304 Stainless Steel Pipe Welding
1, Process flow
Construction preparation → Material entry, Inspection → Cutting → Discharge line, Hanger production and installation → welding → Weld polishing and pickling passivation → Weld inspection → Pipeline pressure test, flushing
2, operating points
2.1 Construction Preparation
(1) Prepare construction plans and construction schedules and establish quality work standards.
(2) Operators are mainly pipework, argon arc welders, other types of work, and argon arc welders should have a certificate issued by the relevant department.
(3) Materials for construction are prepared according to the material plan, delivered to the site, and guaranteed to be supplied as planned.
(4) on-site operating personnel in writing technical tests, field technicians, safety tests.
2.2 Welding Material Preparation
(1) The selection of pipes and fittings should be based on the use of environmental media factors, chemical composition and the use of pressure, and select the appropriate grade of products to ensure the weld metal structure and mechanical properties.
(2) Argon gas should meet the requirements of the national standard "Argon" GB4842. Argon gas with a purity of 99.96% should be used. If the impurity content is too much, the protective effect of argon will be impaired and the weld quality will be directly affected.
(3) use of cerium tungsten electrode material.
The shape and diameter of the end of the Cerium tungsten pole have a great influence on the stability of the welding process and the weld formation. The conical flat end works best, see Figure 1.1. The tungsten electrode is selected according to the thickness of the welded pipe and the welding current. The welding technical parameters are shown in Table 1.1.
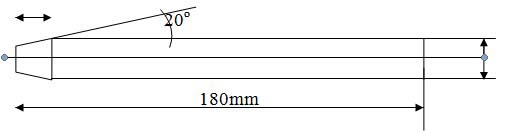
Figure 1.1Conical schematic
Table 1.1 Welding several technical parameters
(4) The welding torch uses PW-150 type Wind gun, the size of the nozzle aperture directly affects the protection effect, generally the nozzle aperture chooses Φ10mm.
3, welding methods and technical parameters
The socket type argon arc welding method makes the pipeline dissolved into one body, and it is a "no joint connection" connection mode.
3.1 Specific Construction Steps
3.1.1 After the stainless steel pipe enters the site, it shall not be in direct contact with other materials such as cement slurry, cement, mortar, mix concrete and welded steel pipes. According to the site and drawings for cutting, cutting of the pipeline and cross-section processing: Before the pipe is cut, it is confirmed that there is no damage or deformation. Use a pipe cutter (stainless steel special cutting equipment) to cut perpendicular to the axis of the pipe. If the incision is inclined, the insertion amount will be incorrect. After the removal, remove the burrs, chips, and foreign materials from the tube end.
3.1.2 The stainless steel tube had a good cutting, insert pipe socket, Schematic see 1.2, socket socket size shown in Table 1.2
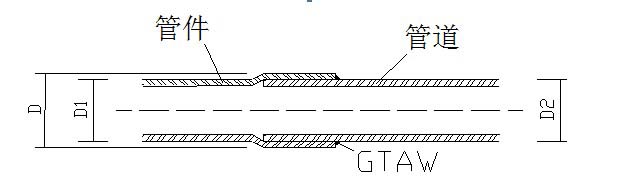
Stainless steel argon arc welding socket fitting socket Schematic 1.2
Table 1.2 Socket argon arc welded pipe socket size (mm)
3.1.3 When welding, ensure that the socket and the pipeline are on the same axis and are in a horizontal state and cannot be angled. Brush a chalk powder with a width of 40-50 mm outside the end of the socket and start the welding after drying. First spot welding, 3 to 5 points is appropriate.
