Application of 5-axis linkage machining center in processing wood mold production
The annual output of a customer's V-castings is more than 100,000 tons, and the casting molds are all wood molds. About 60 kinds of new products are developed each year. The products are mainly balanced and heavy, and the casting molds are large in size. Our company introduced the Master546 five-axis linkage machining center produced by Paolino Bacci of Italy. In the mold making process, casting mold design was carried out by software such as Solidworks and Cimatron E, and Cimatron E software was used for programming. Mold processing with machining centers saves a lot of labor costs, reduces labor intensity, and makes mold making more precise and efficient.
1. Customer five-axis linkage machining center main parameters
The machining center has a gantry structure with a table size of 1600×1600 mm, an X×Y×Z stroke of 3000×2600×950 mm, an A-axis tilt angle of ±135°, and a C-axis rotation angle of ±200°. It has a disc turret type magazine that can hold 16 tools, all of which are automatically changed, and the main machine adopts FANUC servo control system.
2. Traditional wood mold making process
The traditional wood mold manufacturing method is based on the casting process drawings of the parts, determining the model classification, module structure, hand drawing the stakeout drawing, and making the block making and assembling.
Among them, the lofting is the specificization of the dimensions of the two-dimensional drawings of the parts, that is, the standard of module production.
At the same time, it is also a key process in the design and manufacture of the model, which requires high technical level for the mold maker.
For some complicated parts, in the mold manufacturing process, due to the imperfect dimensions of the two-dimensional drawings and the incomplete understanding of the drawings by the mold makers, the molds produced are inevitably subject to inaccurate dimensions.
Most of these problems can only be gradually verified in the model manufacturing process, and some can only be discovered after the castings are manufactured. This not only increases the workload of mold development, delays the development of new products, but also has problems such as low mold accuracy.
3. Five-axis machining center application process
3.1 Casting mold three-dimensional design
At this stage, the V-balanced heavy-duty product design is generally carried out using 3D CAD software. During the casting mold design process, enter the customer's product 3D map into Solidworks software. According to the casting process drawings of the product, the parameters such as shrinkage of the mold and draft of the draft are set, and the three-dimensional drawing of the upper and lower molds is drawn, as shown in Fig. 1.
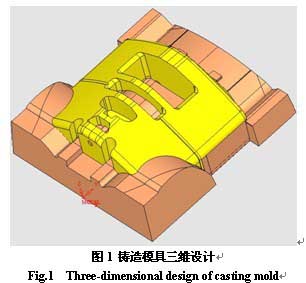
Fig. 1 Casting mold
3.2 Processing and post-processing
Our company uses Cimatron E8.5 programming software, Cimatron E8.5 is a product of Israel Cimatron company. Cimatron E's CNC machining technology has always been a world leader and is widely regarded as one of the most outstanding CNC programming software. Cimatron E8.5 supports programming from 2.5 to 5 axes.
The processing program is generally divided into the following steps:
1) According to the characteristics of casting molds, preliminary development of processing technology;
2 》Program according to the different surfaces of the mold, select the appropriate machining program. Select the appropriate tool, spindle speed, feed speed, tool path and other machining parameters to generate the tool path. as shown in picture 2;
3) Post processing to generate NC program
The post-processing program is a compiling software between the tool path source file generated by the general-purpose numerical control programming software and the NC program in the ISO format that can be recognized by the special numerical control machining center. Figure 3 shows the postprocessor developed by Cimatron for our Master546 model.
3.3 Five-axis machining program simulation check
Italy Paolino Bacci developed an intelligent 3D solid machine simulation software Pitagora. Accurate and realistic dynamic simulation of the motion process of the 5-axis CNC machining center can be directly read into the ISO code generated by Cimatron E post processing. It can perform dynamic zoom rotation, machining over stroke check, interference collision check, tool head fast moving track adjustment and machining time calculation, as shown in Figure 4. Pitagora ensures the accuracy and security of the programs programmed by Cimatron E and is very practical.
3.4 Five-axis production of mold blanks
According to the casting process drawings, a mold blank with appropriate margin can be produced without considering the detailed dimensions, which reduces the workload of the mold maker.
3.5 Model processing
As shown in Figure 5. The model blank is fixed on the machining center table by a special pressing tool, and the relationship between the workpiece coordinate system and the machining coordinate system is realized through setting;
The NC program is input to the machining center, and the conversion of the encoder is realized to realize the linkage of the respective cutter axes of the machining center, thereby completing the model processing. For the mold is not easy to take the mold, need to do the live block, the live block can be directly processed on the model.
4 Conclusion
Through the application of the five-axis linkage machining center, the labor cost is saved and the development cycle of the V-method is shortened. Moreover, it is possible to produce high-precision curved surfaces to produce high-precision models, and to produce high-precision grade castings. With the increase of labor cost and the improvement of the precision of wood mold, the application of five-axis linkage machining center to make V-wood mold will become the development trend of the foundry mold industry.
1. Customer five-axis linkage machining center main parameters
The machining center has a gantry structure with a table size of 1600×1600 mm, an X×Y×Z stroke of 3000×2600×950 mm, an A-axis tilt angle of ±135°, and a C-axis rotation angle of ±200°. It has a disc turret type magazine that can hold 16 tools, all of which are automatically changed, and the main machine adopts FANUC servo control system.
