Varios materiales principales procesamiento de la cavidad auricular, usted sabe cuánto?
La apariencia de los auriculares también afecta directamente el deseo de comprar de todos. Los auriculares atractivos no solo tienen un sentido visual, sino que la elección de los materiales también hará una gran diferencia en la apariencia.
Si miras hacia atrás, los primeros auriculares deben estar hechos de metal. Pero los tapones para los oídos eran solo un producto del laboratorio, no un producto de consumo. Por lo tanto, el diseño no necesita considerar la apariencia.
Los primeros auriculares estaban hechos principalmente de plástico tipo ABS. Más tarde, la tecnología de tratamiento de superficie de la cavidad del tapón auditivo aumentó gradualmente, y se utilizaron cromado y pintura en aerosol esmerilada, y la apariencia gradualmente se volvió llamativa. Hasta ahora, el plástico sigue siendo el material principal para la producción de la cavidad de la carcasa del tapón auditivo. La razón principal es que el plástico es barato de moldear y adecuado para la producción en masa. Además, el fácil procesamiento de los plásticos también facilita a los diseñadores implementar diseños de cavidades de varias formas especiales.
Pero el plástico siempre es un material frágil y fácil de usar. Otra situación es que el plástico siempre es propenso a la impresión de precios bajos y no puede hacer que el producto se venda a un precio más alto, por lo que los tapones para los oídos de las cavidades metálicas han aumentado gradualmente.
Mecanizar la cavidad de un auricular de metal es mucho más complicado que hacer una cavidad de plástico para auriculares. La mayoría de los auriculares de metal necesitan usar tecnología CNC para cortar y fresar una pieza entera de metal en forma de cavidad. El uso de una fresadora consume mucho tiempo y se puede procesar una pequeña cantidad por día. Después de la escisión de la CNC, es posible que tenga que ser pulido, pulido, pintado o chapado o similares procesamiento. Una vez que haya un problema con cada paso aquí, afectará el rendimiento y, por lo tanto, el costo, por lo que los auriculares de metal de buen aspecto a menudo no son baratos.
Sin embargo, la cavidad hecha de metal, textura de la mirada de alto grado, pero también tienen que ser tratados con cuidado. Especialmente después del proceso de recubrimiento metálico de la superficie, puede ser fácilmente arañazos plagadas.
Y entre el metal CNC y el plástico, hay una resina fotosensible de material recientemente popular. Este es un material líquido que puede sufrir rápidos cambios físicos y químicos en un corto período de tiempo después de ser irradiado con rayos ultravioleta, y luego reticular y curar el oligómero. Primero fue desarrollado y aplicado por Bayer en Alemania en 1968.
Este material se ha utilizado en el campo de los auriculares durante algún tiempo y, de hecho, a menudo entramos en contacto con este material en nuestras vidas. Por ejemplo, los materiales de relleno que usamos para rellenar los dientes y la "manicura de fototerapia" que las mujeres suelen llamar, las materias primas utilizadas son en realidad una especie de resina fotosensible.
En el campo de los auriculares, el material más antiguo también se utilizó en audífonos médicos. Más tarde, en 1995, un mezclador estadounidense Jerry Harvey utilizó este material para desarrollar un monitor in-ear personalizado para músicos de la banda. Esto también se convirtió en el punto de partida de la ola de auriculares personalizados.
The custom earphone mentioned here is made by collecting earprints of the contours of individual ears, and according to its shape, using a photosensitive resin to make a shell of the same shape as the cavity of the earphone, and placing a sounding unit in it. After the cavity and the panel are joined together, a layer of bright lacquer is completed after polishing. This layer of bright lacquer is harder and more abrasion-resistant, which makes the shell look brighter and protects the shell. Because the shape is customizable, the photosensitive resin itself can blend many different colors. It can even create the appearance of "multicolored black", so custom headphones have always been considered as the most personalized headset products.
El audífono personalizado mencionado aquí se hace recolectando huellas de los contornos de los oídos individuales y, de acuerdo con su forma, utilizando una resina fotosensible para hacer una carcasa de la misma forma que la cavidad del audífono y colocando una unidad de sonido en él. Después de que la cavidad y el panel se unen, se completa una capa de laca brillante después del pulido. Esta capa de laca brillante es más dura y más resistente a la abrasión, lo que hace que la carcasa se vea más brillante y protege la carcasa. Debido a que la forma es personalizable, la resina fotosensible puede combinar muchos colores diferentes. Incluso puede crear la apariencia de "negro multicolor", por lo que los auriculares personalizados siempre se han considerado los productos de auriculares más personalizados.
Hoy en día, la aplicación de la tecnología de impresión 3D ha hecho que los auriculares mencionados anteriormente requieran corte CNC y moldeo por inyección de resina para formar una cavidad, que ha evolucionado nuevamente en la producción. Además de imprimir metal, los materiales fotosensibles también se usan muy comúnmente en la impresión 3D. Como resultado, muchas marcas de auriculares han comenzado a utilizar la tecnología de impresión 3D para hacer caries, y se cree que en el futuro estarán disponibles más productos que utilizan tecnologías relacionadas.
Si miras hacia atrás, los primeros auriculares deben estar hechos de metal. Pero los tapones para los oídos eran solo un producto del laboratorio, no un producto de consumo. Por lo tanto, el diseño no necesita considerar la apariencia.