3.1.4 The welding operation takes the waist as the center, the upper body radius as the power, and the upper body rotating from the right to the left. Such welding is easy to observe the weld pool and protect the weld pool better. After the normal combustion of the arc forms the molten pool, the arc moves horizontally and forward. The socket welding end for a circular ring, to control the size of the molten pool and the temperature of the molten pool. The length of the tungsten pole is 4 to 8mm, the distance between the tungsten pole and the workpiece is 1 to 1.5mm, and the distance from the nozzle to the seam is 5 to 10mm. When the welding is stopped in the middle of the welding or the welding is finished, the arc extinguishing method is used for the attenuation. That is, when arcing, the torch is lightly moved to the outside of the groove to extinguish the arc, and then the torch is immediately closed to the arc-arresting position and the air supply is continued for 3 to 5 seconds. The welding pool is cooled under the protection of delayed gas to prevent shrinkage and cracks. After welding, it is cooled in natural environment.
3.1.6 The current is adjusted to the right during welding. The specific technical parameters are shown in Table 1.1. Welding current is too large, not only easy to burn-through, welding and prone to stay undercut, tungsten and lead to burning. Welding current is too small, and an unstable arc blow, easy to produce incomplete penetration, slag and porosity and other defects. The welding speed is selected according to the size of the welding current with reference to Table 1.1. The speed is too fast, the gas protection effect is damaged, and the weld metal and tungsten are also vulnerable to oxidation defects. When it is too slow it will cause easy melting welding.
3.1.7 The principle of small current and rapidity shall be followed during welding. Corresponding current requirements shall apply to different wall thicknesses of pipes. Relying on airflow protection, rapid temperature increase and temperature reduction aim at avoiding the post-chemical temperature of 6000C~8000C so as to avoid intergranular corrosion.
3.1.8 In the absence of short circuiting, the use of short arc welding, gas protection effect, heat concentration, arc stability, uniform penetration, deformation; When the arc voltage is too high, the gas protection effect is not good, which will cause the weld metal to oxidize and produce defects such as incomplete penetration.
3.1.9 The wind speed during welding should not exceed 2m/s. When it exceeds, the windshield should block the construction area.
3.1.10 When welding in wet areas, The relative humidity within 1m of the welding arc shall not be greater than 90%. When it is greater than 90%, the welding shall be stopped.
4, weld polishing, passivation, cleaning
4.1 After welding, use the grinding machine to abrade the pipeline and weld surface excess welds.
4.2 After the welding is completed and cooled to the natural temperature, the passivation is performed using a pickling passivation paste at the welding position. The stainless steel pickling passivation paste is a chemical agent that removes the yellow, blue and black weld spots and oxide scales produced after welding and high temperature processing of stainless steel. Suitable for ferrite, austenitic and other stainless steels. It is fully pickled and passivated for stainless steel and improves its corrosion resistance, making the surface of stainless steel as bright as new.
The characteristics of pickling passivation paste: 1. The reaction speed is quick, thorough removal, moderate viscosity, easy to observe, no corrosion to the substrate.
2. Does not contain CL, P, etc. to destroy the surface of the stainless steel ions.
(1) Finished stainless steel passivation paste for construction, and passivation paste is fully stirred.
(2) Apply the passivation paste evenly to the surface of the weld of the pipe. The thickness of the paste layer is about 2~3mm. The general time is 5-15 minutes. When the scale is thick or the temperature is lower than 0°C, the reaction time should be prolonged.
(3) After pickling, rinse thoroughly with water (if there is still oxide scale after washing with water, use stainless steel wire brush or hard plastic nylon brush to remove oxide scale), Then test with litmus paper. After no reaction, water stains are wiped or dried to prepare for passivation.
Weld inspection
1. The welder must perform a 100% self-test on the surface quality of all welds.
2. Cracks, pores, unfused, Oversize undercuts and other defects are not allowed on the weld surface.
3. The external dimensions of the weld should meet the design requirements and the edge of the weld should be rounded to the base material.
4. The weld must not be severely oxidized or burned (meaning the front or back of the weld is black, slagging, etc.).
5. For the judgment of the weld effect, silver and gold are best shown in Figure 1.4, blue is good, red ash is better, ash is not good, and black is the worst.
