Aluminum Electrolytic Polishing Method
YB-66 environment-friendly aluminum and aluminum alloy electrolytic polishing additive new process
1. Features
1.>The polishing solution does not contain chromic acid, which is in line with today's environmental protection requirements, saving investment in environmental protection equipment and wastewater treatment costs.
2> The polishing current density is smaller than the conventional process, so not only the power consumption is low, but also the polishing liquid has a long service life, and it is more suitable for the surface polishing of large aluminum and aluminum alloy parts.
3> Wide application range, suitable for pure aluminum and various types of aluminum alloys with silicon content greater than 2%.
2, the polishing liquid composition and operating conditions
Concentrated phosphoric acid (specific gravity 1.74) 70% (by weight)
YB-66 additive 30% (by weight)
Temperature 55–65°C Best 60°C
Anode current density, DA 2–8 A/dm2 (without stirring)
12–20 A/dm2 (stirring)
Voltage 10–15 volts
Polishing time 3–5 minutes
Cathode Material Lead or Stainless Steel
Cathode area: anode area 2–3:1
3, slotting step
1> The specific gravity of the polishing liquid before use is in the range of 1.50 - 1.52. The amount of phosphoric acid to be added is calculated and added based on the polishing fluid volume to be prepared, the specific gravity of the polishing fluid, and the weight ratio of phosphoric acid in the polishing fluid.
2> Calculate the weight of the required YB-66 additive and add it.
3> Heat to operating temperature.
4, the operation guide
1> Whether to use agitation during polishing (cathode movement, air agitation) depends mainly on the shape of the polishing element:
If the shape of the polishing element is simple and the lateral width is narrow, stirring is not used. Conversely, if the shape of the polishing part is irregular or the lateral width is large, especially when some parts of the polishing part obstruct the gas from escaping to form a "air bag," and the surface polishing is affected, stirring must be used. In the case of agitation, the anode current density must be increased accordingly, otherwise it is difficult to achieve a high brightness on the polished surface.
2> During the polishing, most of the impurities are deposited on the surface of the cathode, but some of the solid sludge generated by the polishing remains in the polishing liquid. Therefore, it is necessary to periodically filter the polishing liquid to remove the impurities.
3> in the polishing process, due to the production of phosphate, water electrolysis and volatilization and entrainment loss of the polishing fluid, it is necessary to continue to add phosphoric acid and YB-66 additives.
4> The addition ratio of phosphoric acid and YB-66 additive is still generally added at 70%:30%. However, after each addition, the specific gravity of the polishing slurry should be measured and then adjusted appropriately according to the measurement results.
5> The original proportion of the unused polish fluid is in the range of 1.50–1.52. In the polishing bath operation, the proportion of the polishing fluid should be controlled within the range of 1.50–1.65. The proportion of the polishing fluid is too high, indicating that the water content of the polishing fluid is insufficient; Conversely, the proportion of the polishing fluid is too low, indicating that the polishing solution contains too much water and the phosphoric acid content is low. Densimeter is often used to determine the specific gravity of the polishing liquid, which is an effective means to control the concentration of polishing fluid components and polishing quality.
6> Long-term polishing at higher anode current density may cause excessive aluminum content in the polishing liquid (a semi-melting substance at the top of the polishing liquid is a sign of high aluminum content). At this time, the new polishing liquid must be partially replaced. To reduce the aluminum content in the polishing liquid.
5. Pre-plating treatment and post-plating treatment
1> before plating
Aluminum or aluminum alloy parts must be degreasing before polishing. According to the degree of contamination of the surface of the polishing part, one of the following two degreasing processes can generally be selected for treatment.
The first kind of process: Sludge contamination on the surface of aluminum parts is slight and evenly distributed. A weakly erosive alkaline degreasing fluid is usually used. Its composition and operating conditions are as follows:
Anhydrous sodium carbonate 25 g/L
Trisodium phosphate 25 g/L
Temperature 60–70°C
Immersion time 1–3 minutes
The second kind of process: the sludge on the surface of aluminum pieces is heavily contaminated. Commonly used non-etching alkaline degreasing fluid, its composition and operating conditions are as follows:
Anhydrous sodium carbonate 40–60 g/L
Trisodium phosphate 40–60 g/L
Sodium silicate 20–30 g/L
Temperature 50–70°C
Immersion time 15–30 minutes
Sodium silicate is a corrosion inhibitor, which can inhibit the corrosion of aluminum, but the use of such corrosion inhibitors will produce a layer of aluminum silicate film on the surface of aluminum parts. Therefore, after degreasing and washing, desludge treatment (often referred to as glaring) must be performed in a solution containing fluoride ions. The composition and operating conditions of the aluminum and aluminum alloy de-sludge treatment liquids are as follows:
Nitric acid (content 65%) 500–700 ml/L
Ammonium hydrogen fluoride 50–120 g/L
Temperature 20–25°C
Immersion time 30 seconds
2, post-processing
Most aluminum and aluminum alloys can be applied with various plating coatings after electrolytic polishing and cleaning, such as anodization, electrophoretic painting and various metal platings. However, some aluminum alloys, such as aluminum alloys with high copper content, need to be de-sludge treated after electropolishing and cleaning to improve the surface brightness.
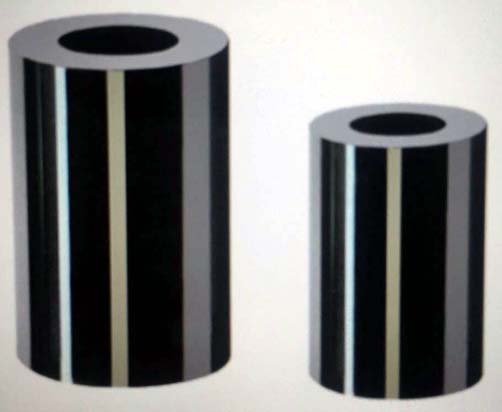