Stainless Steel Processing Method
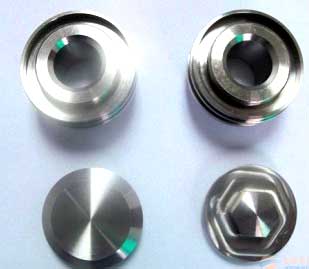
1. With the vigorous development of aviation, aerospace, petroleum, chemical, metallurgy and food industries, Stainless steel materials have been widely used, and stainless steel materials have high toughness, high thermal strength, low thermal conductivity, large plastic deformation during cutting, severe work hardening, high cutting heat, and heat dissipation problems. Causes high cutting temperature at the tip of the cutting edge, severe adhesion of the cutting edge, It is easy to produce debris, which not only aggravates the wear of cutting tools, but also affects the roughness of machined surfaces. In addition, because the chips are not easily curled and broken, the processed surface is also damaged, affecting the quality of the workpiece. In order to improve the machining efficiency and workpiece quality, it is important to accurately select the tool material, turning tool geometry and cutting amount.
2. The accuracy of the choice of tool material is the deciding factor in ensuring efficient machining of stainless steel. According to the cutting characteristics of stainless steel, the tool material should have sufficient strength, toughness, high hardness and high wear resistance, and have less adhesion to stainless steel. Commonly used tool materials are two types of cemented carbide and high speed steel. The tool with complicated shape is mainly made of high speed steel. Because high-speed steel cutting stainless steel cutting speed can not be too high, thus affecting the production efficiency.
For simpler turning tools, the tool material should be high strength, good thermal conductivity of carbide, because its hardness, wear resistance and other functions superior to high-speed steel. The commonly used cemented carbide materials are: tungsten cobalt (YG3, YG6, YG8, YG3X, YG6X), Tungsten cobalt and titanium (YT30, YT15, YT14, YT5), general class (YW1, YW2).
YG cemented carbide has good toughness and thermal conductivity, and it is not easy to bond with swarf, so it is suitable for stainless steel rough machining. The YW carbide has better hardness, wear resistance, heat resistance, oxidation resistance and toughness, and is suitable for precision turning of stainless steel.
When machining 1Cr18Ni9Ti austenite stainless steel, YT hard alloy should not be selected because the Ti in the stainless steel and the Ti in the YT cemented carbide have a pro-combination effect, and the swarf easily take away the Ti in the alloy and promote the wear of the tool.
3. Selection of geometric angle of tool
The Geometric angle of cutting tool has a great influence on the productivity of stainless steel cutting, the cost of tool resistance, the roughness of the surface to be machined, the cutting force, and the work hardening. The correct choice and improvement of tool geometry angle parameters is an effective way to ensure the quality of processing, improve efficiency and reduce costs.
(1) The size of the rake angle of the rake angle γ0 determines the sharpness and strength of the cutting edge. Increasing the rake angle can reduce the deformation of the swarm, thereby reducing the cutting force and cutting power, lowering the cutting temperature, and increasing the tool resistance cost. However, increasing the rake angle will reduce the wedge angle, reduce the blade edge strength, cause chipping, and reduce the tool resistance cost. Turning of stainless steel, without reducing the strength of the tool, the rake angle should be suitable to get bigger. When the tool front angle is large, its plastic deformation is small, the cutting force and cutting heat are reduced, the work hardening tendency is reduced, and the tool resistance cost is improved. Generally, the tool front angle should be 12° to 20°.
(2) The choice of turning angle α0 of the turning tool During the cutting process, the back angle can reduce the friction between the flank surface and the cutting surface. If the relief angle is too large, the wedge angle will decrease, so that the heat dissipation condition will be worsened, the tool edge strength will decrease, and the tool resistance cost will be reduced. If the relief angle is too small and the friction is severe, the cutting edge becomes blunt, the cutting force is increased, the cutting temperature is increased, and the tool wear is increased. In general, the angle change little, but there must be a reasonable value, the cost of resistance to facilitate advancement of the tool. When turning stainless steel, stainless steel is more elastic and plastic than ordinary carbon steel. Therefore, if the clearance angle of the tool is too small, the contact area between the cutting surface and the back angle of the turning tool will increase, and the high temperature area generated by the friction will be concentrated on the back angle of the turning tool to accelerate the wear of the turning tool and reduce the surface finish of the machined surface. Therefore, the turning angle of the lathe when turning stainless steel is slightly larger than that when turning ordinary carbon steel. However, if the back angle is too large, the blade strength will be reduced, which will directly affect the cost of turning the lathe. Therefore, in general, the lathe angle should be 6° to 10°.