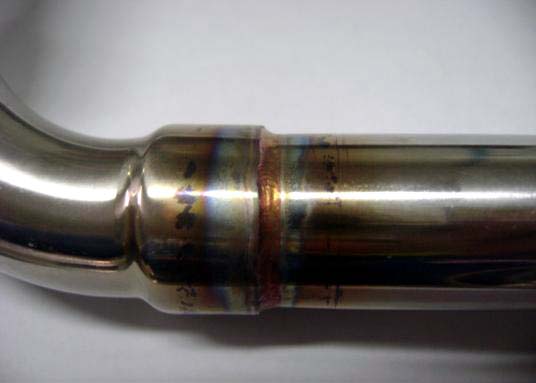
Figure 1.4 stainless steel weld effect map
Construction preparation → Material entry, Inspection → Cutting → Discharge line, Hanger production and installation → welding → Weld polishing and pickling passivation → Weld inspection → Pipeline pressure test, flushing
2, operating points
2.1 Construction Preparation
(1) Prepare construction plans and construction schedules and establish quality work standards.
(2) Operators are mainly pipework, argon arc welders, other types of work, and argon arc welders should have a certificate issued by the relevant department.
(3) Materials for construction are prepared according to the material plan, delivered to the site, and guaranteed to be supplied as planned.
(4) on-site operating personnel in writing technical tests, field technicians, safety tests.
2.2 Welding Material Preparation
(1) The selection of pipes and fittings should be based on the use of environmental media factors, chemical composition and the use of pressure, and select the appropriate grade of products to ensure the weld metal structure and mechanical properties.
(2) Argon gas should meet the requirements of the national standard "Argon" GB4842. Argon gas with a purity of 99.96% should be used. If the impurity content is too much, the protective effect of argon will be impaired and the weld quality will be directly affected.
(3) use of cerium tungsten electrode material.
The shape and diameter of the end of the Cerium tungsten pole have a great influence on the stability of the welding process and the weld formation. The conical flat end works best, see Figure 1.1. The tungsten electrode is selected according to the thickness of the welded pipe and the welding current. The welding technical parameters are shown in Table 1.1.
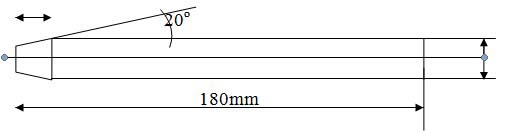
Figure 1.1Conical schematic
Table 1.1 Welding several technical parameters
Pipe diameter |
Tube thickness (mm) |
Welding current | Arc speed | Argon flow | Applied glow pole | Welding vertical angle | Welding angle |
The distance between the nozzle weldment |
DN32 DN40 |
0.8 | 30/A | 45mm/min | 5(L/min) | 1.6mm | 10o~15o | 50o~75o | ≤2mm |
DN50 | 1.0 | 35/A | 45mm/min | 5(L/min) | 1.6mm | 10o~15o | 50o~75o | ≤2mm |
DN65 | 1.2 | 40/A | 45mm/min | 5(L/min) | 1.6mm | 10o~15o | 50o~75o | ≤2mm |
DN80 DN100 |
1.5 | 45/A | 60mm/min | 5(L/min) | 1.6mm | 10o~15o | 50o~75o | ≤2mm |
3, welding methods and technical parameters
The socket type argon arc welding method makes the pipeline dissolved into one body, and it is a "no joint connection" connection mode.
3.1 Specific Construction Steps
3.1.1 After the stainless steel pipe enters the site, it shall not be in direct contact with other materials such as cement slurry, cement, mortar, mix concrete and welded steel pipes. According to the site and drawings for cutting, cutting of the pipeline and cross-section processing: Before the pipe is cut, it is confirmed that there is no damage or deformation. Use a pipe cutter (stainless steel special cutting equipment) to cut perpendicular to the axis of the pipe. If the incision is inclined, the insertion amount will be incorrect. After the removal, remove the burrs, chips, and foreign materials from the tube end.
