What is Sheet Metal Processing?
Sheet metal processing is a pivotal technology that sheet metal technicians need to grasp. It is also an important process for forming sheet metal products. Sheet metal processing includes conventional cutting, punching, bending and other methods and process parameters.
Also includes a variety of cold stamping die structure and process parameters, various equipment working principles and operating methods, including new stamping technology and new technology. Parts sheet metal processing is called sheet metal processing.
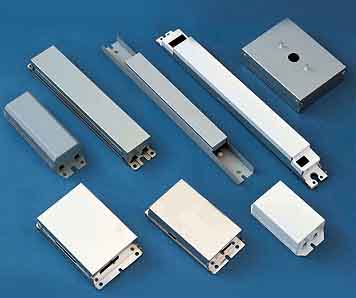
Industry terms
Each industry has its own terminology, and the sheet metal processing industry is no exception. The following 25 are common.
(1) Pressure riveting: Refers to the process of press-fastening the workpiece to the workpiece by using a punch or hydraulic press to press the riveting nut, pressure riveting screw or riveting nut column fastener.
(2) Riveting: Refers to countersinking the workpiece first. Then press the rivet nut firmly on the workpiece with punch or hydraulic press.
(3) Pulling mother: Refers to the use of similar riveting process. The process of connecting the rivet nut (POP) and other connectors firmly to the workpiece by means of a pull gun.
(4) Pull riveting: Refers to the riveting gun as a tool, using pull stud two or more than two pieces of work closely linked to the process.
(5)Rivet bond: A process in which two or more workpieces are joined together face to face with rivets. If countersunk riveting, the workpiece should be counterbored first.
(6) Cut-off angle: Refers to the process of cutting off the corner of the workpiece by using a die on a punch press or an oil press.
(7) bending: the process of forming a workpiece from a bending machine.
(8) forming: refers to the process of using a mold on a common punch or other equipment to deform the workpiece.
(9) shear material: refers to the material through the shearing machine to obtain rectangular workpiece process.
(10) Cutting: Refers to the process of the workpiece after LASER cutting or blanking of numerical control punch press.
(11) Blanking: Refers to the process of using a mold to obtain the shape of a product on an ordinary punch or other equipment.
(12) punching: refers to the process of machining holes by ordinary punches and dies.
(13) punching convex hull: Refers to the process of forming the convex shape of the workpiece in the punch or hydraulic press mold.
(14) tearing and tearing: refers to the process of forming a bridge like shape in a punch or hydraulic press mold.
(15) draw holes: also called "flanging", which refers to the process of forming circular holes on the workpiece by using dies on ordinary punching machines or other equipment.
process.
(16) Tapping: refers to the process of machining internal threads on the workpiece.
(17) Leveling: Refers to the unevenness of the workpiece before and after machining, and the use of other equipment to flatten the workpiece.
(18) back teeth: refers to the workpiece with teeth on the pre attack process, repair second times the thread.
(19) Drilling: The process of drilling holes in a workpiece using a drill or a milling machine.
(20) Chamfer: Refers to the use of molds, boring tools, grinding machines, etc., to process the sharp corners of the workpiece.
(21) punch mark: refers to the process of using a mold to punch out characters, symbols or other imprints on the workpiece.
(22) Counterbore: Refers to the process of machining a tapered hole in a workpiece to match a connector such as a countersunk head screw.
(23) clap: Refers to a certain shape of the workpiece, the transition to a smooth process.
(24) punching mesh: It means to punch a net hole on the workpiece with a die on an ordinary punch or CNC punch.
(25) reaming: The process of machining small holes on the workpiece with a drill or milling cutter into large holes.
Process flow
Selection of materials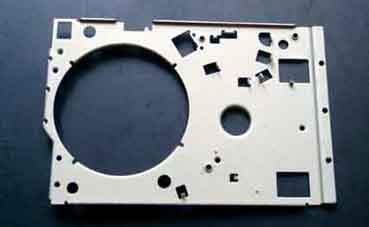
The commonly used materials for sheet metal processing include cold-rolled sheet (SPCC), hot-rolled sheet (SHCC), galvanized sheet (SECC, SGCC), copper (CU) brass, red copper, beryllium copper, aluminum (6061, 5052) 1010, 1060, 6063, hard aluminum, etc.), stainless steel (mirror, brushed surface, matte), depending on the role of the product, different materials, generally need to consider the use of the product and cost.