(3) Choice of turning angle Kr of turning tool, When the cutting depth ap and the feed amount f are constant, reducing the main declination angle Kr can improve the heat dissipation conditions, reduce tool damage, and make the tool cut in and out smoothly. However, reducing the main deflection angle will increase the radial force and cause vibration easily during cutting. Turning stainless steel tends to have a strong tendency to harden, and is prone to vibration, which in turn makes the work hard. Therefore, the main declination angle should generally be 45° to 90°. The detailed angle should be selected according to the rigidity of the machine tool, parts, tool system and cutting amount.
(4) The inclination of the cutting edge angle λs of the turning tool can control the flow of the swarf. When the rake angle λs is negative, the swarf flows to the machined surface. When the blade inclination λs is positive, the swarf flows toward the surface to be machined. In order to prevent the swarf from scratching the machined surface, the edge angle λs is a positive value during finishing. When λs is a positive value, the blade tip is low in strength and contacts the workpiece first and is easily damaged. When λs is a negative value, the blade tip has high strength and impact resistance, which can avoid the collapse of the tool tip, and it can smoothly cut in and cut out. When turning stainless steel, the general tool edge angle should be 0° to 20°.
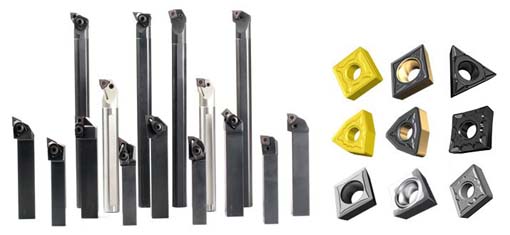
4. Choice of cutting amount
The amount of cutting volume has a great influence on production efficiency and processing quality. Therefore, after determining the geometric parameters of the tool, it is necessary to select a fair amount of cutting. When choosing the amount of cutting, Should pay attention to consider the following factors: One is to select the cutting amount according to the hardness of stainless steel and various blanks; The second is to select the amount of cutting according to the tool material, welding quality and cutting conditions of the turning tool; The third is to select the cutting amount according to the diameter of the part, the machining allowance and the accuracy of the lathe. Meanwhile, in order to prevent the built-up edge and Burr, improve the quality of the surface, when employed in the processing carbide tool, The cutting amount should be slightly lower than that of turning general carbon steel workpieces, especially the cutting speed should not be too high (vc = 50 ~ 80m/min);
The cutting depth ap should not be too small to avoid the cutting edge and the blade tip across the hardened layer, ap = 0.4 ~ 4mm; Therefore, the feed rate f is not as effective as the cutting speed, but it will affect the chip breaking and chip removal, pulling, scratching the surface of the workpiece and affecting the surface quality. The feed rate is generally f=0.1-0.5 mm/ r. Stainless steel, especially austenitic stainless steel, has good plasticity. When machining, the resulting swarf is difficult to break, increasing the friction between the swarf and the rake face of the tool and increasing the cutting force. At the same time, the work hardening will increase the hardness and strength of the material to be cut, which will also increase the cutting force. For this reason, on the basis of fair choice of tool material, tool geometry and cutting amount, a comparison of cutting force was made on stainless steel and 45 steel. The test results show that when the same cutting amount is used, the cutting force when machining stainless steel is only increased by 8.5% compared with the processing of 45 steel.
5. Fair choice of tool materials, tool geometry, and cutting amounts are all achievable for improving the efficiency of the stainless steel cutting process and the quality of the machined workpiece.
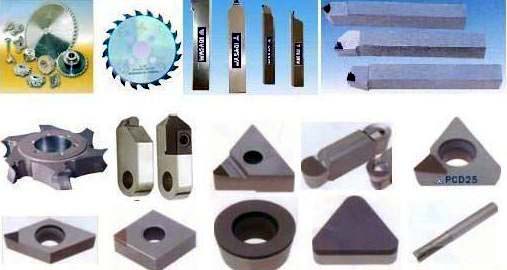