3.1.2 The stainless steel tube had a good cutting, insert pipe socket, Schematic see 1.2, socket socket size shown in Table 1.2
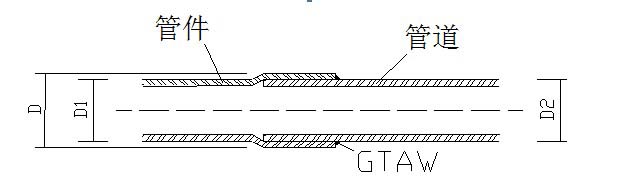
Stainless steel argon arc welding socket fitting socket Schematic 1.2
Table 1.2 Socket argon arc welded pipe socket size (mm)
Nominal diameter DN | Pipe outer diameter D1 | Tube outside diameter D | Socket inner diameter D2 | Socket length L |
15 | φ16 | 17.6 | 16+0.1~0.05 | 10 |
20 | φ22 | 24 | 20+0.05~0.2 | 10 |
25 | φ26 | 28 | 25+0.1~0.25 | 10 |
32 | φ35 | 37.6 | 32+0.1~0.35 | 12 |
40 | φ40 | 42.6 | 40+0.1~0.3 | 12 |
50 | φ50.8 | 53.4 | 50+0.1~0.3 | 15 |
65 | Φ63.5 | 67.9 | 65+0.1~0.3 | 15 |
80 | Φ76.2 | 82.2 | 80+0.1~0.3 | 15 |
100 | Φ101.6 | 107.7 | 100+0.1~0.3 | 20 |
3.1.3 When welding, ensure that the socket and the pipeline are on the same axis and are in a horizontal state and cannot be angled. Brush a chalk powder with a width of 40-50 mm outside the end of the socket and start the welding after drying. First spot welding, 3 to 5 points is appropriate.
3.1.4 The welding operation takes the waist as the center, the upper body radius as the power, and the upper body rotating from the right to the left. Such welding is easy to observe the weld pool and protect the weld pool better. After the normal combustion of the arc forms the molten pool, the arc moves horizontally and forward. The socket welding end for a circular ring, to control the size of the molten pool and the temperature of the molten pool. The length of the tungsten pole is 4 to 8mm, the distance between the tungsten pole and the workpiece is 1 to 1.5mm, and the distance from the nozzle to the seam is 5 to 10mm. When the welding is stopped in the middle of the welding or the welding is finished, the arc extinguishing method is used for the attenuation. That is, when arcing, the torch is lightly moved to the outside of the groove to extinguish the arc, and then the torch is immediately closed to the arc-arresting position and the air supply is continued for 3 to 5 seconds. The welding pool is cooled under the protection of delayed gas to prevent shrinkage and cracks. After welding, it is cooled in natural environment.
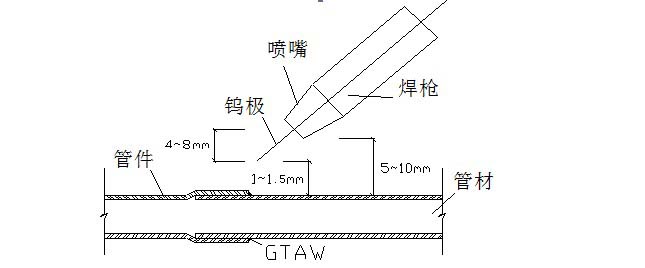
Welding operation diagram 1.3
3.1.5 When welding, observe the color of the weld. If the color of the weld is gray and black, it means that the protection of argon gas is not enough, and the flow of argon gas should be adjusted until the color of the weld is golden, blue and red.3.1.6 The current is adjusted to the right during welding. The specific technical parameters are shown in Table 1.1. Welding current is too large, not only easy to burn-through, welding and prone to stay undercut, tungsten and lead to burning. Welding current is too small, and an unstable arc blow, easy to produce incomplete penetration, slag and porosity and other defects. The welding speed is selected according to the size of the welding current with reference to Table 1.1. The speed is too fast, the gas protection effect is damaged, and the weld metal and tungsten are also vulnerable to oxidation defects. When it is too slow it will cause easy melting welding.