1. Cold-rolled plate SPCC, mainly used for electroplating and baking paint parts, low cost, easy molding, material thickness ≤ 3.2mm.
2. Hot-rolled plate SHCC, material T ≥ 3.0mm, is also used for electroplating, lacquer pieces, low cost, but difficult to shape, mainly used flat pieces.
3. Galvanized sheet SECC, SGCC, SECC electrolysis board is divided into N material and P material. N material is not used for surface treatment and the cost is high. P material is used for spraying parts.
4. Copper; mainly conductive materials, the surface treatment is nickel, chrome, or no treatment, high cost.
5. Aluminum plate; general use of surface chromate (J11-A), oxidation (conductive oxidation, chemical oxidation), high cost, silver plating, nickel plating.
6. Aluminium profiles; Cross-section structure of complex materials, used in a variety of plug-in box. The surface treatment is the same as the surface treatment of the aluminum plate.
7. Stainless steel; mainly used without any surface treatment, high cost.
Drawing review
To write the part's process flow, we must first understand the various technical requirements of the parts drawing; then the drawing review is the most important part of the preparation of the part's process flow.
1. Check the drawing is complete.
2. The relationship between drawings and views, whether the labels are clear and complete, and the dimension units are marked.
3. Assembly relations, assembly requirements focus on size.
4. The difference between the old and new drawings.
5. Translation of foreign languages.
6. Table code number conversion.
7. Mapping problems and feedback.
8. material
9. Quality requirements and process requirements
10. Official release drawings, shall be stamped with quality control chapter.
Precautions
The expansion diagram is a plan (2D) based on part diagram (3D).
1. The way of expansion should be combined, so as to save materials and workability.
2. Reasonable choice of clearance and wrapping style, T=2.0 or less gap 0.2, T=2-3 gap 0.5, wrapping edge method using long side wrapping short side (door panel)
3. Reasonable consideration of tolerance dimension: negative deviation to the end, positive deviation half; Hole size: positive difference goes to the end, negative difference takes half.
4. burr direction
5. Extraction, riveting, tearing, punching (bumps), etc., drawing a cross-sectional view
6. Check material, plate thickness, thickness tolerance
7. Special angle, the radius of bending angle (general R = 0.5) should be measured and expanded.
8. Where error-prone (similar asymmetry) should focus on the prompt
9. Where there are more sizes, add a larger image
10. Need to spray protection place must be expressed
Manufacturing processes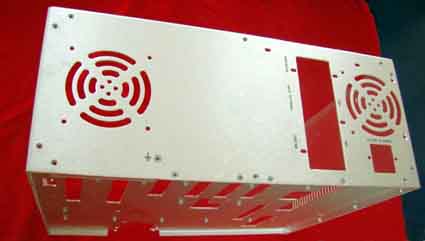
According to the difference in the structure of the sheet metal parts, the process flow may be different, but the total does not exceed the following points.
1, under the material: There are various ways of cutting, mainly in the following ways
a. Shears: Shears are used to cut strips of simple materials. It is mainly used for blank blank forming and processing.The cost is low, the precision is lower than 0.2, but can only process the no-holes and no-cornered strips or blocks.
b. Punching machine: It is the use of punching machine to divide the flat parts of the parts into one piece or multiple steps on the plate to form a variety of shape materials. Its advantages are short working hours, high efficiency, high precision, low cost, and suitable for mass production, but it is necessary to design molds.
c. NC cutting, when CNC cutting, firstly write the NC machining program, and use the programming software to compile the drawn development diagram into a recognizable program of the NC machining machine. According to these procedures, it can be used to punch flat parts of various shapes on the flat plate one by one, but its structure is affected by the structure of the cutter. The cost is low and the precision is 0.15.
d. Laser cutting is the use of laser cutting methods to cut the shape of the flat plate on a large flat plate. The same as the NC cutting need to write a laser program, it can be a variety of complex shapes of flat parts, high cost, accuracy of 0.1.
e. Sawing machine: mainly used in the cutting ,aluminum, square tube, round tube, round bar and the like, low cost and low precision.
