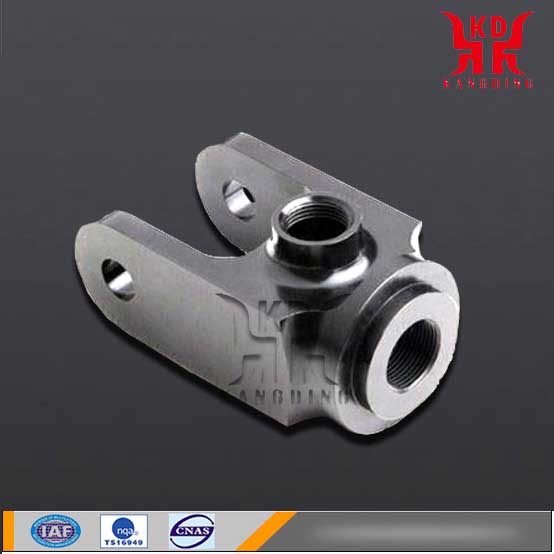
CNC Machining, Precision Machining, Computer boring, China CNC Processing Factory
Features:
1.CNC machining center is an efficient, high-precision CNC machine tool. Workpieces can be processed in multiple stages in one setup. At the same time, there is also a tool magazine and an automatic tool change function. The CNC machining center can implement three-axis or three-axis linkage control to ensure that the tool performs complex surface machining. In addition to the functions of linear interpolation and arc interpolation, the CNC machining center also has various machining canned cycles, automatic tool radius compensation, automatic tool length compensation, graphic display of machining processes, human-machine dialogue, automatic fault diagnosis, off-line programming, etc. Features.
2. a large number of reduction in the number of tooling, machining complex shapes of parts does not require complicated tooling. If you want to change the shape and size of parts, you only need to modify the parts processing program, which is suitable for the development and modification of new products.
3. The parts have stable processing quality, high processing precision, high repeatability, and meet the processing requirements of the aircraft.
4. The CNC can process complex surfaces that are difficult to process by conventional methods. It can even process some unobserved processing sites.
Process:
The cnc processing technology is an automated processing method with high efficiency, high precision and high flexibility. The cnc processing is to input the numerical control program of the workpiece to the machine tool, and the machine tool automatically processes the workpiece that meets the wishes of the people under the control of the data and creates a wonderful product. CNC machining is an advanced processing technology in today's machine-building, and it is a technology that can turn an artist's imagination into a reality. CNC machining technology can effectively solve the complex, precise and small-batch-changing processing problems such as molds, and fully meet the needs of modern production.
Precision And Tolerance Standard:
CNC machining is associated with ISO standards. It needs to look at the level of a machining center. It depends on its repeat positioning accuracy. If a machine tool's repeat positioning accuracy can reach 0.005mm (ISO standard, statistical method), it is a High-precision machine tools, in the 0.005mm (ISO standard, statistical methods) below, is ultra-high-precision machine tools, high-precision machine tools, have the best bearings, screw.
When it comes to the "accuracy" of CNC machine tools, it is important to understand the definition of standards, indicators, and calculation methods. When the Japanese machine tool production mark is set to “accuracy”, JISB6201 or JISB6336 or JISB6338 standards are generally used.
JISB6201 is generally used for general-purpose machine tools and general CNC machine tools, JISB6336 is generally used for machining centers, and JISB6338 is generally used for vertical machining centers.
The above three standards are basically the same when defining the positional accuracy. Herein, only JIS B6336 is taken as an example because on the one hand the standard is relatively new, on the other hand it is slightly more accurate than the other two standards.
European machine tool manufacturers, especially German manufacturers, generally use the VDI/DGQ3441 standard.
U.S. machine tool manufacturers usually use the National Machine Tool Builder's Assn (NMTBA) standard (this standard originates from a study of the American Machine Tool Manufacturing Association, which was promulgated in 1968 and later modified).
The dimensional accuracy and shape accuracy of the typical machining parts in the machining center are compared with those in other countries. The value in the country is generally about 0.008 to 0.010 mm, It is roughly 0.008 to 0.010mm in China, and the international advanced level is 0.002 to 0.003mm.