3.1.7 The principle of small current and rapidity shall be followed during welding. Corresponding current requirements shall apply to different wall thicknesses of pipes. Relying on airflow protection, rapid temperature increase and temperature reduction aim at avoiding the post-chemical temperature of 6000C~8000C so as to avoid intergranular corrosion.
3.1.8 In the absence of short circuiting, the use of short arc welding, gas protection effect, heat concentration, arc stability, uniform penetration, deformation; When the arc voltage is too high, the gas protection effect is not good, which will cause the weld metal to oxidize and produce defects such as incomplete penetration.
3.1.9 The wind speed during welding should not exceed 2m/s. When it exceeds, the windshield should block the construction area.
3.1.10 When welding in wet areas, The relative humidity within 1m of the welding arc shall not be greater than 90%. When it is greater than 90%, the welding shall be stopped.
4, weld polishing, passivation, cleaning
4.1 After welding, use the grinding machine to abrade the pipeline and weld surface excess welds.
4.2 After the welding is completed and cooled to the natural temperature, the passivation is performed using a pickling passivation paste at the welding position. The stainless steel pickling passivation paste is a chemical agent that removes the yellow, blue and black weld spots and oxide scales produced after welding and high temperature processing of stainless steel. Suitable for ferrite, austenitic and other stainless steels. It is fully pickled and passivated for stainless steel and improves its corrosion resistance, making the surface of stainless steel as bright as new.
The characteristics of pickling passivation paste: 1. The reaction speed is quick, thorough removal, moderate viscosity, easy to observe, no corrosion to the substrate.
2. Does not contain CL, P, etc. to destroy the surface of the stainless steel ions.
(1) Finished stainless steel passivation paste for construction, and passivation paste is fully stirred.
(2) Apply the passivation paste evenly to the surface of the weld of the pipe. The thickness of the paste layer is about 2~3mm. The general time is 5-15 minutes. When the scale is thick or the temperature is lower than 0°C, the reaction time should be prolonged.
(3) After pickling, rinse thoroughly with water (if there is still oxide scale after washing with water, use stainless steel wire brush or hard plastic nylon brush to remove oxide scale), Then test with litmus paper. After no reaction, water stains are wiped or dried to prepare for passivation.
Weld inspection
1. The welder must perform a 100% self-test on the surface quality of all welds.
2. Cracks, pores, unfused, Oversize undercuts and other defects are not allowed on the weld surface.
3. The external dimensions of the weld should meet the design requirements and the edge of the weld should be rounded to the base material.
4. The weld must not be severely oxidized or burned (meaning the front or back of the weld is black, slagging, etc.).
5. For the judgment of the weld effect, silver and gold are best shown in Figure 1.4, blue is good, red ash is better, ash is not good, and black is the worst.
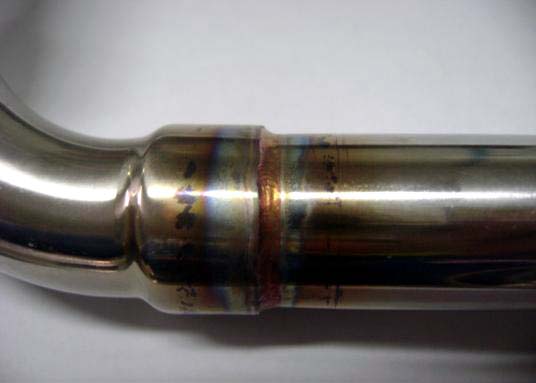
Figure 1.4 stainless steel weld effect map