2. Fitter: Counterbore, Tapping, Reaming, Drilling
Counterbore angle is generally 120 °C, used to pull rivets, 90°C for Countersunk Screws, tapping Inch bottom hole.
3. Flange: It is also called pumping holes and turning holes, which is to draw a slightly bigger hole on a smaller base hole and then tapping. Mainly use sheet metal with relatively thin plate thickness to increase its strength and number of thread turns to avoid slipping. Generally used for relatively thin plate thickness, its normal shallow hole flanging, the thickness does not change, When the thickness is allowed to be thinned by 30-40%, a height of 40-60% higher than the normal flange height can be obtained. When the thickness is reduced by 50%, the maximum flange height can be obtained. When the plate thickness is large, such as 2.0, 2.5, etc., the plate thickness can be directly tapped.
4. punch: It is a manufacturing process using mold forming. General punching processes include punching, corner cut, blanking, Punching bag and embossing (bumps), punching, drawing, forming, etc. The processing requires a corresponding mold to complete the operation, such as punching and blanking dies, convex buckling dies, tearing dies, hole die, forming dies, etc. The operation mainly pays attention to position and directionality.
5. Pressure riveting: The company mainly has pressure rivet nuts, screws, loose fasteners, etc. It completes the operation by hydraulic press riveting or punching and rivets it to the sheet metal part. There is also a rise in riveting, and it is necessary to pay attention to the direction.
6. Bend: Bending is folding a 2D panel into a 3D part. Its processing requires a folding bed and a corresponding bending die, and it also has a certain bending sequence. The principle is that the first cut does not interfere with the next knife, and it will produce a back fold of interference.
l The number of bends is calculated as follows: T=3.0mm and 6 times the thickness of the plate to calculate the groove width, such as: T=1.0, V=6. 0 F=1.8, T=1.2, V=8, F=2.2, T=1.5, V=10, F=2.7, T=2.0, V=12, F=4.0
Folding bed mold classification, straight knife, machete (80°C, 30°C)
When the aluminum plate bends, there is a crack, which can increase the width of the lower mold groove to increase the upper mold R (annealing can avoid cracks)
Note when bending:
Plane, required sheet thickness, quantity; bending direction, bending angle; bending size; appearance, electroplating chrome parts must not crease.
7. welding: Also referred to splicing, is a manufacturing process and technique for joining metals or other thermoplastic materials, such as plastics, by heating, high temperature, or high pressure.
Classification:
a fusion welding: argon arc welding, CO2 welding, gas welding, manual welding
b pressure welding: spot welding, butt welding, bump welding
c brazing: electrochromic welding, copper wire
Welding method: a CO2 gas shielded welding
b. Argon arc welding
c. spot welding
d. Robot welding
The choice of welding method is based on actual requirements and materials,
In general, CO2 gas shielded welding is used for iron plate welding.
Argon arc welding for stainless steel, aluminum plate welding,
Robot welding saves man hours, improves work efficiency and welding quality, and reduces work intensity.
Welding symbol: Δ fillet welding, Д, type I welding, V-type welding, One-sided V-type welding (V) With blunt edge V-type welding (V), Spot welding (O), Plug welding or groove welding (∏), flanged edge weld (χ), With blunt edge unilateral V-welding (V), Blunt U welding, with blunt J-type welding, back cover welding, Soldering
Arrow Lines and Connectors
Loss of welding and its prevention
Spot welding: insufficient strength, bump, welding area.