Kang Dingxin ultra-precision machining currently refers to the size and position accuracy of 0.01 ~ 0.3μm, shape and contour accuracy of 0.003 ~ 0.1μm, surface roughness of steel Ra≤0.05μm, copper Ra≤0.01μm.
Domestically developed ultra-precision CNC lathes and CNC milling machines have been put into production.
At present, ultra-precision grinding machines and ultra-precision compound processing machines need to be developed on the varieties, and at the same time, super-precision spindle units, ultra-precision rail sub units, ultra-precise and smooth drive systems, ultra-precise contour control technologies, and nano-resolution numerical control systems must be further improved. Performance and speed up its engineering.
Processing materials:
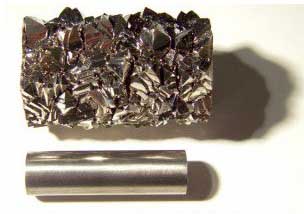
There are many materials suitable for machine tools in machining centers, such as 45# steel, ABS, PC, POM, PP, PMMA, nylon, bakelite, aluminum alloy, zinc alloy, low carbon steel, copper, stainless steel, and Teflon. Materials processing centers such as PBT, PPS, PEET and polyurethane foam are suitable for processing. Some very hard material processing centers can also process, But the prerequisite is that the hardness of the tool material used must be higher than the hardness of the material of the workpiece. Otherwise, the tool may be damaged during machining and the workpiece machining may not be successful.
It solves the problem of variety of aerospace products, small quantities, complex shapes, high precision, and effective ways to achieve high-efficiency and automated processing.
Programming design:
Computer programming also depends on various types of programming software (such as Pro/E, UG, and CAXA). These softwares are mainly based on the principles of CAD design, CAM manufacturing, and CAE analysis.
The most important thing when learning these softwares is to learn to build 3D digital models. Only after the digital models are built, can the actual processing routes be specified, and finally NC programs can be generated through processing routes.
The main steps of CNC machining program design are:
1. Analysis of parts design drawings and product assembly drawings
Understand the use, performance and working conditions of the product, and define the position, function and technical requirements of the part in the product. This is the basis of CNC machining.
2, process review
The process review relates to the precision and quality of the subsequent product processing. It is necessary to review the dimensions, views and technical integrity of the drawings and analyze whether their technical requirements are scientific, reasonable and appropriate.
3, determine the type of blank and manufacturing methods
The basis for determining the blank is mainly the role of the part in the product, the structural characteristics and dimensions of the part itself, and the process characteristics of the part material. The types of blanks that are frequently used include castings, forgings, weldments, stampings, and profiles.
Device
Metal cutting CNC machine tools, including CNC center, drilling machine, EDM wire cutting apparatus, thread cutting machine, milling machine, grinding machine, boring machine and processing center. These machines are suitable for single-piece, small-batch and multi-species and parts processing, have a good consistency of processing dimensions, high productivity and degree of automation, and high equipment flexibility.
CNC special processing machine tools; such machine tools include CNC wire (electrode) cutting machine tools, EDM machine tools, flame cutting machines, CNC laser cutting machine tools, special combination machine tools.
Other types of numerical control equipment; non-CNC machining technology equipment, such as automatic assembly machine, multi-coordinate measuring machines, industrial robots and automatic drawing machine and the like.
Kangding owns first-class mechanical processing equipment such as high-speed precision CNC machining center (DMG MORI,Mazak,SMTCL,EMAG)
Quote
1, first of all to confirm the product drawings and technical requirements.
2. The price of materials and labor varies from place to place.
3, the general parts are calculated according to the material fee + processing fee + profit, the processing fee depends on the process to determine, the use of different processing equipment, of course, the price is different according to some time calculation (turning time, grinding time, etc.). Some calculations by operations (such as wire cutting, how much money is drilled, etc.)
2, the valuation process:
Look at the business evaluation book - content analysis -Fill in the valuation details - supervisor approval - Originally sent to the business department - tracking quotes and confirming - The business will confirm the original quote details into the computer -Confirm the cost of each process.
PREVIOUS:NONE
NEXT:Metal Parts Processing
NEXT:Metal Parts Processing