and it is an important technical element that must be taken into consideration when optimizing the selection of the cooling lubrication method for numerical control machining of titanium aerospace structural parts.
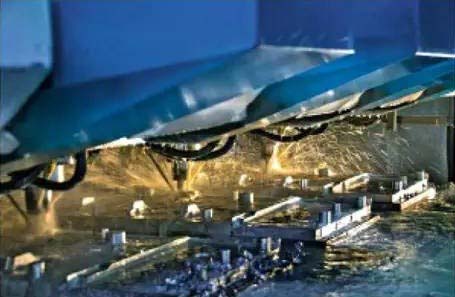
To solve the cutting problem of titanium alloy materials requires the use of high-temperature-resistant high-performance tools and effective cooling and lubrication of the cutting tools. In the conventional speed cutting of titanium alloys, wet cutting is generally adopted so as to reduce the temperature in the cutting zone and thus extend the service life of the cutter. However, the manufacturing, use, treatment, and discharge of cutting fluids consume large amounts of energy and resources and cause environmental pollution. If high-speed wet cutting titanium alloys such as emulsions are used, tool life is extremely low due to thermal fatigue damage. At present, in the high-speed processing of titanium alloys, cooling lubrication methods such as air-cooling and micro-lubrication under normal or low temperature conditions are mainly used, and the gaseous media mainly include air, N2, and CO2. In addition, the use of liquid nitrogen cooling high-speed processing of titanium alloy, can effectively extend the tool life, but the tool cooling device requirements are higher, it is not easy to promote the application.
In view of the research on the cooling lubrication methods of difficult-to-machine materials such as titanium alloys, many tool manufacturers and colleges and universities at home and abroad have carried out a large number of experimental studies. In Germany, especially institutions such as Darmstadt University of Technology, Aachen University of Technology, Braunschweig University of Technology and Dortmund University of Technology, in the titanium alloy cutting mechanism, finite element model analysis, simulation, cutting test and adoption A series of studies have been carried out on different cooling methods. Among them, the Machine Tool Laboratory (WZL) of Aachen University of Technology also works with cutting tools such as Iscar, Kennametal, Seco Tools and Sandvik. Close cooperation has been carried out with research including high-pressure cooling and other technologies. From the information provided by Iscar, you can learn about the chip formation when turning titanium alloys under different cooling lubrication pressures. When large-flow external cooling is performed with a pressure of 2 MPa, long-winding-shaped chips are generated; When internal cooling with 8MPa pressure is used, the chips are broken into small arc-shaped chips under high-pressure impact; If 30 MPa ultra high pressure is used for internal cooling, needle-shaped chips will be changed. It is not difficult to see from the above examples that high-pressure cooling can control chip formation, improve the reliability of the cutting process, and increase the amount of cutting.
In recent years, China has made great progress in the theoretical research and application of titanium alloy cooling lubrication. It has been shown that in the high-speed cutting of titanium alloys, the use of ordinary cutting fluids will exacerbate the spalling frequency of the titanium alloy material on the bonding surface of the tool, and increase the bond peeling of the tool coating. Therefore, the general cutting fluid has the tendency of aggravating the wear of the composite coating tool, and the traditional cutting fluid will also cause the cooling stroke of the milling tool to be quenched during the processing of the titanium alloy. As a result, the thermal stress gradient of the tool is aggravated, and the formation of thermal cracks on the surface of the tool aggravates tool wear and damage. Therefore, when using a diamond tool to cut titanium alloy parts, a new type of processing technology using carbon dioxide, water and vegetable oil atomized mist mixture as a cooling medium can be used to achieve the purpose of cooling, lubricating, and protecting diamond tools. In addition, the use of low-temperature nitrogen gas jet combined with micro-lubrication of high-speed milling of titanium alloys can effectively reduce the milling force and suppress tool wear. Under low-temperature nitrogen jet conditions, as long as the formation and expansion of thermal cracking does not cause tool chipping and flaking of the blade surface, further reduction of the temperature of the cryogenic nitrogen gas will increase the service life of the tool.