CO2 welding: high productivity, low energy consumption, low cost, strong rust resistance
Argon arc welding: It is light in depth, slow in splicing speed, low in efficiency, and high in production cost. It has tungsten defect, but has the advantage of better welding quality. Can weld non-ferrous metals, such as aluminum, copper, magnesium and so on.
welding deformation causes: insufficient preparation before welding, need to increase the fixture
Welding fixture bad improvement process
Bad welding sequence
Welding Deformation Effect Positive Method: Flame Effect Method
Vibration method
Hammering
Artificial aging
Technological development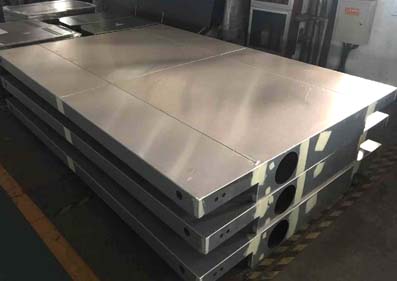
The processing steps of the processing components in the sheet metal workshop are: preliminary product testing, product processing trial production and product batch production. In the trial process of product processing, it is necessary to communicate with customers in a timely manner to obtain the evaluation of the corresponding processing, and then carry out the production of product batches.
Laser drilling technology is the earliest practical laser technology in laser material processing technology. The laser drilling in the sheet metal workshop generally uses a pulsed laser, which has a higher energy density and a shorter time and can process 1 μm holes. It is especially suitable for processing small holes with a certain angle and thin material, and is also suitable for deep holes and tiny holes in parts with high strength or relatively brittle soft materials.
The laser can realize the drilling of the burner components of the gas turbine. The drilling effect can achieve three-dimensional direction and the number can reach thousands. Perforated materials include stainless steel, nichrome, and HASTELLOY based alloys. Laser drilling technology is not affected by the mechanical properties of materials, and automation is easier.
In the development of laser drilling technology, laser cutting machine realizes automatic operation.
The application in the sheet metal industry changed the processing methods of traditional sheet metal technology, realized unmanned operation, greatly increased production efficiency, realized full-automatic operation, and led to the economic development of sheet metal. In the punching effect to enhance a grade, the processing effect is impressive.
Also includes a variety of cold stamping die structure and process parameters, various equipment working principles and operating methods, including new stamping technology and new technology. Parts sheet metal processing is called sheet metal processing.
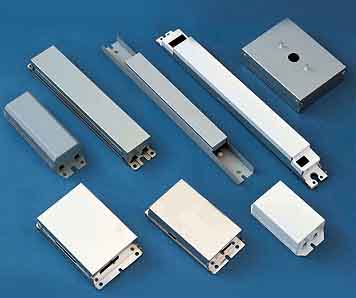
Industry terms
Each industry has its own terminology, and the sheet metal processing industry is no exception. The following 25 are common.
(1) Pressure riveting: Refers to the process of press-fastening the workpiece to the workpiece by using a punch or hydraulic press to press the riveting nut, pressure riveting screw or riveting nut column fastener.
(2) Riveting: Refers to countersinking the workpiece first. Then press the rivet nut firmly on the workpiece with punch or hydraulic press.
(3) Pulling mother: Refers to the use of similar riveting process. The process of connecting the rivet nut (POP) and other connectors firmly to the workpiece by means of a pull gun.
(4) Pull riveting: Refers to the riveting gun as a tool, using pull stud two or more than two pieces of work closely linked to the process.
(5)Rivet bond: A process in which two or more workpieces are joined together face to face with rivets. If countersunk riveting, the workpiece should be counterbored first.
(6) Cut-off angle: Refers to the process of cutting off the corner of the workpiece by using a die on a punch press or an oil press.
(7) bending: the process of forming a workpiece from a bending machine.
(8) forming: refers to the process of using a mold on a common punch or other equipment to deform the workpiece.
(9) shear material: refers to the material through the shearing machine to obtain rectangular workpiece process.
(10) Cutting: Refers to the process of the workpiece after LASER cutting or blanking of numerical control punch press.
(11) Blanking: Refers to the process of using a mold to obtain the shape of a product on an ordinary punch or other equipment.
(12) punching: refers to the process of machining holes by ordinary punches and dies.