2. Traditional wood mold making process
The traditional wood mold manufacturing method is based on the casting process drawings of the parts, determining the model classification, module structure, hand drawing the stakeout drawing, and making the block making and assembling.
Among them, the lofting is the specificization of the dimensions of the two-dimensional drawings of the parts, that is, the standard of module production.
At the same time, it is also a key process in the design and manufacture of the model, which requires high technical level for the mold maker.
For some complicated parts, in the mold manufacturing process, due to the imperfect dimensions of the two-dimensional drawings and the incomplete understanding of the drawings by the mold makers, the molds produced are inevitably subject to inaccurate dimensions.
Most of these problems can only be gradually verified in the model manufacturing process, and some can only be discovered after the castings are manufactured. This not only increases the workload of mold development, delays the development of new products, but also has problems such as low mold accuracy.
3. Five-axis machining center application process
3.1 Casting mold three-dimensional design
At this stage, the V-balanced heavy-duty product design is generally carried out using 3D CAD software. During the casting mold design process, enter the customer's product 3D map into Solidworks software. According to the casting process drawings of the product, the parameters such as shrinkage of the mold and draft of the draft are set, and the three-dimensional drawing of the upper and lower molds is drawn, as shown in Fig. 1.
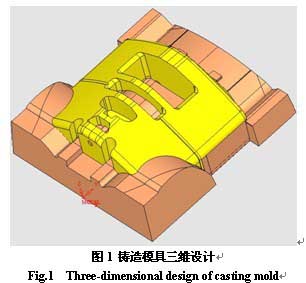
Fig. 1 Casting mold
3.2 Processing and post-processing
Our company uses Cimatron E8.5 programming software, Cimatron E8.5 is a product of Israel Cimatron company. Cimatron E's CNC machining technology has always been a world leader and is widely regarded as one of the most outstanding CNC programming software. Cimatron E8.5 supports programming from 2.5 to 5 axes.
The processing program is generally divided into the following steps:
1) According to the characteristics of casting molds, preliminary development of processing technology;
2 》Program according to the different surfaces of the mold, select the appropriate machining program. Select the appropriate tool, spindle speed, feed speed, tool path and other machining parameters to generate the tool path. as shown in picture 2;
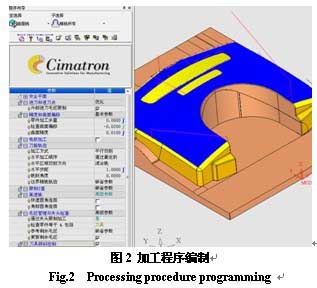
The post-processing program is a compiling software between the tool path source file generated by the general-purpose numerical control programming software and the NC program in the ISO format that can be recognized by the special numerical control machining center. Figure 3 shows the postprocessor developed by Cimatron for our Master546 model.
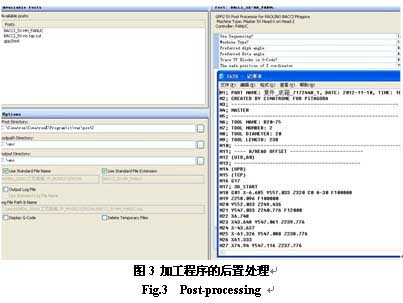
3.3 Five-axis machining program simulation check
Italy Paolino Bacci developed an intelligent 3D solid machine simulation software Pitagora. Accurate and realistic dynamic simulation of the motion process of the 5-axis CNC machining center can be directly read into the ISO code generated by Cimatron E post processing. It can perform dynamic zoom rotation, machining over stroke check, interference collision check, tool head fast moving track adjustment and machining time calculation, as shown in Figure 4. Pitagora ensures the accuracy and security of the programs programmed by Cimatron E and is very practical.
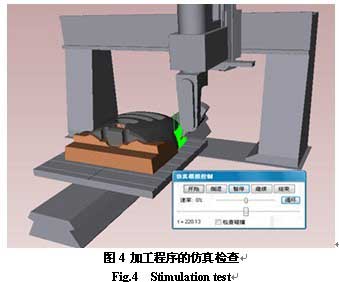
3.4 Five-axis production of mold blanks
According to the casting process drawings, a mold blank with appropriate margin can be produced without considering the detailed dimensions, which reduces the workload of the mold maker.
3.5 Model processing
As shown in Figure 5. The model blank is fixed on the machining center table by a special pressing tool, and the relationship between the workpiece coordinate system and the machining coordinate system is realized through setting;
The NC program is input to the machining center, and the conversion of the encoder is realized to realize the linkage of the respective cutter axes of the machining center, thereby completing the model processing. For the mold is not easy to take the mold, need to do the live block, the live block can be directly processed on the model.
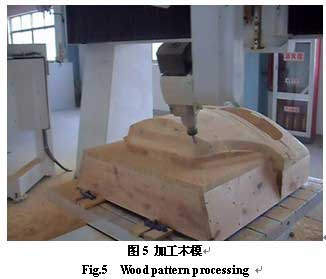
4 Conclusion
Through the application of the five-axis linkage machining center, the labor cost is saved and the development cycle of the V-method is shortened. Moreover, it is possible to produce high-precision curved surfaces to produce high-precision models, and to produce high-precision grade castings. With the increase of labor cost and the improvement of the precision of wood mold, the application of five-axis linkage machining center to make V-wood mold will become the development trend of the foundry mold industry.