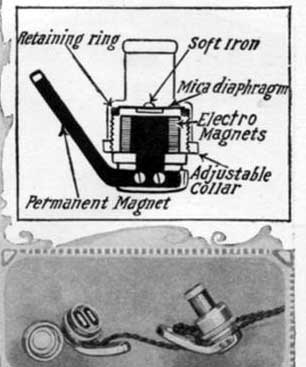
Los primeros auriculares estaban hechos principalmente de plástico tipo ABS. Más tarde, la tecnología de tratamiento de superficie de la cavidad del tapón auditivo aumentó gradualmente, y se utilizaron cromado y pintura en aerosol esmerilada, y la apariencia gradualmente se volvió llamativa. Hasta ahora, el plástico sigue siendo el material principal para la producción de la cavidad de la carcasa del tapón auditivo. La razón principal es que el plástico es barato de moldear y adecuado para la producción en masa. Además, el fácil procesamiento de los plásticos también facilita a los diseñadores implementar diseños de cavidades de varias formas especiales.
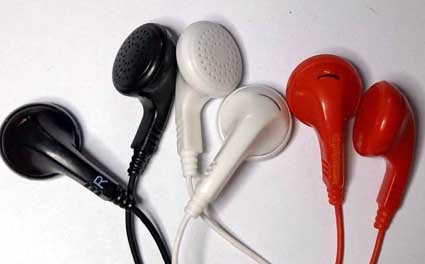
Pero el plástico siempre es un material frágil y fácil de usar. Otra situación es que el plástico siempre es propenso a la impresión de precios bajos y no puede hacer que el producto se venda a un precio más alto, por lo que los tapones para los oídos de las cavidades metálicas han aumentado gradualmente.
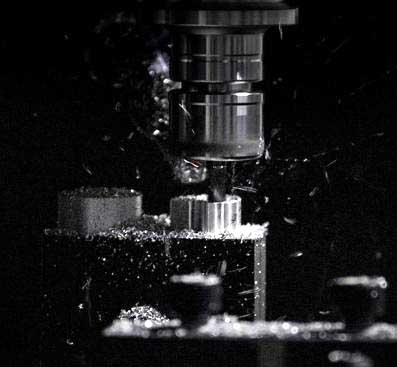
Mecanizar la cavidad de un auricular de metal es mucho más complicado que hacer una cavidad de plástico para auriculares. La mayoría de los auriculares de metal necesitan usar tecnología CNC para cortar y fresar una pieza entera de metal en forma de cavidad. El uso de una fresadora consume mucho tiempo y se puede procesar una pequeña cantidad por día. Después de la escisión de la CNC, es posible que tenga que ser pulido, pulido, pintado o chapado o similares procesamiento. Una vez que haya un problema con cada paso aquí, afectará el rendimiento y, por lo tanto, el costo, por lo que los auriculares de metal de buen aspecto a menudo no son baratos.
Sin embargo, la cavidad hecha de metal, textura de la mirada de alto grado, pero también tienen que ser tratados con cuidado. Especialmente después del proceso de recubrimiento metálico de la superficie, puede ser fácilmente arañazos plagadas.
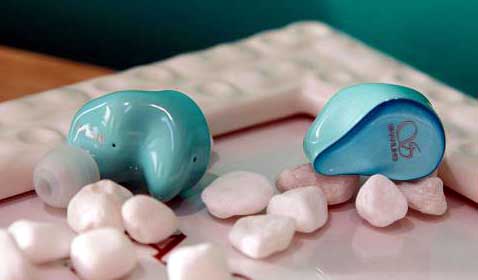
Este material se ha utilizado en el campo de los auriculares durante algún tiempo y, de hecho, a menudo entramos en contacto con este material en nuestras vidas. Por ejemplo, los materiales de relleno que usamos para rellenar los dientes y la "manicura de fototerapia" que las mujeres suelen llamar, las materias primas utilizadas son en realidad una especie de resina fotosensible.
En el campo de los auriculares, el material más antiguo también se utilizó en audífonos médicos. Más tarde, en 1995, un mezclador estadounidense Jerry Harvey utilizó este material para desarrollar un monitor in-ear personalizado para músicos de la banda. Esto también se convirtió en el punto de partida de la ola de auriculares personalizados.
The custom earphone mentioned here is made by collecting earprints of the contours of individual ears, and according to its shape, using a photosensitive resin to make a shell of the same shape as the cavity of the earphone, and placing a sounding unit in it. After the cavity and the panel are joined together, a layer of bright lacquer is completed after polishing. This layer of bright lacquer is harder and more abrasion-resistant, which makes the shell look brighter and protects the shell. Because the shape is customizable, the photosensitive resin itself can blend many different colors. It can even create the appearance of "multicolored black", so custom headphones have always been considered as the most personalized headset products.
El audífono personalizado mencionado aquí se hace recolectando huellas de los contornos de los oídos individuales y, de acuerdo con su forma, utilizando una resina fotosensible para hacer una carcasa de la misma forma que la cavidad del audífono y colocando una unidad de sonido en él. Después de que la cavidad y el panel se unen, se completa una capa de laca brillante después del pulido. Esta capa de laca brillante es más dura y más resistente a la abrasión, lo que hace que la carcasa se vea más brillante y protege la carcasa. Debido a que la forma es personalizable, la resina fotosensible puede combinar muchos colores diferentes. Incluso puede crear la apariencia de "negro multicolor", por lo que los auriculares personalizados siempre se han considerado los productos de auriculares más personalizados.
Hoy en día, la aplicación de la tecnología de impresión 3D ha hecho que los auriculares mencionados anteriormente requieran corte CNC y moldeo por inyección de resina para formar una cavidad, que ha evolucionado nuevamente en la producción. Además de imprimir metal, los materiales fotosensibles también se usan muy comúnmente en la impresión 3D. Como resultado, muchas marcas de auriculares han comenzado a utilizar la tecnología de impresión 3D para hacer caries, y se cree que en el futuro estarán disponibles más productos que utilizan tecnologías relacionadas.