(13) punching convex hull: Refers to the process of forming the convex shape of the workpiece in the punch or hydraulic press mold.
(14) tearing and tearing: refers to the process of forming a bridge like shape in a punch or hydraulic press mold.
(15) draw holes: also called "flanging", which refers to the process of forming circular holes on the workpiece by using dies on ordinary punching machines or other equipment.
process.
(16) Tapping: refers to the process of machining internal threads on the workpiece.
(17) Leveling: Refers to the unevenness of the workpiece before and after machining, and the use of other equipment to flatten the workpiece.
(18) back teeth: refers to the workpiece with teeth on the pre attack process, repair second times the thread.
(19) Drilling: The process of drilling holes in a workpiece using a drill or a milling machine.
(20) Chamfer: Refers to the use of molds, boring tools, grinding machines, etc., to process the sharp corners of the workpiece.
(21) punch mark: refers to the process of using a mold to punch out characters, symbols or other imprints on the workpiece.
(22) Counterbore: Refers to the process of machining a tapered hole in a workpiece to match a connector such as a countersunk head screw.
(23) clap: Refers to a certain shape of the workpiece, the transition to a smooth process.
(24) punching mesh: It means to punch a net hole on the workpiece with a die on an ordinary punch or CNC punch.
(25) reaming: The process of machining small holes on the workpiece with a drill or milling cutter into large holes.
Process flow
Selection of materials
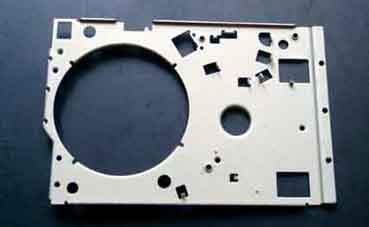
The commonly used materials for sheet metal processing include cold-rolled sheet (SPCC), hot-rolled sheet (SHCC), galvanized sheet (SECC, SGCC), copper (CU) brass, red copper, beryllium copper, aluminum (6061, 5052) 1010, 1060, 6063, hard aluminum, etc.), stainless steel (mirror, brushed surface, matte), depending on the role of the product, different materials, generally need to consider the use of the product and cost.
1. Cold-rolled plate SPCC, mainly used for electroplating and baking paint parts, low cost, easy molding, material thickness ≤ 3.2mm.
2. Hot-rolled plate SHCC, material T ≥ 3.0mm, is also used for electroplating, lacquer pieces, low cost, but difficult to shape, mainly used flat pieces.
3. Galvanized sheet SECC, SGCC, SECC electrolysis board is divided into N material and P material. N material is not used for surface treatment and the cost is high. P material is used for spraying parts.
4. Copper; mainly conductive materials, the surface treatment is nickel, chrome, or no treatment, high cost.
5. Aluminum plate; general use of surface chromate (J11-A), oxidation (conductive oxidation, chemical oxidation), high cost, silver plating, nickel plating.
6. Aluminium profiles; Cross-section structure of complex materials, used in a variety of plug-in box. The surface treatment is the same as the surface treatment of the aluminum plate.
7. Stainless steel; mainly used without any surface treatment, high cost.
Drawing review
To write the part's process flow, we must first understand the various technical requirements of the parts drawing; then the drawing review is the most important part of the preparation of the part's process flow.
1. Check the drawing is complete.
2. The relationship between drawings and views, whether the labels are clear and complete, and the dimension units are marked.
3. Assembly relations, assembly requirements focus on size.
4. The difference between the old and new drawings.
5. Translation of foreign languages.
6. Table code number conversion.
7. Mapping problems and feedback.
8. material
9. Quality requirements and process requirements
10. Official release drawings, shall be stamped with quality control chapter.
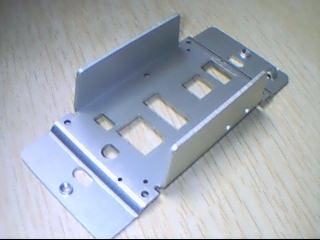
Precautions
The expansion diagram is a plan (2D) based on part diagram (3D).
1. The way of expansion should be combined, so as to save materials and workability.
2. Reasonable choice of clearance and wrapping style, T=2.0 or less gap 0.2, T=2-3 gap 0.5, wrapping edge method using long side wrapping short side (door panel)
3. Reasonable consideration of tolerance dimension: negative deviation to the end, positive deviation half; Hole size: positive difference goes to the end, negative difference takes half.
4. burr direction
5. Extraction, riveting, tearing, punching (bumps), etc., drawing a cross-sectional view
6. Check material, plate thickness, thickness tolerance
7. Special angle, the radius of bending angle (general R = 0.5) should be measured and expanded.
8. Where error-prone (similar asymmetry) should focus on the prompt
9. Where there are more sizes, add a larger image
10. Need to spray protection place must be expressed
Manufacturing processes
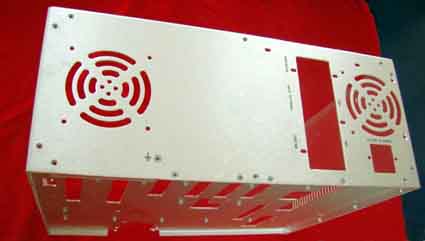
According to the difference in the structure of the sheet metal parts, the process flow may be different, but the total does not exceed the following points.
1, under the material: There are various ways of cutting, mainly in the following ways
a. Shears: Shears are used to cut strips of simple materials. It is mainly used for blank blank forming and processing.The cost is low, the precision is lower than 0.2, but can only process the no-holes and no-cornered strips or blocks.
b. Punching machine: It is the use of punching machine to divide the flat parts of the parts into one piece or multiple steps on the plate to form a variety of shape materials. Its advantages are short working hours, high efficiency, high precision, low cost, and suitable for mass production, but it is necessary to design molds.
c. NC cutting, when CNC cutting, firstly write the NC machining program, and use the programming software to compile the drawn development diagram into a recognizable program of the NC machining machine. According to these procedures, it can be used to punch flat parts of various shapes on the flat plate one by one, but its structure is affected by the structure of the cutter. The cost is low and the precision is 0.15.
d. Laser cutting is the use of laser cutting methods to cut the shape of the flat plate on a large flat plate. The same as the NC cutting need to write a laser program, it can be a variety of complex shapes of flat parts, high cost, accuracy of 0.1.
e. Sawing machine: mainly used in the cutting ,aluminum, square tube, round tube, round bar and the like, low cost and low precision.
2. Fitter: Counterbore, Tapping, Reaming, Drilling
Counterbore angle is generally 120 °C, used to pull rivets, 90°C for Countersunk Screws, tapping Inch bottom hole.
3. Flange: It is also called pumping holes and turning holes, which is to draw a slightly bigger hole on a smaller base hole and then tapping. Mainly use sheet metal with relatively thin plate thickness to increase its strength and number of thread turns to avoid slipping. Generally used for relatively thin plate thickness, its normal shallow hole flanging, the thickness does not change, When the thickness is allowed to be thinned by 30-40%, a height of 40-60% higher than the normal flange height can be obtained. When the thickness is reduced by 50%, the maximum flange height can be obtained. When the plate thickness is large, such as 2.0, 2.5, etc., the plate thickness can be directly tapped.
4. punch: It is a manufacturing process using mold forming. General punching processes include punching, corner cut, blanking, Punching bag and embossing (bumps), punching, drawing, forming, etc. The processing requires a corresponding mold to complete the operation, such as punching and blanking dies, convex buckling dies, tearing dies, hole die, forming dies, etc. The operation mainly pays attention to position and directionality.
5. Pressure riveting: The company mainly has pressure rivet nuts, screws, loose fasteners, etc. It completes the operation by hydraulic press riveting or punching and rivets it to the sheet metal part. There is also a rise in riveting, and it is necessary to pay attention to the direction.
6. Bend: Bending is folding a 2D panel into a 3D part. Its processing requires a folding bed and a corresponding bending die, and it also has a certain bending sequence. The principle is that the first cut does not interfere with the next knife, and it will produce a back fold of interference.
l The number of bends is calculated as follows: T=3.0mm and 6 times the thickness of the plate to calculate the groove width, such as: T=1.0, V=6. 0 F=1.8, T=1.2, V=8, F=2.2, T=1.5, V=10, F=2.7, T=2.0, V=12, F=4.0
Folding bed mold classification, straight knife, machete (80°C, 30°C)
When the aluminum plate bends, there is a crack, which can increase the width of the lower mold groove to increase the upper mold R (annealing can avoid cracks)
Note when bending:
Plane, required sheet thickness, quantity; bending direction, bending angle; bending size; appearance, electroplating chrome parts must not crease.
7. welding: Also referred to splicing, is a manufacturing process and technique for joining metals or other thermoplastic materials, such as plastics, by heating, high temperature, or high pressure.
Classification:
a fusion welding: argon arc welding, CO2 welding, gas welding, manual welding
b pressure welding: spot welding, butt welding, bump welding
c brazing: electrochromic welding, copper wire
Welding method: a CO2 gas shielded welding
b. Argon arc welding
c. spot welding
d. Robot welding
The choice of welding method is based on actual requirements and materials,
In general, CO2 gas shielded welding is used for iron plate welding.
Argon arc welding for stainless steel, aluminum plate welding,
Robot welding saves man hours, improves work efficiency and welding quality, and reduces work intensity.
Welding symbol: Δ fillet welding, Д, type I welding, V-type welding, One-sided V-type welding (V) With blunt edge V-type welding (V), Spot welding (O), Plug welding or groove welding (∏), flanged edge weld (χ), With blunt edge unilateral V-welding (V), Blunt U welding, with blunt J-type welding, back cover welding, Soldering
Arrow Lines and Connectors
Loss of welding and its prevention
Spot welding: insufficient strength, bump, welding area.
CO2 welding: high productivity, low energy consumption, low cost, strong rust resistance
Argon arc welding: It is light in depth, slow in splicing speed, low in efficiency, and high in production cost. It has tungsten defect, but has the advantage of better welding quality. Can weld non-ferrous metals, such as aluminum, copper, magnesium and so on.
welding deformation causes: insufficient preparation before welding, need to increase the fixture
Welding fixture bad improvement process
Bad welding sequence
Welding Deformation Effect Positive Method: Flame Effect Method
Vibration method
Hammering
Artificial aging
Technological development
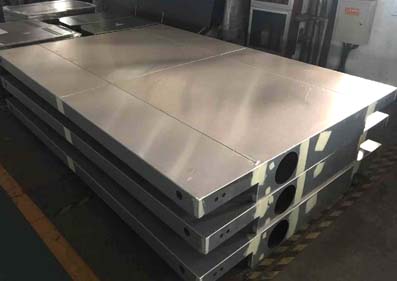
The processing steps of the processing components in the sheet metal workshop are: preliminary product testing, product processing trial production and product batch production. In the trial process of product processing, it is necessary to communicate with customers in a timely manner to obtain the evaluation of the corresponding processing, and then carry out the production of product batches.
Laser drilling technology is the earliest practical laser technology in laser material processing technology. The laser drilling in the sheet metal workshop generally uses a pulsed laser, which has a higher energy density and a shorter time and can process 1 μm holes. It is especially suitable for processing small holes with a certain angle and thin material, and is also suitable for deep holes and tiny holes in parts with high strength or relatively brittle soft materials.
The laser can realize the drilling of the burner components of the gas turbine. The drilling effect can achieve three-dimensional direction and the number can reach thousands. Perforated materials include stainless steel, nichrome, and HASTELLOY based alloys. Laser drilling technology is not affected by the mechanical properties of materials, and automation is easier.
In the development of laser drilling technology, laser cutting machine realizes automatic operation.
The application in the sheet metal industry changed the processing methods of traditional sheet metal technology, realized unmanned operation, greatly increased production efficiency, realized full-automatic operation, and led to the economic development of sheet metal. In the punching effect to enhance a grade, the processing effect is impressive.